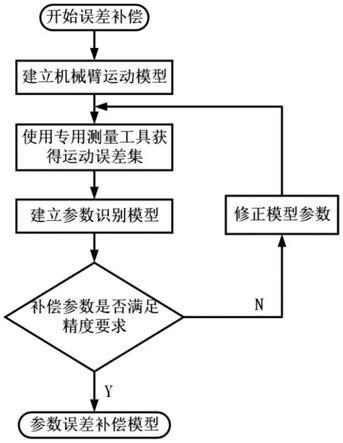
1.本发明属于机械臂精度控制技术领域,涉及一种机械臂参数误差识别及补偿方法。
背景技术:2.有研究结果表明:绝大多数的机械臂位置误差都是由机械臂内部运动学模型的不准确描述引起的,所以对机械臂运动学模型参数进行标定是很有必要的。因此,需要对机械臂本身存在的参数误差进行识别和补偿,从而提高机械臂的绝对定位精度,这对于扩展机械臂的应用范围有着极其重要的意义
3.目前国内外常用高精密激光跟踪仪直接测量机械臂末端执行器的位置,通过对末端执行器的实际位置与理论位置进行比较,从而反算出末端执行器的位置与位姿误差。
4.激光跟踪仪工作范围大,测量效率高,而且在测量时为非接触式测量,可以实时对移动中物体的相关数据进行采集,适合对大尺寸的装配任务和机器人进行测量,但造价较为昂贵,在安装和使用上对人员有一定的要求,测量所使用的光源对周围的环境要求也比较高,不适用于设备密集的工厂环境。
5.因此,在机械臂领域内,需要一种操作方便,受环境影响小,价格相对低廉的机械臂参数识别方法。
技术实现要素:6.本发明的目的是提供一种机械臂参数误差识别及补偿方法,解决了现有检测技术价格昂贵、操作不便、对环境要求高的问题。
7.本发明所采用的技术方案是,一种机械臂参数误差识别及补偿方法,利用一套测量工具,按照以下步骤实施:
8.步骤1:安装试件,
9.将机械臂末端与气动夹具连接牢靠,气动夹具上的夹爪夹持住夹持柄;调整测量架上的激光位移传感器和位移传感器一、位移传感器二的位姿,使其与标定件的测量平面垂直;
10.步骤2:建立机械臂运动学模型,
11.2.1)设置相关的机械臂模型参数,
12.2.2)通过坐标变换,建立机械臂运动学模型;
13.步骤3:向机器人控制系统输入-z方向的运动指令,利用位移传感器一、位移传感器二测量x、y向的运动误差,利用激光位移传感器测量机械臂末端-z方向的位移,
14.步骤4:建立机械臂的参数误差补偿模型;
15.步骤5:完成机械臂误差补偿,
16.根据vj的数值补偿机械臂控制系统中的几何参数设定,得到补偿后的几何参数误差的机械臂系统。
17.本发明的有益效果是,使用简单高效的算法,避免了传统测量机械臂参数误差方法带来的价格昂贵、操作复杂的缺点。
附图说明
18.图1为本发明方法采用的测量工具的结构示意图;
19.图2为本发明方法对机械臂参数误差过程识别运动示意图;
20.图3为本发明方法中的机械臂运动学模型的简图;
21.图4为本发明方法中的参数误差识别计算流程图;
22.图5是本发明方法的整体流程示意图;
23.图6a参数误差补偿前后x方向数据误差值对比图;
24.图6b参数误差补偿前后y方向数据误差值对比图。
25.图中,1.气动夹具,2.夹爪,3.夹持柄,4.测量架,5.激光位移传感器,6.位移传感器一,7.位移传感器二,8.标定件。
具体实施方式
26.下面结合附图和具体实施方式对本发明进行详细说明。
27.参照图1、图2,本发明方法采用的机械臂参数误差识别的测量工具结构是,包括气动夹具1,气动夹具1上的夹爪2与夹持柄3连接;夹持柄3另一端固定有测量架4,测量架4上设置有激光位移传感器5、位移传感器一6、位移传感器二7,测量时该三个传感器均与标定件8的测量平面垂直。
28.参照图5,本发明所描述的参数误差识别及补偿方法,利用上述的测量工具,按照以下步骤实施:
29.步骤1:安装试件,
30.将机械臂末端与气动夹具1连接牢靠,气动夹具1上的夹爪2夹持住夹持柄3;调整测量架4上的激光位移传感器5和位移传感器一6、位移传感器二7的位姿,使其与标定件8的测量平面垂直;
31.步骤2:建立机械臂运动学模型,
32.2.1)设置相关的机械臂模型参数,
33.参照图3,选取机械臂安装基座建立基坐标系,x0、y0、z0表示机械臂基坐标系的坐标轴;对机械臂的六个关节分别建立关节坐标系,其中xi、yi、zi分别表示六自由度机械臂的六个关节坐标系的坐标轴;依据上述的测量工具在基坐标系下的相对位置,建立测量工具坐标系,其中x7、y7、z7表示测量工具的坐标轴;dj表示沿zj轴正方向的j关节坐标系原点从x
j-1
移动到xj的距离;ak表示沿xk轴正方向的k关节坐标系原点从zk移动到z
k+1
的距离;
34.本步骤中,i=1,2,...,6,j=1,2,...,7,k=1,2,...,6;
35.2.2)通过坐标变换,建立机械臂运动学模型,表达式为:
36.37.其中,
38.i
x
=c1[c
2,3
(c4c5c
6-s4s6)-s
2,3
s5c6]-s1(s4c5c6+c4s6);
[0039]iy
=s1[c
2,3
(c4c5c
6-s4s6)-s
2,3
s5c6]+c1(s4c5c6+c4s6);
[0040]iz
=s
2,3
(s4s
6-c4c5c6)+c
2,3
s5c6;
[0041]jx
=-c1[c
2,3
(c4c5s6+s4c6)+s
2,3
s5s6]+s1(s4c5s
6-c4c6);
[0042]jy
=-s1[c
2,3
(c4c5s6+s4c6)+s
2,3
s5s6]-c1(s4c5s
6-c4c6);
[0043]jz
=s
2,3
(c4c5s6+s4c6)-c
2,3
s5s6;
[0044]kx
=c1(-c
2,3
c4s5+s
2,3
c5)+s1s4s5;
[0045]ky
=s1(-c
2,3
c4s5+s
2,3
c5)+c1s4s5;
[0046]kz
=c
2,3
c5+s
2,3
c4s5;
[0047]
p
x
=c1[a2c2+(a
3-d7c4s5)c
2,3
+(d4+d7c5)s
2,3
]+s1(d7s4s
5-d3);
[0048]
py=s1[a2c2+(a
3-d7c4s5)c
2,3
+(d4+d7c5)s
2,3
]-c1(d7s4s
5-d3);
[0049]
pz=d1+(d7c4s
5-a3)s
2,3
+(d7c5+d4)c
2,3-a2s2;
[0050]
上式中,i
x
表示机械臂末端坐标系x轴在基坐标系x轴上的分量;
[0051]iy
表示机械臂末端坐标系x轴在基坐标系y轴上的分量;
[0052]iz
表示机械臂末端坐标系x轴在基坐标系z轴上的分量;
[0053]jx
表示机械臂末端坐标系y轴在基坐标系x轴上的分量;
[0054]jy
表示机械臂末端坐标系y轴在基坐标系y轴上的分量;
[0055]jz
表示机械臂末端坐标系y轴在基坐标系z轴上的分量;
[0056]kx
表示机械臂末端坐标系z轴在基坐标系x轴上的分量;
[0057]ky
表示机械臂末端坐标系z轴在基坐标系y轴上的分量;
[0058]kz
表示机械臂末端坐标系z轴在基坐标系z轴上的分量;
[0059]
p
x
表示机械臂末端相对于原点坐标在x向的位移;
[0060]
py表示机械臂末端相对于原点坐标在y向的位移;
[0061]
pz表示机械臂末端相对于原点坐标在z方向的位移;
[0062]si,j
=sin(θi+θj),c
i,j
=cos(θi+θj),θi与θj分别表示各个关节转角值,本步骤中,i=1,2,
…
,6,j=1,2,
…
,6;
[0063]
步骤3:向机器人控制系统输入-z方向的运动指令,利用两个位移传感器(即位移传感器一6、位移传感器二7)测量x、y向的运动误差,利用激光位移传感器5测量机械臂末端-z方向的位移,
[0064]
本步骤的目的是测量移动过程中机械臂参数误差对机械臂末端运动轨迹的影响,通过读取上述测量工具中相关传感器的数值,获得x、y向的运动误差集e
x
={x1,x2,...,xi}i=1,2,...,n和ey={y1,y2,...,yi}i=1,2,...,n;再通过机械臂控制系统,获得位移误差集对应的关节转角集合,表达式如下:
[0065][0066]
式中,表示在运动到某个点时关节角θ2,θ3,θ4,θ5组成的向量;
[0067]
步骤4:参照图4,建立机械臂的参数误差补偿模型,
[0068]
4.1)根据步骤2得到的机械臂运动学模型,建立参数误差补偿模型,机械臂x、y向
的坐标表达式如前所示,分别为:
[0069]
p
x
=c1[a2c2+(a
3-d7c4s5)c
23
+(d4+d7c5)s
23
]+s1(d7s4s
5-d3)
ꢀꢀꢀꢀꢀꢀꢀꢀꢀꢀꢀꢀꢀ
(1)
[0070]
py=s1[a2c2+(a
3-d7c4s5)c
23
+(d4+d7c5)s
23
]-c1(d7s4s
5-d3)
ꢀꢀꢀꢀꢀꢀꢀꢀꢀꢀꢀꢀꢀꢀ
(2)
[0071]
设机械臂运动平面为工作坐标系的xoz面,将上述两式简写为:
[0072]
p
x
=f
x
(θ2,θ3,θ4,θ5,d3,d4,d7,a2,a3);
ꢀꢀꢀꢀꢀꢀꢀꢀꢀꢀꢀꢀꢀꢀꢀꢀꢀꢀꢀꢀꢀꢀꢀꢀꢀꢀꢀꢀꢀꢀꢀꢀꢀ
(3)
[0073]
py=fy(θ2,θ3,θ4,θ5,d3,d4,d7);
ꢀꢀꢀꢀꢀꢀꢀꢀꢀꢀꢀꢀꢀꢀꢀꢀꢀꢀꢀꢀꢀꢀꢀꢀꢀꢀꢀꢀꢀꢀꢀꢀꢀꢀꢀꢀꢀ
(4)
[0074]
式中,ai表示连杆长度;θi表示关节转角;di表示连杆偏置距离;
[0075]
引入参数误差后,机械臂x、y向的坐标变换为:
[0076][0077]
py'=fy(θ2+δθ2,θ3+δθ3,θ4+δθ4,θ5+δθ5,d3+δd3,d4+δd4,d7+δd7);
ꢀꢀ
(6)
[0078]
式中,δai表示连杆长度误差;δθi表示关节转角误差;δdi表示连杆偏置距离误差;
[0079]
由误差和理论位置的关系,则有:p
′
x
=p
x
+δx,p
′y=py+δy,将该两式相减后整理得到下式(7):
[0080]
δy=p
′
y-py+p
′
x-p
x
+δx
ꢀꢀ
(7)
[0081]
将测量得到的误差集带入式(7)中,得到非线性参数拟合方程组:
[0082]
yi=p
′
y-py+p
′
x-p
x
+x
i i=1,2,...,n
ꢀꢀ
(8)
[0083]
为了推导方便,令yi=g(θ2,θ3,θ4,θ5,xi)i=1,2,...,n;
[0084]
4.2)由式(8)可知:机械臂在z向上运动的参数误差补偿问题能够描述如下:通过非线性方程拟合一组系数δθ2,δθ3,δθ4,δθ5,δd3,δd4,δd7,δa2,δa3,使得在不同的关节转动角度θi下,并且残差值最小,则该问题中的待求解系数δθ2,δθ3,δθ4,δθ5,δd3,δd4,δd7,δa2,δa3即为机械臂几何参数误差,其解法具体如下:
[0085]
4.2.1)在非线性参数拟合方程式(8)中待求解参数总共包含九个,分别是δθ2,δθ3,δθ4,δθ5,δd3,δd4,δd7,δa2,δa3,为方便计算,下文中将其命名为v
j,i
(j=1~9,j∈z),i为迭代次数,对九个未知量赋初值,在理想状况下,机械臂的几何参数误差均为0,因此将九个未知量的初始值均设为0;
[0086]
4.2.2)根据给定未知量的初始值,将实验得到的n组相对位移误差集的数值分别代入方程yi=g(θ2,θ3,θ4,θ5,xi)i=1,2,...,n中,得到n组计算结果,将计算出的集合命名为f
i-1
,将f
i-1
与ey中对应的值进行对比,计算第一个残差平方和γ
i-1
;
[0087]
4.2.3)引入增幅系数λ=0.001,使用v
j,i
=v
j,i-1
+λ对vj的数值进行替代,并将n组数据的θ2,θ3,θ4,θ5代入方程yi=g(θ2,θ3,θ4,θ5,xi)i=1,2,...,n中,计算出n组函数的数值,将计算出的数组命名为fi,将fi与ey中对应的函数值进行对比,计算第二个残差平方和γi,将计算得到的两个残差平方和γi与γ
i-1
进行对比,
[0088]
对比后存在两种结果,分别分析如下:
[0089]
a)当γi≤γ
i-1
时,认为改变后的vi的数值所对应的解为更优解,并使用10λ对v
j,i
=v
j,i-1
+λ中的λ进行替代,并重复步骤4.2.3)中计算过程,直到计算出γi>γ
i-1
;
[0090]
b)当γi>γ
i-1
时,认为改变前的v
j,i-1
的数值所对应的解为更优解,此时,未知量
中有一个数值已经达到了最优解,改变其中的一个数值,并固定另外八个未知量的数值不变,并进行计算,具体过程是:
[0091]
①
固定v2~v9八个数值不变,同时改变v1的数值,在v
1,i
=v
1,i-1
+λ中,使用λ/10对原有λ进行替代,并重复步骤4.2.3)中计算过程,直到计算出γi>γ
i-1
,此时v1的数值已经达到最优解,并记录此时v1的具体数值;
[0092]
②
当v1得到最优解后,固定v1与v3~v9八个数值不变,同时改变v2的数值,在v
2,i
=v
2,i-1
+λ中,使用λ/10对原有λ进行替代,并重复步骤4.2.3)中计算过程,直到计算出γi>γ
i-1
,此时v2的数值已经达到最优解,并记录此时v2的数值;
[0093]
③
其余7个参数的数值均按照上述
①②
中的方法进行计算,最终得到记录下v的9组数值;
[0094]
4.2.4)完成前述v的9组数值记录后,上述迭代过程结束,此时对应的为最小的残差平方和,即vj数值就是机械臂几何参数误差的求解结果;
[0095]
在步骤4.2)中的z向表述的是机械臂末端的运动方向,并非误差采集方向。在式(8)中,已将xy两个方向的误差集综合考虑,这里计算时只需控制等式左侧y的残差数值即可,并不需要单独再对x方向的残差进行计算,最终使得残差平方和最小的解即为机械臂几何参数误差求解结果。
[0096]
步骤5:完成机械臂误差补偿,
[0097]
根据vj的数值补偿机械臂控制系统中的几何参数设定,得到补偿后的几何参数误差的机械臂系统,即成。
[0098]
实验验证:
[0099]
使用本发明公开的机械臂参数误差识别及补偿方法,根据vj的数值补偿机械臂控制系统中的几何参数设定,得到补偿后的几何参数误差的机械臂系统。接下来将对几何参数误差的补偿结果进行检验。几何参数误差补偿结果检验的实验步骤与前述步骤3基本相同,区别是使用的机械臂系统参数是补偿后的参数,并且补偿结果检验的实验过程中仅需对位移传感器的读数进行记录,不需要对关节转动角度进行读取。
[0100]
表1、实验结果
[0101][0102]
根据图6a、图6b与表1中得到的实验结果可以发现,几何参数误差补偿后,实验测得的数据在x方向与y方向均较为平稳,机器人末端执行器位置精度得到了显著提升,位置a处x方向位置精度提升57.6%,y方向位置精度提升52.5%。