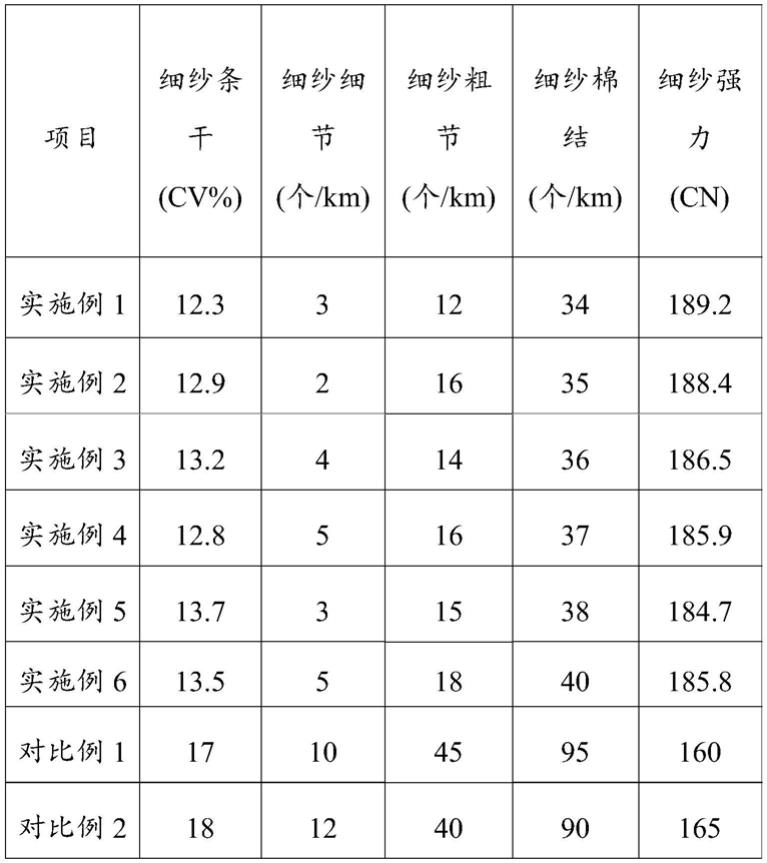
1.本发明涉及纺织领域,尤其涉及一种吸湿速干纱及其生产方法和应用。
背景技术:2.莫代尔面料轻薄、柔软、舒适、透气性好,但是易起球,而涤纶面料抗皱性和保形性很好,但是不透气。
3.若能将两者混纺可得到结合两者优点的单纱,但莫代尔纤维和涤纶纤维性能差异大,将两者混纺在生产过程中易出现重量不匀及条干机械波等现象,现有技术中将莫代尔纤维和涤纶纤维进行混纺时不能得到纱较细且品质优良的中高支纱。
技术实现要素:4.本发明所要解决的技术问题是:如何克服莫代尔纤维和涤纶纤维的差异得到纱较细且支数较高的吸湿速干纱。
5.为解决上述技术问题,本发明提出了一种吸湿速干纱及其生产方法和应用。
6.本发明提出一种吸湿速干纱,由莫代尔纤维和涤纶纤维混纺而成,按照质量百分比计算,所述莫代尔纤维占60%
‑
80%,所述涤纶纤维占20
‑
40%。
7.进一步地,所述莫达尔纤维的比强为3.5
‑
3.8cn/dtex、断裂伸长率为15
‑
18%;
8.和/或,所述涤纶纤维的比强为6
‑
6.5cn/dtex、断裂伸长率为20
‑
22.1%。
9.本发明还提出上述吸湿速干纱的生产方法,包括将莫代尔纤维和涤纶纤维作为原料依次经清花工序、梳棉工序、并条工序、粗纱工序、细纱工序和络筒工序加工制得;
10.其中,所述并条工序为:经过二道预并三道并合;
11.所述二道预并分别为:莫代尔纤维预并和涤纶纤维预并,均为8根并合,干重定量18
‑
18.5g/5米;
12.所述三道并合分别为:一并5根并合,并合分配为4根莫代尔纤维预并条、1根涤纶预并条,干重定量16
‑
16.5g/5米;二并8根并合,干重定量16
‑
16.5g/5米;三并8根并合,干重定量16
‑
16.5g/5米。
13.进一步地,在所述二道预并中,所述莫代尔纤维预并的隔距为12mm
×
20mm,所述涤纶纤维预并的隔距为10mm
×
14mm
×
26mm。
14.进一步地,在所述三道并合中,所述一并的罗拉隔距12mm
×
20mm,喇叭口直径3.2mm;所述二并的罗拉隔距12mm
×
20mm,喇叭口直径3.2mm;所述三并的罗拉隔距12mm
×
20mm,喇叭口直径3.2mm。
15.进一步地,所述清花工序中,所述莫代尔纤维和所述涤纶纤维在抓棉圆台上分别成卷的棉卷干重定量为335.5
‑
336.5g/m。
16.进一步地,所述梳棉工序中,梳棉干重定量为18.5
‑
19g/5m。
17.进一步地,所述粗纱工序中,粗纱捻度3.5
‑
4捻/10cm。
18.进一步地,所述细纱工序中,细纱捻度95
‑
120捻/10cm。
19.另外,本发明还提出一种上述吸湿速干纱或者上述生产方法生产得到的吸湿速干纱在制作高档服装面料中的应用。
20.本发明与现有技术对比的有益效果包括:通过控制莫代尔纤维和涤纶纤维的质量百分比,所述莫代尔纤维占60%
‑
80%,所述涤纶纤维占20
‑
40%得到了支数为40
‑
60支的中高支纱,而且纱较细且品质优良。
21.另外本发明将莫代尔纤维和涤纶纤维作为原料依次经清花、梳棉、并条、粗纱、细纱、络筒工序,并通过将并条工序设置为:经过二道预并三道并合;所述二道预并分别为:莫代尔纤维预并和涤纶纤维预并,均为8根并合,干重定量18
‑
18.5g/5米;所述三道并合分别为:一并5根并合,并合分配为4根莫代尔纤维预并条、1根涤纶预并条,干重定量16
‑
16.5g/5米;二并8根并合,干重定量16
‑
16.5g/5米;三并8根并合,干重定量16
‑
16.5g/5米,混纺得到支数为40
‑
60支的紧密纺纱,克服了因莫代尔纤维和涤纶纤维性能差异大,生产过程中易出现重量不匀及条干机械波等现象而导致将莫代尔纤维和涤纶纤维进行混纺时不能得到纱较细且品质优良的中高支纱的问题,所得吸湿速干纱具有轻薄舒适、透气性好、易洗快干、挺括等优点,可用于制作高档服装面料。
具体实施方式
22.本具体实施方式提出一种吸湿速干纱,由莫代尔(简写为mod)纤维和涤纶(简写为t)纤维混纺而成,按照质量百分比计算,所述莫代尔纤维占60%
‑
80%,所述涤纶纤维占20
‑
40%;吸湿速干纱的号数为9.8
‑
14.8tex;其中所述莫代尔纤维和涤纶纤维优选按照80:20的质量比例混纺而成;
23.进一步地,所述莫达尔纤维优选为印度博拉莫代尔纤维的比强为3.5
‑
3.8cn/dtex、断裂伸长率为15
‑
18%、线密度为1.2dtex、长度为38mm;所述涤纶纤维优选为半消光涤纶纤维,涤纶纤维的比强为6
‑
6.5cn/dtex、断裂伸长率为20
‑
22.1%、线密度为1.33dtex、长度为38mm;
24.本具体实施方式还包括上述吸湿速干纱的生产方法,包括将莫代尔纤维和涤纶纤维作为原料依次经清花工序、梳棉工序、并条工序、粗纱工序、细纱工序和络筒工序加工;
25.其中,所述清花工序中,莫代尔纤维和所述涤纶纤维在抓棉圆台上分别成卷的棉卷干重定量为335.5
‑
336.5g/m;
26.所述梳棉工序中,给棉板与刺辊隔距14英丝,锡林与盖板5点隔距为12英丝
×
11英丝
×
10英丝
×
10英丝
×
11英丝,刺辊与小漏底入口隔距10mm,出口隔距2mm,梳棉干重定量为18.5
‑
19g/5m;本具体实施方式中采用对纤维有良好穿刺、握持能力的针布,该针布具有良好的锋利度、光洁度、耐磨性及平整度;生产过程中能够严控棉结杂质,棉结可控制在2粒/克,杂质可控制在0粒/克,减少搓转纤维。
27.所述并条工序为:经过二道预并三道并合,所述二道预并分别为:mod预并和t预并,均为8根并合,干重定量18
‑
18.5g/5米,mod预并隔距为12mm
×
20mm,t预并隔距为10mm
×
14mm
×
26mm;
28.所述三道并合为:一并5根并合,并合分配为4根mod预并条、1根t预并条,干重定量16
‑
16.5g/5米,罗拉隔距12mm
×
20mm,喇叭口直径3.2mm;二并8根并合,干重定量16
‑
16.5g/5米,罗拉隔距12mm
×
20mm,喇叭口直径3.2mm;三并8根并合,干重定量16
‑
16.5g/5米,罗拉
隔距12mm
×
20mm,喇叭口直径3.2mm;因mod纤维和t纤维性能差异过大,为进一步避免生产过程中产生机械波,定期对轴、孔的磨损情况,键与键槽的松动情况,齿轮齿尖磨损与形态,轴承晃动情况定期检查,并定期对轴承部件加油,确保其无缺油或损坏;清理轴套及加油和胶辊校正工作,杜绝轴套、胶辊不良导致出现牵伸机械波;
29.所述粗纱工序中,粗纱捻度3.5
‑
4捻/10cm,罗拉隔距采用26mm
×
37mm,后区牵伸1.2倍,钳口隔距7mm,粗纱干重定量为4.63克/10米,前罗拉转速160r/min,前罗拉直径28mm;粗纱工序的参数设置避免了由前罗拉、胶辊、胶圈在牵伸过程中引起的胶辊、胶圈机械波及齿轮运转不良或齿轮磨损引发的机械波。
30.所述细纱工序中,罗拉隔距为19mm
×
36mm,后区牵伸倍数为1.18倍,钳口隔距3mm,前罗拉直径27mm,前罗拉转速143r/min,细纱捻度95
‑
120捻/10cm,钢领的型号为pg1/2
‑
3854,所用钢丝圈的型号为oss 10/0。细纱生产过程中注意揩车周期,避免出现齿轮咬合不良、胶辊磨损、缠花等造成的机械波。
31.所述络筒工序中,单纱络筒在日本村田的自动络筒机上生产,采用的是乌斯特电子清纱器和空捻无结技术,空捻接头强力占原纱的80%以上,并保证纱疵有效清除;电清参数:棉结n:350%、短粗s:140%
×
1.4cm、长粗l:35%
×
30cm、细节t:
‑
35%
×
30cm;生产出mod/t 80/20 9.8tex紧的单纱,该单纱即为吸湿速干纱。
32.本具体实施方式还包括上述吸湿速干纱或者上述生产方法生产得到的吸湿速干纱在制作高档服装面料中的应用。
33.下面具体描述本发明的优选实施例阐释本发明的原理,并非用于限定本发明的范围。
34.下述实施例中的吸湿速干纱由生产线设备生产得到,生产线采用的设备包括:a002c型自动抓棉机、a036b豪猪开棉机、a092a型双棉箱给棉机、a076c型成卷机、a186梳棉机、fa305型并条机、fa454粗纱机、dtm129细纱机、21c~s络筒机。
35.下述实施例中莫达尔纤维为印度博拉莫代尔纤维,至少达到以下性能标准:比强3.7cn/dtex、断裂伸长率17%、线密度1.2dtex、长度38mm;涤纶纤维为半消光涤纶纤维,至少达到以下性能标准:比强6.3cn/dtex、断裂伸长率22.1%、线密度1.33dtex、长度38mm。
36.实施例1
37.本实施例提出一种吸湿速干纱,按照质量百分比计算,所述莫代尔纤维占80%,所述涤纶纤维占20%,其通过以下工序步骤生产得到:
38.(1)清花工序
39.抓棉机打手速度936r/min,刀片伸出肋条高度2
±
1mm,打手刀片高低控制
±
1mm,打手和天平罗拉的隔距12mm,莫代尔纤维和涤纶纤维需在抓棉圆台上分别成卷,棉卷干重定量为336g/m。
40.(2)梳棉工序
41.梳棉在a186梳棉机上生产,给棉板与刺辊隔距14英丝,锡林与盖板5点隔距为12英丝
×
11英丝
×
10英丝
×
10英丝
×
11英丝,刺辊与小漏底入口隔距10mm,出口隔距2mm,梳棉干重定量为18.7g/5m。
42.(3)并条工序
43.并条经fa305并条机上生产,经过二道预并三道并合,使mod纤维与t纤维充分混
合,避免重量波动。二道预并分别为:mod预并和t预并,均为8根并合,干重定量18.2g/5米,mod预并隔距为12mm
×
20mm,t预并隔距为10mm
×
14mm
×
26mm;
44.所述三道并合分别为:一并5根并合,并合分配为4根mod预并条、1根t预并条,干重定量16.5g/5米,罗拉隔距12mm
×
20mm,喇叭口直径3.2mm;二并8根并合,干重定量16.2g/5米,罗拉隔距12mm
×
20mm,喇叭口直径3.2mm;三并8根并合,干重定量16g/5米,罗拉隔距12mm
×
20mm,喇叭口直径3.2mm。
45.(4)粗纱工序
46.粗纱在fa454粗纱机上生产,粗纱捻度3.95捻/10cm,罗拉隔距采用26mm
×
37mm,后区牵伸1.2倍,钳口隔距7mm,粗纱干重定量为4.63克/10米,机械牵伸7.25倍,前罗拉转速160r/min,前罗拉直径28mm;粗纱工序注意由前罗拉、胶辊、胶圈在牵伸过程中引起的胶辊、胶圈机械波及齿轮运转不良或齿轮磨损引发的机械波。
47.(5)细纱工序
48.细纱在dtm129型细纱机上采用紧密纺生产,机械牵伸倍数54倍,罗拉隔距为19mm
×
36mm,后区牵伸倍数为1.18倍,钳口隔距3mm,前罗拉直径27mm,前罗拉转速143r/min,捻度120捻/10cm,钢领的型号为pg1/2
‑
3854,所用钢丝圈的型号为oss 10/0。
49.(6)络筒工序
50.单纱络筒在日本村田的自动络筒机上生产,采用的是乌斯特电子清纱器和空捻无结技术,空捻接头强力占原纱的80%以上,并保证纱疵有效清除;电清参数:棉结n:350%、短粗s:140%
×
1.4cm、长粗l:35%
×
30cm、细节t:
‑
35%
×
30cm;生产出mod/t 80/20 9.8tex紧的单纱,支数为60支,该单纱即为吸湿速干纱。
51.实施例2
52.本实施例的生产方法与实施例1相同,区别点仅在于莫代尔纤维和涤纶纤维的质量百分比与实施例1不同,所述莫代尔纤维占60%,所述涤纶纤维占40%。生产出mod/t 60/40 11.5ex紧的单纱,支数为51支,该单纱即为吸湿速干纱。
53.实施例3
54.本实施例的生产方法与实施例1相同,区别点仅在于两者的质量百分比与实施例1不同,所述莫代尔纤维占50%,所述涤纶纤维占50%;生产出mod/t 80/20 13.5ex紧的单纱,支数为44支,该单纱即为吸湿速干纱。
55.实施例4
56.本实施例的生产方法与实施例1相同,区别点仅在于两者的质量百分比与实施例1不同,所述莫代尔纤维占70%,所述涤纶纤维占30%。;生产出mod/t 70/30 14ex紧的单纱,支数为42支,该单纱即为吸湿速干纱。
57.实施例5
58.本实施例的生产方法与实施例1基本相同,区别点在于区别点在于各工序的部分工序条件不同,具体如下:
59.所述清花工序中,莫代尔纤维和所述涤纶纤维在抓棉圆台上分别成卷的棉卷干重定量为335.5g/m;
60.所述梳棉工序中,给棉板与刺辊隔距14英丝,锡林与盖板5点隔距为12英丝
×
11英丝
×
10英丝
×
10英丝
×
11英丝,刺辊与小漏底入口隔距10mm,出口隔距2mm,梳棉干重定量
为19g/5m;
61.所述并条工序为:经过二道预并三道并合,所述二道预并分别为:mod预并和t预并,均为8根并合,干重定量18g/5米,mod预并隔距为12mm
×
20mm,t预并隔距为10mm
×
14mm
×
26mm;
62.所述三道并合为:一并5根并合,并合分配为4根mod预并条、1根t预并条,干重定量16g/5米,罗拉隔距12mm
×
20mm,喇叭口直径3.2mm;二并8根并合,干重定量16
‑
16.5g/5米,罗拉隔距12mm
×
20mm,喇叭口直径3.2mm;三并8根并合,干重定量16g/5米,罗拉隔距12mm
×
20mm,喇叭口直径3.2mm;因mod纤维和t纤维性能差异过大,为进一步避免生产过程中产生机械波,定期对轴、孔的磨损情况,键与键槽的松动情况,齿轮齿尖磨损与形态,轴承晃动情况定期检查,并定期对轴承部件加油,确保其无缺油或损坏;清理轴套及加油和胶辊校正工作,杜绝轴套、胶辊不良导致出现牵伸机械波;
63.所述粗纱工序中,粗纱捻度3.5捻/10cm,罗拉隔距采用26mm
×
37mm,后区牵伸1.2倍,钳口隔距7mm,粗纱干重定量为4.63克/10米,前罗拉转速160r/min,前罗拉直径28mm;粗纱工序的参数设置避免了由前罗拉、胶辊、胶圈在牵伸过程中引起的胶辊、胶圈机械波及齿轮运转不良或齿轮磨损引发的机械波。
64.所述细纱工序中,罗拉隔距为19mm
×
36mm,后区牵伸倍数为1.18倍,钳口隔距3mm,前罗拉直径27mm,前罗拉转速143r/min,细纱捻度95捻/10cm,钢领的型号为pg1/2
‑
3854,所用钢丝圈的型号为oss 10/0。
65.所述络筒工序中,单纱络筒在日本村田的自动络筒机上生产,采用的是乌斯特电子清纱器和空捻无结技术,空捻接头强力占原纱的80%以上,并保证纱疵有效清除;电清参数:棉结n:350%、短粗s:140%
×
1.4cm、长粗l:35%
×
30cm、细节t:
‑
35%
×
30cm;生产出mod/t 80/20 9.8tex紧的单纱,支数为60支,该单纱即为吸湿速干纱。
66.实施例6
67.本实施例的生产方法与实施例1基本相同,区别点在于区别点在于各工序的部分工序条件不同,具体如下:
68.所述清花工序中,莫代尔纤维和所述涤纶纤维在抓棉圆台上分别成卷的棉卷干重定量为336g/m;
69.所述梳棉工序中,给棉板与刺辊隔距14英丝,锡林与盖板5点隔距为12英丝
×
11英丝
×
10英丝
×
10英丝
×
11英丝,刺辊与小漏底入口隔距10mm,出口隔距2mm,梳棉干重定量为18.5g/5m;
70.所述并条工序为:经过二道预并三道并合,所述二道预并分别为:mod预并和t预并,均为8根并合,干重定量18.2g/5米,mod预并隔距为12mm
×
20mm,t预并隔距为10mm
×
14mm
×
26mm;
71.所述三道并合为:一并5根并合,并合分配为4根mod预并条、1根t预并条,干重定量16.5g/5米,罗拉隔距12mm
×
20mm,喇叭口直径3.2mm;二并8根并合,干重定量16.5g/5米,罗拉隔距12mm
×
20mm,喇叭口直径3.2mm;三并8根并合,干重定量16.5g/5米,罗拉隔距12mm
×
20mm,喇叭口直径3.2mm;
72.所述粗纱工序中,粗纱捻度3.5捻/10cm,罗拉隔距采用26mm
×
37mm,后区牵伸1.2倍,钳口隔距7mm,粗纱干重定量为4.63克/10米,前罗拉转速160r/min,前罗拉直径28mm;粗
纱工序的参数设置避免了由前罗拉、胶辊、胶圈在牵伸过程中引起的胶辊、胶圈机械波及齿轮运转不良或齿轮磨损引发的机械波;
73.所述细纱工序中,罗拉隔距为19mm
×
36mm,后区牵伸倍数为1.18倍,钳口隔距3mm,前罗拉直径27mm,前罗拉转速143r/min,细纱捻度95捻/10cm,钢领的型号为pg1/2
‑
3854,所用钢丝圈的型号为oss 10/0;
74.所述络筒工序中,单纱络筒在日本村田的自动络筒机上生产,采用的是乌斯特电子清纱器和空捻无结技术,空捻接头强力占原纱的80%以上,并保证纱疵有效清除;电清参数:棉结n:350%、短粗s:140%
×
1.4cm、长粗l:35%
×
30cm、细节t:
‑
35%
×
30cm;生产出mod/t 80/20 12ex紧的单纱,支数为49支,该单纱即为吸湿速干纱。
75.对比例1
76.该对比例中的吸湿速干纱,按照质量百分比计算,所述莫代尔纤维占52%,所述涤纶纤维占48%;按照实施例1的生产方法生产得到。
77.对比例2
78.本对比例中的并条工序与实施例1不同,其余都相同,并条工序具体如下:
79.所述二道预并分别为:莫代尔纤维预并和涤纶纤维预并,均为7根并合,干重定量18.2g/5米,mod预并隔距为12mm
×
20mm,t预并隔距为10mm
×
14mm
×
26mm;
80.所述三道并合分别为:一并7根并合,并合分配为5根mod预并条、2根t预并条,干重定量16.5g/5米,罗拉隔距12mm
×
20mm,喇叭口直径3.2mm;二并7根并合,干重定量16.2g/5米,罗拉隔距12mm
×
20mm,喇叭口直径3.2mm;三并7根并合,干重定量16g/5米,罗拉隔距12mm
×
20mm,喇叭口直径3.2mm。
81.性能测试
82.根据纺织领域的常规方法或国家标准对实施例1、2生产出的吸湿速干纱进行相关性能的测试,测试结果见表1。需要说明的是,本发明中,纱线截面等于或小于平均截面的50%为细纱细节、纱线截面大于或等于平均截面的50%细纱粗节。
83.表1实施例1
‑
6及对比例1
‑
2中生产出的吸湿速干纱的性能测试结果
[0084][0085]
由上表1的数据可知,实施例1
‑
6中得到的吸湿速干纱的细纱条干较小,并且具有较好的细纱强力,而且细纱粗节和细纱细节都较少。因此,通过本发明提供的方法可以得到品质较好的吸湿速干纱。
[0086]
同时,本发明生产的吸湿速干纱,轻薄舒适、透气性好、易洗快干、挺括,既保持了涤纶易洗快干、耐磨、挺括、凉爽的优点,又能弥补涤纶吸湿性差、舒适性差的缺点,可广泛应用于高档服装领域。
[0087]
本发明的其他有益效果包括:
[0088]
1)本发明将莫代尔纤维和涤纶纤维混纺得到支数为40
‑
60支的紧密纺纱,克服了因莫代尔纤维和涤纶纤维性能差异大,生产过程中易出现重量不匀及条干机械波等现象而导致将莫代尔纤维和涤纶纤维进行混纺时不能得到纱较细且品质优良的中高支纱的问题;
[0089]
2)本发明提供的生产方法以莫代尔纤维和涤纶纤维作为原料,依次经清花、梳棉、并条、粗纱、细纱、络筒工序,并合理调节各工艺参数,可得到支数为40
‑
60支的紧密纺纱;
[0090]
3)本发明得到的吸湿速干纱具有轻薄舒适、透气性好、易洗快干、挺括等优点,可用于制作高档服装面料。
[0091]
以上所述,仅为本发明较佳的具体实施方式,但本发明的保护范围并不局限于此,
任何熟悉本技术领域的技术人员在本发明揭露的技术范围内,可轻易想到的变化或替换,都应涵盖在本发明的保护范围之内。