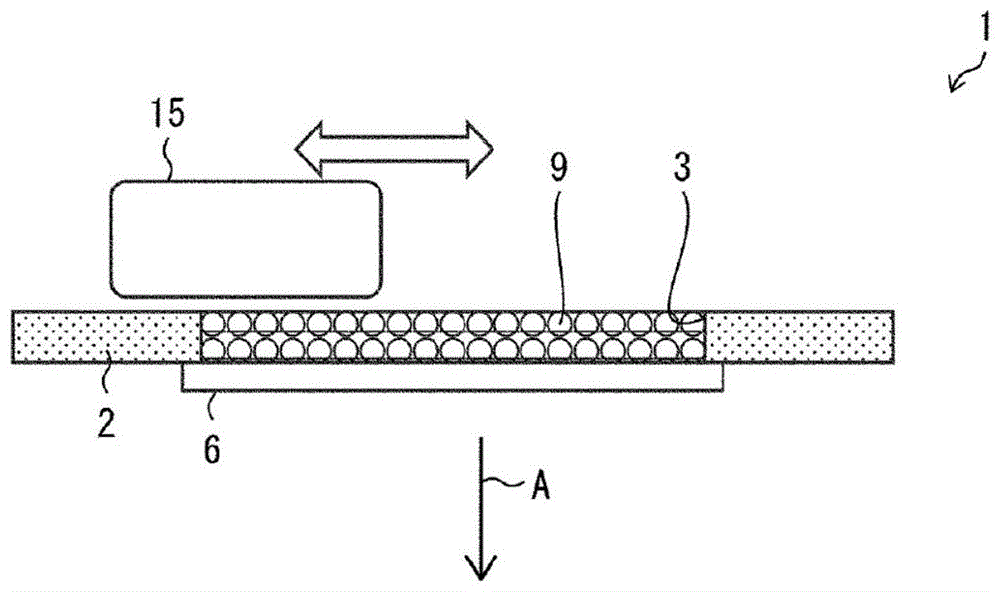
本发明涉及通过使用了固定粉体材料的印刷技术在基板上形成粉体膜的粉体膜形成方法以及粉体成膜装置。
背景技术:
:作为现有技术,已知有用刮入体将粉体刮入到丝网来形成粉体膜的静电丝网印刷法(专利文献1)。该专利文献1所记载的静电成膜装置具备将粉体刮入到丝网的刮入体(丝网刷)、以及将粉体供给到刮入体的料斗。通过使上述料斗与上述刮入体能够彼此独立地动作,能够提高由上述静电成膜装置成膜的粉体膜的膜厚精度。已知有一种通过静电丝网印刷装置在基板上形成粉体膜的技术(专利文献2)。该专利文献2所记载的静电丝网印刷装置具备多孔体的丝网印版。丝网印版与直流电源的一端连接。供给到丝网印版上的粉体被刮入体刮入丝网印版。由此,粉体与丝网印版接触而带电。这样带电的粉体通过静电感应而附着于与直流电源的另一端连接的被印刷物,形成粉体膜。专利文献1:日本公开公报“特开2012-179786号公报(2012年09月20日公开)”专利文献2:日本公开公报“特开2012-140016号公报(2012年07月26日公开)”但是,在上述的专利文献1的现有技术中,在基于被刮入体刮入到丝网的粉体而在基板上成膜的粉体膜中,由于供给到丝网的粉体的散布状态、以及刮入体的移动的轨迹而产生成膜偏差。因此,存在由静电成膜装置成膜的粉体膜的膜厚精度不够的问题。技术实现要素:本发明的一个方式的目的在于实现能够以良好的膜厚精度形成粉体膜的粉体膜形成方法以及粉体成膜装置。为了解决上述的课题,本发明的一方式所涉及的粉体膜形成方法的特征在于,包括:填充工序,在该填充工序中,向形成于粉体填充部件的开口部填充粉体;以及成膜工序,在该成膜工序中,在所述粉体填充部件与基板之间产生电位差,使填充于所述开口部的粉体向所述基板移动而形成粉体膜。为了解决上述的课题,本发明的一方式所涉及的粉体成膜装置的特征在于,具备:粉体填充部件,形成有被填充粉体的开口部;刮入体,从所述开口部的一端侧通过刮入而将所述粉体填充于所述开口部;电源,在所述粉体填充部件与基板之间产生电位差,使填充于所述开口部的粉体向所述基板移动。为了解决上述的课题,本发明的一方式所涉及的其他粉体膜形成方法的特征在于,包括:填充工序,在该填充工序中,使粉体振动而填充于形成于粉体填充部件的开口部;成膜工序,在该成膜工序中,使填充于所述开口部的粉体向所述基板移动而形成粉体膜。根据本发明的一个方式,能够以良好的膜厚精度形成粉体膜。附图说明图1是示出实施方式1所涉及的粉体膜形成方法的填充工序的剖视图。图2是示出在上述填充工序中使用的丝网印版的构成的剖视图。图3是示出上述粉体膜形成方法的成膜工序的剖视图。图4的(a)是示出实施方式2所涉及的粉体膜形成方法的填充工序的剖视图,图4的(b)是实施方式2所涉及的压板的俯视图。图5是示出实施方式4所涉及的粉体膜形成方法的填充工序的剖视图。图6是示出上述粉体膜形成方法的成膜工序的剖视图。图7是示出实施方式5所涉及的粉体膜形成方法的填充工序的剖视图。图8是示出比较例所涉及的粉体膜形成方法的剖视图。图9是示出实施方式6所涉及的粉体膜形成方法的供给工序的剖视图。图10是示出在上述供给工序中散布粉体试样的供给容器的照片。图11是示出上述粉体膜形成方法的填充工序的剖视图。图12是示出在上述填充工序中使用的丝网印版的构成的剖视图。图13的(a)是从乳剂侧观察经上述填充工序填充后的丝网印版的照片,图13的(b)是从网孔侧观察的照片。图14是示出上述粉体膜形成方法的成膜工序中的即将刮入之前的状态的剖视图。图15是示出在上述成膜工序中通过静电感应使粉体向被印刷物附着的状态的剖视图。图16是示出在上述成膜工序中成膜于被印刷物的粉体膜的照片。图17是示出实施方式7所涉及的粉体膜形成方法的填充工序的剖视图。图18是示出实施方式8所涉及的粉体膜形成方法中的乳剂厚度与涂布量之间的关系的图表。图19是示出比较例所涉及的粉体膜形成方法的剖视图。具体实施方式以下,对本发明的实施方式详细地进行说明。静电丝网印刷法由于附着以及堆积粉体的对象物不被压迫,所以在担心由于压迫而被压碎的食品等对象物中被广泛使用。该静电丝网印刷法是通过静电力堆积原料的粉体的方法。因此,在静电丝网印刷法中存在多个难以为了确保膜厚精度而再现性良好地进行管理的项目。该项目例如是丝网印版上的粉体的散布状态、以及丝网刷在丝网印版上扫描的次数等。因此,在静电丝网印刷法中,存在有时无法获得足够的膜厚精度的课题。例如,在(
背景技术:
)一栏的上述的专利文献1的现有技术中,在基于被刮入体刮入丝网的粉体而成膜于基板的粉体膜中,由于供给到丝网的粉体的散布状态、以及刮入体的移动的轨迹,而产生成膜偏差。因此,存在由静电成膜装置成膜的粉体膜的膜厚精度不够的问题。因此,本申请的发明人们针对上述课题进行了深入研究,结果发现:通过在丝网印版等的多孔体的开口部填充粉体,基于静电力和刮入体的刮入将填充于该开口部的粉体涂布于对象物,从而能够得到足够的膜厚精度。在本申请说明书中,所谓“填充”是指:向开口部的空出的部位塞入粉体并堵塞,维持该状态。因而,例如,粉体仅在开口部通过这样的方式不是本申请说明书中的“填充”。(实施方式1)实施方式所涉及的粉体膜形成方法涉及粉体成膜时使用的制造方法,更详细地说,是粉体的干式成膜方法。该粉体膜形成方法包括:向被实施了微细加工的丝网印版、金属印版等多孔体的开口部填充粉体的填充工序;以及使填充的粉体移动而在对象物成膜的成膜工序。由此,通过使以一定的厚度填充于多孔体的开口部并保持于多孔体的粉体向基板移动,能够形成一定厚度的粉体膜。因此,能够形成成膜精度良好的粉体膜。以下,首先对实施方式所涉及的填充工序进行说明。(填充工序)图1是示出实施方式1所涉及的粉体膜形成方法的填充工序的剖视图。粉体成膜装置1具备丝网印版2(粉体填充部件)。图2是示出在上述填充工序中使用的丝网印版2的构成的剖视图。丝网印版2包括丝网网孔(screenmesh)4(多孔体)和形成于丝网网孔4的一个面的丝网乳剂部5(被覆部)。开口部3形成于该丝网乳剂部5。丝网印版2能够使用丝网印刷用的一般的不锈钢网孔。丝网印版2的开口部3的形状能够设为例如边长为50mm的正方形状。但是,能够通过改变开口部3的形状而形成任意形状的粉体膜11。在本实施方式中,使用具有网孔数300/inch、线径30μm(纱厚t1=60μm)、开孔55μm的丝网网孔4的丝网印版2。如图2所示,本实施方式中使用的丝网印版2形成为:丝网乳剂部5从丝网网孔4的一个面朝向另一个面从另一个面露出。这样,丝网乳剂部5形成为从丝网网孔4的另一个面侧朝向一个面侧进入至丝网网孔4。以下,将丝网网孔4的另一个面侧称为乳剂侧,将丝网网孔4的一个面侧称为网孔侧,将从丝网网孔4露出的丝网乳剂部5的厚度t2称为乳剂厚度。在本实施方式中,通过改变该乳剂厚度t2,来调整能够填充于丝网印版2的开口部3的粉体9的容积,控制在基板10上成膜的粉体膜11(图3)的成膜量。但是,上述粉体9的容积能够通过改变丝网网孔4的纱厚t1和丝网网孔4的开孔数中的至少一方来调整。丝网印版2配置成:开口部3的轴向(由箭头a所示的铅垂方向)成为重力作用的方向。在丝网印版2的网孔侧配置由聚氨酯海绵形成的刮入体15。刮入体15可以不是聚氨酯海绵,而由橡胶、刮板或刷毛等构成。在向丝网印版2的开口部3填充粉体9时,通过刮入体15在丝网网孔4上移动,将粉体9刮入丝网网孔4使其进入开口部3,从而能够在整个开口部3均匀地填充粉体9。堵塞开口部3的平滑的压板6(按压部件)配置于开口部3的下侧。然后,向丝网印版2的网孔侧供给粉体9。被供给到丝网印版2的网孔侧的粉体9,被在丝网印版2的丝网网孔4上移动的刮入体15刮入丝网网孔4,被平滑的压板6从下侧挤压而填充于开口部3。之后,从开口部3除去压板6。通过利用压板6堵塞开口部3,能够避免填充于开口部3的粉体9落下。另外,通过利用压板6堵塞开口部3,能够使填充于开口部3的粉体9的下侧的面平滑化,能够使粉体膜11更均匀地成膜。能够通过丝网印版2的开口部3的容积、粉体9的压入量(粉体密度)控制粉体9的填充量或者粉体膜11的成膜量。通过以将压板6压靠于丝网印版2的开口部3的下侧的状态向开口部3填充粉体9,能够唯一地确定填充粉体9的空间的容积。因此,能够以所期望的厚度形成粉体膜11,并且即使反复进行成膜也始终保持一定的成膜量。另外,通过在填充时将刮入体15压靠于丝网网孔4的压力一定,能够使填充于开口部3的粉体9的密度一定。因此,能够控制要成膜的粉体膜11的厚度。填充粉体9的多孔体并不限定于丝网印版2,例如能够使用筛子、冲孔金属、以及在金属板上形成有多个微细孔的金属印版。通过改变形成于丝网网孔4的丝网乳剂部5的图案或形成于金属板的孔的位置,能够将粉体膜11形成为任意的形状。通过使用多孔体,能够任意地设定粉体9的成膜量、粉体膜11的形状,能够形成膜厚精度良好的粉体膜11。在本实施方式所涉及的粉体膜形成方法中,首先,向丝网印版2的丝网网孔4上供给粉体9。丝网印版2能够使用不锈钢网孔、聚酯网孔或者尼龙网孔等。在本实施方式中,通过利用静电感应进行成膜,从而能够进行成膜精度更好的成膜。因此,优选使用适合于利用静电感应进行成膜的不锈钢网孔作为丝网印版2。另外,通过改变丝网印版2的开口部3的图案,能够将粉体膜11形成为任意的形状。在使用丝网印版2的情况下,在通常的丝网印刷时可以从使刮板扫描的网孔侧向开口部3填充粉体9,也可以从乳剂侧向开口部3填充粉体9。能够通过丝网印版2的开口部3的容积控制粉体膜11的成膜厚度等成膜量。例如,在使用丝网印版2时,能够通过丝网网孔4的线径、丝网网孔4的网孔数、以及乳剂厚度t2控制开口部3的容积,由此能够控制粉体膜11的成膜量。供给到丝网印版2的开口部3的粉体9的量只要为开口部3的容积以上的量即可。另外,从向丝网印版2的开口部3内均匀地填充粉体9的观点出发,优选粉体9被破碎成没有大的凝集粒的程度。接下来,将供给到丝网印版2的丝网网孔4上的粉体9填充至丝网印版2的开口部3。此处,重要的是将压板6压靠在开口部3的下侧。通过压靠压板6,能够将所填充的粉体9保持于丝网印版2。另外,成膜后的粉体膜11的表面状态依赖于压板6的开口部3侧的表面状态。因此,为了形成均匀的粉体膜11,优选压板6的厚度均匀且压板6的开口部3侧的表面的凹凸也尽量微小。另一方面,当有意在粉体膜11设置厚度分布时,通过对压板6的面方向的厚度设定分布,从而能够任意改变要成膜的粉体膜11的厚度分布。作为此处使用的压板6,能够使用不锈钢等金属、树脂等,但是,若考虑表面的平滑性、耐久性等,则优选使用金属。在将该压板6配置于开口部3的状态下,供给到丝网网孔4的粉体9被刮入体15填充于开口部3。刮入体15能够使用聚氨酯海绵这样的海绵、刮板、刷子等。以将供给到丝网网孔4的粉体9压入开口部3的方式,使刮入体15在开口部3上的丝网网孔4扫描,将粉体9填充于开口部3。此时,虽然也取决于开口部3的面积,但通过刮入体15的数次扫描完成粉体9向开口部3的填充,因此,能够在短时间内将粉体9填充于开口部3。另外,能够通过将粉体9压入开口部3时的刮入体15的压入压力以及扫描次数来控制粉体膜11的成膜量。接下来,对实施方式所涉及的成膜工序进行说明。(成膜工序)图3是示出粉体膜形成方法的成膜工序的剖视图。在形成粉体膜11时,在丝网印版2与基板10之间设置电位差。填充于开口部3的粉体9通过从开口部3向基板10上的被印刷物16移动,由此形成粉体膜11。此时,丝网印版2与直流电源8的负极连接。然后,填充于开口部3的粉体9带负电。另外,此时,基板10与直流电源8的正极连接。接下来,通过使用刮入体15从丝网网孔4的上表面对填充于开口部3的粉体9进行刮擦,使填充于开口部3的粉体9向基板10上移动。此时,粉体9在维持填充于开口部3的膜厚等的形状的同时,被基板10静电感应而附着于基板10上的被印刷物16的表面。就丝网印版2与基板10连接的直流电源8而言,可以在正极连接丝网印版2,在负极连接基板10。根据丝网印版2与基板10之间的距离以及电位差计算的静电感应所需要的电场强度根据所使用的粉体9而不同。因此,适当地设定电场强度对于使填充于开口部3的粉体9产生静电感应是重要的。(实施方式2)通过在填充时改变堵塞开口部3的压板6的面内的厚度,能够任意地改变要成膜的粉体膜11的厚度分布。填充于开口部3的粉体9的压板6a侧的面形成为转印有压板6的开口部3侧的面的状态的形状。因而,通常为了使粉体膜11的厚度分布均匀,优选压靠于开口部3的压板6的厚度分布均匀,且压板6的开口部3侧的表面的凹凸也尽量微小。另一方面,当想要在粉体膜11设定厚度分布时,通过使压靠于开口部3的压板6的面内厚度具有分布,也能够形成具有任意的厚度分布的表面形状的粉体膜11。图4的(a)是示出实施方式2所涉及的粉体膜形成方法的填充工序的剖视图,图4的(b)是实施方式2所涉及的压板6a的俯视图。针对与在实施方式1中所述的构成要素相同的构成要素标注相同的参照符号。因此,不再重复上述的构成要素的说明。例如,有时想要仅使粉体膜11的端部(周围)增大厚度。在假设粉体膜11的形状是正方形的情况下,仅在与粉体膜11的端部对应的部位,在压板6a预先设置槽。例如,如图4的(a)、(b)所示,在压板6a沿着开口部3的外缘形成“ロ”字形的槽17。于是,在填充粉体时,在与槽17对应的部位,粉体的填充量/膜厚增大,因此所形成的粉体膜11也能够增大与槽17对应的部位的膜厚。通过改变槽17的形状,能够形成具有任意的膜厚分布的粉体膜11。另外,在图4中,示出了槽17的深度一定的例子,但是本发明并不限定于此。槽17的深度可以不是呈台阶状地变化,而是连续地变化。(实施方式3)在实施方式1以及2中,示出了从丝网印版2的丝网网孔4侧向开口部3填充粉体9,从开口部3的丝网乳剂部5侧使粉体9向基板10移动而成膜的例子。但是,本发明并不限定于此。也可以从丝网印版2的丝网乳剂部5侧向开口部3填充粉体9,从开口部3的丝网网孔4侧使粉体9向基板移动10而成膜。在这种情况下,首先,从丝网乳剂部5侧将粉体9填充于开口部3。然后,将丝网印版2翻转配置成图2所示的状态。然后,使刮入体15在丝网网孔4侧扫描,使粉体9向基板10移动。存在通过该方法使粉体膜11的成膜精度提高的情况。(实施例)当基于图1~图3对本发明的一实施例进行说明时,如下所述。首先,作为要成膜的粉体9,准备了粒径(d50)为4μm的大致球形的干燥粉体。然后,作为填充粉体9的多孔体,在实施例1~2、实施例4~6中准备了丝网印刷用的丝网印版2。丝网网孔4使用不锈钢网孔,网孔的线径为30μm、纱厚t1为60μm、网孔数为300/inch、开孔为55μm、开口部3的形状为50mm×50mm的实心图案。在本实施例中,为了改变开口部3的容积,如[表1]所示那样改变了乳剂厚度。[表1]示出实施例1~6、以及比较例1的试验条件以及评价结果。表1另外,在实施例5中,准备了通过电铸加工制作出的金属掩模。开口部的形状为与丝网印版2同样的50mm×50mm的实心图案,在开口部形成与网孔数300/inch相当的孔,金属部的厚度为60μm。接下来,准备了从丝网印版2的开口部3的下侧压靠的压板6。将尺寸70mm×70mm、厚度300μm、平面度50μm以下的不锈钢板用作压板6。尤其是,在[表1]所示的实施例6中,尺寸40mm×40mm的区域与压板6同样,厚度为300μm、平面度为50μm以下,在40mm~70mm的范围内,从内侧朝向外侧设置斜度为6.7μm/mm的倾斜。之后,作为刮入体15,准备了聚氨酯的海绵、氨基甲酸乙脂的刮板。然后,按照[表1]所记载的各试验条件形成粉体膜11。在成膜时,使用与压板6相同的板作为基板10。通过使填充于开口部3的粉体9移动至该基板10而形成粉体膜11,从而实施成膜。在实施例1~4以及6中,实施3次成膜,形成了3层粉体膜11。在实施例5中,实施了5次成膜,形成了5层粉体膜11。此处,为了计算出单层的成膜量,测定了实施成膜之前的被印刷物16的不锈钢板的重量、与实施了单层的成膜之后的被印刷物16的不锈钢板的重量。然后,从所形成的粉体膜11的横向向粉体膜11照射光,目视确认有无粉体膜11的面内的厚度分布。接下来,对成膜的粉体膜11进行了加压成形。加压力为10ton/cm2,加压时间为30秒。然后,为了确认加压后的粉体膜11的面内的厚度偏差,使用直径10mm的手动冲头对粉体膜11的四角以及中央部进行冲裁,对冲裁后的四角以及中央部的重量进行测定。求出该重量测定结果的平均值,以%计算出以该平均值为基准的偏差的范围。将计算出的偏差表示于[表1]。(比较例1)在比较例1中,使用与实施例1同样的粉体9、丝网印版2以及刮入体15,以1,0kv/mm的电场强度进行不实施填充工序的现有的静电成膜。现有的静电成膜与实施例1~6不同,不是形成多层粉体膜的方法,因此没有实施单层的成膜量测定。成膜后的粉体膜的加压成形、使用手动冲头的冲裁以及重量测定与实施例1~6同样地实施。在比较例1中,成膜工序未分割成向多孔体的开口部填充粉体的工序、以及使填充于多孔体的开口部的粉体从开口部向基板移动的工序。因此,在基板上形成的粉体膜的面内厚度的精度不足,通过使用手动冲头的冲裁测量出的偏差的值也为30.7%这样大的值。另一方面,在实施例1中,成膜工序分割为向多孔体(丝网印版2)的开口部3填充粉体9的工序、以及使填充于丝网印版2的开口部3的粉体9从开口部3向基板移动10而形成粉体膜11的工序。因此,上述偏差的值降低为上述比较例1的约1/3的9.4%。在实施例2中,在使填充于丝网印版2的开口部3的粉体9从开口部3向基板移动10时,在丝网印版2与基板10之间设置了电场强度1kv/mm的电位差。因此,上述偏差的值进一步降低为6.7%。在实施例3中,在多孔体使用金属掩模来形成粉体膜11。使用金属掩模的结果是,多孔体的孔的容积相比丝网印版2的开口部3的容积减少,因此,单层成膜量比实施例1以及2少。但是,偏差的值与实施例1以及2同样成为10%以下的良好的值。结果,确认了作为多孔体能够使用丝网印版2以外的金属掩模。在实施例4中,作为刮入体15,代替海绵而使用了刮板。偏差的值成为10%以下的良好的值。结果,确认了能够使用海绵以外的多种刮入体15。在实施例5中,将丝网印版2的乳剂厚度从50μm变为10μm,使作为多孔体的丝网印版2的开口部3的容积减少。结果,偏差的值成为10%以下的良好的值。单层成膜量相比实施例4减少。结果,确认了能够通过丝网印版2的开口部3的容积控制成膜量。在实施例6中,在压靠于丝网印版2的开口部3的压板6设置了厚度分布。因此,确认在形成的粉体膜11产生了面内厚度分布,以及偏差的值增加。结果,确认了通过在压板6设置厚度分布,能够任意控制形成的粉体膜11的面内厚度分布。另外,示出了使用具有丝网网孔4(多孔体)和丝网乳剂部5(被覆部)的丝网印版2的例子,但是本发明并不限定于此。如果仅凭多孔体便能够获得所期望的膜厚,那么不需要被覆部。例如,如果针对金属板仅在成膜部位实施了微细的多孔加工,那么不需要丝网印版的乳剂部这样的部分。但是,在想要获得的膜厚大的情况下,优选使用具有丝网网孔4(多孔体)和丝网乳剂部5(被覆部)的丝网印版2。在(
背景技术:
)一栏中上述的专利文献2的现有技术是利用刮入体将供给到丝网印版上的粉体刮入丝网印版的方式,但并非供给到丝网印版上的粉体的全部都在被印刷物上成膜。即,在供给到丝网印版上的粉体之中,产生未在被印刷物上成膜而残留于丝网印版上的粉体、以及被刮入体保持的粉体。因此,存在难以控制通过静电感应从丝网印版的网孔(孔)向被印刷物附着粉体而形成的粉体膜的膜厚。如以下的实施方式4以及5所示那样解决上述问题。(实施方式4)(粉体成膜装置1的构成)图5是示出实施方式4所涉及的粉体膜形成方法的填充工序的剖视图。粉体成膜装置1具备设于丝网框12的丝网印版2(粉体填充部件)。丝网印版2具有丝网网孔4(多孔体)、以及形成于丝网网孔4的一个面的丝网乳剂部5(被覆部)。丝网印版2以丝网乳剂部5位于丝网网孔4的下侧的方式配置。在丝网乳剂部5形成开口部3。压板6(按压部件)以堵塞开口部3的方式配置于丝网乳剂部5的下侧。粉体9供给到丝网网孔4上。防止供给到丝网网孔4上的粉体9飞散的飞散防止板13设置成将粉体9以及开口部3覆盖。粉体9例如是jis试验用粉体1(17种、重质碳酸钙)。但是,所使用的粉体并不限定于此。在粉体成膜装置1设置用于使丝网印版2振动的励振部件7。丝网印版2的丝网乳剂部5的开口部3的形状是正方形。但是,通过改变开口部3的形状能够形成任意形状的粉体膜。在丝网网孔4中,网孔数300/inch、线径30μm、开口尺寸55μm。丝网网孔4的材质可以是通常的聚酯、尼龙、不锈钢、聚乙烯等。但是,网孔数、线径、开口尺寸、材质应当根据所使用的粉体9选择。丝网印版2只要是具有微细孔且能够在该微细孔的内部保持粉体9的多孔体即可,例如能够使用冲孔金属、筛子、实施了微细加工的金属板等。(粉体膜形成方法)以下,将实施方式4所涉及的粉体膜形成方法分为流动化处理工序、粉体填充工序(填充工序)、以及成膜工序这3个工序进行说明。(流动化处理工序)在所使用的粉体9的流动性不好的情况下,首先,进行提高粉体9的流动性的流动化处理。但是,如果粉体9的流动性良好,那么无需进行本流动化处理工序。作为提高粉体9的流动性的方法,考虑粉体9的粒径的增大化(颗粒化、造粒)、粒径分布的均匀化、粒子的正球形化、以及除电等。本流动化处理工序的流动化处理可以是上述的任意一种方法,另外,可以是上述方法的组合。在本实施方式中,以干式进行流动化处理。因此,通过依次经过原料压缩、破碎、筛分这样的工序,进行粒子的造粒、粒径分布的均匀化、以及稍微的正球形化。(粉体填充工序(填充工序))首先,向丝网印版2的丝网网孔4上供给粉体9。然后,以覆盖粉体9以及开口部3的方式将飞散防止板13配置在丝网网孔4上。接着,通过励振部件7对丝网印版2施励振动。于是,供给到丝网网孔4上的粉体9由于施加于丝网印版2的振动而通过丝网网孔4填充于开口部3。优选在以覆盖开口部3的方式将压板6配置于丝网乳剂部5的下侧的状态下施加对丝网印版2施加的振动。在使用丝网印版2的情况下,如图5所示,优选配置成丝网网孔4在丝网乳剂部5上,对丝网印版2施励振动。由此,填充于开口部3的粉体9的下表面被压板6限制而成为平坦形状。然后,填充于开口部3的粉体9上表面被丝网网孔4限制而成为平坦形状。因此,通过丝网印版2的内部的开口部3的容积能够精密地控制向开口部3的粉体9的填充量。施加于丝网印版2的适当的振动虽然因粉体9而不同,但是能够使用一般的振动筛机作为励振部件7。但是,如果粉体9的流动性不好,那么与在垂直于丝网印版2的表面的方向励振的“振动筛”相比,使用沿着丝网印版2的表面的方向励振的“面内筛”的填充的效率较好。另外,优选根据粉体9组合高频率振动与低频率振动来进行励振。另外,若重叠使用图5的粉体成膜装置1,一次性对各个丝网印版2施励振动,则能够通过1次粉体填充工序同时获得填充有粉体9的多个丝网印版2。由此,能够缩短每一张丝网印版2的填充时间。在图5所示的实施方式4中,使用一般的面内筛机作为励振部件7,通过在使丝网印版2相对于水平方向倾斜几度左右的状态下实施面内筛,用30秒左右完成了粉体9向丝网印版2的开口部3的填充。若重叠10台粉体成膜装置1一次性施励振动,则认为每一张的丝网印版2的填充时间为3秒左右。粉体膜11的成膜厚度以及粉体重量由粉体9向丝网印版2的开口部3的填充精度决定。因此,将粉体9的规格、丝网印版2的规格、以及振动条件等最优化,供给到丝网网孔4上的粉体9应当全部被充足地填充于丝网印版2的开口部3。另外,在无论如何粉体9的一部分都成为粘块等而无法完全填充于丝网印版2的开口部3的情况下,优选在转移到接下来的成膜工序之前,预先去除剩余粉体。此处,所谓粘块的意思是指:粉体9在丝网印版2上滚动而形成的凝结块。在该凝结块的直径比丝网网孔4的开口大的情况下,凝结块无法经过丝网网孔4,因此,凝结块成为剩余粉体(即使数次振动也无法填充的成为阻碍的粉体)。(成膜工序)图6是示出粉体膜形成方法的成膜工序的剖视图。通过利用励振部件7对在开口部3填充有粉体9的丝网印版2施励振动,从而填充于开口部3的粉体9落下,在基板10上形成粉体膜11。在成膜工序中,将丝网印版2配置成丝网乳剂部5位于丝网网孔4的下侧,以使得填充于丝网印版2的开口部3的粉体9易于向配置于开口部3的下侧的基板10落下。在成膜工序中,不需要在粉体填充工序中使用的压板6,但是可以根据需要而使用飞散防止板13。但是,优选找出填充于丝网印版2的开口部3的粉体9不超过丝网网孔4而向上侧飞散的振动条件,以使得可以不使用飞散防止板13。在成膜工序中施加于丝网印版2的振动可以是与在粉体填充工序中施加于丝网印版2的振动相比励振力小的振动。在成膜工序中施加的振动因粉体9的规格、丝网印版2的规格而不同,但是,需要施加超声波振动、低频率振动、或1次碰撞振动。仅通过利用励振部件7对在开口部3填充有粉体9的丝网印版2施励振动,粉体9就落到配置于丝网印版2的下侧的基板10上,能够形成粉体膜11。但是,为了使成膜精度提高,优选设置在丝网印版2与基板10之间产生电位差的直流电源8,通过在丝网印版2与基板10之间产生的静电力将粉体9吸引至基板10。在实施方式4中,将丝网印版2与基板10之间的距离设为10mm左右、电位差设为8kv,但是,本发明并不限定于此。这是因为根据粉体9的规格、丝网印版2的规格改变适当的条件。在使用了实施方式4所涉及的粉体9、丝网印版2的情况下,在丝网印版2与基板10之间产生了上述电位差的状态下,仅通过对丝网印版2施加一次轻微的碰撞振动,完成了粉体膜11向基板10的成膜。由此,针对每张丝网印版2在3秒以内完成成膜工序。(实施方式5)(粉体填充工序)图7是示出实施方式5所涉及的粉体膜形成方法的填充工序的剖视图。针对与在图5中说明的构成要素相同的构成要素标注相同的参照符号,不再重复这些构成要素的详细说明。与在图5中说明的粉体膜形成方法的填充工序的不同点在于:使图5所示的丝网印版2上下翻转,将丝网印版2配置成丝网网孔4位于丝网乳剂部5的下侧。向丝网乳剂部5上供给粉体9,若利用励振部件7对丝网印版2励振,则粉体9一边振动一边填充于开口部3。优选在将压板6设置在丝网网孔4的下侧的状态下对丝网印版2励振,但是,在丝网网孔4能够可靠地保持粉体9的情况下,可以不设置压板6。在粉体9由于被施励振动而剧烈飞散的情况下,通过以覆盖粉体9的方式设置飞散防止板13而能够抑制粉体9的飞散。若如图5所示那样将丝网网孔4配置于丝网乳剂部5上侧,则粉体9必须经过丝网网孔4,因此,有时无法由粉体9良好地填充于开口部3。在这种情况下,如图7所示,如果翻转丝网印版2后填充粉体9,那么能够将几乎所有种类的粉体9良好地填充于开口部3。但是,在使该丝网印版2翻转的情况下,在将粉体9填充于开口部3之后,必须将填充于开口部3的粉体9刮平、去除未填充于开口部3而剩余的剩余粉,使填充于开口部3的粉体9的上表面尽量变得平坦。(比较例)图8是示出比较例所涉及的粉体膜形成方法的剖视图。比较例所涉及的粉体膜形成方法是一般的静电丝网印刷方法。首先,通过利用刷入体21向与直流电源8的负极、或地极(接地)连接的丝网22刮入粉体9,从而使粉体9与丝网22接触而带电或者接地。这样,带电或者接地的粉体9被静电感应而附着于与直流电源8的正极连接的基板10上的被印刷物16,形成粉体膜11。也可以使丝网22与直流电源8的正极连接,使基板10与直流电源8的正极连接。在上述的比较例中,与丝网22接触的粉体9的粒子被带电或者接地而强力地附着于被印刷物16。但是,未与丝网22接触的粒子、以及在丝网22上结合而成块的粒子组没有良好地被带电或者接地。该没有带电或者接地的粉体9的粒子由于与刷入体21/丝网22摩擦而摩擦带电,有时导致粉体9的电荷变得不均匀。因此,存在以下问题,即:上述没有良好地带电的粒子以及粒子组成为使粉体膜11的成膜精度变差的原因。在实施方式4以及5中,使填充于丝网印版2的开口部3的粉体9振动并向基板10移动,从而在基板10形成粉体膜。因此,粉体9的粒子并不是一定要带电。另外,带电或者接地的丝网网孔4内的粉体9的粒子从丝网网孔4直接或者经由带电或接地的粉体9的其他粒子带电或接地。因此,不会发生上述没有良好地带电的粒子以及粒子组导致粉体膜11的成膜精度恶化的情况。另外,这样没有良好地带电的粒子以及粒子组没有充分发挥由于静电感应而被向被印刷物16吸引的吸引力。因此,存在以下问题,即:丝网22的网孔(孔)被上述粒子以及粒子组堵塞而引起粉体膜11的成膜不良。在实施方式4以及5中,通过使填充于丝网印版2的开口部3的粉体9振动并向基板10移动,从而在基板10形成粉体膜。因此,粉体9的粒子并不是一定要带电。因此,不会由于丝网22的网孔(孔)被上述粒子以及粒子组堵塞而导致粉体膜11的成膜不良。另外,在上述的比较例中,理想情况是在使全部粉体粒子与丝网22的网孔接触而良好地带电的状态下,落到丝网22下的被印刷物16。但是,若向丝网22的网孔(孔)一次供给大量的粉体粒子,则难以使全部粉体粒子与丝网22的网孔接触。因此,无法一次将大量的粉体粒子供给到丝网22的网孔(孔)。因此,还存在粉体膜11的成膜所需的时间变长的问题。例如,在上述的比较例中,为了形成100×100mm、膜厚100μm的粉体膜需要约10分钟(约600秒)的时间。在实施方式4以及5中,通过使填充于丝网印版2的开口部3的粉体9振动而向基板10移动,从而在基板10形成粉体膜,因此,无需使全部粉体粒子与丝网网孔接触而良好地带电。因此,能够缩短粉体膜11的成膜时间。使用上述比较例和实施方式4,将以100×100mm、膜厚100μm为目标进行成膜的结果表示于(表2)。表2实施例结果根据实施方式4,与比较例相比,无需担心因刷入体21的磨损等导致污染的混入,成膜时间短,且容易控制成膜厚度、粉体重量,因此,能够在短时间内以τ量进行稳定的粉体膜的成膜。另外,例示了具有丝网网孔4(多孔体)和丝网乳剂部5(被覆部)的丝网印版2的例子,但是本发明并不限定于此。如果仅凭多孔体便能够获得所期望的膜厚,那么不需要被覆部。例如,如果使用针对金属板仅对成膜部位实施了微细的多孔加工的印版,那么不需要存在丝网印版的乳剂部那样的部分。但是,在想要得到的膜厚大的情况下,优选使用具有丝网网孔4(多孔体)和丝网乳剂部5(被覆部)的丝网印版2。在(
背景技术:
)一栏中,在上述那样的专利文献2的现有技术中,通过海绵等的刮入体在供给到丝网印版上的粉体上移动,从而,粉体经过丝网印版的丝网网孔以及开口部涂布于基板上而形成粉体膜。因此,由于丝网印版上的粉体的散布状况、以及丝网印版上的刮入体的移动轨迹而产生粉体膜的成膜偏差。因此,在寻求成膜的均匀性的
技术领域:
中,存在无法以足够的膜厚精度形成粉体膜的问题。另外,在上述的专利文献2的现有技术中,理想的是:在使全部粉体粒子与丝网印版的网孔接触而良好地带电的状态下落在丝网印版下的被印刷物。但是,若向丝网印版的网孔(孔)一次供给大量的粉体粒子,则难以使全部粉体粒子与丝网印版的网孔接触。因此,无法将大量的粉体粒子一次供给到丝网印版的网孔(孔)。因此,还存在粉体膜的成膜所需的时间变长的问题。按照以下的实施方式6~8那样解决上述问题。(实施方式6)根据本实施方式所涉及的粉体膜形成方法,改进了现有的静电丝网印刷方法,能够在短时间内形成膜厚更均匀的粉体的薄膜。本实施方式包括:供给工序,向具有多孔体的丝网印版的下侧供给被粉碎的粉体;填充工序,使用静电力将供给到上述丝网印版的下侧的粉体填充于上述丝网印版的开口部;以及成膜工序,使用静电力使粉体从填充有上述粉体的丝网印版的开口部附着于基板而形成粉体膜。尤其是,在填充工序中,为了向上述丝网印版的开口部填充粉体,也使用静电力的原理。上述多孔体能够使用丝网网孔、筛子、冲孔金属、其他在金属板形成有多个微细的孔的部件。通过改变上述的部件的形状、形成孔的部位,能够形成任意的形状的粉体膜。以下,按照各工序对实施方式6所涉及的粉体膜形成方法进行说明。(供给工序)图9是示出实施方式6所涉及的粉体膜形成方法的供给工序的剖视图。首先,粉碎粉体9并散布到供给容器14中。粉体9被粉碎至粉体9彼此不凝集的程度即可。例如,如图9所示,有利用配置于供给容器14的上侧的筛子17将粉体9粉碎而供给到供给容器14的方法。一边从筛子17筛落粉体9一边向以底面由金属等具有导电性的原材料形成的供给容器14散布粉体9。此时,粉体9无需那么均匀地散布至供给容器14。将比后述的填充工序中的图11以及图12所示的丝网印版2的开口部3的容积多的量的粉体9,以不露出供给容器14的底面的程度散布至供给容器14的整个底面即可。因此,作为粉碎粉体9并将粉体9供给到供给容器14的方法,并不限定于筛子17,能够使用基于超声波筛子的供给、基于喷涂的供给、基于涂布机送料器的供给、或者它们的组合等通常能想到的供给方法。另外,可以使用气流、离心力粉碎粉体9。另外,供给容器14可以由平板构成。作为粉体9,能够使用粒径d50为5μm的干燥粉体。但是,本实施方式所涉及的粉体膜形成方法中使用的粉体9并不限定于此。筛子17能够使用jisz-8801的内径φ75、网眼500μm的筛子。但是,筛子17并不限定于此。另外,粉碎方法也并不限定于利用筛子17的方法。需要根据粉体9选定适当的粉碎方法。图10是示出在供给工序中散布粉体9的供给容器14的照片。作为供给容器14,使用边长为70mm的正方形状的sus(不锈钢)制的平板。用筛子17一边粉碎一边将粉体9散布到该sus制的平板上。被粉碎的粉体9无需那么均匀地散布。只要散布sus制平板的底面不露出的程度的量(0.50~0.55克(g))的粉体9即可。(填充工序)图11是示出粉体膜形成方法的填充工序的剖视图。粉体成膜装置1具备形成有填充粉体9的开口部3的丝网印版2(粉体填充部件)。图12是示出在填充工序中使用的丝网印版2的构成的剖视图。丝网印版2包括丝网网孔4(多孔体)和形成于丝网网孔4的一个面的丝网乳剂部5(被覆部)。开口部3形成于该丝网乳剂部5。作为丝网印版2,能够使用丝网印刷用的一般的不锈钢网孔。丝网印版2的开口部3的形状能够为边长50mm的正方形状。但是,通过改变开口部3的形状,能够形成任意形状的粉体膜11。在本实施方式中,使用了具有网孔数300/inch、线径30μm(纱厚t1=60μm)、开孔55μm的丝网网孔4的丝网印版2。如图12所示,在本实施方式中使用的丝网印版2形成为,丝网乳剂部5从丝网网孔4的一个面朝向另一个面而从另一个面露出。以下,将丝网网孔4的另一个面侧称为乳剂侧,将丝网网孔4的一个面侧称为网孔侧,将从丝网网孔4露出的丝网乳剂部5的厚度t2称为乳剂厚度。在本实施方式中,通过改变该乳剂厚度t2,调整能够填充于丝网印版2的开口部3的粉体9的容积,控制在基板10成膜的粉体膜11(图15)的成膜量。但是,也能够通过改变丝网网孔4的纱厚t1与丝网网孔4的开口中的至少一方,来调整上述粉体9的容积。然后,将在供给工序中散布有粉体9的供给容器14配置于丝网印版2下。接下来,将堵塞开口部3的上表面侧的压板6(按压部件)载置在丝网印版2上。然后,将负极与丝网印版2连接的直流电源8(电源)的正极与供给容器14连接。于是,供给容器14上的粉体9因直流电源8的正极而带正电。然后,带正电的粉体9通过静电感应而被朝向因直流电源8的负极而带负电的丝网印版2吸引,填充于丝网印版2的开口部3。当然,也可以使直流电源8的正负翻转,在丝网印版2连接直流电源8的正极而在供给容器14连接负极。为了通过静电感应将粉体9从供给容器14吸引至丝网印版2所需要的供给容器14与丝网印版2之间的电场强度(电位差、距离)根据粉体9的种类而不同。因此,上述电场强度(电位差、距离)应当按照粉体9的种类设定适当的值。图13的(a)是从乳剂侧观察经上述填充工序填充后的丝网印版2的照片,图13的(b)是从网孔侧观察经上述填充工序填充后的丝网印版2的照片。在本实施方式中,如图11所示,在放置有sus板制的压板6的丝网印版2的下方配置供给粉体9的sus板制的供给容器14。在本实施方式中,丝网印版2配置成以网孔侧为下侧而以乳剂侧为上侧。设定为丝网印版2的乳剂厚度t2=50μm。然后,将压板6载置于丝网印版2的乳剂侧。丝网印版2与供给有粉体9的sus板制的供给容器14之间的距离为7mm。丝网印版2接地。对sus板制的供给容器14施加了8kv的电压。丝网印版2与sus板制的供给容器14之间的电场强度成为1.14kv/mm。于是,如图11以及图13所示,粉体9通过基于上述电场强度的静电力而从sus板制的供给容器14被填充于形成于丝网印版2的丝网乳剂部5的开口部3。另外,在填充工序中,使带电的粉体9如后述的实施方式7所示那样通过静电喷涂喷附于施加有电压的开口部3,将粉体9填充于开口部3。另外,示出了从开口部3的下表面侧将粉体9填充于开口部3的例子,但是本发明并不限定于此。可以从开口部3上表面侧将粉体9填充于开口部3。(成膜工序)图14是示出粉体膜形成方法的成膜工序中的即将刮入之前的状态的剖视图。图15是示出粉体9基于上述成膜工序中的静电感应而向被印刷物16附着的状态的剖视图。如图14所示,在填充工序中向开口部3填充了粉体9的丝网印版2与直流电源8的负极连接。于是,填充于开口部3的粉体9由于接触而带负电。然后,将搭载有被印刷物16的基板10与直流电源8的正极连接。接下来,通过在丝网印版2移动的刮入体15将填充于丝网印版2的开口部3的粉体9从丝网印版2的开口部3刮落。于是,如图15所示,粉体9维持填充于开口部3时的膜厚而直接通过静电感应从开口部3移动并附着于被印刷物16,形成粉体膜11。当然可以与上述的填充工序同样地使直流电源8的正负翻转,在丝网印版2连接直流电源8的正极而在供给容器14连接负极。被印刷物16与丝网印版2之间的电场强度(电位差)越大,粉体9越密地附着于被印刷物16。因此,上述电场强度越大,则越能够增大粉体膜11的密度。但是,与前述的填充工序同样,为了通过静电感应将粉体9从丝网印版2吸引至被印刷物16所需的被印刷物16与丝网印版2之间的电场强度(电位差、距离),根据粉体9的带电性等而不同。因此,上述电场强度(电位差、距离)应当根据粉体9的带电性等设定适当的值。能够通过完全同样的方法实施填充工序中的电压施加和成膜工序中的电压施加。均能够通过使丝网印版2接地(gnd(接地极))或者施加负电压而对基板10或者供给容器14施加正电压来实施。但是,所施加的电压的值、以及丝网印版2与基板10或者供给容器14之间的距离在填充工序和成膜工序中不同。当然,可以使直流电源8的正负翻转,在丝网印版2连接直流电源8的正极而在供给容器14连接负极。通过在丝网印版2施加电压,从而填充于丝网印版2的开口部3而与开口部3接触的粉体9带电。因此,若通过直流电源8使丝网印版2与基板10之间产生电位差,则同时出现粉体9的带电现象和在丝网印版2与基板10之间的静电场的产生现象。本来,仅通过在丝网印版2与基板10之间形成静电场,便应当能够通过静电力将填充于开口部3的粉体9吸引至基板10。但是,由于粉体9向丝网印版2的附着力比作用于粉体9的静电力大,因此,能够想到仅通过静电力未必能使填充于开口部3的粉体9良好地向基板10移动。因此,通过利用在丝网印版2移动的刮入体15从丝网印版2的开口部3刮落粉体9,或通过对丝网印版2施励振动,能够使粉体9向基板10良好地移动。不使用静电力,而仅通过使填充于开口部3的粉体9落下也能够在基板10形成粉体膜11。但是,通过使用静电力,能够高密度地形成且成膜结实的粉体膜11。另外,通过使用静电力,在使填充于开口部3的粉体9落下时,粉体9不扩散而直线地向基板10落下。因此,能够形成膜厚均匀的粉体膜11。图16是示出在上述成膜工序中成膜于被印刷物16的粉体膜11的照片。在开口部3填充有粉体9的丝网印版2的下方配置有由边长70mm的正方形的sus板构成的被印刷物16。在将填充工序中的丝网印版2翻转而使乳剂侧位于网孔侧的下方来配置丝网印版2。丝网印版2与被印刷物16的sus板之间的距离被设定为6mm。丝网印版2接地(gnd(接地极))。在sus板制的被印刷物16施加了8kv的电压。丝网印版2与sus板制的被印刷物16之间的电场强度为1.33kv/mm。在该状态下,利用由海绵构成的刮入体15在丝网印版2的丝网网孔4上刮擦多次,使填充于开口部3的粉体9向被印刷物16的sus板移动,如图16所示那样在被印刷物16形成粉体膜11。另外,刮入体15可以不是海绵而是由橡胶、刮板或刷毛等构成。将以与上述同样的的条件进行8次制膜时的粉体9的供给量与粉体膜11的成膜量之间的关系表示于下述(表3)。表3试验no.1345678avestdstd(%)供给量0.515g0.512g0.507g0.503g0.525g0.531g0.529g0.5174g0.0102g2.0%成膜量0.128g0.120g0.124g0.123g0.125g0.132g0.132g0.1263g0.0042g3.4%(效果)以上是本实施方式中的一系列的工序。在本实施方式中,形成于丝网印版2的开口部3的容积越大,能够使粉体9向开口部3的填充量、或者基于填充有开口部3的粉体9的粉体膜11的成膜量增大。例如,能够通过丝网印版2的丝网乳剂部5的厚度、丝网网孔4的开口的大小控制上述填充量或者成膜量。另外,在本实施方式中,能够在形成于被印刷物16上的粉体膜11上再重叠形成粉体膜。因此,通过以任意次数形成粉体膜,还能够控制粉体膜的成膜量。进而,还能够在形成于被印刷物16上的粉体膜11上形成不同种类的粉体膜。因此,能够形成层积有多层种类不同的粉体膜的薄膜。(实施方式7)图17是示出实施方式7所涉及的粉体膜形成方法的填充工序的剖视图。在实施方式6中,将散布有粉体9的供给容器14配置于丝网印版2的开口部3的下侧,通过在丝网印版2与供给容器14之间产生电位差而使散布于供给容器14的粉体9带电,使所述带电后的粉体9填充于开口部3。但是,本发明并不限定于此。可以通过静电喷涂器17将带电的粉体9喷附于开口部3,将所述带电后的粉体9填充于开口部3。可以向开口部3施加电压。与丝网印版2的开口部3对置地配置静电喷涂器17。在直流电源8的正极连接静电喷涂器17。在直流电源8的负极连接丝网印版2。粉体9和空气被供给到静电喷涂器17。供给到静电喷涂器17的粉体9被带正电,通过空气从静电喷涂器17朝向带负电的丝网印版2的开口部3喷射。然后,粉体9被填充于开口部3。另外,可以将静电喷涂器17与直流电源8的负极连接,将丝网印版2与正极连接。静电喷涂器17可以从丝网印版2的开口部3的下侧填充粉体9,也可以从开口部3上侧填充粉体9。在图17中,示出从开口部3的下侧填充粉体9的例子。在图17中,丝网印版2与静电喷涂器17通过直流电源8连接,在填充工序时在丝网印版2与静电喷涂器17之间产生电位差。但是,本发明并不限定于此。在使用了静电喷涂器17的填充工序中,只要将带电的粉体9物理地喷附至开口部3即可,并非必须在丝网印版2与静电喷涂器17之间产生电位差。(实施方式8)图18是示出实施方式8所涉及的粉体膜形成方法中的乳剂厚度与涂布量之间的关系的图表。在实施方式8中,用与实施方式6同样的方法,除了使用乳剂厚度t2=50μm的丝网印版2之外,还使用乳剂厚度t2=10μm、30μm的丝网印版2,比较了以这3个条件形成粉体膜11时的成膜量的不同。横轴表示丝网印版2的乳剂厚度t2,纵轴表示粉体膜11的成膜量(涂布量)。图18所示的实心圆表示以空心圆所示的各乳剂厚度时的各成膜量的平均值。通过该结果可知,随着丝网印版2的乳剂厚度t2(开口部3的容积)增大,粉体膜11的成膜量(涂布量)增多。(效果)根据实施方式8,通过调整丝网印版2的乳剂厚度t2,能够控制粉体膜11的成膜量(涂布量)。(比较例)图19是示出比较例所涉及的粉体膜形成方法的剖视图。比较例所涉及的粉体膜形成方法是一般的静电丝网印刷方法。首先,通过用刮入体21向与直流电源8的负极连接的丝网22刮入粉体9,能够使粉体9与丝网22接触而带电。这样带电的粉体9通过静电感应而附着于与直流电源8的正极连接的基板10上的被印刷物16,形成粉体膜11。当然,可以在直流电源8的正极连接丝网22,在直流电源8的负极连接基板10。但是,由于丝网22上的粉体9的散布状况、将粉体9刮入丝网22的刮入体21在丝网22上的移动方法,在丝网22上的特定的部位产生粉体9的滞留。并且,越是该粉体9的滞留量多的部位,向丝网22的下侧落下的粉体9的量变得越多。因而,存在形成于被印刷物16的粉体膜11的膜厚产生偏差的问题。在实施方式6~8中,填充于丝网印版2的开口部3的粉体9的平滑状态反映于成膜于基板10的粉体膜11。因此,能够不受粉体9的散布状况、刮入体21的移动方法影响而形成均匀的薄膜。另外,在比较例中,由于不能一次向丝网22的开口部3供给大量的粉体9,因此,存在成膜时间长时间化的问题。并且,伴随该成膜时间的长时间化而刮入体21被磨损,存在基于刮入体21的磨损而导致的污染混入到粉体膜11中的问题。在实施方式6~8中,刮入体15刮入的对象是填充于丝网印版2的开口部3的粉体9,因此,仅通过用刮入体15在丝网印版2多次刮擦,便能够使填充于开口部3的粉体9向基板10落下。因此,与比较例相比,能够大幅缩短成膜时间,而且能够降低基于刮入体21的磨损而导致的污染量。在实施方式6~8所涉及的填充工序中,通过静电力以非接触方式将粉体9吸引并填充至丝网印版2的开口部3。因此,基于刮入体21的磨损而导致的污染不会混入到向开口部3填充的粉体9中。另外,粉体9基于静电力向开口部3的填充所需的时间短至数秒左右。因此,即便分成填充工序和成膜工序,成膜时间的整体也不会变长。这样,在实施方式6~8中,并不是如比较例那样使散布在丝网22上的粉体9经过丝网22而向基板移动10上,而是在用平滑的压板6堵塞丝网印版2的开口部3的一个面侧的状态下,使用静电力使粉体9从另一个面侧吸引至丝网印版2而填充于开口部3。然后,通过从开口部3拆去压板6,利用静电力和刮入体15使填充于开口部3的粉体9移动至被印刷物16上,形成膜厚均匀的粉体膜11。尤其是,为了将粉体9填充于丝网印版2的开口部3而使用静电力。表4使用粉体膜面内的重量偏差,对通过比较例所涉及的粉体膜形成方法形成的粉体膜和通过实施方式7所涉及的粉体膜形成方法形成的粉体膜的成膜精度进行了比较。通过用直径10mm的冲孔冲头对以10ton/cm2的压力加压成型的粉体膜的四角和中央的5处部位进行冲裁,测定被冲裁下的5处部位的粉体膜的重量,从而求出粉体膜面内的重量偏差。为了形成实施方式7所涉及的粉体膜而使用的丝网印版2的乳剂厚度t2为10μm。为了对粉体膜加压成型,粉体膜需要一定程度的厚度。因此,实施方式7所涉及的粉体膜使用层积了3层的粉体膜。在(表4)中示出测定结果。通过实施方式7可知,粉体膜面内的重量偏差从22.15%大幅度改善为2,53%。针对实施方式6和比较例(现有法)对通过静电填充方式成膜时的各工序所需的时间进行了计测。各工序的计测时间不包括粉体9的重量的测定、以及供给容器14的配置之类的前准备所需的时间。在供给工序中,计测出从利用筛子17开始散布到结束散布为止的时间,在填充工序中计测出从开始施加电压到填充结束为止的时间。在成膜工序中,计测出从开始施加电压到成膜结束为止的时间。在下述(表5)中示出计测结果。表5实施方式1现有方法供给工序(材料供给)15sec5sec填充工序1sec0sec成膜工序5sec90sec合计21sec95sec根据计测的结果能够确认:与比较例相比,根据实施方式6,每次的成膜所需的时间整体上从95秒缩短至21秒,能够缩短74秒。另外,使用实施方式6以及比较例各自的方式构建生产线时的节拍时间、即在所有工序中最费时间的工序所需的时间,在实施方式6所涉及的静电填充法的情况下为供给工序的15秒,在比较例的情况下为成膜工序的90秒。因此,就节拍时间而言,实施方式6与比较例相比能够缩短75秒。另外,实施方式6所涉及的供给工序如果应用利用筛子17进行散布的散布方法以外的散布方法,则也能够实现进一步的节拍时间的缩短。另外,示出了使用具有丝网网孔4(多孔体)和丝网乳剂部5(被覆部)的丝网印版2的例子,但是本发明并不限定于此。如果仅由多孔体便能够获得所期望的膜厚,那么不需要被覆部。例如,如果针对金属板而使用了仅成膜部位施加了微细的多孔加工的板,那么不需要丝网印版的乳剂部这样的部分。但是,在想要得到的膜厚大的情况下,优选使用具有丝网网孔4(多孔体)和丝网乳剂部5(被覆部)的丝网印版2。(总结)以上那样的实施方式所涉及的粉体膜形成方法包括:填充工序,向形成于粉体填充部件(丝网印版2)的开口部3填充粉体9;成膜工序,使所述粉体填充部件(丝网印版2)与基板10之间产生电位差,使填充于所述开口部3的粉体9向所述基板10移动而形成粉体膜11。根据该构成,通过刮入体而以一定的厚度填充于粉体填充部件的开口部的粉体,由于粉体填充部件与基板之间的电位差向基板移动而形成一定的厚度的粉体膜。因此,能够以良好的膜厚精度形成粉体膜。在上述粉体膜形成方法中,优选在上述填充工序中通过刮入体15的刮入填充上述粉体9。根据该构成,能够高效地向开口部填充粉体。在上述粉体膜形成方法中,优选在上述填充工序中通过振动填充上述粉体9。根据该构成,能够以简单的构成向开口部3填充粉体。在上述粉体膜形成方法中,优选在上述填充工序中填充带电的粉体9。根据该构成,能够可靠地向开口部填充粉体。在上述粉体膜形成方法中,优选在上述填充工序中通过静电喷涂器17的喷附向上述粉体填充部件(丝网印版2)填充上述带电的粉体9。根据该构成,能够可靠地向开口部填充粉体。在上述粉体膜形成方法中,优选在上述成膜工序中通过刮入体15的刮入使上述粉体9向上述基板10移动。根据该构成,能够高效地使粉体向基板移动。在上述粉体膜形成方法中,优选在上述成膜工序中通过振动使上述粉体9向上述基板10移动。根据该构成,能够以简单的构成使粉体向基板移动。在上述粉体膜形成方法中,上述粉体填充部件(丝网印版2)具备多孔体(丝网网孔4)和在上述多孔体(丝网网孔4)的一个面形成的被覆部(丝网乳剂部5),在上述被覆部(丝网乳剂部5)形成有上述开口部3,在上述成膜工序中,上述被覆部(丝网乳剂部5)配置于上述基板10侧。根据该构成,能够通过一般的丝网印版构成粉体填充部件。如上所述,实施方式所涉及的粉体成膜装置1具备:粉体填充部件(丝网印版2),形成有被填充粉体9的开口部3;刮入体15,通过刮入使上述粉体9从上述开口部3的一端侧填充于上述开口部3;以及电源(直流电源8),使上述粉体填充部件(丝网印版2)与基板10之间产生电位差,使填充于上述开口部3的粉体9向上述基板10移动。在上述粉体成膜装置1中,优选具备对上述粉体填充部件(丝网印版2)励振的励振部(励振部件7)。在上述粉体成膜装置1中,优选具备向上述开口部3填充粉体9的静电喷涂器17。如上所述,实施方式所涉及的粉体膜形成方法包括:填充工序,使粉体9振动并将粉体9填充于形成于粉体填充部件(丝网印版2)的开口部3;成膜工序,使填充于上述开口部3的粉体9向上述基板10移动,形成粉体膜11。在上述粉体膜形成方法中,优选在上述成膜工序利用刮入体15的刮入使上述粉体9向上述基板10移动。在上述粉体膜形成方法中,优选在上述成膜工序中通过振动使上述粉体9向上述基板10移动。在上述粉体膜形成方法中,优选上述粉体填充部件(丝网印版2)具备多孔体(丝网网孔4)和形成于上述多孔体(丝网网孔4)的一个面的被覆部(丝网乳剂部5),在上述被覆部(丝网乳剂部5)形成有上述开口部3,在上述成膜工序中,上述被覆部(丝网乳剂部5)配置于上述基板10侧。(总结-1)如上所述,实施方式1所涉及的粉体膜形成方法包括:填充工序,利用基于刮入体15的刮入向形成于粉体填充部件(丝网印版2)的开口部3填充粉体9;成膜工序,使上述粉体填充部件(丝网印版2)与基板10之间产生电位差,通过使填充于上述开口部3的粉体9向上述基板10移动,在上述基板10形成粉体膜11。根据该构成,被刮入体以一定的厚度填充于粉体填充部件的开口部的粉体向基板移动,形成一定的厚度的粉体膜。因此,以良好的膜厚精度形成粉体膜。在上述粉体膜形成方法中,优选在上述填充工序中,将堵塞上述开口部3的按压部件(压板6)配置于上述开口部3的下侧,从上述开口部3上侧填充上述粉体9后,去除上述按压部件(压板6),在上述成膜工序中,在上述开口部3的下方配置上述基板10,使被填充于上述开口部3的粉体9从上述开口部3的下侧向上述基板10移动。根据该构成,堵塞开口部的按压部件配置于开口部的下侧,从开口部上侧填充粉体。通过利用压板堵塞开口部,能够使填充于开口部的粉体的表面平滑化。其结果是,通过粉体从开口部向基板的移动,能够更均匀地形成粉体膜。在上述粉体膜形成方法中,优选上述粉体填充部件(丝网印版2)包括多孔体(丝网网孔4)和形成于上述多孔体(丝网网孔4)的一个面侧的被覆部(丝网乳剂部5),在上述被覆部(丝网乳剂部5)形成有上述开口部3。根据该构成,作为粉体填充部件,能够使用一般的丝网印版。在上述粉体膜形成方法中,优选从以上述被覆部(丝网乳剂部5)位于上述多孔体(丝网网孔4)上侧的方式配置的上述粉体填充部件(丝网印版2)的被覆部(丝网乳剂部5)侧将上述粉体9填充于上述开口部3,然后,将上述粉体填充部件(丝网印版2)翻转,使填充于上述开口部3的上述粉体9从上述被覆部(丝网乳剂部5)侧向上述基板10移动,在上述基板10形成上述粉体膜11。根据该构成,成膜精度更进一步提高。实施方式1所涉及的粉体成膜装置具备:粉体填充部件(丝网印版2),形成有被填充粉体9的开口部3;刮入体15,利用刮入而从上述开口部3的一端侧将粉体9填充于上述开口部3;按压部件(压板6),设置成能够堵塞上述开口部3的另一端侧;电源(直流电源8),在上述粉体填充部件(丝网印版2)与上述基板10之间产生电位差,以便通过使填充于上述开口部3的粉体9向基板移动10而在上述基板10形成粉体膜11。(总结-2)如上所述,根据实施方式4以及5所涉及的粉体膜形成方法,包括:填充工序,使粉体9振动而将粉体9填充于形成于粉体填充部件(丝网印版2)的开口部3;成膜工序,通过使填充于上述开口部3的粉体9向基板移动10,在上述基板10形成粉体膜11。根据该构成,通过填充于在粉体填充部件(丝网印版2)形成的开口部3的粉体9向基板移动10,从而在上述基板10形成粉体膜11。因此,填充于开口部3的粉体9的平滑的厚度状态反映于成膜后的粉体膜11。因此,通过刷入体21在丝网22上移动,与丝网22上的粉体经过开口部3而向基板移动10的现有构成相比,能够使形成于基板10的粉体膜11的膜厚接近均匀的状态。在上述粉体膜形成方法中,优选在上述成膜工序,使填充于上述开口部3的粉体9振动而向上述基板10移动。根据上述构成,通过设置励振部件,能够使粉体9向基板10移动。在上述粉体膜形成方法中,优选在上述成膜工序中,在上述粉体填充部件(丝网印版2)与上述基板10之间施加电压而使上述粉体9向上述基板10移动。根据上述构成,通过设置直流电源,能够使粉体9向基板10移动。在上述粉体膜形成方法中,优选上述粉体填充部件(丝网印版2)包括多孔体(丝网网孔4)和形成于上述多孔体(丝网网孔4)的一个面的被覆部(丝网乳剂部5),在上述被覆部(丝网乳剂部5)形成有上述开口部3。根据上述构成,能够利用一般的丝网印版构成粉体填充部件。在实施方式4所涉及的粉体膜形成方法中,优选在上述填充工序中,上述被覆部(丝网乳剂部5)配置成位于铅垂方向下侧,在配置有将形成于上述被覆部(丝网乳剂部5)的开口部3的铅垂方向下侧堵塞的按压部件(压板6)的状态下,经过上述多孔体(丝网网孔4)将上述粉体9填充于上述开口部3。根据上述构成,由于所填充的粉体9的下表面通过压板6而变得平坦,粉体9的上表面通过丝网网孔4而变得平坦,因此,能够通过开口部3的容积适当地控制粉体9的填充量。在实施方式4以及5所涉及的粉体膜形成方法中,在上述填充工序之前实施上述粉体9的造粒、正球形化以及粒径分布均匀化中的至少一个工序。根据上述构成,能够提高向丝网印版2的开口部3填充的粉体9的流动性。(总结-3)如上所述,实施方式6~8所涉及的粉体膜形成方法包括:填充工序,向形成于粉体填充部件(丝网印版2)的开口部3填充带电的粉体9;成膜工序,通过在所述粉体填充部件(丝网印版2)与基板10之间产生电位差,使填充于所述开口部3的粉体9向所述基板10移动,从而在所述基板10形成粉体膜11。根据该构成,通过基于所述粉体填充部件(丝网印版2)与基板10之间的电位差而使填充于所述开口部3的粉体9向所述基板10移动,从而在所述基板10形成粉体膜11。因此,填充于开口部3的粉体9的平滑的厚度状态反映于成膜后的粉体膜11。因此,通过刮入体21在丝网22上移动,从而,与丝网22上的粉体经过开口部3向基板移动10的现有构成相比,能够使形成于基板10的粉体膜11的膜厚接近均匀的状态。另外,基于上述电位差,填充于开口部3的粉体9一次性向基板10移动。因此,能够缩短粉体膜的成膜时间。在上述粉体膜形成方法中,优选在上述填充工序中,散布上述粉体9的供给容器14配置于上述开口部3的下侧,通过在上述粉体填充部件(丝网印版2)与上述供给容器14之间产生电位差而使被上述供给容器14散布出的粉体9带电,向上述开口部3填充上述带电的粉体9。根据该构成,能够以简单的构成从开口部3的下侧将粉体9填充于开口部3。在上述粉体膜形成方法中,优选在上述填充工序中,利用静电喷涂器17将上述带电的粉体9喷附于被施加了电压的上述开口部3,使上述带电的粉体9填充于上述开口部3。根据该构成,能够以静电喷涂器17之类的简单的构成将粉体9填充于开口部3。在上述粉体膜形成方法中,优选在上述填充工序中,配置将上述开口部3上表面侧堵塞的按压部件(压板6),从上述开口部3的下表面侧填充上述粉体9。根据该构成,能够利用按压部件(压板6)确保填充于开口部3的粉体9的平滑状态。在上述粉体膜形成方法中,优选上述粉体填充部件(丝网印版2)包括多孔体(丝网网孔4)和形成于上述多孔体(丝网网孔4)的一个面的被覆部(丝网乳剂部5),在上述被覆部(丝网乳剂部5)形成有上述开口部3。根据该构成,能够利用丝网印刷用的一般的不锈钢网孔构成粉体填充部件。在上述粉体膜形成方法中,优选在上述填充工序中,上述被覆部(丝网乳剂部5)配置成位于铅垂方向上侧,配置将形成于上述被覆部(丝网乳剂部5)的开口部3的上表面侧堵塞的按压部件(压板6),经过上述多孔体(丝网网孔4)从上述开口部3的下表面侧填充上述粉体9,在上述成膜工序中,使在上述填充工序中被填充了粉体9的多孔体(丝网网孔4)翻转,在上述基板10形成上述粉体膜11。根据该构成,能够以简单的构成利用按压部件(压板6)确保填充于开口部3的粉体9的平滑状态。在上述粉体膜形成方法中,优选在上述成膜工序中,通过利用刮入体15从上述粉体填充部件(丝网印版2)的与上述基板10相反的一侧向上述开口部3的刮入粉体、或者对上述开口部3施加振动,使上述粉体9向上述基板10移动。根据该构成,填充于开口部3的粉体9的平滑的厚度状态能够更忠实地反映于成膜后的粉体膜11。实施方式6~8所涉及的粉体成膜装置具备:粉体填充部件(丝网印版2),形成有被填充带电的粉体9的开口部3;电源(直流电源8),在上述粉体填充部件(丝网印版2)与上述基板10之间产生电位差,以便通过使填充于上述开口部3的粉体9向基板移动10而在上述基板10形成粉体膜11。为了解决上述的课题,本发明的一方式所涉及的粉体膜形成方法的特征在于,包括:填充工序,通过利用刮入体的刮入,向形成于粉体填充部件的开口部填充粉体;以及成膜工序,通过在上述粉体填充部件与基板之间产生电位差,使填充于上述开口部的粉体向上述基板移动,从而在上述基板形成粉体膜。为了解决上述的课题,本发明的一方式所涉及的粉体成膜装置的特征在于,具备:粉体填充部件,形成有被填充粉体的开口部;刮入体,通过刮入从上述开口部的一端侧将粉体填充于上述开口部;按压部件,设置成能够堵塞上述开口部的另一端侧;电源,使上述粉体填充部件与上述基板之间产生电位差,以便通过使填充于上述开口部的粉体向基板移动而在上述基板形成粉体膜。为了解决上述的课题,本发明的一方式所涉及的粉体膜形成方法的特征在于,包括:填充工序,使粉体振动而将粉体填充于形成于粉体填充部件的开口部;以及成膜工序,通过使填充于上述开口部的粉体向基板移动,从而在上述基板形成粉体膜。为了解决上述的课题,本发明的一方式所涉及的粉体成膜装置的特征在于,具备:粉体填充部件,形成有被填充粉体的开口部;励振部件,对上述粉体填充部件励振,以便向上述开口部填充上述粉体;直流电源,在上述粉体填充部件与基板之间施加电压,使上述粉体向上述基板移动。为了解决上述的课题,本发明的一方式所涉及的粉体膜形成方法的特征在于,包括:填充工序,向形成于粉体填充部件的开口部填充带电的粉体;成膜工序,通过在上述粉体填充部件与基板之间产生电位差,使填充于上述开口部的粉体向上述基板移动,从而在上述基板形成粉体膜。为了解决上述的课题,本发明的一方式所涉及的粉体成膜装置的特征在于,具备:粉体填充部件,形成有被填充带电的粉体的开口部;电源,在上述粉体填充部件与上述基板之间产生电位差,以便通过使填充于上述开口部的粉体向基板移动而在上述基板形成粉体膜。本发明的方式的目的在于实现一种粉体膜形成方法以及粉体成膜装置,能够使形成于被印刷物的粉体膜的膜厚接近均匀的状态。本发明的方式的目的在于实现一种粉体膜形成方法以及粉体成膜装置,能够使形成于被印刷物的粉体膜的膜厚接近均匀的状态,并且能够缩短粉体膜的成膜时间。根据本发明的方式,能够实现使形成于被印刷物的粉体膜的膜厚接近均匀的状态的效果。根据本发明的方式,起到如下效果:能够使形成于被印刷物的粉体膜的膜厚接近均匀的状态,并且能够缩短粉体膜的成膜时间。附图标记说明:1:粉体成膜装置;2:丝网印版(粉体填充部件);3:开口部;4:丝网网孔(多孔体);5:丝网乳剂部(被覆部);6:压板(按压部件);7:励振部件(励振部);8:直流电源(电源);9:粉体;10:基板;11:粉体膜;15:刮入体;16:被印刷物;17:静电喷涂器。当前第1页12