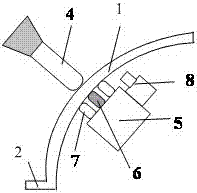
本发明涉及数控加工领域,具体涉及运载火箭贮箱整体成形箱底五轴镜像铣数控加工方法。
背景技术:箱底是运载火箭燃料贮箱的关键承力结构,其加工质量对火箭整体性能和可靠性等都有着极为重要的影响。箱底设计面形为椭圆第I象限曲线段绕短轴的回转面,对应不同型号火箭,其大小(φ2250mm~φ5000mm)、几何尺寸(壁厚0.8mm~2.6mm)及精度要求(壁厚公差±0.1mm~±0.2mm)各异,但都属于大尺寸、薄壁、复杂双曲率曲面类高精度零件。目前,塑性整体成形工艺(如充液拉深、旋压等),逐步成为箱底成形的重要方法。按设计减重要求,整体成形箱底需加工大面积减轻区域且减轻区壁厚相等。图1所示为现有的化铣加工工艺流程示意图;图2所示为现有的基于“模胎式装夹”的数控加工工艺流程示意图。现有化铣方法存在的问题:(1)化学腐蚀极易出现过腐蚀或不均匀腐蚀,导致整体成形箱底出现点蚀坑、壁厚偏薄,零件强度不满足设计要求,或者腐蚀不到位、费重过大;(2)排放大量化学废液,环境污染严重、后续处理成本大。数控加工替代化铣已成为必然趋势。现有基于“模胎式装夹”的数控加工方法存在的问题:(1)箱底减轻区与模胎之间无法“夹紧”,只有“定位”关系,属于不可靠装夹;(2)不可靠装夹下,切削力/热耦合导致零件加工变形,刀具实际切削厚度呈随机变化,剩余壁厚尺寸无法保证(合格率不到10%)、精度严重超差(实际壁厚公差±0.5mm~±1.5mm);(3)需要多次测量厚度并反复补偿,箱底加工一致性差、可靠性低,只能采用极为保守的工艺参数,加工效率极低。对此,亟需一种更为先进可靠的数控加工方法,实现整体成形箱底等壁厚、变形可控、高精度加工。
技术实现要素:本发明解决的问题是,如何实现整体成形箱底等壁厚变形可控精密数控加工;为解决所述问题,本发明提供整体成形箱底五轴镜像铣数控加工方法。本发明提供的整体成形箱底五轴镜像铣数控加工方法,包括:步骤一、将零件置于回转工装台面,并定位;步骤二、刀具沿所述零件外型面切削;随动装置沿零件内型面移动,刀具的轴线、随动装置的轴线与零件的法线在同一条直线上;步骤三、测厚仪测量当前点厚度,如果和设定的厚度相同,刀具移动到下一点;如果比设定的厚度大,继续切削当前点。进一步,所述零件为贮箱整体成形箱底,采用回转工装台上的夹紧机构夹紧箱底裙边;调节回转工装台面的位置调整机构,调整已夹紧箱底的整体位置,使得箱底轴线与回转工装台回转轴同轴。进一步,实现箱底轴线与回转工装台回转轴同轴包括:步骤1.1、采用非接触式线激光扫描箱底内型面的底部和中部,得到两组环形点云,点云数不小于500万个;步骤1.2、采用垂直于回转工装台回转轴的横截面截取环形点云,计算环形点云横截面形状的圆心,横截面数量不小于300个;步骤1.3、采用最小二乘算法拟合所述圆心所在的直线,调节回转工装台上的位置调整机构,调整已夹紧箱底的整体位置,使得拟合直线与回转工装台回转轴同轴,即整体成形箱底轴线与回转工作台回转轴同轴。进一步,所述刀具的走刀方式为“Zig-Zag”型或螺旋型。进一步,所述切削包括粗加工切削和精加工切削,所述粗加工切削设定的厚度为2mm~3mm,进给速度4000mm/min~6000mm/min;转速为5000rpm~8000rpm;精加工切削设定的厚度为0.5mm~0.8mm、进给速度6000mm/min~8000mm/min、转速为8000rpm~10000rpm。进一步,通过摆动刀具调整刀具轴线;通过摆动随动装置调整随动装置轴线。本发明的有益效果包括:本发明所提供的方案的刀具具有直角坐标系下的三个自由度、摆动自由度、转动自由度;随动装置具有直角坐标系下的三个自由度和摆动自由度;刀具切削零件时,随动装置同步移动,对零件形成支撑与保护,提高了切削位置的支撑刚度与夹紧效果,进而控制切削变形;随动装置的测厚仪精确测量零件厚度,实时对比测量厚度与设定厚度的差值并反馈,根据反馈的厚度差进行加工,确保零件等厚,提高精度。随动装置由回转工装台带动转动,随动装置、刀具同轴,且轴线与零件的法线重合,所以可以提高精度和可靠性。附图说明图1为现有的基于化铣加工的工艺流程示意图;图2为现有的基于“模胎式装夹”的数控加工工艺流程示意图;图3为本发明所述的一种运载火箭燃料贮箱整体成形箱底等厚度五轴镜像铣数控加工方法示意图。具体实施方式下文中,结合附图和实施例对本发明作进一步阐述。本发明实施例提供的整体成形箱底五轴镜像铣数控加工为例,包括:步骤一、将零件放置在五轴镜像铣加工装置的回转工装台面上,工装台包括夹紧机构和位置调整机构,采用夹紧机构夹紧箱底裙边2,如图3。参考图3,本发明实施例采用的五轴镜像铣数控加工装置包括:刀具4、随动装置5;所述随动装置5包括测厚仪6;工作时,所述刀具4的轴线、随动装置5的轴线、零件1的法线重合;所述测厚仪6测量零件的厚度。所述刀具包括动力头,所述动力头连接驱动装置,通过驱动装置驱动刀具运动;所述刀具具有沿零件表面移动的自由度,即在直角坐标系中的三个自由度、摆动自由度和绕垂直于动力头轴线转动的自由度。所述随动装置与刀具同步运动。所述随动装置具有沿零件内表面移动的自由度和摆动自由度,通过摆动调节刀具和随动装置的轴线的方向;所述随动装置由回转工装台带动转动。步骤二、调节所述零件的位置,满足零件轴线与回转工作台同轴;步骤三、刀具沿零件的外型面切削零件,随动装置沿零件内型面同步移动;其中刀轴方向与箱底各切削点位置外法线方向一致,走刀方式为“Zig-Zag”型或螺旋型。为了对零件形成支撑与可靠装夹,所述随动装置还包括支撑于随动装置平台表面和零件内型面之间的支撑单元7,参考图3。为保证零件轴线与回转工作台轴线重合,如图3所示,所述随动装置还包括扫描仪8,在一个实施例中,所述扫描仪采用非接触式线激光扫描仪。所述步骤二包括:步骤1.1、采用非接触式线激光扫描箱底内型面,线激光宽度为32mm,扫描位置分别为箱底中部,(例如:箱底高度1/2处)和底部(例如:靠近裙边),得到两组环形点云,点云数不小于500万个(例如:线激光宽度分辨率为0.01mm,则采样点数量约为500万个);步骤1.2、根据逆向工程中成熟的算法(例如:基于最小距离原则的去噪算法),消除冗余点、噪声点与重叠点,计算点云环形横截面圆心,横截面数量不小于300个(例如:按0.1mm等分线激光宽度,可得横截面320个);步骤1.3、采用最小二乘算法拟合直线,调节位置调整机构,调整已夹紧箱底的整体位置,使得拟合直线与回转工装台回转轴同轴,同轴度不大于3mm(例如:1mm、2mm、3mm),固定零位调整工装。所述步骤三包括粗加工切削和精加工切削,刀具为聚晶金刚石刀具,粗加工切削设定的厚度为2mm~3mm、进给速度4000mm/min~6000mm/min、转速为5000rpm~8000rpm,精加工切削设定的厚度为0.5mm~0.8mm、进给速度6000mm/min~8000mm/min、转速为8000rpm~10000rpm,刀轴方向与箱底各切削点位置外法线方向一致,走刀方式为“Zig-Zag”型或螺旋型。本发明的优点包括:本发明方法整体成形箱底五轴镜像铣,壁厚加工精度高且一致性好、效率高,随动装置可实现任意切削区域的可靠装夹、加工变形小,可实现厚度实时测量与补偿。采用“整体成形箱底五轴镜像铣方案”较“化铣方案”加工精度高、可靠性高、减重效果好、无污染、无需后续处理、加工后的切屑可重复利用;采用“整体成形箱底五轴镜像铣方案”较“基于‘模胎式装夹’数控铣削方案”装夹稳定可靠、加工精度高、加工变形小、可满足箱底等壁厚加工要求、无需反复测量与补偿,效率大幅提升。本发明虽然已以较佳实施例公开如上,但其并不是用来限定本发明,任何本领域技术人员在不脱离本发明的精神和范围内,都可以利用上述揭示的方法和技术内容对本发明技术方案做出可能的变动和修改,因此,凡是未脱离本发明技术方案的内容,依据本发明的技术实质对以上实施例所作的任何简单修改、等同变化及修饰,均属于本发明技术方案的保护范围。