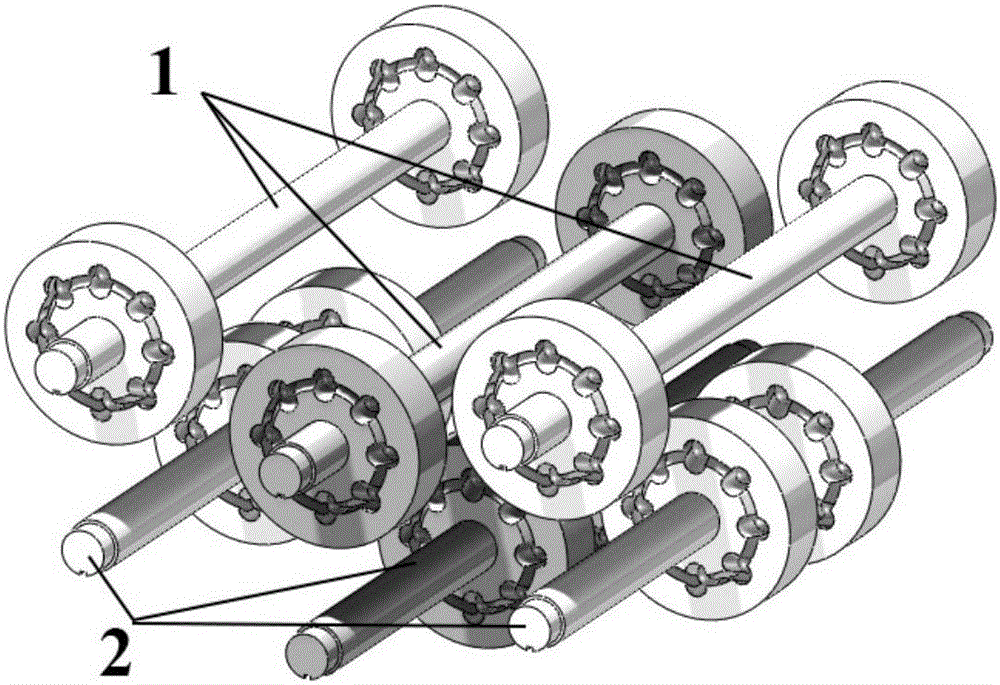
本发明属于复合板矫直技术领域,特别涉及一种热轧金属复合板预矫直辊系。
背景技术:目前,热轧金属复合板在造船、石油、化工等行业中的应用日益广泛,对其品质的要求也日益提高。金属复合板由于层间材料的物理性能和力学性能的不同,复合板截面为非对称结构,造成其在生产过程中普遍出现板形的双向瓢曲缺陷(如图1所示)。板形的双向瓢曲缺陷表现为复合板沿板长与板宽方向皆存在大曲率的瓢曲,造成复合板的边部与中部存在一个较大的挠度差,往往会超过矫直机的开口度,造成矫直设备无法咬入;而复合板即使能够顺利进入矫直机,传统矫直辊系也仅仅能够矫正复合板长度方向的挠曲,对复合板宽度方向的大曲率挠曲的矫正能力十分有限;因此需要对其进行预矫直处理。目前针对热轧金属复合板的预矫直设备还是一片空白。
技术实现要素:本发明的目的就是克服现有技术的不足,针对热轧金属复合板在宽度方向上存在大挠度差造成矫直机无法咬入的问题,提供一种热轧金属复合板预矫直辊系,能有效消除复合板沿宽度方向的大挠度挠曲,保证后续矫直设备的顺利咬入,同时调整中间矫直单元的高度位置能够有效消除复合板长度方向的整体挠曲。本发明一种热轧金属复合板预矫直辊系,包括中间矫直单元、2个边侧矫直单元;所述中间矫直单元、边侧矫直单元分别包括上、下2个矫直辊;所述中间矫直单元的整体高度及2个矫直辊的开口度均可调;所述边侧矫直单元沿复合板进给方向的位置及2个矫直辊的开口度均可调。进一步的,所述上、下矫直辊均分别包括传动轴、2个矫直辊片和套筒,2个矫直辊片通过套筒与对应的传动轴连接。进一步的,所述矫直辊片2个成组装配于所述传动轴上;当上矫直辊的2个矫直辊片装配于对应传动轴的两端时,下矫直辊的2个矫直辊片装配于对应传动轴的中部;当上矫直辊的2个矫直辊片装配于对应传动轴的中部时,下矫直辊的2个矫直辊片装配于对应传动轴的两端。进一步的,所述传动轴上开有1个贯穿轴向的键槽,所述套筒内径与所述传动轴内径呈间隙配合,对所述矫直辊片起轴向定位作用。进一步的,所述矫直辊片包括内球笼、钢珠和外辊环。进一步的,所述内球笼的外径与所述外辊环的内径上均开有凹槽,通过所述钢珠配合,具有实时保持所述外辊环与复合板面接触的自调节功能;所述内球笼与所述传动轴为间隙配合,内径处开有键槽,通过键与传动轴实现沿传动轴的周向定位。本发明的突出有益效果为:1、通过调整中间矫直单元的高度位置能有效消除复合板沿长度方向的大挠度挠曲;2、两组矫直辊片分别装配于上下矫直辊的两端或中部;通过调整矫直单元内上下矫直辊的开口度使复合板沿宽度方向形成塑性弯曲,能有效消除沿复合板宽度方向的大挠度挠曲;3、矫直辊片的自调节设计能够保证矫直辊片与复合板在预矫直过程中保持面接触,避免过大的接触应力对复合板表面造成伤害;4、不同规格的套筒可以调整矫直辊片在矫直辊上的装配位置,以适应不同的复合板板宽;5、中间矫直单元的整体高度与两辊开口度可调,两边矫直单位纵向位置和两辊开口度可调,能适应不同的来料板形与板形缺陷。附图说明图1所示为热轧金属复合板的双向瓢曲缺陷示意图。图2所示为本发明实施例一种热轧金属复合板预矫直辊系整体结构立体示意图。图3所示为矫直单元调整方式示意图。图4所示为矫直辊结构示意图。图5所示为矫直辊片结构示意图。图6所示为矫直辊片与复合板接触角度自调节示意图。图7所示为金属复合板在辊系中宽度方向弯曲状态示意图。图8所示为金属复合板在辊系中长度方向弯曲状态示意图。图中:1-上矫直辊、2-下矫直辊、3-中间矫直单元、4-边侧矫直单元、5-传动轴、6-套筒、7-矫直辊片、8-内球笼、9-外辊环、10-钢珠、11-复合板沿宽度方向初始挠曲状态、12-复合板沿宽度方向矫直过程挠曲状态、13-复合板沿长度方向初始挠曲状态、14-复合板沿长度方向矫直过程挠曲状态。具体实施方式下文将结合具体附图详细描述本发明具体实施例。应当注意的是,下述实施例中描述的技术特征或者技术特征的组合不应当被认为是孤立的,它们可以被相互组合从而达到更好的技术效果。在下述实施例的附图中,各附图所出现的相同标号代表相同的特征或者部件,可应用于不同实施例中。如图2、3所示,本发明实施例一种热轧金属复合板预矫直辊系,包括中间矫直单元3、2个边侧矫直单元4;所述中间矫直单元3、边侧矫直单元4分别包括上、下2个矫直辊1、2;所述中间矫直单元3的整体高度及2个矫直辊1、2的开口度均可调;所述边侧矫直单元4沿复合板进给方向的位置及2个矫直辊1、2的开口度均可调。如图4所示,优选的,所述上、下矫直辊1、2均分别包括传动轴5、2个矫直辊片7和套筒6,2个矫直辊片7通过套筒6与对应的传动轴5连接。优选的,所述矫直辊片7两个成组装配于所述传动轴5上;当上矫直辊1的2个矫直辊片7装配于对应传动轴5的两端时,下矫直辊2的2个矫直辊片7装配于对应传动轴5的中部;当上矫直辊1的2个矫直辊片7装配于对应传动轴5的中部时,下矫直辊2的2个矫直辊片7装配于对应传动轴5的两端。优选的,所述传动轴5上开有1个贯穿轴向的键槽,所述套筒6内径与所述传动轴5内径呈间隙配合,对所述矫直辊片7起轴向定位作用,同时配合使用与传动轴5直径呈间隙配合的具有不同长度的套筒6,使两个矫直辊片7能够定位在传动轴5轴向的任意位置。如图5、6所示,优选的,所述矫直辊片7包括内球笼8、钢珠10和外辊环9;所述内球笼8的外径与所述外辊环9的内径上均开有凹槽,通过所述钢珠10配合,具有实时保持所述外辊环9与复合板面接触的自调节功能;所述内球笼8与所述传动轴5为间隙配合,内径处开有键槽,通过键与传动轴实现沿传动轴的周向定位;矫直辊片7主要实现对复合板的纵向及横向弯曲矫正,及转动带动复合板实现连续进给的功能,同时需要具备随复合板的弯曲状态而随时与其保持面接触的接触角度自调节功能。首先,内球笼8与传动轴5通过键连接实现内球笼8与传动轴5的同步转动;其次,内球笼8与外辊环9上开有滚道,通过钢珠10传动实现外辊环9与内球笼8的同步转动,继而带动复合板实现连续进给,该结构还能够使内球笼8与外辊环9在轴向呈任意夹角的条件下实现传动,继而能够保证外辊环9随复合板的弯曲状态而随时与其保持面接触的状态,实现矫直辊片7接触角度自调节功能。使用时,根据复合板的复合板宽度及沿宽度方向的缺陷形态,确定上下矫直辊1、2各自矫直辊片7的装配位置及装配形式,若复合板缺陷形态为图1中a所示的双向凹入缺陷,则在所有矫直单元3、4中上矫直辊1的矫直辊片7装配在传动轴5两端,下矫直辊2的矫直辊片7装配在传动轴5中部;若复合板缺陷形态为图1中b所示的双向凸出缺陷,则所有矫直单元3、4中的上矫直辊1的矫直辊片7装配在传动轴5中部,下矫直辊2的矫直辊片7装配在传动轴5两端,再通过计算机或手动方式调整各矫直单元3、4上、下矫直辊1、2的开口度;其效果是使复合板在各矫直单元3、4中沿宽度方向形成与原始缺陷弯曲方向相反的塑性弯曲状态(如图7所示,其中11为复合板沿宽度方向初始挠曲状态、12为复合板沿宽度方向矫直过程挠曲状态),从而实现矫后复合板宽度方向挠曲的消除。然后要根据复合板的规格尺寸及沿长度方向的缺陷形态,通过计算机或手动方式调整中间矫直单元3的整体高度位置及两边侧矫直单元4沿复合板进给方向的位置;其效果是通过三个矫直单元3、4高度位置的不同,使复合板沿长度方向形成与原始缺陷弯曲方向相反的塑性弯曲状态(如图8所示,其中13为复合板沿长度方向初始挠曲状态、14为复合板沿长度方向矫直过程挠曲状态),从而实现矫后复合板沿长度方向挠曲的消除;同时,通过调整两边侧矫直单元4的纵向位置,使预矫直辊系根据不同的复合板规格形成需要的辊距,从而保障辊系对于各种规格复合板的承载能力。最后,通过驱动装置转动各矫直辊1、2的传动轴5实现复合板的连续进给矫直过程。本发明的突出有益效果为:1、通过调整中间矫直单元的高度位置能有效消除复合板沿长度方向的大挠度挠曲;2、两组矫直辊片分别装配于上下矫直辊的两端或中部;通过调整矫直单元内上下矫直辊的开口度使复合板沿宽度方向形成塑性弯曲,能有效消除沿复合板宽度方向的大挠度挠曲;3、矫直辊片的自调节设计能够保证矫直辊片与复合板在预矫直过程中保持面接触,避免过大的接触应力对复合板表面造成伤害;4、不同规格的套筒可以调整矫直辊片在矫直辊上的装配位置,以适应不同的复合板板宽;5、中间矫直单元的整体高度与两辊开口度可调,两边矫直单位纵向位置和两辊开口度可调,能适应不同的来料板形与板形缺陷。本文虽然已经给出了本发明的几个实施例,但是本领域的技术人员应当理解,在不脱离本发明精神的情况下,可以对本文的实施例进行改变。上述实施例只是示例性的,不应以本文的实施例作为本发明权利范围的限定。