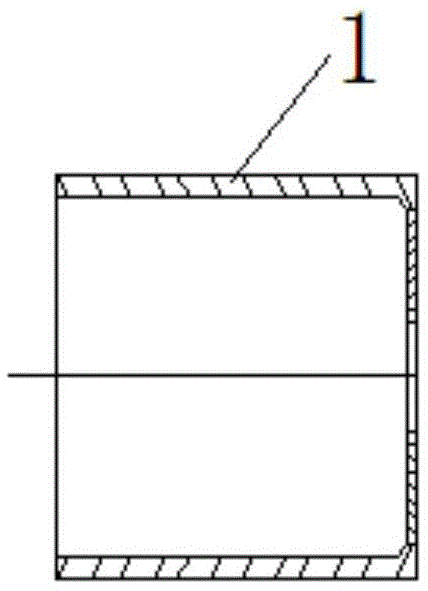
本发明涉及固体火箭发动机燃烧室壳体生产技术,具体地指一种小直径多台阶变壁厚圆筒的精密旋压加工方法。
背景技术:
:在固体火箭发动机中需要用到燃烧室壳体,燃烧室壳体内灌装动力药柱,为发动机的飞行提供动力。在固体火箭发动机燃烧室壳体制造领域,高强度钢是我国目前发动机壳体制造领域的主导材料。为了提高导弹武器的打击范围及突防能力,要求火箭发动机为导弹武器提供更大的射程和速度,要求壳体结构紧凑,以减小壳体比重,增加弹药比重,提高武器威力。高强度钢在退火状态下具有较好的延伸率和断面收缩率,塑性加工效果好的优势,可以用于冷态旋压。但变壁厚圆筒的旋压一直是旋压的技术难点。实际生产中一般通过精确计算和控制旋压过程中的金属流动,调整工艺参数和旋轮轨迹,实现对不同部分尺寸和位置度的控制,同时还必须考虑由于多种减薄率、旋轮轨迹等多种因素,防止在过渡区域出现各种缺陷。现有某型号小直径多台阶变壁厚细长圆筒,采用反向旋压方式成形,其工艺流程为:锻造制坯→旋压→中间退火→旋压→旋压→中间退火→旋压→旋压→检验→超声检测→退火→油封包装入库。目前这种方法存在以下问题:1)反向旋压的圆筒台阶长度尺寸、圆筒壁厚、直径均很难满足精度要求,产品质量不稳定,只能用于相关飞行试验,不能正式使用;2)工艺流程复杂;3)材料利用率低。技术实现要素:本发明的目的就是要提供一种小直径多台阶变壁厚圆筒的精密旋压加工方法,该方法制的的产品尺寸精度高,质量稳定可控,材料利用率高,工艺流程简单,既降低生产成本,又能缩短生产周期。为实现上述目的,本发明采用的技术方案是:一种小直径多台阶变壁厚圆筒的精密旋压加工方法,包括以下步骤:1)按旋压工艺要求精车出锻环(1),然后在所述锻环(1)后端焊接堵板并将所述锻环(1)装夹到位;2)在数控旋压机上将所述锻环(1)进行第一道次旋压开坯;主轴转速50~60rpm,进给比1.8~2.0mm/r,道次减薄率19~25%,形成一旋筒段(2);3)继续在数控旋压机上将所述一旋筒段(2)进行第二道次旋压;主轴转速50~60rpm,进给比1.8~2.0mm/r,道次减薄率38.8%,用超声波测厚仪测量厚度后进行第三道次旋压,形成二旋筒段(3);4)接着在数控旋压机上将所述二旋筒段(3)进行第四道次旋压;旋压时主轴转速50~60rpm,进给比1.8~2.0mm/r,道次减薄率26.6%,形成具有1~5个台阶的三旋筒段(4);5)最后在数控旋压机上将所述三旋筒段(4)进行第五道次旋压;旋压时主轴转速50~60rpm,进给比1.2~1.4mm/r,道次减薄率20%~49%,形成具有6~9个台阶的小直径多台阶变壁厚圆筒(5)。进一步地,所述步骤2)中,第一道次旋压开坯完成后,对所述一旋筒段(2)脱模,进行中间去应力退火,消除旋压加工应力。进一步地,所述步骤3)中,第三道次旋压完成后,对所述二旋筒段(3)脱模,进行中间去应力退火,消除旋压加工应力。进一步地,所述步骤1)中,所述锻环(1)采用高强度钢或超高强度钢锻环或厚壁钢管,经退火或球化退火,晶粒度≥4级,单边壁厚≥20mm,精车后表面粗糙度≥1.6μm。进一步地,所述步骤2)和步骤3)中,采用双锥面结构旋轮,旋轮硬度为hrc60-65,表面粗糙度为ra1.6μm,旋轮工作角为25°,旋轮退出角为30°,圆角半径r为8mm。进一步地,所述步骤4)和步骤5)中,采用双锥面结构旋轮,旋轮硬度为hrc60-65,表面粗糙度为ra1.6μm,旋轮工作角为30°,旋轮退出角为30°,圆角半径r为8mm。进一步地,所述步骤2)中,中间去应力退火温度为600℃±15℃,保温时间为60~80min,空冷。进一步地,所述步骤3)中,中间去应力退火温度为600℃±15℃,保温时间为60~80min,空冷。进一步地,所述步骤1)中,锻环(1)退火温度为600℃±15℃,保温时间为40~60min,空冷;球化退火温度为750℃±15℃,保温时间为60~90min,随炉冷却。更进一步地,所述小直径多台阶变壁厚圆筒的最小直径为160.8~1600mm,最小壁度为0.8~7.3mm,长径比为6~12,长l为300~2300mm。与现有技术相比,本发明具有以下优点:其一,本发明的用于固体火箭发动机壳体的小直径多台阶变壁厚的薄壁圆筒的精密旋压加工方法,与已有的反向旋压方式相比,具有旋压尺寸精度高,稳定性好的优点。其二,本发明的旋压加工方法只需投入一套正向旋压芯模,利用设备尾顶机构,旋压过程模具刚性优良,筒体直线度高,而已有的反向旋压方式中的旋压芯模未利用设备尾顶机构,旋压过程模具刚性不良,芯模跳动大,筒体直线度低。其三,本发明方法工艺流程简单,操作简单,产品质量稳定可控,材料利用率高,既降低生产成本,又能缩短生产周期。附图说明图1为实施例1中锻环结构示意图。图2为实施例1中一旋筒段结构示意图。图3为实施例1中二旋筒段结构示意图。图4为实施例1中三旋筒段结构示意图。图5为实施例1中小直径多台阶变壁厚圆筒结构示意图。具体实施方式下面结合附图和具体实施例对本发明作进一步的详细说明,便于更清楚地了解本发明,但它们不对本发明构成限定。实施例1一种用于固体火箭发动机的小直径多台阶变壁厚圆筒的精密旋压加工方法,包括如下步骤:1)按旋压工艺要求精车出锻环(1):锻环采用高强度钢或超高强度钢锻环或厚壁钢管,经退火或球化退火,晶粒度≥4级,单边壁厚≥20mm,精车后表面粗糙度达到1.6μm以上,后焊接堵板;2)芯模安装和旋轮安装调整,试运行检测合格,将上述旋压坯料(1)安装于旋压芯模上,固定于芯模尾端,启动尾顶,轴向移动,推动坯料将锻环(1)装夹到位。3)启动三旋轮,在数控旋压机上将锻环(1)进行一道次旋压开坯;主轴转速50~60rpm,进给比1.8~2.0mm/r,道次减薄率道次减薄率19%~25%,形成一旋筒段(2);4)一道次旋压完成后,对一旋筒段(2)脱模,进行中间去应力退火,消除旋压加工应力;5)将一旋筒段(2)再次装模,启动三旋轮,在数控旋压机上将一旋筒段(2)进行第二道次旋压;主轴转速50~60rpm,进给比1.8~2.0mm/r,道次减薄率38.8%,用超声波测厚仪测量厚度后进行第三道次旋压;形成二旋筒段(3);6)第三道次旋压完成后,对二旋筒段(3)脱模,进行中间去应力退火,消除旋压加工应力;7)二旋筒段(3)再次装模,启动三旋轮,在数控旋压机上将二旋筒段(3)进行第四道次旋压;旋压时主轴转速50~60rpm,进给比1.8~2.0mm/r,道次减薄率26.6%,形成具有5个台阶的三旋筒段(4);8)启动三旋轮,在数控旋压机上将三旋筒段(4)进行第五道次旋压;旋压时主轴转速50~60rpm,进给比1.2~1.4mm/r,道次减薄率20%~49%,形成9个台阶的小直径多台阶变壁厚圆筒(5)。实施例1所加工的旋压圆筒的圆筒最小直径φ为360.8mm,圆筒的最小壁度δ为2.8mm,圆筒的长径比m为6.7,圆筒的长l为2400mm,圆筒的变壁厚台阶n为9个。将实施例1所加工的旋压圆筒置于工艺车上检测,检测结果如表1所示。表1序号设计要求圆筒检测值结论1.台阶1长度≥897990合格2.台阶2长度788±3.5790合格3.台阶3长度733±3736合格4.台阶4长度448±2450合格5.两处台阶5长度130±2128合格6.台阶6长度285±3286合格7.两处台阶7长度505±4502合格8.筒体有效长度≥23002400合格9.圆筒壁厚2.8+0.15-0.10,2.80~2.88合格10.台阶壁厚4+0.3004.06~4.16合格11.台阶壁厚5.5±0.25.45~5.55合格12.台阶壁厚7.50-0.37.40~7.50合格13.台阶壁厚4+0.3004.19~4.25合格14.台阶壁厚7.50-0.37.40~7.49合格15.台阶壁厚5.5±0.25.50~5.59合格16.台阶壁厚4+0.3004.18~4.24合格17.圆筒最小壁厚2.8+0.15-0.10,2.84~2.88合格18.圆筒最小直径φ360.8±0.5,φ361合格19.直线度0.8/10000.6合格从表1数据可以看出,按本发明方法所旋压的小直径多台阶变壁厚的薄壁圆筒尺寸精度高,筒体直线度高,稳定性好。当前第1页12