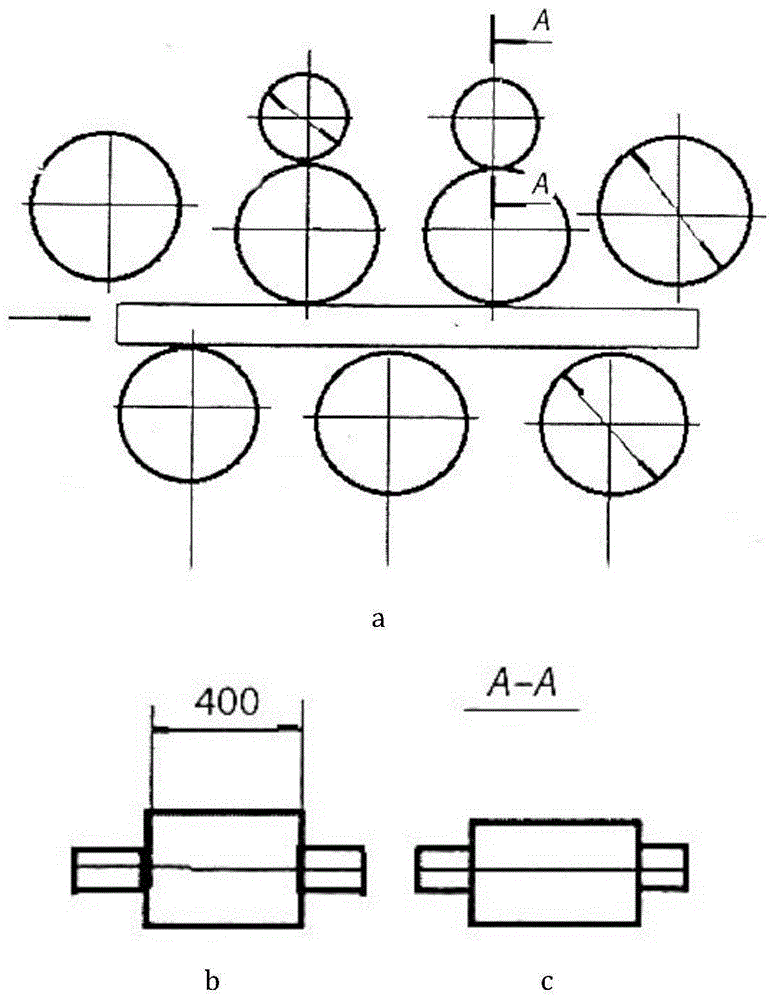
本实用新型涉及的是一种机器制造领域的技术,具体是一种带前端卷起装置的七辊辊式高精度矫直机。
背景技术:
:在钛及钛合金板材的加热、轧制、精整、运输及各种加工过程中,由于外力作用,温度变化及内力消长等因素影响,会产生不同程度的弯曲、浪形、镰弯或歪扭等塑性变形或内部残余应力。为消除这些形状缺陷和残余应力以获得平直的钛及钛合金板材成品,板材需要在矫直机上进行矫直整平,而整平装置是矫直机的核心装置。钛合金板材加工设备中的平行辊矫直机往往需要高速运行且要达到很好的整平效果,而矫直机的整平装置在运行过程中会因为工作辊径和辊距的大小与布局情况而影响到矫直效果。工作辊径大相应要求辊距要大,而辊距大又会使板材塑性变形不足,保证不了矫直精度,同时板件可能打滑,无法咬入。工作辊径小,则强度不足,刚度弱,工作辊易起弧,矫直效果不佳。而且,现有矫直机板材前端一段自由下荡,得不到矫直,不得不切去一段昂贵的钛材。技术实现要素:本实用新型针对现有技术存在的上述不足,提出一种具有改进钛合金板材矫直精度的带前端卷起装置的七辊矫直机,通过在矫直装置外加入板材前端卷起装置,改变了板材在矫直辊间的受力弯曲状态,与辊式矫直机一起形成新的矫直系统,在液压缸增加压力条件下,活塞杆传给非传动辊上的力增大,解决了板材前端没有被矫直辊碾压矫直的问题。从而改善板材质量。本实用新型是通过以下技术方案实现的:本实用新型包括:设置于机床上的用于提供向上压力的卷起装置和矫直装置。所述的卷起装置包括:框架、液压缸、支架、非传动辊和平板,其中:框架设置于机床上,液压缸设置于框架内最底部,平板设置于液压缸上并且两端与框架相连,支架设置于平板上,非传动辊设置于支架之间并且两端与支架相连;通过电机驱动油泵,使液压缸内的活塞杆上顶,通过平板抬升板材抵近非传动辊,使板材上翘从而将原来为负号弯曲变为正号平板。所述的液压缸内设有充液阀、压力管路、活塞和回程管路,其中:压力管路和回程管路分别位于活塞的上下两端,充液阀位于液压缸顶部,由压力油的作用产生力,通过输入压力油使液压缸产生往复运动,由输入压力油的流量控制速度,由液压油的流动方向控制液压缸的往复运动。所述的液压缸的工作压力为0-16mpa,活塞杆的最大轴向力为0-20.1kn,液压缸的长度为580mm,活塞杆行程为435mm,活塞杆直径为25mm,活塞直径40mm。所述的支架为高度可调结构,根据板材的弯曲情况及厚度,限制板材上趐高度,避免框架内矫直辊受力过大,同时保证进料板材的弯曲经矫直后一直保持在工艺限定尺寸公差范围内。所述的非传动辊直径为120mm,因带前端卷起装置,非传动辊会根据板材的形状和液压缸的压力,自动调整板材的送料高度,始终保证板材翘起,保持矫直辊间的板材一直处于正号弯曲的状态。所述的平板为活动结构,可随液压缸活塞杆上下,保持与非传动辊的高度和抵抗板材的下压力,使板材始终处于上趐状态。所述的矫直,采用矫直装置实现,其包括:箱体、工作辊和三角支撑架,其中:三角支撑架和箱体分别设置于机床上两侧,工作辊分别设置于箱体内上下两侧,三角支撑架和卷起装置设置于机床的同一侧。技术效果与现有技术相比,本实用新型通过在矫直装置外加入板材前端卷起装置,与辊式矫直机一起形成新的矫直系统,在液压缸增加压力条件下,降低了板材的弯曲度,从而改善板材质量,使得矫正效率由78%提高到81.6%。附图说明图1为传统七辊矫直机系统结构示意图;图中:a为侧视图;b和c分别为图1a中的a-a面局部剖视图;图2为本实用新型整体结构示意图;图中:机床1、箱体2、工作辊3、三角支撑架4、非传动辊5、支架6、液压缸7、框架8、平板9、矫直装置10、卷起装置11、充液阀12、压力管路13、活塞14、回程管路15。图3为卷起装置a-a剖面结构示意图;图4为液压缸示意图;图中:a为工作行程示意图,b为回程示意图;图5为干涉条纹照片;图6为框架模型测量点分布图。具体实施方式如图2所示,为本实施例涉及一种具有改进钛合金板材矫直精度的带前端卷起装置的七辊矫直机,包括:机床1和设置于机床1上的矫直装置10和卷起装置11,其中:卷起装置11与矫直装置10相连。所述的矫直装置10包括:箱体2、两个工作辊3和三角支撑架4,其中:三角支撑架4和箱体2分别设置于机床1上两侧,两个工作辊3分别设置于箱体2内上下两侧,三角支撑架4和卷起装置11设置于机床1的同一侧。所述的卷起装置11包括:框架8、液压缸7、支架6、非传动辊5和平板9,其中:框架8设置于机床1上,液压缸7设置于框架8内底部,平板9设置于液压缸7上并且两端与框架8相连,支架6设置于平板9上,非传动辊5设置于支架6之间并且两端与支架6相连。上述装置工作过程具体如下:通过将板材沿设置于机床1上下的箱体2承重滚道进给,板材在工作辊3之间被拉直且变向弯曲,使其弯曲度降至最低;在压力驱动系统增加压力条件下,通过液压缸7的活塞杆向非传动辊5上施加上升力,使得板材轧制前端在变向弯曲条件下降低弯曲度,改善板材质量。所述的液压缸7共两个,且特征尺寸为40.25×435.17,工艺参数列如表1所示:表1参数数值液压缸的工作压力,mpa16活塞杆最大轴向力,kn20.1辊直径,mm40.25活塞行程,mm435.17液压缸长度,mm580活塞杆直径,mm25在实验室条件下,对板材前端卷曲装置框架进行了最优偏光试验研究,以确定在装置工作状态下出现的应力分布。研究装置的框架是块状封闭式结构,要确定整个框架应力张量。为了用极优-偏光方法确定板材应力状态,用活性材料ed-6制造了模型。在冻结研究模型变形基础上,用极优-偏光方法解决了板材强度所有问题。冻结过程实质包括如下:对材料ed-6在保温箱中慢慢加热到+135℃,研究其模型。最佳的活性材料有双向组织。在冻结条件下,它的非结晶状态转变为新的状态。如果在该状态下,研究模型承受系统力状态,逐渐降低温度到室温,模型出现变形被拍照记录下来。非结晶材料模型恢复到通常弹性状态,仿佛像冻结样。牌号bfw-10冻结模型在保温箱中按照一昼夜规范,而负荷用气动负荷施加。气动负荷单位压力值为7.84×104pa,总的力为26068n。冻结后模型切割成单个局部图。获得的切块加工成极化装置фмв-53。干涉照片示于图5。为了破译条纹密码,确定最佳状态4096mpa×mm/条纹。如图6所示,为针对卷起装置11中的框架8的模型分布状态试验结果,对应选择切割截面平行xyz平面的中间平面,根据该模型得到:名义应力名义应力且(σx-σy)+(σy-σz)+(σz-σx)=0;切向应力切向应力切向应力切向应力其中:σ0为干涉条纹值,αyz为假等倾线参数,mx为观察模型点干涉带序列,tx为切片厚度。根据上述模型得到等效应力为:σm={0.5[(σx-σy)2+(σy-σz)2+(σz-σx)2-6(τxy+τyz+τzx)]}0.5。模型最大负荷处名义应力和切向应力差试验计算结果如表2所示:表2模型上4个点应力计算结果(pa)应力点a×104点b×104点c×104点d×104(σx-σy)-36.26+17.64-17.24+8.13(σy-σz)+42.14-25.48+20.58-9.3(σz-σx)-5.88-7.84-3.33+1.17σm-39.65-22.54-12.7+8.82注:点a、b分布在上横梁;点c、d分布在底座上。由表2可得,最大应力位于上横截面点a,为σm=39.65×104pa;最小应力在底座d点,为σm=8.82×104pa;框架模型应力转化为实际应力即σp=βσm,其中:β为力的模拟系数,β=ph/pm;ph、pm分别为实际力和模型上施力点;σm为模型应力。试验结果确定,框架最大负荷在上横梁a-b截面和框架底座c-d截面,框架与上横梁过渡区域没有出现应力集中,过渡区域半径选择合理。板材前端缺陷及矫正后参数如表3所示,表中:a为缺陷尺寸(从板材上表面到矫正轴距离),mm;l为缺陷长度,mm。表3钛合金板前端缺陷及校正后参数(板厚h=10mm,宽b=2000mm)ala/laa/l效率,%1504000.374500.08078.02004500.446700.08580.03005000.6010900.1181.6从表3可得,校正参数a的变化范围150~300mm,参数l的变化范围400~500mm。矫正后,a参数位于4~10mm,l参数位于50~90mm。因此,矫正率得到大幅提升,由78%提高到81.6%。通过上述装置进行钛合金板材矫直能够显著提高矫直质量,且框架计算方法用于板材前端弯曲矫直装置可行;研究在装置中轴对称零件的平面的应力状态,作用在这些区域的高水平波动应力是确定机架强度和耐久性重要指标。由实验室研究条件计算可得,研究装置框架最大负荷分别位于上横梁和底座垂直轴截面上,可确定框架与上横梁过渡区域没有应力集中。确定钛合金板材前端矫直前缺陷及矫直后的数据参数,可得出矫直的效率由78%提升到81.6%。上述具体实施可由本领域技术人员在不背离本实用新型原理和宗旨的前提下以不同的方式对其进行局部调整,本实用新型的保护范围以权利要求书为准且不由上述具体实施所限,在其范围内的各个实现方案均受本实用新型之约束。当前第1页1 2 3