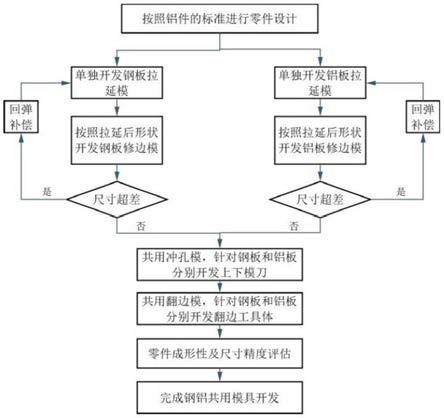
1.本发明涉及零部件制造领域,尤其涉及一种应用于钢、铝材质零件通用的冲压模具设计方法。
背景技术:2.目前,国内各家工业机械整机或零件生产企业对零部件的轻量化需求日益迫切,其中,作为相对轻量金属材质的铝板由于其具有良好的性能和减重效果,已经被广泛应用,尤其在汽车用材中,特别是发动机罩、车门以及翼子板等汽车外部覆盖件上越来越多采用轻量化的铝板来代替钢板。
3.然而,铝板和钢板在力学性能上显然存在有较大的差异,其主要区别在于:
4.1.与传统汽车钢板相比,汽车铝板的断裂延伸率和厚向异性指数均较低,导致其成形性能较差,在冲压过程中容易产生开裂、起皱以及尺寸超差等问题,为此,铝制零件在设计时应该着重考虑铝板材料的成形性,避免外形轮廓的急剧变化,尽可能降低产品的拉伸深度;
5.2.汽车铝板的弯曲性能也较差,对于覆盖件外板零件,其包边圆角半径需要保证大于等于1/2的材料厚度;
6.3.铝板制成的汽车外部覆盖件需要对产品的表面质量、成形充分性和尺寸精度有着较高的要求,为了,如果要将零件从钢质改为铝质,往往需要重新开模,从而给主机厂增加了较大的设备成本。
7.除了上述问题,钢、铝零件的冲压工艺也存在差异,所谓的冲压是靠压力机和模具对板材施加外力,使之产生塑性变形或分离,从而获得所需形状和尺寸的冲压零件的成形加工方法。由于冲压加工生产效率高,成形精度好,材料消耗少,操作方便,易于实现机械化与自动化,因此,成为了汽车零部件的主要生产制造方式。一般汽车零件的主要冲压工序包括拉延、修边冲孔、翻边等。结合上述的钢、铝板的力学性能特点,来简述两种材料冲压各工序工艺上的差异:
8.1.拉延工艺差异:
9.由于铝板的成形性较差,且变形抗力较低,容易发生开裂和起皱等缺陷。因此,铝板拉延模压料面轮廓应避免较大的起伏,尽可能采用单曲率曲面;铝板拉延模的工艺补充面也应降低立壁倾角,并适当放大凸凹模圆角,以提高模具内材料的流动性,防止出现局部变形量过大,导致开裂;
10.2.修边冲孔工艺差异:
11.铝合金板在修边和冲孔等冲裁过程中非常容易产生碎屑、毛刺等问题,碎屑附着在模具表面,在冲压成形过程中导致零件表面出现划伤、麻点、凹坑等缺陷,影响冲压件的表面质量和生产效率。为此,在铝板的冲裁工艺设计时需要通过有效的方法优化冲裁角度、等工艺参数,已达到无毛刺无铝屑的冲裁加工效果;
12.3.回弹补偿工艺差异:
13.铝的弹性模量是钢的1/3,而屈服强度一般是普通钢板的2/3,因此,铝板经过拉延修边后,其最大回弹量往往是钢的两倍以上。为了保证零件最终的成形精度,必须对冲压模面进行回弹补偿。回弹补偿的策略一般是对拉延模模面进行反向补偿,并对修边模的压料面进行符形处理,从而保证零件在进入后工序之前,将尺寸偏差控制在合理的范围内;
14.4.翻边工艺差异:
15.对于车门、发动机罩等需要通过包边工序来实现连接的零件,其外板必须要进行翻边处理。由于铝板弯曲性能较差,因此,上弯刀圆角半径、下模圆角半径、翻边间隙等工艺参数的设置均与钢板翻边模有一定的差异。此外,为了降低翻边后边部回弹的影响,铝板翻边模的压料面压着尺寸也要进行调整。
16.为了解决上述问题,现有技术也做了不少尝试:
17.申请号为201510237918.2的专利提供了一种基于变间隙压边的铝板冲压成形工艺优化方法。同现有技术相比,通过建立各压边块间隙与成形质量之间的数学模型,结合试验设计方法、响应面技术和多目标优化方法得到最优压边块间隙组合,改善铝板冲压成形过程中的起皱和拉裂,为铝板的冲压成形工艺优化提供了一种具有创新性和可行性的方法。
18.申请号为201810387228.9的发明专利提出了一种钢铝混合热冲压自动化生产线。该生产线包括依次布设的上料台、多层加热炉、压力机组、激光切边冲孔装置、传送带和控制系统,本发明能实现热冲压件的钢铝混线生产,减少生产线的布置,大幅降低生产成本。
19.申请号为201611192189.4的发明专利“一种控制铝合金冲压件回弹的模具结构”,通过凸包改变车体包边r角台阶处的形状,令铝板冲压过程中的回弹应力被部分分解,可有效的控制铝板成型后的回弹,提高产品品质。
20.而经过对上述公开专利的分析得知,现有技术主要是通过改进并优化现有冲压工艺来实现汽车铝板冲压零件的可靠生产,或是通过改进现有钢制产线来实现钢铝的并线生产,没有解决钢板和铝板的冲压模具本身的问题,同时也无法同时适用于钢板和铝板的两种不同零件的制造。
技术实现要素:21.为了解决上述问题,本发明提供了一种钢、铝零件通用的冲压模具设计方法,通过该方法设计出的冲压模具可以实现在一套冲压模具上完成钢板和铝板的冲压成形,并同时保证冲压后的零件满足无开裂、尺寸无超差等质量要求。
22.本发明的一种钢、铝零件通用的冲压模具设计方法,其具体步骤如下所述:
23.一种钢、铝零件通用的冲压模具设计方法,其具体步骤如下:
24.1)零件基础设计工序:
25.本步骤中,按照铝件的标准进行零件设计,避免外形轮廓的急剧变化,增大特征圆角半径至5mm以上,降低产品的拉伸深度至120mm以内,避免零件成形时产生质量缺陷;
26.2)拉延模设计工序:
27.拉延成形为冲压成形的第一工序,本步骤中,按照钢、铝塑性及回弹特性差异,分别设计钢板拉延模和铝板拉延模两套模具,其中,钢板拉延模工艺补充面立壁倾角为5
°
~15
°
,凸凹模圆角半径大于2mm,而相较于钢板拉延模,铝板拉延模的工艺补充面立壁倾角
20
°
~40
°
,凸凹模圆角半径大于5mm,并采用过拉延的方式,从而保证铝板零件的成形性和拉延充分性,并控制拉延后的零件回弹;
28.3)修边模设计工序:
29.模具修边为冲压成形的第二工序,本步骤中,按照钢板和铝板拉延后的形状差异,分别设计钢板修边模和铝板修边模两套模具;
30.4)回弹补偿工序:
31.本步骤中,基于钢板和铝板零件修边后的形状偏差,进行步骤2)中的拉延模具的回弹补偿,同时修改修边模的模面形状以达到符形的效果,直至零件在修边后满足尺寸精度偏差在
±
1mm以内;
32.5)后续工序设计:
33.上述步骤1)~4)完成后进行后续工序设计,本步骤的具体设计要点如下:
34.5.1)修边冲孔模具设计工序:
35.按照钢、铝材质差异,分别针对钢板和铝板设置不同的上模冲头,该上模冲头对置于下模上的板料进行修边冲孔,工作时上模冲头需要根据板料进行更换,模具的其余部分共用,其中,钢板的冲裁双边间隙设置为料厚的9%~12%,而铝板的冲裁双边间隙设置为料厚的15%~18%;
36.5.2)翻边模具设计工序:
37.按照钢、铝弯曲性能差异,分别针对钢板和铝板设置不同的翻边上模刀,该翻边上模刀与上模座连接,对被压料模压制在翻边下模体上的冲压材料进行翻边,工作时翻边上模刀需要根据不同的冲压材料进行更换,模具其余部分共用,其中,翻边参数具体如下:
38.翻边弯缘角度设计为0.5~1mm,翻边区域的压着面宽度大于50mm,钢板的翻边间隙设计为料厚的80%~95%,上模翻边圆角大于3mm,而铝板的翻边间隙设计为料厚的100%~110%,上模翻边圆角则大于6mm;
39.6)上述步骤1)~5)完成后即进入最后的成形性及尺寸精度评估阶段,具体如下:
40.对冲压后零件的成形性和尺寸精度进行评估,无开裂现象且形状尺寸精度满足预定的使用要求,若出现缺陷需对设计的模具进行调整,直至冲压后的零件满足生产质量要求。
41.使用本发明的一种钢、铝零件通用的冲压模具设计方法获得了如下有益效果:
42.(1)本发明的一种钢、铝零件通用的冲压模具设计方法设计出的模具可以同时实现钢板和铝板的冲压成形;
43.(2)本发明的一种钢、铝零件通用的冲压模具设计方法基于钢板和铝板的性能差异,能够保证冲压后的零件满足无开裂、尺寸无超差等质量要求;
44.(3)本发明的一种钢、铝零件通用的冲压模具设计方法针对某些车型的特定零件,避免分别为汽车钢板和汽车铝板各开一套冲压模具,节省了部分的模具开发费用和开发时间;
45.(4)本发明的一种钢、铝零件通用的冲压模具设计方法结合了钢板和铝板冲压模具的基本特点,易于掌握和实现。
附图说明
46.图1为本发明的一种钢、铝零件通用的冲压模具设计方法的具体流程图;
47.图2为本发明的一种钢、铝零件通用的冲压模具设计方法的步骤5.1)的修边冲孔模具结构图;
48.图3为本发明的一种钢、铝零件通用的冲压模具设计方法的步骤5.2)的翻边模设计
49.图中:a-上模冲头,b-下模,c-板料,d-冲裁双边间隙,1-翻边上模刀,2-上模座,3-压料模,4-翻边下模体,5-冲压材料,r1-上模翻边圆角,r2-翻边弯缘角度,w-压着面宽度,c-翻边间隙。
具体实施方式
50.下面结合附图和实施例对本发明的一种钢、铝零件通用的冲压模具设计方法做进一步的描述。
51.实施例-发动机罩外板钢铝共用冲压模具的设计开发,如图1~图3所示,其具体如下:
52.1.零件设计:
53.按照铝件的标准进行零件设计,外形轮廓无急剧变化,特征圆角半径均在5mm以上,产品的拉伸深度为100mm;
54.2.拉延模设计:
55.拉延为该零件成形的第一工序,针对钢铝塑性及回弹特性差异,单独开发了钢板拉延模和铝板拉延模两套模具,钢板拉延模工艺补充面立壁倾角为10
°
~15
°
,凸凹模圆角半径为5~25mm;铝板拉延模的工艺补充面立壁倾角为25
°
~35
°
,凸凹模圆角半径为10~25mm;钢板和铝板在拉延成形后均未产生开裂缺陷;
56.3.修边模设计:
57.针对钢板和铝板拉延后的形状差异,单独开发了钢板修边模和铝板修边模两套模具。
58.应注意,本实施例为发动机罩外板钢铝共用冲压模具的设计开发,由于其修边模具是分别针对钢板和铝板单独开发的,故未采用步骤5.1)修边冲孔模具设计工序,而是在下述的回弹补偿后进行第一、第二翻边模具设计;
59.4.回弹补偿:
60.钢板拉延模和铝板拉延模均分别进行了一次回弹补偿,经过拉延和修边工序后,钢板零件和铝板零件的尺寸偏差均控制在
±
1mm以内;
61.5.1)第一序翻边模具设计:
62.该工序完成发动机罩前端的侧向翻边以及其余周圈位置的正向翻边,共设计了钢板和铝板两种上模翻边工具体,工作时需要根据冲压材料进行更换,模具其余部分共用,模具结构如图3所示,翻边弯缘角度r2设计为0.5mm,翻边区域的压着面宽度w为80~105mm,钢板的翻边间隙c设计为90%的原始料厚,上模翻边圆角r1设计为4mm;而铝板的翻边间隙设计为100%的料厚,上模翻边圆角设计为6mm;
63.5.2)第二序翻边模具设计:
64.该工序完成发动机罩外板四个角部的侧翻成形,均采用斜锲机构完成,模具设计思路及翻边参数设置与前一序翻边相同;
65.6)冲压成形结果评估:
66.完成上述的冲压成形后,钢制和铝制发罩外板均未发生开裂,形状尺寸精度也满足使用要求,测试结果如表1和表2所示:
67.测试次数编号123平均不合格点数14141514合格点数258258257258总测量点数272272272272合格率(%)95%95%94%95%关键点合格率97%97%97%97%
68.表1钢发罩外板的尺寸精度测试结果
69.测试次数编号123平均不合格点数12121212合格点数60260260258总测量点数272272272272合格率(%)96%96%96%95%关键点合格率100%100%100%100%
70.表2铝发罩外板的尺寸精度测试结果
71.本发明的一种钢、铝零件通用的冲压模具设计方法基于钢铝力学性能差异,从而使得按照该方法设计出的模具能够同时实现钢板和铝板的冲压成形,且能保证冲压后零件无开裂、起皱、尺寸超差等质量缺陷。本发明的一种钢、铝零件通用的冲压模具设计方法可以有效应用于发动机罩、车门、翼子板等汽车覆盖件模具的开发,有效减少生产厂商的开模成本,对于推动汽车轻量化发展有着重要的意义。