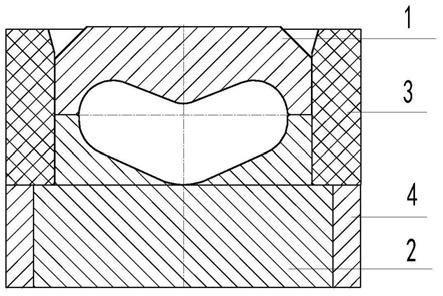
[0001]
本发明属于石油机械设备制造方法技术领域,具体涉及一种石油钻机提升系统用游车提环胎模锻锻造方法。
背景技术:[0002]
游车提环是石油钻机提升系统中的关键件,在钻机提升过程中承受主要重量,设计要求高,力学性能要求严格,一般为高合金钢锻件。
[0003]
以yc-450游车提环为例,其设计要求为:调质处理169-302hbw,力学性能:r
m
≥785mpa,r
el
≥590mpa,a4≥17%,z≥45%,三个试样的平均冲击韧性值kv8≥42j(-20℃),单个值不低于32j(-20℃)。锻件经磁粉探伤,其质量符合api spec 8c《钻机和采油提升设备》psl2级要求。
[0004]
游车提环的形状如一个开口较大的v字形。自由锻工艺流程是先锻成方形块类锻件,再线切割外形,切割掉的部分一般要占到锻件总重的三分之一左右,材料浪费严重;而且线切割过程会切断锻件的金属流线,降低其力学性能,影响使用寿命,线切割费用较高。
技术实现要素:[0005]
本发明的目的在于提供一种石油钻机提升系统用游车提环胎模锻锻造方法,降低了生产成本,得到的锻件力学性能优良。
[0006]
本发明所采用的技术方案是:一种石油钻机提升系统用游车提环胎模锻锻造方法,包括以下步骤:
[0007]
步骤1、根据锻件形状尺寸设计胎模锻模具;
[0008]
步骤2、加热坯料到始锻温度,保温后进行自由锻镦粗并滚圆;
[0009]
步骤3、将步骤2中得到的坯料置于步骤1得到的模具内锻造,出模后堆冷、正火处理即得。
[0010]
本发明的特点还在于,
[0011]
步骤1中设计的胎模锻模具包括直壁套模,直壁套模的中心开设有上下贯通且横截面为矩形的通孔,直壁套模的通孔内配合套设有上下对应的立方形上模和倒t形下模,上模的底部和下模的顶部均凹陷形成与锻件相适应的形状,下模的竖直段位于直壁套模的通孔内,下模的水平段位于直壁套模的下方且外周套设有座套。
[0012]
坯料为圆饼形,坯料的厚度尺寸比锻件的厚度尺寸小5mm。
[0013]
步骤2中的始锻温度为1180-1200℃,保温时长为2h。
[0014]
步骤2中自由锻镦粗的高度为180mm。
[0015]
步骤3具体包括以下步骤:
[0016]
步骤3.1、预热步骤1得到的模具;
[0017]
步骤3.2、将下模套于座套内,直壁套模自上而下套在下模上,将步骤2中得到的坯料置于下模的顶部凹陷内,之后在直壁套模的通孔内套上上模;
[0018]
步骤3.3、通过压机在上模的顶部加压,使坯料在模具内焖型得到锻件;
[0019]
步骤3.4、焖型完成后,操作机加持直壁套模上提,下模在自重下自动脱模,移除下模后,将上模、锻件及直壁套模放在座套上,在上模顶部加圆钢向下顶出锻件和上模;
[0020]
步骤3.5、同批次锻件锻成后堆冷,到最后一件锻完,所有锻件直接装炉,炉温880-890℃,保温2小时,出炉后空冷到室温得到终锻件。
[0021]
步骤3.1中的预热温度为200-300℃。
[0022]
本发明的有益效果是:本发明一种石油钻机提升系统用游车提环胎模锻锻造方法,锻造过程中借助胎模限制金属流向,终锻件外形接近零件,锻件加工余量少,节约原材料,锻造完成后,下模在自重下自动脱模,无需翻转胎模和顶出装置,操作简便,生产效率高,安全可靠;所成锻件内部金属流线符合零件形状,后续机加工不切断金属流线,力学性能优良,能更好的满足游车提环的使用要求。
附图说明
[0023]
图1是本发明一种石油钻机提升系统用游车提环胎模锻锻造方法中模具的剖视图;
[0024]
图2是本发明一种石油钻机提升系统用游车提环胎模锻锻造方法中上模的正视图;
[0025]
图3是本发明一种石油钻机提升系统用游车提环胎模锻锻造方法中上模的侧视剖面图;
[0026]
图4是本发明一种石油钻机提升系统用游车提环胎模锻锻造方法中下模的正视图;
[0027]
图5是本发明一种石油钻机提升系统用游车提环胎模锻锻造方法中下模的侧视图;
[0028]
图6是本发明一种石油钻机提升系统用游车提环胎模锻锻造方法中直壁套模的正视剖面图;
[0029]
图7是本发明一种石油钻机提升系统用游车提环胎模锻锻造方法中直壁套模的侧视剖面图;
[0030]
图8是本发明一种石油钻机提升系统用游车提环胎模锻锻造方法中直壁套模的俯视图;
[0031]
图9是本发明一种石油钻机提升系统用游车提环胎模锻锻造方法中座套的正视剖面图;
[0032]
图10是本发明一种石油钻机提升系统用游车提环胎模锻锻造方法得到的游车提环锻件正视图;
[0033]
图11是本发明一种石油钻机提升系统用游车提环胎模锻锻造方法得到的游车提环锻件侧视图;
[0034]
图12是本发明一种石油钻机提升系统用游车提环胎模锻锻造方法的锻造流程图。
[0035]
图中,1.上模,2.下模,3.直壁套模,4.座套,5.锻件,6.饼坯,7.圆钢。
具体实施方式
[0036]
下面结合附图以及具体实施方式对本发明进行详细说明。
[0037]
本发明提供了一种石油钻机提升系统用游车提环胎模锻锻造方法,如图12所示,包括以下步骤:
[0038]
步骤1、根据锻件形状尺寸设计胎模锻模具,如图1至图9所示,包括矩形块状的直壁套模3,直壁套模3的中心开设有上下贯通且横截面为矩形的通孔,直壁套模3的通孔内配合套设有上下对应的立方形上模1和倒t形下模2,上模1的底部和下模2的顶部均凹陷形成与锻件5相适应的形状,下模2的竖直段位于直壁套模3的通孔内,下模2的水平段位于直壁套模3的下方且外周套设有座套4,座套4也为一个矩形块,中间有矩形通孔,下模2可以套在其中,座套4的外矩形尺寸与直壁套模1一样,座套4还起到锻件脱模时的垫模作用;
[0039]
同一系列的游车提环,厚度相同,外形尺寸有差异,上模1和下模2的模具,根据不同规格的提环尺寸而相应制作,组合在直壁套模3和座套4内,锻出不同尺寸的锻件。
[0040]
步骤2、加热坯料到始锻温度,保温后进行自由锻镦粗并滚圆,大锻造比使坯料内部充分锻透,可以有效锻合原材料中的孔洞、缩松等缺陷;
[0041]
步骤3、将步骤2中得到的坯料置于步骤1得到的模具内锻造,出模后堆冷、正火处理即得,具体包括以下步骤:
[0042]
步骤3.1、预热步骤1得到的模具;
[0043]
步骤3.2、将下模2套于座套4内,直壁套模3自上而下套在下模2上,将步骤2中得到的坯料置于下模2的顶部凹陷内,利用圆饼型坯料的特点,使其在下模2内利用自重滚动自动定位,之后在直壁套模3的通孔内套上上模1;
[0044]
步骤3.3、通过压机在上模1的顶部加压,在上下模和直壁套模3的三向压应力下焖型得到锻件5;
[0045]
步骤3.4、焖型完成后,操作机加持直壁套模3上提,下模2在自重下自动脱模,移除下模2后,将上模1、锻件及直壁套模3放在座套4上,在上模1顶部加圆钢向下顶出锻件和上模1;
[0046]
步骤3.5、锻件出模后堆冷、正火处理得到终锻件5,如图10和图11所示。
[0047]
通过上述方式,本发明一种石油钻机提升系统用游车提环胎模锻锻造方法可以仿型锻造出接近零件的锻件毛坯,减少锻件加工余量,加工过程中保证锻件完整的金属流线,提高锻件机械性能和生产效率;本发明的模具设计可以提高模具的通用性,同系列的提环只需要更换上下模具即可在同一套套模内锻造而成,节省模具费用,降低维护成本。
[0048]
本发明与已有技术相比较具有以下优点:
[0049]
1)胎模结构简单,设备工装投入小,操作简单易行,锻造过程短,锻件出模顺利,生产效率高,锻件形状接近零件,加工余量较自由锻大大减少。
[0050]
2)游车提环的锻件毛坯在制坯过程中通过大锻比的墩粗,可以有效锻合原材料中的孔洞、缩松等缺陷。
[0051]
3)锻件的制坯形式可以实现毛坯在模具内自动定位,锻造过程中金属的流动过程符合模具填充要求,坯料在上模1的压力作用下先填充上模1圆弧部分,再向两侧流动,最后合模时填充最外侧的圆弧部分,金属流动过程先向下,再向两侧,不发生回流,符合金属流动规律,流动阻力小,所需锻造载荷小,利于充满模型;锻件内部金属流线分布符合锻件形
状,后续机加工不切断金属流线,锻件力学性能优良。
[0052]
4)模具通用性高,模具易维护,可以实现同一系列的游车提环在同一套模内锻造。
[0053]
实施例
[0054]
1.以yc450游车提环为例,根据零件图制定锻件图,设计胎模,计算锻件重量,下料重量,下料规格,确定锻造始锻、终锻温度,锻造火次,制坯厚度,锻造变形过程,锻造设备及锻后冷却等,编制锻造工艺。
[0055]
2.根据锻件形状尺寸,计算锻件重量为390kg,锻造2火次,考虑火耗,下料重量为410kg,下料尺寸约为φ400
×
415。
[0056]
3.加热,按照加热规范加热到1180-1200℃的始锻温度,保温2小时。
[0057]
4.自由锻镦粗制坯,坯料为圆饼形,坯料的厚度尺寸比锻件的厚度尺寸小5mm,坯料的外径为下料圆钢镦粗后的自由尺寸,yc450游车提环的坯料尺寸约为将坯料自由墩粗到180mm高,滚圆,外径为自由尺寸。
[0058]
5.模具预热到200-300℃,按既定的顺序组合,将下模2套在座套4的矩形内孔中,直壁套模3自上而下套在下模2上,并与座套4对齐,放入加热到始锻温度的饼坯6,在直壁套模3上套上上模1。
[0059]
6.压机在上模1上加压,使锻件在胎模内焖型。
[0060]
7.焖型完成后,操作机加持直壁套模3上提,下模2在自重下自动脱模,移除下模2后,将上模1和锻件及直壁套模3放在座套4上,在上模以上加圆钢7顶出锻件和上模1,锻造完成。
[0061]
8.同批次(同一冶炼炉号)锻件锻成后堆冷,到最后一件锻完,所有锻件直接装炉(炉温880-890℃),保温2小时,出炉后空冷到室温。