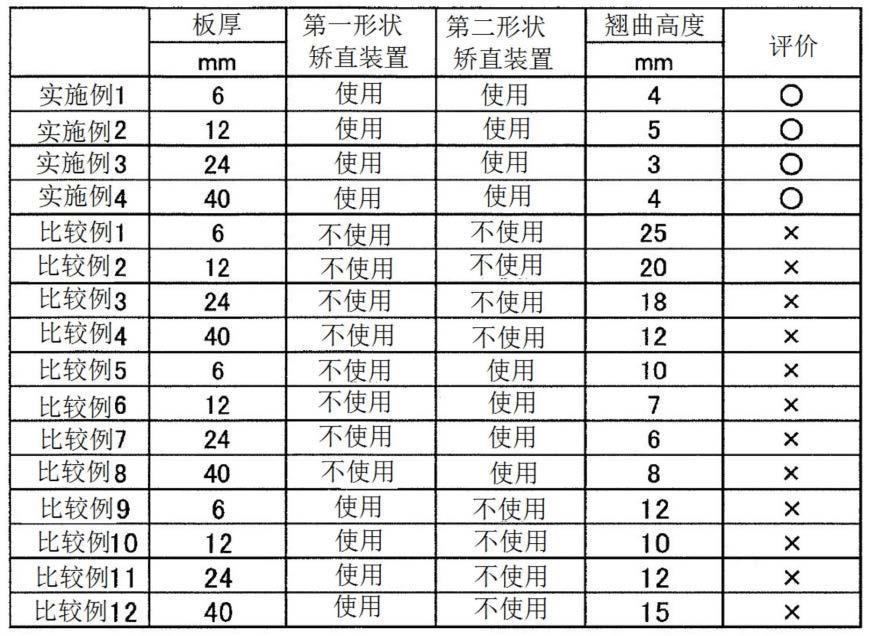
1.本发明涉及一种钢板的制造设备及制造方法。
背景技术:2.在厚钢板等的钢板的制造中,为了调整强度等机械特性,大多实施从高温开始的冷却。冷却大致分为在线型的水冷方法和离线型的水冷方法。在线型的水冷方法中,使用在线配置的水冷装置,进行热轧后的钢板的水冷。离线型的水冷方法中,将轧制后的材料暂时冷却至室温,在离线配置的热处理炉中再次进行加热和水冷。从能量成本的观点考虑,在线型的水冷方法很有利,但是在轧制时容易产生钢板的翘曲等,因此无法在轧制机的附近配置冷却装置。其结果是在轧制后输送到冷却装置为止的期间温度下降,因此存在无法以适当的温度进行水冷的问题。
3.另一方面,离线型的水冷方法由于在加热炉的出口侧配置冷却装置,能够从与加热温度几乎同等的温度开始淬火,因此对机械特性的调整较为有利。
4.一般而言,经热轧的钢板由于轧制后的钢板的温度分布、形状或者表面状态的不同而容易在冷却中产生温度不均。并且,钢板的温度不均也可能由于冷却装置的性能导致。并且,如果产生钢板的温度不均,则在冷却后产生钢板的变形、残留应力、材质的偏差等。作为该对策,开发出了能够进行各种均匀的冷却的冷却装置。然而,已经开发的方法仅改善冷却装置,特别是并未完全实现冷却后的钢板的平坦化。冷却后的钢板的形状不良是导致生产线的通板障碍等操作上的故障的原因,在后续工序中需要加压、利用矫直装置进行的精整处理,因此成本也变高。
5.钢板的温度不均的原因包括冷却喷嘴的设计和轧制时的钢板的形状。根据冷却喷嘴的设计,产生上下表面的温度偏差、宽度方向的温度不均匀等。另一方面,如果轧制时的钢板的形状变差,则冷却水在钢板上不均衡地流动,冷却能力根据场所变化,导致产生温度不均。
6.这里,关于抑制上下表面的温度偏差、宽度方向的均匀性等由冷却喷嘴引起的温度不均的方法,已知有许多技术。另一方面,关于抑制以在轧制时产生的形状不良作为起点产生的温度不均的方法,几乎没有很多技术,作为对应的技术,已知有在加速冷却装置前实施形状矫直,使形状平坦化确保冷却时的均匀性的方法(专利文献1、2)。专利文献1、2中,目的在于利用第一形状矫直装置将钢板的形状矫直刀通过冷却装置的除水辊充分除水的程度。
7.现有技术文献
8.专利文献
9.专利文献1:日本特开2002-11515号公报
10.专利文献2:日本特开2005-74480号公报
技术实现要素:11.然而,近年来,在实际运用将线型的矫直装置设置在冷却装置前这样的专利文献1、2的技术的生产线逐渐增加。然而,在热轧中,由于轧制中的去氧化皮、用于温度调整的水冷等,原则上温度偏差大,在板面内产生的温度偏差成为热收缩量差。因此,即使通过加热进行了形状矫直,也存在温度下降时再次变形的问题。
12.并且,专利文献1、2中提出了在利用第一形状矫直装置进行矫直后加速冷却,接着利用第二形状矫直装置进行最终矫直的在线处理。然而,无论单独采用任何一种技术,均无法对之前论述的上下表面的温度偏差、宽度方向的均匀性等由冷却喷嘴导致的温度不均的产生和由其引起的冷却应变得到很好的效果。
13.以往的离线型的热处理设备按照加热炉、淬火装置以及形状矫直装置依次进行配置。淬火装置冷却至100℃以下,即使无法确保冷却的均匀性,也可冷却至靠近冷却水的水温的低温度,因此钢板的最终的冷却停止温度一定。因此,没有考虑到冷却的均匀性。近年来从提高品质的观点出发,在淬火时板面内减少冷却速度的偏差这样的需求不断提高,通过能够确保淬火前的温度均匀性的离线热处理进行均匀冷却变得重要。另外,即使利用离线热处理,也可以在100℃以上等比室温更高的温度下结束冷却。在该情况下如果冷却不均匀,则冷却结束后的钢板温度也有偏差,因此不仅无法确保规定的品质,而且由于钢板温度的面内的热膨胀差,导致钢板产生应变。
14.本发明鉴于这样的情况而完成,课题在于提供一种在钢板的热处理时,能够进行更均匀的冷却,能够制造平坦、均质的钢板的钢板的制造设备及制造方法。
15.根据本发明的一个方式,提供一种钢板的制造设备,其是对钢板进行热处理的钢板的制造设备,具备:对100℃以下的上述钢板进行加热的加热炉;将加热的上述钢板平坦地矫直的第一形状矫直装置;对被矫直的上述钢板进行淬火的淬火装置以及将经淬火的上述钢板平坦地矫直的第二形状矫直装置。
16.根据本发明的一个方式,提供一种钢板的制造方法,是对钢板进行热处理的钢板的制造方法,具备:对100℃以下的上述钢板进行加热的加热工序;在上述加热工序后将上述钢板平坦地进行矫直的第一矫直工序;在上述第一矫直工序后对上述钢板进行淬火的淬火工序;以及在上述淬火工序后将上述钢板平坦地矫直的第二矫直工序。
17.根据本发明的一个方式,提供在钢板的热处理时能够进行更均匀的冷却,能够制造平坦、均质的钢板的钢板的制造设备及制造方法。
附图说明
18.图1是本发明的一个实施方式涉及的钢板的制造设备的热处理设备的概略构成图。
19.图2是表示第一形状矫直装置和淬火装置的详细的构成的立体图。
具体实施方式
20.以下,参照附图对本发明的实施方式进行说明。以下所示的实施方式例示了用于将本发明的技术思想具体化的装置、方法,本发明的技术思想不是将构成部件的材质、形状、结构、配置等限定为下述的实施方式。另外,附图是示意性的。因此,需要说明的是厚度
与平面尺寸的关系、比率等与实际是不同的,附图相互间也包括彼此尺寸的关系、比率不同的部分。
21.(钢板的制造设备)
22.图1是作为本发明的一个实施方式涉及的钢板的制造设备的厚钢板2的热处理设备1的概略构成,图2分别示出了本实施方式的第一形状矫直装置4和淬火装置5的详细的构成。在本实施方式中,为了确保均质的温度和形状,着眼于通过不与轧制线直接连接的离线型的热处理设备来调整材料的机械特性,热处理设备1不与轧制线直接连接。热处理设备1是对作为钢板的厚钢板2进行热处理的设备,该设备具备加热炉3、第一形状矫直装置4、淬火装置5和第二形状矫直装置6。另外,如图1所示,在热处理设备1中,从厚钢板2的输送方向的上游侧依次配设加热炉3、第一形状矫直装置4、淬火装置5和第二形状矫直装置6。并且,在加热炉3、第一形状矫直装置4、淬火装置5和第二形状矫直装置6的各装置间,分别设置有输送厚钢板2的输送辊(未图示)。
23.加热炉3将热轧结束的100℃以下的厚钢板2加热到奥氏体温度区域。应予说明,厚钢板2是板厚为4.0mm以上的钢板。
24.第一形状矫直装置4是将利用加热炉3加热的厚钢板2平坦地进行矫直的装置,设置于加热炉3与淬火装置5之间。第一形状矫直装置4可以使用压下型的表皮光轧矫直装置或者反复弯曲型的辊式矫直机矫直装置。另外,出于后述的原因,优选第一形状矫直装置4使用辊式矫直机矫直装置。并且,出于后述的原因,在使用辊式矫直机矫直装置的情况下,更优选进一步设置可修正厚钢板2的前端尾端部的翘曲的加压型的矫直机构等。
25.这里,从加热炉3取出厚钢板2后到达第一形状矫直装置4为止,产了厚钢板2的温度下降。如果该温度下降越小,则厚钢板2的变形阻力的增加变小,能够以小的矫直力进行形状矫直。因此,从加热炉3到进入到第一形状矫直装置4为止的距离优选为4m以下。并且,为了缩短了从加热炉3到淬火装置5为止的输送时间,第一形状矫直装置4优选设置空间小的小型的装置。另外,为了进行加热期间的变形阻力比较低的厚钢板2的矫直,第一形状矫直装置4优选使用承载能力比第二形状矫直装置6低的形状矫直装置。第一形状矫直装置4至少为500吨,优选为3000吨左右的承载能力即可。应予说明,在本实施方式中,吨表示公吨(metric ton)。
26.淬火装置5是通过水冷对利用第一形状矫直装置4进行了形状矫直的厚钢板2进行淬火的装置。如图2所示,淬火装置5作为对形状矫直后的厚钢板2进行快速冷却的装置,具有上侧的冷却喷嘴51和下侧的冷却喷嘴52。上侧的冷却喷嘴51和下侧的冷却喷嘴52分别相对于输送线在上下方向呈对地在厚钢板2的宽度方向设置多个,并且沿着厚钢板2的输送方向以规定的间距并列配置多个部位。从上侧的冷却喷嘴51和下侧的冷却喷嘴52的各冷却喷嘴,朝向厚钢板2喷射冷却水53。另外,在淬火装置5,可以在上侧的冷却喷嘴51和下侧的冷却喷嘴52的前后分别设置约束辊50。通过设置约束辊50,即使在厚钢板2产生因冷却不均等导致的形变应变,也能够一定程度地约束厚钢板2,因此能够防止面外变形。
27.第二形状矫直装置6是将利用淬火装置5进行了淬火的厚钢板2平坦地进行矫直的装置,设置于淬火装置5的出口侧(厚钢板2的输送方向的下游侧)。第二形状矫直装置6可以使用压下型的表皮光轧矫直装置、反复弯曲型的辊式矫直机矫直装置或者加压型的矫直装置。另外,从与第一形状矫直装置4相同的原因考虑,优选第二形状矫直装置6使用辊式矫直
机矫直装置。并且,从与第一形状矫直装置4相同的原因考虑,在使用辊式矫直机矫直装置的情况下,更优选进一步设置可修正厚钢板2的前端尾端部的翘曲的加压型的矫直机构等。另外,第二形状矫直装置6从实施室温附近的厚钢板2的形状矫直方面考虑,优选矫直反作用力高,至少优选具有2000tоn以上的承载能力。
28.(厚钢板的制造方法)
29.在本实施方式所涉及的厚钢板的制造方法中,首先,将铸片等作为材料,通过与热处理设备1不同的热轧线(未图示)进行热轧,制造规定的厚度(例如30mm)和宽度(例如2000mm)的厚钢板2。接着,被热轧的厚钢板2在冷却到室温后,通过表面氧化皮除去装置(未图示)除去氧化皮。
30.并且,将除去了氧化皮的厚钢板2装入到加热炉3,加热到奥氏体温度区域(例如910℃左右)(加热工序)。
31.其后,从加热炉3取出厚钢板2,通过设置于加热炉3的出口侧的多个台辊(未图示)输送到第一形状矫直装置4,利用第一形状矫直装置4平坦地进行矫直(平坦化)(第一矫直工序)。
32.这里,以下说明将在淬火装置5前(厚钢板2的输送方向上流侧)设置第一形状矫直装置4的理由。厚钢板2如上述那样利用与热处理设备1不同的热轧线预先热轧成规定的厚度和宽度。此时,在轧制中的厚钢板2具有温度偏差的情况下,冷却至室温的过程中的热收缩的程度根据厚钢板2的部分而不同,因此冷却后产生形状不良。在热处理设备1中,厚钢板2在产生了形状不良的状态下插入到加热炉3,因此即使被加热炉3均匀加热,也会残存形状不良。即使将这样的厚钢板2从加热炉3取出利用淬火装置5进行热处理,形状不良也不会消除,反而冷却水的处理不均匀,从而促进了温度的不均匀。因此,通过利用确保均匀地加热的加热炉3进行加热后,利用第一形状矫直装置4使厚钢板2平坦化,利用淬火装置5进行冷却,能够制造平坦度高的厚钢板2。也就是说,为了得到本发明的效果,需要使进入到淬火装置5前的厚钢板2的形状(初始形状)平坦化。
33.另外,在厚钢板2的前端部产生了翘曲的情况下,存在淬火装置5的喷嘴等与厚钢板2发生碰撞的风险。因此,与对在厚钢板2的前端尾端部产生的长边方向的翘曲的矫直能力低的表皮光轧矫直装置相比,第一形状矫直装置4优选为能够进行反复弯曲加工的辊式矫直机矫直装置。辊式矫直机矫直装置是利用多个辊(例如上面4根、下面3根)进行反复弯曲的矫直机,在辊间的间距部分的距离,矫直效果较低。因此,在使用辊式矫直机矫直装置的情况下,更优选进一步设置能够修正厚钢板2的前端尾端部的翘曲的加压型的矫直机构等。
34.并且,利用第一形状矫直装置4进行形状矫直时的厚钢板2的温度优选为从厚钢板2的奥氏体相变成铁素体的温度ar3温度
±
150℃的范围。通过设为这样的温度,能够充分降低厚钢板2的屈服应力,能够减小形状矫直时的反作用力。
35.第一矫直工序后,利用淬火装置5对厚钢板2进行淬火(淬火工序)。
36.淬火工序后,利用第二形状矫直装置6对厚钢板2进行矫直(第二矫直工序)。对于利用淬火装置5进行的淬火(冷却),不易将从上侧的冷却喷嘴51和下侧的冷却喷嘴52喷射的冷却水53的宽度方向上的流量管理成完全一致。因此,由于因淬火时的温度不均,可能会产生轻微的翘曲,需要利用第二形状矫直装置6进一步对厚钢板2进行矫直。另外,在利用第
二形状矫直装置6进行矫直时,优选厚钢板2的温度为100℃以下。
37.<变形例>
38.以上,参照特定的实施方式说明了本发明,但并不是通过这些说明限定发明。通过参照本发明的说明,对于本领技术人员而言,包括公开的实施方式和各种变形例的本发明的其它的实施方式也是显而易见的。因此,应当理解在专利权利要求记载的发明的实施方式中,涵盖了单独或者组合包括本说明书记载的这些变形例的实施方式。
39.例如,上述实施方式中,虽然记载了钢板具有4.0mm以上的板厚的厚钢板2,但本发明并不限于上述的例子。钢板的板厚也可以小于4.0mm。应予说明,本发明适于板厚为4.0mm以上的钢板,更适于板厚6.0mm以上的钢板。
40.<实施方式的效果>
41.(1)本发明的一个方式所涉及的钢板(例如厚钢板2)的制造设备(热处理设备1)是对钢板进行热处理的钢板的制造设备,该设备具备:加热100℃以下的钢板的加热炉3;将加热的钢板平坦地矫直的第一形状矫直装置4;对被矫直的钢板进行淬火的淬火装置5;以及将经淬火的钢板平坦地矫直的第二形状矫直装置6。
42.根据上述(1)的构成,通过利用第一形状矫直装置4使钢板平坦化,从而能够使淬火时的冷却均匀。因此,能够使钢板平坦且均质。另外,通过在淬火后利用第二形状矫直装置6使钢板平坦化,从而即使在淬火装置5的冷却产生不均的情况下,也能够使最终制造的钢板平坦。
43.(2)在上述(1)的构成中,第一形状矫直装置4的承载能力比第二形状矫直装置6的承载能力低。
44.根据上述(2)的构成,可以根据因钢板的温度不均而产生的变形阻力的不同来优化承载能力,由于第一形状矫直装置4不使用高承载能力的矫直装置,因此初始设备导入费用低。
45.(3)在上述(1)或(2)的构成中,在利用第一形状矫直装置4进行矫直时,钢板的温度为ar3温度
±
150℃的范围。
46.根据上述(3)的构成,钢板的屈服应力足够低,能够降低形状矫直时的反作用力。
47.(4)在上述(1)~(3)中任一构成中,在利用第二形状矫直装置6进行矫直时,钢板的温度为100℃以下。
48.根据上述(4)的构成,矫直温度几乎是室温,矫直后不会产生因进一步的温度下降导致的热收缩所引起的再变形,因此能够得到良好的形状。
49.(5)在上述(1)~(4)中任一个构成中,第一形状矫直装置4和第二形状矫直装置6是辊式矫直机矫直装置。
50.根据上述(5)的构成,能够矫直钢板的前端尾端部的翘曲。因此,不仅能够抑制钢板本身的翘曲,还能够防止淬火时与构成淬火装置5的冷却喷嘴等的设备的接触。
51.(6)在上述(1)~(5)中任一个构成中,淬火装置通过水冷对钢板进行淬火。
52.(7)本发明的一个方式所涉及的钢板的制造方法是对钢板进行热处理的钢板的制造方法,该制造方法具备:对100℃以下的钢板2进行加热的加热工序;加热工序后将钢板平坦地矫直的第一矫直工序;第一矫直工序后对钢板进行淬火的淬火工序;以及淬火工序后将钢板平坦地矫直的第二矫直工序。
53.(8)在上述(7)的构成中,第一矫直工序中,矫直时的钢板的温度为ar3温度
±
150℃的范围。
54.(9)在上述(7)或(8)的构成中,在第二矫直工序中,钢板的温度为100℃以下。
55.根据上述(7)~(9)的构成,可得到与上述(1)、(3)、(4)的构成相同的效果。
56.实施例
57.对于本发明人等实施的实施例进行说明。实施例中,在图1所示的热处理设备1中,将预先通过喷砂加工除去了氧化皮的室温状态的厚钢板2(板厚6mm、12mm、25mm、40mm
×
板宽度3500mm
×
板长7m)用加热炉3在氮气氛下加热至900℃。接着,取出加热的厚钢板2,利用第一形状矫直装置4(辊式矫直机型)矫直厚钢板2,利用淬火装置5淬火至100℃以下。然后,将进行了淬火的厚钢板2利用第二形状矫直装置6再次进行形状矫直。淬火装置5使用喷雾喷嘴作为冷却喷嘴51,52。应予说明,该材料的ar3温度为800℃,从加热炉3取出利用第一形状矫直装置4进行矫直时的厚钢板2的温度约为860℃。
58.实施例中,调查了通过上述的设备配置实施厚钢板2的热处理时的钢板形状。调查中,在定盘上放置厚钢板2,测定从以定盘面作为基准的厚钢板2的最大高度减去板厚得到的量(称为翘曲量),其结果如表1的实施例1~4所示。应予说明,厚钢板2的翘曲量的允许值为5mm以下。对于板厚6mm、12mm、25mm、40mm的厚钢板2,全部翘曲量实现5mm以下为良好的形状(评价:
○
)。
59.作为比较例,第一形状矫直装置4和第二形状矫直装置6都不使用的条件(比较例1~4)、不使用第一形状矫直装置4仅使用第二形状矫直装置6进行矫直的条件(比较例5~8)、仅使用第一形状矫直装置4进行矫直而不使用第二形状矫直装置6的条件(比较例9~12)下进行了热处理。然后,对进行了热处理的厚钢板2与实施例相同地调查了钢板形状。应予说明,除了上述的条件以外,还在与实施例相同的条件下进行热处理。如表1所示,在比较例1~12中,任意条件下翘曲量均大于5mm,作为制品无法得到充分的平坦度(评价:
×
)。
60.[表1]
[0061][0062]
符号说明
[0063]
1 热处理设备
[0064]
2 厚钢板
[0065]
3 加热炉
[0066]
4 第一形状矫直装置
[0067]
5 淬火装置
[0068]
50 约束辊
[0069]
51 上侧的冷却喷嘴
[0070]
52 下侧的冷却喷嘴
[0071]
53 冷却水
[0072]
6 第二形状矫直装置