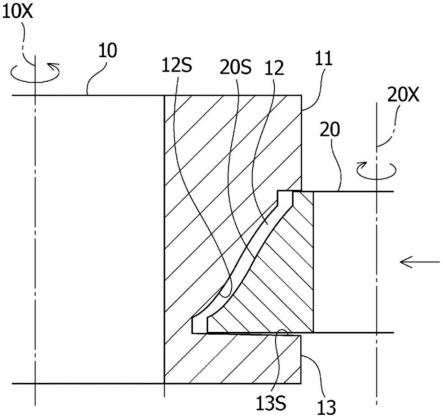
1.本发明涉及环形轧材的制造方法。
背景技术:2.作为对环形坯料进行环形轧制而制造环形轧材的方法,例如,如日本特许第5895111号公报公开的那样可知有以下方法:使主辊和芯辊分别与具有环形形状的环形坯料的外周面和内周面抵接,使主辊和芯辊一边分别绕中心轴线旋转,一边沿环形坯料的径向将该环形坯料夹入且进行按压,并且利用一对轴辊沿环形坯料的中心轴线方向将环形坯料夹入并进行按压,从而制造环形轧材。
3.此外,作为环形轧材的制造方法,例如,在中国专利申请公开第107127279号的说明书中记载了如下的环形轧制的方法:公开了主辊具备位于环形坯料的下方的下部支承板和位于环形坯料的上方的上部按压板,利用上部按压板调整环形构件调节上部按压板的位置,从而能够容易地应对高度不同的环形坯料。
4.现有技术文献
5.专利文献
6.专利文献1:日本特许第5895111号公报
7.专利文献2:中国专利申请公开第107127279号的说明书
技术实现要素:8.发明要解决的问题
9.在对环形坯料进行环形轧制的情况下,特别是若环形坯料具有锥形状或具有环形坯料的壁厚局部不同的形状,则由于因作为模具的主辊和芯辊与环形坯料之间的圆周速度差而产生的阻力、厚壁部与薄壁部之间的扩径量的差等,导致存在环形轧制过程中的环形坯料的姿势难以稳定的问题。若环形坯料的旋转变得不稳定,则存在环形坯料与轴辊、工作台等过度接触而产生缺陷,或轧制后的环形轧材成为变形的形状等问题。
10.为了使环形坯料的旋转稳定化,考虑到在主辊设置位于环形坯料的上下的位置的凸缘部而使环形坯料的姿势稳定化的方法,但若在环形轧制过程中环形坯料失控而与包含上述的凸缘部的主辊、芯辊接触,则存在所得到的环形轧材产生毛刺等缺陷,或由于这样的接触的撞击而对环形轧制装置作用的负荷增大的问题。由此,当如上所述在主辊设置凸缘部的情况下,需要如下的措施等:准备多个模式的包含凸缘部的主辊的形状(所谓的模具),一边调整与环形坯料的抵接一边进行环形轧制,或者为了减轻装置的负荷而较多地进行在加热环形坯料后进行环形轧制这样的工序(增加所谓的加热次数),一点一点地进行环形轧制。
11.因此,本发明是鉴于上述的问题点而完成的,其目的在于提供环形轧材的制造方法,即使在主辊设置位于环形坯料的上下的位置的凸缘部,也不会在所得到的环形轧材产生缺陷等,能够使轧制过程中的环形坯料的姿势稳定化。
12.用于解决问题的方案
13.为了达成上述的目的,本发明是利用环形轧制装置对环形坯料进行环形轧制而制造环形轧材的方法,其中,所述环形轧制装置具备主辊和芯辊,所述主辊的外周面具有:凹部,其容纳所述环形坯料和所述芯辊的外周面;第1凸缘部,其相对于所述凹部位于所述主辊的中心轴线方向的一侧;以及第2凸缘部,其位于所述第1凸缘部的相反侧,所述凹部的内表面具有:轧制面,其与所述环形坯料的外周面接触;所述第1凸缘部侧的第1内表面;以及所述第2凸缘部侧的第2内表面,所述第1内表面和所述第2内表面中的至少一个内表面以相对于所述主辊的中心轴线方向垂直相交的垂直面为基准具有斜度,使得所述凹部的开口变宽。所述斜度开始于从所述至少一个内表面与所述轧制面的相交线起至相当于所述环形轧材的厚度的距离为止的范围内。换言之,所述至少一个内表面和所述轧制面的相交线与所述斜度的所述轧制面侧的末端之间的距离小于所述环形轧材的厚度。所述斜度的角度以所述垂直面为基准时大于0.3
°
且为9
°
以下。
14.优选为,所述环形坯料是ni基合金、co基合金或fe基合金的耐热合金。
15.也可以是,所述环形坯料的外周面的至少局部相对于所述环形坯料的中心轴线倾斜,在该情况下,也可以是,连结所述环形坯料的大径外周的端面角和小径外周的端面角的直线与所述环形坯料的中心轴线之间的角度大于10
°
。而且,在该倾斜的角度大于10
°
的情况下,优选为,所述内表面的斜度的角度以所述垂直面为基准时为0.6
°
以上且9
°
以下。斜度的角度的下限优选为0.8
°
以上,更优选为1
°
以上。斜度的角度的上限优选为4
°
以下,更优选为3
°
以下。
16.也可以是,所述环形坯料的外周面的至少局部相对于所述环形坯料的中心轴线倾斜,在该情况下,也可以是,连结所述环形坯料的大径外周的端面角和小径外周的端面角的直线与所述环形坯料的中心轴线之间的角度为10
°
以下。而且,在该倾斜的角度为10
°
以下的情况下,优选为,所述内表面的斜度的角度以所述垂直面为基准时大于0.3
°
且小于3
°
。对于优选的斜度的角度的下限,优选为0.5
°
以上,更优选为0.6
°
以上。对于斜度的角度的上限,优选为2.5
°
以下,更优选为2
°
以下。
17.发明的效果
18.根据这样的本发明,主辊的外周面具有容纳环形坯料和芯辊的外周面的凹部,该凹部的第1凸缘部侧的第1内表面和第2凸缘部侧的第2内表面中的至少一个内表面在其整个部分或规定的一部分具有斜度,使得凹部的开口变宽,因此,能够适当地约束旋转过程中的环形坯料,使环形坯料的姿势稳定,能够顺畅地进行环形轧制。由此,不需要准备多个模式的模具或增加加热次数,能够减少环形轧制所需的成本。特别是,即使在环形坯料具有锥形状或具有环形坯料的壁厚局部不同的形状的情况下,也能够使环形坯料的姿势稳定化,由此,能够对所得到的环形轧材赋予近净形的形状,能够减少环形坯料的投入重量。
附图说明
19.图1是示意地表示在本发明的环形轧材的制造方法中使用的环形轧制装置的一例的俯视图。
20.图2是示意地表示图1的环形轧制装置中的主辊和芯辊的局部放大剖视图。
21.图3是放大地表示图2的主辊的上凸缘的局部的剖视图。
22.图4是放大地表示图2的主辊的下凸缘的局部的剖视图。
23.图5是示意地表示在本发明的环形轧材的制造方法中使用的环形坯料的一例的剖视图。
具体实施方式
24.以下,参照附图对本发明的环形轧材的制造方法的一实施方式进行说明。另外,附图着重于清楚地示出本发明的实施方式,并不一定按比例绘制。
25.在本实施方式的环形轧材的制造方法中,例如,使用图1~图4所示的环形轧制装置。该环形轧制装置包括分别位于作为轧制对象的具有环形形状的环形坯料1的外周侧和内周侧的主辊10和芯辊20。主辊10的外周面和芯辊20的外周面以夹着环形坯料1的方式互相相对。主辊10构成为能够以其中心轴线10x为中心旋转,芯辊20也构成为能够以其中心轴线20x为中心旋转。主辊10的中心轴线10x和芯辊20的中心轴线20x大致平行。主辊10和芯辊20用于在该主辊10和该芯辊20之间沿环形形状的径向(以下,称为“环形径向”)挤压环形坯料1,芯辊20构成为能够相对于主辊10沿着环形径向移动。另外,主辊的中心轴线方向和环形坯料的中心轴线方向一致。
26.此外,环形轧制装置包括一对轴辊30,其位于在环形形状的中心轴线方向(以下,称为“环形轴线方向”)上夹着环形坯料1的位置。另外,在本说明书中,为了便于说明,沿着中心轴线10x或中心轴线20x,将图2的上侧称为“上”,将下侧称为“下”。即,一对轴辊30位于环形坯料1的上下两侧。一对轴辊30沿环形轴线方向挤压环形坯料1,一对轴辊30的外周面以夹着环形坯料1的方式互相相对。一对轴辊30构成为能够以各自的中心轴线为中心旋转。
27.主辊10的外周面具有:大致字母u状的凹部12,其容纳作为轧制对象的环形坯料1和芯辊20的外周面;第1凸缘部(以下,称为“上凸缘部”)11,其位于主辊的中心轴线方向的一侧;以及第2凸缘部(以下,称为“下凸缘部”)13,其位于上述第1凸缘部的相反侧。而且,主辊10的凹部12的内表面具有:轧制面12s,其与环形坯料1的外周面接触;上凸缘部11侧的第1内表面(以下,称为“上表面”)11s;以及下凸缘部13侧的第2内表面(以下,称为“下表面”)13s。
28.主辊10的凹部12的轧制面12s与轧制后的环形轧材的外周面相对应地倾斜。同样地,芯辊20的外周面20s也同样地与轧制后的环形轧材的内周面相对应地倾斜。如图2所示,主辊10的凹部12的轧制面12s和芯辊20的外周面20s之间的间隙成为轧制后的环形轧材的形状。如此,主辊10的凹部12的轧制面12s和芯辊20的外周面20s分别与期望的环形轧材的外周面和内周面的形状相对应,可以以直线状、曲线状、或者直线状和曲线状的组合倾斜。环形轧材的壁厚也可以不是一样的,由此,环形轧材的外周面和内周面的倾斜也可以不是相同角度。
29.如图2所示,以凹部12的开口朝向主辊10的外周侧变宽的方式对主辊10的凹部12的下表面13s赋予斜度。另外,在图2中,由于下表面13s具有比上表面11s大的面积,因此,对下表面13s赋予斜度,但根据期望的环形轧材的形状的不同,在上表面11s具有比下表面13s大的面积的情况下,以凹部12的开口朝向外周侧变宽的方式对上表面11s赋予斜度。此外,也可以不是像这样仅对上表面11s或下表面13s中的一者赋予斜度,而是对上表面11s和下表面13s两者赋予斜度。
30.如图3所示,用相对于主辊的中心轴线方向垂直相交的垂直面h(通常,作为环形径向的水平面)与上表面11s之间的角度表示上表面11s的斜度角θa。上表面11s的斜度角θa的下限根据后述的环形坯料的倾斜角而变化,优选为大于0.3
°
,更优选为0.5
°
以上,进一步优选为0.6
°
以上,更进一步优选为1
°
以上。此外,对于上表面11s的斜度角θa的上限,优选为9
°
以下,更优选为小于5
°
,进一步优选为3
°
以下,更进一步优选为2
°
以下。
31.此外,如图3所示,对从上表面11s与主辊10的凹部12的轧制面12s的相交线v至外周侧的端的范围(即,整个上表面11s)赋予上表面11s的斜度,但为了得到本发明的效果,也可以不从与轧制面12s的相交线v开始,而是对从期望的轧制后的环形轧材的内周面的位置sa至外周侧的端的范围赋予斜度(即,上述的相交线v与上述的位置sa之间的距离是期望的环形轧材的上端部的厚度ra)。换言之,上表面11s和轧制面12s的相交线v与上表面11s的斜度的轧制面12s侧的末端之间的距离小于环形轧材的厚度ra。
32.如图4所示,用相对于主辊10的中心轴线方向垂直相交的垂直面h(通常,作为环形径向的水平面)与下表面13s之间的角度表示下表面13s的斜度角θb。下表面13s的斜度角θb的下限根据后述的环形坯料的倾斜角而变化,优选为0.3
°
以上,更优选为0.5
°
以上,进一步优选为0.6
°
以上,更进一步优选为1
°
以上。此外,下表面13s的斜度角θb的上限根据后述的环形坯料的倾斜角而变化,优选为小于9
°
,更优选为小于5
°
,进一步优选为小于3
°
,更进一步优选为小于2
°
。
33.此外,如图4所示,对从下表面13s与主辊10的凹部12的轧制面12s的相交线v至外周侧的端的范围(即,整个下表面13s)赋予下表面13s的斜度,但为了得到本发明的效果,也可以不从与轧制面12s的相交线v开始,而是对从期望的轧制后的环形轧材的内周面的位置sb至外周侧的端的范围赋予斜度即可(即,上述的相交线v与上述的位置sb之间的距离是期望的环形轧材的下端部的厚度rb)。换言之,下表面13s和轧制面12s的相交线v与下表面13s的斜度的轧制面12s侧的末端之间的距离小于环形轧材的厚度rb。
34.为了使用这样的环形轧制装置制造环形轧材,首先,将环形坯料1投入环形轧制装置。作为环形坯料1,适合使用由ni基合金、co基合金、fe基合金等耐热合金制作的环形坯料。耐热合金因温度降低引起的热延展性的降低显著,因此,能够塑性加工的温度区域非常小。即,对于耐热合金来说,能够轧制的时间较短,通过能够以稳定的姿势轧制的本实施方式的环形轧制装置得到的效果明显。投入于环形轧制装置的环形坯料1的加热温度根据环形坯料1的材质而不同。例如,在环形坯料1由ni基合金的alloy718制作的情况下,优选为1000℃~1050℃的范围的加热温度,但会因各产品的要求而变化,因此,不限定于该温度范围。
35.此外,投入的环形坯料1的形状例如可以是外周面和内周面大致一定地以直线状倾斜的所谓的锥环形,也可以是以曲线状或以直线状和曲线状的组合倾斜,或者是环形坯料的壁厚局部不同的所谓的异形环形。对于这样的环形坯料1的倾斜角θr,如图5所示,即使在环形坯料的局部的壁厚不同的情况下,在锥环形的情况下,由连结环形坯料1的大径外周的端面角ld和小径外周的端面角sd的线d与环形坯料1的环形形状的中心轴线1x之间的角度来表示上述倾斜角θr。对于环形坯料1的倾斜角θr的下限,优选为5
°
以上,更优选为7
°
以上,进一步优选为大于10
°
,更进一步优选为15
°
以上。环形坯料1的倾斜角θr的上限不特别限定,例如,优选为40
°
以下,更优选为35
°
以下,进一步优选为30
°
以下。作为投入的环形坯
料1,当然也可以是没有倾斜的所谓的矩形环形。
36.然后,使主辊10的外周面和芯辊20的外周面分别与环形坯料1的外周面和内周面抵接,此外,使一对轴辊30的外周面分别与环形坯料1的上下两端面抵接。通过一边使主辊10和芯辊20向图1、图2所示的箭头方向旋转,一边使芯辊20朝向主辊10移动,从而利用主辊10和芯辊20沿环形径向将环形坯料1夹入并进行按压。此外,一边使一对轴辊30向图1所示的箭头方向旋转,一边利用一对轴辊30沿环形轴线方向将环形坯料1夹入并进行按压。由此,对环形坯料1进行环形轧制,得到环形轧材。
37.此时,即使环形坯料1是锥环形、异形环形,如图2所示,以凹部12的开口朝向主辊10的外周侧变宽的方式对主辊10的凹部12的下表面13s赋予斜度,因此,在主辊10的凹部12内容纳的环形坯料1因凹部12的下表面13s和上表面11s而姿势稳定,所以能够使环形坯料1以中心轴线1x为中心稳定地旋转。由此,能够抑制环形坯料1与轴辊30等过多地接触,能够防止缺陷的产生。特别是,对于倾斜角θr大于10
°
的环形坯料1而言,会在模具与坯料之间产生圆周速度差,在环形轧制时姿势难以稳定,由此来看,本发明的效果显著。此外,在为了得到异形环形而对主辊10和芯辊20的外周面赋予了规定的形状的情况下也是,会产生厚壁部与薄壁部之间的扩径量的差,在环形轧制时姿势难以稳定,由此来看,本发明的效果显著。
38.实施例
39.以下,对本发明的实施例进行说明。首先,如表1所示,对环形轧制装置的主辊的凹部的整个下表面分别赋予从0
°
到12
°
的斜度角θb的斜度,进行了将环形坯料环形轧制的试验。此外,对环形坯料是倾斜角大于10
°
的锥环形和倾斜角为10
°
以下的锥环形这两个类型的环形坯料进行了试验。而且,对环形轧制过程中的环形坯料的稳定性和所得到的环形轧材的缺陷进行了评价。将其结果一并记于表1中。
40.此外,对环形轧制装置的主辊的凹部的整个下表面赋予1.5
°
的斜度角θb的斜度,并且如表2所示,对主辊的凹部的整个上表面分别赋予从0
°
到12
°
的斜度角θa的斜度,进行了将环形坯料环形轧制的试验。与上述同样地,对环形坯料是倾斜角大于10
°
的锥环形和倾斜角为10
°
以下的锥环形这两个类型的环形坯料进行了试验。而且,对环形轧制过程中的环形坯料的稳定性和所得到的环形轧材的缺陷进行了评价。将其结果一并记于表2中。
41.[表1]
[0042]
[0043]
[表2]
[0044][0045]
对于表中的“轧制稳定性”,从环形坯料的上部方向和侧面方向进行运动图像拍摄来观察环形轧制时的环形坯料的举动,将环形轧制过程中的环形坯料没有异动(滑动、起伏、失控)的情况评价为
“◎”
,将异动的程度小的情况评价为
“○”
,将异动的程度大的情况(无法在目标时间内轧制至期望的尺寸,中途中止轧制的情况)评价为
“×”
。此外,将其中间的情况评价为
“△”
。
[0046]
对于表中的“缺陷”,利用磨削机去除所得到的环形轧材的缺陷,并对去除瑕疵后的减少重量进行测量,将该减少重量相对于环形坯料的重量小于0.1%的情况评价为
“◎”
,将0.1%以上且小于0.3%的情况评价为
“○”
,将0.3%以上且小于1.5%的情况评价为
“△”
,将1.5%以上的情况评价为
“×”
。
[0047]
如表1、表2所示,若主辊的凹部的下表面、上表面的斜度角都为0.1
°
那样过小的角度,则下表面、上表面对环形坯料的约束过大而成为环形坯料旋转的阻力,使旋转不稳定。相反,若斜度角为大于10
°
那样过大的角度,则环形坯料的保持不充分,环形坯料的姿势倾斜,由于与主辊的摩擦,旋转的不稳定性增加。
[0048]
此外,若投入倾斜角大的环形坯料,则由于主辊与环形坯料之间的圆周速度差,导致在环形轧制过程中环形坯料的姿势倾斜,但在不约束该环形坯料的倾斜的范围的斜度角的情况下,能够得到环形坯料旋转的稳定性。轧制稳定性和缺陷的产生表现出某种程度相同的倾向。
[0049]
特别是,由表1和表2所示的结果可知,无论环形坯料的倾斜角如何,形成于主辊的下表面、上表面中的任一者的斜度的角度都在0.5
°
以上且小于3
°
的范围内时,轧制稳定性优异,缺陷也较少。特别是,在环形坯料的倾斜角为10
°
以下的情况下,在大于0.3
°
且小于3
°
的范围内,轧制稳定性优异,在0.5
°
以上且小于2
°
的范围内,轧制稳定性和缺陷两者显著优异。此外,在环形坯料的倾斜角大于10
°
的情况,在0.6
°
以上且9
°
以下的范围内,轧制稳定性优异,在1
°
以上且小于3
°
的范围内,轧制稳定性和缺陷两者显著优异。
[0050]
附图标记说明
[0051]
1、环形坯料;10、主辊;11、第1凸缘部(上凸缘部);11s、第1内表面(上表面);12、凹部;12s、轧制面;13、第2凸缘部(下凸缘部);13s、第2内表面(下表面);20、芯辊;30、轴辊。