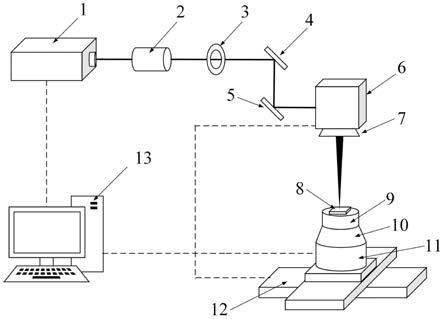
1.本发明属于封装基板激光加工技术领域,具体涉及一种封装基板表面导通孔小锥度高质高效加工方法。
背景技术:2.封装基板是微电子器件的承载和保护平台,通常选用具有优良导热性、电阻率、低介电常数和足够刚度强度的陶瓷材料、环氧树脂材料和铝合金等,在高端大功率电子器件向着智能化、集成化、微小化方向发展的过程中,封装基板技术性能的升级对基板材料的精密加工提出了越来越高的要求。为实现电子系统的高密度互联,通常需要在封装基板表面加工阵列化的导通孔,传统加工方法已很难满足某些材料的工艺要求,激光加工成为了封装基板导通孔制造的首选加工方式。
3.激光加工具有加工效率高,表面变形小,无刀具损耗,无污染等特点,可实现高硬度、高脆性及高熔点材料的高精度加工,但是采用激光对封装基板表面进行导通孔加工也存在以下缺陷:激光打孔时,加工区域的材料在高能量激光下直接熔化或蒸发,熔渣和气化物质会粘附在孔壁和孔入口表面,极易产生二次沉积,影响导通孔质量;沉积物和气化物质形成的等离子体会积聚在孔通道内,对激光产生屏蔽、散射效应,降低作用于材料去除时的激光能量,影响加工效率;对于在厚度≥0.1mm的封装基板材料上加工直径≥100μm的导通孔,普遍采用激光旋切加工方法,该方法是一种基于同心圆填充轨迹的激光加工方法,但存在材料去除率较低,加工速度慢,且加工孔的锥度较大等缺点。
技术实现要素:4.为了克服上述现有技术的缺点,本发明的目的在于提供一种封装基板表面导通孔小锥度高质高效加工装置及方法,通过超声振动辅助激光加工过程,采用激光多圆环切加工轨迹进行材料去除,实现封装基板表面多尺寸导通孔的高质高效加工。
5.为了达到上述目的,本发明采用的技术方案为:
6.一种封装基板表面导通孔小锥度高质高效加工装置,包括超声辅助激光加工系统,超声辅助激光加工系统包括光路系统和超声振动辅助装置,光路系统包括短脉冲激光器1,短脉冲激光器1输出的激光束依次经过扩束镜2、小孔光阑3、第一反射镜4、第二反射镜5、扫描振镜6和聚焦场镜7后作用在封装基片上,短脉冲激光器1、扩束镜2、小孔光阑3、第一反射镜4、第二反射镜5、扫描振镜6和聚焦场镜7构成光路系统;
7.封装基片装夹在激光打孔用夹具8上,激光打孔用夹具8固定在超声振动加工平台9上,超声振动加工平台9连接在超声换能器10上,超声换能器10连接在超声发生器11,超声发生器11固定在精密运动工作台12上,超声振动加工平台9、超声换能器10和超声发生器11构成超声振动辅助装置;
8.短脉冲激光器1、扫描振镜6、超声发生器11、精密运动工作台12和计算机13连接。
9.一种封装基板表面导通孔小锥度高质高效加工方法,包括以下步骤:
10.1)搭建超声辅助激光加工系统,超声辅助激光加工系统包括光路系统和超声振动辅助装置,光路系统包括短脉冲激光器1,短脉冲激光器1输出的激光束依次经过扩束镜2、小孔光阑3、第一反射镜4、第二反射镜5、扫描振镜6和聚焦场镜7后作用在封装基片上,短脉冲激光器1、扩束镜2、小孔光阑3、第一反射镜4、第二反射镜5、扫描振镜6和聚焦场镜7构成光路系统;
11.封装基片装夹在激光打孔用夹具8上,激光打孔用夹具8固定在超声振动加工平台9上,超声振动加工平台9连接在超声换能器10上,超声换能器10连接在超声发生器11,超声发生器11固定在精密运动工作台12上,超声振动加工平台9、超声换能器10和超声发生器11构成超声振动辅助装置;
12.短脉冲激光器1、扫描振镜6、超声发生器11、精密运动工作台12和计算机13连接;
13.2)将封装基板放置于超声清洗机中超声清洗20分钟,将风干后的封装基板装夹在激光打孔用夹具8上;
14.3)通过计算机13控制精密运动工作台12沿x、y轴两个方向进行移动,将超声振动辅助装置移动到聚焦场镜7的正下方,同时控制精密运动工作台12通过z轴调节超声振动辅助装置的高度,使激光聚焦于封装基板上表面;
15.4)通过计算机13控制超声发生器11的通断,使用超声振动辅助装置的自动调频功能寻找封装基板的耦合振动频率,并设置相应的超声振动辅助加工参数;
16.5)通过计算机13设置短脉冲激光器1的激光加工参数,包括激光输出波长、激光脉冲宽度、单脉冲能量和脉冲重复频率;
17.6)通过计算机13在扫描振镜6的控制软件上绘制激光多圆环切加工轨迹,并设置激光扫描轨迹参数;
18.7)通过计算机13控制短脉冲激光器1输出激光,激光经过光路系统后聚焦到封装基板上表面,同时,超声振动辅助装置输出超声波,并通过激光打孔用夹具8将超声振动传导到封装基板上,激光在扫描振镜6的控制下沿设定路径在封装基板上进行通孔加工;
19.8)通孔加工完成后,取下封装基板,先后用丙酮和无水乙醇分别超声清洗20分钟,得到封装基板加工成品。
20.所述的封装基板表面导通孔直径≥100μm。
21.所述的短脉冲激光器1为脉冲宽度≤15ns的纳秒激光器、皮秒激光器或飞秒激光器。
22.所述的激光打孔用夹具8采用铝合金材料以提高超声波传导性能。
23.所述的封装基板为厚度≥0.1mm的陶瓷材料、金属材料、硅基板、金刚石或功能复合材料。
24.所述的步骤4)中超声振动辅助加工参数包括超声振动频率和超声振动功率,超声振动频率为封装基板的耦合振动频率,超声振动功率为10w
‑
500w。
25.所述的步骤6)中激光多圆环切加工轨迹由初始圆图案、圆图案内部螺旋线填充轨迹和最小圆图案组成,激光加工路径具体为:激光先从坐标原点o通过跳转轨迹
①
到达初始圆图案扫描起始点a,开始扫描初始圆图案轨迹
②
,扫描完成后激光回到a点,然后沿着螺旋线填充轨迹
③
进行扫描,到达螺旋线内部的最小圆图案起始点b,接着激光沿最小圆路径
④
进行扫描,扫描结束后激光回到b点完成一轮扫描;此时激光通过跳转轨迹
⑤
回到a点继续
进行第二轮扫描,重复以上扫描过程,直到扫描次数为n次时完成通孔加工,激光从b点直接跳转回原点o,扫描结束。
26.所述的激光多圆环切加工轨迹中初始圆图案即圆环外圆的半径为r1,最小圆即圆环内圆的半径为r2,圆环宽度d等于圆环外圆半径r1减去圆环内圆半径r2,即d=r1‑
r2,当通孔半径r≤250μm时,d=2/5r,当通孔半径r>250μm时,d=100μm;此外,聚焦光斑半径为ω,圆环外圆半径等于预加工通孔半径减去聚焦光斑半径,即r1=r
‑
ω。
27.所述的圆环内部螺旋线填充轨迹的填充线间距为d,填充线间距d应等于聚焦光斑半径,即d=ω,此时激光扫描时垂直于扫描方向的光斑重叠率近似为50%。
28.所述的步骤6)中激光扫描轨迹参数包括激光扫描速度、激光跳转速度和激光扫描次数,激光扫描次数根据基板厚度进行确定。
29.与现有技术相比,本发明具有以下有益效果:
30.(1)本发明利用超声振动辅助激光加工过程,一方面降低了激光加工过程中的熔渣沉积现象,提高了封装基板表面孔的质量;另一方面消除了等离子体屏蔽效应,增大了作用在封装基板表面的激光能量,提高了材料去除率。
31.(2)本发明利用激光多圆环切扫描轨迹进行加工,解决了常规激光旋切加工导通孔时,激光穿透封装基板表面导通孔中心后透射激光的能量损失,极大提高了加工效率,同时增大了照射在孔壁上用于修型的激光作用时间,减小了孔锥度。
32.(3)本发明采用短脉冲激光对封装基板进行孔加工,与毫秒激光等长脉冲激光相比,大大提高了加工质量和加工精度。
附图说明
33.图1为本发明超声辅助激光加工系统示意图。
34.图2为本发明封装基板表面导通孔的激光多圆环切加工轨迹和路径示意图。
35.图3中(a)为实施例1采用超声振动辅助激光多圆环切加工的导通孔入口形貌图,(b)为对比例1采用无超声振动下激光旋切加工的导通孔入口形貌图。
36.图4为对比例1采用的激光旋切加工轨迹示意图。
37.图5为实施例2和对比例2加工导通孔锥度与加工时长的关系图。
38.图6为实施例3和对比例3加工导通孔锥度与加工时长的关系图。
具体实施方式
39.下面结合附图和实施例对本发明方法作进一步详细说明。
40.实施例1,一种封装基板表面导通孔小锥度高质高效加工方法,包括以下步骤:
41.1)搭建超声辅助激光加工系统,如图1所示,超声辅助激光加工系统包括光路系统和超声振动辅助装置;光路系统包括短脉冲激光器1,短脉冲激光器1输出的激光束依次经过扩束镜2、小孔光阑3、第一反射镜4、第二反射镜5、扫描振镜6和聚焦场镜7后作用在封装基片上,短脉冲激光器1、扩束镜2、小孔光阑3、第一反射镜4、第二反射镜5、扫描振镜6和聚焦场镜7构成光路系统;短脉冲激光器1为纳秒激光器,短脉冲激光器1输出激光束经过扩束镜2对其进行扩束,数值孔径增大,以便于减小聚焦后的激光光斑尺寸;扩束光经过小孔光阑3被滤去光斑边缘的衍射光圈,此后依次经过第一反射镜4、第二反射镜5进入扫描振镜6
和聚焦场镜7;
42.封装基片装夹在激光打孔用夹具8上,激光打孔用夹具8固定在超声振动加工平台9上,超声振动加工平台9连接在超声换能器10上,超声换能器10连接在超声发生器11,超声发生器11固定在精密运动工作台12上,超声振动加工平台9、超声换能器10和超声发生器11构成超声振动辅助装置;聚焦场镜7将激光进行聚焦后垂直照射在激光打孔用夹具8上,超声发生器11用于把市电转换成与超声换能器10相匹配的高频交流电信号,超声换能器10用于将输入的电功率转换成机械功率并传递到超声振动加工平台9上,超声振动加工平台9通过与激光打孔用夹具8的连接将超声振动传递到加工样品上;
43.短脉冲激光器1、扫描振镜6、超声发生器11、精密运动工作台12和计算机13连接;精密运动工作台12搭载超声振动辅助装置,控制工位移动及激光聚焦;计算机13控制整个激光加工过程;
44.2)将厚度为0.38mm,质量分数为96%的氧化铝陶瓷封装基板用有机溶剂超声清洗20分钟,去除表面的油脂、灰尘等物质,清洗后使用压缩空气吹干,将风干后的氧化铝陶瓷基板装夹在激光打孔加工用夹具8上;
45.3)通过计算机13控制精密运动工作台12沿x、y轴两个方向进行移动,将超声振动辅助装置移动到聚焦场镜7的正下方,同时控制精密运动工作台12通过z轴调节超声振动辅助装置的高度,使激光聚焦于氧化铝封装基板上表面;
46.4)通过计算机13控制超声发生器11的通断,使用超声振动辅助装置的自动调频功能寻找到封装基板的耦合振动频率为20134hz,并设置相应的超声振动辅助加工参数,超声振动频率为20134hz,超声振动功率为300w;
47.5)通过计算机13设置短脉冲激光器1的激光加工参数,激光输出波长为355nm,激光脉冲宽度为11ns、单脉冲能量为120μj,脉冲重复频率为50khz,使激光功率为6w;
48.6)通过计算机13在扫描振镜6的控制软件上绘制激光多圆环切加工轨迹,并设置激光扫描轨迹参数;
49.在计算机13上打开扫描振镜6的控制软件scanmaster designer,绘制如图2中的(a)所示的激光加工轨迹,预加工直径为200μm的导通孔,设置初始圆图案半径r1为90μm,最小圆图案半径r2为50μm,在圆环图案内部绘制螺旋线填充轨迹,设置填充间距d为10μm;激光的扫描路径如图2中的(b)所示;
50.具体为:激光先从坐标原点o通过跳转轨迹
①
到达初始圆图案扫描起始点a,开始扫描初始圆图案轨迹
②
,扫描完成后激光回到a点,然后沿着螺旋线填充轨迹
③
进行扫描,到达螺旋线内部的最小圆图案起始点b,接着激光沿最小圆路径
④
进行扫描,扫描结束后激光回到b点完成一轮扫描;此时激光通过跳转轨迹
⑤
回到a点继续进行第二轮扫描,重复以上扫描过程,直到扫描次数为300次时完成通孔加工,激光从b点直接跳转回原点o,扫描结束;设置激光扫描轨迹参数,包括扫描速度为300mm/s,激光跳转速度为4000mm/s,激光扫描次数为300次。
51.7)通过计算机13控制短脉冲激光器1输出激光,激光经过光路系统后聚焦到氧化铝陶瓷基板上表面,同时,超声振动辅助装置输出超声波,并通过激光打孔用夹具8将超声振动传递到氧化铝陶瓷基板上,激光在扫描振镜6的控制下沿设定路径在氧化铝陶瓷基板上进行通孔加工;
=r
‑
ω,填充间距d设置为10μm,其他步骤和对比例1相同,得到在不同厚度陶瓷基板上加工不同直径导通孔的加工时长。以导通孔锥度达到饱和时的加工时长作为评价标准,选取加工时长最短的加工方法作为最佳加工方案,得到以本发明超声振动辅助激光多圆环切轨迹加工方法作为最佳加工方案的氧化铝陶瓷基板导通孔加工适用范围。具体为:工业标准氧化铝陶瓷基板厚度为0.12mm时,加工直径≥100μm的导通孔;工业标准氧化铝陶瓷基板厚度为0.25mm时,加工直径100μm
‑
200μm和直径≥500μm的导通孔;工业标准氧化铝陶瓷基板厚度为0.38mm和0.5mm时,加工直径100μm
‑
200μm和直径≥1000μm的导通孔。