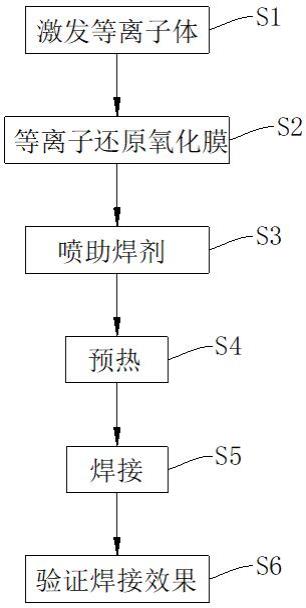
1.本发明涉及焊接组装技术领域,特别地,涉及一种电子装联焊接工艺。
背景技术:2.目前,电子装联焊接中最重要的工艺是在焊接单元表面喷涂助焊剂,通过助焊剂的化学反应来清除焊接表面氧化膜,进而提升焊料的润湿效果,最终在焊接接合面形成合格的imc层。但是,该工艺往往会导致助焊剂残留,助焊剂残留往往会引起电化学,力学可靠性的失效,进而降低产品服役寿命。
技术实现要素:3.基于此,有必要提供一种提高产品服役寿命的电子装联焊接工艺。
4.本发明解决其技术问题所采用的技术方案是:一种电子装联焊接工艺,所述电子装联焊接工艺包括以下步骤:步骤s1:激发等离子体,使用合适的工作气体按设定功率激发等离子体;步骤s2:等离子还原氧化膜,将激发出的所述等离子体喷射至所述电子装联的表面,从而能够对所述电子装联进行还原氧化膜,然后在所述电子装联的表面周围通惰性气体;步骤s3:喷微量助焊剂,利用超声波喷雾阀以合适的喷射气压来控制所述助焊剂的喷射面积和喷射质量;步骤s4:预热,将所述电子装联移动至预热区进行预加热;步骤s5:焊接,将所述电子装联移动至焊接区进行焊接。
5.进一步地,所述工作气体包括h2,或nh3,或h2和nh3的混合气,或h2和ar的混合气,或h2和n2的混合气,或h2和he的混合气,或h2和h2o的混合气,或h2和hcooh的混合气,或nh3和ar的混合气,或nh3和n2的混合气,或nh3和he的混合气,或nh3和h2o的混合气。
6.进一步地,h2或nh3的体积浓度范围为3
‑
20%,所述设定功率为100
‑
1500w。
7.进一步地,所述等离子还原氧化膜的还原时间为30
‑
240s,且等离子还原氧化膜的移动速度为1
‑
15m/min。
8.进一步地,所述惰性气体为ar、n2、he中的一种或者几种的组合。
9.进一步地,所述预热区的加热温度为80
‑
150℃。
10.进一步地,所述电子装联焊接工艺还包括步骤s6:验证焊接效果,对焊接后的所述电子装联进行机械和电化学可靠性测试。
11.进一步地,对焊接后的焊点进行检测的装置包括x
‑
ray、焊接强度测试仪、金相显微镜、扫描电子显微镜、温湿度试验箱、跌落机以及振动台。
12.本发明的有益效果是:本发明提供的电子装联焊接工艺,通过采用等离子还原氧化膜和喷涂微量助焊剂,能够对电子装联的氧化层进行充分清除,与现有技术中的喷涂大量的助焊剂对电子装联的氧化层进行充分清除相比,能够减少助焊剂的残留,进而提高电
子装联的服役寿命,同时,与对电子装联的氧化膜进行多次射流等离子体还原,来实现电子装联的氧化层进行充分清除相比,加工时间较短,进而减少电子装联的加工成本。
附图说明
13.下面结合附图和实施例对本发明作进一步说明。
14.图1是本发明的电子装联焊接工艺的流程图。
具体实施方式
15.现在结合附图对本发明作详细的说明。此图为简化的示意图,仅以示意方式说明本发明的基本结构,因此其仅显示与本发明有关的构成。
16.请参阅图1,本发明提供了一种电子装联焊接工艺,该工艺包括以下步骤:步骤s1:激发等离子体,使用合适的工作气体按设定功率激发等离子体。所述工作气体包括h2,或nh3,或h2和nh3的混合气,或h2与ar、h2与n2、h2与he、h2与h2o以及h2与hcooh的混合气,以及nh3与ar、nh3与n2、nh3与he、nh3与h2o的混合气,从而能够激发出等离子氢活性物质。进一步地,h2或nh3的体积浓度范围为3
‑
20%,所述设定功率为100
‑
1500w。在本实施方式中,激发等离子体的仪器为等离子体发生器。
17.步骤s2:等离子还原氧化膜,将激发出的所述等离子体喷射至所述电子装联的表面,从而能够对所述电子装联进行还原氧化膜;然后在所述电子装联的表面周围通惰性气体,从而能够防止等离子还原氧化膜的过程中升温对所述电子装联造成二次氧化。其中,所述等离子还原氧化膜的还原时间为30
‑
240s,且等离子还原氧化膜的移动速度为1
‑
15m/min。在本实施方式中,所述惰性气体为ar、n2、he中的一种或者几种的组合。
18.所述等离子还原氧化膜选用射流等离子的方式对所述电子装联进行还原氧化膜,一方面能够对所述电子装联进行还原氧化膜,另一方面能够对所述电子装联具有一定的清洁力度。
19.但是,仅采用所述等离子体对所述电子装联进行还原氧化膜,并不能完全还原所述电子装联的氧化膜,若需要对所述电子装联充分还原氧化膜,则需要对所述电子装联的氧化膜进行多次射流等离子体还原,但是,加工时间较长,进而增加所述电子装联的加工成本。
20.进一步地,在本实施方式中,喷射出的等离子体沿着直线轨道多次重复对所述电子装联进行表面还原。在其他未示出的实施方式中,喷射出的等离子体还可以是沿着圆形或者方形轨道多次重复对所述电子装联进行表面还原。
21.步骤s3:喷微量助焊剂,利用超声波喷雾阀以合适的喷射气压来控制所述助焊剂的喷射面积和喷射质量。其中,所述喷射气压为2000
‑
5000pa,所述助焊剂为无卤低活性助焊剂。
22.进一步地,所述超声波喷雾阀上连接有塑形咀,所述塑形咀为注塑一体成型的喷嘴,通过采用塑形咀喷流所述助焊剂,从而能够使得所述助焊剂以雾化的方式喷流至所述电子装联的表面上,其中可以通过所述塑性咀的大小和所述塑性咀与所述电子装联的表面的间距配合上述喷射气压来调节所述助焊剂的量,由此,通过所述电子装联表面剩余的氧化膜进行净化清除,在保证所述电子装联的表面的氧化膜清除的情况下能够减少助焊剂的
残留,从而提高焊接质量。
23.步骤s4:预热,将所述电子装联移动至预热区进行预加热,所述预热区的加热温度为80
‑
150℃,通过对所述电子装联进行预加热,一方面能够激活所述助焊剂的活性,进一步清除所述电子装联的表面的氧化膜,进而使得所述电子装联的表面的氧化膜充分清除;另一方面能够减少所述电子装联的焊接时间,进而减少所述电子装联的加工时间。
24.步骤s5:焊接,将所述电子装联移动至焊接区进行焊接,焊接时,首先使用焊接机对所述电子装联进行焊接。
25.步骤s6:验证焊接效果,对焊接后的所述电子装联进行机械和电化学可靠性测试。
26.在焊接完成后,通常会对焊点进行检测,首先采用x
‑
ray对所述电子装联的焊点进行无损检测,检测所述电子装联的焊接孔洞率或者是否虚焊,从而能够确保所述电子装联上的焊点无质量缺陷;然后,采用焊接强度测试仪对所述电子装联的焊点进行拉力或剪切力测试,确认焊接强度是否满足要求;采用金相显微镜和扫描电子显微镜(即,scanning electron microscope,简称“sem”),通过切片用来测试金相组织和imc层;采用温湿度试验箱检验焊点耐腐蚀性;最后采用跌落机和振动台,评估焊点的耐冲击性能和焊点的耐疲劳性能。
27.本发明提供的电子装联焊接工艺,通过采用所述等离子还原氧化膜和所述喷涂微量助焊剂,能够对所述电子装联的氧化层进行充分清除,与现有技术中的喷涂大量的所述助焊剂对所述电子装联的氧化层进行充分清除相比,能够减少所述助焊剂的残留,进而提高所述电子装联的服役寿命,同时,与对所述电子装联的氧化膜进行多次射流所述等离子体,来实现所述电子装联的氧化层进行充分清除相比,加工时间较短,进而减少所述电子装联的加工成本。
28.以上述依据本发明的理想实施例为启示,通过上述的说明内容,相关的工作人员完全可以在不偏离本发明的范围内,进行多样的变更以及修改。本项发明的技术范围并不局限于说明书上的内容,必须要根据权利要求范围来确定其技术性范围。