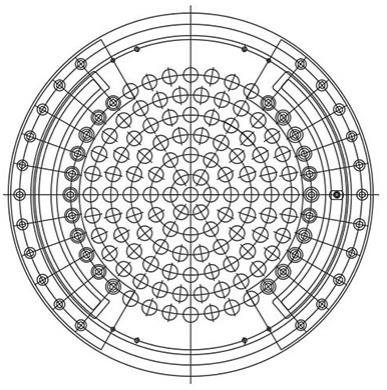
1.本发明涉及航空器件精密加工技术领域,特别涉及一种掺混器冷却面板的加工方法。
背景技术:2.吸气式发动机是航空航天飞行器主要的动力形式,燃油与空气的掺混技术是该类发动机涉及的关键技术之一。掺混效率直接决定了燃烧的进程、效率及稳定性,进而决定发动机的性能。因此,燃油掺混器的设计优化对于吸气式发动机至关重要。
3.掺混器冷却面板是掺混器的重要组成部分,其主要由盖板、底板两部分组成。
4.采用现有工艺对掺混器冷却面板加工时,容易造成以下问题:一是由于底板上的圆孔和盖板上的台阶孔均需加工127个,前期粗铣加工后,由于底板和盖板内部热应力较大,后期直接精铣加工时无法保证精加工精度;二是由于圆孔和台阶孔加工精度均需保证,定位不到位时,会导致精铣的圆孔和台阶孔无法满足精度要求,无法达到底板和盖板的装配要求;三是直接装配盖板和底板时,圆孔和台阶孔的装配间隙小,在钎焊过程中无法保证钎着率,导致钎缝泄露,加工的掺混器冷却面板不达标。
技术实现要素:5.本发明提供了一种掺混器冷却面板的加工方法,解决现有的加工工艺容易导致零件变形、塌陷,影响加工质量和精度的问题。
6.本发明是通过以下方案来实现的:一种掺混器冷却面板的加工方法,步骤如下;a1.在第一圆板的顶面外缘处粗车出环形凹口,使中间形成凸柱;沿所述凸柱顶面向第一圆板底面粗铣多个圆孔;粗车,使原凸柱区向下凹陷形成冷却槽,使圆孔外周形成环柱,使环柱外缘上端形成止口;对第一圆板去应力;精铣所述圆孔,并在所述凹口两边粗铣与所述冷却槽连通的多个流道槽,得到底板;a2.在第二圆板的上表面、下表面分别粗车出第一圆槽、第二圆槽,并在两圆槽之间粗铣多个台阶孔;对第二圆板去应力;精铣所述台阶孔,并在第二圆板与流道槽对应的部位粗车形成水槽,得到盖板;a3.粗车环体,在环体上端面两侧粗车形成倒角,下端面中间粗车出钎料槽,得到加强环;a4.装配底板、盖板与加强环,保证流道槽与水槽对应,环柱向上伸入台阶孔内并在止口与台阶孔上孔之间形成环槽,将加强环置于环槽中,使钎料槽分别与止口底面、台阶孔上孔底面贴合;装配时,在装配间隙中设置钎料;装配后,冷却槽被密封,形成冷却腔;a5.用钎焊工装将底板、盖板和加强环固定,放入真空钎焊炉中钎焊,出炉后得到掺混器冷却面板。
7.进一步地,所述底板、加强环的材质为铬锆铜,盖板的材质为不锈钢或铬锆铜。
8.进一步地,粗铣所述圆孔、台阶孔时,留单边余量1mm,保证台阶孔下孔内径适应于环柱外径,台阶孔上孔内径大于台阶孔下孔内径;加工环柱止口和台阶孔时,在止口上端和台阶孔上端开倒角;粗车环体时,使其外径适应于台阶孔上孔,内径适应于环柱止口。
9.进一步地,对所述第一圆板、第二圆板去应力包括粗车后去应力及粗铣后去应力两个阶段;粗车完成后,去应力的方法为入炉热处理,其中,热处理铬锆铜材质的底板、加强环和盖板时,以150℃
‑
200℃/h的速率加热到500℃
‑
650℃,保温200
‑
300min;热处理不锈钢材质的盖板时,以100℃
‑
150℃/h的速率加热到600℃
‑
690℃,保温200
‑
300min;粗铣完成后,去应力的方法为:在常温下放置2
‑
3天。
10.进一步地,精铣所述圆孔/台阶孔前,用铣加工工装固定所述第一圆板/第二圆板;所述铣加工工装包括直径大于第一圆板/第二圆板且中间开设多个固定孔的底板;所述固定孔与圆孔/台阶孔匹配,固定孔内部可拆卸设置由固定杆、垫片和锁紧件组成的紧固件;固定时,固定杆头部贯穿所述圆孔/台阶孔并固定在固定孔中,垫片、锁紧件依次套接在固定杆尾部,向下压紧第一圆板/第二圆板。
11.进一步地,精加工所述圆孔/台阶孔的方法为:以第一圆板/第二圆板的横轴线、纵轴线以及对角连线上的圆孔/台阶孔为定位点;将紧固件固定在各定位点处,精铣定位点以外的圆孔/台阶孔;逐圈拆除紧固件,精铣各定位点处的圆孔/台阶孔,精铣时,保证被精铣圆孔/台阶孔相邻的定位点被固定。
12.进一步地,所述膏状钎料和粘带钎料均为镍基钎料;所述膏状钎料的设置间隙包括:钎料槽内部,加强环底面与止口底面、台阶孔上孔底面之间的间隙,加强环内周与止口、加强环外周与台阶孔上孔之间的间隙,台阶孔倒角与加强环外侧倒角、止口倒角与加强环内侧倒角之间的间隙,以及底板与盖板接触面外缘的间隙;所述粘带钎料的设置间隙包括:底板与盖板接触面之间的间隙。
13.进一步地,真空钎焊的具体步骤如下:装炉:打开炉门,将零件水平置于真空钎焊炉有效均温区,随即关好炉门;抽真空:冷态抽真空,使炉内真空度达到2
×
10
‑2pa;加热程序:按以下工艺参数编程以60℃
‑
110℃/h的速率加热到380℃
‑
500℃,保温40
‑
60min;以100℃
‑
150℃/h的速率加热到880℃
‑
990℃,保温300
‑
450min;以130℃
‑
180℃/h的速率加热到1010℃
‑
1050℃,开始钎焊,保持30
‑
60min;冷却程序:钎焊完成后冷却至65℃出炉。
14.进一步地,得到掺混器冷却面板后,还需对其进行如下处理:s1.目视检验钎缝,钎缝无缺陷时,在1mpa气压下进行气密试验;s2.水槽中加塞棉布,精车掺混器冷却面板至设计尺寸;s3.水压试验,在4mpa水压下,保压10min,保证钎缝无泄漏。本发明具有以下优点:1).在底板的环柱上设置了止口,在盖板上设置了台阶孔,并设置了尺寸与环柱止口和台阶孔上孔之间形成的环槽匹配的加强环,通过将加强环装配在环槽中,增加了底板
环柱和盖板台阶孔部位的接触面积,能够保证二者钎焊时的钎着率,进而保证冷却腔的密封性;2).在粗车、粗铣完底板的圆孔和盖板的台阶孔后,分别对底板和盖板进行热处理,去除零件内部的热应力,之后再对圆孔和台阶孔进行精铣加工,更能保证加工的精度;3).为了保证底板的127个圆孔和盖板的127个台阶孔的加工、装配精度,设置了铣加工工装,在精铣圆孔和台阶孔的过程中,根据实际加工位置,将铣加工工装固定在相应的定位点,保证底板和盖板被精确固定,更进一步保证圆孔和台孔的精度;装配时,使得127个圆孔和127个台阶孔能够精准对齐,保证装配后的接触面积,提高钎着率。
附图说明
15.图1为底板的俯视图;图2为底板沿横轴线的剖面图;图3为铣加工工装固定底板时的示意图;图4为盖板的俯视图;图5为盖板沿横轴线的剖面图;图6为铣加工工装固定盖板的示意图;图7为加强环的俯视图;图8为加强环沿横轴线的剖面图;图9为底板、盖板和加强环的装配图;图10为钎焊工装的俯视图;图11为钎焊工装固定底板、盖板和加强环的示意图;图12为测试工装的俯视图;图13为测试工装密封掺混器冷却面板的示意图;图中:1
‑
底板,2
‑
盖板,30
‑
底板,31
‑
固定杆,32
‑
垫片,33
‑
锁紧件,4
‑
加强环,50
‑
底座,51
‑
压板,52
‑
压盖,53
‑
主杆,54
‑
锁扣,60
‑
固定座,61
‑
扇形板,62
‑
密封杆,63
‑
密封扣,64
‑
o型密封圈,65
‑
接管嘴。
具体实施方式
16.下面结合具体实施方式对本发明进行详细的说明。
17.一种掺混器冷却面板的加工方法,步骤如下;a1.采用铬锆铜材料粗车形成第一圆板,在第一圆板的顶面外缘处粗车出环形凹口,使第一圆板上表面中间区域形成圆形凸柱,将第一圆板入炉,以150℃
‑
200℃/h的速率加热到500℃
‑
650℃,保温200
‑
300min,去除内部应力;沿凸柱顶面向第一圆板底面均匀粗铣出127个圆孔,留单边余量1mm,在常温下放置2
‑
3天,去除内部应力;粗车去除多余凸柱,使原凸柱区向下凹陷形成冷却槽,使圆孔外周形成环柱,在环柱的外缘上端粗车出止口,并在止口上端开设倒角;精铣圆孔前,用铣加工工装将第一圆板固定,具体的,如图3所示,铣加工工装包括直径大于第一圆板且中间开设多个与圆孔匹配的多个固定孔的底板30,固定孔内部可拆卸设置由固定杆31、垫片32和锁紧件33组成的紧固件,固定第一圆板时,固定杆31头部贯穿圆
孔并固定在固定孔中,垫片32、锁紧件33依次套接在固定杆31尾部,向下压紧第一圆板;精铣圆孔时,以第一圆板的横轴线、纵轴线以及对角连线上的圆孔为定位点;将紧固件固定在各定位点处,精铣定位点以外的圆孔,逐圈拆除紧固件,精铣各定位点处的圆孔,精铣过程中,保证与被精铣圆孔相邻的定位点被固定;精铣完圆孔后,在第一圆板环形凹口的两边粗铣出与冷却槽连通的40个流道槽,得到如图1、图2所示的底板1;a2.采用不锈钢材料或铬锆铜材料粗车形成第二圆板,在第二圆板的上表面、下表面分别粗车出第一圆槽、第二圆槽,保证第一圆槽的直径小于第二圆槽;当采用铬锆铜时,粗车完成后,将第二圆板入炉,以150℃
‑
200℃/h的速率加热到500℃
‑
650℃,保温200
‑
300min,去除内部应力;当采用不锈钢材质时,粗车完成后,将第二圆板入炉,以100℃
‑
150℃/h的速率加热到600℃
‑
690℃,保温200
‑
300min,去除内部应力;在两个圆槽之间粗铣127个台阶孔,留单边余量1mm;粗铣时保证台阶孔下孔的内径适应于环柱的外径,台阶孔上孔的内径大于台阶孔下孔的内径,并在台阶孔上端开设倒角;粗铣完成后,在常温下放置2
‑
3天,使应力自然释放;精加工台阶孔前,再次用铣加工工装将第二圆板固定,具体的,如图6所示,将固定杆31头部贯穿台阶孔并固定在固定孔中,将垫片32、锁紧件33依次套接在固定杆31尾部,向下压紧第二圆板;精铣台阶孔时,以第二圆板的横轴线、纵轴线以及对角连线上的台阶孔为定位点;将紧固件固定在各定位点处,精铣定位点以外的台阶孔,逐圈拆除紧固件,精铣各定位点处的台阶孔,精铣过程中,保证被精铣圆孔相邻的定位点被固定;精铣完台阶孔后,在第二圆板与第一圆板流道槽对应的位置处粗车加工出水槽,得到如图4、图5所示的盖板2;a3.采用铬锆铜材料粗车加工外径适应于台阶孔上孔,内径适应于环柱止口的环体,保证环体的厚度为3.5mm;在环体上端面两侧粗车出倒角,下端面中间粗车出钎料槽,得到如图7、图8所示的加强环4;a4.对底板1、盖板2和加强环4去毛刺、清洗;装配底板1、盖板2与加强环4,具体装配图如图9所示:在底板1与盖板2的接触面粘贴一层镍基粘带钎料,将盖板2放置在底板1上,保证流道槽与水槽对应,并在底板1与盖板2接触面外缘的间隙部位涂注膏状钎料;盖板2放置在底板1上后,底板1的环柱伸入盖板2的台阶孔内,使环柱止口与台阶孔上孔之间形成环槽;在加强环4钎料槽内部,止口底面、台阶孔上孔底面部位涂注膏状钎料,将加强环4装配在环槽中,沿台阶孔倒角与加强环4外侧倒角、止口倒角与加强环内侧倒角部位向加强环内周与止口、加强环外周与台阶孔上孔之间的间隙中涂注膏状钎料至倒角部位填满钎料;a5.用如图10所示的钎焊工装将底板1、盖板2和加强环4固定,具体的,如图11所示,钎焊工装包括直径大于底板和盖板的底座50,底座50环周均匀设有多个外定位孔,底座50与底板1重合的区间内设有多个与圆孔匹配的内定位孔;在外定位孔与最外圈内定位孔之间设置有多个带孔的压板51,压板51上的孔设置在压板51两端,以底座50中心的内定位孔和与之等距的六个内定位孔为中心固定孔,在中心固定孔上方设有带孔压盖52,压盖52底部设置有凹槽,凹槽与压盖上的孔相连通,形成台阶槽;在压板孔与外定位孔之间,压板孔与底板圆孔、内定位孔之间,压盖孔与中心固定孔之间均设置由主杆53和锁扣54组成的
多个压紧件;固定底板1、盖板2和加强环4时,将装配好的底板1、盖板2和加强环4放置在底座50上方,并保证内定位孔与底板的圆孔位置对应,将多个带孔压板51放置在盖板2的边缘部位,使压板51两端的孔分别与底板1圆孔、外定位孔位置对应,并将压盖52放置在中心固定孔上方,使压盖孔与中心固定孔对应,并使压盖52底部凹槽外周的凸棱压紧加强环4的上部,使加强环4底部与台阶孔上孔底面及环柱止口底面相贴合;将多个主杆53头部分别沿压板孔、压盖孔向下贯穿,最终固定在外定位孔和内定位孔中,并将锁扣固定在主杆53尾部,装配后,冷却槽被密封,形成冷却腔;固定中心定位孔部位的锁扣54时,需手动拧紧,避免钎焊时掺混器面板盖板中间部分塌陷;将固定后的底板1、盖板2和加强环4一并置于真空钎焊炉中,通过以下程序进行真空钎焊:装炉:打开炉门,将零件水平置于真空钎焊炉有效均温区,随即关好炉门;抽真空:冷态抽真空,使炉内真空度达到2
×
10
‑2pa;加热程序:按以下工艺参数编程以60℃
‑
110℃/h的速率加热到380℃
‑
500℃,保温40
‑
60min;以100℃
‑
150℃/h的速率加热到880℃
‑
990℃,保温300
‑
450min;以130℃
‑
180℃/h的速率加热到1010℃
‑
1050℃,开始钎焊,保持30
‑
60min;冷却程序:钎焊完成后冷却至65℃出炉。钎焊完成后,将底板1、盖板2和加强环4取出,拆除钎焊工装,得到掺混器冷却面板;得到掺混器冷却面板后,还需对其进行如下处理:s1.目视检验钎缝,钎缝无缺陷时,在1mpa气压下进行气密试验;s2.在盖板的水槽中加塞棉布,精车掺混器冷却面板至设计尺寸;s3.水压试验,在4mpa水压下,保压10min,保证钎缝无泄漏;具体的,水压测试前,用如图12所示的测试工装将掺混器冷却面板密封固定;测试工装包括直径大于底板和盖板的固定座60,在固定座上方设置两个弧度大于水槽且底面开设扇形槽的扇形板61,并在其中一个扇形板61上设置与水槽对应的接管嘴65;固定座60环周开设多个外安装孔,内部开设多个与底座外圈圆孔匹配的内安装孔,扇形板61外周开设与外安装孔对应的外密封孔,内周开设与内安装孔匹配的内密封孔;外安装孔与外密封孔,内安装孔与内密封孔之间设置多个由密封杆62和密封扣63组成的密封件;密封时,如图13所示,将固定掺混器冷却面板放置在固定座60的上方,使内安装孔与底板外圈的圆孔位置对应,在盖板的水槽内周和外周分别设置一个0型密封圈64,并将扇形板61放置在o型密封圈64上方,使o型密封圈顶部伸入扇形板61底面开设的扇形槽中,保证外安装孔与外密封孔,内安装孔与内密封孔分别对应;将多个密封杆62头部分别沿外密封孔和内密封孔向下贯穿,并固定在固定座60的外安装孔、内安装孔中,将密封扣63固定在密封杆62上端,将o型密封圈64压紧,使掺混器冷却面板完全密封;在接管嘴65上连接水管,向掺混器冷却面板内部的冷却腔中注水,在4mpa水压下,保压10min,若水无泄漏,则说明加工的掺混器冷却面板达标。
18.本发明的有益效果是:在底板的环柱上设置了止口,在盖板上设置了台阶孔,并设
置了尺寸与环柱止口和台阶孔上孔之间形成的环槽匹配的加强环,通过将加强环装配在环槽中,增加了底板环柱和盖板台阶孔部位的接触面积,能够保证二者钎焊时的钎着率,进而保证冷却腔的密封性;在粗车、粗铣完底板的圆孔和盖板的台阶孔后,分别对底板和盖板进行热处理,去除零件内部的热应力,之后再对圆孔和台阶孔进行精铣加工,更能保证加工的精度;为了更进一步保证底板的127个圆孔和盖板的127个台阶孔的加工、装配精度,设置了铣加工工装,在精铣圆孔和台阶孔的过程中,根据实际加工位置,将铣加工工装固定在相应的定位点,保证底板和盖板被精确固定,更进一步保证圆孔和台孔的精度;装配时,使得127个圆孔和127个台阶孔能够精准对齐,保证装配后的接触面积,提高钎着率。
19.本发明的内容不限于实施例所列举,本领域普通技术人员通过阅读本发明说明书而对本发明技术方案采取的任何等效的变换,均为本发明的权利要求所涵盖。