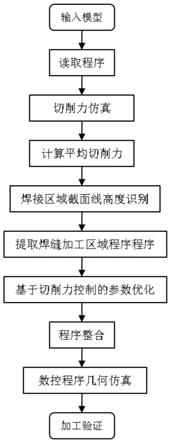
1.本发明属于航空航天数控加工技术领域,尤其适用于航空发动机零部件焊接转接部位的变参数切削力控制下的机械加工。
背景技术:2.整体叶盘在为发动机带来减重、减级、增效和高可靠性的同时,也给发动机维修保障带来了新的挑战。整体叶盘结构复杂、制造难度大、加工周期长、价格昂贵,在制造、试验和工作过程中不可避免地会出现尺寸超差或损伤。以某大型风扇整体叶盘为例,叶身型面采用1把刀具加工1片叶片的方式完成叶片精加工。由于叶片长度接近300mm,叶身刚性弱,精加工时需要预留1mm以上的余量用于增强叶片刚性,通过粗精混合铣的方式完成叶片加工。因叶片余量较大,切削时间较长,国产刀具很难实现1把刀具加工1片叶片的任务;进口刀具加工成本较高,且受限于加工工况,个别叶片仍会出现加工崩刃、加工颤振的情况,影响加工表面质量。
3.为提升整体叶盘的加工效率、降低整体叶盘的加工成本,同时为了整体叶盘的修复及再制造,国内进行了焊接类整体叶盘的技术探索,并且研制了线性摩擦焊整体叶盘零件。然而,线性摩擦焊相关研究表明,焊缝部位材料经历动态再结晶,在焊缝区有明显剪切结构,切削性能改变,目前线性摩擦焊焊后采用通用cam软件编制数控加工程序,只考虑几何空间可达性,而未考略焊缝区域材料属性的变化进而导致的切削力不稳定,加工线性摩擦焊接叶盘叶片焊缝区域较加工叶片母材区域相比机床主轴振动明显,部分叶片加工有刀具崩刃现象,叶片焊缝区域有明显振纹,到目前为止,尚没有公开的基于切削力预调整的焊接类整体叶盘焊缝质量预控制方法。
技术实现要素:4.为解决上述问题,本发明公开一种基于切削力预调整的焊接类整体叶盘焊缝质量控制方法。
5.具体技术方案如下:
6.一种基于切削力预调整的焊接类整体叶盘焊缝质量控制方法,包括如下步骤:
7.步骤1,导入零件的cad模型,使模型尺寸与设计尺寸一致;
8.步骤2,导入数控程序,支持g代码文件;
9.步骤3,完成数控程序切削力仿真,计算平均切削力;
10.步骤4,整体叶盘叶片焊接区域截面线高度识别;
11.步骤5,根据叶片截面线识别结果提取焊缝加工区域数控程序;
12.步骤6,对提取的数控程序进行优化,调整焊缝加工区域数控程序的切削参数,直到焊接区域最大单方向平均切削力为原程序平均切削力最大值的80%,完成焊缝加工区域的数控程序优化;所述原程序平均切削力包括平均切向力平均径向力及平均轴向力
所述平均切削力的计算方式如下:所述平均切削力的计算方式如下:其中t为时间,f为力,t为总时间,所述最大单方向切向平均切削力为三个方向的平均切削力的最大数值;
13.步骤7,将步骤三中优化的数控程序与原数控程序接合,完成数控程序整合;
14.步骤8,完成带机床的数控程序加工过程仿真验证,保证优化后数控程序的加工可达性;
15.步骤9,应用优化后的数控程序进行加工验证;
16.所述对焊缝区域提取的数控程序中每段程序的切削力最大值均小于最大单方向平均切削力;
17.所述焊接区域最大单方向平均切削力为原程序平均切削力最大值的80%,是通过调整数控机床的转速、进给来实现的;
18.所述切削力仿真是通过production module软件来实现的。
19.本发明的优点是:本发明首次提出面向航空发动机大型风扇焊接叶盘焊接叶片加工质量控制方法,基于变参数切削力控制方法有效解决焊接叶片切削加工中刀具崩刃现象,消除刀具崩刃带来零件报废的潜在问题,改善零件表面加工质量。
附图说明
20.图1为本发明的基于变参数大型风扇焊接叶盘加工质量控制方法流程图;
21.图2为本发明案例中应用的零件示意图。
22.图3为本发明案例中零件截面示意图。
23.图4为零件原有数控程序切削力仿真结果示意图;
24.图5为程序经过打断优化后的切削力仿真结果示意图;
25.图6为程序打断优化前后的代码对比。
具体实施方式
26.本发明采用切削力预调整的技术手段,通过分析模型、设置数控程序、切削力预测、焊接区域数控程序提取、针对焊接区域的数控加工切削力调控等方式加工线性摩擦焊整体叶盘的叶身型面,解决焊接叶盘在加工叶片焊接焊缝区域材料属性与母材区属性差异造成的切削力突变所引发的刀具崩刃及零件表面加工质量不稳定问题,成功实现线性摩擦焊整体叶盘的加工及质量控制,本发明以航空发动机某大型风扇钛合金整体叶盘焊接件为例,结合附图和实施过程对本发明作进一步说明,如图所示,一种基于切削力预调整的焊接类整体叶盘焊缝质量控制方法,包括如下步骤:
27.1)导入零件的cad模型,使所述模型尺寸与设计尺寸一致。
28.2)导入数控程序,支持g代码文件。
29.3)完成数控程序切削力仿真,计算平均切削力。
30.所述的平均切削力计算,指计算出有效切削过程平均切向力平均径向力及平均轴向力计算方式及结果如下:
[0031][0032]
4)整体叶盘叶片焊接区域截面线高度识别,如图3所示。
[0033]
5)在数控程序中检索加工焊接区域的进刀点(x100.9124,
‑
70.2018y,262.6176),标记出该条程序n145482;检索加工焊接区域的退刀点(20.3756,
‑
89.5170,360.0874),标记出该条程序n242254,两条程序及中间涵盖所有程序为焊缝加工区域数控程序,提取并保存为.apt文件。
[0034]
6)根据数控程序切削力仿真结果,原始数控程序最大径向切削力可以达到200n,且切削力变化剧烈,其中,焊接区域附近材料受高温高压影响,性能发生变化,需要对该区域的切削力进行进一步控制,如图4所示,横轴代表时间,纵轴代表切削过程中产生的切削力;图中实线是通过计算得到的平均切削力,平均切向力13n,平均径向力80n,平均轴向力为20n;
[0035]
本实施例中,以最大切削力径向切削力为约束对象,将最大切削力的约束条件定义为原平均切削力数值的80%:
[0036][0037]
按照最大切削力约束条件定义为64n,完成焊缝加工区域的数控程序优化;
[0038]
进一步地,通过切削力仿真软件(production module)可以得到在所述提取数控程序,优化后重新计算数控程序的平均径向切削力为44n,如图5所示,图中第一条实线是数控切削过程的切削力上限,为60n;图中虚线是通过计算得到的平均切削力,为44n,优化后的数控程序,相比于图1中的80n,不仅最大径向切削力得到控制,平均径向切削力更是降低了1倍,保证了切削过程的稳定性。
[0039]
7)将优化的数控程序重新写入到原数控程序中,覆盖对应的原始数控程序段,完成数控程序整合,整合后的数控程序可以直接观察到进给的变化。
[0040]
8)将优化后的数空程序导入到几何仿真软件中,完成带机床的数控程序加工过程仿真验证,保证优化后数控程序的加工可达性。
[0041]
9)应用优化后的数控程序进行加工验证;
[0042]
本发明的有益效果是:针对大型风扇焊接叶盘叶片焊接焊缝区域材料属性与母材区属性差异造成的数控加工切削力陡增,进而引发的刀具崩刃及零件表面加工质量不稳定问题,通过仿真软件读取数控加工程序,识别提取加工焊缝区域关键数控程序段,对焊缝加工区域程序分度分段,基于变参数切削力控制原则,从切削力入手针对焊缝区域关键数控程序段开展切削力优化,重新整合形成焊缝区域切削力受控数控程序,保证机械加工过程中切削力平顺,实现大型风扇焊接叶盘焊接叶片数控程序加工质量控制,进而保证零件的加工质量。