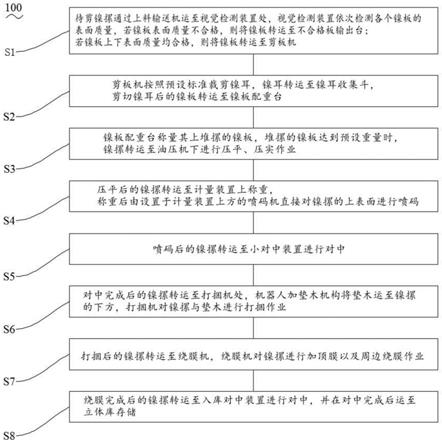
1.本发明涉及电镍的加工包装技术领域,特别是涉及一种电镍智能加工包装方法。
背景技术:2.在电解镍板或电积镍板的生产工艺流程中,需要对电镍进行剪耳、摞板、配重、压平、称重、喷码、打捆、绕膜、对中、入库等生产工艺,且由于工艺流程、工艺参数、后续处理等诸多因素,镍板表面会出现气孔、结粒、夹杂、烧板、裂痕、水印、商标缺失或错位、油污、脚印等缺陷,需要将存在缺陷的镍板剔除。目前,镍板的表面质量检测主要由人工完成,需要人工分片后一张张查看,发现不合格镍板后用粉笔标识并将其挑出。而打捆工序也都得由人工进行加垫木操作。此外,镍板的配重过程也需要人工进行抬板称重。上述电镍加工包装的整体的智能化水平低,需要依靠大量的人力实现,导致传统电镍加工包装方法存在设备噪音大、生产效率低、劳动强度大、劳动定员多、安全隐患大、生产落后、成本高等问题。目前,关于电镍的加工包装并没有完整的自动化机组,只能实现电镍的部分加工包装工艺的自动化与智能化。
3.因此,设计一种结构简单、自动化与智能化程度高、能够实现电镍加工包装的全流程自动化作业的电镍智能加工包装方法就很有必要。
技术实现要素:4.为了克服上述问题,本发明提供一种电镍智能加工包装方法,该方法采用5g技术、机器人技术、视觉技术、agv技术、远程操控技术、工业互联网技术、云平台、以及数字孪生技术,实现了电镍从上料、视觉板面质量检测及定位、镍耳剪切、摞板及配重、压平、称重及喷码、对中、打捆、绕膜、对中、入库等一系列自动化加工,极大地降低了电镍加工包装生产车间中工人劳动强度及安全隐患,能够有效提升生产效率,实现了电镍加工包装全流程自动化、智能化、无人化的生产。
5.为实现上述的目的,本发明采用的技术方案是:
6.一种电镍智能加工包装方法,包括以下步骤:
7.s1、待剪镍摞通过上料输送机运至视觉检测装置处,视觉检测装置依次检测各个镍板的表面质量,若镍板表面质量不合格,则将镍板转运至不合格板输出台;若镍板上下表面质量均合格,则将镍板转运至剪板机;
8.s2、剪板机按照预设标准裁剪镍耳,镍耳转运至镍耳收集斗,剪切镍耳后的镍板转运至镍板配重台;
9.s3、镍板配重台称量其上堆摞的镍板,堆摞的镍板达到预设重量时,镍摞转运至油压机下进行压平、压实作业;
10.s4、压平后的镍摞转运至计量装置上称重,称重后由设置于计量装置上方的喷码机直接对镍摞的上表面进行喷码;
11.s5、喷码后的镍摞转运至小对中装置进行对中;
12.s6、对中完成后的镍摞转运至打捆机处,机器人加垫木机构将垫木运至镍摞的下方,打捆机对镍摞与垫木进行打捆作业;
13.s7、打捆后的镍摞转运至绕膜机,绕膜机对镍摞进行加顶膜以及周边绕膜作业;
14.s8、绕膜完成后的镍摞转运至入库对中装置进行对中,并在对中完成后运至立体库存储。
15.进一步的,在步骤s1中,视觉检测装置对镍板进行表面质量检测包括以下步骤:
16.s11、待剪镍摞上料至第一待剪镍摞工位,上表检遮光罩及光源下降,遮住最上一张镍板上表面环境光,上表检视觉相机对最上一张镍板的上表面拍照,并将拍好的图片传输至智能控制装置及图像处理装置;
17.s12、上表检遮光罩升起,图像处理装置判断当前镍板的上表面是否合格;若检测不合格,则执行s13,若检测合格,则执行s14;
18.s13、图像处理装置判定镍板被上料机械手抓取时位于上料机械手上的位置信息,并将该信息上传至智能控制装置,智能控制装置计算出镍板放置在不合格板输出台上的位移距离以及偏移角度,并控制上料机械手直接将镍板送至不合格板输出台上整齐堆摞,当镍板堆摞到预定数量时,将不合格镍板整摞运走;
19.s14、上料机械手吸取最上一张镍板,移动至下表检遮光罩及光源及下表检视觉相机的上方,下表检视觉相机对镍板的下表面拍照,并将拍好的照片传输至智能控制装置及图像处理装置;视觉检测装置判定镍板被上料机械手抓取时位于上料机械手上的位置信息,并将检测结果反馈给智能控制装置,智能控制装置计算出镍板放置在剪板机上的位移距离以及偏移角度。
20.进一步的,所述图像处理装置内置视觉算法以及缺陷图片数据库,当所述上表检视觉相机和所述下表检视觉相机将拍摄的镍板的图片上传至所述图像处理装置时,所述图像处理装置将图片分割成多个像素点,并将各个像素点与缺陷图片数据库分别进行比对;所述视觉算法智能识别镍板板面轮廓及各种表面缺陷,并运算得出缺陷区域及其边界线,所述视觉算法随后依次判定该张镍板是属于合格或不合格板,以及镍板在所述上料机械手上的位置信息。
21.进一步的,所述智能控制装置内置智能控制系统,所述智能控制系统采用5g技术、机器人技术、视觉技术、agv技术、远程操控技术、工业互联网技术、云平台、以及数字孪生技术;所述智能控制系统与远程移动设备信号连接,以将各个环节的所有生产信息上传到工业互联网,作业人员通过手机、平板、电脑远程查看各种生产数据、设备状况、故障信息、历史记录回看、产品信息追溯,并可以导出生产报表。
22.进一步的,在步骤s2中,镍耳的裁剪标准为上料机械手按照镍板裁剪后镍耳长度≤10mm直接将镍板送至剪板机的剪刃下,剪下的电镍吊耳掉落至剪板机后方的镍耳水平输送机,并由镍耳水平输送机将镍耳输送至镍耳上扬输送机,镍耳上扬输送机进而输送镍耳至镍耳收集斗内。
23.进一步的,在步骤s3中,所述镍板配重台上设置有电子称,所述电子称称量镍摞的重量,当型号为ni9996的镍摞堆摞至重量为1470~1530kg时,镍摞转运至所述油压机,当型号为ni9997的镍摞堆摞至重量为1800~2200kg时,镍摞转运至所述油压机。
24.进一步的,所述镍板配重台的两侧分别设置有上配板台与下配板台,所述上配板
台与下配板台上预先放置一些偏重或偏轻的镍板,当配重的最后一张镍板放置在所述镍板配重台后镍摞的重量不合适时,所述下料机械手将最后一张镍板调换为偏重或偏轻的镍板以完成配重作业。
25.进一步的,在步骤s4中,所述喷码的内容包括生产厂家、品名、批号、包号、生产日期、重量、以及质检人员。
26.进一步的,在步骤s3至步骤s5中,镍板的转运通过自动导引运输车系统实现;在步骤s6至步骤s8中,镍板的转运通过打包输送机实现。
27.进一步的,所述电镍智能加工包装方法还适用于铜板、钴板、铝板、钢板、以及非金属材料的加工包装。
28.与现有技术相比,本发明的有益效果是:
29.1.本发明的电镍智能加工包装方法,通过设置自动导引运输车系统,并在自动导引运输车系统的外侧依次围设有多组剪切单元、油压机、计量装置、喷码装置、以及小对中装置,自动导引运输车能够往返于上述各个装置之间,实现镍板的自动化转运,并在小对中装置的输出端设置打包输送机,打包输送机的沿线依次设置打捆机、机器人加垫木机构、绕膜机、以及入库对中装置,从而将计量喷码后的镍摞连续进行一系列自动化包装,进而实现电镍从上料、视觉板面质量检测及定位、镍耳剪切、摞板及配重、压平、称重及喷码、对中、打捆、绕膜、对中、入库等一系列自动化加工,极大地降低了工人劳动强度及安全隐患,能够有效提升生产效率,实现了电镍加工包装全流程自动化、智能化、无人化的生产。此外,本技术采用各种自动化技术,能够显著降低操作人员的劳动强度,实现1个操作工人代替8-10人/班组的操作工人,减少了劳动定员,显著降低了人力成本,减少了人工加工安全隐患。
30.2.本发明的电镍智能加工包装方法,通过采用视觉系统自动对镍板进行表面质量检测及视觉定位,能够快速剔除缺陷镍板,并对合格镍板进行标记以便于后续切割耳料。此外,本技术设置配重装置与自动化加垫木装置,实现了现有机组的配重及加垫木的自动化工艺,实现了整个机组的全流程的无人化作业,不需要要人工参与或设置其他定位机构及定位动作等,大大提高了生产效率,降低了生产成本及生产安全隐患。
31.3.本发明的电镍智能加工包装方法,通过将智能控制装置与远程移动终端连接,便于作业人员进行远程操作或远程查看电镍加工包装生产情况,并能够远程导出当天生产报表及产品历史记录追溯,提高了电镍加工包装行业自动化及智能化程度,解决了目前电镍加工包装行业自动化与智能化水平较低的行业难题,显著提升生产效率并提高了整体产品的品级率,提高了企业效益及企业形象。
32.4.本发明的电镍智能加工包装方法,通过采用5g技术、机器人技术、视觉技术、agv技术、远程操控技术、工业互联网技术、云平台、数字孪生技术等,证明了新技术可在电脑加工包装行业中应用的可行性,为电镍加工包装行业及其他行业智能化应用中提供了参考实例。
附图说明
33.图1是本发明的电镍智能加工包装方法的流程示意图;
34.图2是本发明的电镍智能加工包装方法的工艺流程图;
35.图3是本发明的电镍智能加工包装机组的结构示意图;
36.图4是图3中a区域的局部放大示意图;
37.图5是图3中b区域的局部放大示意图;
38.附图中各部件的标记如下:1、不合格板输出台;2、不合格板;3、上料机械手;4、待剪镍摞;5、上料输送机;6、上表检视觉相机;7、上表检遮光罩及光源;8、下表检视觉相机;9、下表检遮光罩及光源;10、剪板机;11、镍耳水平输送机;12、镍耳上扬输送机;13、镍耳收集斗;14、操作台;15、安全围栏;16、下料机械手;17、下配板台;18、镍板配重台;19、上配板台;20、显示大屏;21、油压机;22、自动导引运输车;23、智能控制装置;24、小对中装置;25、喷码装置;26、计量装置;27、液压伺服系统;28、垫木托盘;29、机器人加垫木机构;30、打捆机;31、绕膜机;32、打包输送机;33、入库对中装置;34、配电柜组。
具体实施方式
39.为了使本发明的目的、技术方案和优点更加清楚,下面结合附图和具体实施例对本发明进行详细描述。
40.在此,还需要说明的是,为了避免因不必要的细节而模糊了本发明,在附图中仅仅示出了与本发明的方案密切相关的结构和/或处理步骤,而省略了与本发明关系不大的其他细节。
41.另外,还需要说明的是,术语“包括”、“包含”或者其任何其他变体意在涵盖非排他性的包含,从而使得包括一系列要素的过程、方法、物品或者设备不仅包括那些要素,而且还包括没有明确列出的其他要素,或者是还包括为这种过程、方法、物品或者设备所固有的要素。
42.实施例1
43.如图1至3所示,一种电镍智能加工包装方法100,通过建立电镍智能加工包装机组200,并采用5g技术、机器人技术、视觉技术、agv技术、远程操控技术、工业互联网技术、云平台、以及数字孪生技术,实现电镍从上料、视觉板面质量检测及定位、镍耳剪切、摞板及配重、压平、称重及喷码、对中、打捆、绕膜、对中、入库等一系列自动化加工。值得注意的是,本技术的电镍加工包装方法也可在铜板、钴板、铝板、钢板、非金属材料的加工包装中进行应用。
44.电镍智能加工包装机组200,包括智能控制装置23、至少一个剪切单元、设置于剪切单元的一侧的自动导引运输车系统、依次设置于自动导引运输车系统外侧的油压机21、计量装置26、喷码装置25、小对中装置24、与小对中装置24连接的打捆机30、设置于打捆机30下侧的机器人加垫木机构29、与打捆机30连接的绕膜机31、以及与绕膜机31连接的入库对中装置33。剪切单元可以根据需要设置为不同的数量,在本电镍智能加工包装机组200中,剪切单元设置为两组,且二者的结构完全相同,包括剪切单元a与剪切单元b。
45.电镍智能加工包装方法100,包括以下步骤:
46.s1、待剪镍摞4通过上料输送机5运至视觉检测装置处,视觉检测装置依次检测各个镍板的表面质量,若镍板表面质量不合格,则将镍板转运至不合格板输出台1;若镍板上下表面质量均合格,则将镍板转运至剪板机10。
47.在本步骤中,视觉检测装置对镍板进行表面质量检测包括以下步骤:
48.s11、待剪镍摞4通过上料输送机5上料至第一待剪镍摞工位,设置于第一待剪镍摞
工位的上方的上表检遮光罩及光源7下降,遮住最上一张镍板上表面环境光,避免环境光照射到镍板上表面。位于上表检遮光罩内的上表检视觉相机6对最上一张镍板的上表面拍照,并将拍好的图片传输至智能控制装置23及图像处理装置。
49.智能控制装置23及图像处理装置采用数字孪生技术,远程实时反映各设备状态状况与所有生产信息,并采用移动触摸屏技术操作控制整个电镍加工包装生产。
50.具体来讲,智能控制装置23与远程移动设备通讯连接,并包括设置于安全围栏15外侧的操作台14与显示大屏20。远程移动设备为手机、平板、电脑等。智能控制装置23内置智能控制系统。智能控制系统采用5g技术、机器人技术、视觉技术、agv技术(自动导引运输技术)、远程操控技术、工业互联网技术、云平台、以及数字孪生技术。智能控制系统与远程移动设备信号连接,以将各个环节的所有生产信息上传到工业互联网,作业人员通过手机、平板、电脑远程查看各种生产数据、设备状况、故障信息、历史记录回看、产品信息追溯,并可以导出生产报表。同时,作业人员也可以通过5g技术远程操控生产设备。特别的,智能控制系统采用移动触摸屏技术操作控制整个电镍加工包装生产,整个机组智能化水平较高。智能控制装置23及控制柜组、以及配电柜组34均采用强弱电分离的方式,方便故障检修及减少控制系统信号干扰。
51.s12、上表检遮光罩升起,图像处理装置判断当前镍板的上表面是否合格;若检测不合格,则执行s13,若检测合格,则执行s14。
52.在本步骤中,图像处理装置内置视觉算法以及缺陷图片数据库,当上表检视觉相机6和下表检视觉相机8将拍摄的镍板的图片上传至图像处理装置时,图像处理装置将图片分割成多个像素点,并将各个像素点与缺陷图片数据库分别进行比对。视觉算法智能识别镍板板面轮廓及各种表面缺陷,并运算得出缺陷区域及其边界线,视觉算法随后依次判定该张镍板是属于合格或不合格板,以及镍板在上料机械手3上的位置信息,便于后续将不合格镍板输出以及对合格镍板进行定位裁剪镍耳的工艺。
53.s13、图像处理装置判定镍板被上料机械手3抓取时位于上料机械手3上的位置信息,并将该信息上传至智能控制装置23。智能控制装置23计算出镍板放置在不合格板输出台1上的位移距离以及偏移角度,并控制上料机械手3直接将镍板送至不合格板输出台1上整齐堆摞,当镍板堆摞到预定数量时,将不合格板2整摞运走。
54.如图4所示,在本步骤中,上料机械手3设置于剪板机10上方并位于靠近视觉检测装置一侧,上料机械手3与智能控制装置23信号连接,由智能控制装置23控制上料机械手3的动作。上料机械手3为多自由度机械手,并设置有用于吸取镍板的负压装置。同时,依据本领域技术人员对于本技术的技术方案的理解,上料机械手3也可以设置成吸取机器人、桁架伺服系统、以及组合夹具构成对镍板进行抓取及转运的自动化装置。
55.s14、上料机械手3吸取最上一张镍板,移动至下表检遮光罩及光源9及下表检视觉相机8的上方,下表检视觉相机8对镍板的下表面拍照,并将拍好的照片传输至智能控制装置23及图像处理装置。视觉检测装置判定镍板被上料机械手3抓取时位于上料机械手3上的位置信息,并将检测结果反馈给智能控制装置23,智能控制装置23计算出镍板放置在剪板机10上的位移距离以及偏移角度,以便于后续剪切镍耳时能够将镍板自动放置在适宜位置处。
56.在本步骤中,下表检遮光罩挡住环境光,避免环境光照射到镍板的下表面。同时,
罩口布置的光源照亮镍板上下表面,以获得打光一致且无环境光干扰的镍板正反两面照片。
57.s2、剪板机10按照预设标准裁剪镍耳,镍耳转运至镍耳收集斗13,剪切镍耳后的镍板转运至镍板配重台18。
58.如图4所示,在本步骤中,镍耳的裁剪标准为上料机械手3按照镍板裁剪后镍耳长度≤10mm直接将镍板送至剪板机10的剪刃下,剪下的电镍吊耳掉落至剪板机10后方的镍耳水平输送机11,并由镍耳水平输送机11将镍耳输送至镍耳上扬输送机12,镍耳上扬输送机12进而输送镍耳至镍耳收集斗13内。
59.剪切镍耳后的镍板转运至镍板配重台18是通过下料机械手16实现。下料机械手16的结构与上料机械手3的结构与功能相同。当镍板剪切完成后,下料机械手16从剪板机10上吸取剪切后的镍板并将镍板放置在镍板配重台18上设置的电子秤上进行称量,直至堆摞的镍板的数量达到预设值时完成镍板的配重。
60.s3、镍板配重台18称量其上堆摞的镍板,堆摞的镍板达到预设重量时,镍摞转运至油压机21下进行压平、压实作业。
61.如图3至图4所示,在本步骤中,堆摞的镍板达到预设重量的条件为,型号为ni9996的镍摞堆摞至重量为1470~1530kg时,或者,型号为ni9997的镍摞堆摞至重量为1800~2200kg(约为22张镍板)时。
62.特别的,镍板配重台18的两侧分别设置有上配板台19与下配板台17,上配板台19与下配板台17上预先放置一些偏重或偏轻的镍板,当配重的最后一张镍板放置在镍板配重台18后镍摞的重量不合适时,下料机械手16将最后一张镍板调换为偏重或偏轻的镍板以完成配重作业。
63.油压机21具有上下两个工作台面,二者之间形成供镍摞放置的空间,以便于叉车、吊车、链条输送机等将镍摞运至油压机21的上下两个工作台面之间,并对镍摞进行压平、压实作业,且可保护上下工作台不被材料偏硬的镍板压坏。
64.s4、压平后的镍摞转运至计量装置26上称重,称重后由设置于计量装置26上方的喷码机直接对镍摞的上表面进行喷码。
65.如图5所示,在本步骤中,计量装置26与喷码装置25设置于同一工位,能够在计量装置26称出镍摞重量后由喷码装置25立即对其进行喷码作业,防止重量信息喷错镍摞等现象出现。喷码的内容有生产厂家、品名、批号、包号、生产日期、重量、质检人员等生产信息。
66.s5、喷码后的镍摞转运至小对中装置24进行对中,小对中装置24将镍摞对中整齐堆摞,防止镍摞在到打包线后有偏移。
67.在步骤s3至步骤s5中,具体如图3所示,镍板的转运通过自动导引运输车系统实现。自动导引运输车系统包括设置于配重装置右侧的自动导引行走区、以及行走于自动导引行走区内的至少一个自动导引运输车22。自动导引运输车系统采用agv技术(自动导引运输技术),能够自动控制自动导引运输车22的行车路线,实现镍板的自动化、智能化转运。依据本领域技术人员对于本技术技术方案的理解,镍摞的转运,可由链条输送机、自动导引运输车22、桁架机构、以及起重机构成的组合装置等来完成。
68.自动导引运输车22与智能控制装置23信号连接,由智能控制装置23控制自动导引运输车22按照预设的路线往返于配重装置、油压机21、计量装置26、喷码装置25、小对中装
置24之间。
69.具体来讲,油压机21设置于自动导引行走区的上侧,当配重装置完成合格镍板的配重后,智能控制装置23通过5g数据通讯系统控制自动导引运输车22去叉取镍摞,并将镍摞向上运送至油压机21工作台上,油压机21对镍摞进行压平、压实作业。
70.计量装置26与喷码装置25设置于自动导引行走区的右侧,当油压机21完成镍板的压平、压实作业后,智能控制装置23通过5g数据通讯系统控制自动导引运输车22去叉取镍摞,并将镍摞运送至计量装置26上。
71.小对中装置24设置于自动导引行走区的右侧,并位于计量装置26的下方。当计量装置26与喷码装置25完成镍摞的称重喷码作业后,智能控制装置23通过5g数据通讯系统控制自动导引运输车22去叉取镍摞,并将镍摞运送至小对中装置24上。
72.s6、对中完成后的镍摞转运至打捆机30处,机器人加垫木机构29将垫木运至镍摞的下方,打捆机30对镍摞与垫木进行打捆作业。
73.在本步骤中,打捆机30的下侧设置有垫木托盘28,机器人加垫木机构29行走于垫木托盘28与打捆机30之间,能够自动将垫木托盘28内的垫木运至打捆机30处。
74.s7、打捆后的镍摞转运至绕膜机31,绕膜机31对镍摞进行加顶膜以及周边绕膜作业。
75.s8、绕膜完成后的镍摞转运至入库对中装置33进行对中,并在对中完成后运至立体库存储。
76.如图5所示,在步骤s6至步骤s8中,镍板的转运通过打包输送机32实现。打包输送机32沿水平方向设置于小对中装置24的右侧。打捆机30、绕膜机31、入库对中装置33从左往右依次设置于打包输送机32的上方,并在打包输送机32的右端设置有立体库。
77.当小对中装置24对镍摞对中后,镍摞落至打包输送机32上,由打包输送机32将镍摞运至打捆机30的打捆工位处。机器人加垫木机构29自动添加垫木至镍摞下方,由打捆机30进行打捆作业捆扎至镍摞下方,以方便叉车运输及保护镍摞的下底面。打捆完成后的镍摞继续运送至绕膜机31的绕膜工位处,绕膜机31自动添加顶膜至镍摞上方,再在镍摞的周边缠膜,以保护镍摞在储存、运输过程中不受污染。随后,绕膜后的镍摞通过打包输送机32运输至入库对中装置33处,由入库对中装置33对镍摞对中,防止镍摞进入立体库时位置偏移出现掉落事故,镍摞经过入库对中动作后进入立体库储存。
78.如图5所示,在步骤s6至步骤s8中,本方法采用液压伺服系统27作为对中及打捆的驱动系统。液压伺服系统27与小对中装置24、入库对中装置33以及打捆机30的打捆升降台连接,以对三者提供顶起镍摞以及对中镍摞的动力。
79.以上所述仅用以说明本发明的技术方案,而非对其进行限制;尽管参照前述实施例对本发明进行了详细的说明,本领域的普通技术人员应当理解:其依然可以对前述实施例所记载的技术方案进行修改,或者对其中部分或者全部技术特征进行等同替换;凡是利用本发明说明书及附图内容所作的等效结构或等效流程变换,或直接或间接运用在其他相关的技术领域,均同理包括在本发明的专利保护范围内。