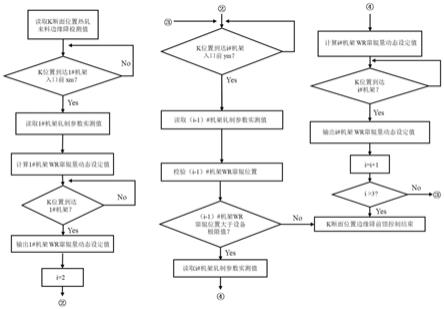
1.本发明涉及冶金机械/酸洗轧制技术领域,尤其涉及一种冷轧连轧精轧机组窜辊控制方法。
背景技术:2.冷轧产品的边缘降(edge drop,简称为边缘降,也称为边部减薄)是尺寸精度指标的重要参数。边缘降的传统定义是距离边部100mm位置的厚度ta减去距离边部15mm位置的厚度tb的差值,edge drop=ta-tb。
3.但随着目前用户对产品质量要求的不断提高,传统的边缘降定义已经难以满足要求,时常发生当传统edge drop的控制水平完全达到机组控制要求时,仍然无法满足用户对断面形状要求的情况。因此目前在生产高边缘降要求的冷轧机组均将边缘降概念拓展至同板差,即带钢中心点厚度hc减去距离边部15mm位置的厚度h15的差值:同板差(边缘降)=hc-h15
4.以此计算得到的边缘降值能够真正体现全板宽范围内的厚度差异,是表征机组精度控制能力的优良指标。
5.当今世界上先进的ucmw型或ucm型轧机在边缘降的控制上主要采用工作辊窜动反馈控制系统进行,其主要控制思路均为使用带倒角或特殊弧形的工作辊或中间辊窜动对边部减薄区域进行补偿以降低边缘降值。相应系统的具体实施方法为根据轧机出口边缘降仪的测量数据与设定阈值的对比来调整轧辊的窜动水平。当检测到的当前同板差值大于系统设定阈值时,由反馈控制系统输出轧辊窜动命令,而在轧辊窜动过程中,由于工作辊窜动与当前速度相关,窜动执行机构在执行相应任务,故无法继续接收新的窜动命令。待执行机构完成相应窜动动作后,再重新开始接收系统所输出指令,有明显大滞后,增大边缘降长度段。
6.但随着用户对产品质量要求的日益提高,目前冷轧产线在边缘降方面的用户抱怨呈现增多趋势,实现整卷窜辊前馈动态控制显得尤为重要。
7.现有技术存在问题:
8.1、当前钢铁生产行业中,尤其在对冷轧硅钢产品有所需求的电机汽车板等行业,对同板差要求极高,目前常用的轧辊弯辊方式虽然可在一定程度上控制同板差,但与用户要求还有较大差距。
9.2、控制同板差的方法除了轧辊弯辊外,轧辊窜动也是一个重要的补充手段。通过头部稳定设定值的建立和过渡,减少了由于头尾设定窜动位置不准而产生的超差长度,大大提高边部厚度的一次精度命中率。
10.3、wr窜辊是带钢同板差控制的主要执行机构。而目前的窜辊控制方法通常由反馈调节和操作工手动控制完成,而这些控制方法容易受到机组反应速度、经验主义的影响而导致控制效果不佳。同板差窜辊前馈动态控制系统可以减小来料凸度突变对带钢同板差的影响。同时结合窜辊的机械结构及动作特点,计算结果具备机架间柔性可配置功能。
11.经查阅相关文献资料,并在中外专利数据库服务平台联机检索,相同领域查询到两个典型专利,1、专利号cn106975663a,名称:解决边部增厚问题的轧机窜辊控制方法,该专利的方法所涉及的主要是一种实现边部厚度超过中心厚度时的窜辊控制方法,而本发明所要实现的对边缘降控制量进行调整的目的和方法有显著不同。2、专利号cn105436208a,名称:轧制过程中的边缘降控制方法,该方法所涉及的主要是关于弯辊控制与窜辊控制同时投入时,对两种控制方法的使用及调节量的优化的相关内容吗,属于边缘降控制方式的选择与调整方法,与本发明所要实现的仅对窜辊实施具体控制策略的方法存在明显区别。
技术实现要素:12.本发明的目的在于通过对同板差控制过程的系统分析,实现在轧制过程中轧辊窜动自动控制,以充分发挥轧辊窜动在控制同板差上的能力,提高冷轧产品的同板差控制总体水平,提高实物质量水平。
13.为了实现上述目的,本发明采用的技术方案是:
14.一种同板差窜辊前馈动态控制方法,用于五机架冷连轧机,在该连轧机入口设置凸度仪实时检测带钢热轧来料凸度值并上传至过程控制计算机,所述过程计算机在不同的轧制阶段动态计算wr窜辊轴向移位位置,输出到1#至3#机架工作辊进行窜辊控制,wr为工作辊,具体方法如下:
15.读取带钢k断面位置热轧来料边缘降检测值,即通过所述凸度仪反馈带钢中心点厚度测量值和距离边部15mm位置厚度测量值;检验该k断面位置是否到达1#机架入口前目标距离xm,若已到达目标位置,则读取1#机架轧制参数实测值,计算1#机架wr窜辊量动态设定值如下:
16.wrs1=((hc
–
h15)-ht)*α1*β1
17.式中,wrs1为1#机架wr窜辊量动态设定值;hc为带钢中心点厚度测量值;h15为距离边部15mm位置厚度测量值;ht为来料凸度目标值;α1为效率系数;β1为加权系数;接着检验该k断面位置是否达到1#机架,若已达到1#机架则输出已计算出的1#机架wr窜辊量动态设定值wrs1;
18.接着,检验该k断面位置是否到达2#机架入口前目标距离ym,若已达到目标位置,则读取1#机架轧制参数实测值并校验1#机架wr窜辊位置;若1#机架wr窜辊位置不大于设备极限值,则该带钢k断面位置边缘降前馈动态控制结束,否则,则读取2#机架轧制参数实测值并计算2#机架wr窜辊量动态设定值如下:
19.wrs2=((hc
–
h15)-ht)*α2*β2
20.式中,wrs2为2#机架wr窜辊量动态设定值;α2为效率系数;β2为加权系数;接着检验该k断面位置是否到达2#机架,若已达到2#机架则输出已计算出的2#机架wr窜辊量动态设定值wrs2;
21.接着,检验该k断面位置是否到达3#机架入口前目标距离ym,若已达到目标位置,则读取2#机架轧制参数实测值并校验2#机架wr窜辊位置;若2#机架wr窜辊位置不大于设备极限值,则该带钢k断面位置边缘降前馈动态控制结束,否则,则读取3#机架轧制参数实测值并计算3#机架wr窜辊量动态设定值如下:
22.wrs3=((hc
–
h15)-ht)*α3*β3
23.式中,wrs3为3#机架wr窜辊量动态设定值;α3为效率系数;β3为加权系数;接着检验该k断面位置是否到达3#机架,若已达到3#机架则输出已计算出的3#机架wr窜辊量动态设定值wrs3,该带钢k断面位置边缘降前馈动态控制结束。
24.本发明的有益效果是:本发明通过对适用于5机架冷连轧机窜辊控制系统的研发,使带钢的同板差得以控制,提高了冷轧产品的同板差控制总体水平。与目前常用的同板差控制系统相比,其主要优点在于:
25.(1)控制方式更符合现场需求
26.目前常用的同板差控制方式中,窜辊是一个重要的控制手段。使用带倒角或特殊弧形的工作辊或中间辊窜动对边部减薄区域进行补偿以降低边缘降值。但由于目前所使用的窜辊控制主要窜辊设定值由后方边降仪测定同板差反馈给控制系统后进行计算再下发至执行机构,容易出现因轧制速度不足导致窜辊调节滞后的情况。故当前控制方式可快速检定同板差并将设定值下发至执行机构提高响应速度,提升同板差控制水平。
27.(2)计算方式更准确
28.目前常用的窜辊控制系统,都经由后方边降仪进行同板差测定,在获取同板差大于预定数值时,再将设定值反馈至机架进行窜辊控制。而本文中所提出的窜辊控制系统,读取某带钢断面位置热轧来料边缘降检测值,并判断该断面位置。通过读取当前机架轧制参数实测值,并根据该实测值计算该机架工作辊弯辊动态设定值,并于断面到达机架时下发该动态设定值。由此多次进行不同机架的设定值动态设定,以提高计算准确性。
29.本发明通过一种基于冷连轧机组入口凸度仪断面检测及满足用户要求边缘降水平的同板差窜辊前馈动态控制技术,各机架窜辊计算值实时前馈控制,提高了冷轧带钢的同板差控制水平。因本发明所提出的想法可针对不同同板差控制能力水平的各类多机架冷连轧机系统,故其可广泛用于目前采用wr窜辊进行同板差控制且轧机前配备凸度仪的冷轧机组。在当前全球电工钢产品产线不断新增的背景下,本发明所提出的技术具有开阔的市场前景。
附图说明
30.图1五机架冷连轧机的同板差窜辊前馈动态控制系统示意图;
31.图2同板差窜辊前馈动态控制流程图。
具体实施方式
32.下面结合实施例对本发明作进一步的详细说明,如图1和2所示,一种同板差窜辊前馈动态控制方法。在连轧机入口设置凸度仪实时检测带钢热轧来料凸度值并上传至过程控制计算机,过程计算机在不同的轧制阶段动态计算wr窜辊轴向移位位置,输出到1#-3#机架工作辊进行窜辊控制。
33.以某五机架冷连轧机,其热轧来料厚度中心点为2614μm,冷轧出口厚度为500μm,来料凸度目标值ht为20μm,出口同板差要求,距离边部15mm位置为5μm为例。
34.首先读取带钢k断面位置热轧来料边缘降检测值,凸度仪反馈带钢中心点厚度测量值hc为2647μm,距离边部15mm位置厚度测量值h15为2619μm。首先判断该k断面位置是否到达1#机架入口前目标距离1m,若已到达目标位置,则读取1#机架轧制参数实测值,即当前
1#机架wr窜辊相对位移值为95mm。计算1#机架wr窜辊量动态设定值如下:
35.wrs1=((hc
–
h15)-ht)*α1*β1
36.该钢种规格对应效率系数α1取值-0.8,加权系数β1取值0.5
37.将各数据代入公式,获得1#机架wr窜辊量动态设定值为:
38.((2647-2619)-20)*(-0.8)*0.5=-3.2mm
39.之后检验该断面位置是否达到1#机架,若已达到1#机架则输出已计算出的1#机架wr窜辊量动态设定值。
40.接着判断该k断面位置是否到达2#机架入口前目标距离1m,若已达到目标位置,则读取1#机架轧制参数实测值并校验1#机架wr窜辊位置;1#机架wr窜辊位置大于设备极限值,读取2#机架轧制参数实测值并计算2#机架wr窜辊量动态设定值:
41.wrs2=((hc
–
h15)-ht)*α2*β2
42.式中,wrs2为2#机架wr窜辊量动态设定值;该钢种规格对应效率系数α2取值-0.5,加权系数β2取值0.5,将各数据代入公式,获得2#机架wr窜辊量动态设定值为:
43.((2647-2619)-20)*(-0.5)*0.5=-2mm
44.等该k断面位置到达2#机架输出2#机架wr窜辊量动态设定值;
45.3#机架计算方式同2#机架,该钢种规格对应效率系数α3取值-0.3,加权系数β3取值0.5;将各数据代入公式,获得3#机架wr窜辊量动态设定值为:
46.((2647-2619)-20)*(-0.3)*0.5=-1.2mm
47.以上内容仅用以说明本发明的技术方案,本领域的普通技术人员对本发明的技术方案进行的简单修改或者等同替换,均不脱离本发明技术方案的实质和范围。