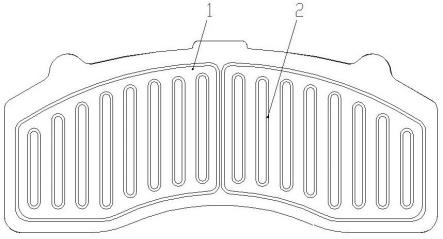
1.本发明属于汽车工业技术领域,具体涉及一种摩擦块锻造新工艺。
背景技术:2.摩擦块又称钢背,属于刹车片的一部分,用于汽车盘式制动器。摩擦块为扁平板状结构,如图1、图2、图3、图4所示,主平面基本呈长方形,一条长侧边为外凸弧形边,另一条长侧边中部为凹弧形,在摩擦块的一侧表面设计有左右对称的两个凹坑1,凹坑1内有均布有若干长条状突起2。这种结构的摩擦块在锻造过程中存在以下问题:(1)摩擦块为扁平状结构,摩擦块的长度方向和宽度方向尺寸分别是其厚度方向尺寸a的二十多倍和十几倍,使用棒材坯料进行锻造时坯料变形程度较大,对于选择坯料尺寸、制坯过程、坯料的放置难度都有较大影响,并最终降低锻件质量和原材料利用率,提高生产成本。
3.(2)摩擦块一条长侧边为外凸弧形边,另一条长侧边中部为凹弧形,棒材坯料为直棒料,原材料的分布与摩擦块锻件形状存在错差,直接进行锻造时需要增大棒料直径,从而增大棒料重量,材料利用率较低。
4.(3)由于摩擦块厚度尺寸a较小而平面尺寸较大,同时其尺寸公差要求
±
0.25mm较为严格,对锻造工艺和模具设计、锻造设备等要求较高。
5.(4)凹坑1内有均布的长条状突起2,在凹坑1部位,由于锻件本身厚度较小,所以最终成形时锻造模具的上模和下模之间金属流动会十分剧烈,对模具型腔的磨损会比较严重,因此需要通过减少毛坯的体积来减小磨损;另一方面,长条形突起2高出摩擦块的平面较高而且突起的宽度尺寸较小,不易充满,需要增加坯料的体积来保证锻件质量。所以锻造过程中的制坯不合适的话对锻件质量和模具寿命有较大影响。
技术实现要素:6.本发明为了解决现有技术中的不足之处,提供一种易成型、材料利用率高、锻件质量高、模具使用寿命长的摩擦块锻造新工艺。
7.为解决上述技术问题,本发明采用如下技术方案:一种摩擦块锻造新工艺,包括以下步骤:(1)下料;(2)加热;(3)压弯;(4)预锻;(5)终锻;(6)切边;(7)校正。
8.步骤(1)下料工序的具体过程为:采用φ34mm的q235圆棒钢材,下料重量为1.66
±
0.02kg;使用p50b高速圆盘锯锯切圆钢棒材为坯料,高速圆盘锯设备转速120-130r/s,齿切厚0.065-0.07mm,单件坯料下料时间为11s,下料长度公差为
±
0.05mm,端面马蹄度≤0.1mm;高速圆盘锯下料速度快,坯料精度高,为锻件质量的一致性提高可靠保障。
9.步骤(2)加热工序的具体过程为:使用630kw的中频感应加热炉对坯料加热,加热温度范围为1120-1200℃,坯料温度的控制方法是利用红外线测温仪对加热后的坯料进行分选,分选为:正常坯料(1120-1200℃)、低温料(<1120℃)、高温料(>1200℃),分选后的坯料通过不同的滑道到达指定的位置;低温料和高温料滑道终端设置低温料筐和高温料筐,料筐顶部开设进料口并加锁,保证不会混料的同时避免工人拿取不合格坯料;低温料可重新再进行加热一次,再次欠温进行报废处理,避免多次加热造成锻件组织不符合要求,同时也避免坯料烧损过多导致锻件产生充不满缺陷;高温料直接报废处理,质量人员定期清理高温料并标识隔离。
10.步骤(3)压弯工序的具体过程为:由于摩擦块锻件一条长侧边为外凸弧形边,另一条长侧边中部为凹弧形,为了保证锻件充满,提高原材料利用率,需要对圆棒料进行压弯制坯,使棒料的截面积分布与摩擦块锻件的截面积分布更一致,在160吨曲柄压力机冲床上面安装压弯模具,压弯过程中可以通过调整压力机的滑块高度来调整压弯凸模向下移动极限,即调整压弯后坯料厚度;同时在压弯凹模的弧形槽两端分别设置有深度为2mm的压弯定位台阶槽,方便工人放置加热后的坯料,减少操作失误,提高生产效率。
11.步骤(4)预锻工序的具体过程为:先使用模具预热炉预热预锻模具,预锻模具预热温度达到350℃左右后,将预锻模具安装在2500吨热模锻压力机上,预锻模具的预锻下模的型腔底部沿长度方向设有弧形定位槽,弧形定位槽的横截面底部轮廓为半径为18mm的弧线段,压弯后的坯料放置在预锻下模的型腔内,通过弧形定位槽对压弯的坯料放置进行定位,最后启动2500吨热模锻压力机,预锻上模对预锻下模型腔内的坯料进行预锻,预锻后的坯料形成弧形扁平板状的预锻件。
12.步骤(5)终锻工序的具体过程为:终锻模具安装在2500吨热模锻压力机上,终锻下模的型腔底部设有与摩擦块终锻件一侧表面的凹坑及若干长条状凸起对应的摩擦面锻造结构,终锻下模内在设有摩擦面锻造结构的外侧垂直开设有四个导孔,每个导孔内均设有一根顶杆,终锻上模和终锻下模之间设有钳口,终锻模具的毛边桥部宽度为8mm;将预锻件放置终锻模具的终锻下模的型腔内,启动热模锻压力机,终锻上模向下锻压终锻下模型腔内的预锻件,终锻完成后,终锻上模向上抬起,四个顶杆在气缸的作用下,向上顶起摩擦块终锻件,使用夹钳夹住摩擦块终锻件,从终锻下模的型腔内取出。
13.步骤(6)切边工序的具体过程为:切边模具安装在400吨闭式单点压力机上,400吨闭式单点压力机的导轨间隙≤0.5mm,保证锻件切边后圆周毛边的一致性;切边模具旁边加装输送带,切边后的摩擦块终锻件放置在输送带上进行降温,还可有效避免锻件堆积产生磕碰伤。
14.步骤(7)校正工序的具体过程为:校正模具安装在300吨摩擦压力机上,按切边后锻件的顺序依次校正,校正温度为550-600℃,校正后的锻件尺寸厚度公差在
±
0.25mm以内。
15.在预锻和终锻工序中,在锻造过程工人利用喷枪对预锻和终锻模具喷洒石墨乳,润滑模具的同时降低模具型腔表面的温度,石墨乳:水按重量配比的比例为1:7,减少石墨
乳用量的同时可以达到最有效的润滑效果。
16.采用上述技术方案,本发明具有以下技术效果:(1)加热工序十分重要,低温料容易造成:
①
坯料流动性减弱,型腔边角处易出现锻件充不满的现象,造成锻件报废;
②
坯料的变形抗力提高,使设备打击力量增大,模具受力增大,造成设备和模具损坏;
③
锻件的成形力量最终超过设备最大打击力量,导致锻件几何尺寸在高度方向超差或者造成设备闷车。高温料容易造成:坯料组织晶粒粗大,锻件强度和机械性能下降,造成锻件报废。
17.为及时发现中频感应加热炉故障,中频感应加热炉红外线测温口配备显示屏和报警器显示屏能实时显示坯料温度,连续出现低温料、高温料2件以上,报警器进行报警,提示工人查看中频感应加热炉是否出现故障,避免批量事故的发生。为了提高摩擦块锻件的表面质量和减少预锻模具和终锻模具的磨损,在中频感应加热炉出料口加设氧化皮处理箱,利用2mp的高压水去除坯料氧化皮,提高锻件表面质量。。
18.(2)模具预热炉加热预锻模具,具有以下好处:
①
预锻模具预热温度均匀性好;
②
安装预锻模具后,预锻模具不用再次预热,提高生产效率;
③
预锻模具使用寿命提高。
19.(3)要保证摩擦块锻造质量的一致性,就要保证预锻、终锻时放置坯料的一致性。预锻模具在预锻下模的型腔内设置了与压弯制坯相配合的弧形定位槽,可以在不影响终锻成形的情况下使压弯制坯料准确地放置在预锻模具的型腔内。调整预锻件四周外形的具体尺寸可以使预锻件的四周轮廓基本与终锻一致,另外调整预锻模具、终锻模具分模线的高度,可以使预锻件准确放置到终锻模具的型腔里面。预锻模具改进后方便工人放置坯料,减少操作失误,提高生产效率。
20.(4)在修改预锻模具的设计时,需要对预锻件的厚度进行调整并在生产过程中严格控制,以保证终锻件充满型腔并且尽量减少终锻时预锻件的金属相对流动,来减少终锻模具型腔的磨损。摩擦块终锻件的一侧面有很多长条状突起,这一侧由于跟终锻型腔贴合较为紧密,在锻造过程中容易发生卡模的情况。为此把突起的一侧型腔设置到终锻模具的下模,并在下模内设置四个顶杆,锻造完成后借助设备的顶出力把摩擦块锻件取出来。同时在模具上设置设置了钳口。针对摩擦块厚度薄,平面尺寸相对较大的情况,将终锻模具的毛边桥部宽度由15mm减少到8mm,并且设置了不同的桥部厚度。在保证终锻件充满成形的情况下,可以降低最终的成形力并减少模具的磨损,延长模具的使用寿命,降低生产成本。
21.为了进一步提高锻件的一致性和模具寿命,降低单件锻件的模具成本。本发明采用智能增材制造焊接强化的方式在预锻、终锻型腔部位堆叠出一定厚度的高强度模具焊材,即使用普通模具材料做模具的基体,使用高强度材料作为模具型腔的工作部分,这样在提高模具寿命的同时也兼顾了模具的制作成本、使用成本。使用该技术经试验后,模具寿命由500件/套提高到3000件/套。
22.综上所述,本发明提出了一种摩擦块锻造新工艺,具有操作简便,生产成本低,材料利用率高,锻造出来的摩擦块锻件质量好、成品率高,各个工序对应的模具结构合理、使用寿命长。
附图说明
23.图1 是摩擦块锻件的正面示意图;
图2 是摩擦块锻件的背面示意图;图3是图1的仰视图;图4是图3中m处的局部放大示意图;图5是压弯模具的截面示意图;图6是图5中压弯定位台阶槽的e-e截面示意图;图7是预锻模具的预锻下模的俯视示意图;图8是图7中弧形定位槽d-d截面示意图;图9是终锻模具的终锻下模的俯视示意图;图10是图9中钳口b-b处的截面示意图;图11是图9中飞边a-a处的截面示意图。
具体实施方式
24.如图5-11所示,本发明的一种摩擦块锻造新工艺,包括以下步骤:(1)下料;(2)加热;(3)压弯;(4)预锻;(5)终锻;(6)切边;(7)校正。
25.步骤(1)下料工序的具体过程为:采用φ34mm的q235圆棒钢材,下料重量为1.66
±
0.02kg;使用p50b高速圆盘锯锯切圆钢棒材为坯料,高速圆盘锯设备转速120-130r/s,齿切厚0.065-0.07mm,单件坯料下料时间为11s,下料长度公差为
±
0.05mm,端面马蹄度≤0.1mm;高速圆盘锯下料速度快,坯料精度高,为锻件质量的一致性提高可靠保障。
26.步骤(2)加热工序的具体过程为:使用630kw的中频感应加热炉对坯料加热,加热温度范围为1120-1200℃,坯料温度的控制方法是利用红外线测温仪对加热后的坯料进行分选,分选为:正常坯料(1120-1200℃)、低温料(<1120℃)、高温料(>1200℃),分选后的坯料通过不同的滑道到达指定的位置;低温料和高温料滑道终端设置低温料筐和高温料筐,料筐顶部开设进料口并加锁,保证不会混料的同时避免工人拿取不合格坯料;低温料可重新再进行加热一次,再次欠温进行报废处理,避免多次加热造成锻件组织不符合要求,同时也避免坯料烧损过多导致锻件产生充不满缺陷;高温料直接报废处理,质量人员定期清理高温料并标识隔离。
27.步骤(3)压弯工序的具体过程为:由于摩擦块锻件一条长侧边为外凸弧形边,另一条长侧边中部为凹弧形,为了保证锻件充满,提高原材料利用率,需要对圆棒料进行压弯制坯,使棒料的截面积分布与摩擦块锻件的截面积分布更一致,在160吨曲柄压力机冲床上面安装压弯模具,压弯过程中可以通过调整压力机的滑块高度来调整压弯凸模3向下移动极限,即调整压弯后坯料厚度;同时在压弯凹模4的弧形槽两端分别设置有深度为2mm的压弯定位台阶槽5,方便工人放置加热后的坯料,减少操作失误,提高生产效率。
28.步骤(4)预锻工序的具体过程为:先使用模具预热炉预热预锻模具,预锻模具预热
温度达到350℃左右后,将预锻模具安装在2500吨热模锻压力机上,预锻模具的预锻下模6的型腔底部沿长度方向设有弧形定位槽7,弧形定位槽7的横截面底部轮廓为半径为18mm的弧线段,压弯后的坯料放置在预锻下模6的型腔内,通过弧形定位槽7对压弯的坯料放置进行定位,最后启动2500吨热模锻压力机,预锻上模对预锻下模6型腔内的坯料进行预锻,预锻后的坯料形成弧形扁平板状的预锻件。
29.步骤(5)终锻工序的具体过程为:终锻模具安装在2500吨热模锻压力机上,终锻下模8的型腔底部设有与摩擦块终锻件一侧表面的凹坑及若干长条状凸起对应的摩擦面锻造结构9,终锻下模8内在设有摩擦面锻造结构9的外侧垂直开设有四个导孔,每个导孔内均设有一根顶杆10,终锻上模12和终锻下模8之间设有钳口11,终锻模具的毛边桥部13宽度为8mm;将预锻件放置终锻模具的终锻下模8的型腔内,启动热模锻压力机,终锻上模12向下锻压终锻下模8型腔内的预锻件,终锻完成后,终锻上模12向上抬起,四个顶杆10在气缸的作用下,向上顶起摩擦块终锻件,使用夹钳夹住摩擦块终锻件,从终锻下模8的型腔内取出。
30.步骤(6)切边工序的具体过程为:切边模具安装在400吨闭式单点压力机上,400吨闭式单点压力机的导轨间隙≤0.5mm,保证锻件切边后圆周毛边的一致性;切边模具旁边加装输送带,切边后的摩擦块终锻件放置在输送带上进行降温,还可有效避免锻件堆积产生磕碰伤。
31.步骤(7)校正工序的具体过程为:校正模具安装在300吨摩擦压力机上,按切边后锻件的顺序依次校正,校正温度为550-600℃,校正后的锻件尺寸厚度公差在
±
0.25mm以内。
32.在预锻和终锻工序中,在锻造过程工人利用喷枪对预锻和终锻模具喷洒石墨乳,润滑模具的同时降低模具型腔表面的温度,石墨乳:水按重量配比的比例为1:7,减少石墨乳用量的同时可以达到最有效的润滑效果。
33.本实施例并非对本发明的形状、材料、结构等作任何形式上的限制,凡是依据本发明的技术实质对以上实施例所作的任何简单修改、等同变化与修饰,均属于本发明技术方案的保护范围。