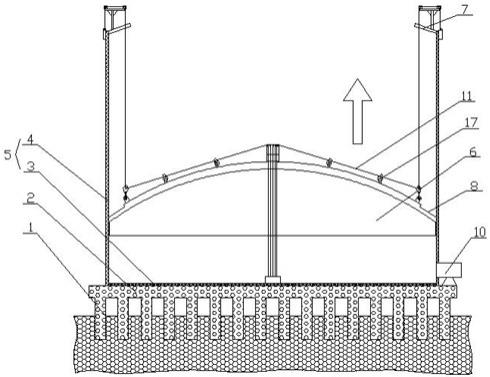
一种超大型lng全容储罐的建造方法
1.技术领域:本发明涉及lng领域,具体地说是一种超大型lng全容储罐的建造方法。
2.
背景技术:目前,低温储罐主要分为单容罐、双容罐、全容罐三种类型,全容型储罐由内罐和外罐组成,此二者共同构成一个完整的储罐,內罐是储存液体产品的自撑式钢质罐,而外罐则是具有拱顶的自支撑钢质或混凝土储罐,由于lng存储温度为-163℃,因此需要在外罐与內罐之间的环形空间内填充珍珠岩颗粒,来对內罐内的lng 进行保冷。
3.lng储罐的施工过程中,储罐气升顶工作是施工过程中最为重要的环节,气升顶是通过空气压力将罐顶升至承压圈并焊接固定,是一项危险性较大的施工作业,目前在气升顶过程中存在如下技术问题:罐顶在气压升顶作用下与承压圈卡合接触,通过多个工作人员在罐顶与承压圈之间的圆周焊缝处进行焊接,使罐顶焊接固定在外罐的上端位置,焊接前先通过多个等圆周分布的楔块将承压圈与罐顶进行夹紧固定,再通过分段点焊的方式将罐顶与承压圈之间的圆周焊缝进行焊接,最终将楔块切割去除,再将多个分段点焊的首尾端依次进行焊接,从而实现对整个圆周焊缝的焊接,然而由于罐顶的承载较大,罐顶与承压圈连接处的受力集中,因此与承压圈的焊接牢固极为重要,如果焊接深度不够,那么必然影响罐顶与承压圈之间的连接牢固度,其次,分段点焊后再进行补焊连接的方式,各焊接分段的焊接强度不一,尤其是首尾端重复受热,焊接分段连接处的热应力集中,从而影响罐顶与承压圈之间的连接强度以及连接稳定性,而且需要多个操作人员同时对圆周焊缝进行焊接,具有极大的安全隐患。
4.
技术实现要素:本发明的目的是为了克服以上的不足,提供一种超大型lng全容储罐的建造方法,实现自动化开坡口以及整体式焊接,保证罐顶与承压圈之间连接强度以及连接稳定性,降低施工安全隐患。
5.本发明的目的通过以下技术方案来实现:一种超大型lng全容储罐的建造方法,具体步骤包括:s1、搭建平台:建造多个插入地面的灌浆柱,多个灌浆柱等圆周分布,在多个灌浆柱的上端建造混凝土平台;s2、建造外罐:在混凝土平台上定位0
°
、90
°
、180
°
和270
°
轴线及中心点并做出标记作为基准以指导外罐底部的铺设,在混凝土平台的基础平面上画出每块外罐底板片体的安装位置,按顺序吊装就位,并进行焊接形成外罐底板;在外罐底板上划出外壳外圆尺寸位置,由下至上组装外罐环板,并在外罐环板内壁用槽钢撑圆以防变形,对所有的外罐环板进行焊接,在对接焊缝进行射线探伤处理,形成外罐;s3、气顶升罐顶:a、在外罐内部建造拱形状结构的罐顶,在外罐环板的顶部安装承压圈,承压圈朝着外罐环板的内侧上方位置延伸,罐顶上端两侧具有与承压圈相配合的环槽;b、在外罐门洞处安装多台升顶用的风机,在罐顶上安装多个钢丝绳以及组装对接装置,同时为保证升顶速度和升顶时的罐顶整体平稳性,在罐顶边缘和外罐内壁之间安装一圈由
铁皮、密封布、压条组成的密封圈,从而减小升顶过程中的气压损失;c、启动多台风机,使外罐内部产生气压而对罐顶进行向上顶起,多个钢丝绳对向上顶起的罐顶进行平衡,罐顶以100mm/min的平均速度向上顶升5m后,增加速度,以200mm/min的平均速度连续升顶,直至达到罐顶需顶升的最后5m,最后5m以100mm/min以内的速度继续顶升,直至与承压圈接触;d、承压圈嵌设在罐顶的环槽内,罐顶上的组装对接装置将承压圈与罐顶进行压紧组装对接,组装对接装置对承压圈与罐顶之间的圆周焊缝进行圆周开坡口以及圆周焊缝的整体式焊接,焊接完毕后,将多个钢丝绳以及组装对接装置进行切割去除;s4、建造內罐:将內罐的吊杆以及铝吊顶安装至罐顶内侧下端位置,在外罐内侧底部通过混凝土浇筑的方式建造內罐底部,由下至上通过焊接的方式安装內罐壁板,从而形成內罐;s5、在內罐与外罐之间填充保冷材料:在罐顶的上端由上至下灌注保冷材料,所述保冷材料为膨胀珍珠岩;s6、附件安装:安装泵平台、泵井、爬梯、管道以及电仪电器。
6.本发明的进一步改进在于:组装对接装置包括设置在罐顶上的多个连接架,连接架竖向设置且多个连接架等圆周分布,连接架的上端向着承压圈的方向垂直延伸有支撑架,支撑架远离连接架的下端连接有上下升降的夹紧气缸,夹紧气缸的驱动端与承压圈的外侧端面接触,多个支撑架的下端共同连接有环形轨道,环形轨道上嵌设有一前一后设置的驱动组,位于前侧的驱动组的下端固定连接有激光切割头,位于后侧的驱动组的下端固定连接有埋弧焊接头,驱动组带动对应的激光切割头以及埋弧焊接头在环形轨道上作圆周运动;驱动组包括嵌设在环形轨道上的驱动块,环形轨道的截面为工字型状结构,驱动块为与环形轨道相配合的c形状结构,且驱动块的开口向上设置,环形轨道的内外侧具有容驱动块的上端两侧嵌设的槽体,槽体的底部具有限位槽,水平贯穿驱动块的上端两侧具有驱动轴,驱动轴置于驱动块的外侧端连接有第一驱动电机,驱动轴置于槽体内的一端连接有嵌设在限位槽内的行走轮,驱动块的下端具有与对应的激光切割头、埋弧焊接头连接的连接块,连接块可水平移动地设置在驱动块的下端,连接块与对应的激光切割头、埋弧焊接头之间通过驱动缸实现上下往复式移动。
7.本发明的进一步改进在于:驱动块的下端面具有容连接块的上端嵌设的t型槽,t型槽的开口朝下设置,连接块为与t型槽相互配合的工字型状结构,且t型槽与连接块之间具有间隙,水平贯穿驱动块以及连接块具有一丝杠,丝杠的一端连接有第二驱动电机,连接块与丝杠为螺纹连接,当第二驱动电机转动,带动连接块与丝杠作螺纹传动,从而使连接块在丝杠上作水平线性位移。
8.本发明的进一步改进在于:组装对接装置对承压圈与罐顶之间的圆周焊缝进行圆周开坡口以及圆周焊缝的整体式焊接,具体步骤包括如下:a、驱动缸收缩使激光切割头、埋弧焊接头向上运动并置于圆周焊缝的正上方位置,激光切割头的下端位于圆周焊缝任意位置z处,此时激光切割头对应的第二驱动电机正转启动并驱动丝杠与连接块作螺纹传动,使连接块在驱动块的下端垂直朝向承压圈移动2cm-3cm;b、激光切割头在对应的夹紧气缸向下驱动作用下与承压圈接触,此时激光切割头
启动,激光切割头对应的驱动缸继续向下驱动5mm-8mm,第二驱动电机反转启动并驱动丝杠与连接块作螺纹传动,使连接块在驱动块的下端逐步向圆周焊缝的位置z处移动复位,从而形成引焊坡口,此时激光切割头对应的第二驱动电机停止,激光切割头对应的第一驱动电机启动,激光切割头在对应驱动组的驱动下对圆周焊缝进行开坡口处理,形成圆周焊缝坡口;c、埋弧焊接头对应的第一驱动电机随着激光切割头对应的第一驱动电机的启动而启动,当埋弧焊接头置于圆周焊缝的位置z处时,埋弧焊接头对应的第二驱动电机正转启动并驱动丝杠与连接块作螺纹传动,使连接块在驱动块的下端垂直朝向承压圈移动2cm-3cm,埋弧焊接头在对应的驱动缸向下驱动作用下与引焊坡口接触,此时埋弧焊接头启动,第二驱动电机反转,在引焊坡口处开始引焊至位置z处,此时埋弧焊接头对应的第二驱动电机停止,埋弧焊接头对应的第一驱动电机启动,从而实现埋弧焊接头在对应驱动组的驱动下对圆周焊缝坡口处进行焊接;d、当激光切割头绕着圆周焊缝转动一圈后,激光切割头在对应的驱动缸作用下向上复位移动,并在对应的第一驱动电机的作用下继续前行2m-3m,当埋弧焊接头绕着圆周焊缝转动一圈后,埋弧焊接头在对应的驱动缸作用下向上复位移动,并在对应的第一驱动电机的作用下继续前行1m-2m,从而实现圆周焊缝的整体式开坡口以及整体式焊接;e、将组装对接装置进行切割拆除,并对焊接后的圆周焊缝处进行打磨。
9.本发明的进一步改进在于:钢丝绳的一端与外罐的上端固定,钢丝绳的另一端经过罐顶的外圆周至罐顶的中心,并垂直向下与外罐内侧中心固定,钢丝绳与罐顶之间通过滑轮实现导向活动连接,多个钢丝绳对罐顶在气顶升过程中实现平衡稳定上升。
10.本发明与现有技术相比具有以下优点:1、本发明中组装对接装置的多个夹紧气缸实现对罐顶以及承压圈之间的夹紧组装,组装对接装置中的多个连接架共同连接的环形轨道以及在环形轨道上绕着环形轨道移动的激光切割头、埋弧焊接头,从而实现对罐顶与承压圈之间圆周焊缝的整体式开坡口以及整体式焊接,避免传统分段点焊后再补焊连接的方式,实现自动化开坡口以及整体式焊接,保证罐顶与承压圈之间连接强度以及连接稳定性,降低施工安全隐患,其次对圆周焊缝进行开坡口后再焊接的方式,提高了圆周焊缝处的焊接深度,进一步保证了罐顶与承压圈之间的连接稳固性。
11.2、在本技术中,第二驱动电机转动带动连接块在t型槽内水平移动,从而带动激光切割头以及埋弧焊接头的水平式移动,实现在圆周焊缝的位置z处进行引焊坡口处理,以及在引焊坡口的起点处进行焊接,避免埋弧焊接头焊接时因瞬间变化的电流电压直接作用在圆周焊缝上而出现圆周焊缝起始焊接处应力集中的焊接缺陷,本发明将引焊坡口设置在承压圈上,即使具有一定的起始焊接缺陷,也会作用在承压圈上不会直接作用在圆周焊缝上,保证圆周焊缝高度一致的焊接质量以及焊接强度。
12.附图说明:图1为本发明中气顶升罐顶的结构示意图。
13.图2为图1中罐顶与承压圈、组装对接装置的结构示意图。
14.图3为图2中罐顶的俯视图。
15.图4为图3中a-a向结构剖视图。
16.图5为图3中b-b向结构剖视图。
17.图6为本发明中引焊坡口、圆周焊缝坡口的结构示意图。
18.图7为本发明中制得的lng储罐的结构示意图。
19.图中标号:1-灌浆柱、2-混凝土平台、3-外罐底板、4-外罐环板、5-外罐、6-罐顶、7-承压圈、8-环槽、9-组装对接装置、10-风机、11-钢丝绳、12-圆周焊缝、13-內罐、14-吊杆、15-铝吊顶、16-保冷材料、17-滑轮;91-连接架、92-支撑架、93-夹紧气缸、94-环形轨道、95-驱动组、96-激光切割头、97-埋弧焊接头;951-驱动块、952-槽体、953-限位槽、954-驱动轴、955-第一驱动电机、956-行走轮、957-连接块、958-t型槽、959-丝杠、960-第二驱动电机、961-引焊坡口、962-圆周焊缝坡口、963-驱动缸。
20.具体实施方式:为了加深对本发明的理解,下面将结合实施例和附图对本发明作进一步详述,该实施例仅用于解释本发明,并不构成对本发明保护范围的限定。
21.本实施例一种超大型lng全容储罐的建造方法,具体步骤包括:s1、搭建平台:建造多个插入地面的灌浆柱1,多个灌浆柱1等圆周分布,在多个灌浆柱1的上端建造混凝土平台2;s2、建造外罐:在混凝土平台2上定位0
°
、90
°
、180
°
和270
°
轴线及中心点并做出标记作为基准以指导外罐底部的铺设,在混凝土平台2的基础平面上画出每块外罐底板片体的安装位置,按顺序吊装就位,并进行焊接形成外罐底板3;在外罐底板3上划出外壳外圆尺寸位置,由下至上组装外罐环板4,并在外罐环板4内壁用槽钢撑圆以防变形,对所有的外罐环板4进行焊接,在对接焊缝进行射线探伤处理,形成外罐5;s3、气顶升罐顶:如图1所示,a、在外罐5内部建造拱形状结构的罐顶6,在外罐环板4的顶部安装承压圈7,承压圈7朝着外罐环板4的内侧上方位置延伸,罐顶6上端两侧具有与承压圈7相配合的环槽8;b、在外罐5门洞处安装多台升顶用的风机10,在罐顶6上安装多个钢丝绳11以及组装对接装置9,同时为保证升顶速度和升顶时的罐顶6整体平稳性,在罐顶6边缘和外罐5内壁之间安装一圈由铁皮、密封布、压条组成的密封圈,从而减小升顶过程中的气压损失;c、启动多台风机10,使外罐5内部产生气压而对罐顶6进行向上顶起,多个钢丝绳11对向上顶起的罐顶6进行平衡,罐顶6以100mm/min的平均速度向上顶升5m后,增加速度,以200mm/min的平均速度连续升顶,直至达到罐顶6需顶升的最后5m,最后5m以100mm/min以内的速度继续顶升,直至与承压圈7接触;d、如图2所示,承压圈7嵌设在罐顶6的环槽8内,罐顶6上的组装对接装置9将承压圈7与罐顶6进行压紧组装对接,组装对接装置9对承压圈7与罐顶6之间的圆周焊缝12进行圆周开坡口以及圆周焊缝的整体式焊接,焊接完毕后,将多个钢丝绳11以及组装对接装置9进行切割去除;s4、建造內罐13:将內罐13的吊杆14以及铝吊顶15安装至罐顶6内侧下端位置,在外罐6内侧底部通过混凝土浇筑的方式建造內罐底部,由下至上通过焊接的方式安装內罐壁板,从而形成內罐13;s5、在內罐13与外罐5之间填充保冷材料16:如图7所示,在罐顶6的上端由上至下
灌注保冷材料16,保冷材料16为膨胀珍珠岩;s6、附件安装:安装泵平台、泵井、爬梯、管道以及电仪电器。
22.进一步的,如图3至图5所示,组装对接装置9包括设置在罐顶6上的多个连接架91,连接架91竖向设置且多个连接架91等圆周分布,连接架91的上端向着承压圈7的方向垂直延伸有支撑架92,支撑架92远离连接架91的下端连接有上下升降的夹紧气缸93,夹紧气缸93的驱动端与承压圈7的外侧端面接触,多个支撑架92的下端共同连接有环形轨道94,环形轨道94上嵌设有一前一后设置的驱动组95,位于前侧的驱动组95的下端固定连接有激光切割头96,位于后侧的驱动组95的下端固定连接有埋弧焊接头97,驱动组95带动对应的激光切割头96以及埋弧焊接头97在环形轨道94上作圆周运动;驱动组95包括嵌设在环形轨道94上的驱动块951,环形轨道94的截面为工字型状结构,驱动块951为与环形轨道94相配合的c形状结构,且驱动块951的开口向上设置,环形轨道94的内外侧具有容驱动块951的上端两侧嵌设的槽体952,槽体952的底部具有限位槽953,水平贯穿驱动块951的上端两侧具有驱动轴954,驱动轴954置于驱动块951的外侧端连接有第一驱动电机955,驱动轴954置于槽体951内的一端连接有嵌设在限位槽953内的行走轮956,驱动块951的下端具有与对应的激光切割头96、埋弧焊接头97连接的连接块957,连接块957可水平移动地设置在驱动块951的下端,连接块957与对应的激光切割头96、埋弧焊接头97之间通过驱动缸963实现上下往复式移动。
23.本发明中组装对接装置9的多个夹紧气缸93实现对罐顶6以及承压圈7之间的夹紧组装,组装对接装置9中的多个连接架91共同连接的环形轨道94以及在环形轨道94上绕着环形轨道94移动的激光切割头96、埋弧焊接头97,从而实现对罐顶6与承压圈7之间圆周焊缝的整体式开坡口以及整体式焊接,避免传统分段点焊后再补焊连接的方式,实现自动化开坡口以及整体式焊接,保证罐顶6与承压圈7之间连接强度以及连接稳定性,降低施工安全隐患,其次对圆周焊缝12进行开坡口后再焊接的方式,提高了圆周焊缝12处的焊接深度,进一步保证了罐顶6与承压圈7之间的连接稳固性。
24.进一步的,驱动块951的下端面具有容连接块957的上端嵌设的t型槽958,t型槽958的开口朝下设置,连接块957为与t型槽958相互配合的工字型状结构,且t型槽958与连接块957之间具有间隙,水平贯穿驱动块951以及连接块957具有一丝杠959,丝杠959的一端连接有第二驱动电机960,连接块957与丝杠959为螺纹连接,当第二驱动电机960转动,带动连接块957与丝杠959作螺纹传动,从而使连接块957在丝杠959上作水平线性位移。
25.进一步的,组装对接装置9对承压圈7与罐顶6之间的圆周焊缝12进行圆周开坡口以及圆周焊缝的整体式焊接,具体步骤包括如下:a、驱动缸963收缩使激光切割头96、埋弧焊接头97向上运动并置于圆周焊缝12的正上方位置,激光切割头96的下端位于圆周焊缝任意位置z处,此时激光切割头96对应的第二驱动电机960正转启动并驱动丝杠959与连接块957作螺纹传动,使连接块957在驱动块951的下端垂直朝向承压圈7移动2cm-3cm;b、激光切割头96在对应的夹紧气缸93向下驱动作用下与承压圈7接触,此时激光切割头96启动,激光切割头96对应的驱动缸963继续向下驱动5mm-8mm,第二驱动电机960反转启动并驱动丝杠959与连接块957作螺纹传动,使连接块957在驱动块951的下端逐步向圆周焊缝的位置z处移动复位,从而形成引焊坡口961,此时激光切割头96对应的第二驱动电
机960停止,激光切割头96对应的第一驱动电机955启动,激光切割头96在对应驱动组95的驱动下对圆周焊缝进行开坡口处理,形成圆周焊缝坡口962,如图6示出了本步骤中圆周焊缝坡口962与引焊坡口961的结构示意图;c、埋弧焊接头97对应的第一驱动电机955随着激光切割头96对应的第一驱动电机955的启动而启动,当埋弧焊接头97置于圆周焊缝12的位置z处时,埋弧焊接头97对应的第二驱动电机960正转启动并驱动丝杠959与连接块957作螺纹传动,使连接块957在驱动块951的下端垂直朝向承压圈7移动2cm-3cm,埋弧焊接头97在对应的驱动缸963向下驱动作用下与引焊坡口961接触,此时埋弧焊接头97启动,第二驱动电机960反转,在引焊坡口961处开始引焊至位置z处,此时埋弧焊接头97对应的第二驱动电机960停止,埋弧焊接头97对应的第一驱动电机955启动,从而实现埋弧焊接头97在对应驱动组95的驱动下对圆周焊缝坡口962处进行焊接;d、当激光切割头96绕着圆周焊缝12转动一圈后,激光切割头96在对应的驱动缸963作用下向上复位移动,并在对应的第一驱动电机955的作用下继续前行2m-3m,当埋弧焊接头97绕着圆周焊缝12转动一圈后,埋弧焊接头97在对应的驱动缸963作用下向上复位移动,并在对应的第一驱动电机955的作用下继续前行1m-2m,从而实现圆周焊缝12的整体式开坡口以及整体式焊接;e、将组装对接装置9进行切割拆除,并对焊接后的圆周焊缝12处进行打磨。
26.在本技术中,第二驱动电机960转动带动连接块957在t型槽958内水平移动,从而带动激光切割头96以及埋弧焊接头97的水平式移动,实现在圆周焊缝12的位置z处进行引焊坡口处理,以及在引焊坡口961的起点处进行焊接,避免埋弧焊接头97焊接时因瞬间变化的电流电压直接作用在圆周焊缝12上而出现圆周焊缝起始焊接处应力集中的焊接缺陷,本发明将引焊坡口961设置在承压圈7上,即使具有一定的起始焊接缺陷,也会作用在承压圈7上不会直接作用在圆周焊缝12上,保证圆周焊缝高度一致的焊接质量以及焊接强度。
27.其次,本技术中采用特制的组装对接装置9,既有效实现了罐顶6与承压圈7之间的夹紧组装,又能实现整体式开坡口以及整体式圆周焊接,同时在开坡口处又能是吸纳引焊坡口以及引焊焊接,实现自动化开坡口以及自动化焊接,降低人员施工安全隐患,同时大大提高了罐顶6与承压圈7之间的连接强度以及连接稳定。
28.进一步的,钢丝绳11的一端与外罐5的上端固定,钢丝绳11的另一端经过罐顶6的外圆周至罐顶6的中心,并垂直向下与外罐5内侧中心固定,钢丝绳11与罐顶6之间通过滑轮17实现导向活动连接,多个钢丝绳11对罐顶6在气顶升过程中实现平衡稳定上升。
29.本行业的技术人员应该了解,本发明不受上述实施例的限制,上述实施例和说明书中描述的只是说明本发明的原理,在不脱离本发明精神和范围的前提下,本发明还会有各种变化和改进,这些变化和改进都落入要求保护的本发明范围内。本发明要求保护范围由所附的权利要求书及其等效物界定。