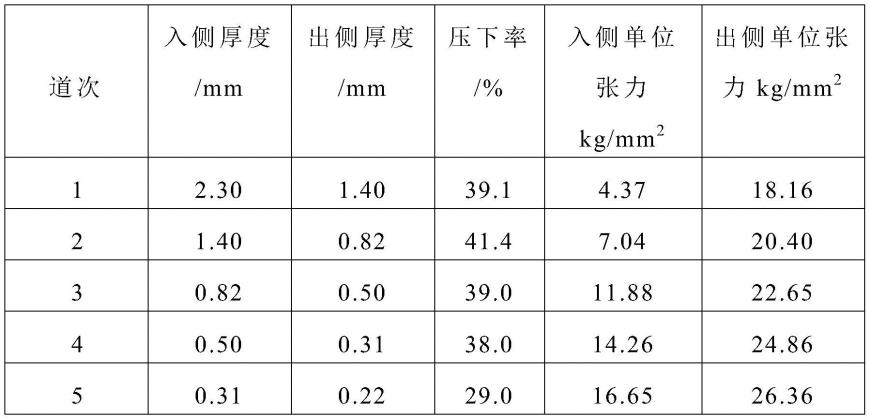
1.本发明涉及硅钢轧制技术领域,具体涉及一种极薄极低铁损取向硅钢的冷轧方法。
背景技术:2.近年来,节能变压器在电力传输领域得到大力推广,市场对极低铁损取向硅钢的需求呈爆发式增长。钢带厚度减薄是制造极低铁损取向硅钢的核心举措。然而,极薄取向硅钢轧制难度极高,存在轧制道次多,断带风险高,单卷轧制耗时长等问题。因此,极薄取向硅钢的生产效率低下,产量较低,不能满足市场爆发式增长的需求,其中冷轧工序成为最大制约瓶颈。
3.极薄取向硅钢中典型产品厚度规格为0.19mm、0.22mm,通常由单机架20辊轧机采用6~8道次一次冷轧至目标厚度。授权公告号cn 106583448 b发明专利中,公开了一种极薄规格高磁感取向硅钢的冷轧方法,主要特征为轧制前厚度2.0mm~2.5mm,采用一次冷轧法,进行连续可逆式七道次冷轧轧制,大幅提高了极薄规格高端硅钢的生产效率,产品无板形质量缺陷,表面质量良好,解决了极薄取向硅钢两次冷轧法的低效率问题。但是,此方法的冷轧小时产量最大为15.7吨/小时,仍不能满足生产线产能平衡需求和市场合同量需求。因此,继续提升极薄取向硅钢冷轧生产效率势在必行。
技术实现要素:4.为了克服现有技术中存在的不足,本发明目的是提供一种极薄极低铁损取向硅钢的冷轧方法。解决大规模工业生产中极薄规格0.19~0.22mm取向硅钢轧制效率低的问题。
5.为实现上述目的,本发明通过以下技术方案实现:
6.一种极薄极低铁损取向硅钢的冷轧方法,包括:
7.钢卷冷轧前厚度为2.0~2.6mm,进行常化酸洗;
8.对钢卷采用一次冷轧法,进行连续可逆式五道次冷轧轧制,具体如下:
9.前四道次采用粗面工作辊,工作辊表面粗糙度控制在2.5~3.2μm,末道次采用精面工作辊,工作辊表面粗糙度控制在0.2~0.4μm;
10.第一道次的压下率控制在35~40%,第二、三、四道次的压下率控制在35~43%,末道次的压下率控制在25~35%;
11.采用乳化液喷淋进行工艺润滑和冷却;控制前三道次板温逐渐升高至100~200℃;第四道次降温轧制;末道次常温轧制,板温控制在65~75℃;
12.第一、二道次手动控制板形,其余道次自动控制板形;
13.各道次轧制力控制在200~600t;各道次入侧张力控制在2~25kg/mm2,出侧单位张力控制在10~35kg/mm2;
14.第一道次速度控制在300~390m/min,第二道次速度控制在400~550m/min,其他道次速度控制在700~800m/min;
15.轧后产品厚度为0.19~0.22mm。
16.优选地,乳化液的浓度控制在3.0~4.5%,温度控制在40~60℃,第一道次采用单边喷淋,后四道次采用双边喷淋;第一道次入侧乳化液流量控制在3000~6000l/min,出侧乳化液流量均完全关闭。
17.优选地,第一、二道次手动控制板形,采用六次函数的目标板形曲线,钢带边部板形控制在35~+80i;六次函数为:
18.f(x)=a1x+a2x2+a4x4+a6x619.式中,f(x)为目标板形曲线,a1、a2、a4、a6为一次、二次、四次、六次项系数;x为横向坐标,经正则化处理后,带钢中部取0,传动侧边部取8,操作侧边部取10。
20.优选地,第一道次入侧单位张力控制在2~8kg/mm2,出侧单位张力控制在16~30kg/mm2;末道次入侧单位张力控制在12~22kg/mm2,出侧单位张力控制在14~32kg/mm2。
21.优选地,末道次轧制力控制在200~350t。
22.优选地,采用森吉米尔二十辊轧机进行轧制。
23.与现有技术相比,本发明具有如下优点:
24.本发明通过控制提高粗面辊粗糙度第一道次工作辊粗糙度2.5~3.2μm和增加出侧单位张力10~35kg/mm2,降低因压下率增加导致的打滑断带风险。
25.本发明通过打破常规的压下率分配方式,适当降低控制第一道次压下率控制在35%~40%,多维度降低第一道次打滑风险,为后续生产创造条件。
26.本发明通过精确控制各道次目标板形曲线,使钢带边部保持微翘,降低因硅含量提高和压下率增加导致的边裂断带风险。
27.本发明通过合理设置乳化液流量,精准控制前三道次轧制变形温度在100~200℃,使塑性变形为主导,降低脆断风险,同时实现了高磁感取向硅钢的时效轧制。
28.本发明进一步提高工业生产中极薄规格高磁感取向硅钢的生产效率,极薄取向硅钢的小时产量由15.7吨/小时提高至17.4吨/小时,生产效率提高了10%。产品无板形质量缺陷,表面质量良好。
具体实施方式
29.为了使本领域的技术人员更好地理解本发明的技术方案,下面结合具体实施例对本发明的优选实施方案进行描述,但是不能理解为对本专利的限制,仅作举例而已。
30.下述实施例中所述试验方法或测试方法,如无特殊说明,均为常规方法;所述试剂和材料,如无特殊说明,均从常规商业途径获得,或以常规方法制备。
31.本发明提供一种极薄极低铁损取向硅钢的冷轧方法,包括如下步骤:
32.1)钢卷冷轧前厚度为2.0mm~2.6mm,进行常化酸洗;
33.2)采用一次冷轧法,进行连续可逆式五道次冷轧轧制(以下子步骤不分先后):
34.2.1)前四道次采用粗面工作辊,工作辊表面粗糙度提高到2.5~3.2μm,降低道次压下率增加导致的打滑风险;末道次采用精面工作辊,工作辊表面粗糙度控制在0.2~0.4μm;
35.2.2)打破常规道次压下率依次降低的分配方式,控制第一道次的压下率在35%~40%,保证第一道次前滑值为正;规避打滑风险,第二、三、四道次采用大压下率,控制压下
率在35%~43%,使晶粒充分破碎;控制末道次的压下率在25%~35%,保证成品带钢板形平直;
36.2.3)采用乳化液喷淋进行工艺润滑和冷却;控制前三道次板温逐渐升高至100~200℃,保证轧制过程中板形曲线无跳动,满足轧制速度;第四道次降温轧制;末道次常温轧制,板温控制在65~75℃;
37.2.4)第一、二道次手动控制板形,其余道次自动控制板形;
38.2.5)各道次轧制力控制在200~600t,其中,末道次轧制力控制在200~350t,保证各道次在起步轧制时带钢不会因轧制力过大导致压薄断带;各道次入侧张力控制在2~25kg/mm2,出侧单位张力控制在10~35kg/mm2;能够有效保证轧制过程的稳定,改善带钢的板形和降低轧制力。
39.2.6)第一道次速度控制在300~390m/min,有效改善第一道次前滑,降低打滑风险;第二道次速度控制在400~550m/min,其他道次速度控制在700~800m/min,能够充分发挥设备潜能,保证轧制效率;
40.2.7)轧后产品厚度为0.19~0.22mm;
41.3)按照常规进行后工序。
42.步骤2.3)中,乳化液的浓度控制在3.0%~4.5%,温度控制在40℃~60℃,第一道次采用单边喷淋,后四道次采用双边喷淋;第一道次入侧乳化液流量控制在3000~6000l/min,出侧乳化液流量均完全关闭。
43.步骤2.4)中,第一、二道次手动动板形控制,采用六次函数的目标板形曲线,钢带边部板形控制在35~+80i,钢带边部翘起,规避边部控制过紧产生边裂;进一步地,所述六次函数为:
44.f(x)=a1x+a2x2+a4x4+a6x645.式中,f(x)为目标板形曲线,a1、a2、a4、a6为一次、二次、四次、六次项系数;x为横向坐标,经正则化处理后,带钢中部取0,传动侧边部取8,操作侧边部取10。
46.优选地,步骤2.5)中,第一道次入侧单位张力控制在2~8kg/mm2,出侧单位张力控制在16~30kg/mm2;末道次入侧单位张力控制在12~22kg/mm2,出侧单位张力控制在14~32kg/mm2。
47.优选地,步骤2)中,采用森吉米尔二十辊轧机进行轧制。
48.下面将结合实施1-4对本发明的冷轧方法进行详细说明。
49.实施例1
50.采用森吉米尔二十辊轧机轧制3.21%si的取向硅钢,具体步骤及控制参数如下:
51.1)冶炼、连铸、热轧沿用常规取向硅钢的生产方法,硅钢卷冷轧前厚度为2.3mm,进行常化酸洗;
52.2)采用一次冷轧法,进行连续可逆式五道次冷轧轧制(以下子步骤不分先后):
53.2.1)前四道次采用粗面工作辊(φ68mm),工作辊表面粗糙度控制在2.7μm;末道次采用精面工作辊(φ66mm),工作辊表面粗糙度控制在0.3μm;
54.2.2)控制压下率在20%~43%,其中,第一道次的压下率为39.13%,末道次的压下率为26.1%,其余各道次的压下率在20%~43%,本实施例各道次的具体压下率参见表1;
55.2.3)采用乳化液喷淋进行工艺润滑和冷却,乳化液的浓度控制在3.6%,乳化液温度为48℃;第一道次采用单边喷淋,入侧乳化液流量控制在4000l/min,出侧乳化液流量均完全关闭;后四道次采用双边喷淋;控制前三道次板温逐渐升高至180℃;第四道次降温轧制;末道次常温轧制,板温控制在67℃;
56.2.4)第一、二道次手动动板形控制,采用如下的六次函数的目标板形曲线:
57.f(x)=a1x+a2x2+a4x4+a6x658.式中,f(x)为目标板形曲线,a1、a2、a4、a6为一次、二次、四次、六次项系数;x为横向坐标,经正则化处理后,带钢中部取0,传动侧边部取8,操作侧边部取10;钢带边部板形控制在+70i,钢带边部微翘;
59.2.5)由于是可逆式轧制,轧制的同时进行卷取;各道次轧制力控制在200~600t;各道次入侧单位张力控制在2~25kg/mm2,出侧单位张力控制在10~35kg/mm2,其中第一道次入侧单位张力为2~8kg/mm2,出侧单位张力为16~30kg/mm2;成品道次入侧单位张力控制在12~22kg/mm2,出侧单位张力控制在14~32kg/mm2,本实施例各道次的具体单位张力参见表1;
60.2.6)稳定轧制速度,第一道次速度控制在360m/min,第二道次速度控制在470m/min,其他道次速度控制在750m/min,轧后产品厚度为0.22mm;
61.3)按照常规进行后工序。
62.该实施例极终产品实物质量优良,磁感b800达到1.89t,铁损p17/50为0.68w,每小时产量达17.4吨。
63.表1
[0064][0065]
实施例2
[0066]
采用森吉米尔二十辊轧机轧制3.21%si的取向硅钢,具体步骤及控制参数如下:
[0067]
1)冶炼、连铸、热轧沿用常规取向硅钢的生产方法,硅钢卷冷轧前厚度为2.6mm,进行常化酸洗;
[0068]
2)采用一次冷轧法,进行连续可逆式五道次冷轧轧制(以下子步骤不分先后):
[0069]
2.1)前四道次采用粗面工作辊(φ67.5mm),工作辊表面粗糙度控制在3.1μm;末道次采用精面工作辊(φ67mm),工作辊表面粗糙度控制在0.4μm;
[0070]
2.2)控制压下率在20~43%,其中,第一道次的压下率为39.2%,末道次的压下率为29%,其余各道次的压下率在20~43%,本实施例各道次的具体压下率参见表2;
[0071]
2.3)采用乳化液喷淋进行工艺润滑和冷却,乳化液的浓度控制在3.0%,乳化液温度为48℃;第一道次采用单边喷淋,入侧乳化液流量控制在3800l/min,出侧乳化液流量均完全关闭;后四道次采用双边喷淋;控制前三道次板温逐渐升高至190℃;第四道次降温轧制;末道次常温轧制,板温控制在68℃;
[0072]
2.4)第一、二道次手动动板形控制,采用如下的六次函数的目标板形曲线:
[0073]
f(x)=a1x+a2x2+a4x4+a6x6[0074]
式中,f(x)为目标板形曲线,a1、a2、a4、a6为一次、二次、四次、六次项系数;x为横向坐标,经正则化处理后,带钢中部取0,传动侧边部取8,操作侧边部取10;钢带边部板形控制在+78i,钢带边部微翘;
[0075]
2.5)由于是可逆式轧制,轧制的同时进行卷取;各道次轧制力控制在200~600t;各道次入侧单位张力控制在2~25kg/mm2,出侧单位张力控制在10~35kg/mm2,其中第一道次入侧单位张力为2~8kg/mm2,出侧单位张力为16~30kg/mm2;成品道次入侧单位张力控制在12~22kg/mm2,出侧单位张力控制在14~32kg/mm2,本实施例各道次的具体单位张力参见表2;
[0076]
2.6)稳定轧制速度,第一道次速度控制在330m/min,第二道次速度控制在455m/min,其他道次速度控制在740m/min,轧后产品厚度为0.22mm;
[0077]
3)按照常规进行后工序。
[0078]
该实施例极终产品实物质量优良,磁感b800达到1.91t,铁损p17/50为0.65w,每小时产量达17.6吨。
[0079]
表2
[0080][0081][0082]
实施例3
[0083]
采用森吉米尔二十辊轧机轧制3.21%si的取向硅钢,具体步骤及控制参数如下:
[0084]
1)冶炼、连铸、热轧沿用常规取向硅钢的生产方法,硅钢卷冷轧前厚度为2.3mm,进行常化酸洗;
[0085]
2)采用一次冷轧法,进行连续可逆式五道次冷轧轧制(以下子步骤不分先后):
[0086]
2.1)前四道次采用粗面工作辊(φ66.7mm),工作辊表面粗糙度控制在2.9μm;末道次采用精面工作辊(φ67.4mm),工作辊表面粗糙度控制在0.35μm;
[0087]
2.2)控制压下率在20%~43%,其中,第一道次的压下率为39.1%,末道次的压下率为29.6%,其余各道次的压下率在20%~43%,本实施例各道次的具体压下率参见表3;
[0088]
2.3)采用乳化液喷淋进行工艺润滑和冷却,乳化液的浓度控制在3.4%,乳化液温度为50℃;第一道次采用单边喷淋,入侧乳化液流量控制在4300l/min,出侧乳化液流量均完全关闭;后四道次采用双边喷淋;控制前三道次板温逐渐升高至190℃;第四道次降温轧制;末道次常温轧制,板温控制在70℃;
[0089]
2.4)第一、二道次手动动板形控制,采用如下的六次函数的目标板形曲线:
[0090]
f(x)=a1x+a2x2+a4x4+a6x6[0091]
式中,f(x)为目标板形曲线,a1、a2、a4、a6为一次、二次、四次、六次项系数;x为横向坐标,经正则化处理后,带钢中部取0,传动侧边部取8,操作侧边部取10;钢带边部板形控制在+74i,钢带边部微翘;
[0092]
2.5)由于是可逆式轧制,轧制的同时进行卷取;各道次轧制力控制在200~600t;各道次入侧单位张力控制在2~25kg/mm2,出侧单位张力控制在10~35kg/mm2,其中第一道次入侧单位张力为2~8kg/mm2,出侧单位张力为16~30kg/mm2;成品道次入侧单位张力控制在12~22kg/mm2,出侧单位张力控制在14~32kg/mm2,本实施例各道次的具体单位张力参见表3;
[0093]
2.6)稳定轧制速度第一道次速度控制在390m/min,第二道次速度控制在550m/min,其他道次速度控制在800m/min,轧后产品厚度为0.19mm;
[0094]
3)按照常规进行后工序。
[0095]
该实施例极终产品实物质量优良,磁感b800达到1.97t,铁损p17/50为0.62w,每小时产量达17.7吨。
[0096]
表3
[0097][0098]
实施例4
[0099]
采用森吉米尔二十辊轧机轧制3.21%si的取向硅钢,具体步骤及控制参数如下:
[0100]
1)冶炼、连铸、热轧沿用常规取向硅钢的生产方法,硅钢卷冷轧前厚度为2.0mm,进
行常化酸洗;
[0101]
2)采用一次冷轧法,进行连续可逆式五道次冷轧轧制(以下子步骤不分先后):
[0102]
2.1)前四道次采用粗面工作辊(φ68.2mm),工作辊表面粗糙度控制在2.6μm;末道次采用精面工作辊(φ69.1mm),工作辊表面粗糙度控制在0.32μm;
[0103]
2.2)控制压下率在20%~43%,其中,第一道次的压下率为37.5%,末道次的压下率为30.9%,其余各道次的压下率在20%~43%,本实施例各道次的具体压下率参见表4;
[0104]
2.3)采用乳化液喷淋进行工艺润滑和冷却,乳化液的浓度控制在3.8%,乳化液温度为49℃;第一道次采用单边喷淋,入侧乳化液流量控制在4100l/min,出侧乳化液流量均完全关闭;后四道次采用双边喷淋;控制前三道次板温逐渐升高至194℃;第四道次降温轧制;末道次常温轧制,板温控制在71℃;
[0105]
2.4)第一、二道次手动动板形控制,采用如下的六次函数的目标板形曲线:
[0106]
f(x)=a1x+a2x2+a4x4+a6x6[0107]
式中,f(x)为目标板形曲线,a1、a2、a4、a6为一次、二次、四次、六次项系数;x为横向坐标,经正则化处理后,带钢中部取0,传动侧边部取8,操作侧边部取10;钢带边部板形控制在+28i,钢带边部微翘;
[0108]
2.5)由于是可逆式轧制,轧制的同时进行卷取;各道次轧制力控制在200~600t;各道次入侧单位张力控制在2~25kg/mm2,出侧单位张力控制在10~35kg/mm2,其中第一道次入侧单位张力为2~8kg/mm2,出侧单位张力为16~30kg/mm2;成品道次入侧单位张力控制在12~22kg/mm2,出侧单位张力控制在14~32kg/mm2,本实施例各道次的具体单位张力参见表4;
[0109]
2.6)稳定轧制速度第一道次速度控制在300m/min,第二道次速度控制在400m/min,其他道次速度控制在700m/min,轧后产品厚度为0.19mm;
[0110]
3)按照常规进行后工序。
[0111]
该实施例极终产品实物质量优良,磁感b800达到1.95t,铁损p17/50为0.63w,每小时产量达17.5吨。
[0112]
表4
[0113][0114][0115]
综上所述,按实施例1~4中工艺冷轧后的极薄取向硅钢,板形值控制在0~+5i,钢
带平直;厚度精度
±
2μm;产品实物质量良好,磁性能达到高磁感低铁损指标,产品已用于昌吉-古泉
±
1100千伏、白鹤滩-江苏
±
800千伏等我国大型特高压直流工程,有力地支撑了国家重点项目建设,完全替代了进口取向硅钢。
[0116]
以上,仅为本发明的具体实施方式,应当指出,任何熟悉本领域的技术人员在本发明所揭示的技术范围内,可轻易想到的变化或替换,都应涵盖在本发明的保护范围之内,其余未详细说明的为现有技术。