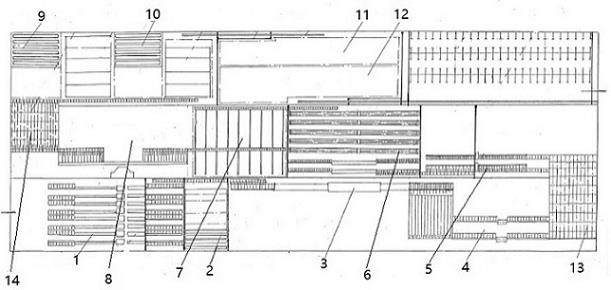
1.本发明涉及不锈钢管生产设备领域,特别是涉及一种半导体制备装置用超高纯净不锈钢管生产线。
背景技术:2.先进制程对晶圆生产环境纯净度再度提升,才能确保半导体芯片不受污染,提升生产良率。从28纳米走到7纳米,要求输送气体管道的金属杂质要求须下降100倍甚至更低。14纳米及以下先进制程的晶圆,其薄膜层非常薄,对氧气十分敏感,很容易被氧化,因此对晶圆制作的输送特种气体的316l不锈钢无缝管的洁净度要求更高。同时,该超高洁净316l不锈钢无缝管,生产工艺流程复杂。而目前不锈钢管整个生产过程以单机作业为主离散型生产,按离散型生产工序间的物料转移难度较大。同时,半导体精密器件生产过程中需要使用大量多种类的超净高纯特种气体,这种气体的纯净程度对半导体产品的质量和性能有着极大影响,为确保输送气体的清洁程度,需要保证不锈钢管内表面极高的光滑度以及优良的耐磨、耐腐蚀特性。因此,从生产线的设计角度入手,合理布局生产线工艺流程,高效、稳定的生产不锈钢管,减少生产流转过程中出现的损失,对半导体制备装置用超高洁净不锈钢管的产业化生产尤为重要。
3.半导体制备装置用超高纯净不锈钢无缝管生产线,通过生产线高质量的制造满足aisi 316l不锈钢无缝管的铁素体含量控制在≤1%、非金属夹杂物超高纯净化、晶粒度控制在5级甚至更细且完全奥氏体组织均匀一致、管内表面粗糙度ra0.13~0.20μm,cr/fe比>1.5:1,crox/feox比>2:1,同时兼顾力学性能、晶间腐蚀性能、疲劳性能等。钢管外径为9.53mm*0.89mm ~76.2mm*2.54mm,外径公差
±
0.02mm~
±
0.05mm,壁厚公差
±
10%,直线0.2mm/m以下,长度为≤12m等技术指标要求。为此,整个精轧管加工要在企业现有管坯制备的基础上,通过配置先进的精轧管、脱脂、固溶热处理、精密矫直、超声波涡流联合探伤、电解抛光、纯化等自动化工序设备以及工序自动联线装置。建立基本的工业化生产工艺技术与流程,使工艺产线布局合理。实现连续稳定生产,减少生产过程的交叉和迂回往返,提高产线自动化水平和生产效率。
技术实现要素:4.本发明主要解决的技术问题是提供一种半导体制备装置用超高纯净不锈钢管生产线,采用自动化装备与流程间的智能化传送装置相结合,构成基本智能化生产线,使流程顺畅、管线连线短,避免生产流程的交叉和迂回往返,使得半导体制备装置用超高纯净不锈钢管制造全程连续生产,保证了整个生产过程高效运行。
5.为解决上述技术问题,本发明采用的一个技术方案是:提供一种半导体制备装置用超高纯净不锈钢管生产线,包括呈平行设置的第一生产区域、第二生产区域和第三生产区域,所述第一生产区域和第二生产区域的左侧通过第一横移区域连通,所述第二生产区域和第三生产区域的右侧通过第二横移区域连通,所述第一生产区域的右端为管坯进口,
第三生产区域的左端为成品超高纯净不锈钢管的出口;所述第一生产区域包括从右往左依次设置的精轧管设备、内外脱脂装置、光亮热处理设备和矫直装置,所述第一生产区域内送入的管坯通过粗轧管和精密轧管、外壁脱脂和内壁脱脂、亮固溶热处理炉、矫直处理后送入第一横移区域,管坯再通过第一横移区域进入第二生产区域;所述第二生产区域包括从左往右依次设置的锯切装置、精密抛光装置、表面检查台和超声波涡流联合无损探伤装置,送入所述第二生产区域的管坯通过锯切齐头、抛光处理、表面检查、无损探伤后送入第二横移区域,不锈钢管再通过第二横移区域送入第三成产区域;所述第三生产区域包括电解抛光清洗装置、纯化清洗装置、吹扫干燥装置和包装装置、送入所述第二生产区域的不锈钢管通过电解抛光清洗、纯化清洗吹扫干燥和包装后送入仓储。
6.在本发明一个较佳实施例中,所述内外脱脂装置对管坯的外壁进油缠绕刮油、环形喷淋、刮脱脂液、二次漂洗和刮水处理进行脱脂,再通过内壁二次脱脂、二次漂洗、管外壁二次漂洗进行内壁脱脂。
7.在本发明一个较佳实施例中,所述矫直装置为高精度矫直管机,管坯经过矫直处理后被矫管材屈服强度达到200mpa及以上,矫后管材直线度<0.10-0.20mm/m,矫直盲区控制<160mm-300mm,矫直速度实现了0-30m/min。
8.在本发明一个较佳实施例中,所述超声波涡流联合无损探伤装置通过涡流检测系统和prp无线传输超声探头旋转体探伤系统对钢管进行无损探伤。
9.在本发明一个较佳实施例中,所述电解抛光清洗装置包括电解抛光设槽区、装卸料区、槽式浸泡超声波清洗区、内孔冲洗区、漂洗区和吹干区,控制酸液温度为45~60℃,直流多脉冲电压≤30v,电流密度为5~50a/dm2,电解抛光时间5~15 min。
10.在本发明一个较佳实施例中,所述纯化清洗装置包括装卸料区、纯化槽区、槽式浸泡超声波清洗区、内孔清洗区、漂洗区和吹干区。
11.在本发明一个较佳实施例中,所述吹扫干燥装置先在风淋间内先完成管表面吹扫,然后逐支对内孔通过高纯氮气吹扫,氮气经0.001μm过滤器过滤,含量达到99.999%,温度为60℃
±
5℃。
12.在本发明一个较佳实施例中,所述第一横移区域和第二横移区域包括定距块式传送带和带式传送带。
13.在本发明一个较佳实施例中,所述第一生产区域、第二生产区域和第三生产区域的内部通过自动连线设备连通各装置,自动连线设备包括水平和升降输送板链、输送辊道、拨料机构、输送v型辊道、翻料机构和顶升调节装置、输送同步带、储料架和立体库。
14.在本发明一个较佳实施例中,所述超高纯净不锈钢管的外径为9.53-76.2mm、壁厚为0.89-2.54mm,长度为6-12m。
15.本发明的有益效果是:本发明半导体制备装置用超高纯净不锈钢管生产线,制造过程主要工序均采用辊道装置平行传送,局部采用桥式超重机吊运,使半导体制备装置用超高洁净不锈钢管全流程自动传送,基本实现全流程智能化生产,保证了整个制造过程连续和稳定运行。
16.本发明半导体制备装置用超高纯净不锈钢管生产线,工艺流程呈s”形布置,整个制造过程非常流畅,避免了制造过程的在制品物流交叉和迂回往返。
附图说明
17.为了更清楚地说明本发明实施例中的技术方案,下面将对实施例描述中所需要使用的附图作简单地介绍,显而易见地,下面描述中的附图仅仅是本发明的一些实施例,对于本领域普通技术人员来讲,在不付出创造性劳动的前提下,还可以根据这些附图获得其它的附图,其中:图1是本发明半导体制备装置用超高洁净不锈钢管生产线一较佳实施例的结构示意图;图2是半导体制备装置用超高洁净不锈钢管生产线的工作流程示意图;附图中各部件的标记如下:1、精细轧制装置,2、内外脱脂装置,3、光亮热处理装置,4、矫直装置,5、齐头装置,6、精密抛光装置,7、表面检查台,8、超声波涡流联合无损探伤装置,9、电解抛光清洗装置,10、纯化清洗装置,11、吹扫干燥装置,12、包装装置,13、第一横移区域,14、第二横移区域。
具体实施方式
18.下面将对本发明实施例中的技术方案进行清楚、完整地描述。本说明书附图所绘示的结构、比例、大小等,均仅用以配合说明书所揭示的内容,以供熟悉此技术的人士了解与阅读,并非用以限定本发明可实施的限定条件,故不具技术上的实质意义,任何结构的修饰、比例关系的改变或大小的调整,在不影响本发明所能产生的功效及所能达成的目的下,均应仍落在本发明所揭示的技术内容得能涵盖的范围内。同时,本说明书中所引用的如“上”、“下”、“左”、“右”、“中间”等用语,亦仅为便于叙述的明了,而非用以限定可实施的范围,其相对关系的改变或调整,在无实质变更技术内容下,当亦视为本发明可实施的范畴。
19.请参阅图1,一种半导体制备装置用超高洁净不锈钢管生产线,包括三个相邻纵向跨区,整个车间流程在ⅲ纵向跨区呈“s”型布置。其中第一纵向跨区的一端为粗轧管进口,第三纵向跨区上与管坯进口相反的一端为成品出库口,在管内外吹扫、在洁净厂房区域进行,确保产品不被污染;离进口另一端的纵向第一跨区与第二跨区侧以及第二纵向跨区另一端与第三纵向跨区侧上部为18m宽钢桁架支承结构,使不锈钢管在三跨间自动搬运通过横向输送板链实现跨间的物流输送;三纵向跨间并列设备布置横向运输,通过设置于对应工位上方的龙门式横向吊运装置,实现局部管子横向吊运。
20.第一纵向跨区包括:半成品管坯进口及存放区、精密冷轧管机、外脱脂装置、内脱脂装置、辊底式光亮固熔炉和矫直机组。从所述半成品管坯进口及存放区、精密冷轧管机、冷轧管机、外脱脂装置、内脱脂装置、辊底式光亮固熔炉和矫直机组的管子,管子被横向输送板链送入第二纵向跨区。
21.第一纵向跨区外脱脂装置到矫直装置之间均设有分段式输送辊道,使第一纵向跨区的管子实现工序间输送。第一纵向跨区并列的外脱脂后部下料存放料框上方,设置了横向龙门式管子吊运装置,纵向为13.5m,横向为22.5m,把每台冷轧管机轧制后管子自动吊运到辊道式传送装置上,通过辊道式传送装置输送到内脱脂工序。第一纵向跨区内脱脂工序,
设置了横向龙门式管子吊运装置,把输送辊道上管子吊入槽式浸泡处理到待洗料架经翻转到内壁清洗工位到外壁漂洗和干燥工位、下料架到检验平台再经横移链排机到内壁热风干燥到翻转排列到向下工序的输送辊道。第一纵向跨区全氢光亮固溶热处理工序,通过平移辊道与上料台相联,使平排在料台上管子通过炉窑上料输送向炉内输送,固溶热处理后管子通过炉窑辊道式输送装置传送到矫直机上料台。第一纵向跨区矫直工序,管子从上料台逐支翻转到矫直保护筒内,保护筒内下部的v型辊把管子喂入高精度矫直机(40型,80型对置式布置),逐支对管子进行高精度矫直,通过设置于下料台间的输送板链向下传送。第一纵向跨区输出端设有横向板链式横移装置,长度为13.5m,使管子横向向第二纵向跨区输送。
22.第二跨区包括切割齐头、精密抛光设备、检查、超声波涡流联合无损探伤工序,从所述切割机、精密抛光设备、检查、超声波涡流联合无损探伤设备加工的管子,管子被横向输送板链送入第三纵向跨区。
23.第二纵向跨区精密抛光工序,有12头钢管自动外抛设备和内孔抛光设备组成,在设备上方横向龙门式管子吊运装置,使管子从一侧的平移辊道移送到并列布置抛光设备的上料台,逐支翻转到v型送料辊列,抛光后管子翻转到下料框内。第二纵向跨区齐头工序,辊道式输送装置把管子移送到齐头工序上料台,逐支翻料到切割台,人工完成两头切割齐头再经设置于下料台偏转式平移辊输送。第二纵向跨区检查工序,通过正反向横向移送板链,把管子排列到检查台上逐支对管子进行宏观检查、成分校验、内孔表面内窥镜检查。第二纵向跨区超声波涡流联合无损探伤设备下料台内设置横向板链移送装置,使加工管子平移到第三纵向跨区。
24.第三跨区包括电解抛光、清洗、纯化、清洗、管内外吹扫干燥、包装工序,从所述电解抛光、清洗、纯化、清洗、管内外吹扫干燥、包装的管子,从第三纵向跨区送出。
25.第三纵向跨区电解抛光工序,为横向布置的电解抛光槽区、装卸料区以及外部配套供酸、供水系统等组成。清洗工序,横向布置的槽式浸泡超声波清洗区、内孔清洗区、漂洗区、吹干等工位组成。第三纵向跨区纯化工序,横向布置的有纯化槽区、装卸料区以及外部配套供酸、供水系统等组成。纯化清洗工序,横向布置的槽式浸泡超声波清洗区、内孔清洗区、漂洗区、吹干等工位组成。管子超高洁净度检验遵循《用电抛光法测定不锈钢钝化》astm912-2002(2013)标准要求,管两端数值均≥18
×
106ωcm时当可合格。第三纵向跨区清洗工序配有集中式纯净水处理设备,设备纯净水处理量为18t/h。第三纵向跨区的纵向工序的物流,均采用分段式输送平移辊道传送,表面尼龙辊道须定时保洁。第三纵向跨区管内外吹扫干燥和包装工序,空气洁净度满足
ⅴ
级及以上等级,在风淋间内完成成品管子吹扫,内孔通过氮气吹扫,要求用含量为99.999%的氮气(经0.001μm过滤器过滤),温度到60℃
±
5℃,对管子内吹扫,达到超高洁净度的要求;包装工序:成品双层袋装防护,内层采用聚乙烯材质的无尘塑料袋抽真空密封,真空度控制在0.02mpa左右,外层采用聚乙烯塑料袋充洁净干燥的氮气后密封,氮气压力控制在0.1~0.3mpa。袋装后的成品,采用专用包装箱内防护。第三纵向跨区设有仓储系统,多层式存放结构,在仓库货架上方,设有轨道式装卸小车。通过轨道平车从洁净厂房移送到储存库一侧装卸工位,实现立体储存。实现自动存储、装卸、出库。
26.第一纵向跨区、第二纵向跨区、第三纵向跨区宽度为24m,纵向长度为198m。
27.半导体制备装置用超高洁净不锈钢管生产线,构成的精密冷轧管机、内外脱脂系统、全氢固溶热处理炉窑、矫直机、抛光设备、超声波涡流联合无损探伤、清洗等设备以及辅助的污水处理系统、供酸、供压缩空气、供氮气、废气处理、纯水处理、风淋系统、净化系统等系统为自动化、数字化设备,配有plc或cnc伺服控制控制系统,切割机、电解抛光、纯化、管内吹扫、包装工位均设有工序间传送按钮,且每个工位配置的扫码枪进行物料追踪,按节奏自动控制。设备上自带顶升调节装置、料台倾斜自动滚落机构及拨料装置与输送装置通过电控使钢管从在生产线中自动输送。可通过mes系统实现远程集中控制。
28.半导体制备装置用超高洁净不锈钢管生产线,为提高管子制造过程的传送效率,避免管子传送中碰撞以及人为操作对管子表面造成污染,不锈钢管在各工序间流转采用自动连线设备,主要有水平和升降输送板链、输送辊道、拨料机构、输送v型辊道、翻料机构和顶升调节装置、输送同步带、储料架、立体库等组成的工序间管子流转系统,由上位机、触摸屏、plc、伺服系统、变频器组和光电开关、接近开关等各类信号感知装置组成的全流程传送系统,保证管子在输送中高洁净度。全自动化冷加工、电解抛光等组成的生产线与自动连线设备组成的基础自动化制造系统,融入erp、crm、mes、pdm系统,不断完善生产过程控制与产品性能在线监测技术工艺,实现数字化制造及远程运维模式的柔性制造。
29.半导体制备装置用超高洁净不锈钢管生产线,在公司现有粗轧管生产线上完成粗轧管后,在本生产线完成精轧管、电解抛光制造,使管子满足超高洁净度要求,产线布置如图2所示,包括三个相邻的纵向跨区ⅰ、ⅱ、ⅲ的平列结构,整个车间生产工艺布局为“s”形。其中第ⅰ纵向跨区的一端为粗轧管进口,第ⅲ纵向跨区与粗轧进口相反的一端为成品包装出口,该区域为洁净厂房区域,确保产品不被污染;离进口另一端的纵向第ⅰ跨区与第ⅱ跨区侧以及第ⅱ纵向跨区另一端与第ⅲ纵向跨区侧上部为18m宽钢桁架支承结构,使不锈钢管在三跨间自动搬运通过横向输送板链实现跨间的物流输送。
30.第ⅰ纵向跨区设有依次连接的精轧管区、外脱脂区、内脱脂区、光亮固溶热处理区、矫直区。精轧管区和外脱脂区分别为8台冷轧管机配8台外脱脂区,选择精密轧管机型号的外径规格覆盖9.53mm~76mm,在外脱脂下料台及内脱脂区上方设置框架式龙门多点吊运装置,使并行分散在8个外脱脂下料台管子吊运到工序间流程辊道装置上;内脱脂依次并列的2条浸泡脱脂槽、管内壁清洗机、管外壁漂洗设备、管外壁吹扫装置、检查平台、干燥箱,依托横移链排机和翻料机构传送工序间传送的辊道输送装置。其中从输送辊道、浸泡脱脂槽和待洗料台采用多吊点式龙门起重装置移送;矫直区的下料平台直接与自动板链输送相联,使管子横向平移到第ⅱ纵向跨区,经升降输送板链平稳传送到切割机上料台。第ⅱ纵向跨区设有依次为切割齐头区、管内外精密抛光区、检查区、超声波涡流联合无损探伤区。其中管内外精密抛光区依次并列40型和100型外抛机及5台三头式内抛机,通过设置于设备上部的横向框架多吊点吊运装置,依次使抛光管从外抛机、内抛机、纵向输送棍道列间移送。第ⅲ纵向跨区设有依次为电解抛光和清洗区、纯化和清洗区、管子风淋区、管内吹扫区、包装区、立体储存。其中进入洁净厂房内依次从风淋区、管内吹扫区、包装区。电解抛光和清洗区依次设有电解抛光区、浸泡槽内超声波清洗、内孔循环冲洗、漂洗、吹干工位;纯化和清洗区依次设有纯化区、浸泡槽内超声波清洗、内孔循环冲洗、漂洗、洁净度检查、吹干工位;其中在酸洗区和纯化区厂房外侧设有供水、供酸、酸雾处理等辅助系统,清洗工位地下设有酸性废水处理系统、漂洗水再生处理系统、纯水系统等。
31.物料在s形生产线内的流向为:从精轧管进口ⅰ跨区进入,依次进入精密冷轧管区、外脱脂区、内脱脂区、光亮固溶热处理区、矫直区、通过横向和升降输送板链传送到ⅱ跨区依次进入切割齐头区、抛光处理区、检查区、超声波涡流联合无损探伤区、通过横向和升降输送板链传送到ⅲ跨区,依次进入电解抛光和清洗区、纯化和清洗区、依次进入洁净厂房内风淋区、管内吹扫区、包装区、立体储存区,然后从立体存储库发送。工序间物料传送采用输送辊道、输送板链、升降输送板链、v型辊、翻料机构、横向工位吊运装置、人工检测料台等组成的自动联线装置,通过plc、伺服系统、变频器组和光电开关、接近开关、扫码枪、按钮、工控机、触摸屏等各类信号感知装置组成,与mes、erp等生产执行系统相融合,实现整个生产线智能化控制。
32.通过本发明的生产线,与产线所有设备通过线缆联通,打通制备全流程生产质量信息流,实现产品生产质量异常追溯和关键生产质量参数在制备全流程的优化,通过装备自动化以及工序间的自动联线设备,再配合以少量的桥式起重机吊运,使超高洁净度精密不锈钢管生产可做到数字化生产,保证了整个生产过程信息畅通,提高了管材生产效率。
33.一种半导体制备装置用超高洁净不锈钢管生产线制备工艺步骤如下:1.在线粗轧管:轧制中间品管按mes生产计划要求,按生产工艺卡的批号、规格、牌号,经工序间连通的电动轨道车送到暂存区,测量检查中间品轧制管并分别吊运到精轧管上料台。
34.2.在线精密高速冷轧管机:上料台上管子经气动拨料机构到v型输送辊道完成自动上料,由夹送辊夹持送进,送进和转角采用伺服控制系统,行星齿轮带动机架运动完成轧制,气动拉出辊气动装置把轧制管快速拉出。mlc实现机组顺序和工艺联锁控制,hmi界面调整参数显示、状态监控和故障报警功能。
35.3.在线外壁脱脂:轧制管的在线外壁脱脂经缠绕刮油、二次脱脂(环形喷淋、刮脱脂液、二次漂洗、刮水完成外脱脂,整个过程有光栅传感器、压力变送器、温度传感器、变频器、plc、触摸屏组成自动控制系统,配套的脱脂液处理和漂洗水再生处理系统,实现外壁脱脂的在线自动控制。
36.4.在线内壁脱脂:轧制管内外壁的脱脂槽内浸泡的进出需要桥式起重机吊运外,管内壁二次脱脂、二次漂洗、管外壁二次漂洗、管外壁干燥、检查、管内壁热风干燥均为自动完成,全流程为plc控制,清洗节拍和速度可调。同步配套的脱脂槽液自动处理系统、漂洗槽液自动处理系统,实现内壁脱脂的在线自动控制。
37.5在线辊底式全氢光亮固溶热处理炉:采取高温抗氧化燃烧加热技术与热处理相结合的综合技术,提高传热效率和循环量,较强的还原作用,提高管子的光洁度、结晶更加均匀化。工序自动横向输送系统把管子堆送到自动辊道列,经进口密封室、入口预热段、热处理炉、高强喷流冷却段、缓冷室、出口密封室、出口辊列、输送辊道向下工序流转。德国ibs套管式自身预热式辐射管燃烧技术,炉温均匀性
±
5℃,控温精度≤
±
1℃、计算机控制、蓄热式技术、变频技术、全氢高强n2喷流快速冷却、辐射水冷却、强对流风冷满足快速冷要求。
38.6. 在线矫直:高精度矫直管机为满足外径规格系列要求,分设于40型、80型矫直管机组呈并列布置于输送辊道列之间,经设置于辊道列中间的横向平移板链(可正反移动)、翻料机构、倾斜式上料台、矫直保护筒、矫直主机、后台辊道列和下料台。实现了全自动程序控制,各机构的传送、保护筒的开合、矫直辊上下和偏转角度调整均由plc,人机界面,
变频器,各类传感器组成并自动程序控制运行。被矫管材屈服强度达到200mpa及以上,矫后管材直线度<0.10~0.20mm/m,矫直盲区控制<160mm~300mm,矫直速度实现了0~30m/min无级可调。
39.7. 管端面在线加工:管端切割加工分设有激光圆锯机、砂轮切割机呈并列布置于输送辊道列之间,经设置于辊道列中间的横向平移板链(可正反移动)、拨料机构、进料台、激光圆锯机、定尺机构、测长机构、出料台组成自动程序控制系统,对钢管端面进行切割加工,去除钢管端面毛刺。
40.8.在线管内外表面抛光:跨间自动传送板链通过横向框架多吊点吊运装置,依次把管子吊到并列40型和100型外抛机再到5台三头式内抛机。依次外抛机、内抛机、下工序输送棍道列移送。内外抛光机均为plc、触摸屏控制自动化设备,可通过光缆与mes系统相联。管内外粗糙度ra≤0.4μm。
41.9. 在线表面检查:通过设置于辊道列间正反向横向移送板链、拨料机构,把管子排列到检查台上,由人工逐支对管子进行宏观检查、成分校验、内孔表面内窥镜检查。
42.10.在线超声波涡流联合无损在线探伤:平放在上料台上管子通过拨料装置逐根把管子送到v型输送辊道上,由传送辊穿过涡流检测系统和prp无线传输超声探头旋转体探伤系统对钢管进行无损探伤,下料台设置合格与不合格品框,实现自动分选。
43.11. 电解抛光和清洗设备:电解抛光设槽区、装卸料区、槽式浸泡超声波清洗区、内孔冲洗区、漂洗区、吹干等工位组成。配套供磷酸、硫酸和供水系统、酸雾处理系统、酸性废水处理系统、漂洗废水处理以及纯净水处理系统均设有独立的plc控制系统。多台电解抛光槽的直流多脉冲电源、电加热棒、抛光液的循环系统的电压、电流密度、温度等参数为数字化控制。控制酸液温度为45~60℃,直流多脉冲电压≤30v,电流密度为5~50a/dm2,电解抛光时间5~15 min;从槽式浸泡超声波清洗区、内孔清洗区、漂洗区、吹干等工位间管子流转均为自动化控制系统。
44.12.纯化和清洗设备:设有装卸料区、纯化槽区、槽式浸泡超声波清洗区、内孔清洗区、漂洗区、吹干工位。配套供硝酸和供水系统、酸雾处理系统、酸性废水处理、漂洗废水处理以及纯净水再生系统与电解抛光工序共用处理系统,均设有独立的plc程序控制系统。多台纯化槽的压力、温度、处理时间等参数为数字化控制。从槽式浸泡超声波清洗区、内孔清洗区、漂洗区、吹干等工位间管子流转均为自动化控制系统。
45.13.管内外吹扫干燥设施,洁净厂房内空气洁净度满足
ⅴ
级及以上等级,其中,风淋间、管内吹扫与纯化和清洗工序衔接设有电动轨道车,在风淋间内先完成管表面吹扫。在洁净厂房内,排列在平台上管子,逐支对内孔通过高纯氮气吹扫,要求氮气经0.001μm过滤器过滤,含量达到99.999%,温度为60℃
±
5℃,达到超高洁净度的要求;14.包装工序:在洁净厂房内完成成品双层袋装防护,内层采用聚乙烯材质的无尘塑料袋抽真空密封,真空度控制在0.02mpa左右,外层采用聚乙烯塑料袋充洁净干燥的氮气后密封,氮气压力控制在0.1~0.3mpa。袋装后的成品,采用专用包装箱内防护。
46.15.仓储系统:通过工序间电动轨道车,从洁净厂房移送到立体仓储系统,在仓库货架上方,设有横向框架式自动装卸系统,完成洁净管的自动存储、装卸和出库。
47.除上述描述外的在制品工序间流转,所述转运设备为输送辊道、v型传送辊道、板链输送装置、输送同步带均为连续无级变频调速式,通过与生产线设备plc程序控制、卡号
扫码、各类传感器等,实现钢管得以平稳的纵、横移送,使整个生产线按节奏自动控制。生产过程中再配合以少量的行车吊运,不锈钢无缝盘管的生产可做到真正意义上的“不落地”生产,保证了整个生产过程连续和稳定进行,降低了管材受污染的可能性。
48.超高洁净管的外径为9.53~76.2mm、壁厚为0.89~2.54mm,长度为6~12m。
49.区别于现有技术,本发明生产线厂房为ⅲ纵向跨,长度为24m跨距,长度方向为198m,工艺流程呈s”形布置。管坯在从左侧ⅰ纵向跨一端进入,按照工艺流程逐步推进,从ⅰ纵向跨区另一端的相邻
ⅰⅱ
之间,经横向输送板链侧向移到ⅱ纵向跨区内,再从ⅱ纵向跨区的另一端设置于
ⅱⅲ
之间,横向输送板链侧面移到ⅲ纵向跨区内,再从ⅲ纵向跨区内另一端的洁净厂房内发出。整个制造过程非常流畅,避免了制造过程的在制品物流交叉和迂回往返。
50.管坯由存放区吊放到冷轧管机的上料台后,全流程工序流转均有各型输送装置输送。在ⅰ纵向跨区内外脱脂下料台和内脱脂装置上方均设有三点式龙门吊运装置,使横向分散多台套加工后管子长度为12m,通过吊运集中到工序辊送传送装置上,再经光亮固溶热处理、矫直、切割齐头工序后,经横向输送板链转运到ⅱ纵向跨区,由于厂房的柱间距为6m,要实现横向转运,在厂房上部设置18m宽纵向钢桁架支承结构,保证管子在转运过程不转向。在ⅱ纵向跨区在内外孔表面抛光处理上方配置三点式龙门吊运装置,在横向完成管子内外孔抛光的吊运、再经检查、超声波涡流联合无损探伤,经横向输送板链转运到ⅲ纵向跨区,经电解抛光、清洗、纯化、清洗,使达标的管子进入洁净车间,通过风淋系统后,再对内孔用用含量为99.999%的氮气(经0.001μm过滤器过滤),温度到60℃
±
5℃,对管子内吹扫,达到超高洁净度的要求。再经包装入库。因酸腐蚀的原因,电解抛光、清洗、纯化、清洗、包装采用桥式起重机吊运。
51.制造过程主要工序均采用辊道装置平行传送,局部采用桥式超重机吊运,使半导体制备装置用超高洁净不锈钢管全流程自动传送,基本实现全流程智能化生产,保证了整个制造过程连续和稳定运行。由于管子采取平移、上下及单支v型辊,板链节距50mm,宽度13.5mm,拉力3000n,每根管子尼龙档块高为40mm逐支传送,解决了管子传送受污染可能性。
52.本发明车间平面布置根据多品种、多规格和少批量的特点,通过工序配置的扫码枪,可满足不同品种的生产工艺要求,增加了组织生产的灵活性。
53.以上示意性的对本发明及其实施方式进行了描述,该描述没有限制性,附图中所示的也只是本发明的实施方式之一,实际的结构并不局限于此。所以,如果本领域的普通技术人员受其启示,在不脱离本发明创造宗旨的情况下,不经创造性的设计出与该技术方案相似的结构方式及实施例,均应属于本发明的保护范围。