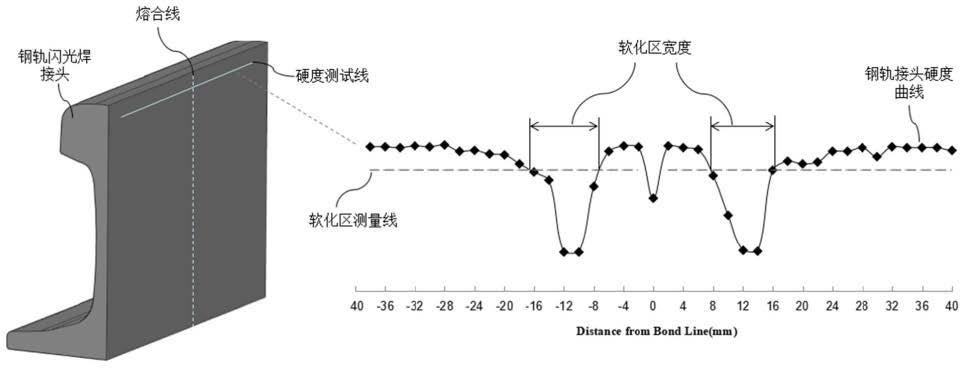
1.本发明涉及钢轨焊接技术领域,尤其涉及一种减小高强珠光体钢轨接头软化区宽度的方法。
背景技术:2.大量研究表明,钢轨焊接接头伤损在国内外重载线路伤损总数中占有很大的比重,是铁路线路关注的焦点。在钢轨焊接接头的上道服役过程中,钢轨接头的结合强度决定了钢轨接头是否容易发生疲劳或脆性断裂,钢轨接头的纵断面硬度决定了接头不同微区的平顺性。
3.钢轨闪光焊接头软化区是指焊接接头硬度明显低于母材的区域,及钢轨接头硬度出现软化现象。与接头再奥氏体化区域硬度低于母材不同,加热过程中软化区的金属未发生奥氏体转变,其温度区间通常处于金属热处理学上的退火区间,故软化区有时被称为退火区。因钢轨材质退火后通常为颗粒状的珠光体组织,故软化区又被称为球化退火区。一般情况下,接头软化区的拉伸、冲击性能较差,是钢轨接头的薄弱环节。因钢轨焊接主要是对钢轨端部进行局部加热,加热部位与未加热的母材间总会存在过渡区,该过渡区中硬度较低的区域就是软化区。软化区是钢轨焊接接头中一直存在的区域,无法彻底消除。相同焊接及焊后处理方法的条件下,不同化学成分及供货状态的钢轨接头的软化区不相同,澳标as标准中规定了不同材质钢轨的软化区宽度从20mm到40mm不等。通常情况下,软化区越窄约有利于接头的服役性能。因此,减小钢轨接头的软化区宽度是提高接头质量的有利途径。
4.然而,与普通线路或高速铁路线路相比,重载铁路线路的主要特点为轴重大。目前研究表明,轴重是对钢轨上道服役表现影响最大的因素,钢轨母材及接头的磨耗、滚动接触疲劳伤损、冲击动载以及脆性断裂等伤损均随着轴重的增大而严重。为提升重载线路钢轨最需要的磨耗性能,重载钢轨的强度和硬度均较高。钢轨的强度和硬度越高,钢轨的焊接性能越差,而焊接接头是铁路线路上的薄弱环节,对重载钢轨焊接接头性能的优化仍然是现有技术中心的研究重点。
5.因此,现有技术中存在对减小高强珠光体钢轨接头软化区的方法改进的需求。
技术实现要素:6.有鉴于此,本发明实施例的目的在于提出一种减小高强珠光体钢轨接头软化区宽度的方法,通过控制焊接过程的各项参数有效减小软化区宽度,远超标准规定的技术指标要求。
7.基于上述目的,本发明实施例的提供了一种减小高强珠光体钢轨接头软化区宽度的方法,该方法包括以下步骤:
8.钢轨接头在焊接时包括预闪光、闪光、加速烧化、顶锻及锻造五个阶段,预闪光阶段和闪光阶段通过闪光爆破整理钢轨待焊接面,加速烧化阶段控制加速烧化电压和闪光加速速度,顶锻阶段控制顶锻量,锻造阶段控制钢轨消耗量和锻造时间以减小软化区宽度;
9.按重量百分比计,高强珠光体钢轨包括0.72%~0.86%的碳、0.10%~1.00%的硅的、0.60%~1.30%的锰、不超过0.020%的磷、不超过0.020%的硫,不超过0.3%的铬,以及不超过0.01%的钒。
10.在一些实施方式中,预闪光阶段的高压时间为45s~65s,高电压为370v~440v,预闪光距离为2mm~10mm,闪光速度为0.1mm/s~0.6mm/s。
11.在一些实施方式中,闪光阶段的低压时间为80s~140s,低电压为320v~390v,闪光速度为0.1mm/s~0.6mm/s。
12.在一些实施方式中,加速烧化阶段的加速烧化电压为380v~450v,闪光加速速度为0.5mm/s~2.0mm/s。
13.在一些实施方式中,顶锻阶段的顶锻量为5.0mm~18.0mm。
14.在一些实施方式中,锻造阶段的钢轨消耗量为2.0mm~4.0mm,锻造时间为1.5s~3.0s。
15.在一些实施方式中,钢轨接头采用移动闪光焊接。
16.本发明另一方面还提供了一种使用上述方法处理的高强珠光体钢轨接头,该高强珠光体钢轨接头软化区宽度为5mm~10mm。
17.本发明至少具有以下有益技术效果:
18.本发明的方法通过将焊接过程分为预闪光、闪光、加速烧化、顶锻及锻造5个主要阶段,通过控制焊接过程的各项参数有效减小了高强珠光体钢轨接头软化区宽度,优化了重载钢轨焊接接头性能,采用该方法焊接的重载铁路用高强珠光体钢轨接头软化区宽度处于5mm~10mm的较好水平,且熔合线两侧软化区宽度相当,其最大值与最小值间的差值为1mm~4mm,远超标准规定的技术指标要求,接头其余性能也均满足标准要求。
附图说明
19.为了更清楚地说明本发明实施例或现有技术中的技术方案,下面将对实施例或现有技术描述中所需要使用的附图作简单地介绍,显而易见地,下面描述中的附图仅仅是本发明的一些实施例,对于本领域普通技术人员来讲,在不付出创造性劳动的前提下,还可以根据这些附图获得其他的实施例。
20.图1为本发明提供的高强珠光体钢轨闪光焊接头软化区实施例的示意图。
具体实施方式
21.为使本发明的目的、技术方案和优点更加清楚明白,以下结合具体实施例,并参照附图,对本发明实施例进一步详细说明。
22.需要说明的是,本发明实施例中所有使用“第一”和“第二”的表述均是为了区分两个相同名称非相同的实体或者非相同的参量,可见“第一”“第二”仅为了表述的方便,不应理解为对本发明实施例的限定,后续实施例对此不再一一说明。
23.本发明针对重载铁路用高强珠光体钢轨连续闪光焊接头软化区宽度过宽无法满足标准要求的问题,提供一种减小高强珠光体钢轨接头软化区宽度的方法,如图1所示为本发明提供的钢轨闪光焊接头软化区示意图,本发明的方法包括以下步骤:
24.钢轨接头在焊接时包括预闪光、闪光、加速烧化、顶锻及锻造五个阶段,预闪光阶
段和闪光阶段通过闪光爆破整理钢轨待焊接面,加速烧化阶段控制加速烧化电压和闪光加速速度,顶锻阶段控制顶锻量,锻造阶段控制钢轨消耗量和锻造时间以减小软化区宽度;
25.按重量百分比计,高强珠光体钢轨包括0.72%~0.86%的碳、0.10%~1.00%的硅的、0.60%~1.30%的锰、不超过0.020%的磷和硫,不超过0.3%的铬,以及不超过0.01%的钒。
26.进一步地,钢轨的最小抗拉强度为1080mpa,轨头最小硬度为310hb。
27.上述的连续闪光焊接,闪光过程主要通过预闪光、闪光、加速烧化实现,闪光过程平稳连续无中断。为达到减小高强珠光体钢轨接头软化区宽度的目的,需严格控制焊接过程各阶段的热量输入、热传导时间以及高温钢轨消耗量。
28.上述的预闪光阶段的主要作用是通过闪光爆破使得钢轨待焊截面平整清洁,为后续的闪光提供相对均匀平整的有利条件和基础热量。为达到控制热量、热传导时间以及高温钢轨消耗量的目的,主要需要控制该阶段高压时间、高电压、预闪光距离为和闪光速度。在一些实施例中,预闪光阶段的高压时间为45s~65s,高电压为370v~440v,预闪光距离为2mm~10mm,闪光速度为0.1mm/s~0.6mm/s。
29.上述的闪光阶段主要作用是通过闪光爆破使得钢轨待焊截面平整清洁,为后续的闪光提供相对均匀平整的有利条件和基础热量。为达到控制热量和热传导时间的目的,主要需要控制该阶段低压时间、低电压和闪光速度。在一些实施例中,闪光阶段的低压时间为80s~140s,低电压为320v~390v,闪光速度为0.1mm/s~0.6mm/s。
30.上述的加速烧化阶段主要作用是在整个焊接区域形成防止端面氧化的保护气氛,最终形成合适的温度场分布,为顶锻提供条件。为达到控制热量和热传导时间的目的,主要需要控制该阶段加速烧化电压和闪光加速速度。在一些实施例中,加速烧化阶段的加速烧化电压为380v~450v,加速速度为0.5mm/s~2.0mm/s。
31.上述的顶锻阶段主要作用是使得处于高温塑性状态的待焊钢轨产生原子间结合。为达到控制钢轨消耗的目的,主要需要控制该阶段的顶锻量。在一些实施例中,顶锻阶段的顶锻量为5.0mm~18.0mm。
32.上述的锻造阶段主要作用是在钢轨顶锻后的接头金属结晶过程中对钢轨接头持续施加载荷。为达到控制钢轨消耗以进一步减小高强珠光体钢轨接头软化区宽度的目的,主要需要控制该阶段的钢轨消耗量和锻造时间。在一些实施例中,锻造阶段钢轨消耗量为2.0mm~4.0mm,锻造时间为1.5s~3.0s。
33.本发明另一方面还提供了一种使用上述方法处理的高强珠光体钢轨接头,轨接头软化区宽度处于5mm~10mm的较好水平,且熔合线两侧软化区宽度相当,其最大值与最小值间的差值为1mm~4mm,远超标准规定的技术指标要求。
34.下面将根据具体实施例对本发明做出进一步解释。
35.实施例1
36.本实施例中试验用钢轨材料中碳的质量分数为0.73%、硅的质量分数为0.81%、锰的质量分数为1.12%。钢轨的抗拉强度为1180mpa~1200mpa,轨头硬度为310hb~320hb。连续闪光焊接的预闪光阶段的高压时间为45s,高电压为370v,预闪光距离为10mm,闪光速度为0.6mm/s;闪光阶段的低压时间为80s,低电压为320v,闪光速度为0.6mm/s;加速烧化阶段的加速烧化电压为380v,加速速度为2.0mm/s;顶锻阶段的顶锻量为18.0mm;锻造阶段钢
轨消耗量为4.0mm,锻造时间为3.0s。经检验,本实施例中钢轨接头左右两侧软化区宽度分别为6mm和7mm,最大值与最小值间的差值为1mm,远超标准规定的技术指标要求,并且接头其余性能也均满足标准要求。
37.实施例2
38.本实施例中试验用钢轨材料中碳的质量分数为0.73%、硅的质量分数为0.81%、锰的质量分数为1.12%。钢轨的抗拉强度为1180mpa~1200mpa,轨头硬度为310hb~320hb。连续闪光焊接的预闪光阶段的高压时间为65s,高电压为440v,预闪光距离为2mm,闪光速度为0.1mm/s;闪光阶段的低压时间为140s,低电压为390v,闪光速度为0.1mm/s;加速烧化阶段的加速烧化电压为450v,加速速度为0.5mm/s;顶锻阶段的顶锻量为5.0mm;锻造阶段钢轨消耗量为2.0mm,锻造时间为1.5s。经检验,本实施例中钢轨接头左右两侧软化区宽度分别为9mm和5mm,最大值与最小值间的差值为4mm,远超标准规定的技术指标要求,并且接头其余性能也均满足标准要求。
39.实施例3
40.本实施例中试验用钢轨材料中碳的质量分数为0.86%、硅的质量分数为0.58%、锰的质量分数为0.81%。钢轨的抗拉强度为1280mpa~1420mpa,轨头硬度为370hb~420hb。连续闪光焊接的预闪光阶段的高压时间为45s,高电压为370v,预闪光距离为10mm,闪光速度为0.6mm/s;闪光阶段的低压时间为80s,低电压为320v,闪光速度为0.6mm/s;加速烧化阶段的加速烧化电压为380v,加速速度为2.0mm/s;顶锻阶段的顶锻量为18.0mm;锻造阶段钢轨消耗量为4.0mm,锻造时间为3.0。经检验,本实施例中钢轨接头左右两侧软化区宽度分别为5mm和7mm,最大值与最小值间的差值为2mm,远超标准规定的技术指标要求,并且接头其余性能也均满足标准要求。
41.实施例4
42.本实施例中试验用钢轨材料中碳的质量分数为0.86%、硅的质量分数为0.58%、锰的质量分数为0.81%。钢轨的抗拉强度为1280mpa~1420mpa,轨头硬度为400hb~420hb。连续闪光焊接的预闪光阶段的高压时间为65s,高电压为440v,预闪光距离为2mm,闪光速度为0.1mm/s;闪光阶段的低压时间为140s,低电压为390v,闪光速度为0.1mm/s;加速烧化阶段的加速烧化电压为450v,加速速度为0.5mm/s;顶锻阶段的顶锻量为5.0mm;锻造阶段钢轨消耗量为2.0mm,锻造时间为1.5s。经检验,本实施例中钢轨接头左右两侧软化区宽度分别为9mm和6mm,最大值与最小值间的差值为3mm,远超标准规定的技术指标要求,并且接头其余性能也均满足标准要求。
43.实施例5
44.本实施例中试验用钢轨材料中碳的质量分数为0.82%、硅的质量分数为0.70%、锰的质量分数为0.92%。钢轨的抗拉强度为1180mpa~1300mpa,轨头硬度为350hb~410hb。连续闪光焊接的预闪光阶段的高压时间为50s,高电压为4050v,预闪光距离为5mm,闪光速度为0.3mm/s;闪光阶段的低压时间为110s,低电压为385v,闪光速度为0.5mm/s;加速烧化阶段的加速烧化电压为420v,加速速度为1.2mm/s;顶锻阶段的顶锻量为11.0mm;锻造阶段钢轨消耗量为2.6mm,锻造时间为2.1s。经检验,本实施例中钢轨接头左右两侧软化区宽度分别为9mm和7mm,最大值与最小值间的差值为2mm,远超标准规定的技术指标要求,并且接头其余性能也均满足标准要求。
45.对比例1
46.本对比例中试验用钢轨材料中碳的质量分数为0.73%、硅的质量分数为0.81%、锰的质量分数为1.12%。钢轨的抗拉强度为1180mpa~1200mpa,轨头硬度为310hb~320hb。连续闪光焊接的预闪光阶段的高压时间为40s,高电压为360v,预闪光距离为11mm,闪光速度为0.7mm/s;闪光阶段的低压时间为70s,低电压为310v,闪光速度为0.8mm/s;加速烧化阶段的加速烧化电压为375v,加速速度为2.3mm/s;顶锻阶段的顶锻量为19.0mm;锻造阶段钢轨消耗量为5.2mm,锻造时间为3.4s。经检验,本对比例中钢轨接头左右两侧软化区宽度分别为4mm和5mm,熔合线左右两侧软化区宽度的差值为1mm,并且接头在静弯试验过程中,当静弯载荷达到800kn时,接头发生断裂,不满足标准要求。本对比例中与实施例1和实施例2的主要区别在于焊接方法上。对比例采用的低于本专利权利要求的高压时间、低压时间,连续闪光过程短,焊接热输入小;采用低于本专利权利要求的电压值,连续闪光过程不剧烈,焊接热输入小;采用高于本专利权利要求各阶段闪光速度,高温金属消耗快,产生的热量损耗快,焊接热输入小;采用高于本专利权利要求的顶端量和锻造量及时间,钢轨高温消耗多,热量损失大,形成了“冷接头”,软化区虽然窄,但接头其余性能急剧下降。在钢轨材质相同的情况下,采用本对比例方法无法达到预期效果。
47.对比例2
48.本对比例中试验用钢轨材料中碳的质量分数为0.73%、硅的质量分数为0.81%、锰的质量分数为1.12%。钢轨的抗拉强度为1180mpa~1200mpa,轨头硬度为310hb~320hb。连续闪光焊接的预闪光阶段的高压时间为69s,高电压为450v,预闪光距离为2mm,闪光速度为0.1mm/s;闪光阶段的低压时间为152s,低电压为400v,闪光速度为0.1mm/s;加速烧化阶段的加速烧化电压为420v,加速速度为0.4mm/s;顶锻阶段的顶锻量为4.0mm;锻造阶段钢轨消耗量为0.5mm,锻造时间为1.0s。经检验,本对比例中钢轨接头左右两侧软化区宽度分别为22mm和23mm,熔合线左右两侧软化区宽度的差值为1mm,不满足标准要求。本对比例中与实施例1和实施例2的主要区别在于焊接方法上。对比例采用的高于本专利权利要求的高压时间、低压时间,连续闪光过程长,焊接热输入大;采用高于本专利权利要求的电压值,连续闪光过程剧烈,焊接热输入大;采用低于本专利权利要求各阶段闪光速度,高温金属消耗少,产生的热量损耗少,焊接热输入大;采用低于本专利权利要求的顶端量和锻造量及时间,钢轨高温消耗少,热量损失小,接头软化区宽度过宽。在钢轨材质相同的情况下,采用本对比例方法无法达到预期效果。
49.对比例3
50.本对比例中试验用钢轨材料中碳的质量分数为0.86%、硅的质量分数为0.58%、锰的质量分数为0.81%。钢轨的抗拉强度为1280mpa~1420mpa,轨头硬度为370hb~420hb。连续闪光焊接的预闪光阶段的高压时间为40s,高电压为360v,预闪光距离为11mm,闪光速度为0.7mm/s;闪光阶段的低压时间为70s,低电压为310v,闪光速度为0.8mm/s;加速烧化阶段的加速烧化电压为375v,加速速度为2.3mm/s;顶锻阶段的顶锻量为19.0mm;锻造阶段钢轨消耗量为5.2mm,锻造时间为3.4s。经检验,本对比例中钢轨接头左右两侧软化区宽度分别为4mm和5mm,熔合线左右两侧软化区宽度的差值为1mm,并且接头在静弯试验过程中,当静弯载荷达到800kn时,接头发生断裂,不满足标准要求。本对比例中与实施例3和实施例4的主要区别在于焊接方法上。对比例采用的低于本专利权利要求的高压时间、低压时间,连
续闪光过程短,焊接热输入小;采用低于本专利权利要求的电压值,连续闪光过程不剧烈,焊接热输入小;采用高于本专利权利要求各阶段闪光速度,高温金属消耗快,产生的热量损耗快,焊接热输入小;采用高于本专利权利要求的顶端量和锻造量及时间,钢轨高温消耗多,热量损失大,形成了“冷接头”,软化区虽然窄,但接头其余性能急剧下降。在钢轨材质相同的情况下,采用本对比例方法无法达到预期效果。
51.对比例4
52.本对比例中试验用钢轨材料中碳的质量分数为0.86%、硅的质量分数为0.58%、锰的质量分数为0.81%。钢轨的抗拉强度为1280mpa~1420mpa,轨头硬度为370hb~420hb。连续闪光焊接的预闪光阶段的高压时间为80s,高电压为420v,预闪光距离为2mm,闪光速度为0.1mm/s;闪光阶段的低压时间为170s,低电压为400v,闪光速度为0.1mm/s;加速烧化阶段的加速烧化电压为420v,加速速度为2.5mm/s;顶锻阶段的顶锻量为3.0mm;锻造阶段钢轨消耗量为2.0mm,锻造时间为1.0。经检验,本对比例中钢轨接头左右两侧软化区宽度分别为25mm和26mm,熔合线左右两侧软化区宽度的差值为1mm,不满足标准要求,同时在静弯试验中,当静弯载荷到达1500kn时,接头发生断裂,最大挠度值为8.4mm,不满足标准要求。本对比例中与实施例1和实施例2的主要区别在于焊接方法上。对比例采用的高于本专利权利要求的高压时间、低压时间,连续闪光过程长,焊接热输入大;采用高于本专利权利要求的电压值,连续闪光过程剧烈,焊接热输入大;采用低于本专利权利要求各阶段闪光速度,高温金属消耗少,产生的热量损耗少,焊接热输入大;采用低于本专利权利要求的顶端量和锻造量及时间,钢轨高温消耗少,热量损失小,接头软化区宽度过宽。同时,当焊接热输入量过大而顶锻量过小,钢轨结合强度降低,静弯性能急剧下降。在钢轨材质相同的情况下,采用本对比例方法无法达到预期效果。
53.对比例5
54.本对比例中试验用钢轨材料中碳的质量分数为0.82%、硅的质量分数为0.70%、锰的质量分数为0.92%。钢轨的抗拉强度为1180mpa~1300mpa,轨头硬度为350hb~410hb。连续闪光焊接的预闪光阶段的高压时间为40s,高电压为360v,预闪光距离为11mm,闪光速度为0.7mm/s;闪光阶段的低压时间为70s,低电压为310v,闪光速度为0.8mm/s;加速烧化阶段的加速烧化电压为375v,加速速度为2.3mm/s;顶锻阶段的顶锻量为20.0mm;锻造阶段钢轨消耗量为5.2mm,锻造时间为3.4s。经检验,本对比例中钢轨接头左右两侧软化区宽度分别为3mm和5mm,熔合线左右两侧软化区宽度的差值为2mm,并且接头在静弯试验过程中,当静弯载荷达到1000kn时,接头发生断裂,最大挠度值为7.6mm,不满足标准要求,且在接头标准检验位置检出异常的马氏体组织,不满足标准要求。本对比例中与实施例5的主要区别在于焊接方法上。对比例采用的低于本专利权利要求的高压时间、低压时间,连续闪光过程短,焊接热输入小;采用低于本专利权利要求的电压值,连续闪光过程不剧烈,焊接热输入小;采用高于本专利权利要求各阶段闪光速度,高温金属消耗快,产生的热量损耗快,焊接热输入小;采用高于本专利权利要求的顶端量和锻造量及时间,钢轨高温消耗多,热量损失大,形成了“冷接头”,软化区虽然窄,但接头其余性能急剧下降。同时,因接头热输入过小,冷却过程中的冷却速率大,局部区域易发生马氏体相变。在钢轨材质相同的情况下,采用本对比例方法无法达到预期效果。
55.对比例6
56.本对比例中试验用钢轨材料中碳的质量分数为0.82%、硅的质量分数为0.70%、锰的质量分数为0.92%。钢轨的抗拉强度为1180mpa~1300mpa,轨头硬度为350hb~410hb。连续闪光焊接的预闪光阶段的高压时间为85s,高电压为415v,预闪光距离为2mm,闪光速度为0.1mm/s;闪光阶段的低压时间为172s,低电压为410v,闪光速度为0.1mm/s;加速烧化阶段的加速烧化电压为425v,加速速度为2.5mm/s;顶锻阶段的顶锻量为3.0mm;锻造阶段钢轨消耗量为2.0mm,锻造时间为1.0。经检验,本对比例中钢轨接头左右两侧软化区宽度分别为24mm和25mm,熔合线左右两侧软化区宽度的差值为1mm,不满足标准要求,同时在静弯试验中,当静弯载荷到达1600kn时,接头发生断裂,最大挠度值为9.3mm,不满足标准要求。本对比例中与实施例5的主要区别在于焊接方法上。对比例采用的高于本专利权利要求的高压时间、低压时间,连续闪光过程长,焊接热输入大;采用高于本专利权利要求的电压值,连续闪光过程剧烈,焊接热输入大;采用低于本专利权利要求各阶段闪光速度,高温金属消耗少,产生的热量损耗少,焊接热输入大;采用低于本专利权利要求的顶端量和锻造量及时间,钢轨高温消耗少,热量损失小,接头软化区宽度过宽。同时,当焊接热输入量过大而顶锻量过小,钢轨结合强度降低,静弯性能急剧下降。在钢轨材质相同的情况下,采用本对比例方法无法达到预期效果。
57.以上是本发明公开的示例性实施例,但是应当注意,在不背离权利要求限定的本发明实施例公开的范围的前提下,可以进行多种改变和修改。根据这里描述的公开实施例的方法权利要求的功能、步骤和/或动作不需以任何特定顺序执行。此外,尽管本发明实施例公开的元素可以以个体形式描述或要求,但除非明确限制为单数,也可以理解为多个。
58.应当理解的是,在本文中使用的,除非上下文清楚地支持例外情况,单数形式“一个”旨在也包括复数形式。还应当理解的是,在本文中使用的“和/或”是指包括一个或者一个以上相关联地列出的项目的任意和所有可能组合。
59.上述本发明实施例公开实施例序号仅仅为了描述,不代表实施例的优劣。
60.本领域普通技术人员可以理解实现上述实施例的全部或部分步骤可以通过硬件来完成,也可以通过程序来指令相关的硬件完成,程序可以存储于一种计算机可读存储介质中,上述提到的存储介质可以是只读存储器,磁盘或光盘等。
61.所属领域的普通技术人员应当理解:以上任何实施例的讨论仅为示例性的,并非旨在暗示本发明实施例公开的范围(包括权利要求)被限于这些例子;在本发明实施例的思路下,以上实施例或者不同实施例中的技术特征之间也可以进行组合,并存在如上的本发明实施例的不同方面的许多其它变化,为了简明它们没有在细节中提供。因此,凡在本发明实施例的精神和原则之内,所做的任何省略、修改、等同替换、改进等,均应包含在本发明实施例的保护范围之内。