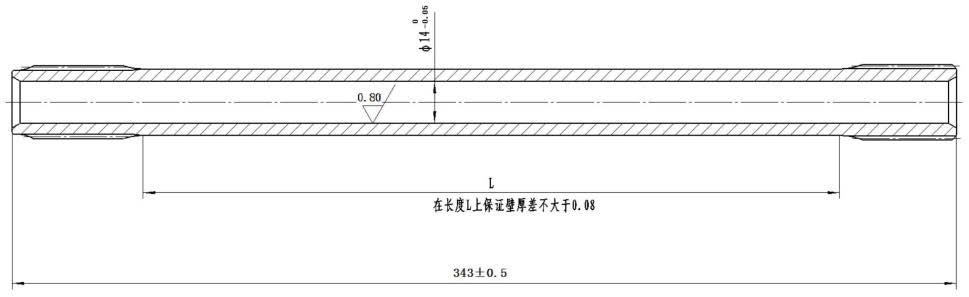
1.本发明属于航空发动机的中央传动轴加工技术领域,具体涉及一种深孔精密加工方法。
背景技术:2.某型别航空发动机的中央传动轴,是发动机中重要传动零件,承受较高扭矩,因此表面完整性要求较高。该零件内孔公差及表面粗糙度要求较严,对发动机起着至关重要的作用。传动轴结构如图1所示。传动杆毛料为自由锻φ40
×
343mm,内孔直径为φ14(0,-0.05)mm,粗糙度为ra0.8μm,且内孔需要表面完整,不能有台阶和划痕等缺陷,且通过现有加工方法加工的中央传动轴的加工公差和粗糙度均不能满足零件的精度要求。
技术实现要素:3.本发明的目的在于提供一种深孔精密加工方法,利用该加工方法可以成功解决某发动机中央传动轴无法加工的问题,通过本发明方法加工的零件的孔公差控制在为0.05mm以内,粗糙度控制为0.8um以为。
4.为了实现上述目的,本发明采用如下技术方案:
5.一种深孔精密加工方法,包括以下步骤:
6.步骤1,刀具选择
7.深孔粗加工采用深孔枪钻完成内孔余量去除;钻削加工后采用深孔拉铰方式进行半精加工;铰削加工后采用滚光方式提高内孔表面粗糙度,进行精加工;
8.步骤2,定位装夹方式
9.采用零件两端锥面顶紧方式装夹定位零件,并在刀杆及刀头处采用定位支架支撑刀杆和刀头防止刀杆变形影响内孔直线度;
10.步骤3,加工参数
11.为了保证零件的加工精度,需严格控制粗加工、半精加工及精加工过程中每把刀具的切削转速和进给量;
12.步骤4,钻孔加工过程
13.通过深孔枪钻完成零件的钻削粗加工;
14.步骤5,铰孔加工过程
15.通过内冷铰刀完成零件内孔的半精加工;
16.步骤6,滚光孔加工过程
17.通过深孔滚光刀完成零件内孔精加工。
18.步骤1深孔枪钻的选用120
°
的v型排屑槽、中空内冷钻杆及钻头;内冷铰刀选用三刃带引导的内冷铰刀;深孔滚光刀选用锥头顶杆支撑圆周均布的四个滚棒,尾端采用螺旋微调机构控制滚光压紧量,且按每0.005mm吃深一次挤压;所述深孔枪钻的钻头、内冷铰刀的刀刃部分及深孔滚光刀的刀头部分材料均采用硬质合金。
19.步骤3中控制粗加工、半精加工及精加工过程中每把刀具的切削转速和进给量,具体为:
20.粗加工采用分段进给加工,切削转速为800r/min,距离入口15mm以内时,进给量为25mm/min,而后采用进给量为15mm/min继续加工,采用分段进给的加工方式,减小偏离中心的趋势;半精加工切削转速1000r/min,进给量800mm/min;精加工切削转速200r/min,进给100mm/min。
21.步骤4,钻孔加工过程具体为:
22.步骤4.1,零件装夹
23.将零件按工艺规程加工到钻孔前状态,将零件放在数控深孔钻床的零件支撑座上支撑外圆d,并用卡盘预紧零件基准a端,调整卡盘座与引导座锥面之间的距离,顶紧零件,再将卡盘拧紧,此时引导座锥套压缩量为5~5.5mm,这时零件的装夹基准为外圆a、端面b、倒角c;
24.步骤4.2,刀具安装及加工
25.将深孔枪钻的钻头装在刀座上并固定,手动调整刀尖到引导座锥面的端面后,再退7~7.5mm设为z轴零点,完成钻孔对刀,开始钻孔,钻孔时采用内冷方式,冷却液将铁屑通过刀体的v型槽冲出,完成零件的钻孔加工。
26.步骤5,铰孔加工过程具体为:
27.步骤5.1,零件装夹
28.将钻孔后的零件卸下,将铰孔锥套安装在卡盘上夹紧,零件放在数控深孔钻床的托架上,用铰孔锥套和引导锥套顶紧零件,这时零件的装夹基准为端面b上的倒角、c处倒角;
29.步骤5.2,刀具安装及加工
30.先将深孔内冷铰刀的铰刀杆装在刀座内固定,手动进给调整刀杆至卡盘座零件b端面后,将铰刀刀头通过铰孔锥套的窗口拧入铰刀杆,调整内冷铰刀引导段进入零件内孔,并调整内冷铰刀切削部位与零件b端面之间距离为0.5~1mm范围内,完成内冷铰孔对刀,开始拉铰孔,铰孔时采用内冷方式,冷却液将铁屑通过刀头的v型槽推出,完成零件内孔的半精加工。
31.步骤6,滚光孔加工过程具体为:
32.步骤6.1,零件装夹
33.卸下半精加工后的零件和内冷铰刀锥套,将半精加工后的零件放在数控深孔钻床的零件支撑座上,将半精加工后的零件在卡盘上预紧基准a端,调整卡盘座与引导座锥面之间的距离,顶紧零件,再将卡盘拧紧,引导座锥套压缩量为5~5.5mm,此时零件的装夹基准为外圆a、端面b、倒角c;
34.步骤6.2,刀具安装及加工
35.将深孔滚光刀装在刀座上并固定,手动调整刀尖到引导座锥面的端面后,再退7~7.5mm设为z轴零点,完成滚光内孔对刀,开始进行滚光内孔,尺寸根据尾端调节旋钮控制,每次吃刀深0.005mm,保证内孔尺寸和粗糙度符合图纸要求,完成零件内孔精加工处理,零件加工完成。
36.本发明的有益技术效果为:
37.采用本专利技术后,可解决某新型发动机研制,解决因发动机无法整机试验的问题。单件成本为5000元,单台数量为件,年修理量为100台,年节约成本为:5000
×1×
100=50万元。此项技术已应用于该零件小批量生产中,此项技术可应用于各型号发动机中央传动轴加工,具有广泛的推广意义。
附图说明
38.图1本发明的中央传动轴结构示意图;
39.图2本发明的深孔加工刀具示意图,图2a为深孔枪钻的钻头,图2b为内冷铰刀,图2c为深孔滚光刀;
40.图3本发明中央传动轴工序图;
具体实施方式
41.下面结合附图和实施例对本发明作进一步的详细说明。
42.一种深孔精密加工方法,包括以下步骤:
43.步骤1,刀具选择
44.深孔粗加工采用深孔枪钻完成内孔余量去除,钻削加工时,刀具选用120
°
v型排屑槽、中空内冷钻杆和钻头,钻头采用硬质合金;钻削加工后采用深孔拉铰方式进行精度控制,进行半精加工,刀具选用三刃带引导的内冷铰刀,控制内孔尺寸精度,内冷铰刀的刀刃部分材料采用硬质合金;铰削加工后采用滚光方式提高内孔表面粗糙度,进行精加工处理,刀具选用锥头顶杆支撑圆周均布的四个滚棒,尾端采用螺旋微调机构控制滚光压紧量,按每0.005mm吃深一次挤压,提高内孔表面的粗糙度,滚刀头部的滚棒材料为硬质合金,如图2所示;
45.本实施例中,钻孔切削深度为钻头直径的1/2,铰孔切削深度为0.2mm,滚光切削深度为0.005mm;
46.步骤2,定位装夹方式
47.采用零件两端锥面顶紧方式装夹定位零件,并在刀杆及刀头处采用定位支架支撑刀杆和刀头防止刀杆变形影响内孔直线度;
48.步骤3,加工参数
49.控制每个刀具的切削转速和进给量,;
50.步骤4,钻孔加工过程
51.步骤4.1,零件装夹
52.如图3所示,将零件按工艺规程加工到钻孔前状态,将零件放在数控深孔钻床的零件支撑座上支撑外圆d,并用卡盘预紧零件基准a端,调整卡盘座与引导座锥面之间的距离,顶紧零件,再将卡盘拧紧,此时引导座锥套压缩量为5mm,这时零件的装夹基准为外圆a、端面b、倒角c;
53.步骤4.2,刀具安装及加工
54.将深孔枪钻的钻头装在刀座上并固定,手动调整刀尖到引导座锥面的端面后,再退7mm设为z轴零点,完成钻孔对刀,开始钻孔,钻孔时采用内冷方式,冷却液将铁屑通过刀体的v型槽冲出;完成零件的钻孔加工;
55.步骤5,铰孔加工过程
56.步骤5.1,零件装夹
57.将钻孔后的零件卸下,将铰孔锥套安装在卡盘上夹紧,零件放在数控深孔钻床的托架上,用铰孔锥套和引导锥套顶紧零件,这时零件的装夹基准为端面b上的倒角、c处倒角;
58.步骤5.2,刀具安装及加工
59.先将深孔内冷铰刀的铰刀杆装在刀座内固定,手动进给调整刀杆至卡盘座零件b端面后,将铰刀刀头通过铰孔锥套的窗口拧入铰刀杆,调整内冷铰刀引导段进入零件内孔,并调整内冷铰刀切削部位与零件b端面之间距离为0.5mm范围内,完成内冷铰孔对刀,开始拉铰孔,铰孔时采用内冷方式,冷却液将铁屑通过刀头的v型槽推出,完成零件内孔的半精加工;
60.步骤6,滚光孔加工过程
61.步骤6.1,零件装夹
62.卸下半精加工后的零件和内冷铰刀锥套,将半精加工后的零件放在数控深孔钻床的零件支撑座上,将半精加工后的零件在卡盘上预紧基准a端,调整卡盘座与引导座锥面之间的距离,顶紧零件,再将卡盘拧紧,引导座锥套压缩量为5mm,此时零件的装夹基准为外圆a、端面b、倒角c;
63.步骤6.2,刀具安装及加工
64.将深孔滚光刀装在刀座上并固定,手动调整刀尖到引导座锥面的端面后,再退7mm设为z轴零点,完成滚光内孔对刀,开始进行滚光内孔,尺寸根据尾端调节旋钮控制,每次吃刀深0.005mm,保证内孔尺寸和粗糙度符合图纸要求,完成零件内孔精加工处理,零件加工完成。