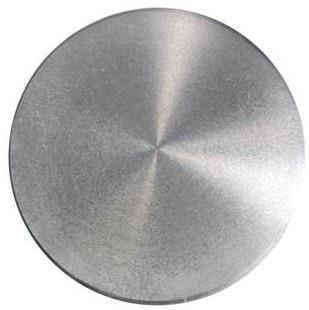
一种
φ
80-φ
120mm高强高韧钛合金棒材制备方法
技术领域
1.本发明涉及钛合金加工技术领域,具体涉及一种φ80~φ120mm高强高韧钛合金棒材制备方法。
背景技术:2.先进钛合金材料的大量应用是新一代飞机先进性的显著标志之一,目前钛合金在新型飞机结构件上的占比达到30~40%,高强钢在飞机结构材料的占比依然较大。为了实现飞机的进一步减重,新型超高强高韧钛合金的应用能够替代原有的高强钢,从而大幅度度提高结构减重效果和安全可靠性。随着飞机设计理念向长寿命发展,这就要求钛合金材料在具备高强度时,同时需要具备较高的韧性,这样才能符合飞机的长寿命设计需求。
3.ti55531合金是一种高强型β钛合金,通常可用于飞机的承力结构件,该合金的力学性能受锻造工艺与冷却速率影响。目前工程化应用的ti55531钛合金棒材在强度达到1350mpa级时,材料的延伸率通常为3~5%, k
ic
≤45 mpa
·m1/2
。为了实现棒材的塑性提升,国内外往往通过多火次镦拔锻造来破碎组织,从而实现塑性的提升,但往往组织细化会带来kic的降低。
4.cn2018113029330公开了一种ti55531钛合金大规格棒材自由锻造方法,该方法经开坯锻造、动态再结晶热处理加工、β转变温度以下锻造来实现,利用再结晶热处理实现ti55531坯料组织的快速细化。但这种方式适用于直径为φ400~φ500mm的大规格棒材,不适合小规格棒材。对于小规格棒材而言,随着棒材规格减小,热处理后的冷却速率加快,合金的强度会急剧提高,同时塑性与韧性会显著降低。因此,发明一种新型加工工艺使ti55531合金强度达到1350mpa级,延伸率达到5%以上,k
ic
≥60mpa
·m1/2
,对于新一代飞机的发展具有重要意义。
技术实现要素:5.针对上述现有技术存在的不足,本发明的目的是提供一种短流程且规格为φ80~φ120mm的高强高韧钛合金棒材制备方法,该方法能够生产出强度达到1350mpa级、延伸率达到5%以上、k
ic
≥60mpa
·m1/2
的钛合金棒材,这种钛合金棒材组织为片层组织,棒材组织均匀性良好,力学性能稳定,各向异性弱,适用于工业化生产。
6.本技术所用的材料为ti55531钛合金φ780mm规格铸锭,其制造方法涉及中间坯的自由锻造与成品棒材全自动化径向锻造,分别包含开坯锻造,两相区拔长锻造,单相区拔长锻造、转序坯成型锻造、径向锻造和成品热处理几个步骤。
7.为实现上述目的,本发明采用的技术方案具体为:一种φ80~φ120mm的高强高韧钛合金棒材制备方法,通过如下步骤来实现:步骤1)、开坯锻造此步骤在45mn快锻机分1~2火完成。首先将ti55531铸锭在1150~1200℃进行加热,随后在45mn快锻机上进行1~2火次镦拔或拔长锻造,最终将坯料锻至成方坯,在锻后采用空
冷;步骤2)、两相区拔长锻造此步骤在45mn快锻机分2~3火完成。先将经过步骤1)处理的坯料在β转变温度以下30℃~70℃进行加热,随后在45mn快锻机上进行2~3火次拔长,锻制成
□
250~260mm的四方方坯;两相区总变形量大于90%,且在执行该步骤时,需严格控制拔长时的压下速率不大于8~15mm/s,每火次锻造完成后,采用空冷;步骤3)、单相区拔长锻造此步骤也在45mn快锻机分1火完成。先将经过步骤2)处理的坯料在β转变温度以上30℃~80℃加热并保温,随后在45mn快锻机上进行1火次拔长锻造,锻制成
□
210~220mm的八方方坯,锻后采用空冷;步骤4)、转序坯成型锻造此步骤也在45mn快锻机分1火完成。将经过步骤3)处理的坯料在β转变温度以下30℃~40℃加热并保温,随后在45mn快锻机上将坯料锻制成φ200mm圆棒,该火次总变形量不大于20%,锻造完成后进行空冷;步骤5)、径向锻造此步骤在skk17精锻机中分2火完成。将经过步骤4)处理的坯料在β转变温度以下40℃~70℃进行加热并保温,随后在skk17精锻机中进行1火次沿着径向锻造至φ120~150mm圆棒,锻造变形量大于50%;锻造完成后立即回炉加热至β转变温度以上15℃~30℃并保温,随后进行1火次沿着径向锻造至成品尺寸,该火次锻造变形量大于60%,锻后采用急速冷却;该步骤需要严格控制精锻频次为240~600次/min,拉打速率控制在3~4m/min;步骤6)、成品热处理成品热处理采用双重退火。将经过步骤5)处理的成品棒材加热至β转变温度以下 10℃~25℃并保温120min,然后以2~10℃/min的冷却速率冷却至700~750℃,随后以30~50℃/min降温至450~600℃,并在该温度下加热4~8h,随后出炉进行空冷。
8.ti55531合金在热变形过程中难以发生再结晶,现有的技术中主要通过增加镦拔火次,积累足够的变形量来破碎组织,从而达到均匀的目的。针对该合金的特点,本发明为了避免镦拔锻造带来的组织不均匀现象,采用了少镦拔、大拔长的锻造方式,同时优化再结晶加热制度、锻造变形量与锻造速率,来实现组织的细化与均匀化。能够实现本发明的目的主要原理为:本发明在步骤2)两相区拔长锻造过程中采用了拔长锻造的方式,粗大的β晶粒尺寸在此过程中因变形协调效应承受主要变形,细小的β晶粒在变形过程中发生转动,拉长程度较弱,此时不均匀的β晶粒拉长变形呈现细小的纤维状组织。在两相区积累不低于90%的变形量,积累了足够的畸变能,增加再结晶的形核点,使得组织破碎充分,提高了组织均匀性。在随后的步骤3)单相区长时间加热过程中,再结晶晶粒在原本拉长的初始β晶界与晶内形核与长大,从而实现组织细化与均匀化。为了突破现有技术的瓶颈,实现该合金超高强度与高韧性的匹配,在步骤5)中,通过调控工艺参数来调控组织,利用高速变形的特点充分破碎组织,同时在高速变形过程中变形储来不及通过再结晶释放而储存在材料内部,在步骤6)的热处理参数调控过程中,残留在内部的残余应力能够弥补网篮组织带来强度降低的步骤,从而实现超高强与高韧性的性能匹配。本发明的工艺设计理念与现有技术相比有着本质的差异,将变形方式与再结晶的机理相结合,实现组织的显著细化。通过高速变形方式
控制残余应力来实现网篮组织强度的提升,各步骤间协调配合获得超高强度-高韧性的良好匹配。
9.优选地,上述步骤2)中,两相区拔长中每火次拔长变形量控制为30%~40%、压下速率控制为8~15mm/s,拔长方式采用对角拔,其中拔长送进量为400~600mm,每一道次拔长时压下量与送进量量的关系满足:压下量s=(1/4~1/3)送进量b。
10.本技术通过在两相区要求控制拔长送进量为400~600mm,通过有限元仿真确定每一道次拔长时压下量与送进量量的关系满足:压下量s=(1/4~1/3)送进量b,拔长时的效率更高,组织一致性更好。
11.优选地,上述步骤3)中,单相区的加热保温时间按照坯料最小截面尺寸
×
加热系数δ (min/mm)计算,加热系数δ一般取0.7~1.0;该步骤中拔长变形量需大于30%。在现有的技术下,为了避免晶粒粗化带来的塑性降低,往往在单相区选用较短的加热时间。本发明在该步骤的加热系数更长,其目的是通过在单相区的长时间加热,使得再结晶后的组织充分长大,从而获得较均匀的组织。此外,本发明通过控制步骤2)的工艺参数,能够获得比现有技术更细小均匀的β再结晶组织。因此,本发明在设计的思路与现有技术有着本质的差别。
12.优选地,上述步骤4)中,两相区的加热保温时间按照坯料最小截面尺寸
×
加热系数δ (min/mm)计算,加热系数δ一般取0.6~0.8;成型锻造需在v型砧或者圆形摔砧上进行。
13.优选地,上述步骤5)中,β转变温度以下加热保温时间按照坯料最小截面尺寸
×
加热系数δ (min/mm)计算,加热系数δ一般取0.6~0.8,锻打频率控制为600次/min,且锻后立刻回炉;而β转变温度以上加热保温时间按照坯料最小截面尺寸
×
加热系数δ (min/mm)计算,加热系数δ一般取0.3~0.5。在单相区径向锻造的第1道次下压量需大于30mm,拉打速率控制在3~4m/min,控制精锻频次为240~600次/min,锻造完成后立刻使用不低于150℃/s的冷却速率进行快速冷却。
14.本技术通过在步骤5)的成品锻造时温度选择在t
β
+(15~30)℃获得片层状组织,在单相区锻造时控制总变形达到60%以上,其中第一道次下压量需大于30mm,拉打速率控制在3~4m/min,从而保证棒材心部的锻透性,使晶界α相充分破碎,从而提高塑性。
15.与现有技术相比,本发明具备的有益效果如下:(1)本发明生产棒材的锻造总火次为7~9火(实际冷料火次为5~7火),较传统钛合金小规格棒材的锻造14~16火加工成本降低约20%,综合成品率提升约10%。与现有技术相比,本发明能够在锻造火次少的情况下,实现超高强度、高塑性与高韧性的良好匹配,生产成本更低;(2)本发明主要通过少镦拔、大拔长、高速锻造的特点来实现组织细化与均匀化;与现有技术相比,本发明在步骤2)两相区拔长锻造过程中采用了拔长锻造的方式,粗大的β晶粒尺寸在此过程中因变形协调效应承受主要变形,细小的β晶粒在变形过程中发生转动,拉长程度较弱,此时不均匀的β晶粒拉长变形呈现细小的纤维状组织。在两相区积累不低于90%的变形量,积累了足够的畸变能,增加再结晶的形核点,使得组织破碎充分,提高了组织均匀性。在随后的步骤3)单相区长时间加热过程中,再结晶晶粒在原本拉长的初始β晶界与晶内形核与长大,从而实现组织细化与均匀化。与现有技术下通过多火次镦拔锻造破碎组织的方式相比,本发明在设计的思路与之有着本质的差别;(3)本发明生产的ti55531棒材强度能够达到1350mpa级,延伸率达到5%以上,k
ic
≥
60mpa
·m1/2
,各项性能均优于现有技术下生产的棒材;(4)本发明在步骤5)中进行高速锻造,能够实现强度的进一步提升。本发明在径向锻造的成品火次采用了单相区锻造获得网篮组织来提高断裂性能,但该组织的强度会有所降低。为了实现强度的进一步提升,棒材在skk17精锻机上进行高速变形,这是因为高速变形会增加材料内部的残余应力,使得组织充分破碎,从而提高了成品棒材的强度。此外,结合ti55531合金两相区锻造易过热的特点,本发明采用精锻机进行单相区快速锻造,无需考虑棒材因锻造温升而过热的问题;(5)本发明中的径向锻造后的冷却方式与成品热处理是提高棒材性能均匀性的关键。β锻造完成后以不低于150℃/s的冷却速率将棒材温度降至室温,保证锻造完成后急速冷却能够抑制晶界α相的析出。在随后的热处理过程中,首先以2~10℃/min的冷却速率冷却至700~750℃,随后以30~50℃/min降温至450~ 600℃,其主要目的是通过控制冷却速率为2~10℃/min冷却至700~750℃,使片层α相厚度增加,保证棒材具有与良好的断裂韧度,在随后加快冷却速率至30~50℃/min降温至450~ 600℃,快速冷却至时效温度进一步提高强度;同时控制热处理的冷却速率减弱了因冷却过程中温度场的不均匀造成性能的差异性,提高了组织的一致性;(6)本发明生产的热处理态ti55531合金小规格棒材性能一致性好,避免了传统工艺加工后的零件在热处理后因尺寸效应而造成性能差异大而造成的零件报废,大大的提高了零件的合格率。
附图说明
16.图1为本发明实施例一中制备的φ80mm规格棒材的低倍组织图;图2为本发明实施例一种制备的φ80mm规格棒材的显微组织图;图3为采用现有技术的方法制备的φ80mm规格棒材的低倍组织图图4为采用现有技术的方法制备的φ80mm规格棒材的正常的显微组织图;图5为为采用现有技术的方法制备的φ80mm规格棒材的过热的显微组织图。
具体实施方式
17.下面结合优选实施例对本发明进行详细阐述,以使本发明的优点和特征能更易于被本领域技术人员理解,从而对本发明的保护范围做出更为清楚明确的界定。任何在不脱离本发明构思前提下的相同或相似方案均应落在本发明的保护范围内。且文中未详述部分,均按本领域常规方式进行。且下文中:“φ”指代的是横截面为圆形的坯料的直径;
“□”
指代的是横截面为方形的坯料的边长;“t
β”为β转变温度;t为保温时间(单位min),δ为加热系数(单位min/mm),h为坯料最小截面尺寸(单位mm),当给定加热系数时,坯料保温时间t的计算方法为t=δ
×
h。
18.实施例(φ80mm规格棒材锻造方法)选用ti55531钛合金φ780mm规格铸锭,铸锭β转变温度为840℃。
19.步骤1:将ti55531铸锭加热至1150℃进行保温,该步骤中加热系数为0.7~0.75min/mm。
20.步骤2:将步骤1中处理后的锭坯进行开坯锻造,设备采用45mn快锻机。锻造方法为
将φ780mm铸锭进行1火次锻造至四方
□
600 mm,锻造方式为2镦2拔,锻后采用空冷;该步骤中累计的总变形量不小于80%,终锻温度不低于850℃。
21.步骤3:将步骤2中所得坯料在800℃加热保温,该步骤中加热系数为0.7~0.8min/mm。
22.步骤4:将步骤3中处理的锭坯分3火次进行拔长锻造,锻造至
□
250mm的四方方坯,每火次锻后均采用空冷。该步骤中每火次拔长变形量控制在30~40%之间,压下速率控制在8~15mm/s,其中第1~2火拔长方式采用对角拔,终锻温度不低于650℃。
23.在进行步骤4中,拔长送进量为500mm,严格控制每一道次拔长时压下量与送进量的关系满足:压下量s=(1/4~1/3)送进量b。
24.步骤5:将步骤4中处理后的锭坯加热至920℃进行保温,该步骤中加热系数为0.9~1.0min/mm。
25.步骤6:将步骤5中处理后的锭坯在45mn快锻机上进行1火次拔长锻造至八方方坯(
□
220mm),终锻温度不低于800℃,锻造完成后进行空冷。
26.步骤7:将步骤6中处理后的坯料在800℃温度进行保温,该步骤中加热系数为0.7min/mm。随后在45mn快锻机上将坯料锻制成φ200mm圆棒,该火次总变形量不大于20%。锻造完成后进行空冷。
27.步骤4、步骤6的主要目的是实现组织的初步细化与均匀化。在步骤4中通过在t
β-40℃进行拔长锻造,锻造总变形量达到90%,使得开坯锻造后的不均匀组织充分破碎,同时积累了大量的变形储能。随后将坯料加热至t
β
+80℃使坯料充分发生再结晶,实现组织的细化与均匀化。
28.为了达到自由锻造过程中均匀变形的目的,在步骤4中采用了对角拔长的锻造方式,同时控制每一道次的压下量与送进量的匹配,控制压下速率为8~15mm/s,实现温度场和应变场的均匀,为步骤6中的再结晶均匀化过程奠定了基础。
29.步骤8:将步骤7中处理后的坯料在连续式加热步进炉中进行800℃保温,该步骤中加热系数为0.75min/mm。
30.步骤9:将步骤8中加热完成后的坯料在skk17精锻机上经过1火次径向拔长锻造至φ130 mm棒材,锻打频率为600次/min,拉打速率为3~3.5m/min,终锻温度不低于700℃。
31.步骤10:将步骤9中锻造完成后的坯料回炉加热至855℃并保温一段时间,回炉加热的加热系数为0.4min/mm。
32.步骤11:将步骤10中加热后的坯料在skk17精锻机上经过1火次径向拔长锻造至φ80 mm棒材,终锻温度不低于800℃,锻造完成后需立刻以不低于150℃/s的速度进行冷却。
33.在步骤11中,径向锻造的第1道次的锻造尺寸为φ100 mm,第2道次的锻造尺寸为φ86 mm,第3道次的锻造尺寸为φ80 mm,控制精锻频率为600次/min。冷却方式可采用介质冷却。
34.步骤12:将步骤11中完成后的棒坯,在经过825℃/120min的第一重退火后,以5℃/min的冷却速率冷却至720℃,随后以50℃/min降温至480℃并加热8h,加热结束后进行空冷。
35.步骤10、步骤11和步骤12是性能调控的关键步骤。在步骤10中,坯料在两相区经过高频率锻造,使得材料内部累计了大量的变形储能,进一步细化组织。步骤11中,在tβ+15℃
进行加热锻造获得网篮组织,提高韧性的关键,坯料经过加热、锻造后再结晶能够充分进行,得到细小且均匀的β再结晶晶粒。同时在该步骤中,单相区的变形量大于60%能够充分破碎β晶粒,使得晶界扭曲提高材料的塑性。锻造完成后快速冷却能够抑制α相的析出。步骤12中,通过控制第一重退火温度和第二重退火温度来调控强度与塑性。热处理时控制第一重退火后的分段冷却速率,解决了材料因温度场不均匀带来性能差异大的问题,同时保证棒材强度与韧性。
36.图1是经过实施例一工艺锻造制备的φ80mm规格棒材的r态低倍组织照片,可以看出r态低倍组织无明显的冶金缺陷,低倍组织均匀;图2为棒材不同位置的高倍组织照片,可以看出,高倍组织十分均匀,组织为典型的网篮组织,原始β晶界扭曲破碎,网篮编织良好,组织一致性好。表1为对应棒材不同位置的力学性能,棒材综合性能优异,不同位置性能差异小。
37.对比例(现有技术下ti55531合金φ80mm规格棒材锻造方法)选用ti55531钛合金φ780mm规格铸锭,铸锭β转变温度为840℃。
38.步骤1:将ti55531铸锭加热至1150℃进行保温,该步骤中加热系数为0.7~0.75min/mm。
39.步骤2:将步骤1中处理后的锭坯进行开坯锻造,设备采用45mn快锻机。锻造方法为将φ780mm铸锭进行1火次锻造至四方
□
600 mm,锻造方式为2镦2拔,锻后采用空冷;该步骤中累计的总变形量不小于80%,终锻温度不低于850℃。
40.步骤3:将步骤2中所得坯料在1080℃加热保温,该步骤中加热系数为0.7~0.75min/mm。
41.步骤4:将步骤3中处理后的坯料进行单相区锻造,设备采用45mn快锻机。锻造方法为将四方
□
600 mm方坯进行1火次2镦2拔锻造至四方
□
600 mm,锻后采用空冷;该步骤中累计的总变形量不小于80%,终锻温度不低于800℃。
42.步骤5:将步骤4中所得坯料在1000℃加热保温,该步骤中加热系数为0.7~0.75min/mm。
43.步骤6:将步骤5中处理后的坯料进行单相区锻造,设备采用45mn快锻机。锻造方法为将四方
□
600 mm方坯进行1火次2镦2拔锻造至八方
□
660 mm,锻后采用空冷;该步骤中累计的总变形量不小于80%,终锻温度不低于800℃。
44.步骤7:将步骤6中所得坯料在800℃加热保温,该步骤中加热系数为0.7~0.8min/mm。
45.步骤8:将步骤7中处理后的坯料在两相区锻造,设备采用45mn快锻机。锻造方法为将八方
□
660 mm方坯进行1火次1镦1拔锻造至八方
□
660 mm,锻后采用空冷;该步骤中累计的总变形量不小于50%,终锻温度不低于650℃。
46.步骤9:将步骤8中所得坯料在900℃加热保温,该步骤中加热系数为0.6~0.7min/mm。
47.步骤10:将步骤9中处理后的坯料在两相区锻造,设备采用45mn快锻机。锻造方法为将八方
□
600 mm方坯进行1火次1镦1拔锻造至四方
□
600 mm,锻后采用空冷;该步骤中累计的总变形量不小于50%,终锻温度不低于700℃。
48.步骤11:将步骤10中所得坯料在800℃加热保温,该步骤中加热系数为0.7~
0.8min/mm。
49.步骤12:将步骤11中处理后的坯料在两相区锻造,设备采用45mn快锻机。锻造方法为将四方
□
600 mm方坯进行1火次2镦2拔锻造至四方
□
600 mm,锻后采用空冷;该步骤中执行完第一个1镦1拔后原温回炉加热120min,待加热完成后出炉执行第二个1镦1拔。该火次累计的镦粗变形量控制在30%,终锻温度不低于650℃。
50.步骤13:将步骤12中所得坯料在800℃加热保温,该步骤中加热系数为0.7~0.8min/mm。
51.步骤14:将步骤13中处理的锭坯分3火次进行拔长锻造,锻造至四方
□
250mm的方坯,每火次锻后均采用空冷。该步骤中每火次拔长变形量控制在30~40%之间,终锻温度不低于650℃步骤15:将步骤14中处理后的坯料在800℃温度进行保温,该步骤中加热系数为0.7~0.8min/mm。随后在45mn快锻机上将坯料锻制成φ200mm圆棒,该火次总变形量不大于20%。锻造完成后进行空冷。
52.步骤16:将步骤15中处理后的坯料在连续式加热步进炉中进行800℃保温,该步骤中加热系数为0.75min/mm。
53.步骤17:将步骤16中加热完成后的坯料在skk17精锻机上经过3火次径向拔长锻造至φ80 mm棒材,锻打频率不高于100次/min,每火次锻造完成后空冷,终锻温度不低于650℃。
54.在步骤17中,径向锻造的锻打频率不能大于100次/min,因为在两相区快速锻打会造成表面温升严重引起组织过热。此外,ti55531合金在两相区变形抗力大,径向锻造需分3火次完成锻造。
55.图3是经过对比例工艺锻造制备的φ80mm规格棒材的r态低倍组织照片,可以看出r态低倍组织有明显的冶金缺陷;图4为棒材不同位置的正常高倍组织照片,可以看出,高倍组织较为均匀,组织为典型的双态组织,原始β晶界破碎,初生α相为等轴状。图5为经过对比例工艺锻造制备的φ80mm规格棒材过热的高倍组织,可以看出,径向锻造速率达到150次/min坯料容易出现过热组织,α相为片层状,组织均匀性较差。表1为对应棒材不同位置的力学性能,相较于本发明的实施例工艺生产的棒材,强度与kic较低,塑性水平相当。
56.表1
ꢀꢀ
ti55531钛合金φ80mm棒材力学性能