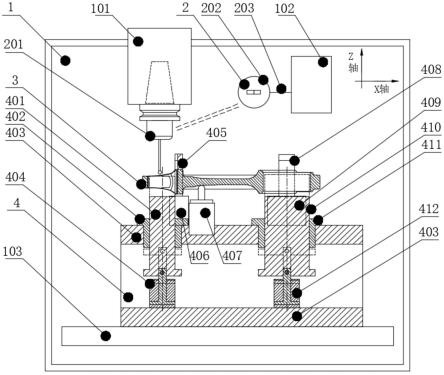
1.本发明属于发动机再制造技术领域,涉及一种发动机连杆返工返修及再制造装置。
背景技术:2.发动机连杆是发动机的重要零部件之一,也是容易损坏的关键零部件之一,市场上报废量和需求量远大于发动机。但发动机连杆精度要求高,从发动机上更换下的连杆普遍存在大头孔、小头孔、中心距和平行度等相关重要尺寸参数的超差现象,同时还存在杆身的弯曲变形和扭曲变形,且工艺基准破坏,修复难度大,发动机连杆的再制造成为实现发动机再制造需要突破的技术难题。
3.连杆小头衬套作为发动机连杆的重要组成部件之一,其主要作用是减震、隔噪,减少疲劳,增加使用寿命,对车辆的操作稳定性起着至关重要的作用。但同时连杆小头衬套也是连杆中极易磨损、寿命最低的部件,一旦衬套损坏,连杆整体损坏无法正常工作,但实质上除连杆小头衬套外,连杆的其他部分仍旧完好,如果将连杆整体报废,成本损失较大,而通过连杆返工返修或者再制造技术,可将连杆形状及精度恢复,使再制造产品质量达到或超过新品,极大减少材料浪费,降低成本。
4.但现有技术中连杆小头衬套取出多采用衬套压装机等压力装备压出衬套,该状态下衬套和连杆小头孔温度相同,衬套与连杆小头孔配合为过盈配合,存在连杆小头衬套的端面轮廓锐边和油孔轮廓容易造成连杆小头孔划伤导致将新的连杆小头衬套压装到连杆小头孔后连杆小头衬套贴合度无法满足大于85%要求造成连杆报废的风险;并且在压出过程中因过盈力不均匀导致连杆小头孔变形、表面纹理被挤压光滑,在压装新的连杆小头衬套后导致连杆小头衬套与连杆小头孔间在连杆工作状态下连杆小头衬套转动风险;
5.此外安装完成小头衬套后的连杆还需进行二次加工,通过切削连杆小头衬套和连杆的大头孔,确保连杆大头孔中心与连杆衬套孔中心的距离精度
±
0.02的要求,但由于连杆使用过程中大头孔也会造成磨损,对于返工返修或者再制造技术生产的连杆,大头孔切削余量不足,无法对大头孔切削加工,并且大头孔径与连杆螺纹孔壁厚一般要求间距大于或等于0.8mm,若连杆大头孔切削过多,会造成大头孔壁强度及刚度降低,反而会造成连杆装配到发动机后因上述壁厚影响导致圆柱度超差和发动机高转速运转过程中上述壁厚微振,引发发动机故障,因此对于大头孔磨损严重的连杆无法实时返工返修或者再制造技术。
技术实现要素:6.针对上述现有技术中存在的问题,本发明公布了一种发动机连杆返工返修及再制造装置,该装置可实现连杆返工返修及再制造过程中无伤移除连杆衬套,确保连杆小头孔内壁无损伤,进而保证连杆小头孔表面质量及形位公差以及新小头衬套与连杆的贴合度。
7.本发明公开一种发动机连杆返工返修及再制造装置,其包括单主轴加工中心、在线测量系统、连杆以及连杆夹具组件四部分,其中所述在线测量系统用于测量连杆小头衬
套及大头孔进行坐标测量,同时向单主轴加工中心反馈测量信号;所述单主轴加工中心用于对连杆进行切削加工;所述单主轴加工中心包括有用于连接刀具的加工主轴、数控中心以及工作台,所述数控中心接收在线测量系统的测试信号并输出加工主轴的控制信号,所述连杆夹具组件设于工作台上,且所述连杆夹具组件将连杆固定。
8.进一步的,所述在线测量系统则包括有无线传感器、信号接收器以及具有屏蔽功能的信号线,所述信号接收器通过信号线电连接数控中心,所述无线传感器则安设于加工主轴上,所述无线传感器测量连杆坐标数据,并将连杆坐标数据无线传输至信号接收器,所述信号接收器将接收的连杆坐标数据经由信号线传输至数控中心。
9.进一步的,所述连杆夹具组件具体包括有夹具主体、小头定位夹具组件以及大头定位夹具组件三部分,所述夹具主体上设有小头销孔和大头销孔,所述小头定位夹具组件安设于小头销孔内,所述大头定位夹具组件则安设于大头销孔中,通过小头定位夹具组件和大头定位夹具组件共同将连杆夹紧固定。
10.进一步的,所述小头定位夹具组件中包括小头衬套孔定位销轴、小头衬套抽销气缸以及小头端面压臂,所述小头衬套孔定位销轴连接于小头销孔,所述小头衬套孔定位销轴底部连接所述小头衬套抽销气缸,所述小头衬套抽销气缸安设于夹具主体内部,通过小头衬套抽销气缸驱动小头衬套孔定位销轴沿轴向移动;所述小头端面压臂安设于夹具主体上表面,且所述小头端面压臂靠近连杆小头端面一侧,通过所述小头端面压臂下压将连杆小头端面压紧。
11.进一步的,所述小头销孔上设有小头导向轴套,所述小头导向轴套与小头衬套孔定位销轴配合连接。
12.进一步的,所述连杆小头衬套孔定位销轴直径小于连杆小头衬套孔直径0.4~0.6mm。
13.进一步的,所述大头定位夹具组件中包括大头孔定位销轴、大头孔抽销气缸以及大头端面压臂,所述大头孔定位销轴连接于大头销孔,所述大头孔定位销轴底部连接所述大头孔抽销气缸,所述大头孔抽销气缸安设于夹具主体内部,通过大头孔抽销气缸驱动大头孔定位销轴沿轴向移动;所述大头端面压臂安设于夹具主体上表面,且所述大头端面压臂靠近连杆大头端面一侧,通过所述大头端面压臂下压将连杆大头端面压紧。
14.进一步的,所述大头销孔上设有大头导向轴套,所述大头导向轴套与大头孔定位销轴配合连接。
15.进一步的,所述连杆大头孔定位销轴的直径小于连杆大头孔直径0.4~0.6mm。
16.进一步的,所述连杆中部位置的连杆体下方在偏向小头衬套孔一侧设有连杆体支撑油缸,所述连杆体支撑油缸伸出支撑连杆。
17.1)本发明的发动机连杆返工返修及再制造装置中在移除旧小头衬套时,通过切削小头衬套至薄壁结构,使连杆刚度及强度下降,轻轻推移便可顺利移除衬套,避免现有技术中通过强压力设备压出衬套,导致连杆小头孔内壁损伤,进而确保连杆小头孔表面质量及形位公差,确保新小头衬套与连杆的贴合度。
附图说明
18.图1为本实施例中发动机连杆返工返修及再制造装置的流程示意图;
19.图2为本实施例中发动机连杆返工返修及再制造装置的结构示意图;
20.图3为本实施例中连杆的俯视结构示意图;
21.图4为本实施例中连杆的侧面剖视结构示意图;
22.图5为本实施例2中移除连杆小头衬套阶段在线测量系统的测量示意图;
23.图6为本实施例2中连杆小头衬套装配阶段在线测量系统的测量示意图;
24.图7为本实施例2中连杆小头衬套二次加工阶段加工中心的位置示意图。
具体实施方式
25.为使本发明实施方式的目的、技术方案和优点更加清楚,下面将结合本发明实施方式中的附图,对本发明实施方式中的技术方案进行清楚、完整地描述,显然,所描述的实施方式是本发明一部分实施方式,而不是全部的实施方式。基于本发明中的实施方式,本领域普通技术人员在没有作出创造性劳动前提下所获得的所有其他实施方式,都属于本发明保护的范围。
26.因此,以下对在附图中提供的本发明的实施方式的详细描述并非旨在限制要求保护的本发明的范围,而是仅仅表示本发明的选定实施方式。基于本发明中的实施方式,本领域普通技术人员在没有作出创造性劳动前提下所获得的所有其他实施方式,都属于本发明保护的范围。
27.实施例1:
28.结合图2-4所示,本实施例1中具体公开了一种发动机连杆返工返修及再制造装置,其包括单主轴加工中心1、在线测量系统2、连杆3以及连杆夹具组件4四部分,其中所述在线测量系统2用于测量连杆小头衬套及大头孔进行坐标测量,同时向单主轴加工中心1反馈测量信号;单主轴加工中心1作为主要加工设备,用于对连杆3进行切削加工;所述单主轴加工中心 1包括有用于连接刀具的加工主轴101、数控中心102以及工作台103,所述数控中心102接收在线测量系统2的测试信号并输出加工主轴101的控制信号,所述连杆夹具组件4设于工作台103上,且所述连杆夹具组件4将连杆3固定。所述连杆3包括大头端、小头端及连杆体三部分组成,其中小头端设有小头孔301,所述小头孔301内安设有连杆小头衬套,所述大头端设有大头孔302,所述连杆大头端多采用分体结构,所述连杆大头端采用两个半圆形构件组成,通过连接螺栓304将两个半圆形构件拼合固定。
29.所述在线测量系统2则包括有无线传感器201、信号接收器202以及信号线203,所述信号接收器202通过具有屏蔽功能的信号线203电连接数控中心102,所述无线传感器201则安设于加工主轴101上,所述无线传感器201测量连杆3坐标数据,并将连杆3坐标数据无线传输至信号接收器202,所述信号接收器202将接收的连杆3坐标数据经由信号线203传输至数控中心102。
30.所述连杆夹具组件4具体包括有夹具主体403、小头定位夹具组件以及大头定位夹具组件三部分。所述夹具主体403上设有小头销孔和大头销孔,所述小头定位夹具组件安设于小头销孔内,所述大头定位夹具组件则安设于大头销孔中,通过小头定位夹具组件和大头定位夹具组件共同将连杆3夹紧固定。
31.所述小头定位夹具组件中包括小头衬套孔定位销轴401、小头衬套抽销气缸404以及小头端面压臂405,其中所述小头销孔上设有小头导向轴套402,所述小头衬套孔定位销
轴401通过小头导向轴套402连接于小头销孔,所述小头衬套孔定位销轴401底部连接所述小头衬套抽销气缸404,所述小头衬套抽销气缸404安设于夹具主体403内部,通过小头衬套抽销气缸404 驱动小头衬套孔定位销轴401沿轴向移动;所述小头端面压臂405安设于夹具主体403上表面,且所述小头端面压臂405靠近连杆3小头端面一侧,通过所述小头端面压臂405下压将连杆3 小头端面压紧,其中所述小头端面压臂405连接有第一液压缸406,通过第一液压缸406驱动小头端面压臂405竖向活动。本实施例中连杆小头衬套孔定位销轴401比连杆小头衬套孔直径小0.4~0.6mm。
32.同理,所述大头定位夹具组件中包括大头孔定位销轴409、大头孔抽销气缸412以及大头端面压臂408,其中所述大头销孔上设有大头导向轴套411,所述大头孔定位销轴409通过大头导向轴套411连接于大头销孔,所述大头孔定位销轴409底部连接所述大头孔抽销气缸412,所述大头孔抽销气缸412安设于夹具主体403内部,通过大头孔抽销气缸412驱动大头孔定位销轴409沿轴向移动;所述大头端面压臂408安设于夹具主体403上表面,且所述大头端面压臂408靠近连杆3大头端面一侧,通过所述大头端面压臂408下压将连杆3大头端面压紧,所述大头端面压臂408连接有第二液压缸410,通过第二液压缸410驱动大头端面压臂408竖向活动。本实施例中连杆3大头孔定位销轴409比连杆3大头孔直径小0.4~0.6mm。
33.所述连杆3的小头衬套孔301和大头孔303配合分别配合小头衬套孔定位销轴401和大头孔定位销轴409,将连杆3进行定位。同时所述连杆3中部位置的连杆体302下方偏向小头衬套孔一侧设有连杆体支撑油缸407,所述连杆体支撑油缸407伸出将连杆3顶起,通过小头端面压臂405和大头端面压臂408共同配合将连杆3夹紧,当连杆3夹紧后小头衬套孔定位销轴 401和大头孔定位销轴409抽出,由单主轴加工中心1分别对连杆3两端进行切削加工。
34.实施例2:
35.结合图1所示,本实施例2中具体公开了一种发动机连杆返工返修及再制造装置,其包括如下步骤:
36.s1.连杆一次清洗:拆卸连杆螺栓,将连杆盖与连杆体分离后,利用超声波清洗设备对连杆的各部分进行清洗,清洗完成后组合装配;
37.在s1过程中具体包括:
38.(1)拆卸连杆螺栓:首先拆卸连杆螺栓,将连杆整体分开为连杆盖与连杆体两部分,同时针对报废使用次数大于或等于2次的连杆螺栓进行替换为新的连杆螺栓,或替换为使用次数为1次的连杆螺栓;该步骤可最大化重复利用连杆螺栓,同时确保修复的连杆质量无降低。
39.(2)清洗连杆表面:使用超声波清洗装备分别清洗上述连杆盖、连杆体和连杆螺栓,清除上述零件表面锈迹、油斑、粘符颗粒等异物;
40.(3)装配连杆螺栓:当连杆清洁完毕,使用连杆装配设备重新装配上述连杆盖、连杆体和连杆螺栓,组成连杆整体。
41.s2.移除连杆小头衬套:将连杆装夹固定,加工中心并经测量计算连杆小头衬套的孔中心坐标后,对连杆小头衬套进行切削,以移除连杆小头衬套;
42.其中,在装夹连杆阶段,首先需使用高压空气清理加工大头孔和小头衬套孔时的刀具及夹具,本实施例中连杆采用小头衬套孔定位销轴和大头孔定位销轴进行定位,通过
将小头衬套孔定位销轴和大头孔定位销轴分别伸出,将连杆的小头衬套孔和大头孔分别配合小头衬套孔定位销轴和大头孔定位销轴实现初步定位,然后通过气缸和端面压臂压紧连杆两端后,并通过液压缸支撑连杆体,实现连杆夹紧,之后下降大头孔定位销轴和小头衬套孔定位销轴,留出刀具的切削加工空间。
43.连杆固定完成后,首先利用刀具测量仪或低压力千分表调校无线传感器测针末端测珠径向跳动小于0.001,
44.本实施例中将无线传感器设置于连杆小头衬套孔上方约为连杆厚度一半高度的位置测量连杆小头衬套孔内表面多个点坐标,其中坐标取值精度不低于0.0001mm,在实施例中点坐标数量为4个,
45.具体的,如图5所示,4个点坐标分别为p
11
(x
11
,y
11
)、p
12
(x
12
,y
12
)、p
13
(x
13
,y
13
)、p
14
(x
14
,y
14
),测量过程中4个点坐标沿小头衬套孔周向均布,其中小头衬套孔的中心点坐标为o
10
(x
10
,y
10
),其中p
11
与p
12
关于o
10
接近中心对称且接近关于过小头孔中心的y轴的对称轴轴对称,对称度均小于5mm;p
13
与p
14
关于o
10
接近中心对称且接近关于过小头孔中心的x轴的对称轴轴对称称,对称度均小于5mm,通过单主轴加工中心的数控系统使用变量运算方法计算出连杆小头衬套孔的中心点坐标o
10
(x
10
,y
10
)。
46.然后采用硬质合金或立方氮化硼或金属陶瓷等材质的可转位刀片安装到单主轴加工中心的刀具夹具中,本实施例中刀具主偏角为90
°
,其目的是减少镗削加工径向力,以减少加工过程中加工径向力造成衬套提前脱落,通过将单主轴加工中心的刀具直径借助对刀仪调节至小于连杆小头孔内径0.2~0.3mm的位置,并将刀具安装到单主轴加工中心的加工主轴上,并进行镗削连杆小头衬套直至轴向贯穿连杆小头衬套,本实施例中镗削加工的线速度控制在 200-350m/min,进给量为0.1~0.25mm/r。
47.通过刀具切削加工,使得连杆小头衬套壁厚仅剩余0.10~0.15mm,呈薄壁结构,该状态下连杆小头衬套的刚性和弹性消失,连杆小头孔和连杆小头衬套之间贴合压力降低甚至消失,使用尼龙棒等软材质辅具轻轻推移便可顺利移除连杆衬套,当连杆衬套被移除后,连杆小头孔的原始表面质量、形位公差保留完好,上述切削加工的目的是确保连杆小头孔内壁表面划痕、表面纹理不被破坏,为后续重新压装新的连杆衬套,提高贴合度提供保障。
48.在压装新的连杆衬套前,首先使用去毛刺刮刀去除连杆小头孔上下端面的锐边和毛刺,防止后续压装新的连杆衬套时划伤连杆小头孔和连杆小头衬套背部。
49.s3.连杆二次清洗:对移除小头衬套的连杆进行再次清洗;
50.在压装新的连杆衬套前,还需对连杆的小头孔进行二次清洗,本实施例中具体为将连杆水平放置在连杆清洗设备中,确保连杆大小头孔的端面水平放置,然后使用环保水剂清洗剂与过滤软质水按一定体积比例勾兑成环保水剂清洗液,将环保水剂清洗液加热到约50℃,启动清洗设备,清洗篮和高压喷淋喷头共同进行回旋与往复复合运动,对连杆小头衬套孔喷淋清洗,使得连杆小头衬套孔等连杆各部位彻底清洗干净,清洗质量达到杂质重量3mg/件,最大金属颗粒长度0.6mm,保证工件表面无明显油迹。进一步的,清洗装备中配备有油水分离器、磁选分离器、离心式颗粒分离器、滤芯及滤袋过滤器和沉淀箱等,可保证环保水剂清洗液的纯净度。在连杆清洗完成后,通过热风及连杆清洗后余温对连杆进行烘干时,环保水剂清洗机的防锈成分会在连杆表面形成保护膜以隔离空气,有效防止连杆生锈。
51.s4.连杆小头衬套装配:加热连杆小头孔至一定温度后,将新的小头衬套压入连杆
小头孔内;
52.具体操作为:首先使用无尘布擦拭连杆小头孔,将连杆小头孔放置于在电磁加热装备上,启动电磁加热将连杆小头孔加热至至130℃
±
10℃,使连杆小头孔受热膨胀至直径增大。
53.加热完成后,将连杆立即转移至连杆衬套液压或伺服压装装备的安装工位上,按预定位置放置连杆小头衬套,并启动连杆衬套压装装备将连杆小头衬套压入连杆小头孔内,压装过程中实时监控连杆小头孔位置的温度和衬套压力。
54.当压装完成后,将压装好的连杆放置到洁净的连杆周转箱中自然冷却至常温后,再用塞尺检验连杆小头孔与连杆小头衬套背部的间隙,并按预设频率抽检连杆衬套的贴合度,该贴合度的检验方法包含且不限于超声波检验和表格涂色面积法检验等。
55.s5.连杆小头衬套二次加工:将装配完成的连杆装夹固定,加工中心分别测量计算连杆大头孔中心位置和小头衬套孔中心位置,根据连杆大头孔中心位置和小头衬套孔中心位置计算加工中心的加工位置,并对连杆大头孔和小头衬套孔进行切削。该步骤目的是要确保连杆小头衬套孔的中心与大头孔的中心间距满足l0
±
0.02的要求,从而确保连杆使用过程中运转流畅,保证发动机压缩比稳定,降低发动机故障风险。
56.具体的,该步骤的操作方法为:
57.首先将装夹在单主轴加工中心内,并使用高压空气清理将要加工连杆大头孔和小头衬套孔的连杆夹具组件,该夹具中具有连杆大头孔定位销轴和连杆小头孔定位销轴,大头孔定位销轴比连杆大头孔直径小0.4~0.6mm、连杆小头孔定位销轴比连杆小头衬套孔直径小0.05~ 0.15mm。然后将大头孔定位销轴和小头衬套孔定位销轴上升至上限位,将连杆通过大头孔定位销轴和小头衬套孔定位销轴定位放置在夹具上,将连杆的小头衬套孔和大头孔分别配合小头衬套孔定位销轴和大头孔定位销轴实现初步定位,然后通过气缸和端面压臂压紧连杆两端后,并通过液压缸支撑连杆体,实现连杆夹紧,之后下降大头孔定位销轴和小头衬套孔定位销轴,留出刀具的切削加工空间。
58.连杆固定完成后,首先利用刀具测量仪或低压力千分表调校无线传感器测针末端测珠径向跳动小于0.001,
59.本实施例中将无线传感器设置于连杆小头衬套孔上方约为连杆厚度一半高度的位置测量连杆小头衬套孔内表面多个点坐标,其中坐标取值精度不低于0.0001mm,在实施例中连杆小头衬套孔的点坐标数量为4个;并在连杆大头孔内表面取值4个点坐标,连杆大头孔的点坐标取值精度不低于0.0001mm。
60.如图6所示,其中连杆小头衬套孔的4个测量点坐标分别为p
21
(x
21
,y
21
)、p
22
(x
22
,y
22
)、 p
23
(x
23
,y
23
)、p
24
(x
24
,y
24
)且接近在连杆小头衬套孔内均布,小头中心点为o
20
(x
20
,y
20
)。更详细的是,p
21
与p
22
关于o
20
接近中心对称且接近关于过小头孔中心的y轴的对称轴轴对称,对称度均小于5mm;p
23
与p
24
关于o
20
接近中心对称且接近关于过小头孔中心的x轴的对称轴轴对称称,对称度均小于5mm。然后通过单主轴加工中心的数控系统使用变量运算计算出连杆小头衬套孔中心o
20
坐标(x
20
,y
20
),x
20
=(x
21
+x
22
)/2,y
20
=(y
23
+y
24
)/2。
61.而连杆大头孔的4个测量点坐标分别为p
31
(x
31
,y
31
)、p
32
(x
32
,y
32
)、p
33
(x
33
,y
33
)、p
34
(x
34
,y
34
) 且接近在连杆小头衬套孔内均布,大头中心点为o
30
(x
30
,y
30
)。p
31
与p
32
关于o
30
接近中心对称且接近关于过小头孔中心的y轴的对称轴轴对称,对称度均小于5mm;p
33
与p
34
关
于o
30
接近中心对称且接近关于过小头孔中心的x轴的对称轴轴对称称,对称度均小于5mm。通过单轴加工中心数控系统使用变量运算计算出连杆小头衬套孔中心o
30
坐标(x
30
,y
30
),利用下述公式x
30
=(x
31
+x
32
)/2,y
30
=(y
33
+y
34
)/2即可计算获得连杆大头孔中心o
30
。
62.在计算获得连杆的大头孔中心坐标以及小头衬套孔的中心坐标后,由于连杆小头衬套孔中心与连杆大头中心的距离公差一般为
±
0.05mm,而实际使用时设定的距离公差一般为
±ꢀ
0.02mm,且连杆小头衬套压装后,连杆小头衬套因连杆小头衬套背部过盈力作用以及连杆小头衬套周向厚度存在一定不均匀现象,连杆小头衬套中心o
20
与连杆大头中心o
30
的距离l1一般不满足连杆小头衬套中心与连杆大头中心距离为l
±
0.02要求,如图7所示,因此需要对连杆的两个孔壁进行二次切削加工,进而需计算出加工中心的加工位置坐标o0(x0,y0)。
63.其计算公式可按照下述公式进行:
64.首先计算出连杆小头衬套中心o
20
与连杆大头中心o
30
的距离l1:
65.l1=sqrt(abs((x
30-x
20
)2+(y
30-y
20
)2)),
66.式中abs为绝对值函数,sqrt为正平方根函数;
67.然后根据三角形相似或三角函数可得加工中心的加工位置坐标o0(x0,y0):
68.x0=x
30
+a*l0;y0=y
30
+b*l0;
69.其中
70.接下来则采用加工中心进行切削,本实施例中首先将可转位金刚石刀片安装到刀具夹具上,上述刀片的主切削刃与副切削刃过渡处采用大圆角修光刃,第一前角采用正前角设计以减少切削力,第二前角采用负前角有利于切削加工过程中防止不断屑造成划伤已加工表面。将刀具使用对刀仪调整刀具直径至加工尺寸后,将刀具安装到加工中心的加工主轴上,启动加工中心加工程序以o0为中心加工连杆小头衬套。当加工完成后,加工中心自动换刀,使用铝基颗粒尼龙毛刷刷除连杆小头衬套孔进行切削加工所产生的锐边和毛刺。
71.而当需加工连杆大头孔时,只需在加工连杆小头衬套完成后,加工中心自动换刀,使用尺寸调整至连杆大头孔尺寸的装夹硬质合金或立方氮化硼或金属陶瓷材质可转位刀片的刀具以连杆大头中心o
30
坐标切削加工连杆大头孔。当切削完成后,加工中心自动换刀,使用铝基颗粒尼龙毛刷刷除连杆大头孔进行切削加工产生的锐边和毛刺。
72.s6最后针对加工完成的连杆可进行后续的清洗、打标、检测、包装等后处理步骤,具体的,在本实施例中操作如下:
73.首先针对加工完成的连杆使用清洗设备清洗连杆表面,例如采用履带通过式的清洗机;
74.然后使用连杆综合检测称重打标复合装备全面检查连杆的关键重要尺寸,并对连杆进行称重、打刻二维码和连杆重量分组代码等标识符;
75.接下来通过视觉检测设备检验连杆大头端、连杆小头端、连杆毛坯面、连杆标识、二维码等各部位的外观表面质量;
76.针对检验合格的连杆产品,将再次拆卸分体为连杆体、连杆盖、连杆螺栓,并分别放置到连杆总成清洗篮中,使用超声波复合清洗装备分别清洗上述连杆盖、连杆体和连杆螺栓,清除上述零件表面锈迹、油斑、粘符颗粒等异物,清洗完成后重新组装,且预紧连杆螺
栓至 10n.m~15n.m;最终采用打包设备/人工进行包装。
77.以上所述仅为本发明的优选实施例而已,并不用于限制本发明,对于本领域的技术人员来说,本发明可以有各种更改和变化。凡在本发明的精神和原则之内,所作的任何修改、等同替换、改进等,均包含在本发明的保护范围之内。