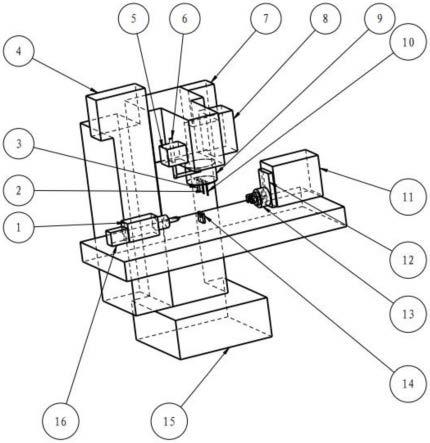
1.本实用新型涉及一种凸轮轴径向孔加工装置。
背景技术:2.凸轮轴是燃油发动机上非常重要的部件,专门负责驱动气门按时开启和封闭,保障发动机在工作中定时为气缸吸收新鲜可燃混合气,并及时排出燃烧后的废气;凸轮轴主体结构包括主轴,主轴上设有多个不同角度的凸轮,现在普遍采用在主轴径向方向上设置油孔,主轴的端面上设有与每个相对应连通的轴向孔。
3.目前加工凸轮轴径向油孔的工艺有手工钻孔工艺和加工中心钻孔工艺,手工钻孔工艺采用钻孔、孔口倒角和除毛刺工序,分别在多台式钻床上配合相应工装通过手工操作完成,手工在不同机床上逐个完成钻孔、倒角和除毛刺加工工序,耗时较长,生产效率低下,若要满足产能需求,往往需要投入较多人力,由于人工操作工序多,劳动强度比较大,加工过程中易出现遗漏现象,甚至影响产品质量稳定性。
4.若利用加工中心钻孔,必须使用加工中心机床,加工中心机床完成钻孔加工需要配套的专用工装,同时需要专业技术水平较高的作业人员操作,而且加工中心机床以及配套的工装价格昂贵,导致加工成本提高。
技术实现要素:5.本实用新型的目的旨在提供一种凸轮轴径向孔加工装置,克服现有技术的不足,实现一次装夹完成钻孔、孔口倒角及毛刺除去的工序,提高生产效率,降低设备采购成本,提高产品质量稳定性,降低工人的劳动强度。
6.为实现上述目的,本实用新型的凸轮轴径向孔加工装置,包括伺服电机、动力头、导向定位机构,所述动力头底部平行设置倒角钻头、定心钻头和去毛刺钻头,倒角钻头、定心钻头和去毛刺钻头由内向外依次排列,倒角钻头、定心钻头和去毛刺钻头上端置入动力头内并分别与齿轮固定连接,倒角钻头、定心钻头和去毛刺钻头上端齿轮相互啮合,中间的定心钻头上端齿轮与连接齿轮啮合,连接齿轮与电机转轴齿轮啮合,连接齿轮直径大于或等于定心钻头上端齿轮,导向定位机构由导向定位杆和导向定位块构成,导向定位块与动力头侧面固定连接,导向定位块上设置上下贯通孔,导向定位杆设置为“l”型,导向定位杆一端置入导向定位块上的贯通孔中,导向定位杆另一端与动力头无限接近。
7.倒角钻头、定心钻头和去毛刺钻头上端齿轮设为圆柱体形,长度大于连接齿轮,也大于各钻头下行距离的长度。
8.本实用新型的凸轮轴径向油孔加工装置与现有技术相比具有如下优异效果。
9.本实用新型的凸轮轴径向孔加工装置,采用一体式组装结构,通过固定板上的定位机构和顶尖座上的活动顶尖将凸轮轴准确而牢固的定位在待加工位置,定位机构设计时直接选用凸轮轴端面作为定位面,减少油孔长度累积误差,定位机构与凸轮轴无相对运动,避免了凸轮轴定位面划伤风险,在伺服电机二和伺服电机一的作用下,使凸轮轴周向各部
位的径向油孔定位加工准确无误,在伺服电机三和伺服电机二的作用下,使孔口倒角、油孔钻通、孔口去毛刺加工顺畅、简洁,倒角钻头、定心钻头和去毛刺钻头上端齿轮长度的设置,使各钻头分别下行加工变为可能,实现了在一台机床上完成凸轮轴径向油孔加工的三道工序,提高了生产效率,提高了产品质量稳定性,降低了工人的劳动强度,在保障凸轮轴径向油孔加工精度的质量下,规避了高端机床加工中心设备的购置,避免了高端机床加工中心设备高要求、高成本给企业带来的高成本投入。
附图说明
10.图1为本实用新型的凸轮轴径向孔加工装置示意图。
11.其中:1、为气动顶尖,2、为倒角钻头,3、为定心钻头,4、为控制系统,5、为导向定位座,6、为导向定位杆,7、为伺服电机三,8、为伺服电机二,9、为动力头,10、为去毛刺钻头,11、为伺服电机一,12、为固定板,13、为定位机构,14、为v型块,15、为万能工具铣床,16、为气缸。
具体实施方式
12.下面结合附图对本实用新型的凸轮轴径向油孔加工装置做进一步的详细说明。
13.图1所示的凸轮轴径向孔加工装置,包括伺服电机、动力头9、导向定位机构,所述动力头9底部平行设置倒角钻头2、定心钻头3和去毛刺钻头10,倒角钻头2、定心钻头3和去毛刺钻头10由内向外依次排列,倒角钻头2、定心钻头3和去毛刺钻头10上端置入动力头9内并分别与齿轮固定连接,倒角钻头2、定心钻头3和去毛刺钻头10上端齿轮相互啮合,中间的定心钻头3上端齿轮与连接齿轮啮合,连接齿轮与伺服电机二8转轴齿轮啮合,连接齿轮直径大于或等于定心钻头3上端齿轮,导向定位机构由导向定位杆6和导向定位座5构成,导向定位座5与动力头9侧面固定连接,导向定位座5上设置上下贯通孔,导向定位杆6设置为“l”型,导向定位杆6一端置入导向定位座5上的贯通孔中,导向定位杆6另一端与动力头9无限接近。
14.倒角钻头2、定心钻头3和去毛刺钻头10上端齿轮设为圆柱体形,长度大于连接齿轮,也大于各钻头下行距离的长度。
15.万能工具铣床15上有一个工作台,工作台上两侧分别设有尾部顶尖和头部顶尖,在工作台上的尾部顶尖和头部顶尖之间的设有v型块14,尾部顶尖和头部顶尖分别顶紧凸轮轴的两端,定位机构13将凸轮轴待加工径向孔位置准确定位,控制系统4按照设定程序,控制伺服电机工作,伺服电机还通过信号线与控制系统4连接,倒角钻头2、定心钻头3和去毛刺钻头10均通过信号线与控制系统4连接,将凸轮轴定位准确的装在工作台上,启动控制系统4,首先伺服电机三7工作,将动力头9沿凸轮轴径向孔加工位置移动,待倒角钻头2与凸轮轴径向孔加工位置对应,停止平行移动,动力头9立刻下移,使倒角钻头2对准凸轮轴径向孔加工位置,伺服电机8工作,驱动倒角钻头2下行对凸轮轴径向孔位置进行倒角加工,倒角加工结束后,动力头9上行,然后伺服电机三7工作,平行反方向移动,待定心钻头3与与凸轮轴径向孔加工位置对应,停止平行移动,动力头9立刻下移,使定心钻头3对准凸轮轴径向孔加工位置,伺服电机8工作,驱动定心钻头3下行对凸轮轴径向孔位置进行钻孔加工,钻孔加工结束后,动力头9上行,然后伺服电机三7工作,平行反方向移动,待去毛刺钻头10与凸轮
轴径向孔加工位置对应,停止平行移动,动力头9立刻下移,使去毛刺钻头10对准凸轮轴径向孔加工位置,伺服电机8工作,驱动去毛刺钻头10下行对凸轮轴径向孔加工所产生的毛刺进行削除,去毛刺加工结束后,伺服电机8停止工作,动力头9在伺服电机三7作用下复位,之后,伺服电机一工作,沿凸轮轴轴向移动凸轮轴,使下一个待加工径向孔的位置与倒角钻头2、定心钻头3和去毛刺钻头10在同一直线上,重复上述工序,依次加工径向孔。
技术特征:1.一种凸轮轴径向孔加工装置,包括伺服电机、动力头(9)、导向定位机构,其特征在于所述动力头(9)底部平行设置倒角钻头(2)、定心钻头(3)和去毛刺钻头(10),倒角钻头(2)、定心钻头(3)和去毛刺钻头(10)由内向外依次排列,倒角钻头(2)、定心钻头(3)和去毛刺钻头(10)上端置入动力头(9)内并分别与齿轮固定连接,倒角钻头(2)、定心钻头(3)和去毛刺钻头(10)上端齿轮相互啮合,中间的定心钻头(3)上端齿轮与连接齿轮啮合,连接齿轮与伺服电机二(8)转轴齿轮啮合,连接齿轮直径大于或等于定心钻头(3)上端齿轮,导向定位机构由导向定位杆(6)和导向定位座(5)构成,导向定位座(5)与动力头(9)侧面固定连接,导向定位座(5)上设置上下贯通孔,导向定位杆(6)一端置入导向定位座(5)上的贯通孔中,导向定位杆(6)另一端与动力头(9)无限接近。2.根据权利要求1所述的凸轮轴径向孔加工装置,其特征在于倒角钻头(2)、定心钻头(3)和去毛刺钻头(10)上端齿轮设为圆柱体形,长度大于连接齿轮,也大于各钻头下行距离的长度。3.根据权利要求1所述的凸轮轴径向孔加工装置,其特征在于导向定位杆(6)设置为“l”型。
技术总结本实用新型公开了一种凸轮轴径向孔加工装置,包括伺服电机、动力头(9)、导向定位机构,所述动力头(9)底部平行设置倒角钻头(2)、定心钻头(3)和去毛刺钻头(10),倒角钻头(2)、定心钻头(3)和去毛刺钻头(10)由内向外依次排列,采用本实用新型,实现了在一台机床上完成凸轮轴径向油孔加工的三道工序,提高了生产效率,提高了产品质量稳定性,降低了工人的劳动强度,在保障凸轮轴径向油孔加工精度的质量下,规避了高端机床加工中心设备的购置,避免了高端机床加工中心设备高要求、高成本给企业带来的高成本投入。的高成本投入。的高成本投入。
技术研发人员:王刚 朱振滔 杨启明 余天 纪金强
受保护的技术使用者:江西同欣机械制造股份有限公司
技术研发日:2022.09.02
技术公布日:2022/11/22