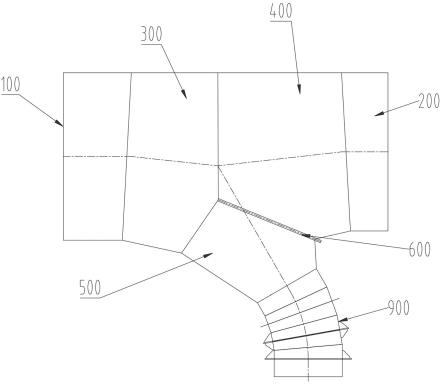
1.本发明涉及一种金属材料成型领域,具体涉及一种超大型钢岔管的制作方法。
背景技术:2.一座提水泵站一般设有 2 台以上水泵机组。对于多机组、长管道的泵站,常采用岔管并联管路,这不仅能节省管路投资,而且可在小流量下运行时使管内流速明显降低,减少管路损失,达到节约能源的目的。泵站出水管的内径一般为 500 ~ 1000mm 范围,岔管是水电站压力输水系统中用于分流以及合流的重要构件,岔管中包括多个锥管,其中与月牙板邻近的相贯锥管制造要求较高,要求其具有较高的连接强度以及较高的精度,现实生产中,在制作锥管时在锥筒上划角度等分线,这个等分线又称素母线,制作时,用压力机沿素母线进行间歇压制,形成的产品呈多边线,圆度不是很好,失圆严重,很难满足规范的要求,强度和精度较低,无法满足焊接和使用需求。
技术实现要素:3.本发明的目的是针对现有技术的不足,提供一种超大型钢岔管的制作方法,它能够在保证岔管较高的成型精度下,同时能够节省用料,降低生产成本。
4.本发明的目的是这样实现的:一种超大型钢岔管的制作方法,包括以下步骤:根据岔管的设计尺寸在平面内分别对主管、支管、支弯管、主管相贯锥管、支管相贯锥管、支弯管相贯锥管、月牙肋板展开放样,得到对应的放样图,以及各相贯锥管对应的小端补料放样图;在数控切割机上,根据各放样图下料得到对应的下料板以及与各相贯锥管对应的小端补料板;将各相贯锥管的下料板的小锥端边缘与对应的小端补料板的大锥端边缘连接固定形成对应的组合扇形板,小端补料板用于使组合扇形板小口端部形成正锥结构以及防止小锥端边缘磨损;在油压机上装载压头模具,所述压头模具包括成型凹模和成型凸模,对主管、支管、主管的下料板以及组合扇形板的侧边部进行压头和起弧;在三辊卷板机上把预弯好的下料板进行卷制,得到筒形瓦片;卷制组合扇形板时,三辊卷板机上辊倾斜,将组合扇形板小口端边缘抵靠上辊旁的挡轮上,三辊卷板机上辊的压线与锥管圆锥等分的素母线重合,持续卷制,得到锥形瓦片;分割,将锥形瓦片上对应的补料部分进行分割;将多个筒形瓦片、割去补料的锥形瓦片焊接后并与月牙肋板组装并焊接形成完整的岔管。
5.支弯管相贯锥管、支管相贯锥管放样时,对应的放样图分纵边时候,纵边下端与其放样的相贯线相交,纵边并与最短轴线在圆周方向错开布置。
6.支管相贯锥管的放样图包括第一、第二扇形板放样图;对应于第二扇形板放样有
第二补料板放样图;下料得到的第一扇形下料板、第二扇形下料板以及第二补料板,第二补料板的两端边缘具有用于包覆所述第二扇形下料板边缘的第一左侧补料片、第二右侧补料片;将第一扇形下料板的小锥端边缘与对应的小端补料板的大锥端边缘连接固定形成第一组合扇形板,将第二扇形下料板小锥端上边缘与第二补料板的大锥端边缘连接固定,第一左侧补料片、第二右侧补料片分别与第二扇形下料板边缘连接固定,形成第二组合扇形板;对组合形成的组合扇形板圆周方向上的边部进行压头和起弧;在三辊卷板机上进行组合扇形板卷制,得到组合锥形瓦片;进行组圆检验,再将两组合锥形瓦片焊接成完整支管相贯锥管。
7.第二扇形下料板、第一扇形下料板均分别由两下料板拼接连接固定,拼接缝为纵缝,两条纵缝在圆周方向错开布置。
8.支弯管相贯锥管的放样图包括第三、第四扇形板放样图;对应于第四扇形板放样图放样有第三补料板放样图;下料得到的第三扇形下料板、第四扇形下料板以及第三补料板,所述第三补料板的两端边缘具有用于包覆所述第四扇形下料板边缘第三左侧补料片、第四右侧补料片;将第三扇形下料板的小锥端边缘与对应的小端补料板的大锥端边缘连接固定形成第三组合扇形板,将第四扇形下料板小锥端上边缘与第三补料板放样图的大锥端边缘连接固定,第三左侧补料片、第四右侧补料片分别与第四扇形下料板边缘连接固定,形成第二组合扇形板;对组合形成的组合扇形板圆周方向上的边部进行压头和起弧;在三辊卷板机上进行组合扇形板卷制,得到组合锥形瓦片;将每个组合锥形瓦片上对应的补料部分进行分割;进行组圆检验,再焊接成支弯管相贯锥管。
9.所述第二补料板两端边缘分别与第一左侧补料片、第二右侧补料片一体成型。
10.筒形瓦片、锥形瓦片周边及拼接边开k形坡口,坡口角25
°
。
11.根据各放样图下料得到对应的下料板以及与各相贯锥管对应的小端补料板的材质为07mnmovr。
12.采用本发明,它能够在保证岔管较高的成型精度下,同时能够节省用料,降低生产成本。
13.下面结合附图和具体实施例对本发明作进一步说明。
附图说明
14.图1为岔管的结构示意图;图2为支管相贯锥管展开放样图;图3为支管相贯锥管的排料图;图4为第一组合扇形板的结构示意图;图5为第二组合扇形板的结构示意图;图6为支弯管相贯锥管展开放样图;
图7为主管相贯锥管展开放样图;图8挡轮与上辊的相对位置示意图。
15.附图中,40为第一组合扇形板,41为第二组合扇形板, 100为主管,200为支管,300为主管相贯锥管,400为支管相贯锥管,410为第一扇形下料板,420为第二扇形下料板,430为第二补料板,440为第一左侧补料片,450为第二右侧补料片, 500为支弯管相贯锥管, 600为月牙肋板, 800为上辊,900为支弯管,810为挡轮,a为相贯线。
具体实施方式
16.参照附图,将详细描述本发明的具体实施方案。
17.参见图1-8, 一种超大型钢岔管的制作方法的一种实施例,包括以下步骤,根据岔管的设计尺寸在平面内分别对主管100、支管200、主管相贯锥管300、支管相贯锥管400、支弯管相贯锥管500、月牙肋板600展开放样,岔管的结构参照图1,得到对应的放样图,以及各相贯锥管对应的小端补料放样图,由放样图进一步进行排料;展开工具,可通过solidworks、catia等三维软件进行展开,也可射线展形作图法得到。得到对应的放样图,以及各相贯锥管对应的小端补料放样图。
18.在数控切割机上,数控切割机可为数控火焰切割机,根据各放样图下料得到对应的下料板以及与各相贯锥管对应的小端补料板;下料板以及与各相贯锥管对应的小端补料板的材质为07mnmovr,07mnmovr为低焊接裂纹敏感性钢,强度较高,且韧性、焊接性及低温韧性也较好,对应主管100、支管200、支弯管900下料后呈带状,而各相贯锥管以及小端补料板呈锥形展开的扇形结构。
19.将各相贯锥管的下料板的小锥端边缘与对应的小端补料板的大锥端边缘连接固定形成对应的组合扇形板,连接固定可通过焊接实现,补料板用于使组合扇形板小口端部形成正锥结构以及防止小锥端边缘磨损;特别地,主管相贯锥管300、支管相贯锥管400具有较大的相贯豁口以形成三通区域,且呈成斜锥台状,展开后其展开线不具有相同的曲率半径,直接卷板时不能按设计曲率成形;且由于小端与卷板机的挡轮相接触,会产生磨损;为防止这些缺陷,需将对应的下料板的小锥端补为正锥,补料板的作用有二,其一是将其补为正锥更方便成形,其二是对产品小锥端形成保护,防止产生磨损,因此本实施例中,其对应的小端补料板中间窄,两端宽;对应小端是正锥的情形,例如支弯管相贯锥管500展开,小锥端为正锥结构,也需要补料,为防止其边部磨损,导致素线方向宽度缩短,对应的小端补料板可为等宽的弧形带状结构。
20.在油压机上装载压头模具,所述压头模具包括成型凹模和成型凸模,对主管100、支管200、主管100的下料板以及组合扇形板的侧边部进行压头和起弧,由于卷制时,下辊在固定位置转动;上辊800调节沿铅垂线位置,并沿上辊800圆面的中心转运,其中心线与下辊之间有一段距离,起始段由于不能三辊连续受力,从而形成直边,随着卷板机的卷板能力增加,两下辊之间的中心距越来越大,形成的直边长度就越长,由于直边不符合产品质量要求,通常就需要卷到一定程度时将其去除,这就形成了材料浪费,对弧度的起始段进行预制,可有效节约材料。
21.在三辊卷板机上把预弯好的主管100、支管200、主管100的下料板进行卷制,得到筒形瓦片;卷制组合扇形板时,三辊卷板机上辊800倾斜,将组合扇形板小口端边缘抵靠上
辊800旁的挡轮810上,三辊卷板机上辊800的压线与锥管圆锥等分的素母线重合,卷制时不断移动大端,大端的进入速度要加快小端的边缘就会倚着挡轮往里进,持续卷制,得到锥形瓦片。
22.将锥形瓦片上对应的补料部分进行分割。筒形瓦片、组合扇形板周边及拼接边开k形坡口,坡口角25
°
,钝边2mm,便于后期焊接。
23.将多个筒形瓦片、割去补料的锥形瓦片焊接后并与月牙肋板600组装并焊接形成完整的岔管,参见图1。
24.在一些实施例中,为提高坯料利用率,也即钢板的利用率,将具有相贯口开口设置在展开料的边部,也即需要从相贯线a处分缝,具体到本实施例中,支弯管相贯锥管500、主管相贯锥管300、支管相贯锥管400放样时,对应的放样图分纵边时候,纵边下端与其相贯豁口的相贯线a相交,纵边并与最短轴线在圆周方向错开布置;不应在轴线最短边分纵缝,以防止卷起时此部分板材的强度不足以支撑整块板的重量而引起意外的变形,因此是从纵边并与最短轴线在圆周方向错开布置;从该处分纵边,从而使展开长度上的左、右长度基本相等,以减少钢板的供货规格。
25.进一步地,为提高板材的利用率,可将支管相贯锥管400的下料板的分为两个在素线方向上的板料部分,可通过环形焊缝,连接成整体;具体到本实施例中,可在放样时,支管相贯锥管400的放样图包括第一扇形板放样图、第二扇形板放样图;对应于第二扇形板放样图有第二补料板放样图;下料得到的第一扇形下料板410、第二扇形下料板420以及第二补料板430,第二补料板430的两端边缘具有用于包覆所述第二扇形下料板420边缘第一左侧补料片440、第二右侧补料片450,第一左侧补料片440、第二右侧补料片可通过焊接方式与第二扇形下料板420连接;将第一扇形下料板410的小锥端边缘与对应的小端补料板的大锥端边缘连接固定形成第一组合扇形板40,将第二扇形下料板420小锥端上边缘与第二补料板430的大锥端边缘连接固定,第一左侧补料片440、第二右侧补料片450分别与第二扇形下料板420边缘连接固定形成第二组合扇形板41;对组合形成的两组合扇形板圆周方向上的边部进行压头和起弧;在三辊卷板机上进行组合扇形板卷制,得到组合锥形瓦片;进行组圆检验,再将两组合锥形瓦片焊接成完整支管相贯锥管400。采用该种方式,在可相对整块钢板下料,可显著节约钢材,同时钢材的规格较小,便于运输和加工;将第二扇形下料板420,设计为需要补料的情形,是因为可以使第二扇形下料板420与第一扇形下料板410在素线方向上的宽度更接近,如果第二扇形下料板420按正锥展开下料,第二扇形下料板420在素线方向上的变化较大,需要更宽的板材下料,浪费也较为严重,因此,第二补料板430呈中间窄,两头宽的趋势。
26.由于,第一扇形下料板410与第二扇形下料板420对接环形缝向两端与相贯线a相接,因此,第二扇形下料板420两端形成尖角,当扇形下料板的两端小锥呈尖角时,宜对小端进行加强,可以补宽度200~300mm,长度600~800mm的矩形板作为第一左侧补料片440、第二右侧补料片450,使之参与起始段的卷曲,并在任一端由行车起吊时,第二组合扇形板41另一端承受一定的重量,防止被折弯,第一左侧补料片440、第二右侧补料片450也能够便于进行压头操作,在压头时候,由于尖角部分比较薄弱,同时由于尖角部分较为薄弱,无法直接进行压头,压头时候,尖角部分不能支承整个钢板弹性变形,在尖角区域容易出现塑形变形,导致较大形状偏差,无法满足要求,但是在进行卷制时候,如果不进行压头,则尖角部分
为直边,组合扇形板的边部,如果进料端不补料,必定会有直段,无法顺利进行给料,上辊800的下边际低于下辊的上边线,无法实现其起始段的卷曲;通过增加左、右侧补料片,在进行压料时候,对补料片部分开始压料,压料导致的误差不会影响第二扇形下料板420本身,对应于第二扇形下料板420尖角处有较长的素线宽度,具有较高强度,特别是第二组合扇形板41尖角部分对应的补料部分在后期进行去除,从而可以使相贯线a对应的尖角部分符合设计精度。
27.再者,在卷制时候,从左或右边侧进行第二组合扇形板41卷制时,在卷制初期,相比较于没有补料的结构,受卷部分,特别是尖角对应部分,素线方向上长度较长,强度较高,持续卷制时候,能够在素线方向以及与素线垂直方向上对钢板进行支承,强度变化区间较小,能够显著提高三辊机的使用寿命,同时能够防止在卷折过程中的突变,以保证较小形位偏差,在卷制后期,补料后尖角部分,也具有较高的支承强度,能够支承其余板身的重量。 第一左侧补料片440、第二右侧补料片450也以对小端形成正锥,当小端参与卷制时,可以有效地导向使锥管成形良好,补料的同时可以防止小锥端与挡轮产生磨损,以保护扇形下料板小端,防止素线长度减短。所述第二补料板430两端边缘分别与第一左侧补料片440、第二右侧补料片一体成型,一体成型,具有较高的强度和材料的连续性,使成型后的精度较高。
28.再进一步地,第二扇形下料板420、第一扇形下料板410均分别由两下料板拼接连接固定,拼接缝为纵缝,两条纵缝在圆周方向错开布置,采用该方式也可使用更小规格的钢板,能够降低生产成本,同时在放样以及下料时候,两侧的板材的长轴方向可倾斜设置,可更加节省材料。
29.同理地,支弯管相贯锥管500的放样图包括第三、第四扇形板放样图;对应于第四扇形板放样图放样有第三补料板放样图;下料得到的第三扇形下料板、第四扇形下料板以及第三补料板,所述第三补料板的两端边缘具有用于包覆所述第四扇形下料板边缘第三左侧补料片、第四右侧补料片;将第三扇形下料板的小锥端边缘与对应的小端补料板的大锥端边缘连接固定形成第三组合扇形板,由于支弯管相贯锥管500小锥端为正锥结构,小端补料板可为等环宽的弧形板,第三补料板也可为等环宽的弧形板。同理地,第四扇形板两端小锥呈尖角时,宜对小端进行加强,可以补宽度200~300mm,长度600~800mm的矩形板作为第三左侧补料片、第四右侧补料片,第三左侧补料片、第四右侧补料片分别与第四扇形下料板小锥端上边缘连接固定,第四扇形下料板小锥端上边缘与第三补料板的大锥端边缘连接固定形成第四组合扇形板;对组合形成的组合扇形板圆周方向上的边部进行压头和起弧;在三辊卷板机上进行组合扇形板卷制,得到组合锥形瓦片;将每个组合锥形瓦片上对应的补料部分进行分割;进行组圆检验,再焊接成支弯管相贯锥管500。
30.当然地,第三扇形下料板、第四扇形下料板也均分别由两下料板拼接连接固定,拼接缝为纵缝,两条纵缝在圆周方向错开布置,采用该方式也可使用更小规格的钢板,能够降低生产成本,同时在放样以及下料时候,两侧的板材的长轴方向可倾斜设置,可更加节省材料。
31.由于支管相贯锥管400整体展开图与主管相贯锥管300整体展开图近似,主管相贯锥管300可参考支管相贯锥管400成型原理,同理地,主管相贯锥管300的放样图也可包括第多个放样图,下得的下料板的分为两个在素线方向上的板料部分,可通过环形焊缝,连接成整体,其下方的板料下料有对应的补料板,用于将小锥端补齐为正锥结构,同时增加磨损余
量,两组合扇形板,卷制后,再分割补料部分,最后组焊为主管相贯锥管300。当然,两个下料板又可由多个更小的料板组成,可进一步降低对板材规格要求,节省成本。
32.采用本发明,能够在保证岔管较高的成型精度下,同时能够节省用料,降低生产成本。作为本发明的一个应用例,采用本发明成型的岔管在黄金峡水利枢纽坝后泵站,进行应用,黄金峡水利枢纽坝后泵站共7台抽水机组,总装机12.6万千瓦,泵站抽水流量每秒70立方米,设计扬程106.45米,其综合指标位列亚洲之冠。泵站出口压力钢管7个支管200通过6个岔管与主流管相接,泵站出口压力钢管岔管设计水头为200米,岔管水压试验压力为2.5兆帕。
33.以上所述仅为本发明的优选实施例,并不用于限制本发明,显然,本领域的技术人员可以对本发明进行各种改动和变型而不脱离本发明的精神和范围。这样,倘若本发明的这些修改和变型属于本发明权利要求及其等同技术的范围之内,则本发明也意图包含这些改动和变型在内。