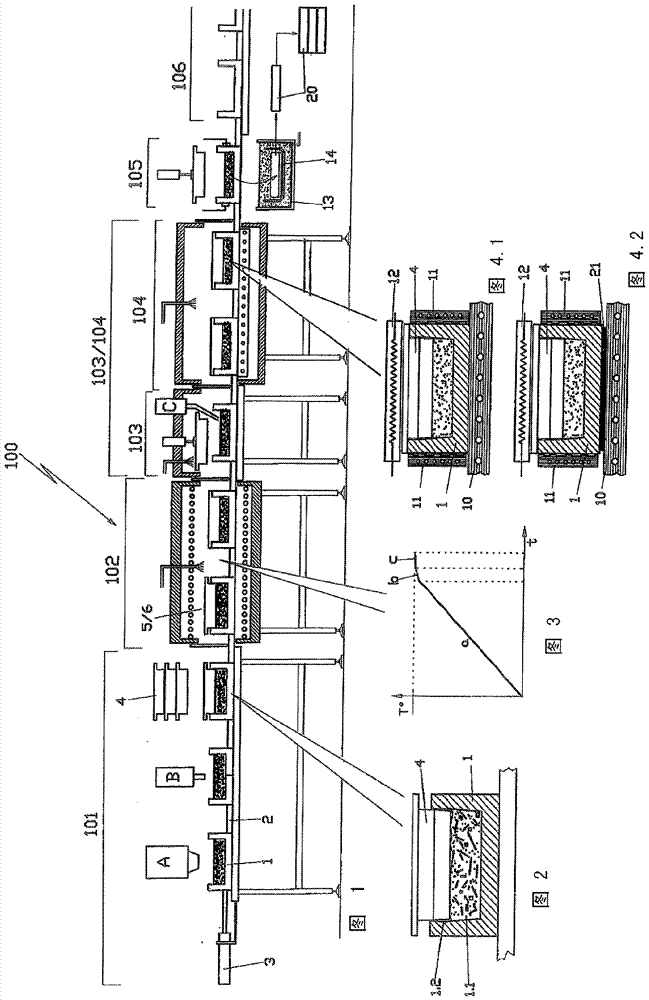
用于形成金属棒的机器本申请是国际申请日为2012年3月29日、名称为“用于形成金属棒的机器”、国家申请号为201280016462.1(国际申请号为PCT/US2012/001377)的专利申请的分案申请。技术领域本发明涉及用于形成金属棒、尤其适用于对诸如金、银的贵金属、贵金属合金以及其他纯金属或不同合金进行熔化和随后的连续固化以制造铸块的机器。
背景技术:如所已知,制造尤其由金、银、贵金属合金、其他纯金属和不同合金制成的铸块通常借助于两种不同的方法来获得。当制造5g至50g的轻铸块时,习惯于进行从诸如圆柱形的预先形成的垫料或坯料的半成品开始冷模塑和模压过程。当制造重量在50g与50Kg之间变化的铸块时,替代地使用熔化方法和随后在特定模具中对金属进行固化。在实践中,将各种尺寸的粉末、颗粒或松散原料形式的待熔化的金属放置在钢包内,在该钢包中使其熔化。随后,将熔化的金属倾倒在通常成形以形成截梯形的单个铸块模具中,在该模具中,使其具有铸块的形状固化。考虑到所获得的最终产品必须符合严格且特定标准要求,这两个操作(熔化操作和随后固化材料的操作)必须特别小心地进行。实际上,市场可购得的铸块(除了在由纯金属制成的情况下具有精确纯度或者在由合金制成的情况下具有精确的纯金属百分比(所谓的“计数”))必须具有极其精确的尺寸和重量、具有规则表面的外部配置、没有凹陷或破裂、均匀的着色以及首要地它们必须具有完美的内部金相结构、没有气孔、微孔以及结构张力。为了避免获得不能允许获得“冲压”的有缺陷的铸块(其因此将会被认为是废料),必须非常小心地进行整个制造周期,尤其在熔化、固化以及冷却金属的步骤过程中。根据现有的技术状态,除了手工制造之外,制造铸块通过使用具备熔缸(来自该熔缸的熔化的金属被倾倒至铸块模具中)的熔炉也使用相当大尺寸的机械设备来进行,其中通过连续的自动周期来执行主要的工作步骤。先前技术的最重要文件是:JP4305359A、US2001/050157A1、DE20012066U1以及US2007/289715A1。
技术实现要素:本发明的目标在于提供一种用于形成金属棒、尤其用于制造由贵金属和非贵金属材料制成的铸块并且尽管包括熔化和固化材料的步骤但是不具有已知类型的机械设备所展示的缺点的机器。此目标是通过提供其中存在接连布置的六个操作台的机器来获得,其中:–在定义为“装载区”的第一台中,进行将固体金属放置在铸块模具中、添加特定的化学添加剂(该添加剂与材料的结晶结构反应以防止在随后的熔化步骤过程中形成不均匀和内部张力)、放置盖子用于封闭铸块模具,并且其中存在用于在整个操作周期中将所有铸块模具向前移动的推动装置;–在通常定义为“熔炉”的第二台中,进行根据预定温度/时间参数来熔化包含在铸块模具中的金属;–在定义为“二次添加”的第三台中,将化学添加剂放置在仍是液体的金属上,这消除了趋向于在随后的固化步骤过程中形成在铸块表面上的不均匀。–在定义为“固化区”的第四台中,进行根据预定温度/时间参数来固化铸块模具中的金属;–在定义为“冷却区”的第五台中,进行冷却固体铸块,并且其中,当需要快速冷却时,将以上提及的铸块卸载到包含有冷却流体的桶中,该铸块在得到完全冷却时从桶中进行收集;–在定义为“卸载区”的第六台中,卸载铸块模具,铸块模具在正常冷却的情况下可以包含铸块或者在快速冷却并且单独地收回冷却的铸块的情况下它们可以是空的。附图说明将通过参照附图藉由非限制性示例提供的本发明的可能实施例来描述使得本发明的特征更加清楚,附图中:图1表示根据本发明的机器的正视图;图2表示装载台中的铸块模具的详细图;图3表示金属熔化台中的t/T°(时间/温度)图示;图4.1和4.2表示不同冷却模式下固化台中的铸块模具的详细图;图5表示在固化步骤过程中铸块模具的滑板的三种不同配置。具体实施方式如从图中可观察出,根据本发明的机器(通常以参考数字100指示)包括:–用于装载和推动铸块模具1的第一台(以参考数字101指示);–包含在铸块模具中的金属熔化台(以参考数字102指示);–用于静止的液体金属上的二次添加的二次添加台(以参考数字103指示);–用于固化熔化的金属的固化台(以参考数字104指示);–用于冷却固体铸块的冷却台(以参考数字105指示);–用于卸载铸块模具的卸载台(以参考数字106指示);如从图1可以看出,在第一台101的装载表面上放置有空的铸块模具1,由石墨或任何其他耐熔材料制成的隔板2置于铸块模具与下一个铸块模具之间或者两个或更多个相邻铸块模具的群组之间,所述隔板具有维持单个铸块模具之间或者铸块模具群组之间的预定距离的功能,方式为使得形成“铸块模具队列”的铸块模具1在向前移动过程中始终正确地放置在工作区域内;另外,所述操作表面还具备推动设备3,推动设备可以不同的方式进行驱动,诸如通过蜗杆螺钉、气动装置、液压装置或者任何其他装置,其提供以预定“节距”推动上述队列向前并且随后返回,并因此空出上述装载表面上的空间,以便允许放置另外的空的铸块模具。从操作的观点来看,在每个单个铸块模具1中,倾倒有各种尺寸的粉末、颗粒或细屑形式精确重量的金属(倾倒元件“A”),并且添加有化学添加剂(给料元件“B”),化学添加剂与金属中含有的杂质发生化学反应并且由硼酸、硼砂、硝酸钾、铵、钠、锂和钾和氯化钠单独使用地或混合使用地制成。最后,在所述第一台101中,进行放置盖子4以用于封闭填满的铸块模具。从构造的观点来看,如图2中可以详细看出,铸块模具1可以具有的高度尺寸使得当其填满精确重量的金属时,其盖子4抵靠在金属上,但是相对于铸块模具的边缘的邻接部保持升高,这允许盖子的底部挤压并且因此规则地压紧粉末、颗粒或细屑,这样使得在随后的熔化步骤过程中,当金属质量所占据的体积逐渐减小甚至达到初始固体体积的三分之一时,盖子随着金属熔化逐步降低,直到其抵靠在上述邻接部上,因此密封地封闭铸块模具。此外,铸块模具1的内部空间由两个不同体积组成:下部体积1.1构成实际“模具”,其中根据国际标准(诸如像LMBA标准)或者通过客户的其他具体要求确定铸块的形状和尺寸;以及可以不同地配置的第二上部体积1.2,目的在于在装载步骤过程中促进金属的放置。随后,推动设备3将“队列”从第一台101推动用于将铸块模具供应到金属熔化台102,其中可从存在其中铸块模具和隔板在没有受控的大气压下在耐熔表面上滑动的加热熔炉5或者在其中铸块模具和隔板在隧道表面上或者导轨上滑动、以不同方式被加热(穿过电阻器、通过电磁感应、穿过气体类型或任何其他类型的燃烧器)达到操作温度的隧道6;通过示例,对于由银(Ag)制成的铸块来说,此温度为约1150℃。而对于由金(Au)制成的铸块来说,此温度为约1250℃,并且在隧道中或导轨中存在吹入的惰性气体,诸如氮、氮与氢混合物(其中氢(H)最大量为4.5%)以便产生“惰性”环境,这防止铸块模具和盖子受到氧化并且因此防止快速磨损并保持熔化的金属免受氧的影响。实际上,重复地并且不断地调整隧道内的铸块的熔化温度的困难通过使用“感应”加热得到了部分地克服,其中加热温度的增加(热梯度)以至少两个斜度发生(图3):高达达到熔化温度的设定值的至少90%的快速斜度(a)和具有较小倾斜轮廓的一个或多个斜度(b、c)(参见图3)。此外,为了减少隧道6内的惰性气体的热量和大气压的目的,在“队列”的出口和入口的侧向开口处提供通过例如剪切技术获得的移动隔壁的应用,这些隔壁产生移动的或柔韧的绝缘耐熔屏障,其移动是手动的或自动的。随后,仍然从操作的观点来看,一旦经过了熔化时间,则启动推动设备3,这提供将“队列”向前移动;存在于装载表面上的铸块模具被推到熔炉5/隧道6中,并且同样又将存在于熔炉5/隧道6中的铸块模具推动离开,目的在于允许包含熔化的金属的铸块模具随后进入二次添加台103并且随后进入固化台104中。从操作的观点来看,在二次添加台103中,进行借助于机械类型、气动类型或任何其他类型的夹具使铸块模具的盖子升高,同时机械类型、气动类型或任何其他类型的给料系统在每个单个铸块模具1中在熔化的金属上添加精确量的化学添加剂(给料元件“C”),化学添加剂与熔化的金属中含有的杂质发生反应,该添加剂由硼酸、硼砂、硝酸钾、铵、钠、锂和钾以及氯化钠单独使用地或混合使用地制成;随后,将盖子重新放置在铸块模具上。另外,在“二次添加”的过程中,应产生“惰性”环境,对此来说,引入诸如氮气、氩或氮与氢混合物的惰性气体流,这防止铸块模具和盖子的氧化并且保护以液体形式静止的金属免受氧的影响。随后,在固化台104中,包含熔化的金属并且由盖子封闭的炽热温度的铸块模具滑动直到它们停止在冷却表面10上,冷却表面10借助于存在于其内的通孔通过水来冷却并且使用铜、铝或其合金或使用适用于受控的热消散的其他材料制成,其中它们根据有待固化的材料量保持预定的时间段(平均1至5分钟),直到整个质量的完全固化。另外,在固化过程中,应产生“惰性”环境,因此引入诸如氮、氩或氮与氢混合物的惰性气体流,这防止铸块模具和盖子的氧化并且保护被固化的金属免受氧影响。具体来说,取决于铸块需要获得的内部金属结构(应具有大、中等或小结晶体和或多或少显著的固化收缩),固化台104可以具备:用于使热消散减缓的另外的绝缘或耐熔冷却板11;此类板可以能够具备用于限定局部的热区域的凹槽,这些板放置在铸块模具和盖子的一个或多个侧面附近或与其接触(参见图4.1);和/或用于使冷却减缓的另外的加热板21,其由石墨、金属或耐熔或绝缘材料制成、平滑或具备凸起或凹入的适合的轧齿边,其可以放置在冷却表面10与铸块模具1之间(参见图4.2)。替代地,当需要精确控制热力固化梯度时,为了获得具有最适合的固化金属结构的铸块的目的,固化台104可以具备也定位在铸块模具周围和盖子上的例如使用电阻器、气体或使用任何其他装置来加热的加热面板12。此外,为了具有精确地确定热力梯度的进一步可能性的目的,取决于铸块需要采用的内部金属结构,冷却表面10可以具有滑动表面(铸块模具在固化步骤中停留在该表面上),其具有平坦并且平滑的表面或者具备凸起或凹入的轧齿边;另外,冷却流体的通过可以相对于铸块模具的“队列”的移动方向纵向地和/或横向地来实现(参见图5)。由于构造原因,在一些情况下,二次添加台103和固化台104可以合并在单个台中,其中顺序地执行添加和固化步骤。随后,铸块模具在冷却台105中通过,并且根据设定的制造时间并且根据材料类型和制造的铸块的“大小”,此操作可以通过两个不同的操作模式而进行。具体来说,两种冷却方法是:–正常冷却:具有仍然非常热的铸块的铸块模具在自由环境中经受受控的冷却并且它们随后被发送到卸载台106。–铸块的快速冷却:当将具有仍然非常热的固体铸块的铸块模具带到冷却区域时,它们被清空并且铸块投入冷却水桶13中,而空的铸块模具被发送到卸载台106。从操作的观点来看,快速冷却提供借助于机械类型、气动类型或任何其他类型的夹具来升高铸块模具的盖子,而机械类型、气动类型或任何其他类型的致动器将铸块模具锁定在底座上。随后,上述致动器使铸块模具旋转并倾斜,并且通过重力,热的铸块落到没入冷却桶13中的筐14中,该筐在适当的冷却时间之后通过平移运动从上述桶离开以允许收集冷却的铸块20。随后,相反,在空的筐14返回之后,重新定位空的铸块模具并且降低盖子,头部推动设备3将“队列”向前移动,这样使得空的铸块模具滑动,最后定位在卸载台106中,从卸载台与铸块20一起被收集。具体来说,所述卸载台106可以适当地延伸,以便允许铸块模具的“队列”保持暴露在冷却表面上持续长时间段,以便能够逐渐达到适于允许应收集那些空模具(在快速冷却的情况下)或者应移除盖子并且从铸块模具收集冷却的铸块(在正常冷却的情况下)的操作者容易操纵的温度。因此,所设想的发明可以经受多种变体和修改,并且其构造细节可以由技术上等效的元件替换。