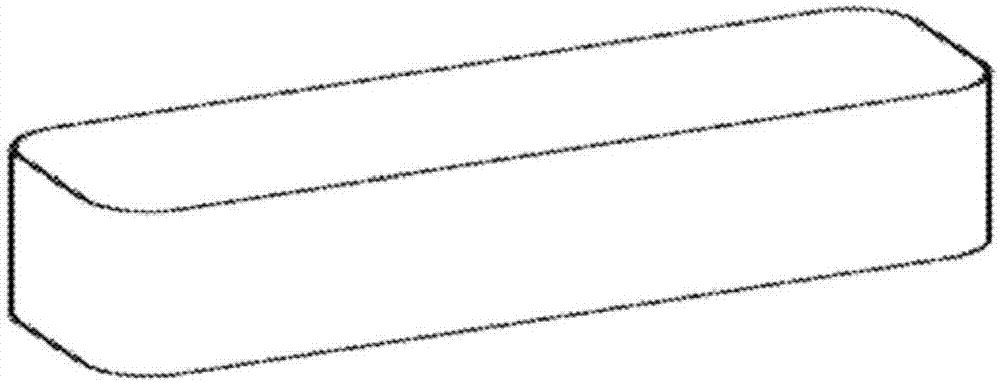
本发明涉及铂族金属或铂族基合金的制造方法,具体涉及铂族金属或铂族基合金的制造方法中的熔解锭制造。
背景技术:
:铂族金属或铂族基合金通过利用铂族金属所具备的耐热性、耐氧化性、耐化学品性而设计,广泛用作高温构件和/或耐蚀制品。此处铂族金属是指Pt、Pd、Rh、Ir、Ru、Os的总称。铂族金属或铂族基合金的制造工序通常包含合金原料的配混工序、熔解工序、塑性加工工序等,在熔解工序中制造熔解锭的熔解方法分为几个类型。主要成分的铂族金属的熔点非常高(1500℃以上),因而使用了具有2000℃以上的熔解能力的电感加热熔解炉或能量束熔解炉。在能量束熔解方面,存在有非消耗型电弧熔炼、真空等离子体熔解、大气压等离子体电弧熔炼、电子束熔解等,对水冷却铜坩埚内的原料照射能量束而熔解这一点是共通的。熔解原料是铸块、包含废料(scrap)的板、线、粉末等的形状,适当配混规定量而使用。在能量束熔解方面,水冷却铜坩埚的方式按照大致划分而存在有两种。一种方式是使用舟形水冷却铜坩埚的方式。舟形水冷却铜坩埚是具有圆形、方形等形状的空腔(洼部)的水冷却铜坩埚,将装载于该空腔的原料总量进行熔解而获得熔解锭(专利文献1)。另一种方式是使用具备底面被贯通的空腔的水冷却铜坩埚的方式。在该方式中,一边将作为原料的原料棒保持为水平,一边将原料棒的一端插入于能量束中进行熔解,连续性地使熔液滴下,在接受熔液的空腔中形成熔融池。将该熔融池底部连续性地降低,从而获得棒状的熔解锭(专利文献2)。该原料棒通常事先将原料进行熔解而制造。在熔解原料的一部分或全部是粉末的情况下,在粉末状的状态下熔解时则因能量束的流动会发生飞舞或飞散。为了防止粉末的飞舞,因而有时会通过压制成形、CIP成形等成形方法预先将粉末进行压缩成形(专利文献3)。压缩成形了的粉末中,颗粒彼此接触,相互缠绕而在表观上一体化了,即使被照射能量束也可抑制吹跑而飞舞的情况。通常的成形体的相对密度为30%乃至60%左右,包含了相当程度的空隙,在空隙中存在气氛气体或残留气体。另外,由于成形体仅仅是在表观上一体化了,因而不但因落下等的冲击而容易地破坏,而且在运送中表面的粉末也发生剥落,降低材料成品率。此处所说的材料成品率是指熔解锭的质量相对于熔解原料的质量的比例。然而,对该成形体照射能量束时,则利用传导热、辐射热以及焦耳热进行加热,以照射部分为中心,成形体的温度急剧升高。此时,由于在空隙中存在的气体急剧地膨胀,因而仅仅在表观上一体化了的颗粒向水冷却铜坩埚之外弹飞。同时部分性地熔融了的熔融金属也被弹出,结果是熔解锭的质量相应地减少。即,材料成品率降低,在非常昂贵的铂族金属的制造方面,经济损失大。进一步,在原料是混合粉的情况下,不但材料成品率降低而且在组成上也有可能发生变动。成形体发生破裂而使其破片落下,或者成形体表面的粉末剥落,或者在熔解中熔融金属飞散时,则该部分中所含的成分不包含于熔解锭,因而无法制成准确的合金组成。另外,在使用舟形水冷却铜坩埚的能量束熔解中,从上表面照射能量束而熔解,但是通常将原料进行上下反转,使得从相反面也熔解,反复进行这一操作而制成均匀组成的熔解锭。此时,落下了的破片以及剥落了的粉末有时会未熔化而残留于水冷却铜坩埚(hearth)的舟形空腔角落部。在这样的情况下,也妨碍制成准确的合金组成。现有技术文献专利文献专利文献1:日本特开2002-105631专利文献2:日本特开2009-93881专利文献3:日本特开2004-137580技术实现要素:发明想要解决的课题本发明鉴于上述那样的现有技术的问题而开发,其目的在于,提供一种材料成品率高的铂族金属或铂族基合金的制造方法。用于解决问题的方案本发明关于一种铂族金属或铂族基合金的制造方法,其特征在于,在所述铂族金属或铂族基合金的制造方法中包含如下的工序:将一部分或全部是粉末的原料进行称量,在以合金制造为目的的情况下将前述称量出的原料进行混合以获得混合粉的配混工序;将前述称量出的原料进行成形固化以获得成形体的成形工序;将前述成形体烧结以获得烧结体的烧结工序;将前述烧结体熔解以制造熔解锭的熔解工序;对前述熔解锭进行加工的塑性加工工序,在前述烧结工序中,通过一边将多个该成形体彼此进行堆积,一边焙烧以制成作为接合体的烧结体。配混工序是指按照所希望的熔解锭量以称量原料的工序,在目的为合金制造的情况下,按照成为规定的合金组成的方式称量各原料。原料的形状可以是任何样的,但是至少一部分或全部是粉末。成形工序是将原料总量的一部分或全部的粉末原料进行成形固化而获得成形体的工序,单轴加压成形、片剂成形、CIP(冷等静压成形)、橡胶压制等公知的干式成形法是合适的。形状可任意选择,可从圆板、圆柱状、包含多边形的方形板、棱柱状、无定形的煤球状等中选择。关于成形体的数量,可根据水冷却铜坩埚的形状、尺寸而确定,设为一个或多个。烧结工序是将成形体烧结而在实质上成为一体的工序,可利用燃气炉、电炉等公知的焙烧炉,分批式、连续式中的任一种都适合。焙烧温度可根据原料的种类而适当选择,但是在熔点超过1500℃的铂族金属或铂族基合金方面,1000℃以上且不超过原料的熔点的范围是更加适合的。焙烧气氛可适用大气、非活性气体或真空,根据原料的种类进行适当选择。关于烧结体,由于将各个颗粒进行一体化,因而强度高,且通过烧结收缩而成为高密度。相对密度不需要特别限定,但是优选为60%以上,更优选为70%以上。制成这样的烧结体时,则颗粒彼此发生一体化而使得强度变高,不可能发生成形体的破片的落下以及粉末的剥落。由于可进一步抑制熔解工序中的熔解时的飞散,因而也可抑制合金组成的变动。如前述那样,成形体由于强度不足,因而在降低方式的熔解工序中用作原料棒的情况下,存在有在熔解中折损的危险性,因在轻微的力的作用下崩溃,由此难以夹持于原料棒运送机构中,不易直接使用。根据本发明,由于通过烧结使得颗粒彼此发生一体化而获得高的强度,因而也不存在折损、崩解的担忧,可用作原料棒。在烧结工序中,可通过一边将多个该成形体彼此进行堆积,一边焙烧而进行焙烧,并且制成作为接合体的烧结体。成形体的形状可任意选择,可从圆板、圆柱状、包含多边形的方形板、棱柱状等中选择。即,在烧结工序中,堆积成形体而焙烧时,则不仅在各个成形体内部颗粒被烧结,而且在堆积了的成形体彼此的界面上接触着的颗粒彼此也烧结,进行一体化。通过这样操作而获得棒状的烧结体(接合体)。通过适当选择要堆积的烧结体的尺寸以及数量,从而具有如下的优点:可根据需要,从极少量的短尺寸的原料棒直到长尺寸的原料棒为止,进行变更。特别是在降低方式的熔解工序中用作原料棒,因而优选。关于以往的原料棒,在熔解工序之前,预先利用能量束熔解炉在舟形水冷却铜坩埚中制造熔解锭,将该熔解锭制成了长尺寸的原料棒。这样地制造的熔解锭的形状不是一定的。即,熔解锭的底部转印舟形水冷却铜坩埚的形状并且成为一定形状,但是熔解锭的侧面以及上表面熔液进行凝固,成为本来的形状。如铂族金属以及铂族基合金那样在熔解的定容潜热高的情况下,熔液远离能量束(加热源)时则容易即时凝固,因而熔解锭侧面的毛刺产生以及上表面的波纹起伏变显著,使得原料棒的截面积成为不一定。此处定容潜热(kJ/cm3)是指为了熔融单位体积的物质而必需的潜热,由熔解热(kJ/mol)和摩尔质量(g/mol)和密度(g/cm3)进行定义。使用这样的原料棒而进行降低熔解时,不易以一定速度滴下熔液,容易发生如下的事故:在小截面积的部分处滴下的熔液不足并且在熔解锭产生空孔等缺陷,在大截面积的部分处滴下的熔液变得过多,并且从水冷却铜坩埚的空腔溢出来而凝固。根据本发明,在烧结工序中可烧结稳定尺寸的成形体,可将该成形体以稳定尺寸的原料棒的形式使用,因而不产生这样的问题。另外,在原料棒的制作中需要专用的熔解设备(熔解炉、坩埚等),但是本发明中,一概不需要那样的设备,可通过使用一般的电炉等而非常简便地制造原料棒(烧结体)。用于该原料棒所用的成形体可采取任意的形状,但是利用单轴加压成形而制成大致长方体时,则成形特别容易,即使在烧结时堆积也非常便利(权利要求2)。然而,关于能量束熔解的炉内压力,根据熔解方式和/或熔解原料而不同(高真空~大气压)。特别是电子束熔解炉必须为0.1Pa以下的高真空域。在真空度这样高的情况下,由于与烧结体的空隙中残留的气体成分的压力差大,因而有时也会略微地飞散。因此,熔解中的炉内压力更优选为1Pa以上。熔解工序是以烧结体为原料而制造熔解锭的工序。不仅可适用前述能量束熔解,而且可适用在铂族贵金属以及铂族基合金的制造中广泛使用的以往的熔解炉或熔解方法。例如,在粉末原料的电感加热熔解中,颗粒间的接触面积小,因而无法获得充分的感应电流,并不适合,但是在本发明中,通过烧结而使得颗粒彼此在实质上一体化了,获得充分的感应电流,因而也可适用于电感加热熔解。另外,关于熔解工序,使用具备有水冷却铜坩埚的能量束熔解炉,该水冷却铜坩埚具备底面被贯通的空腔。将棒状的烧结体(接合体)用为原料棒,而将其一端插入于能量束,进行熔解,连续性地使熔液滴下,在接受熔液的空腔形成熔融池,将该熔融池底部连续性地降低,从而可获得棒状的熔解锭。即,在降低方式的熔解工序中优选将棒状的烧结体(接合体)用作原料棒。另外,本发明是一种铂族金属或铂族基合金的制造方法,其特征在于,在所述铂族金属或铂族基合金的制造方法中包含如下的工序:将一部分或全部是粉末的原料进行称量,在以合金制造为目的的情况下将前述称量出的原料进行混合以获得混合粉的配混工序;将前述配混了的原料进行成形固化以获得成形体的成形工序;将前述成形体烧结以获得烧结体的烧结工序;通过使用能量束熔解法将前述烧结体熔解而制造熔解锭的熔解工序,其中,该能量束熔解法应用了形成有空腔的舟形水冷却铜坩埚;对前述熔解锭进行加工的塑性加工工序,在前述烧结工序中,使得前述烧结体的形状、尺寸对应于前述空腔,在前述熔解工序中,使得对应于前述空腔的前述烧结体紧密地并排配置于前述舟形水冷却铜坩埚的前述空腔内,以制造前述熔解锭。能量束熔解的舟形水冷却铜坩埚通常是在埋设了水冷却回路的铜的上表面形成着圆形或方形的空腔(洼部)。将熔解原料设置于空腔内,从上表面照射能量束而加热熔解。对应空腔地设计烧结体的形状、尺寸时,则可获得更多的熔解锭。即,在圆形空腔中将圆柱或圆盘状的成形体烧结而配置、在方形空腔中将立方体、长方体或者六棱柱的成形体烧结而配置时,可在平面上密密排列,也容易堆积起来。塑性加工工序是将熔解锭加工为板和/或线等所希望的形状的工序,可适用公知方法。关于通过本发明制造的熔解锭,可与通过以往的不经由烧结工序的工序而获得的熔解锭同样地进行塑性加工。例如,在加工为板形的情况下,经由锻造加工、轧制加工。在加工为线形的情况下,经由锻造加工、沟槽轧制加工、拉丝加工。在任一种情况下,都根据加工固化的程度,在加工过程中进行适当热处理而软化。在加工为板或线之后,也可根据使用目的进行切断、弯曲、焊接等加工。另外,关于各加工,可适用冷加工或将材料加热而加工的热加工中的任一种。发明的效果如以上说明的那样,根据本发明的制造方法,相比较于以往的制造方法而言,可有效地抑制熔解时的原料飞散,可提高昂贵的铂族金属或铂族基合金的材料成品率。另外,与成形体相比,烧结体的强度高并且不容易破坏,也可抑制在运送中粉末剥落。这使其具有如下的优点,即,不使原料的一部分发生落下或剥落以导致发生组成变动,进一步在用作原料棒的情况下,可在装置内合理地支撑、夹持。进一步也具有如下的优点,与成形体相比密度高,即,可减小同一质量下的体积,因而可在水冷却铜坩埚装载更多的原料,并且有助于生产率提高。附图说明图1是表示烧结体的例子的图。图2是表示烧结体的另一例的图。具体实施方式列举内燃机用火花塞的电极头(electrodetip)的制造方法作为例子,更详细说明。火花塞的电极头优选使用了铱基合金或铂基合金。在此例子中,原料的总量是粉末,使用Ir粉末与Pt粉末。(配混工序)按照成为规定的组成的方式称量规定量的各个的粉末,使用V型混合机而混合,制成均匀的混合粉末。(成形工序)将混合粉末填充于自动压制成形机(单轴加压成形)的料斗。在成形模具中设置有短边20mm、长边50mm的长方形的空腔,四角为R2mm。成形体尺寸是20×20×50mm且角落部是R2mm的大致长方体(图1)。成形压力为200MPa。这可任意地设定,但是大概设为120MPa以上即可,如果设为200MPa以上则获得相对密度为约50%以上的更高密度的成形体。成形体密度越高则越可减低烧结所必需的热能,是有利的,但是如果过量则导致成形体发生破裂。除此之外,还将混合粉末填充于橡胶软管、密封,进行CIP成形时,则也可获得圆棒状的成形体。即使在此情况下,也将成形压力设为120MPa以上即可,优选为300MPa左右。如以往那样直接地熔解这两例的成形体时,则可以视认出在熔解炉内加热的粉末以及熔融金属的一部分发生飞散、将火花弄散的情形。另外,用手接触时则粉末附着于手指,为从5cm左右的高度落下时,则角部发生破裂的程度的强度。(烧结工序)将成形体的20×20mm的面作为上下面,在纵向堆积5个,将其计数为1根(图2)。将计4根配置于碳制安放器(setter)内,每个安放器插入于具备有碳加热器的气氛炉内,在1500℃在氩气流下焙烧3小时。烧结体进行烧结收缩,获得相对密度70%以上、约16×16×220mm的原料棒(图2)。(熔解工序)将该原料棒水平地夹持于大气压等离子体电弧熔炼炉(降低方式)的原料棒运送机构,在0.9~1.2atm(大气压)的氩气氛下连续性地熔解、滴下,将水冷却铜坩埚底部降低时,则获得的圆柱状锭。在熔解中未发现飞散的情形,可确认烧结工序的效果。另外,此时原料棒虽然是悬臂梁的状态,但是在工序中也不会弯折,而且粉末也不会剥落。(塑性加工工序)对于熔解锭,通过热锻造而形成为角棒,接着通过热间沟槽轧制加工而制成大致四边形剖面的线。进一步,利用基于口模的热拉拔加工而制成规定外径的圆线。(切断工序)关于圆线,切断为适于线锯的长度。将多条线分别平行地排列,进行树脂固定,利用线锯而切断,从而制成规定长度的火花塞用电极头。实施例以实施例来进一步说明。表1是结果,按照下面的基准来评价。关于质量减少,以百分率表示配混时间点的原料粉末与熔解锭的质量减少,将超过3%设为×,将3%以下设为○。关于粉末剥落,用手指拿起了熔解前的烧结体或成形体时,将在手指上发现了粉末的附着的情况设为×,将完全没有附着的情况设为○。关于熔解状态,在熔解中进行目视观察,将继续性地观察到火花样的飞散现象的情况设为×,将稀少地观察到的情况设为△,将基本上没有观察到的情况设为○。关于综合判定,斟酌这些结果,将没有本发明的效果的情况设为×,将具有效果的情况设为○,将效果更高的情况设为◎。(实施例1)实施例1是前述说明(具体实施方式)的例子。由尺寸与质量计算出的成形体密度按照相对密度为52%,烧结体密度为74%。将该烧结体设为原料棒,制作出约的熔解锭。在熔解中(压力1.1×105Pa)中目视观察,结果是完全没有发现飞散的现象,起自熔解锭的配混工序的质量减少为0.6%以下。另外,烧结后到熔解完结为止之间,原料棒也没有发生弯折或者剥落。在熔解后的炉内,几乎完全没有飞散了的材料,也没有看到对水冷却铜坩埚的附着。(实施例2)在实施例2中,与实施例1同样地制作成形体。成形体尺寸是20×20×50mm且角落部是R2mm的大致长方体。不堆积该成形体并且个别地焙烧,制作出约16×16×44mm的烧结体。将该烧结体装载于舟形水冷却铜坩埚,利用真空等离子体熔解法熔解,制作出约15×30×100mm的熔解锭。将熔解时的压力调整为5×10-1Pa(Ar)。在熔解中的目视观察中,观察到偶尔飞散的情形,在熔解后的炉内,略微存在有飞散了的材料,其一部分附着于水冷却铜坩埚。熔解锭的质量减少为2.5%。另外,关于熔解锭的形状,底部沿着舟形水冷却铜坩埚的形状而制成大概平滑,但是在侧面存在有毛刺状的突起,上表面在凝固了的状态下是波纹起伏。(比较例1)在比较例1中,利用V型混合机混合原料粉末后,通过CIP法而制作出的圆柱状成形体。成形压力为300MPa时,由尺寸与质量计算出的成形体密度以相对密度计为48%。将该成形体分割为长度约30mm,装载于舟形水冷却铜坩埚,利用电弧熔炼法熔解,制作出约t15×w30×L100mm的熔解锭。熔解时的压力调整为8×104Pa(Ar)。成形体不是用手接触即碎裂程度的低强度,但是从CIP型取出时,粉末附着于手指,另外,可确认有附着于CIP模具内壁的粉末。在熔解中的目视观察中确认有,到成形体的整体熔化掉落为止期间,源自熔解部的飞散被断续地接续。在熔解后的炉内,存在有飞散了的材料,对水冷却铜坩埚的附着也显著。另外,在舟形水冷却铜坩埚的底部角落部,残留下飞散了的材料以及从成形体剥落了的粉末。这样地,所配混的原料粉末的一部分不熔解而被残留,起自熔解锭的配混工序的质量减少为3.2%。关于熔解锭的形状,与实施例2同样地具有毛刺状的突起和/或波纹起伏。(比较例2)在比较例2中,将与比较例1同样地制作出的成形体装载于舟形水冷却铜坩埚,通过真空等离子体熔解法而制作出约t15×w30×L100mm的熔解锭。熔解时的压力调整为5×10-1Pa(Ar)。在熔解中的目视观察中确认为,到成形体的整体熔化掉落为止之间,源自熔解部的飞散被断续地连续。在熔解后的炉内,更多地存在有飞散了的材料,对水冷却铜坩埚的附着也更显著。另外,在舟形水冷却铜坩埚的底部角落部,残留下飞散了的材料以及从成形体剥落了的粉末。这样地,所配混的原料粉末的一部分不熔解而被残留,起自熔解锭的配混工序的质量减少为4.5%。根据以上的结果确认有,在不经由烧结工序直接将成形体熔解的方法中,质量减少较多并且材料成品率恶化,在基于本发明的方法的烧结体熔解中,这些情况大大减轻。表1表1-实施例的结果No.质量减少粉末剥落溶解状态综合判定实施例1○○○◎实施例2○○△○比较例1××××比较例2××××当前第1页1 2 3