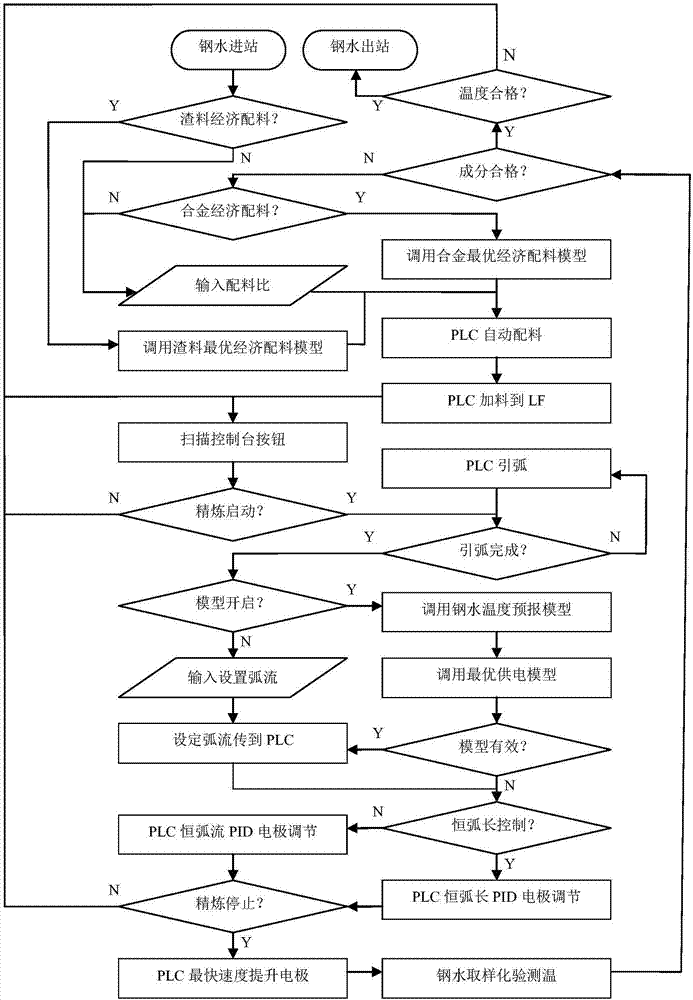
本发明涉及冶金炉外精炼控制
技术领域:
,尤其涉及一种lf精炼炉最优经济配料和智能控制模型。
背景技术:
:lf钢包精炼炉用于对转炉初炼钢水进行二次精炼处理。即:钢水加热、升温、成份调整、脱硫、去气、去除夹杂、均匀钢水成份和温度。经过钢包精炼处理,可获得品质更高的钢水,品种转换机动灵活,成份、温度控制更为准确,并且作为转炉与板坯连铸机之间的缓冲环节,均衡协调转炉与连铸机的生产节奏,解除了连铸生产的后顾之忧,是实现多包连浇高效生产的关键设备。lf钢包精炼炉自动控制系统的控制品质直接影响最终钢水产品质量,特别是电极升降调节模式,不仅决定钢水的加热、升温品质,还关系到吨钢电耗。目前已有的lf炉控制系统只针对钢水的加热、升温加以考虑,仅满足工艺要求为目标,而忽略了对lf系统电耗的综合考虑。现有的lf钢包精炼炉钢水测温都是断电离线测温模式,测温等待期间散热损失不可避免,从而额外增加了电耗,而且炉前测温操作人员的劳动强度相应增大。现有lf钢包精炼炉配料(渣料和铁合金及喂丝)都采用离线计算模式人工计算渣料和铁合金及喂丝配比,不仅繁琐,而且实时性滞后,也会间接导致钢水品质降低。技术实现要素:针对lf钢包精炼炉的控制缺陷,发明了一种lf精炼炉最优经济配料和智能控制模型,克服现有lf控制技术的缺陷和不足。结合lf炉的特点,推导出lf炉最优经济配料数学模型和钢水温度预报数学模型及以电耗最低为目标的电极智能调节数学模型,通过编制vbs脚本程序嵌入到wincc,即可实现lf钢包精炼炉最优经济配料和智能控制。用于在线预报钢水温度、自动获得最优经济配料、在满足工艺要求的条件下使吨钢电耗达到最低。为了达到上述目的,本发明采用以下技术方案实现:一种lf精炼炉最优经济配料和智能控制模型,包括lf炉最优经济配料模型和lf炉钢水温度预报和最优供电模型;一、所述lf炉最优经济配料模型过程如下:首先,将公式中用到的参数进行说明:lf炉渣料化学成分和价格及加入量见表1;其中渣料化学成分和价格为已知量,加入量为待求未知量;表1渣料化学成分和价格lf炉合金(含喂丝)化学成分和价格及加入量见表2;其中合金(含喂丝)化学成分和价格为已知量,加入量为待求未知量;表2合金化学成分和价格注:合金中含喂丝;合金中化学元素收得率见表3;收得率为已知量;表3合金中化学元素收得率成分1成分2...成分m收得率η1η2...ηm目标钢水化学成分见表4;化学成分上下限为已知量;表4目标钢水标准和初始钢水化学成分钢包几何参数:d—钢包底部外径,md—钢包底部内径,mh--钢包外部高度,mh—钢包内部深度,mθ—钢包侧面半锥角,弧度;1.1模型简化(1)由转炉来的钢包,钢包中的钢渣渣层厚度忽略不计;(2)合金中元素除标明的收得率外,其它元素均全部进入钢相中;1.2建模1.2.1约束条件1.2.1.1熔渣碱度(二元碱度)约束为保障炉渣流动性,熔渣碱度(二元碱度cao/sio2)应该控制在一定范围内;式中:rh、rl--熔渣碱度(二元碱度)上、下限;1.2.1.2熔渣中mgo含量约束熔渣中合适的mgo含量是提高钢包炉衬耐火材料寿命的保证;式中:am,h、am,l--渣中mgo含量上、下限;1.2.1.3熔渣层厚度约束钢水重量mg对应的渣线直径dz则mg--钢水质量,kgρg--钢水密度,kg/m3ρg=7138由上式解出dz为保证埋弧操作,熔渣线上部渣层厚度不低于hz式中ρb,j--j=1,2,3,4分别为cao、sio2、mgo、al2o3密度,kg/m3ρa,1=3350,ρa,2=2600,ρa,3=3580,ρa,4=3960;1.2.1.4钢水合金元素化学成分约束lf目标钢水成分需满足国标要求;式中:ch,j、cl,j--合金元素化学成分j国家标准上、下限;1.2.2目标函数总配料成本最低1.3模型求解式(1)~(5)可以分解为2个独立的线性规划问题分别求解;1.3.1渣料最优经济配料模型s.t.xa,i≥0(i=1,2,...,k)变量个数k,约束条件个数5,用两阶段单纯形法可求出最优解;1.3.2合金最优经济配料模型s.t.xb,i≥0(i=1,2,...,n)变量个数n,约束条件个数2m,用两阶段单纯形法可求出最优解;目标钢水化学成分见表4;化学成分上下限为已知量;二、所述lf炉钢水温度预报和最优供电模型过程如下:根据lf系统能量平衡,确定钢水当前温度与实时输入的有功电功率的函数关系;2.1模型简化(1)电极形成电弧无电抗,仅等效为电阻;(2)三相平衡,即变压器负载侧abc三相内阻、内抗相同、空载电压相同,abc三相短网内阻、内抗相同;(3)冶炼时间仅从电极通电开始计算,中间断电(取样、测温、加料)不计入冶炼时间,忽略断电期间的lf炉热损;(4)忽略熔渣化学反应生成热;(5)忽略合金(含喂丝)熔化潜热;2.2供电策略(1)输入lf炉内的三相电功率平衡(相等);(2)满足供电制度条件下,总电耗最低;rb、xb为变压器负载侧单相电阻(ω)、电抗(ω),随变压器电压档位变化,rd、xd为lf炉单相短网电阻(ω)、电抗(ω),r为电弧等效电阻(ω),i为单相有效电流(a),ub为变压器负载侧空载电压(v);ub与lf当前温度t有关,即不同的升温阶段选择不同的电压等级;上式中:r0=rb(ub)+rdx0=xb(ub)+xd2.3建模2.3.1钢水温度预报模型2.3.1.1能量收入(1)输入电能q1,jq1=ni2rdt(7)式中:n—电极根数,交流lf炉,n=3,直流lf炉n=1i—负载侧单相电流,ar—单相电弧等效电阻,ωdt—微元时间,s(2)电极燃烧放热q2,jq2=n[-δhc(t)]dcdt(8)式中:dc—单根电极平均消耗速度,kg/sδhc(t)--石墨燃烧生成co的热效应,j/kgδhc(t)为温度t(k)的函数;ac=-9.15×106,bc=-310.8,cc=0.3817,dc=-9.642×1072.3.1.2能量支出(1)钢水升温显热q1’,j式中:cg--钢水平均比热,j/(kgk)cg=1.046×106dt—钢水微升温,k(2)渣料升温显热q2’,j式中:cz(t)—熔渣比热,j/(kgk)cz(t)为温度t(k)的函数;aa,1=886.0,ba,1=0.0807,ca,1=-1.241×107aa,2=732.0,ba,2=0.6468,ca,2=-1.133×107aa,3=1224.5,ba,2=0.0785,ca,3=-2.860×107aa,4=1125.2,ba,2=0.1255,ca,3=-3.475×107(3)lf炉衬耐火材料升温显热q3’,jq3'=(ccmc+cdmd)dt(11)式中:mc—钢包衬侧面耐火材料质量,kgcc—钢包衬侧面耐火材料比热,j/(kgk)md—钢包衬底部耐火材料质量,kgcd—钢包衬底部耐火材料比热,j/(kgk)ρc—钢包衬侧面耐火材料密度,kg/m3ρd—钢包衬底部耐火材料密度,kg/m3(4)氩气带走显热q4’,jq4'=farcar(t-t0)dt(12)式中:ca—氩气比热,j/(m3k)car=928.1far—氩气流量,m3/st0—环境温度,k(5)冷却水带走显热q5’,jq5'=fh2och2o(th2o1-th2o0)dt(13)式中:ch2o—水比热,j/(kgk)ch2o=4962fh2o—lf炉(炉盖)冷却水流量,kg/sth2o0—冷却水入口温度,kth2o1—冷却水出口温度,k(6)lf炉表面辐射和对流热损q6’,jq6'=qrdt(14)式中:qr—单位时间表面辐射和对流热损,wqr通常为一常数,通过历史数据统计得到;3.2.3能量平衡lf炉能量收入=lf炉能量支出lf炉能量收入=输入电能+电极燃烧放热lf炉能量支出=钢水升温显热+渣料升温显热+lf炉衬耐火材料升温显热+氩气带走显热+冷却水带走显热+lf表面辐射和对流热损式(7)~(14)代入式(15):fh2och2o(th2o1-th2o0)dt+qrdt整理上式得到:式中:q(t)=nδhc(t)dc+farcar(t-t0)+fh2och2o(th2o1-th2o0)+qrq(t)为各项与时间无关的热损失速度(热收入为负)之和,是温度t的函数;c(t)为各项与质量有关的热容之和,是温度t的函数;式(16)为钢水升温速度与供电功率和钢水温度的函数关系式;如果考虑三相不平衡(变压器内阻抗不平衡、短网阻抗不平衡、电流不平衡),根据式(16)的意义,并用式(6)的r代入得到:式中:tt—t时刻的钢水温度,ktt+δt—t+δt时刻的钢水温度,k式(17)即为钢水温度预报数学模型,只要给定初始钢水温度,经过迭代计算即可达到当前时刻钢水温度;其中ii为实测得到的各单相电流值,r0,i、x0,i分别为变压器内阻与短网电阻之和、变压器内抗与短网电抗之和;2.3.2最优供电模型根据供电策略,输入lf炉三相功率相同,lf炉总电耗为:式(16)代入上式中,并用式(6)的i代入得到:式中:t1—加热开始温度,kt2—加热结束温度,k当时,式(18)取得极值;求出极值点等效电阻r*:式(19)代入式(6)中,求出极值点单相电流i*:在极值点:由式(21)可知,在极值点处,说明式(18)恒存在极小值;式(20)即为lf炉最优供电模型,最佳设定电流是钢水温度t单调函数,按照设定的最佳电流冶炼,可以得到最低的电耗;但lf精炼过程必须按照供电制度u(t)满足工艺升温要求,即钢水升温速度不低于工艺设定值;由式(16)可知,钢水升温速度要求满足:式中:δ(t)—由精炼工艺确定的升温速度,不同温度区间升温速度不同,k/simin—满足精炼工艺要求的单相最小电流,a式(6)中的r代入上式,解出关于imin的方程:式中:为单相电弧最小功率;由式(20)、(22),得到lf炉最佳设定电流为:i0=min[imax,max(i*,imin)]i0=min(imax,max(i*,imin))其中:imax--为变压器相应电压ub(t)下的额定电流,a功率因数:式(19)代入上式中,求出最优功率因数:上述lf炉最优供电模型是针对三相交流lf炉导出的,导出的结果也适用于直流lf炉,用于直流lf炉时,只需令n=1(电极根数),并且r0=3rb+rd,x0=3xb;2.4控制策略电弧电压与电弧长度关系:u=α+βl(24)式中:u—电弧电压,vα—阴极区和阳极区电压降之和,vβ—弧柱中的电位梯度,v/ml—电弧长度,m由于电弧等效电阻:r带入式(6),得到:由式(24)和式(25),得到:由式(26)可见,在特定电压下,电弧长度l只是单相电流i的单调函数,最佳电流i0对应的电弧长度l(i0);电极的升降运动是通过比例阀控制液压传动系统实现的,比例阀通过控制液压介质的流量改变电极升降速度,与电极升降直接关联的被控参数是电弧长度,而电弧电压又与电弧长度成线性关系,因而通过电极升降即可直接控制电弧电压,给定电流最佳设定值i0,最佳电弧电压设定值u0由式(25)得到;采用pid控制电极升降,以u0作为被控参数,通过适当选取比例值、积分时间、微分时间,可以达到快速达到稳态。与现有技术相比,本发明的有益效果是:1、lf渣料、铁合金(含喂丝)配料在满足工艺要求最终钢水质量的前提下,达到最经济配料;2、实现lf炉钢水在线温度预报,免除人工测温带来测温元件消耗和额外劳动强度;3、在供电制度给定的条件下,按照最优供电智能模型得到的最佳电流进行电极控制,可以获得最低吨钢电耗。附图说明图1为本发明的交流lf炉的单相等效电路图;图2为本发明的plc控制系统上位机vbs脚本语言编程逻辑程序框图。具体实施方式以下结合附图对本发明提供的具体实施方式进行详细说明。一种lf精炼炉最优经济配料和智能控制模型,包括lf炉最优经济配料模型和lf炉钢水温度预报和最优供电模型;一、所述lf炉最优经济配料模型过程如下:首先,将公式中用到的参数进行说明:lf炉渣料化学成分和价格及加入量见表1;其中渣料化学成分和价格为已知量,加入量为待求未知量;表1渣料化学成分和价格lf炉合金(含喂丝)化学成分和价格及加入量见表2;其中合金(含喂丝)化学成分和价格为已知量,加入量为待求未知量;表2合金化学成分和价格注:合金中含喂丝;合金中化学元素收得率见表3;收得率为已知量;表3合金中化学元素收得率成分1成分2...成分m收得率η1η2...ηm目标钢水化学成分见表4;化学成分上下限为已知量;表4目标钢水标准和初始钢水化学成分钢包几何参数:d—钢包底部外径,md—钢包底部内径,mh--钢包外部高度,mh—钢包内部深度,mθ—钢包侧面半锥角,弧度;1.1模型简化(1)由转炉来的钢包,钢包中的钢渣渣层厚度忽略不计;(2)合金中元素除标明的收得率外,其它元素均全部进入钢相中;1.2建模1.2.1约束条件1.2.1.1熔渣碱度(二元碱度)约束为保障炉渣流动性,熔渣碱度(二元碱度cao/sio2)应该控制在一定范围内;式中:rh、rl--熔渣碱度(二元碱度)上、下限;1.2.1.2熔渣中mgo含量约束熔渣中合适的mgo含量是提高钢包炉衬耐火材料寿命的保证;式中:am,h、am,l--渣中mgo含量上、下限;1.2.1.3熔渣层厚度约束钢水重量mg对应的渣线直径dz则mg--钢水质量,kgρg--钢水密度,kg/m3ρg=7138由上式解出dz为保证埋弧操作,熔渣线上部渣层厚度不低于hz式中ρb,j--j=1,2,3,4分别为cao、sio2、mgo、al2o3密度,kg/m3ρa,1=3350,ρa,2=2600,ρa,3=3580,ρa,4=3960;1.2.1.4钢水合金元素化学成分约束lf目标钢水成分需满足国标要求;式中:ch,j、cl,j--合金元素化学成分j国家标准上、下限;1.2.2目标函数总配料成本最低1.3模型求解式(1)~(5)可以分解为2个独立的线性规划问题分别求解;1.3.1渣料最优经济配料模型s.t.xa,i≥0(i=1,2,...,k)变量个数k,约束条件个数5,用两阶段单纯形法可求出最优解;1.3.2合金最优经济配料模型s.t.xb,i≥0(i=1,2,...,n)变量个数n,约束条件个数2m,用两阶段单纯形法可求出最优解;目标钢水化学成分见表4;化学成分上下限为已知量;二、所述lf炉钢水温度预报和最优供电模型过程如下:根据lf系统能量平衡,确定钢水当前温度与实时输入的有功电功率的函数关系;lf炉冶炼不同钢种,有不同的供电制度,即在某一温度区间,送电电压等级不同,在给定的供电制度和最低升温速度下,钢水升温速度对冶炼电耗影响很大,为了减少热损失项(lf炉体表面散热、冷却水带走的热、氩气搅拌带走的热),应尽可能加大电流,缩短冶炼时间。但加大电流的同时,lf炉短网和变压器电能损耗急剧增加(电能损耗与电流平方成正比),因此存在一个使得总电耗最低的平衡点,这个平衡点是动态的,随着供电电压等级和钢水温度而改变,在平衡点的电流即为最佳电流。lf最优供电模型就是要找到最佳电流设定值。2.1模型简化(1)电极形成电弧无电抗,仅等效为电阻;(2)三相平衡,即变压器负载侧abc三相内阻、内抗相同、空载电压相同,abc三相短网内阻、内抗相同;(3)冶炼时间仅从电极通电开始计算,中间断电(取样、测温、加料)不计入冶炼时间,忽略断电期间的lf炉热损;(4)忽略熔渣化学反应生成热;(5)忽略合金(含喂丝)熔化潜热;2.2供电策略(1)输入lf炉内的三相电功率平衡(相等);(2)满足供电制度条件下,总电耗最低;如图1所示,为交流lf炉的单相等效电路图;图1中,rb、xb为变压器负载侧单相电阻(ω)、电抗(ω),随变压器电压档位变化,rd、xd为lf炉单相短网电阻(ω)、电抗(ω),r为电弧等效电阻(ω),i为单相有效电流(a),ub为变压器负载侧空载电压(v);ub与lf当前温度t有关,即不同的升温阶段选择不同的电压等级;上式中:r0=rb(ub)+rdx0=xb(ub)+xd2.3建模2.3.1钢水温度预报模型2.3.1.1能量收入(1)输入电能q1,jq1=ni2rdt(7)式中:n—电极根数,交流lf炉,n=3,直流lf炉n=1i—负载侧单相电流,ar—单相电弧等效电阻,ωdt—微元时间,s(2)电极燃烧放热q2,jq2=n[-δhc(t)]dcdt(8)式中:dc—单根电极平均消耗速度,kg/sδhc(t)--石墨燃烧生成co的热效应,j/kgδhc(t)为温度t(k)的函数;ac=-9.15×106,bc=-310.8,cc=0.3817,dc=-9.642×1072.3.1.2能量支出(1)钢水升温显热q1’,j式中:cg--钢水平均比热,j/(kgk)cg=1.046×106dt—钢水微升温,k(2)渣料升温显热q2’,j式中:cz(t)—熔渣比热,j/(kgk)cz(t)为温度t(k)的函数;aa,1=886.0,ba,1=0.0807,ca,1=-1.241×107aa,2=732.0,ba,2=0.6468,ca,2=-1.133×107aa,3=1224.5,ba,2=0.0785,ca,3=-2.860×107aa,4=1125.2,ba,2=0.1255,ca,3=-3.475×107(3)lf炉衬耐火材料升温显热q3’,jq3'=(ccmc+cdmd)dt(11)式中:mc—钢包衬侧面耐火材料质量,kgcc—钢包衬侧面耐火材料比热,j/(kgk)md—钢包衬底部耐火材料质量,kgcd—钢包衬底部耐火材料比热,j/(kgk)ρc—钢包衬侧面耐火材料密度,kg/m3ρd—钢包衬底部耐火材料密度,kg/m3(4)氩气带走显热q4’,jq4'=farcar(t-t0)dt(12)式中:ca—氩气比热,j/(m3k)car=928.1far—氩气流量,m3/st0—环境温度,k(5)冷却水带走显热q5’,jq5'=fh2och2o(th2o1-th2o0)dt(13)式中:ch2o—水比热,j/(kgk)ch2o=4962fh2o—lf炉(炉盖)冷却水流量,kg/sth2o0—冷却水入口温度,kth2o1—冷却水出口温度,k(6)lf炉表面辐射和对流热损q6’,jq6'=qrdt(14)式中:qr—单位时间表面辐射和对流热损,wqr通常为一常数,通过历史数据统计得到;3.2.3能量平衡lf炉能量收入=lf炉能量支出lf炉能量收入=输入电能+电极燃烧放热lf炉能量支出=钢水升温显热+渣料升温显热+lf炉衬耐火材料升温显热+氩气带走显热+冷却水带走显热+lf表面辐射和对流热损式(7)~(14)代入式(15):fh2och2o(th2o1-th2o0)dt+qrdt整理上式得到:式中:q(t)=nδhc(t)dc+farcar(t-t0)+fh2och2o(th2o1-th2o0)+qrq(t)为各项与时间无关的热损失速度(热收入为负)之和,是温度t的函数;c(t)为各项与质量有关的热容之和,是温度t的函数;式(16)为钢水升温速度与供电功率和钢水温度的函数关系式;如果考虑三相不平衡(变压器内阻抗不平衡、短网阻抗不平衡、电流不平衡),根据式(16)的意义,并用式(6)的r代入得到:式中:tt—t时刻的钢水温度,ktt+δt—t+δt时刻的钢水温度,k式(17)即为钢水温度预报数学模型,只要给定初始钢水温度,经过迭代计算即可达到当前时刻钢水温度;其中ii为实测得到的各单相电流值,r0,i、x0,i分别为变压器内阻与短网电阻之和、变压器内抗与短网电抗之和;2.3.2最优供电模型根据供电策略,输入lf炉三相功率相同,lf炉总电耗为:式(16)代入上式中,并用式(6)的i代入得到:式中:t1—加热开始温度,kt2—加热结束温度,k当时,式(18)取得极值;求出极值点等效电阻r*:式(19)代入式(6)中,求出极值点单相电流i*:在极值点:由式(21)可知,在极值点处,说明式(18)恒存在极小值;式(20)即为lf炉最优供电模型,最佳设定电流是钢水温度t单调函数,按照设定的最佳电流冶炼,可以得到最低的电耗;但lf精炼过程必须按照供电制度u(t)满足工艺升温要求,即钢水升温速度不低于工艺设定值;由式(16)可知,钢水升温速度要求满足:式中:δ(t)—由精炼工艺确定的升温速度,不同温度区间升温速度不同,k/simin—满足精炼工艺要求的单相最小电流,a式(6)中的r代入上式,解出关于imin的方程:式中:为单相电弧最小功率;由式(20)、(22),得到lf炉最佳设定电流为:i0=min[imax,max(i*,imin)]i0=min(imax,max(i*,imin))其中:imax--为变压器相应电压ub(t)下的额定电流,a功率因数:式(19)代入上式中,求出最优功率因数:上述lf炉最优供电模型是针对三相交流lf炉导出的,导出的结果也适用于直流lf炉,用于直流lf炉时,只需令n=1(电极根数),并且r0=3rb+rd,x0=3xb;2.4控制策略电弧电压与电弧长度关系:u=α+βl(24)式中:u—电弧电压,vα—阴极区和阳极区电压降之和,vβ—弧柱中的电位梯度,v/ml—电弧长度,m由于电弧等效电阻:r带入式(6),得到:由式(24)和式(25),得到:由式(26)可见,在特定电压下,电弧长度l只是单相电流i的单调函数,最佳电流i0对应的电弧长度l(i0);电极的升降运动是通过比例阀控制液压传动系统实现的,比例阀通过控制液压介质的流量改变电极升降速度,与电极升降直接关联的被控参数是电弧长度,而电弧电压又与电弧长度成线性关系,因而通过电极升降即可直接控制电弧电压,给定电流最佳设定值i0,最佳电弧电压设定值u0由式(25)得到;采用pid控制电极升降,以u0作为被控参数,通过适当选取比例值、积分时间、微分时间,可以达到快速达到稳态。本发明所述的模型方法利用plc控制系统实现,具体实现方法如下:一、将现场仪表检测到各参量信号送至plc,并经由tcp/ip网络总线送至上位计算机监控系统,钢水重量、化学成分通过通过tcp/ip网络总线传送至上位计算机系统。仪表系统涉及的检测参量有:(1)加料系统称量仓重量;(2)氩气系统流量;(3)设备冷却水系统流量、进出口温度;(4)钢水检测温度;(5)变压器二次侧电压、电流。仪表系统涉及的控制参量有:电极升降调节比例阀输信号出(-10~+10v)。电气系统涉及控制参量有:(1)变压器二次侧有载调压开关输出信号(脉冲);(2)渣料仓、合金仓振动给料器输出信号(开关量);(3)渣料称量仓、合金称量仓振料器输出信号(开关量);(4)下料和上料皮带运行输出信号(开关量)。二、上位机用vbs脚本语言编程,逻辑程序框图见附图2,采用本发明列出的各数学模型算法,通过时间周期(10秒)事件调用脚本语言。本发明的优选实现方式是选用simatic的plc,上位机平台软件wincc,下位机平台软件step7。电极调节模式提供恒弧长或恒电流可选模式,建议实施过程采用恒弧长控制模式,用pid算法实现电极跟随调节,pid参数现场整定。上位机设置一pid参数整定画面,设置pid参数时以便实时观察pid整定后的效果。上位机设置一lf炉自动配料画面,内嵌一按钮单击事件,当按下该按钮时,调用最优配料程序,得到当前最佳配比,按确认按钮后,自动按照最佳配比加料到指定的lf炉内(预先储存在缓冲仓)。采用一个独立的plc可编程控制器组成电极升降自动调节系统,通过信号变换电路及输入模块采集系统各相电弧电压、电弧电流、变压器电压等级以及其它相关的给定信号,先将弧流、弧压、变压器阻抗、短网阻抗进行运算处理,并将运算结果与给定值进行比较,将输出信号送至液压系统电极升降比例阀,实现电极位置自动调节,从而控制输入到炉内的功率,按照最佳功率曲线运行,满足精炼工艺要求。在电极自动调节过程中,随时可以手动干预。采用另一个独立的plc可编程控制器组成自动加料系统,通过信号变换电路及输入模块采集系统各振动给料器、各称量仓振料器、下料和上料皮带开关量状态信号,从上位机获取最佳经济配料各料仓的加料量,plc下位程序按顺序称量各料仓渣料和铁合金(不同称量仓可以同时称量操作),同时在上位机显示各料仓称量进度。一旦遇有料仓下料堵料情况(一定时间内不下料),自动标记堵料,进行后续料仓配料,配料完毕plc把实际配料量传送到上位机显示和记录。以上实施例在以本发明技术方案为前提下进行实施,给出了详细的实施方式和具体的操作过程,但本发明的保护范围不限于上述的实施例。上述实施例中所用方法如无特别说明均为常规方法。当前第1页12