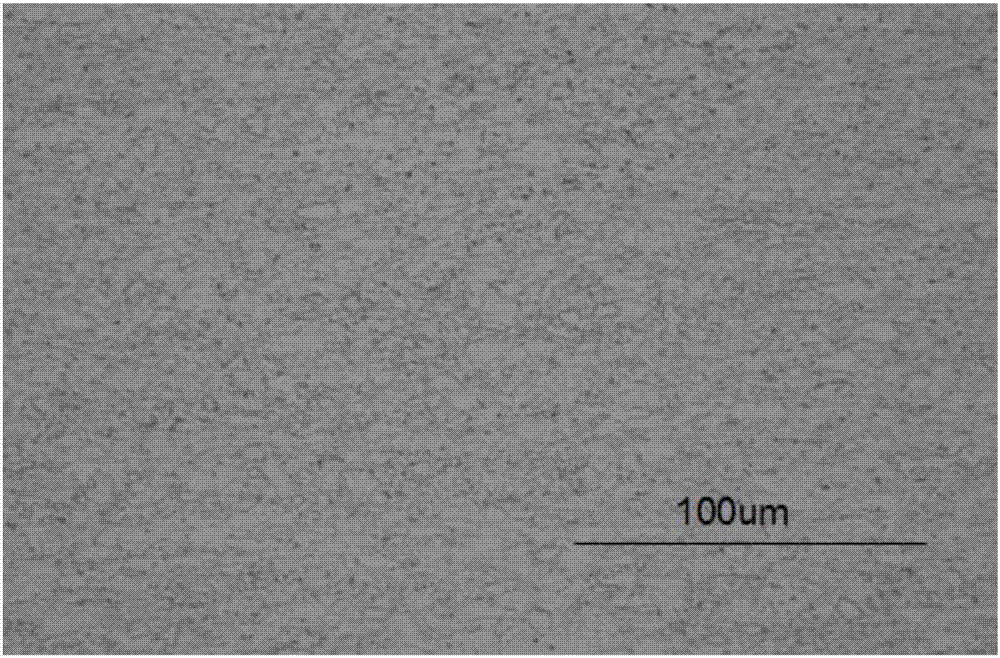
本发明专利涉及薄规格超高强度热轧汽车用钢及其制造方法,具体涉及一种屈服强度在700mpa以上的1.5~3.0mm薄规格高强度热轧钢板及其制造方法。
背景技术:
:随着我国环保、能源形势日趋严峻,政府对新能源汽车的支持力度在不断加大。电动汽车与燃油汽车最大的区别就在于车体骨架的构成。目前,采用具有高强度、高韧性、高成形精度等优点的高强度钢板的应用正成为实现汽车轻量化的重要途径。通过提高材料的强度、减少钢板的厚度,可实现车辆自重和能耗的降低。当前各大钢铁企业对于屈服强度700mpa级别的热轧高强钢的主要生产厚度为3~12mm,对于小于3mm的产品少之又少,因为这对产品的成分设计、生产的控制要求高,同时要求产品具有高的强度,还要具有良好的焊接性能、成型性能及冲击韧性。技术实现要素:本发明提供了一种厚度1.5~3.0mm屈服强度大于700mpa的热轧汽车用钢及其制造方法,在保证组织性有要求的同时,可实现稳定的工业化生产。本发明制造的厚度1.5~3.0mm屈服强度大于700mpa的热轧汽车用钢组织为铁素体+粒状贝氏体组织+岛状马氏体,晶粒度达到12.5,屈强比0.85~0.95,冷成形性能优良,适合新能源汽车骨架底盘等结构件冲压或辊压工艺要求。本发明提供的技术方案为:一种厚度1.5~3.0mm屈服强度大于700mpa的热轧汽车用钢,所含化学成分及重量百分比为:c0.02~0.06%、mn1.20~2.00%、al0.010~0.050%、p≤0.01%、s≤0.05%、nb0.01~0.05%、ti0.05~0.12%,v0.05~0.20%,mo0.12~0.20%,其余为fe和不可避免杂质。进一步地,所含化学成分及重量百分比优选为:c0.044~0.06%、mn1.5~1.8%、al0.025~0.04%、p≤0.005%、s≤0.01%、nb0.015~0.045%、ti0.06~0.085%,v0.07~0.18%,mo0.14~0.18%,其余为fe和不可避免杂质。更进一步地,所含化学成分及重量百分比优选为:c0.044%、mn1.60%、als0.034%、p0.003%、s0.006%、nb0.042%、ti0.07%、v0.09%、mo0.17%,其余为fe和不可避免杂质。本发明还提供了厚度1.5~3.0mm屈服强度大于700mpa的热轧汽车用钢的制造方法,包括以下步骤:铁水预处理→转炉冶炼→合金微调站→lf精炼→rh精炼→连铸→铸坯缓冷→热连轧→层流冷却→卷取;高合金成分体系的铸坯具有高裂纹敏感性特点,为避免铸坯在脆性区产生内部裂纹,进一步保证铸坯内部质量,对铸坯进行堆垛或者进保温坑缓冷处理,缓冷保温温度不得低于600℃,缓冷处理时间为72~80小时。进一步地,在连铸步骤中,中包温度控制在目标液相线温度以上15℃~40℃,拉速为1.0~1.5m/min,以保证液态钢中溶质分配均匀,避免产生铸态偏析;浇铸时投用动态轻压下,同时使用电磁辊搅拌,以保证溶质元素分配均匀减少铸坯内部偏析、疏松等内部缺陷;同时利用电磁辊搅拌使得杂质上浮以获得好的铸坯内部质量。进一步地,在热连轧步骤中,为了保证合金元素充分固溶,加热炉出炉温度控制在1230℃~1270℃,粗轧采用3+3道次轧制,在2250mm热连轧机上进行精轧,精轧入口温度为1030~1050℃,为了实现厚度1.5~3.0mm屈服强度大于700mpa的热轧汽车用钢的稳定轧制,终轧温度控制在880℃~920℃。进一步地,以保证材料高强度、高韧性匹配,在层流冷却步骤中,采用前段快速冷却方式,冷却速度大于30℃/s,一方面可以减少nb、ti元素在高温阶段的析出,促进nb、ti元素在低温阶段的析出,增加析出强化效果;同时使析出的二相粒子尺寸更加细小、分布更弥散。进一步地,卷取温度控制在580℃~620℃,此温度区间为nb、ti元素的最佳析出温度。根据上述制造方法制备得到的热轧汽车用钢,其组织为铁素体+粒状贝氏体组织+岛状马氏体。针对新能源汽车轻量化的需求,本发明采用低c-mn-mo-ti-nb-v合金系统设计和合适的tmcp工艺,成功开发了厚度1.5~3.0mm屈服强度大于700mpa超高强汽车板,其具有优异的冷弯性能、焊接性能和强塑性匹配,同时具有良好的工业生产适应性。在合金元素的设计中,为了保证材料高强度和高韧性,同时考虑到其焊接性能和成形性能,c含量控制在0.02%~0.06%;考虑到汽车用材对表面质量的严格要求,钢中不添加si元素;mn元素可通过固溶强化提高钢的强度,同时可促进碳氮化物析出相在加热时候的溶解,抑制析出相在轧制时候的析出,有利于保持较多的析出元素于轧后的冷却过程中在铁素体中析出,加强了析出强化,此外mn还可扩大奥氏体相区,降低过冷奥氏体相的转变温度,有利于相变组织的细化;nb、ti、v微合金化的主要作用是在钢中形成碳氮化合物,利用在不同条件下产生的溶解和析出机理起到细化晶粒和析出强化作用,同时也可以改善材料的焊接性能;mo是奥氏体稳定元素,同时细化晶粒并抑制珠光体组织和大的渗碳体析出,同时还能够提高ti、nb在奥氏体的固溶度,使更多的微合金元素在较低温度形核析出;为了降低钢中夹杂物含量,以保证材料的焊接性能和韧性,严格控制p、s杂质元素的含量。本发明通过对以上元素及含量的控制,并在生产工艺过程中,控制rh精炼过程中的中包温度,在浇注过程中投入动态轻压下同时利用电磁辊搅拌以获得内部质量优良的铸坯;并采用堆垛或者保温坑缓冷处理,防止铸坯在脆性区产生内部裂纹;在热连轧步骤中精确控制加热炉出炉温度、精轧入口温度以及精轧终轧温度以实现1.5~3.0mm薄规格屈服强度大于700mpa的热轧汽车用钢的稳定轧制;终轧后采用冷却速度大于30℃的前段快速冷却方式,促进细小、弥散的二相粒子充分析出,保证了材料的高强度与高韧性;并将卷取温度控制在nb、ti元素最佳析出温度区间,进一步保证了材料的高强度与高韧性。本发明通过上述合金元素的含量的精确控制结合特定的工艺步骤,生产出了厚度1.5~3.0mm屈服强度大于700mpa的热轧汽车用钢,其屈服强度为700~760mpa,抗拉强度为760~870mpa,延伸率a80为18~21%,屈强比为0.85~0.95,冷弯性能良好,主要可用作轻量化车身底盘结构件。附图说明图1为实施例1公开的热轧汽车用钢的金相组织图;图2为实施例2公开的热轧汽车用钢的金相组织图。具体实施方式下面结合附图及实施例对本发明进行详细说明一种厚度1.5~3.0mm屈服强度大于700mpa的热轧汽车用钢,所含化学成分及重量百分比为:c0.02~0.06%、mn1.20~2.00%、als0.010~0.050%、p≤0.01%、s≤0.05%、nb0.01~0.05%、ti0.05~0.12%,v0.05~0.20%,mo0.12~0.20%,其余为fe和不可避免杂质。采用以下步骤制备得到:经铁水预处理→转炉冶炼→合金微调站→lf精炼→rh精炼→连铸→铸坯缓冷→热连轧→层流冷却→卷取;其中,在连铸步骤中,为了确保铸坯质量,浇铸时投用动态轻压下以减少铸坯内部偏析、疏松等内部缺陷;同时利用电磁辊搅拌使得杂质上浮以获得好的铸坯内部质量,中包温度控制在目标液相线温度以上15℃~40℃,拉速为1.0~1.5m/min;连铸板坯尺寸为230mm;所述铸坯缓冷包括对铸坯进行堆垛或者进保温坑缓冷处理,缓冷保温温度不得低于600℃,缓冷处理时间为72~80小时;在热连轧步骤中,加热炉出炉温度控制在1230℃~1270℃,粗轧采用3+3道次轧制,在2250mm热连轧机上进行精轧,精轧入口温度为1030~1050℃,终轧温度控制在880℃~920℃;在层流冷却步骤中,采用前段快速冷却方式,冷却速度大于30℃/s;卷取温度控制在580℃~620℃。下面以具体的实施例1~5对本发明进行详细说明,各实施例中热轧汽车用钢的化学成分及重量百分比见表1,制造工艺参数见表2,力学性能见表3。表1各实施例中热轧汽车用钢的化学成分及重量百分比cmnalspsnbtivmo实施例10.044%1.60%0.034%0.003%0.006%0.042%0.07%0.09%0.17%实施例20.054%1.73%0.028%0.004%0.008%0.028%0.08%0.15%0.15%实施例30.032%1.36%0.017%0.006%0.035%0.015%0.05%0.06%0.13%实施例40.057%1.82%0.04%0.007%0.010%0.034%0.10%0.12%0.18%实施例50.039%2.00%0.05%0.005%0.028%0.048%0.12%0.05%0.20%表2各实施例中热轧汽车用钢制造工艺参数表3各实施例中热轧汽车用钢力学性能参数由以上性能参数可以看出,本发明公开的热轧汽车用钢属于薄规格高强度热轧钢板,其厚度在1.5~3mm,屈服强度为700~760mpa,抗拉强度为760~870mpa,延伸率a80为18~21%,屈强比为0.85~0.95,冷弯性能良好,主要可用作轻量化车身底盘结构件。上述参照实施例对厚度1.5~3.0mm屈服强度大于700mpa的热轧汽车用钢及其制造方法进行的详细描述,是说明性的而不是限定性的,可按照所限定范围列举出若干个实施例,因此在不脱离本发明总体构思下的变化和修改,应属本发明的保护范围之内。当前第1页12