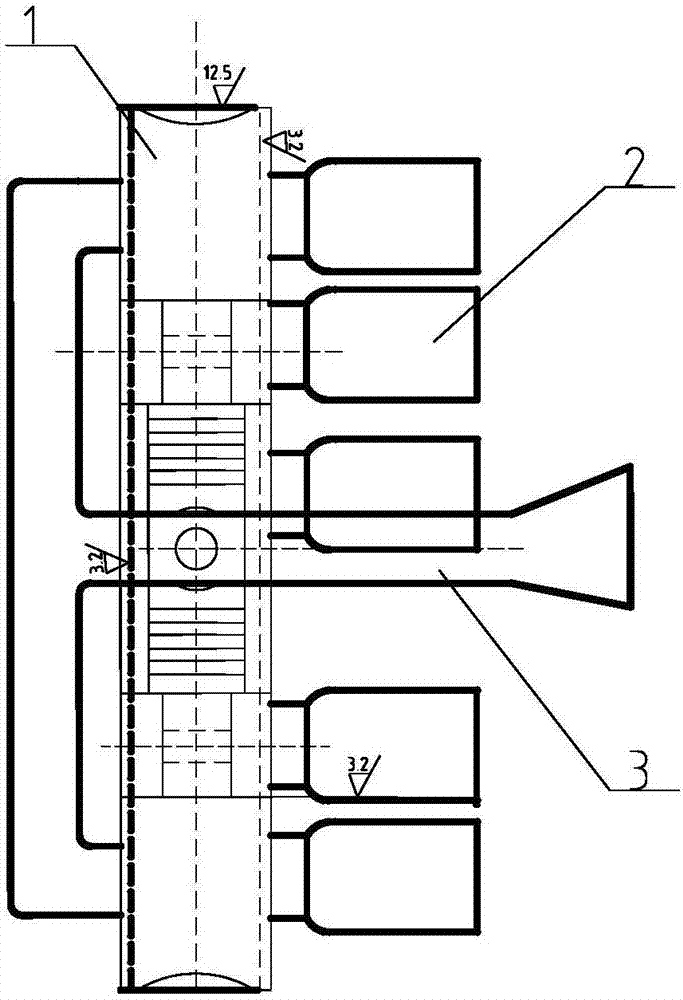
本发明涉及刹车盘生产
技术领域:
,尤其涉及一种高铁刹车盘的生产方法。
背景技术:
:高铁刹车盘对材质和铸造精度要求较高,目前普遍采用超纯铁素体不锈钢制作高铁刹车盘,但是典型的超纯铁素体不锈钢如本专利的zg00cr24mo1ninbw中铬含量为24%,而高铬钢中铬含量很高而含碳量很低,造成了在铸造过程中易产生氧化夹渣;又由于高铬钢在高温时极易和空气中的氧固溶形成皮下气孔,在铸造生产过程中由于流动性差容易产生冷隔;另外其高温时易氧化,铸件表面易产生氧化膜褶皱,氧化膜卷入内部易形成氧化夹杂物夹渣、气孔、缩松、冷隔等缺陷,导致工艺设计的难度加大,因而增大了铸造生产难度。高铁刹车盘如采用硅砂覆膜砂造型铸造,其铸造精度往往难以保证;为了保证铸造精度,有的生产企业采用硅溶胶精密铸造,所生产的高铁刹车盘表面光洁度和尺寸精度均较高,但是其生产成本较高,而且造成环境严重污染。技术实现要素:本发明提供了一种高铁刹车盘的生产方法,采用特殊成分组成的超纯铁素体不锈钢,经中频炉熔炼+lf-vod精炼后浇注,采用全自动铸造生产线,用宝珠覆膜砂进行造型和造芯,所生产的高铁刹车盘不仅各项性能指标符合要求,而且表面光洁度和尺寸精度能够达到硅溶胶精密铸造水平;为高铁刹车盘的生产开辟了新的途径。为了达到上述目的,本发明采用以下技术方案实现:一种高铁刹车盘的生产方法,包括如下步骤:1)钢水冶炼;浇铸高铁刹车盘用的钢水为超纯铁素体不锈钢,经中频炉熔炼+lf-vod精炼;具体过程如下:所述超纯铁素体不锈钢的化学成分按重量百分比为:c≤0.02%;si0.4%~1.0%;mn0.4%~1.0%;p≤0.02%;s≤0.02%;cr22%~24%;ni1.5%~2.0%;mo2.5%~3.5%;nb0.2%~0.4%;v0.5%~1.0%;w1.0%~3.0%;其余为铁及不可避免的杂质;中频炉炉前采用光谱仪进行钢水成分分析,出炉温度1640℃~1650℃;lf精炼过程用于对钢水进行加热升温及调整化学成分,加热时采用3根电极插入渣层中的埋弧加热方法,保持渣量为金属量的2%~8%;吹氩搅拌,加合金调整化学成分;vod精炼过程用于将在lf精炼炉中升温精炼后的钢水送入vod真空精炼设备真空罐中进行二次精炼,二次精炼后的钢水中o含量在10ppm以下、h含量在0.8ppm以下,s含量在0.01%以下;钢中夹杂物含量符合astm标准2.5级以上规定;2)采用全自动铸造生产线铸造高铁刹车盘;具体过程如下:采用70~140目宝珠覆膜砂进行造型和造芯,全自动铸造生产线由12工位36台热芯盒机组成,具有自动造型造芯、自动起模、自动合箱、自动浇注、自动打箱及砂处理功能;超纯铁素体不锈钢钢水出炉浇注温度为1570~1590℃;3)浇铸后的高铁刹车盘铸件经抛丸表面处理后再进行热处理及机加工,热处理过程为:正火处理950℃~970℃;回火处理570℃~590℃;热处理后的高铁刹车盘半成品热处理后进行产品检验,要求表面光洁度1.6~3.2级;尺寸精度5~6级;检验合格后的高铁刹车盘半成品经探伤、补焊及机加工,最终得到高铁刹车盘成品;4)成品检验;高铁刹车盘成品的性能指标如下:力学性能指标:抗拉强度≥600mpa;屈服强度≥430mpa;延伸率≥25%;硬度≥220hb;摩擦性能:滑动摩擦系数≤0.2;金相组织:铁素铁+少量奥氏体+柱状碳化物;以上检验合格的高铁刹车盘成品再经动平衡试验合格后,包装入库。所述中频炉熔炼时投加原材料时,cr铁采用金属cr和微碳cr,二者按1:1重量比添加。与现有技术相比,本发明的有益效果是:1)采用特殊成分组成超纯铁素体不锈钢,经中频炉熔炼+lf-vod精炼后浇注,精炼后的钢水中o含量在10ppm以下、h含量在0.8ppm以下,s含量在0.01%以下;钢中夹杂物含量符合astm标准2.5级以上规定;2)采用全自动铸造生产线,具有自动造型造芯、自动起模、自动合箱、自动浇注、自动打箱及砂处理功能;符合我国2025工业革命4.0实现工业自动化、数字化和智能化的总要求;3)采用宝珠覆膜砂作为铸造用砂,其为高效的环保型铸造用砂,强度高、耐火性能好,造型后免刷涂料,并能够明显提高铸件的表面光洁度及内在质量;与硅溶胶精密铸造相比,能够降低生产成本20%以上,生产周期缩短5天以上,砂的回收率可达98%以上;附图说明图1是本发明所述高铁刹车盘铸件浇注结构示意图一。图2是本发明所述高铁刹车盘铸件浇注结构示意图二。图3是本发明所述高铁刹车盘生产工艺流程图。具体实施方式下面结合附图对本发明的具体实施方式作进一步说明:一种高铁刹车盘的生产方法,包括如下步骤:1)钢水冶炼;浇铸高铁刹车盘用的钢水为超纯铁素体不锈钢,经中频炉熔炼+lf-vod精炼;具体过程如下:所述超纯铁素体不锈钢的化学成分按重量百分比为:c≤0.02%;si0.4%~1.0%;mn0.4%~1.0%;p≤0.02%;s≤0.02%;cr22%~24%;ni1.5%~2.0%;mo2.5%~3.5%;nb0.2%~0.4%;v0.5%~1.0%;w1.0%~3.0%;其余为铁及不可避免的杂质;中频炉炉前采用光谱仪进行钢水成分分析,出炉温度1640℃~1650℃;lf精炼过程用于对钢水进行加热升温及调整化学成分,加热时采用3根电极插入渣层中的埋弧加热方法,保持渣量为金属量的2%~8%;吹氩搅拌,加合金调整化学成分;vod精炼过程用于将在lf精炼炉中升温精炼后的钢水送入vod真空精炼设备真空罐中进行二次精炼,二次精炼后的钢水中o含量在10ppm以下、h含量在0.8ppm以下,s含量在0.01%以下;钢中夹杂物含量符合astm标准2.5级以上规定;2)采用全自动铸造生产线铸造高铁刹车盘;具体过程如下:采用70~140目宝珠覆膜砂进行造型和造芯,全自动铸造生产线由12工位36台热芯盒机组成,具有自动造型造芯、自动起模、自动合箱、自动浇注、自动打箱及砂处理功能;超纯铁素体不锈钢钢水出炉浇注温度为1570~1590℃;3)浇铸后的高铁刹车盘铸件经抛丸表面处理后再进行热处理及机加工,热处理过程为:正火处理950℃~970℃;回火处理570℃~590℃;热处理后的高铁刹车盘半成品热处理后进行产品检验,要求表面光洁度1.6~3.2级;尺寸精度5~6级;检验合格后的高铁刹车盘半成品经探伤、补焊及机加工,最终得到高铁刹车盘成品;4)成品检验;高铁刹车盘成品的性能指标如下:力学性能指标:抗拉强度≥600mpa;屈服强度≥430mpa;延伸率≥25%;硬度≥220hb;摩擦性能:滑动摩擦系数≤0.2;金相组织:铁素铁+少量奥氏体+柱状碳化物;以上检验合格的高铁刹车盘成品再经动平衡试验合格后,包装入库。所述中频炉熔炼时投加原材料时,cr铁采用金属cr和微碳cr,二者按1:1重量比添加。超纯铁素体不锈钢是近几年研制开发的新品种钢,是取代于镍铬不锈钢的新产品,由于超纯铁素体不锈钢的开发和应用,不但可节约大量的镍,有利于降低生产成本,且超纯铁素体不锈钢它是一种抗氧化、抗硫化、抗海水、抗氯离子、抗高温浓硫酸以及各种酸类非常理想的材料,其不但可以用于铸造也可以锻造、轧制各种工件和钢板;因此超纯铁素体不锈钢是制造高铁刹车盘的理想材料。其化学成分中由于加入nb和ti元素,能够固溶c和n,改变碳的形状,解决了轧制、铸造和焊接裂纹问题,也大大提高了材料耐晶间腐蚀性能,大大提高了产品加工切削性能。lf-vod精炼是将由中频电炉熔化钢水送入lf-vod精炼炉,采用双联法进行二次精炼的一种钢包精炼的方法。lf-vod精炼炉的钢水精炼过程是提高钢液纯净度、改善铸件内在质量的最重要的方法之一,具有精炼能力强,脱氧、脱氢、脱氮、脱硫、净化钢水效果好的特点,适于生产超低硫,超低氧钢种。lf-vod精炼过程主要分为两个过程:第一个过程是lf炉钢水精炼过程;lf精炼的最大优点是可以对钢水进行加热升温和控制调节化学成份,加热时采用3根电极插入渣层中即埋弧加热法,这种方法的辐射小,对炉衬有保护作用,而且加热效率高。lf精炼炉本身一般不具有真空设备。在精炼时,即在不抽真空的大气压下进行精炼时是靠还原性渣以及加热时石墨电极与渣中feo、mno、c等氧化物作用生成co气体,增加炉气的还原性气氛。氩气搅拌是lf精炼的最重要步骤,氩气搅拌有利于促进钢渣之间的化学反应,可以加速钢渣之间的物质传递,有利于钢液的脱氧、脱硫反应的进行。吹氩搅拌还可以去除非金属夹杂物,精确的调整复杂的化学组成;此外吹氩搅拌还可加速渣中氧化物的还原,可回收铬等有价值的合金元素。lf炉是靠白渣进行精炼的,白渣在lf炉内具有很强的还原性,吹氩气搅拌能提高lf炉内良好的还原气氛,通过良好的造渣功能,保持渣量为金属量的2~8%。可以有效的降低钢中氧、硫及夹杂物含量。第二个过程是vod真空精炼钢水过程:在lf精炼炉升温精炼后的钢水进入vod真空精炼设备真空罐中进行二次精炼,以获得纯净的钢水及较低h、o、n气体含量和低硫、低夹杂物的钢水。vod真空精炼主要靠顶吹氧枪、同时经钢包底部透气砖吹入氩气进行高强度搅拌,在钢液中氢、氮不断向氩气泡扩散,在氮气泡内形成一定的分压,氢和氮在氩气泡中的分压会随着气泡的上浮时受热体积膨胀,因而氢、氮的分压仍能保持较低的水平,故继续吸收氢和氮,最后随氩气泡溢出到钢液的表面而被去除。超纯铁素体不锈钢钢水经以上过程精炼后可将o含量降低至10ppm以下、h含量降低到0.8ppm以下;在精炼过程中由于脱氧作用良好,可吸收al2o3、sio2等杂质,有一定的变性作用,铸件夹杂物含量符合astm标准2.5级以上要求。宝珠砂的颗粒形状近似圆形,具有较高的强度和高的耐火度,其应用于铸造生产解决了精密铸造生产的严重污染问题,改善了铸造的生产环境,解决了一直困扰铸造工人的矽肺病问题,还大大的缩短了生产周期,减少了废品率,更重要的是降低了树脂和固化剂的加入量,相对精密铸造增加了透气性,减少了铸件的缺陷产生,也大大的降低了制造成本。宝珠砂是一种中性材料,适合于生产各种材质的铸件,也适合于生产高合金钢、不锈钢和镍基高温合金不锈钢及精密的超纯铁素体不锈钢刹车盘铸件。宝珠砂的应用也是国家13.5计划的重点研究和推广项目,是国家环保重点项目。宝珠砂是以铝钒土为原料经过锻烧、电溶造粒、分筛而制成的一种球状的铸造用砂,它是石英砂的替代品,也是高效的环保型铸造用砂,自宝珠砂问世以来得到广泛的应用,主要用于砂型铸造的面砂,静压线用砂,但其用于消失模和v法铸造虽然也取得了一些效果,如能够明显提高铸件的表面光洁度和内在质量,但目前还没有更多应用的资料报道。本发明采用宝珠覆膜砂代替精密铸造生产高铁刹车盘,不但大大的缩短了生产周期,也大大的减少了废品率,降低了生产成本,填补了国内宝珠覆膜砂代替了硅溶胶铸造的空白,是铸造领域的一种创新。宝珠覆膜砂生产各种铸件时的生产工艺简单,主要根据铸件的要求和铸件的大小来选择工艺方法和宝珠砂的粒度,采用热加工固化成型,免刷涂料,直接合箱浇注。宝珠覆膜砂生产铸件与石英砂相比较,其强度高,耐火度高达1900℃(石英砂只有1700℃),因此型砂在高温浇注时不易烧损和破碎,在回收砂中产生的灰粉很少,可使砂的回收量达到98%以上;又由于宝珠砂是呈圆形的,因而节约了大量的粘结剂和固化剂,大大的增加了砂型的透气性;由于宝珠砂具有以上优点,结合其在节约填加剂、砂回收、降低废品率、生产工艺简单等方面的优点,综合计算大约可降低生产成本20%。以下实施例在以本发明技术方案为前提下进行实施,给出了详细的实施方式和具体的操作过程,但本发明的保护范围不限于下述的实施例。下述实施例中所用方法如无特别说明均为常规方法。【实施例】本实施例中,所生产的高铁刹车盘铸件1结构如图1、图2所示,高铁刹车盘铸件重量约120kg,外形尺寸为(直径)x150(厚度)mm;铸造砂箱尺寸850x850x(200/400)mm、上箱高400mm,下箱高200mm。图中标号2为冒口,3为浇道,4为下箱设置的冷铁;采用自动化铸造生产线,造型速度10箱/小时.年产量2万吨。本实施例中高铁刹车盘所用超纯铁素体不锈钢的主要化学成分组成(其余为fe及不可避免的杂质)如下:由本发明所述方法生产的高铁刹车盘的力学性能检测结果如下表所示:采用宝珠覆膜砂铸造与精密铸造及酚醛树脂砂铸造所生产的刹车盘铸件各项指标比较如下表所示:铸造方法宝珠覆膜砂铸造精密铸造酚醛树脂砂铸造表面光洁度1.6-0.81.6-0,824尺寸精度5级5级12级每箱放置量1件1件1件砂铁比3:13:14:1砂回收率98%不可回收85%生产周期/天2109成品率100%96%98%返修率低低高加工余量337以上所述,仅为本发明较佳的具体实施方式,但本发明的保护范围并不局限于此,任何熟悉本
技术领域:
的技术人员在本发明揭露的技术范围内,根据本发明的技术方案及其发明构思加以等同替换或改变,都应涵盖在本发明的保护范围之内。当前第1页12