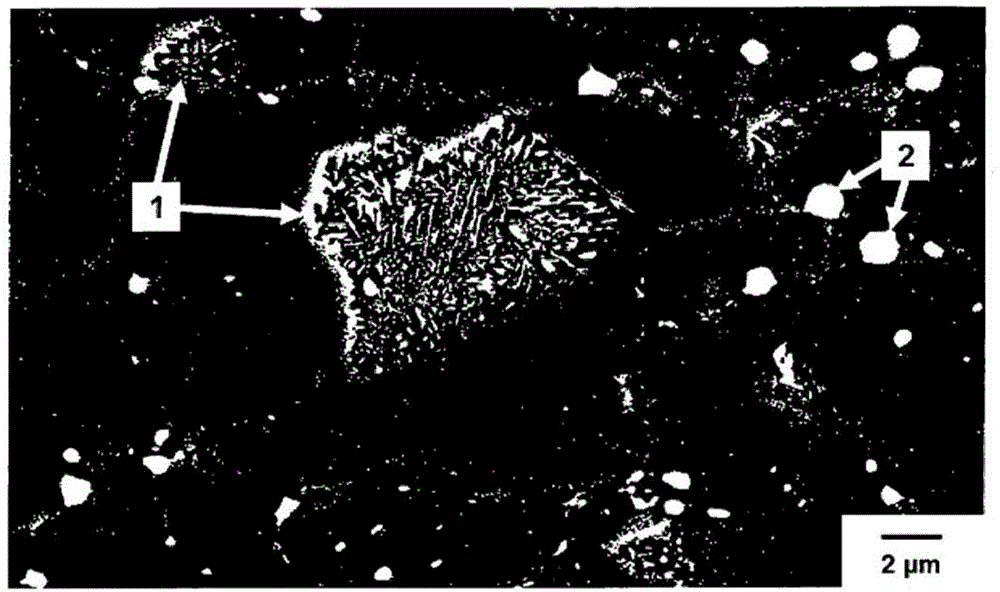
由于它们良好的强度性能和它们良好的耐腐蚀性以及对热和电流的传导性,二元铜/锡合金在机械工程和机动车辆结构以及大部分的电子和电气工程中均具有重要意义。这组材料具有高的耐磨料磨损性。而且,铜/锡合金确保了良好的滑动性能和高耐疲劳性,这使得它们对于发动机结构和机动车辆结构中以及一般的机械工程中的滑动元件具有极好的适用性。与二元铜/锡材料相比,铜-镍-锡合金具有改善的机械性能,例如硬度、拉伸强度和屈服点。在本文中,机械指数的增加经由cu-ni-sn合金的淬透性来实现。除了元素镍和锡的比率对于cu-ni-sn合金中存在自发亚稳线(spinodal)偏析所在的温度具有重要性外,沉淀工艺对于建立这组材料的性能是必不可少的。在文献中,特别是在cu-ni-sn合金的显微结构的颗粒边界处存在不连续的沉淀物与在动态应力下的韧性性能的劣化相关。例如,公开文献de0833954t1提出生产亚稳线cu-ni-sn连铸合金,其具有8%重量至16%重量的ni、5%重量至8%重量的sn,并且可选地具有高达0.3%重量的mn、高达0.3%重量的b、高达0.3%重量的zr、高达0.3%重量的fe、高达0.3%重量的nb和高达0.3%重量的mg,没有通过捏和的任何加工。在进行铸造状态的固溶退火处理之后和在亚稳线时效之后,在每种情况下均必须通过水淬火快速冷却该合金,以获得没有不连续沉淀物的亚稳线地偏析的显微结构。相比之下,公开文献de2350389c关于具有2%重量至98%重量的ni和2%重量至20%重量的sn的cu-ni-sn合金,说明了必须进行具有至少一度的ε=75%的形成的冷成形,以能够防止时效退火期间脆化不连续沉淀物的出现。文献de69105805t2提到了从铜-镍-锡合金工业,大规模生产半成品和构件时出现的困难。例如,特别是在铸造显微结构的晶界处的富sn偏析的出现极大地限制了经济地进一步加工的机会。即使通过对铸造状态的cu-ni-sn合金进行的热机械加工操作也不能容易地消除的富sn偏析阻止合金元素在基体中的均质分布。然而,这是这组材料的淬透性的基本先决条件。因此,提出的是用4%重量至18%重量的ni和3%重量至13%重量的sn精细地雾化铜合金的熔体,并在收集表面上收集喷雾颗粒。随后的快速冷却旨在抵消富sn的晶界偏析的形成。文献de4126079c2公开了许多铜合金可以通过常规的块铸造方法生产,随后进行热成形和冷成形,中间退火操作仅具有较差的经济可行性,如果有的话,因为由于晶界沉淀物、偏析或其他非均质性使得热成形是困难的。这些铜合金还包括铜-镍-锡材料。因此,为了确保这种铸造状态的合金的冷成形,推荐使用精确控制熔体凝固速率的薄带铸造方法。由于现代发动机、机器、设备和机组中的操作温度和压力升高,出现了对各个系统元件的各种不同的损坏机制。因此,从材料和结构的角度来看,特别是在设计滑动元件和插头连接器的情况下,不仅要考虑滑动磨损的类型而且还要考虑通过振动摩擦磨损造成的损坏机理,这是非常必要的。振动摩擦磨损,行话也称为微振磨损,是在振动的接触面之间发生的一种摩擦磨损。除了构件的几何磨损或体积磨损之外,与周围介质的反应导致摩擦腐蚀。对材料的损坏可明显降低磨损区的局部强度,尤其是疲劳强度。疲劳裂纹可以从受损的构件表面行进,并且这些导致疲劳断裂/疲劳失效。在摩擦腐蚀下,构件的疲劳强度可以正好降低到材料的疲劳指数以下。在一种意义上,振动摩擦磨损的其机理与滑动磨损的类型在运动方面有很大不同。更具体地,在振动摩擦磨损的情况下,腐蚀的影响特别显著。文献de102012105089a1描述了由滑动轴承的振动摩擦磨损引起的损坏的后果。为了确保滑动轴承的稳定定位,它们缩进轴承座。缩进操作在滑动轴承上产生很大的应力,通过现代发动机中增加的应力、热膨胀和动态轴载荷,甚至进一步增加了该应力。由于过大的应力,滑动轴承的几何形状可能发生变化,这减少了原始轴承重叠。这使得滑动轴承能够相对于轴承座微动。在轴承与轴承座之间的接触面处具有低振动宽度的这些循环相对运动导致滑动轴承的背衬的振动摩擦磨损/摩擦腐蚀/微振磨损。结果是裂纹的起始并最终是滑动轴承的摩擦疲劳失效。用各种滑动轴承材料进行微振磨损试验的结果表明,特别是ni含量高于2%重量的cu-ni-sn合金,如亚稳线地硬化铜镍锡合金的情况,对微振磨损的抗性不足。在发动机和机器中,电插头连接器通常设置在它们受到机械振动的环境中。如果连接结构的元件存在于由于机械应力而彼此进行相对运动的不同组件中,则结果可以是连接元件的相应的相对运动。这些相对运动导致振动摩擦磨损和插头连接器的接触区的摩擦腐蚀。微裂纹在该接触区中形成,这极大地降低了插头连接器材料的抗疲劳性。插头连接器因疲劳失效而失效可能是后果。此外,由于摩擦腐蚀,存在接触电阻的增加。因此,足以抵抗振动摩擦磨损/摩擦腐蚀/微振磨损的关键因素是耐磨性、延展性和耐腐蚀性的材料性能的组合。为了提高铜-镍-锡合金的耐磨性,必须在这些材料中加入合适的磨损基质。这些以硬颗粒形式的磨损基质旨在承担防止磨料磨损和粘着磨损的后果的功能。cu-ni-sn合金中有用的硬颗粒包括各种形式的沉淀。文献us6379478b1公开了一种用于插头连接器的铜合金的教导,所述铜合金具有0.4%重量至3.0%重量的ni、1%重量至11%重量的sn、0.1%重量至1%重量的si和0.01%重量至0.06%重量的p。据说,硅化镍和磷化镍的细小沉淀物可确保合金的高强度和良好的抗应力松弛性。为了在钢基基底上生产滑动层,文献us2129197a命名一种铜合金,所述铜合金通过应用焊接施加到基础基底,并含有77%重量至92%重量的cu、8%重量至18%重量的sn、1%重量至5%重量的ni、0.5%重量至3%重量的si和0.25%重量至1%重量的fe。本文使用的磨损基底据说是合金元素镍和铁的硅化物和磷化物。文献us3392017a公开了一种低熔点铜合金,其具有高达0.4%重量的si、1%重量至10%重量的ni、0.02%重量至0.5%重量的b、0.1%重量至1%重量的p和4%重量至25%重量的sn。该合金可以通过浇铸棒的形式做为填充材料施加到合适的金属基底表面。与现有技术相比,该合金具有改善的延展性,并且是机器可加工的。除了用于沉积焊接之外,该cu-sn-ni-si-p-b合金可通过喷涂方法用于沉积。本文据说加入磷、硅和硼是为了改善熔融合金的自发流动性和基底表面的润湿性,并且不必使用任何额外的助熔剂。该文献中公开的教导规定了在合金中具有强制性0.05%重量至0.15%重量的si含量和0.2%重量至0.6%重量特别高的p含量。这强调了对材料的自发流动性能的主要要求。随着该高p含量,则合金的热成形性将变差,并且显微结构的亚稳线可偏析性将不充分。根据文献us4818307a,在铜基合金中沉淀的硬颗粒的尺寸对其耐磨性具有很大影响。例如,尺寸达到5μm至100μm的元素镍和铁的复杂硅化物形成/硼化物形成显著提高了具有5%重量至30%重量的ni、1%重量至5%重量的si、0.5%重量至3%重量的b和4%重量至30%重量的fe的铜合金的耐磨性。元素锡不存在于该材料中。该材料通过沉积焊接做为抗磨层施加到合适的基底上。文献us5004581a描述了与上述us4818307a相同,具有额外含量的含量在5%重量至15%重量范围内的锡和/或额外含量的含量在3%重量至30%重量的锌的铜合金。sn和/或锌的添加特别改善了材料对粘着磨损的抗性。该材料同样通过沉积焊接做为为抗磨层施加到合适的基底上。然而,根据文献us4818307a和us5004581a的铜合金,由于所需的硅化物形成/镍和铁元素的硼化物形成的所要求的尺寸为5μm至100μm,将仅具有非常有限的冷成形性。可沉淀硬化的铜-镍-锡合金的公开内容来自文献us5041176a。该铜基合金含有0.1%重量至10%重量的ni、0.1%重量至10%重量)的sn、0.05%重量至5%重量的si、0.01%重量至5%重量的fe和0.0001%重量至1%重量的硼。该材料具有ni-si体系的分散的金属间相的含量。通过不含任何fe含量的加工实施例也阐明了合金的性能。文献kr1020020008710a(摘要)指出,sn含量大于6%重量的亚稳线cu-ni-sn合金是不可热成形的。给出的原因是在cu-ni-sn合金的铸造显微结构的晶界处的富sn偏析。因此,对于所公开的cu-ni-sn多物质合金,对于高强度线材和片材,指明了1%重量至8%重量的ni、2%重量至6%重量的sn和0.1%重量至5%重量的来自al、si、sr、ti和b组的两种或更多种元素的组分。文献us5028282a公开了一种铜合金,其具有6%重量至25%重量的ni、4%重量至9%重量的sn和含量为0.04%重量至5%重量(单独或一起)的进一步的添加。这些进一步的添加%重量是:0.03%至4%的zn、0.01%至0.2%的zr、0.03%至1.5%的mn、0.03%至0.7%的fe、0.03%至0.5%的mg、0.01%至0.5%的p、0.03%至0.7%的ti、0.001%至0.1%的b、0.03%至0.7%的cr、0.01%至0.5%的co。说明了合金元素zn、mn、mg、p和b被加入用于合金熔体的脱氧。元素ti、cr、zr、fe和co具有晶粒细化和强度增强功能。通过与类金属(例如硼,硅和磷)合金化,可以实现相对高的基础熔化温度的降低,这对于加工目的是重要的。因此,这些合金添加特别用于耐磨涂层材料和高温材料领域,所述材料包括例如ni-si-b体系和ni-cr-si-b体系的合金。在这些材料中,特别是合金元素硼和硅被认为是镍基硬质合金熔化温度显著降低的原因,这使得它们可以用作自发流动的镍基硬质合金。公开的说明书de2033744b包括关于合金元素硼在含si金属熔体中的进一步功能的重要说明。据此,硼的添加导致在熔体中形成的氧化物的消化和形成硼硅酸盐,所述硼硅酸盐上升到涂层的表面,并因此阻止氧的进一步进入。以这种方式,可以实现涂层的光滑表面。文献de10208635b4描述了存在金属间相的扩散焊料位点中的工艺。通过扩散焊接,具有不同热膨胀系数的部件将彼此结合。在该焊接位点或焊接操作本身存在热机械应力的情况下,在界面处产生很大的应力,这可导致特别是在金属间相环境中的裂纹。提出的补救措施是将焊料组分与颗粒混合,所述颗粒实现连接配对件的不同膨胀系数的平衡。例如,由于其有利的热膨胀系数,硼硅酸盐或磷硅酸盐颗粒可以使焊料结合中的热机械应力最小化。此外,已经诱发的裂纹的扩散受到这些颗粒的阻碍。公开的说明书de2440010b尤其强调了元素硼对具有0.1%重量至2.0%重量的硼和4%重量至14%重量的铁的铸造硅合金的导电率的影响。在这种si基合金中,高熔点si-b相沉淀出,这称为硼化硅。通常由硼含量确定的sib3、sib4、sib6和/或sibn多晶型物中存在的硼化硅在它们的性能方面与硅显著不同。这些硼化硅具有金属特性,因此它们是导电的。它们具有极高的热稳定性和氧化稳定性。由于其非常高的硬度和高耐磨料磨损性,优选用于烧结产品的sib6多晶型物用于例如陶瓷生产和陶瓷加工。用于表面涂层的常规耐磨硬质合金由相对延展性的基质组成,该基质由金属铁、钴和镍构成,具有做为硬颗粒的间生的硅化物和硼化物(knotek,o.;lugscheider,e.;reimann,h.:einbeitragzurbeurteilungverschleiβfesternickel-bor-silicium-hartlegierungen《acontributiontotheassessmentofwear-resistanthardnickel-boron-siliconalloys》。zeitschriftfürwerkstofftechnik8(1977)10,第331-335页)。ni-cr-si体系、ni-cr-b体系、ni-b-si体系和ni-cr-b-si体系的硬质合金的广泛使用是基于这些硬颗粒的耐磨性的增加。除了硅化物ni3si和ni5si2之外,ni-b-si合金还包含硼化物ni3b和ni-si硼化物/ni硅硼化物ni6si2b。还报道了在元素硼存在下形成硅化物的某种缓慢。对ni-b-si合金体系的进一步研究导致了高熔点ni-si硼化物ni6si2b和ni4.29si2b1.43的检测(lugscheider,e.;reimann,h.;knotek,o.:dasdreistoffsystemnickel-bor-silicium《thetriphasicnickel-boron-siliconsystem》.monatsheftefürchemie106(1975)5,p.1155-1165)。这些高熔点ni-si硼化物在硼和硅的方向上存在相对宽的均质性。在许多应用中,将元素锌添加到铜-镍-锡合金中以降低金属成本。在功能方面,合金元素锌的作用是从熔体中更显著地形成富sn或富ni-sn的相。此外,锌增强了亚稳线cu-ni-sn合金中沉淀物的形成。此外,在许多应用中,还向铜-镍-锡合金中添加了一定的pb含量,以改善空运行性能和更好的材料去除可加工性。本发明的目的是提供一种高强度铜-镍-锡合金,所述高强度铜-镍-锡合金在每种情况下在整个镍含量和2%重量至10%重量的锡含量范围内均具有优异的热成形性。通过常规铸造方法,而不需要进行喷射压实或薄带铸造生产的前体材料应该可用于热成形。在铸造之后,铜-镍-锡合金应该没有气孔、收缩孔和应力裂纹,并且其特征在于具有均质分布的富锡的相成分的显微结构。而且,铸造后铜-镍-锡合金的显微结构中已经存在金属间相。这是重要的,以便合金即使在铸造状态下也具有高强度、高硬度和足够的耐磨性。此外,即使铸造状态也应具有高耐腐蚀性。首先,铜-镍-锡合金的铸造状态不应该首先通过合适的退火处理进行均质化,以便能够建立足够的热成形性。关于铜-镍-锡合金的加工性能,首先目的是其冷成形性没有显著恶化,尽管相对于常规的cu-ni-sn合金的金属间相的含量。另一方面,就合金而言,应该消除在所进行的冷成形操作中对最小成形程度的要求。这被认为是根据现有技术的先决条件,以便能够确保cu-ni-sn材料的显微结构的亚稳线偏析,而不形成不连续的沉淀物。对应于现有技术的cu-ni-sn材料的进一步加工的进一步要求是基于材料时效硬化后的冷却速率。因此,在亚稳线时效硬化之后,认为必须通过水淬火快速冷却材料,以获得没有不连续沉淀物的亚稳线偏析的显微结构。然而,由于这种冷却方法,在时效硬化之后可以形成危险的内应力,本发明的另一个目的是即使对于合金,也在包括时效硬化的整个制造过程中防止形成不连续的沉淀物。通过包括至少一个退火操作或至少一个热成形和/或冷成形操作以及至少一个退火操作的进一步加工操作,可以建立具有高强度、高热阻、高硬度、高抗应力松弛性和耐腐蚀性,足够的导电率以及对摩擦磨损机制和振动摩擦磨损机制的高度抵抗性的含细粒硬颗粒的显微结构。关于铜-镍-锡合金,本发明通过权利要求1至3中任一项所述的特征,关于通过权利要求9至10所述的特征执行的生产方法和关于通过权利要求16至18的特征执行的用途来反映。其他从属权利要求涉及本发明的有利形式和发展。本发明包括一种具有优良的铸造性、热成形性和冷成形性、高耐磨料磨损性、高耐粘着磨损性和高耐微振磨损性以及改善的耐腐蚀性和抗应力松弛性的高强度铜-镍-锡合金,以%重量计,组成如下:2.0%至10.0%的ni,2.0%至10.0%的sn,0.01%至1.5%的si,0.002%至0.45%的b,0.001%至0.09%的p,可选地,高达2.0%co的最大值,可选地,高达2.0%zn的最大值,可选地,高达0.25%pb的最大值,余量:铜和不可避免的杂质,其特征在于,–以元素硅和硼的%重量计的元素含量的si/b比率的最小值为0.4,最大值为8;–铜-镍-锡合金包括含si相、含b相和体系ni-si-b、ni-b、ni-p和ni-si的相,所述相显著改善了合金的加工性能和使用性能。本发明还包括一种具有优良的铸造性、热成形性和冷成形性、高耐磨料磨损性、高耐粘着磨损性和高耐微振磨损性以及改进的耐腐蚀性和抗应力松弛性的高强度铜-镍-锡合金,以%重量计,组成如下:2.0%至10.0%的ni,2.0%至10.0%的sn,0.01%至1.5%的si,0.002%至0.45%的b,0.001%至0.09%的p,可选地,高达2.0%co的最大值,可选地,高达2.0%zn的最大值,可选地,高达0.25%pb的最大值,余量:铜和不可避免的杂质,其特征在于,–以元素硅和硼的%重量计的元素含量的si/b比率的最小值为0.4,最大值为8;–铸造后合金中存在以下显微结构成分:a)含si和含p的金属基组分,其基于整体显微结构具有:a1)可以通过经验公式cuhniksnm报告,并且具有以2至6个原子%计的元素含量的(h+k)/m比率的高达35%体积的第一相成分,a2)可以通过经验公式cupnirsns报告,并且具有以10至15个原子%计的元素含量的(p+r)/s比率的高达15%体积的第二相成分,a3)固体铜溶液的余量;b)基于整体显微结构存在的相,b1)以0.01%体积至10%体积计,做为含si的相和含b的相,b2)以1%体积至15%体积计,做为具有经验公式nixsi2b(x=4至6)的ni-si硼化物,b3)以1%体积至15%体积计,做为ni硼化物,b4)以1%体积至5%体积计,做为ni磷化物,b5)以1%体积至5%体积计,做为ni硅化物在显微结构中,它们单独地存在和/或做为加成化合物和/或混合化合物存在,并由锡和/或第一相成分和/或第二相成分包裹;–在铸造过程中,单独地存在和/或做为加成化合物和/或混合化合物存在的硼化硅、ni-si硼化物和ni硼化物、ni磷化物和ni硅化物的形式的含si和含b相构成在熔体凝固/冷却过程中均匀结晶的晶种,使得第一相成分和/或第二相成分均匀地分布在如类似岛和/或类似网状物的显微结构中;–硼硅酸盐和/或硼磷硅酸盐与磷硅酸盐一起的形式的含si和含b相,在合金的半成品材料和构件上起到磨损保护和腐蚀保护的涂层的作用。有利地,第一相成分和/或第二相成分在合金的铸造显微结构中以至少1%体积存在。岛形式和/或网状物形式的第一相成分和/或第二相成分的均匀分布意味着显微结构没有偏析。这种偏析理解为意味着铸造显微结构中第一相成分和/或第二相成分的累积,所述累积采取晶界偏析的形式,所述晶界偏析在铸造时在热和/或机械应力下可导致对显微结构损坏,该损坏是可以导致断裂的裂纹形式。铸造后的显微组织仍然没有(cu,ni)-sn体系的气孔、收缩孔、应力裂纹和不连续沉淀物。在该变型中,合金处于铸造状态。本发明还包括一种具有优良的铸造性、热成形性和冷成形性、高耐磨料磨损性、高耐粘着磨损性和高耐微振磨损性以及改进的耐腐蚀性和抗应力松弛性的高强度铜-镍-锡合金,以%重量计,组成如下:2.0%至10.0%的ni,2.0%至10.0%的sn,0.01%至1.5%的si,0.002%至0.45%的b,0.001%至0.09%的p,可选地,高达2.0%co的最大值,可选地,高达2.0%zn的最大值,可选地,高达0.25%pb的最大值,余量:铜和不可避免的杂质,其特征在于,–以元素硅和硼的%重量计的元素含量的si/b比率的最小值为0.4,最大值为8;–在通过至少一次退火操作或通过至少一次热成形操作和/或冷成形操作以及至少一次退火操作,进一步处理合金之后,存在以下显微结构成分:a)具有以下的基于整体显微结构的金属基组分,a1)可以通过经验公式cuhniksnm报告,且具有以2至6个原子%计的元素含量的(h+k)/m比率的高达15%体积的第一相成分,a2)可以通过经验公式cupnirsns报告,且具有以10至15个原子%计的元素含量的(p+r)/s比率的高达5%体积的第二相成分,以及a3)固体铜溶液的余量;b)基于整体显微结构,以下方式存在的相,b1)以2%至30%体积计,在显微结构中做为含si相和含b相,具有经验公式nixsi2b(x=4至6)的ni-si硼化物,做为ni硼化物、ni磷化物和ni硅化物,它们单独存在和/或做为加成化合物和/或混合化合物存在,并由(cu,ni)-sn体系的沉淀物包裹,b2)以高达80%体积计,在显微结构中做为(cu,ni)-sn体系的连续沉淀物,b3)以2%至30%体积计,在显微结构中做为ni磷化物和ni硅化物,所述ni磷化物和ni硅化物单独存在和/或做为加成化合物和/或混合化合物存在,由(cu,ni)-sn体系的沉淀物包裹且具有小于3μm的尺寸;–以单独地存在和/或做为加成化合物和/或混合化合物存在的硼化硅、ni-si硼化物和ni硼化物、ni磷化物和ni硅化物的形式的含si相和含b相在合金的进一步加工过程中构成用于显微结构的静态和动态再结晶的晶种,这使得能够建立均匀和细晶粒的显微结构;–以硼硅酸盐和/或硼磷硅酸盐与磷硅酸盐一起的形式的含si相和含b相,在合金的半成品材料和构件上起到磨损保护和腐蚀保护的涂层的作用。有利地,(cu,ni)-sn体系的连续沉淀物在合金的进一步加工状态的显微结构中以至少0.1%体积计存在。即使在进一步加工合金之后,显微结构也没有偏析。这种偏析理解为意味着显微结构中第一相成分和/或第二相成分的累积,所述累积采取晶界偏析的形式,所述晶界偏析特别是在构件上的动态应力下,可导致对显微结构的损害,该损害是可导致断裂的裂纹形式。进一步加工后合金的显微结构没有气孔、收缩孔和应力裂纹。做为本发明的基本特征应该强调,进一步加工状态的显微结构没有(cu,ni)-sn体系的不连续沉淀物。在该第二变体中,合金处于进一步被加工状态。本发明出于提供具有含si相和含b相和具有ni-si-b体系、ni-b体系、ni-p体系和ni-si体系的相的铜-镍-锡合金的考虑而进行。这些相显著地改善了可铸性、热成形性和冷成形性的加工性能。此外,这些相通过增加强度和耐磨料磨损性、耐粘着磨损性和耐微振磨损性来改善合金的使用性能。这些相做为本发明的进一步使用性能另外改善了耐腐蚀性和抗应力松弛性。本发明的铜-镍-锡合金可以通过砂铸工艺、壳模铸造工艺、精密铸造工艺、全模铸造工艺、压力压铸工艺、消失模工艺和永久模铸工艺生产或在连续或半连续连铸工艺的帮助下生产。使用在加工技术和成本方面复杂的初级成形技术是可能的,但对于本发明的铜-镍-锡合金的生产不是绝对必要的。例如,可以省去使用喷雾压实或薄带铸造。本发明的铜-镍-锡合金的铸造形式尤其可以在sn含量和ni含量的整个范围内,例如通过热轧、连铸压或锻造直接热成形,而不必绝对必须进行均质化退火。同样值得注意的是,在由本发明的合金制成的壳模铸造或连铸铸造的形式后,也不需要在升高的温度下进行任何复杂的锻造工艺或压缩工艺以焊接(即封闭)材料中的毛孔和裂纹。因此,进一步消除了迄今为止从铜-镍-锡合金生产半成品和构件中存在的加工相关限制。取决于铸造工艺,在合金的sn含量上升的情况下,在铸造状态下的本发明的铜-镍-锡合金的显微结构的金属基材料由均匀地分布在固体铜溶液中的富锡相(α相)的增加的比例组成。这些金属基材料的富锡相可分为第一相成分和第二相成分。第一相成分可以通过经验公式cuhniksnm报告,并且具有以2至6个原子%计的元素含量的(h+k)/m比率。第二相成分可以通过经验公式cupnirsns报告,并且具有以10至15个原子%计的元素含量的(p+r)/s比率。本发明的合金的特征在于含si相和含b相,它们可分成两组。第一组涉及含硅相和含b相,所述含硅相和含b相采用硼化硅的形式,并且可以存在sib3、sib4、sib6和sibn多晶型物中。化合物sibn中的“n”表示元素硼在硅晶格中的高溶解度。第二组含si相和含b相涉及硼硅酸盐和/或硼磷硅酸盐的硅酸盐化合物。在本发明的铜-镍-锡合金中,以硼化硅形式和硼硅酸盐和/或硼磷硅酸盐形式的含si相和含b相的显微结构成分不小于0.01%体积且不超过10%体积。本发明合金的显微结构中第一相成分和/或第二相成分的均匀排列特别是由于含硅相和含硼相的作用引起,所述含硅相和含硼相以硼化硅和ni-si硼化物的形式,所述ni-si硼化物具有经验公式nixsi2b(x=4至6),主要地已在熔体中沉淀出来。随后,在熔体的凝固/冷却期间,优选在已经存在的硼化硅和ni-si硼化物上沉淀ni硼化物。单独地存在和/或做为加成化合物和/或混合化合物存在的硼化合物的全体在熔体的第一次固化/冷却期间用作初级晶种。稍后在熔体的凝固/冷却中,ni磷化物和ni硅化物优先做为二次晶种沉淀在硼化硅、ni-si硼化物和ni硼化物的初级晶种上,所述硼化硅、ni-si硼化物和ni硼化物已经单独地存在和/或做为加成化合物和/或混合化合物存在。ni-si硼化物和ni硼化物各自以1%体积至15%体积存在于显微结构中,并且ni磷化物和ni硅化物各自以1%体积至5%体积存在。因此,在显微结构中,以硼化硅、具有经验公式nixsi2b(x=4至6)的ni-si硼化物和ni硼化物、ni磷化物和ni硅化物形式的含si相和含b相单独地存在和/或做为加成化合物和/或混合化合物存在。这些相在下文中称为结晶晶种。最后,金属基材料的元素锡和/或第一相成分和/或第二相成分优选在结晶晶种的区中结晶,结果,锡和/或第一相成分和/或第二相成分的结晶晶种被包裹。由锡和/或第一相成分和/或第二相成分包裹的这些结晶晶种在下文中称为第一类硬颗粒。在本发明合金的铸造状态下,第一类硬颗粒的尺寸小于80μm。有利地,第一类硬颗粒的尺寸小于50μm。随着合金的sn含量的增加,岛形式的第一相成分和/或第二相成分的排列在显微结构中转变成网状物排列。在本发明的铜-镍-锡合金的铸造显微结构中,第一相成分可占高达35%体积的比例。第二相成分占高达15%体积的显微结构分数。有利地,第一相成分和/或第二相成分在合金的铸造状态的显微结构中以至少1%体积存在。由于合金元素硼的添加,在铸造本发明的合金期间,存在抑制的并且由此仅不完全形成的磷化物和硅化物。为此,磷和硅的含量保持溶解在铸造状态的金属基材料中。传统的铜-镍-锡合金具有相对宽的凝固间隔。铸造中这种宽的凝固间隔增加了气体吸收的风险,并因此增加了熔体的不完全、粗糙、通常树枝状的结晶。结果通常是气孔和粗锡富集偏析,在其相界处经常出现收缩孔和应力裂纹。在这组材料中,富含sn的偏析还另外地优先在晶界处发生。借助于硼、硅和磷的组合含量,本发明合金熔体中的各种过程被激活,与传统的铜-镍-锡合金相比,这关键地改变了其凝固特性。在本发明的熔体中,元素硼、硅和磷具有脱氧功能。硼和硅的添加使得可以降低磷含量而不降低熔体的脱氧强度。使用该措施,可以通过磷的添加来抑制熔体的充分脱氧的不利影响。因此,高p含量将另外延长铜-镍-锡合金的凝固间隔,所述凝固间隔在任何情况下已经非常大,这将导致在该材料类型中孔的倾向和偏析倾向的增加。通过将本发明合金中的p含量限制在0.001%重量至0.09%重量的范围内而减少了磷的不利影响。特别是通过元素硼和结晶晶种降低基础熔化温度导致本发明合金的凝固间隔减小。结果,本发明的铸造状态具有非常均匀的显微结构,各个相成分具有精细分布。因此,在本发明的合金中,特别是在晶界处,不会发生富含锡的偏析。在本发明合金的熔体中,元素硼、硅和磷的作用是金属氧化物的还原。元素本身同时被氧化并且通常上升到铸件的表面,在那里它们以硼硅酸盐和/或硼磷硅酸盐和磷硅酸盐的形式形成保护层,所述保护层保护铸件免于吸收气体。发现了本发明合金铸件的特别光滑的表面,这表明这种保护层的形成。本发明的铸造状态的显微结构在铸件的整个横截面上也没有气孔。在与所引用的文献有关的评论的背景下,提到了引入硼硅酸盐和磷硅酸盐以避免在扩散焊接期间具有不同热膨胀系数的相之间的应力裂纹的优点。本发明的基本概念是应用硼硅酸盐、硼磷硅酸盐和磷硅酸盐的效果,关于将扩散焊接中的连接配对件的不同热膨胀系数与铜镍锡材料的铸造、热成形和热处理的工艺匹配。由于这些合金的宽凝固间隔,在低sn和富sn结构区之间出现高机械应力,所述结构区以偏移方式结晶并且可导致裂纹和孔隙。此外,由于不同的热成形特性和低sn和富sn显微结构成分的不同热膨胀系数,这些损伤特征也可发生在铜-镍-锡合金的热成形和高温退火操作中。硼、硅和磷的组合添加对本发明的铜-镍-锡合金的影响在熔体凝固期间,通过结晶晶种的作用首先是具有均匀分布的以岛形式和/或以网状物形式的金属基材料的第一相成分和/或第二相成分的显微结构。除了结晶晶种之外,在熔体凝固过程中以硼硅酸盐和/或硼磷硅酸盐与磷硅酸盐一起形式形成的含si相和含b相确保了第一相成分和/或第二相成分和金属基材料的固体铜溶液的热膨胀系数的必要的匹配。以这种方式,防止了在具有不同sn含量的相之间形成孔和应力裂纹。本发明的铜-镍-锡合金的合金含量的进一步效果是铸造状态的晶粒结构的显著变化。因此,发现在初级铸造显微结构中,形成具有小于30μm的亚晶粒的晶粒尺寸的子结构。可替代地,本发明的合金可以通过退火或通过热成形和/或冷成形操作以及至少一次退火操作进行进一步处理。进一步加工本发明的铜-镍-锡合金的一种方式是通过至少一次冷成形操作以及至少一次退火操作将铸件转换成具有所需性能的最终形式。由于均匀的铸造显微结构和在其中沉淀出的第一类硬颗粒,本发明的合金即使在铸造状态下也具有高强度。结果,铸件具有相对低的冷成形性,这使得难以进一步经济地加工它们。为此,已经发现在冷成形操作之前对铸件进行均质化退火操作的实施是有利的。为了确保本发明的时效硬化性,已发现均质化退火工艺后的加速冷却是有利的。在此已经发现,由于沉淀机理和分离机理的缓慢,除了水淬火之外,还可以使用具有相对低的冷却速率的冷却方法。例如,已经发现加速空气冷却的使用同样是可行的,以便在本发明的均质化退火操作期间,降低显微结构中的沉淀过程和分离过程的硬度增强和强度增加的效果到充足的程度。结晶晶种对本发明显微结构的再结晶的显著效果表现在显微结构中,该显微结构可在冷成形后通过在170℃至880℃的温度范围内和在10分钟至6小时之间退火时间内退火而建立。再结晶合金的特别精细的结构能够实现进一步冷成形步骤,其成形度ε通常大于70%。以这种方式,可以建立合金的超高强度状态。在本发明的进一步加工中已经成为可能的这些高度冷成形可以建立拉伸强度rm、屈服点rp0.2和硬度的特别高的值。特别是rp0.2参数的水平对于滑动元件和引导元件是重要的。此外,rp0.2的高值是电子和电气工程中插头连接器必要的弹簧特性的先决条件。在描述与铜-镍-锡材料的加工和性能有关的现有技术的许多文献的说明中,参考了观察75%的最小程度的冷成形的需要,例如,以便防止显微结构中(cu,ni)-sn体系的不连续沉淀物的沉淀。相比之下,不管冷成形的程度如何,本发明合金的显微结构保持没有(cu,ni)-sn体系的不连续沉淀物。例如,对于本发明的特别有利的实施方案,发现即使在小于20%的极小程度的冷成形情况下,本发明的显微结构仍然没有(cu,ni)-sn体系的不连续沉淀物。根据现有技术,传统的、可亚稳线地偏析的cu-ni-sn材料被认为是可热成形的,但是有很大困难,如果有的话。在热成形本发明的铜-镍-锡合金工艺的过程中,同样观察到结晶晶种的影响。考虑结晶晶种主要与这样的事实有关,即本发明合金的热成形中的动态再结晶优先在600℃至880℃的温度范围内发生。这导致显微结构的均匀性和细粒度的进一步增加。有利地,在热成型之后半成品和构件的冷却可以用平静或加速的空气或用水实现。与铸造后的情况一样,也可以在铸件的热成形之后建立特别光滑的部件表面。该观察结果表明采取硼硅酸盐和/或硼磷硅酸盐和磷硅酸盐的形式的含si相和含b相的形成在热成形过程中在该材料中发生。即使在热成形过程中,硅酸盐与结晶晶种一起导致本发明金属基材料的相的不同热膨胀系数的匹配。因此,热成形部件的表面和显微结构(如铸造后的情况那样)在热成形之后也没有裂纹和孔隙。有利地,本发明的铸造状态和/或热成形状态的至少一种退火处理可以在170℃至880℃的温度范围内进行,持续时间为10分钟至6小时,并且可替代地通过在平静的或加速的空气下或使用水的冷却进行。本发明的一个方面涉及包括进行至少一次冷成形操作的铸造状态或热成形状态或退火铸造状态或退火热成形状态的用于进一步加工的有利工艺。优选地,本发明的冷成形状态的至少一次退火处理可以在170℃至880℃的温度范围内进行,持续时间为10分钟至6小时,并且可替代地通过在平静或加速的空气下或使用水的冷却进行。有利地,消除应力退火/时效硬化退火操作可170℃至550℃的温度范围内进行,持续时间为0.5小时至8小时。在通过至少一次退火操作或通过至少一次热成形和/或冷成形操作以及至少一次退火操作进一步处理合金之后,优选在结晶晶种的区中形成(cu,ni)-sn体系的沉淀物,结果,该结晶晶种被这些沉淀物包裹。由(cu,ni)-sn体系的沉淀物包裹的这些结晶晶种在下文中称为第二类硬颗粒。做为本发明合金的进一步加工的结果,与第一类硬颗粒的尺寸相比,第二类硬颗粒的尺寸减小。特别是随着冷成形程度的增加,第二类硬质颗粒的尺寸逐渐减小,因为这些是合金中最硬的成分,不能有助于围绕它们的金属基材料的形状变化。取决于冷成形的程度,所得到的第二类硬颗粒和/或第二类硬颗粒的所得区段具有小于40μm至甚至小于5μm的尺寸。本发明的ni含量和sn含量各自在2.0%重量-10.0%重量的范围内变化。ni含量和/或sn含量低于2.0%重量会导致强度值和硬度值过低。而且,合金在滑动应力下的运行性能将不足。合金对磨粒磨损和粘着磨损的抗性不能满足要求。当ni含量和/或sn含量大于10.0%重量时,本发明合金的韧性会迅速恶化,结果降低了由该材料制成的构件的动态耐久性。关于由本发明合金制成的构件的最佳动态耐久性的保证,发现镍和锡的含量在每种情况下在3.0%重量至9.0%重量范围内是有利的。在这方面,对于本发明,在每种情况下,对于元素镍和锡的含量,特别优选4.0%重量至8.0%重量的范围。关于含ni和含sn的铜材料,从现有技术中已知,显微结构的亚稳线偏析度随着%重量的元素镍和锡的ni/sn元素含量比率的增加而增加。对于超过和高于约2%重量的ni含量和sn含量,这是正确的。随着ni/sn比率的降低,(cu,ni)-sn体系的沉淀形成机理获得更大的重量,这导致亚稳线地偏析的显微结构部分的减少。一个特别的结果是,随着ni/sn比率的降低,(cu,ni)-sn体系的不连续沉淀物的形成程度越大。本发明的铜-镍-锡合金的基本特征包括严重抑制ni/sn比率对显微结构中不连续沉淀物形成的影响。因此,已经发现,在本发明的显微结构中,很大程度上与ni/sn比率无关,并且与时效硬化条件无关,没有(cu,ni)-sn体系的不连续沉淀物的沉淀。相比之下,在本发明合金的进一步加工过程中,(cu,ni)-sn体系的连续沉淀物以高达80%体积形成。有利地,(cu,ni)-sn体系的连续沉淀物在合金的进一步加工状态的显微结构中以至少0.1%体积存在。结晶晶种在熔体的凝固/冷却过程中的效果、结晶晶种做为再结晶晶种的效果以及硅酸盐基相对于磨损防护和腐蚀防护的作用,当硅含量至少为0.01%重量和硼含量至少为0.002%重量时只能达到本发明的合金的一定程度的技术意义。相比之下,如果si含量超过1.5%重量和/或b含量超过0.45%重量,这导致铸造特性的劣化。过高的结晶晶种含量会使熔体变得越来越厚。此外,结果是降低了本发明合金的韧性。si含量的有利范围被认为在0.05%重量至0.9%重量的极限的范围内。已发现硅的特别有利的含量为0.1%重量至0.6%重量。对于元素硼,0.01%重量至0.4%重量的含量被认为是有利的。已发现硼的含量为0.02%重量至0.3%重量是特别有利的。为了确保充足含量的ni-si硼化物以及以硼硅酸盐和/或硼磷硅酸盐形式的含si相和含b相,硅和硼元素的元素比率的下限已被发现是重要的。因此,在本发明的合金中,元素硅和硼的以%重量计的元素含量的最小si/b比率为0.4。对于本发明的合金,元素硅和硼的以%重量计的元素含量的有利的最小si/b比率为0.8。优选地,元素硅和硼的以%重量计的元素含量的最小si/b比率为1。对于本发明的另一个重要特征,元素硅和硼的以%重量计的元素含量的si/b比率固定上限为8是重要的。在铸造之后,硅的一部分溶解在金属基材料中,并结合在第一类硬颗粒中。在铸造状态的热或热机械进一步加工操作期间,第一类硬颗粒的硅化物组分至少部分溶解。这增加了金属基材料的si含量。如果这超过上限,则随着尺寸的增加,过量比例的ni硅化物会沉淀。这些将关键地降低本发明的冷成形性。为此,本发明合金的元素硅和硼的以%重量计的元素含量的最大si/b比率为8。通过这种措施,可以将在热或热机械进一步是合金的铸造状态的加工操作的过程中形成的ni硅化物的尺寸降低至3μm以下。另外,这限制了ni硅化物的含量。在这方面,已发现将元素硅和硼的以%重量计的元素含量的si/b比率限制至最大值6是特别有利的。结晶晶种的沉淀影响本发明合金熔体的粘度。这一事实强调了为什么磷的添加是必不可少的。磷的作用是尽管有结晶晶种,但熔体仍具有足够的流动性,这对本发明的可铸性具有重要意义。本发明合金的磷含量为0.001%重量至0.09%重量。低于0.001%重量,p含量不再有助于确保本发明的足够的可铸性。如果合金的磷含量呈现高于0.09%重量的值,则一方面,过度大的ni组分以磷化物的形式结合,这降低了显微结构的亚稳线可分离性。另一方面,在p含量高于0.09%重量的情况下,本发明的热成形性会有严重的劣化。为此,已发现p含量为0.01%重量至0.09%重量是特别有利的。优选p含量为0.02%重量至0.08%重量。由于另一个原因,合金元素磷具有非常重要的意义。与元素硅和硼的以%重量计的元素含量的所需最大si/b比率为8一起,其可归因于合金的磷含量,在进一步加工本发明后,单独地存在和/或做为加成化合物和/或混合化合物存在并由(cu,ni)-sn体系的沉淀物包裹的ni磷化物和ni硅化物(尺寸不大于3μm且含量为2%体积至高达30%体积)可以在显微结构中形成。单独地存在和/或做为加成化合物和/或混合化合物存在,并且被(cu,ni)-sn体系的沉淀物包裹,并且具有不大于3μm的尺寸的这些ni磷化物和ni硅化物以下称为第三类硬颗粒。在本发明特别优选构造的进一步加工状态的显微结构中,第三类硬颗粒甚至具有小于1μm的尺寸。这些第三类硬颗粒首先在其做为磨损基底的功能中补充第二类硬颗粒。因此,它们增加了金属基材料的强度和硬度,从而提高了合金对磨料磨损应力的抗性。其次,第三类硬颗粒增加了合金的耐粘合磨损性。最后,这些第三类硬颗粒的效果是本发明合金的热强度和抗应力松弛性的关键性增加。这是本发明的合金特别是用于电子/电气工程中的滑动元件和构件以及连接元件的重要先决条件。由于铸造状态的显微结构中的第一类硬颗粒和进一步加工状态的显微结构中的第二和第三类硬颗粒的含量,本发明的合金具有沉淀-可硬化材料的特征。有利地,本发明对应于沉淀-可硬化的和亚稳线地可偏析的铜-镍-锡合金。元素硅、硼和磷的元素含量的总和有利地为至少0.2%重量。本发明合金的铸造变体和进一步加工变体可包括以下可选的元素:元素钴可以以高达2.0%重量的含量被添加到本发明的铜-镍-锡合金中。由于镍和钴元素之间的相似性关系以及由于钴相对于镍的类似的si硼化硅形成、硼化物形成、硅化物形成和磷化物的形成性质,可以添加合金元素钴以便参与形成结晶晶种和合金中第一、第二和第三类硬颗粒的形成。结果,可以减少硬颗粒内结合的ni含量。这可以实现这样的效果:在金属基材料中有效可用的用于显微结构的亚稳线偏析的ni含量增加。通过有利地添加0.1%重量至2.0%重量的co,可以显著提高本发明的强度和硬度。元素锌可以被添加到本发明的铜-镍-锡合金中,含量为0.1%重量至2.0%重量。发现合金元素锌取决于合金的ni含量和sn含量,增加了本发明金属基材料中第一相成分和/或第二相成分的比例,这导致强度和硬度的增加。ni组分和zn组分之间的相互作用被认为是造成这种情况的原因。由于ni组分和zn组分之间的这些相互作用,同样发现第一类硬颗粒尺寸和第二类硬颗粒尺寸的减小,其因此在显微结构中形成更精细的分布。低于0.1%重量的zn,不可能观察到这些对本发明的显微结构和机械性能的影响。当zn含量高于2.0%重量时,合金的韧性降低到较低水平。本发明的铜-镍-锡合金的耐腐蚀性也劣化。有利地,可以将0.1%重量至1.5%重量范围的锌含量添加到本发明中。可选地,可以向本发明的铜-镍-锡合金中加入高于污染限度高达最大0.25%重量的小比例的铅。在本发明特别优选的有利实施方案中,铜-镍-锡合金除了任何不可避免的污染外不含铅,这符合当前的环境标准。在这方面,预期铅含量高达pb最大的0.1%重量。以硼硅酸盐和/或硼磷硅酸盐和磷硅酸盐形式的含si相和含b相的形成不仅导致本发明的合金显微结构中孔隙和裂纹含量的显著降低。这些硅酸盐基相也在构件上起到磨损保护和腐蚀保护涂层的作用。在由本发明的铜-镍-锡合金制成的构件上的粘合磨损应力期间,合金元素锡对摩擦配对件之间的所称摩擦层的形成起特别的作用。特别是在混合摩擦条件下,当材料的空运行性能变得越来越重要时,这种机理是重要的。摩擦层导致摩擦配对件之间的纯金属接触面积的大小减小,这防止了元件的焊接或微振磨损。由于现代发动机、机器和机组的效率提高,甚至出现了更高的操作压力和操作温度。特别是在其中目标是燃料的更完全燃烧的新开发的内燃机中观察到这一点。除了内燃机周围空间的升高温度之外,还存在在滑动轴承体系运行期间发生的热量的演变。由于轴承操作中的高温,在由本发明的合金制成的部件中,类似于在铸造和热成形期间,形成以硼硅酸盐和/或硼磷硅酸盐和磷硅酸盐形式的含si相和含b相。这些化合物还增强了主要由合金元素锡而形成的摩擦层,这导致由本发明的合金制成的滑动元件的耐粘合磨损性的增加。因此,本发明的合金确保了耐磨损性和耐腐蚀性的组合。这种性能的组合导致所要求的对摩擦磨损机理的高抗性和对摩擦腐蚀的高材料抗性。以这种方式,本发明具有极好的适用性,可用作滑动元件和插头连接器,因为它具有高度的耐滑动磨损性和耐称为微振磨损的振动摩擦磨损性。除了第三类硬颗粒对增加本发明的摩擦磨损的耐磨性和耐粘合性机理的重要贡献之外,第三类硬颗粒对增加抗振性起着至关重要的作用。与第二类硬颗粒一起,第三类硬颗粒构成了疲劳裂纹扩展的障碍,所述疲劳裂纹可以特别是在振动摩擦磨损(称为微振磨损)下被引入应力构件。因此,关于本发明合金的耐振动摩擦磨损(称为微振磨损)的增加,第二类硬颗粒和第三类硬颗粒特别补充了以硼硅酸盐和/或硼磷硅酸盐和磷硅酸盐形式的含si相和含b相的磨损保护作用和腐蚀保护作用。耐热性和抗应力松弛性是用于发生较高温度的最终用途的合金的进一步基本性能。为了确保足够高的耐热性和抗应力松弛性,高密度的细小沉淀物被认为是有利的。在本发明的合金中这种沉淀物是第三类硬颗粒和(cu,ni)-sn体系的连续沉淀物。由于基本上没有孔隙、没有裂纹和没有偏析的均匀和细晶粒的显微结构和第一类硬颗粒的含量,本发明的合金,即使在铸造状态下,也具有高度的强度、硬度、延展性、复合耐磨性和耐腐蚀性。这种性能的组合意味着甚至可以从铸造形式生产滑动元件和引导元件。本发明的铸造状态还可以另外用于生产配件的壳体和水泵、油泵和燃料泵的壳体。本发明的合金还可用于造船的螺旋桨、翼、螺钉和轮毂。本发明的进一步加工的变型可发现用于具有特别高的复杂的和/或动态的构件应力的应用领域的用途。本发明的铜-镍-锡合金的优异的强度性能和耐磨性以及耐腐蚀性意味着可能的进一步用途。因此,本发明适用于在用于养殖海水栖息生物(水产养殖)的结构中的金属制品。此外,本发明可用于生产海事行业和化学行业中所需的管道、密封件和连接螺栓。对于本发明的合金来生产打击乐器的用途,该材料具有重要意义。特别迄今为止是高质量的钹在它们通常通过钟或壳转换成最终形状之前,通常通过热成形和至少一次退火操作由通常含锡的铜合金生产。随后,在材料去除最终处理之前,再次对钹进行退火。因此,钹的各种变型(例如节奏镲、踩镲、吊镲、中国钹、镲片和效果钹)的生产需要材料的特别有利的热成形性,这由本发明的合金确保。在本发明化学组分的范围限度内,金属基材料和不同硬颗粒的相的不同显微结构组分可以在很宽的范围内设定。以这种方式,甚至从合金的角度来看也可以影响钹的声音特性。特别是对于复合滑动轴承的生产,本发明可以用于通过连接方法应用于复合材料配对件。因此,本发明的片材、板材或带材与优选地由淬火和回火钢制成的钢筒或钢带之间的复合生产可以通过锻造、钎焊或焊接可选地在温度范围为170℃至880°c内进行至少一次退火操作来实现。例如,同样可以通过轧制包覆、感应或传导轧制包覆或通过激光轧制包覆,同样可选地在170至880℃的温度范围内进行至少一次退火操作来生产复合轴承杯或复合轴承衬套。在本发明的合金中形成显微结构产生了用于生产复合滑动元件(例如复合轴承杯或复合轴承衬套)的进一步选择。例如,可以通过热浸镀锡或电解镀锡、溅射或通过pvd方法或cvd方法,在本发明的基体上施加用作轴承操作中的运行层的锡或富sn材料的涂层。通过这种方式,诸如复合轴承杯或复合轴承衬套的高性能复合滑动元件也可以制成为三层体系,轴承衬垫由钢制成,实际轴承由本发明的合金制成,以及运行层由锡或富含sn的涂层制成。该多层体系对滑动轴承的适应性和磨合的容易性具有特别有利的影响,并且改善了外来颗粒和磨料颗粒的嵌入性,而没有即使在对滑动轴承的热或热机械下由于各个层的边界区中的孔形成和裂纹形成而导致的层复合体系的重叠所造成的损坏。通过使用本发明的合金,特别是在强度、弹性和抗应力松弛性方面,可以将铜-镍-锡材料的巨大潜力利用于电子和电气工程中的镀锡构件、线元件、引导元件和连接元件。因此,本发明的显微结构减少了本发明的合金与镀锡之间的边界区中的孔形成和裂纹形成的破坏机理,即使在升高温度下也是如此,这抵消了构件的电通道阻力的任何增加或甚至镀锡的分离。由在每种情况下均具有高达约10%重量的ni含量和sn含量的传统的铜-镍-锡捏和合金制成的半成品和构件的机械加工,由于材料的可移除性不足,是非常难以实现的。因此,特别是长切屑的出现导致长的机器停机时间,因为必须首先用手从机器的加工区移除切屑。相比之下,在本发明的合金中,不同的硬颗粒用作切屑破碎机。由此产生的短脆性切屑和/或缠结切屑有利于材料的可移除性,因此,由铸造状态和本发明合金的进一步加工状态制成的半成品和构件具有更好的机加工性。表1至10阐明了本发明的一个重要的加工实施例。本发明的铜-镍-锡合金和参考材料的铸造板通过连铸铸造生产。从表1上可以看出铸件的化学组分。表1显示了加工实施例a和参考材料r的化学组分。加工实施例a的特征在于ni含量为6.0%重量、sn含量为5.75%重量、si含量为0.3%重量、b含量为0.15%重量、p含量为0.070%重量和余量为铜。参考材料r,即传统的铜-镍-锡-磷合金,具有5.78%重量的ni含量、5.75%重量的sn含量、0.032%重量的p含量,余量为铜。表1:加工实施例a和参考材料r的化学组分(以%重量计)合金cunisnsibpa余量6.05.750.30.50.070r余量5.785.75--0.032参考材料r的连铸板的显微结构具有气孔和收缩孔,以及特别是在晶界处的富sn偏析。与参考材料r相比,由于结晶晶种的作用,加工实施例a的连铸件具有均匀固化的、无孔和无偏析的显微结构。加工实施例a的铸造状态的金属基材料由固体铜溶液组成,基于整体显微结构,有约10%体积至15%体积的岛形式的间生的第一相成分,所述第一相成分可通过经验式cuhniksnm报告,并且具有以2-6个原子%计的元素含量的比率(h+k)/m。可以检测具有比率(h+k)/m为3.4和4的化合物cuni14sn23和cuni9sn20。在金属基材料中以岛的形式间生,基于整体显微结构,有约5%体积至10%体积是第二相成分,所述第二相成分可以通过经验式cupnirsns报告,并具有以10-15个原子%计的元素含量的比率(p+r)/s。化合物cuni3sn8和cuni4sn7经检测具有11.5和13.3的比率(p+r)/s。金属基材料的第一相成分和第二相成分主要在结晶晶种的区中结晶并包裹它们。加工实施例a的铸造状态的第一类硬颗粒的分析对做为含si相和含b相代表的化合物sib6、对做为ni-si硼化物代表的ni6si2b、对做为ni硼化物代表的ni3b、对做为ni磷化物代表的ni3p和对做为ni硅化物代表的ni2si给出指示,这些化合物单独地存在于显微结构中和/或做为加成化合物和/或混合化合物存在。此外,这些硬颗粒被锡和/或金属基材料的第一相成分和/或第二相成分包裹。在铸造工作实例a的过程中,在初级铸造晶粒中形成子结构。本发明的加工实施例a的铸造显微结构中的这些亚晶粒的晶粒尺寸小于10μm。由于本发明的加工实施例a的显微结构中沉淀的亚晶粒结构和硬颗粒,铸造状态的硬度hb在156处远高于r的连铸件的94hb的硬度(表2)。表2:在400℃/3h/空气下经过时效硬化的铸造状态和合金a和r状态的硬度hb2.5/62.5同样显示在表2中是在400℃下经过3小时持续时间的时效硬化的合金a和r的连铸件上确定的硬度值。在参考材料r的其最大处是硬度从94升至145hb。硬化特别归因于显微结构中富sn相偏析的热活化形成。富锡相成分在工作实例a的显微结构中的硬颗粒区中以更精细的形式沉淀出来。因此,硬度从156hb至176hb的提升并不显著。本发明的一个目的是尽管引入了硬颗粒,但仍保持常规铜-镍-锡合金的良好冷成形性。为了验证达到此目标的程度,制造程序1根据表3进行。该制造程序由冷成形和退火操作的一个循环组成,其中冷轧步骤各自以最大可能的冷成形程度进行。由于加工实施例a的铸造状态的高硬度,将其在740℃的温度下煅烧,持续2小时,然后在水中以加速的方式冷却。这导致a和r的铸造状态关于强度和硬度的性能的同化。对于加工实施例a可实现的冷成形度ε为60%和91%强调了本发明的合金尽管含有硬颗粒,但仍可实现甚至超过传统的铜镍锡合金r的形状变化性能的事实。.在两个冷成形步骤之间的退火(表3中的序号4)中也发现了参考材料r对于富sn偏析形成的热敏感性。因此,用于合金a的冷轧板的中间退火的740℃的退火温度对于r必须降低到690℃。表3:由加工实施例a和参考材料r的连铸板制成的带材的制造程序1在进行制造程序1之后,在表4中列出的最后的冷轧操作之后和时效硬化完成之时确定材料a和r的带材指数。显而易见的是,在300℃下冷轧和时效硬化的加工实施例a的带材的强度和硬度高于参考材料带材r的相应性能。受益于高含量的硬颗粒,超过约400℃的温度,发生合金a的显微结构的再结晶。这种再结晶导致强度和硬度下降,因此不能表现出沉淀硬化和亚稳线偏析的效果。在450℃的时效硬化之后,进一步加工的加工实施例a的显微结构包括第二类硬颗粒(图3中标记为3)。此外,在进一步加工的合金a的显微结构中沉淀出更多的相。这些包括在图3中标识为4的(cu,ni)-sn体系的连续沉淀物和第三类的硬颗粒。第三类硬颗粒的尺寸小于3μm是本发明的进一步加工的合金的特征。对于本发明的进一步加工的加工实施例a,在450℃的时效硬化后,其实际上小于1μm(图4中标记为5)。表4:经过制造程序1后(表3),合金a和r的冷轧和时效硬化带材的晶粒尺寸、电导率和机械指数■=尚未完全再结晶为了降低冷成形性和再结晶温度对各合金性能的影响,进行了进一步的制造程序。该制造程序2追求的目的是在对于冷成形程度和退火温度的每种情况下使用相同的参数,通过冷成形和退火操作加工材料a和r的连铸板以得到带材(表5)。由于加工实施例a的铸造状态的高硬度,其在第一次冷轧步骤之前,在740℃的温度下再次煅烧2小时的持续时间,然后在水中以加速方式冷却。表5:由加工实施例a和参考材料r的连铸板制成的带材的制造程序2在最后一次冷轧步骤至3.0mm的最终厚度后,加工实施例a的带材具有最高的强度值和硬度值(表6)。在400℃下进行3小时的时效硬化操作,由于显微结构的亚稳线偏析,强度rm(从498mpa到717mpa)和rp0.2(从439mpa到649mpa)的升高和硬度hb的升高(从166mpa到230mpa)对于合金r来说是最清楚的。然而,合金r的时效硬化状态的显微结构非常不均匀,具有5到30μm之间的晶粒尺寸。而且,参考材料r的时效硬化状态的显微结构由(cu,ni)-sn体系的不连续沉淀物标记(在图1和图2中标记1)。在参考材料r的进一步加工状态的显微结构中还存在ni磷化物(在图1和图2中标记为2)。相比之下,本发明的加工实施例a的时效硬化带材的显微结构非常均匀,具有2至8μm的晶粒尺寸。而且,即使在450℃,时效硬化3小时,然后空气冷却后,加工实施例a的结构缺少不连续的沉淀物。相比之下,第二类硬颗粒在显微结构中是可检测的。这些相在图5和图6中标记为3。此外,在进一步加工的合金a的显微结构中已经沉淀出进一步的相。这些包括图5中标记为4的(cu,ni)-sn体系的连续沉淀物和第三类硬颗粒。对于本发明的进一步加工的加工实施例a,在450℃时效硬化后的第三类硬颗粒的尺寸甚至小于1μm(图6中标记为5)。由于显微结构的亚稳线偏析,在400℃/3h/空气时效硬化后,合金a的带材的强度rm和rp0.2呈现675mpa和600mpa的值。因此,rm和rp0.2低于合金r的相应时效硬化状态的指数。如果r的强度水平是特殊要求,则可以在本发明的合金中添加更高比例的合金元素镍。表6:经过制造程序2后(表5),合金a和r的冷轧和时效硬化带材的晶粒尺寸、电导率和机械指数■=非均质的下一步包括合金a和r的连铸件的热成形性的测试。为此,铸造板在720℃的温度下热轧(表7)。对于冷成形和中间退火的进一步加工步骤,采用制造程序2的参数。表7:由加工实施例a和参考材料r的连铸板制成的带材的制造程序3在参考合金r的铸造板的热轧期间,甚至几次道次之后形成深热裂纹,这导致板通过破裂而失效。相比之下,本发明的加工实施例a的铸造板可热轧而没有损坏,并且可以在多次冷轧工艺和煅烧工艺之后可以被制造成3.0mm的最终厚度。时效硬化的带材的特性(表8)主要地与通过制造程序2(标签6),未经热成形制造的带材的特性相对应。同样可比较的是由本发明合金的加工实施例a制成的带材的显微结构,所述带材是在有热成形步骤和没有热成形步骤的情况下制造的。因此,图7和图8显示了由加工实施例a制成的带材的均匀结构,通过热成形阶段和随后在400℃/3h/空气冷却的时效硬化操作制造该带材。在图中7和图8中,标记为3的第二类硬颗粒再次显而易见。另外,图7显示了标记为4的(cu,ni)-sn体系的连续沉淀物和第三类硬颗粒。在工作实例a的进一步加工的变型的显微结构中,第三类硬颗粒实际上呈现小于1μm的尺寸(在图8中标记为5)。在加工实施例a的该进一步加工状态中的第二类硬颗粒和第三类硬颗粒的分析对做为含si相和含b相代表的化合物sib6、对做为ni-si硼化物代表的ni6si2b、对做为ni硼化物代表的ni3b、对做为ni磷化物代表的ni3p以及对做为ni硅化物代表的ni2si再次给出了指示,这些化合物单独地存在和/或做为加成化合物和/或混合化合物存在在显微结构中。此外,这些硬质颗粒被(cu,ni)-sn体系的沉淀物包裹。表8:经过制造程序3后(表7),合金a的冷轧和时效硬化带材的晶粒尺寸、电导率和机械指数在设施、装置、发动机和机械的构造中,许多应用需要具有相对高尺寸的构件。例如,滑动轴承领域经常出现这种情况。相应构件的生产需要具有适当大尺寸的前体材料。由于无限大型铸件的可生产性有限,因此,如果可能的话,有必要也通过小程度的冷成形来建立所需的材料特性。表9列出了在制造程序4的过程中使用的工艺步骤。制造操作通过冷成形和退火操作的一个循环实现。由于参考材料r和加工实施例a的铸造状态的相对高的强度和硬度的常规连铸中确定的温度敏感性,在740℃的第一次冷轧操作之前仅煅烧合金a的铸造板。对合金r的铸造板和合金a的退火铸造板上的第一次冷轧操作在成形度ε为16%的情况下实施。在690℃下进行退火操作,然后进行ε为12%的冷轧操作。最后,带材的时效硬化发生在350℃、400℃和450℃的温度下。表9:制造程序4在ε=16%的第一冷轧步骤中低程度冷成形与随后在690℃下的退火操作一起不足以消除参考材料r的树枝状和粗晶显微结构。而且,这种热机械处理增强了具有富sn偏析的合金r的晶界覆盖。跨越富sn偏析所覆盖的r的晶界和跨越树枝状结构,从带材的表面深入到带材内部的裂纹在第二次冷轧步骤期间形成。加工实施例a的带材的无裂纹和均质的显微结构的特征在于第二类硬颗粒和第三类硬颗粒的排列。与前述制造程序之后的情况一样,即使在该制造程序4之后,第三类硬颗粒的尺寸小于1μm。在最后一次冷轧操作之后和时效硬化操作之后所得到的带材的特性显示在表10中。由于高密度的裂纹,不可能从材料r的带材中取出未损坏的拉伸样品。因此,可以仅对这些带材进行金相学分析和硬度测量。加工实施例a具有高度的时效硬化性,这通过显微结构的沉淀硬化和亚稳线偏析的机制的相互作用来表现。因此,由于在400℃下从517mpa至639mpa和481mpa至568mpa的时效硬化,指数rm和rp0.2增加。表10:经过制造程序4后(表9),合金a和r的冷轧和时效硬化的带材的晶粒尺寸、电导率和机械指数■=树枝状,具有富sn偏析因此,可以说明,通过化学组分的变化、冷成形操作的成形程度以及通过时效硬化条件的变化,可以调整沉淀硬化的程度和本发明显微结构的亚稳线偏析达到所需的材料性能的程度。以这种方式,可以特别地使本发明的合金的强度、硬度、延展性和电导率与所设想的使用领域一致。附图标记列表1(cu,ni)-sn体系的不连续沉淀物2ni磷化物3第二类硬颗粒4(cu,ni)-sn体系和第三类硬颗粒的连续沉淀物5第三类硬颗粒当前第1页12