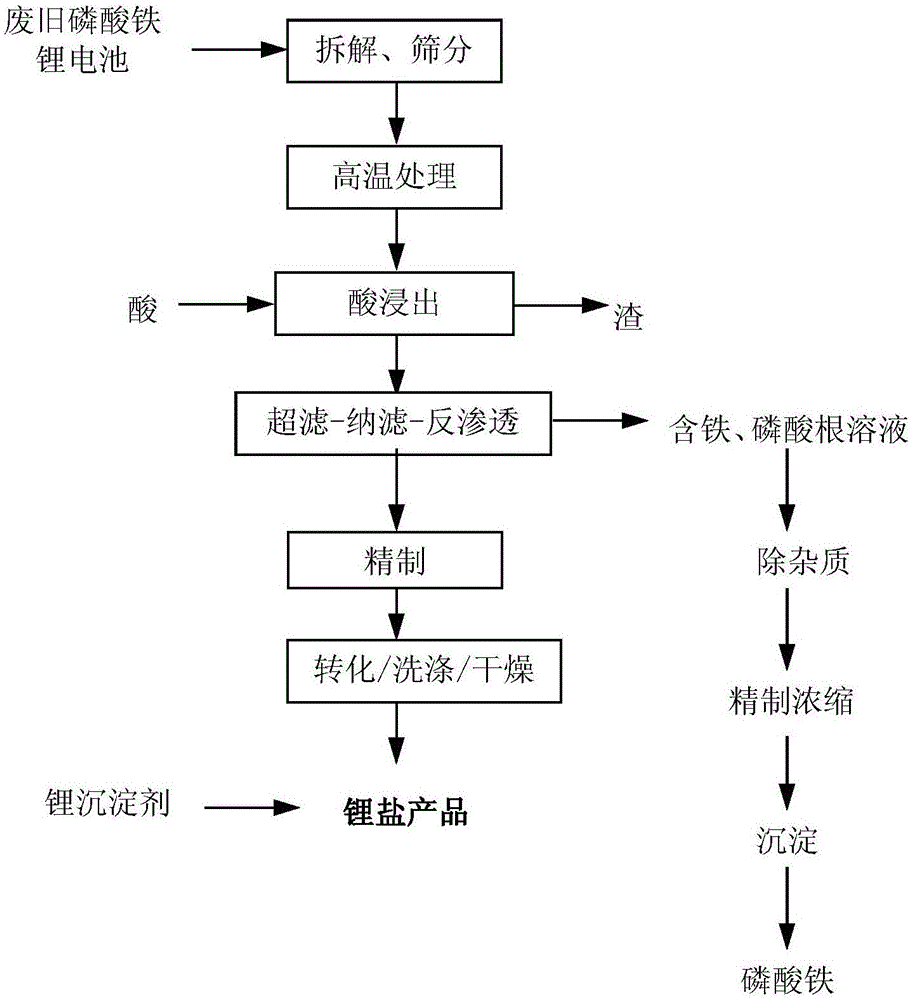
本发明涉及一种从废旧磷酸铁锂电池中回收锂的方法及相应的系统,属于锂电池回收
技术领域:
。
背景技术:
:锂及其化合物是国民经济和国防建设中具有重要意义的战略物资,也是与人们生活息息相关的新型绿色能源材料。锂离子电池作为一种新型化学电源,已成为3c电子产品的主要能源,占据消费电子市场80%以上的份额。近年来锂电技术的持续进步,能量密度的提升,在新能源汽车和储能电源领域需求大幅增加,带动了锂离子电池产销同比大幅增长。近年来锂电技术的持续进步,能量密度的提升,在新能源汽车和储能电源领域需求大幅增加,带动了锂离子电池产销同比大幅增长。2016年中国锂电池的产量达到78.42亿只,同比增长40%,其中动力电池产量达到29.39gwh,超过3c电池产量,成为最大的消费端。随着纯电动汽车的推广和普及,锂离子电池市场将继续保持高速增长,2017年中国锂电市场规模达到82gwh,未来三年复合增长率将为25%。在国内动力电池磷酸铁锂和电池和三元电池为主流,磷酸铁锂电池因安全性能突出和成本较低在大型公共汽车上使用较多,具有较强的竞争优势。然而锂离子电池实际使用中充放循环在500-1000次左右,寿命年限在3-5年。可以预见到2020年前后,国内将迎来废旧锂电池的报废高峰。虽然报废的锂离子电池不含铅、镉、汞等重金属,对环境污染相对较小,但是含有钴、镍、锰、锂等有价金属和六氟磷酸锂等有毒有害物质,处置不当易造成严重的污染和资源浪费。废弃锂离子电池中含有大量的稀贵金属,具有显著的经济效益。因此如何科学的绿色的高效的从废旧锂电池中回收锂等有价金属,已成为当前回收领域的技术热点。废旧锂电池的回收技术较多,早期的回收技术只关注于某些经济价值最高的金属元素的提纯,方法比较单一,具有代表性的就是回收废旧磷酸铁锂,没有综合回收锂。而当前对废旧锂电池的回收技术主要集中于湿法冶金、火法冶金两个方面,这些方法都实现了从废旧锂电池中回收有价金属元素或者合成前驱体。使用最多的方法是火法-酸浸出或者碱溶-酸浸出,再结合沉淀、电化学、萃取等方式回收有价金属元素。火法冶金主要使用高温煅烧去除有机物和粘结剂,然后再筛分、磁选、除杂、浸出,纯化得到目标产品。湿法冶金法碱溶-酸浸出-萃取镍钴锰工艺技术中,主要采用碱溶酸浸出然后采用分步沉淀或者萃取法回收有价金属元素,其中使用的碱主要有氢氧化钠、氢氧化钾;酸分为无机酸和有机酸,例如常见的无机酸盐酸、硫酸、硝酸甚至磷酸,有机酸有柠檬酸、苹果酸等,使用的萃取剂有p204、p507等有机溶剂,回收的产品多为硫酸盐。虽然溶剂萃取法萃取效率高,得到的产物纯度高,但是有机溶剂或多或少的存在着溶损且易挥发污染环境,造成二次污染,另外萃取法成本较高,在工业生产中存在着局限。又如由于镍、钴等电位相近,电沉积技术中镍钴会产生同步沉积,形成钴镍合金,影响后续的纯化,制约了扩大化的应用。再者,现有的废旧电池回收工艺基本上都是沉淀铁,然后纯化含锂溶液。该过程特别繁琐,需要分4-5阶段调节ph值,耗用大量酸碱且工艺冗长,不易精确控制。磷酸铁锂电池的回收中利用高温煅烧再生的方法较多,如中国专利cn105375079a和cn102288707a中将磷酸锂电池拆解、分离出正极片,然后添加锂源或者碳源,混合均匀后直接进行高温固相烧结,得到磷酸铁锂正极材料。该工艺条件苛刻,流程复杂,修复的正极材料性能稳定性有待进一步验证。还有业界研究人员采用碱溶酸浸+沉淀等湿法冶金技术分离提纯锂,比如中国专利cn102956936a中废旧磷酸铁锂动力电池拆解得到正极片,经过高温焙烧去除粘结剂,将焙烧渣酸浸出得到酸浸渣和酸浸液,将酸浸渣继续碱浸,得到碱浸出液,将加入硝酸锂,固液分离得到磷酸锂产品。该发明锂收率达到了94%,但是产生了较多的碱浸渣和酸浸液,带来环境风险,且产品为磷酸锂,经济价值相对较低。其他方法如离子交换法、硫化细菌浸出等都成功的将有价金属元素回收,但是这些方法都存在着一定的局限,如离子交换法操作比较复杂,步骤比较繁琐,只适合少量离子的分离提纯;硫化细菌浸出技术细菌的培养、使用条件苛刻,难于工业化等因素都制约了技术的应用推广。技术实现要素:本发明的主要目的在于提供一种从废旧磷酸铁锂电池中回收锂的方法及系统,从而克服了现有技术中的不足。为实现上述发明目的,本发明采用了如下技术方案:本发明实施例提供了一种从废旧磷酸铁锂电池中回收锂的方法,其包括:从废旧磷酸铁锂电池中拆解出正极片;去除所述正极片中的粘结剂,再经酸溶浸出所述正极片中的有价金属元素,获得酸化浸出液;利用超滤膜对所述酸化浸出液进行超滤处理;利用纳滤膜技术,将酸化浸出液中的锂离子与不同于锂离子的其它阳离子分离,获得含锂溶液和含有其它阳离子的溶液,再采用反渗透技术分别对含锂溶液、含有其它阳离子的溶液进行浓缩富集,所述其它阳离子包括铁离子;以及,采用锂沉淀剂使所述含锂溶液中的锂离子沉淀析出,并采用碱性物质使所述含有其它阳离子的溶液中的铁离子沉淀析出,实现锂的回收。在一些实施例中,所述从废旧磷酸铁锂电池中回收锂的方法具体包括:(1)对废旧磷酸铁锂电池进行放电、拆解、分类,获得正极片;(2)对所述正极片进行高温处理,至少用于去除所述正极片中的粘结剂;(3)将经高温处理的正极片与酸性物质持续接触,使所述正极片中的有价金属元素浸出,获得酸化浸出液;(4)将所述酸化浸出液分别经过超滤膜、纳滤膜和反渗透膜,获得浓缩后的含锂溶液和含有其它阳离子的溶液;(5)向所述含锂溶液中加入锂沉淀剂,反应得到锂沉淀物;(6)对所述含有其它阳离子的溶液进行除杂处理,之后加入碱性物质,反应得到铁沉淀物。本发明实施例还提供了一种从废旧磷酸铁锂电池中回收锂的系统,其包括:拆分机构,其能够对废旧磷酸铁锂电池进行拆解、分类,获得正极片;酸化浸出机构,其能够使所述正极片中的有价金属元素浸出,获得酸化浸出液;超滤-纳滤-反渗透联用系统,其包括超滤膜、纳滤膜和反渗透膜,至少用于将酸化浸出液中的锂离子与其它阳离子分离、浓缩;锂沉淀机构,其至少用于使锂离子沉淀析出;铁沉淀机构,其至少用于使其它阳离子中的铁离子沉淀析出。较之现有技术,本发明的有益效果在于:1)本发明提供的从废旧磷酸铁锂电池中回收锂的方法锂分离技术先进,分离效果好,采用超滤-纳滤-反渗透联用的方式优先使锂离子与其他二价、三价阳离子分离,简化工艺流程,且该过程为物理过程,不会引入有机物或者杂质离子;2)本发明提供的从废旧磷酸铁锂电池中回收锂的方法分离提纯理念新,优先采用超滤预处理酸化浸出液去除残留的有机大分子,减少对纳滤膜的污染和堵塞,再在酸化浸出液中分离锂和其他二价、三价金属离子,然后分别再处理含锂和含铁溶液,除杂浓缩得到产品,大大缩短了工艺流程,减少锂离子在繁琐的除杂过程中的夹带损耗,大幅提高锂的回收率;3)本发明采用物理的分离过程能耗较低,其浓缩纯化过程在常温下进行,无相变,无化学反应,不带入其他杂质,分离提纯过程大幅减少酸碱使用量,采用常见的无机酸酸化浸出,减少了成本,以及杜绝了有机萃取剂的使用,能耗低,绿色环保;4)本发明回收的碳酸锂产品纯度高,有价金属离子回收率高。该纳滤膜工艺技术提高产品纯度,杂质离子去除彻底,锂离子综合回收率高;5)本发明配备数显和在线检测设施,全程设备先进,工艺条件容易控制,操作简便,自动化程度高,且易于放大,适于工业化生产应用。6)本发明工艺过程中为闭路循环系统,母液可进行循环使用,不外排废液,减少对环境的二次污染。附图说明图1是本发明一典型实施方案中从废旧磷酸铁锂电池中回收锂的方法的流程示意图。具体实施方式鉴于现有磷酸铁锂废旧锂电池回收效率低、工艺冗长、对环境存在二次污染的不足,本案发明人经长期研究和大量实践,得以提出本发明的技术方案,其主要是包括电池拆解、分类、正极片破碎、热处理、酸浸出、超滤膜-纳滤膜-反渗透分离富集有价金属离子、除杂、沉淀等工艺步骤,利用超滤预处理酸化浸出液去除残留的有机大分子,减少对纳滤膜的污染和堵塞,利用纳滤膜法高效分离锂与其他二价、三价离子,反渗透分别浓缩富集锂离子和铁离子,然后再分别沉淀出碳酸锂和磷酸铁。如下将对该技术方案、其实施过程及原理等作进一步的解释说明。纳滤膜-反渗透联合工艺技术在海水淡化处理、生物医药领域有着广泛的应用。纳滤膜是复合膜,其表而分离层由聚电解质构成,对无机盐具有截留的效果。相关的膜透过理论主要有溶解扩散理论、氢键理论、扩散细孔流动理论、选择吸附细孔流动理论。纳滤膜的过滤性能还与膜的荷电性、膜制造的工艺过程等有关。根据纳滤膜对溶质有不同的选择透过性,对二价离子的截留率要比一价离子高的特点,利用纳滤膜技术分离浸出液中的一价阳离子和二价阳离子,然后再用反渗透分别浓缩一价离子和二价离子的溶液实现锂元素与铁元素的分离与浓缩。该过程大幅减少了酸碱的使用量以及避免了使用有机溶剂萃取等工艺过程,同时结合反渗透浓缩技术,减少溶液浓缩蒸发能耗,可以快速的实现有价金属离子对分离与提纯,具有绿色环保、低能耗、回收效率高的特点,且工艺操作简单,易于放大实现工业化。作为本发明技术方案的一个方面,其所涉及的系一种从废旧磷酸铁锂电池中回收锂的方法,其包括:从废旧磷酸铁锂电池中拆解出正极片;去除所述正极片中的粘结剂,再经酸溶浸出所述正极片中的有价金属元素,获得酸化浸出液;利用超滤膜对所述酸化浸出液进行超滤处理,去除残留的有机物等大分子,减少对后续膜的堵塞和污染;利用纳滤膜技术,将酸化浸出液中的锂离子与不同于锂离子的其它阳离子分离,获得含锂溶液和含有其它阳离子的溶液,再采用反渗透技术分别对含锂溶液、含有其它阳离子的溶液进行浓缩富集,所述其它阳离子包括铁离子;以及,采用锂沉淀剂使所述含锂溶液中的锂离子沉淀析出,并采用碱性物质使所述含有其它阳离子的溶液中的铁离子沉淀析出,实现锂的回收。在一些实施例中,所述从废旧磷酸铁锂电池中回收锂的方法具体包括:(1)对废旧磷酸铁锂电池进行放电、拆解、分类,获得正极片;(2)对所述正极片进行高温处理,至少用于去除所述正极片中的粘结剂;(3)将经高温处理的正极片与酸性物质持续接触,使所述正极片中的有价金属元素浸出,获得酸化浸出液;(4)将所述酸化浸出液分别经过超滤膜、纳滤膜和反渗透膜,获得浓缩后的含锂溶液和含有其它阳离子的溶液;(5)向所述含锂溶液中加入锂沉淀剂,反应得到锂沉淀物;(6)对所述含有其它阳离子的溶液进行除杂处理,之后加入碱性物质,反应得到铁沉淀物。在一些实施例中,所述废旧磷酸铁锂电池主要以磷酸铁锂为正极材料或者磷酸铁锂正极边角料,例如废旧磷酸铁锂动力电池、3c产品以及磷酸铁锂电池生产工序产生的废弃正极片等,但不限于此。在一些实施例中,步骤(2)具体包括:对所述正极片进行煅烧,进行所述高温处理,以去除粘结剂。进一步地,所述煅烧的时间为0.5~6h,煅烧温度为300~800℃。在一些实施例中,步骤(3)具体包括:将经高温处理的正极片浸置于酸性物质中,同时加入双氧水,控制固液比为40~120g/l,并于30~90℃搅拌,使所述正极片中的有价金属元素浸出,获得酸化浸出液。进一步地,所述酸性物质包括盐酸、硫酸、硝酸、磷酸、高氯酸、氢氟酸等中的任意一种或者两种以上的组合,但不限于此。本发明适用范围宽泛,适用了常见的无机酸酸化浸出,减少了成本。进一步地,所述酸性物质的浓度为1~10mol/l。在一些实施例中,步骤(4)具体包括:将步骤(3)所获酸化浸出液分别输入超滤膜、纳滤膜和反渗透膜,其中,所述超滤膜的孔径为优选为工作压力为0.1~1.5mpa,所述纳滤膜的工作压力为0.1~6mpa,单片膜流速为0.1~5l/min,工作ph值为2~10,最终获得浓缩后的含锂溶液和含有其它阳离子的溶液。所述的超滤-纳滤-反渗透技术指采用超滤预处理酸化浸出液去除残留的有机大分子,减少对纳滤膜的污染和堵塞,采用纳滤膜分离锂和其他金属离子,主要用于一价和二价、三价离子分离即锂和铁、磷酸根的分离,采用反渗透膜法浓缩富集含锂溶液,减少浓缩蒸发量,提高锂离子浓度。进一步地,所述纳滤膜的材质包括聚酰胺(pa)、聚砜(ps)、聚乙烯醇(pva)、磺化聚砜(sps)、磺化聚醚砜(spes)、醋酸纤维素(ca)等中的任意两种以上的组合,尤其优选为聚酰胺和聚砜复合膜。进一步地,所述纳滤膜包括板式纳滤膜或卷式纳滤膜。本发明采用两种或者以上的膜聚合复合后组装成板式、卷式等类型的膜组。进一步地,所述纳滤膜膜截留分子量为50~1000道尔顿,具有良好的离子选择性,对二价离子的截留率达到95%以上。进一步地,浓缩后的含锂溶液的浓度在15g/l以上。本发明采用超滤-纳滤-反渗透联用工艺技术,实现锂离子的分离、富集、浓缩减少酸碱使用量。在超滤过程中预处理酸化浸出液去除残留的有机大分子,减少对纳滤膜的污染和堵塞,在纳滤过程中使锂离子进入淡水中,而其他二价及以上离子截留在浓水中,磷酸根和铁离子截留效果好,然后结合反渗透再度浓缩含锂溶液,使锂浓度达到3-10%。该联用过程采用串联或并联相结合的方式进行,提高分离、浓缩效果。在一些实施例中,步骤(5)中所述锂沉淀剂包括碳酸钠、碳酸氢钠或氟化钠等,但不限于此。进一步地,所述锂沉淀物包括碳酸锂、氟化锂,除了碳酸锂、氟化锂也可能是氯化锂、硫酸锂产品等中间产物,可根据实际情况浓缩、转化即可。进一步地,回收的所述锂沉淀物中碳酸锂或氟化锂的含量在99.5wt%以上,铝含量小于0.001wt%,铁含量小于0.001wt%,钠含量小于0.025wt%,镁含量小于0.008wt%。在一些实施例中,步骤(6)具体包括:向步骤(4)所获含有其它阳离子的溶液中加入除铜剂,并调节ph值为3~5,之后加入碱性物质,反应得到铁沉淀物。进一步地,所述除铜剂包括硫化钠、硫化镍、铁粉等中的任意一种或两种以上的组合,但不限于此。进一步地,所述碱性物质包括氢氧化钠、氢氧化钾、氧化钠、氧化钾、氢氧化钙等中的任意一种或两种以上的组合,但不限于此。进一步地,所述碱性物质的浓度为0.5~8mol/l。进一步地,所述铁沉淀物包括磷酸铁,回收的磷酸铁可在下游电池中使用。其中,作为本发明的更为具体的实施案例之一,参见图1所示,所述从废旧磷酸铁锂电池中回收锂的方法可具体包括以下步骤:以废旧磷酸铁锂电池(包括废旧磷酸铁锂动力电池、3c产品以及磷酸铁锂电池生产工序产生的废弃正极片)为原料,经放电、破解、拆除、筛分,得到正极片,高温处理去除粘结剂,经酸溶浸出有价金属元素,将滤液经过超滤膜-纳滤膜-反渗透处理,分别得到含锂溶液和含铁溶液。将含锂溶液经过浓缩到15g/l以上,在加入饱和的锂沉淀剂,沉淀出碳酸锂。经纳滤膜分离得到的含铁溶液,加入除铜剂去除铜离子,调节ph值为3-5,沉淀除去铝等杂质,然后加入碱沉淀出磷酸铁,实现了对锂的回收。浓缩母液可采用循环利用不外排,在循环中适当添加去离子水稀释即可,碳酸锂产品经重结晶、洗涤、干燥后得到的锂产品达到了电池级的要求,可直接回用。本发明实施例的另一个方面还提供了一种从废旧磷酸铁锂电池中回收锂的系统,其包括:拆分机构,其能够对废旧磷酸铁锂电池进行拆解、分类,获得正极片;酸化浸出机构,其能够使所述正极片中的有价金属元素浸出,获得酸化浸出液;超滤-纳滤-反渗透联用系统,其包括超滤膜、纳滤膜和反渗透膜,至少用于将酸化浸出液中的锂离子与其它阳离子分离、浓缩;锂沉淀机构,其至少用于使锂离子沉淀析出;铁沉淀机构,其至少用于使其它阳离子中的铁离子沉淀析出。进一步地,所述系统还包括:高温处理机构,其至少用于对所述正极片进行高温处理,以去除所述正极片中的粘结剂。进一步地,所述系统还包括:除杂机构,其至少用于对含有其它阳离子的溶液进行除杂处理。更进一步地,所述系统可以具体包括粉碎机、酸化槽、超滤-纳滤-反渗透联用装置、马弗炉、结晶器、高速离心机、筛网、磁选机、干燥箱等,但不限于此。综上,本发明采用超滤膜预处理酸化浸出液去除残留的有机大分子,减少对纳滤膜的污染和堵塞,利用纳滤膜技术分离浸出液中的一价阳离子和二价、三价阳离子,然后再用反渗透分别浓缩一价离子和二价、三价离子的溶液实现锂元素与铁元素的分离与浓缩。该过程大幅减少了酸碱的使用量以及避免了使用有机溶剂萃取等工艺过程,同时结合反渗透浓缩技术,减少溶液浓缩蒸发能耗,可以快速的实现有价金属离子对分离与提纯,具有绿色环保、低能耗、回收效率高的特点,且工艺操作简单,易于放大实现工业化。下面结合若干优选实施例及附图对本发明的技术方案做进一步详细说明,显然,所描述的实施例仅仅是本发明一部分实施例,而不是全部的实施例。基于本发明中的实施例,本领域普通技术人员在没有做出创造性劳动的前提下所获得的所有其他实施例,都属于本发明保护的范围。下列实施例中未注明具体条件的试验方法,通常按照常规条件。实施例1以某类型的废旧磷酸铁锂电池为原料。首先将废旧电池放电、拆解、筛选得到正极材料。称取磷酸铁锂正极材料600g在400℃下马弗炉中处理2h后,去除粘结剂,水淬冷并在超声震荡中处理60min,使正极材料和铝箔剥离。采用大网筛孔拆除分离铝箔,铝箔经冲洗处理可直接用于铝材冶炼。得到的黑色细碎渣经2mol/l的硫酸处理,同时加入30%双氧水,控制固液比为100g/l,温度控制在80℃并不断搅拌4h,然后过滤得到有价金属的浸出液。酸浸渣主要为碳粉等酸不溶物。经检测浸出液中的化学成分,结果如下表1所示:表1浸出液中的化学成分(单位:g/l)类别铝磷酸根锂铁so42-含量1.1262.124.5836.64155.23用碱调节酸浸出液ph值至3.5左右,并稀释调节阴阳总离子浓度,控制到60g/l,进入超滤-纳滤-反渗透处理工艺,控制超滤膜的压力为1mpa,纳滤膜的压力为3.5mpa,浓水流速为3.0l/min,铁、磷酸根等离子被膜截留,在浓水侧富集,锂离子则进入淡水中,分别检测得到含锂溶液和其他离子混合溶液。锂离子在淡水中富集,将富集的含锂溶液进一步蒸发,使锂浓度达到30g/l,在85℃条件下加入饱和的碳酸钠沉淀出碳酸锂,经洗涤-重结晶-洗涤-干燥等处理得到电池级碳酸锂,其检测结果如下表2:表2电池级碳酸锂检测结果含铁、磷酸根溶液经铁粉置换除铜、调节ph值至3去除铝,再次调节ph值沉淀磷酸根得到磷酸铁。该工艺流程短,绿色环保,优先分离锂,操作简便,易于大规模生产,碳酸锂产品达到下游电池企业对原料的质量要求。实施例2以某类型的废旧磷酸铁锂电池为原料。首先将废旧电池放电、拆解、筛选得到正极材料。称取磷酸铁锂正极材料800g在450℃下马弗炉中处理2h后,去除粘结剂,水淬冷并在超声震荡中处理60min,使正极材料和铝箔剥离。采用大网筛孔拆除分离铝箔,铝箔经冲洗处理可直接用于铝材冶炼。得到的黑色细碎渣经3mol/l的硫酸处理,同时加入30%双氧水,控制固液比为100g/l,温度控制在80℃并不断搅拌4h,然后过滤得到有价金属的浸出液。酸浸渣主要为碳粉等酸不溶物。经检测浸出液中的化学成分,结果如下表3所示:表3浸出液中的化学成分(单位:g/l)类别铝磷酸根锂铁so42-含量1.1967.114.8937.65169.89用碱调节酸浸出液ph值至2左右,用去离子水稀释调节阴阳总离子浓度,控制到50g/l,进入超滤-纳滤-反渗透处理工艺,控制超滤膜的压力为1.2mpa,纳滤膜的压力为6mpa,浓水流速为5.0l/min,铁、磷酸根等离子被膜截留,在浓水侧富集,锂离子则进入淡水中,分别检测得到含锂溶液和其他离子混合溶液。锂离子在淡水中富集,将富集的含锂溶液进一步蒸发,使锂浓度达到25g/l,在85℃条件下加入饱和的碳酸钠沉淀出碳酸锂,经洗涤-重结晶-洗涤-干燥等处理得到电池级碳酸锂,其检测结果如下表4:表4电池级碳酸锂检测结果含铁、磷酸根溶液经铁粉置换除铜、调节ph值至3.5去除铝,再次调节ph沉淀磷酸根得到磷酸铁。该工艺流程短,绿色环保,优先分离锂,操作简便,易于大规模生产,碳酸锂产品达到下游电池企业对原料的质量要求。实施例3以某类型的废旧磷酸铁锂电池为原料。首先将废旧电池放电、拆解、筛选得到正极材料。称取磷酸铁锂正极材料900g在500℃下马弗炉中处理2h后,去除粘结剂,水淬冷并在超声震荡中处理60min,使正极材料和铝箔剥离。采用大网筛孔拆除分离铝箔,铝箔经冲洗处理可直接用于铝材冶炼。得到的黑色细碎渣经8mol/l的硫酸处理,同时加入30%双氧水,控制固液比为100g/l,温度控制在80℃并不断搅拌4h,然后过滤得到有价金属的浸出液。酸浸渣主要为碳粉等酸不溶物。经检测浸出液中的化学成分,结果如下表5所示:表5浸出液中的化学成分(单位:g/l)类别铝磷酸根锂铁so42-含量1.7571.354.8938.25161.36用碱调节酸浸出液ph值至3.5左右,并稀释调节阴阳总离子浓度,控制到60g/l,进入超滤-纳滤-反渗透处理工艺,控制超滤膜的压力为0.8mpa,纳滤膜的压力为4mpa,浓水流速为3.0l/min,铁、磷酸根等离子被膜截留,在浓水侧富集,锂离子则进入淡水中,分别检测得到含锂溶液和其他离子混合溶液。锂离子在淡水中富集,将富集的含锂溶液进一步蒸发,使锂浓度达到30g/l,在85℃条件下加入饱和的碳酸钠沉淀出碳酸锂,经洗涤-重结晶-洗涤-干燥等处理得到电池级碳酸锂,其检测结果如下表6:表6电池级碳酸锂检测结果含铁、磷酸根溶液经铁粉置换除铜、调节ph去除铝,再次调节ph沉淀磷酸根得到磷酸铁。该工艺流程短,绿色环保,优先分离锂,操作简便,易于大规模生产,碳酸锂产品达到下游电池企业对原料的质量要求。实施例4以某类型的废旧磷酸铁锂电池为原料。首先将废旧电池放电、拆解、筛选得到正极材料。称取磷酸铁锂正极材料1000g在600℃下马弗炉中处理2h后,去除粘结剂,水淬冷并在超声震荡中处理60min,使正极材料和铝箔剥离。采用大网筛孔拆除分离铝箔,铝箔经冲洗处理可直接用于铝材冶炼。得到的黑色细碎渣经2mol/l的盐酸处理,同时加入30%双氧水,控制固液比为85g/l,温度控制在30℃并不断搅拌4h,然后过滤得到有价金属的浸出液。酸浸渣主要为碳粉等酸不溶物。经检测浸出液中的化学成分,结果如下表7所示:表7浸出液中的化学成分(单位:g/l)类别铝磷酸根锂铁cl-含量2.3675.124.9339.61123.24用碱调节酸浸出液ph值至3.5左右,并稀释调节阴阳总离子浓度,控制到60g/l,进入超滤-纳滤-反渗透处理工艺,控制超滤膜的压力为0.5mpa,纳滤膜的压力为3.5mpa,浓水流速4.0l/min,铁、磷酸根等离子被膜截留,在浓水侧富集,锂离子则进入淡水中,分别检测得到含锂溶液和其他离子混合溶液。锂离子在淡水中富集,将富集的含锂溶液进一步蒸发,使锂浓度达到30g/l,在85℃条件下加入饱和的碳酸钠沉淀出碳酸锂,经洗涤-重结晶-洗涤-干燥等处理得到电池级碳酸锂,其检测结果如下表8:表8电池级碳酸锂检测结果含铁、磷酸根溶液经铁粉置换除铜、调节ph值至3去除铝,再次调节ph沉淀磷酸根得到磷酸铁。该工艺流程短,绿色环保,优先分离锂,操作简便,易于大规模生产,碳酸锂产品达到下游电池企业对原料的质量要求。实施例5以某类型的废旧磷酸铁锂电池为原料。首先将废旧电池放电、拆解、筛选得到正极材料。称取磷酸铁锂正极材料900g在800℃下马弗炉中处理0.5h后,去除粘结剂,水淬冷并在超声震荡中处理90min,使正极材料和铝箔剥离。采用大网筛孔拆除分离铝箔,铝箔经冲洗处理可直接用于铝材冶炼。得到的黑色细碎渣经10mol/l的高氯酸处理,同时加入30%双氧水,控制固液比为120g/l,温度控制在80℃并不断搅拌2h,然后过滤得到有价金属的浸出液。酸浸渣主要为碳粉等酸不溶物。经检测浸出液中的化学成分,结果如下表9所示:表9浸出液中的化学成分(单位:g/l)类别铝磷酸根锂铁cl-含量1.9572.124.5635.62135.24用碱调节酸浸出液ph值至3.5左右,并稀释调节阴阳总离子浓度,控制到40g/l,进入超滤-纳滤-反渗透处理工艺,控制超滤膜的压力为1.5mpa,纳滤膜的压力为1.2mpa,浓水流速2.0l/min,铁、磷酸根等离子被膜截留,在浓水侧富集,锂离子则进入淡水中,分别检测得到含锂溶液和其他离子混合溶液。锂离子在淡水中富集,将富集的含锂溶液进一步蒸发,使锂浓度达到25g/l,在80℃条件下加入饱和的碳酸钠沉淀出碳酸锂,经洗涤-重结晶-洗涤-干燥等处理得到电池级碳酸锂。其检测结果如下表10:表10电池级碳酸锂检测结果含铁、磷酸根溶液经铁粉置换除铜、调节ph值至4.5去除铝,再次调节ph沉淀磷酸根得到磷酸铁。该工艺流程短,绿色环保,优先分离锂,操作简便,易于大规模生产,碳酸锂产品达到下游电池企业对原料的质量要求。实施例6以某类型的废旧磷酸铁锂电池为原料。首先将废旧电池放电、拆解、筛选得到正极材料。称取磷酸铁锂正极材料900g在300℃下马弗炉中处理6h后,去除粘结剂,水淬冷并在超声震荡中处理90min,使正极材料和铝箔剥离。采用大网筛孔拆除分离铝箔,铝箔经冲洗处理可直接用于铝材冶炼。得到的黑色细碎渣经1mol/l的硝酸处理,同时加入30%双氧水,控制固液比为40g/l,温度控制在90℃并不断搅拌2h,然后过滤得到有价金属的浸出液。酸浸渣主要为碳粉等酸不溶物。经检测浸出液中的化学成分,结果如下表11所示:表11浸出液中的化学成分(单位:g/l)类别铝磷酸根锂铁含量1.9572.124.5635.62用碱调节酸浸出液ph值至10左右,并稀释调节阴阳总离子浓度,控制到40g/l,进入超滤-纳滤-反渗透处理工艺,控制超滤膜的压力为0.1mpa,纳滤膜的压力为0.1mpa,浓水流速0.1l/min,铁、磷酸根等离子被膜截留,在浓水侧富集,锂离子则进入淡水中,分别检测得到含锂溶液和其他离子混合溶液。锂离子在淡水中富集,将富集的含锂溶液进一步蒸发,使锂浓度达到35g/l,在80℃条件下加入氟化钠沉淀出氟化锂,经洗涤-重结晶-洗涤-干燥等处理得到电池级氟化锂。其检测结果如下表12:表12电池级氟化锂检测结果含铁、磷酸根溶液经铁粉置换除铜、调节ph值至5去除铝,再次调节ph沉淀磷酸根得到磷酸铁。该工艺流程短,绿色环保,优先分离锂,操作简便,易于大规模生产,碳酸锂产品达到下游电池企业对原料的质量要求。综上所述,藉由上述技术方案,本发明采用物理的纳滤膜法优先分离锂,且采用超滤-纳滤-反渗透联用技术回收的碳酸锂纯度高,具有工艺简单、绿色环保、酸碱用量少,膜分离效果好且稳定、易于操作、适用于工业化连续生产特点。此外,本案发明人还参照实施例1-6的方式,以本说明书中列出的其它原料和条件等进行了试验,并同样回收了从废旧磷酸铁锂电池中回收锂,获得了高质量的电池级碳酸锂。需要说明的是,在本文中,在一般情况下,由语句“包括……”限定的要素,并不排除在包括所述要素的步骤、过程、方法或者实验设备中还存在另外的相同要素。应当理解,以上较佳实施例仅用于说明本发明的内容,除此之外,本发明还有其他实施方式,但凡本领域技术人员因本发明所涉及之技术启示,而采用等同替换或等效变形方式形成的技术方案均落在本发明的保护范围内。当前第1页12