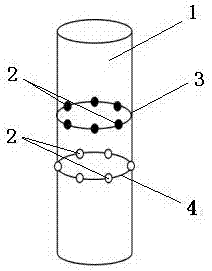
本实用新型涉及一种RH精炼炉供气结构,尤其涉及一种RH精炼炉上升管吹气孔布置结构。
背景技术:
:RH炉是一种对钢液进行循环处理的真空精炼装置,通过上升管鼓入的驱动气体,气泡在上升管中膨胀上升使得整个钢液在装置中循环流动。RH精炼炉真空脱气法是在真空室内进行。脱气时,将真空室底部的两根浸渍管(上升管、下降管)插入钢水中,当真空室抽真空后,钢液在两根管子内上升到一定高度。根据气力提升泵的工作原理,从上升管的下部向钢液吹氩气等驱动气体,使上升管内的钢液产生大量气泡核,钢液中的气体向氩气泡扩散,同时气泡在高温以及低压作用下,迅速膨胀,使其具备提升能力。气泡上浮过程中驱动钢液上升,使钢液呈喷泉状喷入真空室,钢液得到充分脱气。脱气后的钢液沿下降管流回钢包,从而实现了钢液的连续循环脱气处理。目前,上升管吹气孔布置如图1、图2、图3所示。RH精炼炉的驱动气体由吹气孔吹入上升管,上升管的吹气孔一般是在上升管的下部区域分成上下两层且上下层孔位在水平面上错开均衡布置,吹气孔数量根据RH精炼炉的大小设置,一般每层6~8个,且吹气孔垂直穿过上升管壁。这种吹气孔布置方式存在的缺陷:第一,由于每层吹气孔6~8个,吹气孔之间间隔过大,不利于初期气泡之间碰撞长大,也无法控制后期气泡过度长大,导致气体的提升能力下降,单位时间内通过RH真空室的钢液循环流量小,脱气时间长,精炼效率低;其次,吹气孔垂直穿过上升管壁,造成吹入上升管气体的动能损失,导致气体的提升能力下降,钢液循环流量小,脱气时间长,精炼效率低。因此,探索一种RH精炼炉上升管吹气孔布置结构,来增强气体的提升能力,从而增大钢液循环流量,提高RH精炼效率,是RH精炼技术发展趋势。技术实现要素:针对上述现状,本实用新型根据RH精炼设备工作特性,通过水模型实验研究和生产现场试验研究,提供一种RH精炼炉上升管吹气孔布置结构,有效提高气体驱动钢液上升的能力,来增大钢液循环流量,减少脱气时间,从而提高精炼效率。为实现上述目的,本实用新型采用以下技术方案,一种RH精炼炉上升管吹气孔布置结构,包括真空室、上升管、下降管、吹气孔、吹气孔道、供气管道及气源,真空室的底部连接上升管及下降管,吹气孔通过供气管道与气源连接,其特征在于:吹气孔在上升管下部的上下两层水平面的半圆面上左右对应布置6~8个吹气孔,所述吹气孔道在上升管壁内倾斜向上。所述吹气孔道与上升管壁的倾斜角为15°~45°;所述上下两层的吹气孔高度差为130mm~200mm。本实用新型与现有技术相比,其优点是:改变现有的上升管在上下两层的水平面上每层均匀布置6~8个吹气孔的结构形式,设计在上升管的上下两层水平面上每层的半圆面上相对应布置6~8个吹气孔,使每层半圆面上的吹气孔之间间隔缩小,有利于初期大量气泡核之间碰撞长大和有效防止(抑制)后期气泡过度长大,有效的提高驱动气体的提升能力;上升管壁内吹气孔道倾斜向上的好处是气体动能损失最小,由气体携带的动能转化成钢液的势能增加,从而提高气体的提升能力和提升效率,增大钢液循环流量,减少脱气时间,从而提高精炼效率。附图说明图1是现有的RH精炼炉上升管吹气孔布置结构示意主视图。图2是图1的俯视图。图3是现有的RH精炼炉上升管的吹气孔垂直穿过上升管壁的结构示意剖视图。图4是本实用新型RH精炼炉上升管吹气孔布置结构示意主视图。图5是图4的俯视图。图6是本实用新型RH精炼炉上升管的吹气孔倾斜向上穿过上升管壁的结构示意剖视图。图中:1、上升管,2、吹气孔,3、上层,4、下层,5、上升管壁,6、吹气孔道。具体实施方式:下面结合附图和实施例对本实用新型作进一步说明,参见图4、图5、图6,一种RH精炼炉上升管吹气孔布置结构,包括真空室、上升管1、下降管、吹气孔2、吹气孔道6、供气管道及气源,真空室的底部连接上升管1及下降管,吹气孔2通过供气管道与气源连接,其特征在于:吹气孔2在上升管1下部的上下两层水平面的左右半圆面上对应布置6~8个吹气孔2,所述吹气孔道6在上升管壁5内倾斜向上。所述吹气孔道6与上升管壁5的倾斜角为15°~45°;所述上下两层的吹气孔2高度差为130mm~200mm。如图4~图6所示,上升管1的材质为镁铬耐火砖砌成的浸渍管,上升管1共有12个吹气孔2,吹气孔2在上下层水平面的两个半圆面上相对应布置有6个吹气孔2,即上层3的6个吹气孔2集中均匀分布在上升管1的右半圆面上,下层4的6个吹气孔2集中均匀分布在上升管1的左半圆面上,使每层的吹气孔2之间间隔缩小。这种吹气孔布置结构能使上升管1一侧的钢液内产生更多的气泡核,增加碰撞几率,在初期迅速碰撞长大,提高驱动气体的提升能力;同时,上下两层的两个圆面上单侧设置吹气孔2,可以延缓气泡上浮过程中过度长大,避免单纯在每层上增加吹气孔2而使气泡上浮过程中个体过度长大和气泡数量减少,使气泡的个体和数量控制在能使驱动气体的提升能力处于最佳状态。如图6所示,吹气孔道6在上升管壁5内倾斜向上,吹气孔道6与上升管壁5的倾斜角α为15°~45°,最佳倾斜角α为30°。吹气孔道6在上升管壁5内倾斜向上的设计使吹入气体动能损失小,并且由气体携带的动能转化成钢液的势能,提高气体的提升能力和提升效率明显。将上升管1、下降管插入钢水中,与真空室连接好,吹气孔2通过供气管道与气源连接,即可使用。实施例1:应用本实用新型所述上升管吹气孔布置结构在100tRH精炼炉上冶炼耐磨钢NM500钢种。如图4~图6所示,本实用新型在100tRH精炼炉上设置的真空室上升管1的材质为镁铬耐火砖砌成的浸渍管,长度为1600mm,管径为450mm。上层3水平面的吹气孔2距离上升管1下端距离为380mm,下层4水平面的吹气孔2距离上升管1下端距离为230mm,两层吹气孔2之间相距150mm。上升管1共有12个吹气孔2,吹气孔2为直径6mm的气孔,上层3的6个吹气孔2集中均匀分布在上升管1的右半圆面上,下层4的6个吹气孔2集中均匀分布在上升管1的左半圆面上。吹气孔道6在上升管壁5内倾斜向上,吹气孔道6与上升管壁5的倾斜角α为30°。将本实用新型安装在100tRH精炼炉上,烘烤五天,待烘烤完毕,进行洗槽操作。洗槽完毕,对RH炉进行生产。生产的钢种为NM500,钢水进站温度为1605℃,精炼过程中供气量为40Nm3/h,脱气时间为12min,真空度为78.13Pa,合金加入量为100kg,定氢仪测得钢液氢含量为1.8ppm,出站温度为1556℃。探伤显示为一级合格,符合产品质量要求。实施例2:应用本实用新型所述上升管吹气孔布置结构在100tRH精炼炉上冶炼高强度船板CCSE36钢种。如图4~图6所示,本实用新型在100tRH精炼炉上设置的真空室上升管1的材质为镁铬耐火砖砌成的浸渍管,长度为1600mm,管径为450mm。上层3水平面的吹气孔2距离上升管1下端距离为360mm,下层4水平面的吹气孔2距离上升管1下端距离为230mm,两层吹气孔2之间相距130mm。上升管1共有12个吹气孔2,吹气孔2为直径6mm的气孔,上层3的6个吹气孔2集中均匀分布在上升管1的右半圆面上,下层4的6个吹气孔2集中均匀分布在上升管1的左半圆面上。吹气孔道6在上升管壁5内倾斜向上,吹气孔道6与上升管壁5的倾斜角α为20°。本实用新型安装在100tRH精炼炉上,烘烤五天,待烘烤完毕,进行洗槽操作。洗槽完毕,对RH炉进行生产。生产的钢种为CCSE36,钢水进站温度为1614℃,精炼过程中供气量为60Nm3/h,脱气时间为13min,真空度为89.40Pa,合金加入量为98kg,定氢仪测得钢液氢含量为1.6ppm,出站温度为1568℃。探伤显示为一级合格,符合产品质量要求。实施例3:应用本实用新型所述上升管吹气孔布置结构在210tRH精炼炉上冶炼管线钢X65钢种。参考图4~图6,本实用新型在210tRH精炼炉上设置的真空室上升管1的材质为镁铬耐火砖砌成的浸渍管,长度为900mm,管径为600mm。上层3水平面的吹气孔2距离上升管1下端距离为480mm,下层4水平面的吹气孔2距离上升管1下端距离为280mm,两层吹气孔2之间相距200mm。上升管1共有16个吹气孔2,吹气孔2为直径6mm的气孔,上层3的8个吹气孔2集中均匀分布在上升管1的右半圆面上,下层4的8个吹气孔2集中均匀分布在上升管1的左半圆面上。吹气孔道6在上升管壁5内倾斜向上,吹气孔道6与上升管壁5的倾斜角α为35°。本实用新型安装在210tRH精炼炉上,烘烤五天,待烘烤完毕,进行洗槽操作。洗槽完毕,对RH进行生产。生产的钢种为X65,钢水进站温度为1619℃,精炼过程中供气量为150Nm3/h,脱气时间为15min,真空度为62.9Pa,定氢仪测得钢液氢含量为1.9ppm,出站温度为1582℃。探伤显示为一级合格,符合产品质量要求。实施例4:应用本实用新型所述上升管吹气孔布置结构在210tRH精炼炉上冶炼电工钢XG600WR钢种。参考图4~图6,本实用新型在210tRH精炼炉上设置的真空室上升管1的材质为镁铬耐火砖砌成的浸渍管,长度为900mm,管径为600mm。上层3水平面的吹气孔2距离上升管1下端距离为460mm,下层4水平面的吹气孔2距离上升管1下端距离为280mm,两层吹气孔2之间相距180mm。上升管1共有16个吹气孔2,吹气孔2为直径6mm的气孔,上层3的8个吹气孔2集中均匀分布在上升管1的右半圆面上,下层4的8个吹气孔2集中均匀分布在上升管1的左半圆面上。吹气孔道6在上升管壁5内倾斜向上,吹气孔道6与上升管壁5的倾斜角α为45°。本实用新型安装在210tRH精炼炉上,烘烤五天,待烘烤完毕,进行洗槽操作。洗槽完毕,对RH进行生产。生产的钢种为XG600WR,钢水进站温度为1610℃,精炼过程中供气量为230Nm3/h,脱气时间为8min,真空度为93.18Pa,合金加入量为26kg/t钢,定氢仪测得钢液氢含量为1.2ppm,出站温度为1575℃。探伤显示为一级合格,符合产品质量要求。本实用新型上述四个钢种的生产应用实例与改进前上升管1上下两层错开均衡布置6~8个吹气孔2,且吹气孔2垂直穿过上升管壁5的效果比较见表1。表1本实用新型与现有技术比较案例RH炉型钢种供气量Nm3/h脱气时间min钢液氢含量ppm实施例1100tRH精炼炉NM50040121.8比较例1100tRH精炼炉NM50040161.9实施例2100tRH精炼炉CCSE3660131.6比较例2100tRH精炼炉CCSE3660181.8实施例3210tRH精炼炉X65150151.9比较例3210tRH精炼炉X65150202.2实施例4210tRH精炼炉XG600WR23081.2比较例4210tRH精炼炉XG600WR230121.5从表1可以看出,在相同炉型工况条件下,实施例的脱气时间明显缩短,并且钢液氢含量比比较例低,说明采用本实用新型所述上升管吹气孔布置结构增强了气体的提升能力,从而增大钢液循环流量,节约了脱气时间,提高了RH炉精炼效率,降低了生产综合成本。以上具体实施方式仅为说明本实用新型的技术构思及特点,其目的在于让熟悉此项技术的人士能够了解本实用新型的内容并据以实施,并不能以此限制本实用新型的保护范围。凡根据本实用新型精神实质所作的等效变化或修饰,都应涵盖在本实用新型的保护范围之内。当前第1页1 2 3