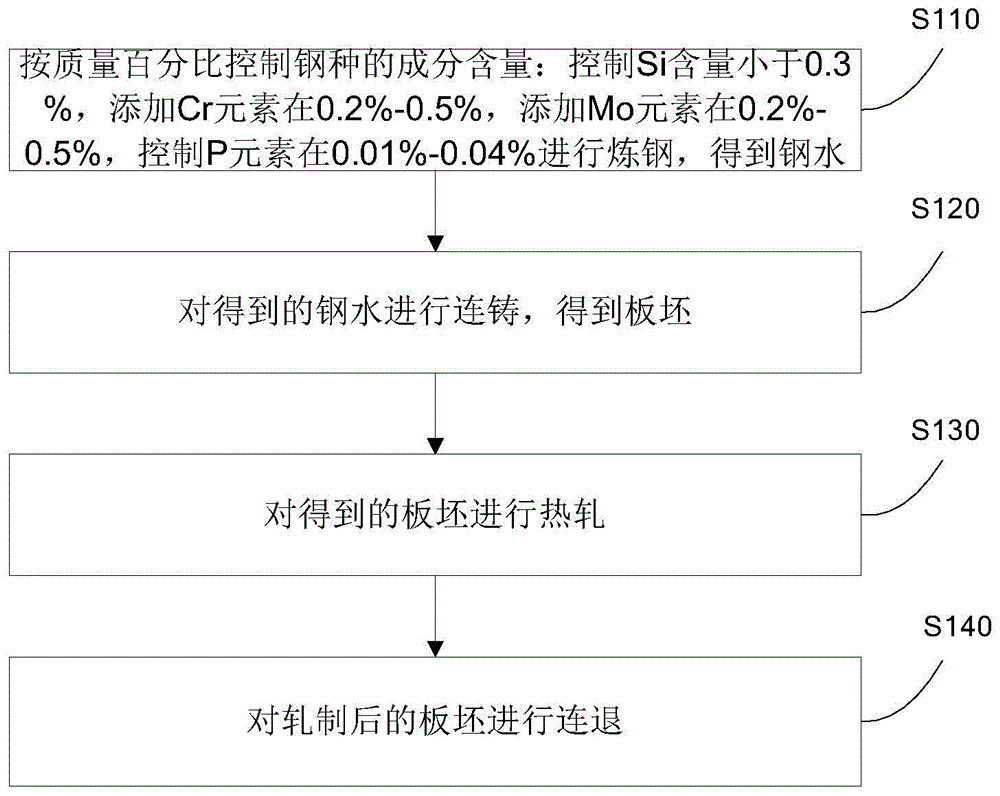
本发明涉及轧钢
技术领域:
,尤其涉及一种高强钢的生产方法。
背景技术:
:在汽车制造领域,汽车零件对钢铁有较高的需求,包括良好的强度、优良的成型性、良好的耐蚀性、可焊接性及涂装性能等。高强钢除了需要满足安全性需求外,表面质量也面临越来越高的要求。高强钢也逐步应用于可视位置的零件,如车门、门槛等位置采用了400mpa级别的高强钢;车门内板采用了590mpa级别的高强钢;内板加强件采用了980mpa-1470mpa的高强钢等。但是,dp及trip钢由于si、cr等易氧化合金元素的添加,表面会产生一系列的色差问题,例如铁皮粘附性增加,红铁皮残留酸洗不净进而遗传到冷轧成品,表现为酸洗后条带色差继而导致冷轧色差缺陷等。这直接限制了钢板在作为可视部件上的使用,成为了瓶颈,为客户带来了麻烦。技术实现要素:本发明通过提供一种高强钢的生产方法,解决了现有技术中存在色差缺陷的技术问题,实现了能有效降低冷轧板色差缺陷的发生率,从而提高产品表面质量的技术效果。本发明提供了一种高强钢的生产方法,包括:按质量百分比控制钢种的成分含量:控制si含量小于0.3%,添加cr元素在0.2%-0.5%,添加mo元素在0.2%-0.5%,控制p元素在0.01%-0.04%进行炼钢,得到钢水;对得到的钢水进行连铸,得到板坯;对得到的板坯进行热轧;对轧制后的板坯进行连退。进一步地,所述对得到的板坯进行热轧,包括:对所述得到的板坯进行加热、粗轧、精轧和卷取。进一步地,在所述加热的过程中,将出炉温度控制在1180℃-1200℃,均热段时间控制在30min-35min,总在炉时间控制在150min-180min。进一步地,在所述精轧的过程中,采用双道次除鳞工艺。进一步地,在所述精轧的过程中,前三轧机机架间冷却水比例为50%,辊缝水开启比例达到80%。进一步地,在所述卷取的过程中,采用前端密集冷却模式或者超快冷冷却模式对热轧板进行冷却。进一步地,在所述卷取的过程中,将卷取温度控制在500℃-600℃。进一步地,在所述对得到的板坯进行热轧之后,还包括:对热轧之后的板坯进行酸洗。进一步地,在所述对热轧之后的板坯进行酸洗之后,还包括:对酸洗之后的板坯进行冷轧。进一步地,在所述酸洗的过程中,将冷轧总体压下率控制在70%以内。本发明中提供的一个或多个技术方案,至少具有如下技术效果或优点:对钢种的成分进行了设计。具体为:在钢种中添加0.3%的si元素进行强化,在高温加热后,添加界面出现明显的锚状钉扎形貌,feo包裹fe2sio4向钢基体内进行浸入,钉扎深度最深可达50μm,内侧铁皮粘附力较好,不易于基体脱落。另外,在钢种中还添加了0.2%-0.5%的cr和0.2%-0.5%的mo,降低了si含量后的网状铁皮的形貌得到明显的削弱,特别在靠近基体的内氧化层富集,网状铁皮链明显断裂弱化。同时,由于mo元素的添加,在基体界面处存在较明显的mo元素富集带,富集深度与内氧化质点相对应。同时,mo元素较少参与内氧化质点的形成,主要起到封闭氧化界面的作用。另外,通过添加p元素,可显著改善铁皮的去除力。fe-si-o系统中含p可以降低该系氧化物的熔点,这主要是因为形成了三元共晶体系:feo-fe2sio4-fe3(po4)2。因此,添加p元素后可显著提高铁皮的去除力,从而降低铁皮的黏附力。综上,本发明解决了现有技术中存在色差缺陷的技术问题,实现了能有效降低冷轧板色差缺陷的发生率,从而提高产品表面质量的技术效果。附图说明图1为本发明实施例提供的高强钢的生产方法的流程图;图2为实施例一中采用本发明实施例提供的高强钢的生产方法后的高强钢冷轧后的表面形貌;图3为实施例二中采用本发明实施例提供的高强钢的生产方法后的高强钢冷轧后的表面形貌。具体实施方式本发明实施例通过提供一种高强钢的生产方法,解决了现有技术中存在色差缺陷的技术问题,实现了能有效降低冷轧板色差缺陷的发生率,从而提高产品表面质量的技术效果。本发明实施例中的技术方案为解决上述问题,总体思路如下:对钢种的成分进行了设计。具体为:在钢种中添加0.3%的si元素进行强化,在高温加热后,添加界面出现明显的锚状钉扎形貌,feo包裹fe2sio4向钢基体内进行浸入,钉扎深度最深可达50μm,内侧铁皮粘附力较好,不易于基体脱落。另外,在钢种中还添加了0.2%-0.5%的cr和0.2%-0.5%的mo,降低了si含量后的网状铁皮的形貌得到明显的削弱,特别在靠近基体的内氧化层富集,网状铁皮链明显断裂弱化。同时,由于mo元素的添加,在基体界面处存在较明显的mo元素富集带,富集深度与内氧化质点相对应。同时,mo元素较少参与内氧化质点的形成,主要起到封闭氧化界面的作用。另外,通过添加p元素,可显著改善铁皮的去除力。fe-si-o系统中含p可以降低该系氧化物的熔点,这主要是因为形成了三元共晶体系:feo-fe2sio4-fe3(po4)2。因此,添加p元素后可显著提高铁皮的去除力,从而降低铁皮的黏附力。综上,本发明实施例解决了现有技术中存在色差缺陷的技术问题,实现了能有效降低冷轧板色差缺陷的发生率,从而提高产品表面质量的技术效果。为了更好地理解上述技术方案,下面将结合说明书附图以及具体的实施方式对上述技术方案进行详细的说明。参见图1,本发明实施例提供的高强钢的生产方法,包括:步骤s110:按质量百分比控制钢种的成分含量:控制si含量小于0.3%,添加cr元素在0.2%-0.5%,添加mo元素在0.2%-0.5%,控制p元素在0.01%-0.04%进行炼钢,得到钢水;步骤s120:对得到的钢水进行连铸,得到板坯;步骤s130:对得到的板坯进行热轧;对本步骤进行具体说明,步骤s130包括:对得到的板坯进行加热炉加热、粗轧、精轧和卷取。为了最大限度降低由si元素高温形成的铁橄榄石相液化对铁皮的侵入以及锚状铁皮结构的钉扎深度,在加热的过程中,将出炉温度控制在1180℃-1200℃,均热段时间控制在30min-35min,总在炉时间控制在150min-180min。为了将精轧入口温度控制在轧制允许范围内,在粗轧后采用保温罩。为了保证精轧除鳞效果,在精轧的过程中,采用双道次除鳞工艺。将轧制速度提高到8m/s以上。为了提高下机辊面质量,从而提高热轧带钢表面质量,在精轧的过程中,前三轧机机架间冷却水比例为50%,辊缝水开启比例达到80%。同时,投入轧制润滑工艺,将终轧温度控制在900℃-920℃。为了强化热轧板表层的组织强度,降低表层组织和心部的硬度差,细化热轧板晶粒尺寸,提高钢板表层的抑制冷轧开裂能力,在卷取的过程中,采用前端密集冷却模式或者超快冷冷却模式对热轧板进行冷却。为了进一步细化热轧板的组织晶粒度,抑制次表层条带状组织形成,减小冷轧过程表层轧裂的产生,在卷取的过程中,将卷取温度控制在500℃-600℃。步骤s140:对轧制后的板坯进行连退。对本发明实施例提供的高强钢的生产方法进行具体说明,在对得到的板坯进行热轧之后,还包括:对热轧之后的板坯进行酸洗。对本发明实施例提供的高强钢的生产方法进行进一步说明,在对热轧之后的板坯进行酸洗之后,还包括:对酸洗之后的板坯进行冷轧。为了避免表层和心部由于相界强度差以及热轧组织晶粒尺寸差异而导致的冷轧过程沿晶界开裂情况的发生,在酸洗的过程中,将冷轧总体压下率控制在70%以内。对本发明实施例提供的高强钢的生产方法进行更进一步说明,在对轧制后的板坯进行连退之后,还包括:对连退之后的板坯进行平整。利用本发明实施例提供的生产方法在首钢迁安2250热连轧产线以及首钢顺义酸轧产线上进行了具体实施,进行现场表面质量跟踪。实施例一:钢种成分设计如下表1所示,成分设计仅采取si-cr-mo成分体系,si元素含量高达0.2%,cr元素控制在0.5%,mo元素控制在0.2%,同时添加适量p元素到0.03%,制定的热轧工艺路线如下表2所示。将热轧出炉温度控制在1180℃,在炉时间控制在170min,精轧采用双道次除鳞,精轧入口温度为1000℃,精轧前三机架机架间冷却水比例为50%,辊缝水开启比例达到80%。同时,投入轧制润滑工艺,将终轧温度控制在910℃。卷取采用前端密集冷却模式,将卷取温度控制在580℃,冷轧压下率控制在70%。跟踪冷轧后的表面,表面质量良好无色差缺陷如图2所示。钢种csicrmopdp7800.10.20.50.20.03表1钢种成分设计表2热轧工艺路线实施例二:钢种成分设计如下表3所示,成分设计仅采取si-cr-mo成分体系,si元素含量高达0.2%,cr元素控制在0.2%,mo元素控制在0.5%,同时添加适量p元素到0.02%,制定的热轧工艺路线如下表4所示。将热轧出炉温度控制在1190℃,在炉时间控制在180min,精轧采用双道次除鳞,精轧入口温度为990℃,精轧前三机架机架间冷却水比例为50%,辊缝水开启比例达到80%。同时,投入轧制润滑工艺,将终轧温度控制在900℃。卷取采用前端超快冷冷却模式,将卷取温度控制在570℃,冷轧压下率控制在65%。跟踪冷轧后的表面,表面质量良好无色差缺陷如图3所示。钢种csicrmopdp7800.150.20.20.50.02表3钢种成分设计表4热轧工艺路线【技术效果】1、对钢种的成分进行了设计。具体为:在钢种中添加0.3%的si元素进行强化,在高温加热后,添加界面出现明显的锚状钉扎形貌,feo包裹fe2sio4向钢基体内进行浸入,钉扎深度最深可达50μm,内侧铁皮粘附力较好,不易于基体脱落。另外,在钢种中还添加了0.2%-0.5%的cr和0.2%-0.5%的mo,降低了si含量后的网状铁皮的形貌得到明显的削弱,特别在靠近基体的内氧化层富集,网状铁皮链明显断裂弱化。同时,由于mo元素的添加,在基体界面处存在较明显的mo元素富集带,富集深度与内氧化质点相对应。同时,mo元素较少参与内氧化质点的形成,主要起到封闭氧化界面的作用。另外,通过添加p元素,可显著改善铁皮的去除力。fe-si-o系统中含p可以降低该系氧化物的熔点,这主要是因为形成了三元共晶体系:feo-fe2sio4-fe3(po4)2。因此,添加p元素后可显著提高铁皮的去除力,从而降低铁皮的黏附力。综上,本发明实施例解决了现有技术中存在色差缺陷的技术问题,实现了能有效降低冷轧板色差缺陷的发生率,从而提高产品表面质量的技术效果。2、在加热的过程中,将出炉温度控制在1180℃-1200℃,均热段时间控制在30min-35min,总在炉时间控制在150min-180min。通过降低出炉温度、缩短在炉时间,一方面可以减少炉生氧化铁皮的生成量,另一方面可以减少铁橄榄石相液化后对氧化铁皮的粘附作用,可大大提高除鳞效果,改善热轧板表面铁皮状态,抑制铁皮残留,提高铁皮和基体界面平直度,避免了酸洗后发麻缺陷的产生,进而抑制了冷轧后色差缺陷的产生。3、在精轧的过程中,通过采用双道次除鳞工艺,保证了精轧除鳞效果。4、在精轧的过程中,前三轧机机架间冷却水比例为50%,辊缝水开启比例达到80%,提高了下机辊面质量,从而提高了热轧带钢表面质量。5、在粗轧后采用保温罩,避免了由于带钢温度过低而造成轧制力升高、堆钢等风险的发生。6、在精轧的过程中,将终轧温度控制在900℃-920℃,不仅降低了轧制力,而且还提高了铁皮塑性。7、在卷取的过程中,将卷取温度控制在500℃-600℃,可以改变组织类型,不仅可以获得期望的组织,而且还可以避免热轧卷强度过高而造成冷轧轧制力过大。本发明实施例深入研究了si、cr、mo、p等元素及其复合作用对带钢高温氧化特性的影响,设计出了适宜冷轧高强钢表面控制的成分体系。另外,还指明了冷轧色差的根本在于带钢冷轧过程浅表层轧裂理论,将热轧红铁皮酸洗后产生的表面粗糙与材料组织特点造成的冷轧过程开裂有机融合,提出了一系列控制措施。另外,还探明了热卷红鳞缺陷遗传、热卷冷却特征、带钢组织特征等因素在浅表层轧裂中的作用,并根据其作用机理制定了控制策略。利用本发明实施例可以在不增加设备的条件下较容易地去除高强钢冷轧后的色差缺陷。此外,本发明实施例还具有方法简单、经济高效、适用性强、效果显著等优点。尽管已描述了本发明的优选实施例,但本领域内的技术人员一旦得知了基本创造性概念,则可对这些实施例作出另外的变更和修改。所以,所附权利要求意欲解释为包括优选实施例以及落入本发明范围的所有变更和修改。显然,本领域的技术人员可以对本发明进行各种改动和变型而不脱离本发明的精神和范围。这样,倘若本发明的这些修改和变型属于本发明权利要求及其等同技术的范围之内,则本发明也意图包含这些改动和变型在内。当前第1页12