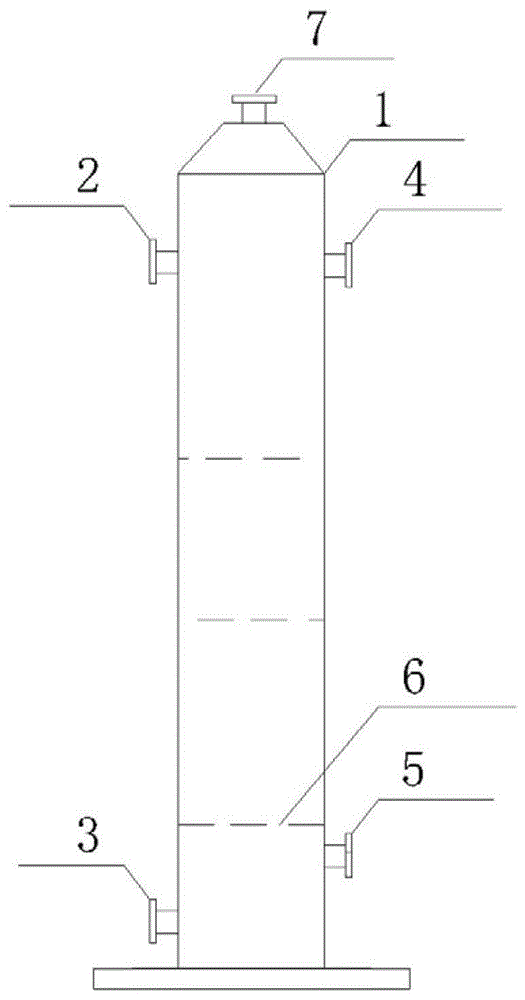
本发明涉及冶金
技术领域:
,尤其涉及一种去除金属原料浸出液中表面活性剂的方法、净化装置及用途。
背景技术:
:白钨矿、黑白钨混合矿、钨细泥、人造白钨、低品位钨钼混合矿、氧化锌、含金属催化剂废料等金属原料已成为金属工业的主要原料。在这些原料处理过程中,经常会加入以表面活性剂为主的选矿药剂,而表面活性剂的存在会对后续的工艺产生各种各样的不良影响。例如,含有表面活性剂的钨矿物原料在浸取制备钨酸钠溶液的过程中,表面活性剂会进入到钨酸钠溶液中,含有表面活性剂的钨酸钠溶液在采用萃取工艺(包括酸性萃取工艺和碱性萃取工艺)生产仲钨酸铵过程中,钨酸钠溶液中的表面活性剂会污染萃取剂,造成萃取剂的损失,或造成萃取时分相困难、产生第三相,从而破坏生产线正常运行甚至导致生产线瘫痪。cn106011504b公开了一种分解白钨矿的方法,包括以下步骤:步骤一:将白钨矿进行研磨,使其粒度小于325目;步骤二:将研磨后的白钨矿与硅酸钠混合,得到混合物;步骤三:将上述混合物置于高温炉中进行焙烧,得到焙烧物;步骤四:对上述焙烧物进行研磨,并水浸出处理,然后进行过滤、烘干操作,即完成白钨矿的分解,可提取钨。cn107287445a公开了一种从铁闪锌矿中真空提取金属锌的方法。首先将铁闪锌矿在空气气氛下、温度为1050~1080℃条件下氧化焙烧生成焙砂;将焙砂与金属铁混合均匀,然后在压强为10~30pa,温度为1050℃~1200℃下恒温蒸馏20~60min,得到金属锌蒸汽,冷凝得到金属锌以及铁渣残留物。该发明首先将铁闪锌矿进行氧化焙烧,矿物中的锌和铁从硫化物转化为氧化物;然后将焙烧产物与金属铁混合,放入真空炉内,在一定的温度和压力条件下,锌以金属蒸汽的形式在冷凝区冷凝,获得金属锌;铁残留于残渣中,作为铁精矿使用,产出的铁可作为还原剂循环使用。cn102730748b公开了一种利用中低品位氧化锌矿和氧化锌、氧化铅共生矿制备氯化铅和硫酸锌的方法,该方法包括以下步骤:(1)将锌矿破碎,磨细后与硫酸铵混合焙烧;(2)焙烧熟料溶出,所得滤液进行沉铁、铝,提锌渣进一步分离铅;(3)沉铁、铝后所得的硫酸锌溶液蒸浓后用于电解;(4)提锌渣用nacl溶液浸出,浸出后所得滤液浓缩,冷却结晶析出pbcl2晶体,nacl溶液返回浸出工序,实现循环利用。以上现有技术中,为了除去金属原料中的表面活性剂,均采用氧化焙烧的方法对金属原料进行处理,即在氧化性气氛下将金属原料在高温下氧化一定时间,从而保证浸出后的金属盐溶液中不含表面活性剂。现有技术的缺点在于焙烧过程温度高导致能耗高,劳动强度大和作业环境差,产生大量难以治理的焙烧烟气从而造成巨大的环境风险。特别是一部分金属原料产量小、价格高,而金属原料批次与批次之间金属含量差别较大,在焙烧过程中多批次金属原料随机混合,会造成浸取时金属原料入冶品位不清楚,从而严重影响后续的配料、浸取等作业过程。为保证金属原料的浸出率,生产上通常过量配入浸取剂,因此又造成浸取剂浪费。此外,焙烧过程还导致一定比例的金属损失,例如,现有技术中钨矿物原料焙烧过程造成的钨损失率约为2.5%,会造成极大的资源浪费,经济性差。因此,本领域亟待开发一种新的去除金属原料浸出液中的表面活性剂的方法,既能够有效去除表面活性剂,又能够降低金属原料的损失、避免浸取剂的浪费,并且具有能耗低、劳动强度低、作业环境良好、无污染气体释放等优点。技术实现要素:针对现有技术的不足,本发明的目的之一在于提供一种去除金属原料浸出液中表面活性剂的方法,所述方法包括如下步骤:对所述金属原料浸出液进行高级氧化处理,得到净化的金属原料浸出液。“高级氧化”指的是通过产生羟基自由基,对难以被普通氧化剂氧化的有机物进行氧化降解的过程。本发明对金属原料浸出液进行高级氧化处理,通过过程产生的羟基自由基将表面活性剂氧化,达到去除金属原料中表面活性剂的目的。相比于直接处理金属原料去除表面活性剂,本发明选择在金属浸出之后再去除表面活性剂,此时表面活性剂均匀分散于浸出溶液中,再进行高级氧化处理可达到更佳的去除效果。同时又能降低金属原料的损失、避免浸取剂浪费,并且具有能耗低、劳动强度低、作业环境良好、无污染气体释放等优点。优选地,针对含碳酸钠的金属原料浸出液,在所述高级氧化处理之前,对所述金属原料浸出液进行冷冻结晶。本发明的优选方案中,在高级氧化步骤之前,进行冷冻结晶步骤,由于大部分金属原料的浸出剂均选用碳酸钠,因此在浸出液中会剩余一部分碳酸根离子,而碳酸根离子对于高级氧化反应具有一定的抑制作用,对此,采用冷冻结晶的方法去除浸出液中的碳酸根离子,避免对高级氧化反应的抑制作用,进一步优化表面活性剂的去除效果。优选地,所述冷冻结晶的温度为-10~10℃,例如-9℃、-8℃、-7℃、-6℃、-5℃、-4℃、-3℃、-2℃、-1℃、0℃、1℃、2℃、3℃、4℃、5℃、6℃、7℃、8℃或9℃等,优选-7~5℃。优选地,所述冷冻结晶具体包括如下步骤:将金属原料浸出液冷冻至-10~10℃,碳酸钠晶体析出后过滤,收集滤液。优选地,所述高级氧化处理的氧化剂包括臭氧、过氧化氢、过硫酸盐和单过硫酸盐中的任意一种或至少两种组合。优选地,所述氧化剂包括臭氧和/或过氧化氢,优选臭氧和过氧化氢。臭氧和过氧化氢两种氧化剂共同作用,能够产生更多的羟基自由基,即具有较高的自由基生成率,可以更彻底地去除表面活性剂。优选地,所述臭氧与所述金属原料浸出液中表面活性剂对应toc的质量比为4~10:1,例如4:1、5:1、6:1、7:1、8:1、9:1、10:1等。toc为总有机碳(totalorganiccarbon,文中简称toc),在本发明中代表表面活性剂对应的总有有机碳。优选地,所述高级氧化处理的温度为0~100℃,例如2℃、5℃、10℃、15℃、20℃、25℃、30℃、35℃、40℃、45℃、50℃、55℃、60℃、65℃、70℃、75℃、80℃、85℃、90℃、95℃或98℃等,优选为25~75℃,进一步优选30~50℃。优选地,所述高级氧化处理的时间为0.25~12h,例如0.3h、0.5h、1h、2h、3h、4h、5h、6h、7h、8h、9h、10h或11h等,优选0.5~3h。优选地,所述高级氧化处理在外加能量场作用下进行。在优选方案中,加入外加能量场,能够促进氧化剂形成羟基自由基,从而更大程度地氧化表面活性剂,去除效果更佳。优选地,所述外加能量场包括紫外光和/或超声。优选地,所述高级氧化处理在催化剂作用下进行。优选地,所述催化剂为非均相催化剂,优选活性炭、二氧化钛、过渡金属负载二氧化钛和过渡金属负载活性炭中的任意一种或至少两种组合。优选地,所述金属原料包括矿物原料。优选地,所述矿物原料包括钨矿物原料、锌矿物原料、铜矿物原料和铁矿物原料中的任意一种或至少两种组合,优选钨矿物原料。优选地,所述金属原料浸出液包括钨酸钠浸出液。优选地,所述钨矿物原料浸出液是通过碳酸钠溶液浸出得到的。优选地,所述金属原料浸出液的ph为7.5~14,例如8、9、10、11、12或13等,优选为8.5~10.5。本发明优选金属原料浸出液的ph为7.5~14,因为许多金属矿相可通过碱溶液浸出分离,而且外加氧化剂在碱性溶液中容易产生强氧化性自由基,例如臭氧、过硫酸钠、臭氧和过氧化氢、臭氧和过硫酸钠等氧化剂或氧化剂的组合,从而高效去除表面活性剂,并且在ph为8.5~10.5时效果最佳。优选地,所述方法具体包括如下步骤:在ph为7.5~14的金属原料浸出液中加入氧化剂,在外加能量场和催化剂的作用下,在0~100℃下进行高级氧化处理0.25~12h,得到净化的金属原料浸出液。本发明的目的之二在于提供一种实现目的之一所述方法的装置,所述净化装置包括高级氧化反应器1,在所述高级氧化反应器的上部设置有金属原料浸出液加入装置2、废气排出装置7,在所述高级氧化反应器的下部设置有净化液排出装置3、至少一个臭氧加入装置5,在所述高级氧化反应器的内部设置有至少一个曝气装置6,所述曝气装置与所述臭氧加入装置通过管线连接。本发明的净化装置是为了实现本发明目的之一所述的方法而设计的。优选地,在所述高级氧化反应器的内部设置有两个或三个曝气装置。优选地,在所述高级氧化反应器上部设置有氧化剂加入装置4。优选地,在所述高级氧化反应器的内部设置有催化剂床层。优选地,在所述高级氧化反应器内部设置有至少一个外加能量场发生装置。优选地,所述外加能量场发生装置包括紫外光发生装置和超声发生装置。优选地,所述紫外光发生装置设置在所述高级氧化反应器的顶部。优选地,所述超声发生装置包括超声探头。优选地,所述超声发生装置设置在所述高级氧化反应器的底部。优选地,所述外加能量场发生装置包括紫外光发生装置和超声发生装置。本发明的目的之三在于提供一种目的之一所述方法的用途,所述方法用于冶金工业。优选地,所述方法用于钨矿物原料冶炼。相对于现有技术,本发明具有如下有益效果:本发明对金属原料浸出液进行高级氧化处理,通过氧化剂产生的羟基自由基将表面活性剂氧化。相比于直接去除金属原料中的表面活性剂,本发明选择在金属浸出之后处理,表面活性剂均匀分散于浸出溶液中,能够达到更佳的氧化去除效果。同时又能够降低金属原料损失、避免浸取剂浪费,并且具有能耗低、劳动强度低、作业环境良好、无污染气体释放等优点。附图说明图1是本发明具体实施方式提供的净化装置的结构示意图。其中:1-高级氧化反应器;2-金属原料浸出液加入装置;3-净化液排出装置;4-氧化剂加入装置;5-臭氧加入装置;6-曝气装置;7-废气排出装置;8-外加能量场发生装置。图2是本发明一个具体实施方式去除金属原料浸出液中表面活性剂的方法流程图。具体实施方式为便于理解本发明,本发明列举实施例如下。本领域技术人员应该明了,所述实施例仅仅是帮助理解本发明,不应视为对本发明的具体限制。以下实施例中的去除金属原料浸出液中表面活性剂的方法中均按照如图2中所示流程进行,并采用图1所示的装置实现。实施例1本实施例提供一种去除金属原料浸出液中表面活性剂的方法,具体步骤如下:(1)将含有表面活性剂的钨酸钠浸出液在0℃下冷冻结晶,晶体析出后过滤,收集滤液,取350ml滤液(钨浓度为81.4g/l,表面活性剂对应的总有机碳(totalorganiccarbon,以下都简称toc)浓度为73.5mg/l,ph为11.0),向其中添加硫酸溶液调节ph至10.0,将ph值调节后的钨酸钠浸出液经过金属原料浸出液加入装置2加入至高级氧化反应器1中,反应器1中包括活性炭催化剂床层,通过臭氧加入装置5向高级氧化反应器1中通入臭氧,并经曝气装置6使臭氧均匀分布在钨酸钠浸出液中,同时通过氧化剂加入装置4以1ml/h的速度加入30%的双氧水,钨酸钠浸出液与高级氧化剂和催化剂充分混合,反应温度为35℃,开启紫外光发生装置反应3h,加入臭氧的总量为toc质量的4倍,获得净化的钨酸钠浸出液(一次净化液)。(2)向步骤(1)得到的一次净化液中添加硫酸镁溶液进行净化去除硅、磷、砷、氟等杂质元素,过滤后获得二次净化液,将二次净化液转移至硫化调酸除钼装置中,往二次净化液中添加硫化钠溶液硫化调酸除钼获得精钨酸钠溶液,随后在萃取和反萃取装置中,以n235(三辛烷胺基铵)为萃取剂对精钨酸钠溶液进行萃取获得负载有机相,对负载有机相用纯水进行两次洗涤,以氨水为反萃剂对负载有机相进行反萃,获得钨酸铵溶液,钨酸铵溶液蒸发结晶获得仲钨酸铵产品。实施例2与实施例1的区别在于,滤液中的钨浓度为82.4g/l,toc浓度为75.6mg/l,ph为10.5,不进行冷冻结晶步骤。实施例3与实施例1的区别在于,滤液中的钨浓度为81.9g/l,toc浓度为74.5mg/l,ph为11.0,将30%的双氧水替换为等量的过硫酸盐。实施例4与实施例1的区别在于,滤液中的钨浓度为82.1g/l,toc浓度为72.0mg/l,ph为10.7,不通入臭氧。实施例5与实施例1的区别在于,滤液中的钨浓度为81.3g/l,toc浓度为71.4mg/l,ph为11.3,步骤(1)中高级氧化的温度为30℃。实施例6与实施例1的区别在于,滤液中的钨浓度为82.3g/l,toc浓度为74.0mg/l,ph为11.7,步骤(1)中高级氧化的温度为50℃。实施例7与实施例1的区别在于,滤液中的钨浓度为80.4g/l,toc浓度为75.1mg/l,ph为10.7,步骤(1)中高级氧化的温度为25℃。实施例8与实施例1的区别在于,滤液中的钨浓度为80.9g/l,toc浓度为73.1mg/l,ph为10.9,步骤(1)中高级氧化的温度为75℃。实施例9与实施例1的区别在于,滤液中的钨浓度为82.0g/l,toc浓度为74.8mg/l,ph为11.1,步骤(1)中高级氧化的温度为0℃。实施例10与实施例1的区别在于,滤液中的钨浓度为82.1g/l,toc浓度为76.0mg/l,ph为11.2,步骤(1)中高级氧化的温度为100℃。实施例11与实施例1的区别在于,滤液中的钨浓度为81.6g/l,toc浓度为73.7mg/l,ph为10.7,将ph值调节至8.5。实施例12与实施例1的区别在于,滤液中的钨浓度为81.0g/l,toc浓度为72.5mg/l,ph为10.2,步骤(1)中,将硫酸溶液替换为氢氧化钠溶液,将ph值调节至10.5。实施例13与实施例1的区别在于,滤液中的钨浓度为80.9g/l,toc浓度为73.9mg/l,ph为10.5,步骤(1)中,将ph值调节至7.5。实施例14与实施例1的区别在于,滤液中的钨浓度为83.8g/l,toc浓度为74.0mg/l,ph为10.6,步骤(1)中,将硫酸溶液替换为氢氧化钠溶液,将ph值调节至14.0。实施例15与实施例1的区别在于,滤液中的钨浓度为83.7g/l,toc浓度为73.1mg/l,ph为10.5,步骤(1)中,加入硫酸溶液,将ph值调节至6.5。实施例16本实施例提供一种去除金属原料浸出液中表面活性剂的方法,具体步骤如下:(1)将含有表面活性剂的钨酸钠浸出液在-10℃下冷冻结晶,晶体析出后过滤,收集滤液,取350ml滤液(钨浓度为82.1g/l,toc浓度为76.0mg/l,ph为10.6),向其中添加硫酸溶液调节ph,将ph调节至10.0,将调节好ph值的钨酸钠浸出液经过金属原料浸出液加入装置2加入至高级氧化反应器1中,反应器1中含活性炭催化剂床层,通过臭氧加入装置5向高级氧化反应器1中通入臭氧(加入臭氧总量为toc质量的5倍),并经曝气装置6使臭氧均匀分布在钨酸钠浸出液中,同时通过氧化剂加入装置4以1ml/h的速度加入30%的双氧水,钨酸钠浸出液与高级氧化剂和催化剂充分混合,设置温度为35℃,开启超声波发生装置,反应0.25h,获得净化的钨酸钠浸出液(一次净化液)。(2)向步骤(1)得到的一次净化液中添加硫酸镁溶液进行净化去除硅、磷、砷、氟等杂质元素,过滤后获得二次净化液,将二次净化液转移至硫化调酸除钼装置中,往二次净化液中添加硫化钠溶液硫化调酸除钼获得精钨酸钠溶液,随后在萃取和反萃取装置中,以n235为萃取剂对精钨酸钠溶液进行萃取获得负载有机相,对负载有机相用纯水进行两次洗涤,以氨水为反萃剂对负载有机相进行反萃,获得钨酸铵溶液,钨酸铵溶液蒸发结晶获得仲钨酸铵产品。实施例17本实施例提供一种去除金属原料浸出液中表面活性剂的方法,具体步骤如下:(1)将含有表面活性剂的钨酸钠浸出液在10℃下冷冻结晶,晶体析出后过滤,收集滤液,取350ml滤液(钨浓度为80.9g/l,toc浓度为74.8mg/l,ph为11.1),向其中添加硫酸溶液调节ph,将ph调节至10.0,将调节好ph值的钨酸钠浸出液经过金属原料浸出液加入装置2加入至高级氧化反应器1中,反应器1中含二氧化钛催化剂床层,通过臭氧加入装置5向高级氧化反应器1中通入臭氧,并经曝气装置6使臭氧均匀分布在钨酸钠浸出液中,同时通过氧化剂加入装置4以1ml/h的速度加入30%的双氧水,钨酸钠浸出液与高级氧化剂和催化剂充分混合,设置温度为35℃,开启紫外光发生装置,反应12h,加入臭氧的总量为toc质量的10倍,获得净化的钨酸钠浸出液(一次净化液)。(2)向步骤(1)得到的一次净化液中添加硫酸镁溶液进行净化去除硅、磷、砷、氟等杂质元素,过滤后获得二次净化液,将二次净化液转移至硫化调酸除钼装置中,往二次净化液中添加硫化钠溶液硫化调酸除钼获得精钨酸钠溶液,随后在萃取和反萃取装置中,以n235为萃取剂对精钨酸钠溶液进行萃取获得负载有机相,对负载有机相用纯水进行两次洗涤,以氨水为反萃剂对负载有机相进行反萃,获得钨酸铵溶液,钨酸铵溶液蒸发结晶获得仲钨酸铵产品。实施例18与实施例1的区别在于,滤液中的钨浓度为81.4g/l,toc浓度为76.6mg/l,ph为10.3,加入臭氧的总量为表面活性剂对应toc质量的8倍。实施例19与实施例1的区别在于,滤液中的钨浓度为82.4g/l,toc浓度为77.1mg/l,ph为10.3,加入臭氧的总量为表面活性剂对应toc质量的10倍。实施例20与实施例1的区别在于,滤液中的钨浓度为81.6g/l,toc浓度为71.6mg/l,ph为10.3,加入臭氧的总量为表面活性剂对应toc质量的3倍。实施例21与实施例1的区别在于,滤液中的钨浓度为80.9g/l,toc浓度为76.2mg/l,ph为10.3,加入臭氧的总量为表面活性剂对应toc质量的11倍。对比例1(1)将含有表面活性剂的钨酸钠浸出液在0℃下冷冻结晶,晶体析出后过滤,收集滤液,取350ml滤液(钨浓度为82.4g/l,toc浓度为71.5mg/l,ph为10.5)。(2)向步骤(1)得到的滤液中添加硫酸镁溶液进行净化去除硅、磷、砷、氟等杂质元素,过滤后获得二次净化液,将二次净化液转移至硫化调酸除钼装置中,往二次净化液中添加硫化钠溶液硫化调酸除钼获得精钨酸钠溶液,随后在萃取和反萃取装置中,以n235为萃取剂对精钨酸钠溶液进行萃取获得负载有机相,对负载有机相用纯水进行两次洗涤,以氨水为反萃剂对负载有机相进行反萃,获得钨酸铵溶液,钨酸铵溶液蒸发结晶获得仲钨酸铵产品。对比例2将同一批的白钨矿分为两部分,将第一部分与碳酸钠溶液混合,在190℃条件下浸取3h,得到净化前的钨酸钠浸出液(钨浓度为81.0g/l,toc浓度为76.4mg/l,ph为10.1);第二部分在750℃下焙烧1.5h,将焙烧后的白钨矿与碳酸钠溶液混合,在190℃条件下浸取3h,得到净化后的钨酸钠浸出液。效果测试(1)采用总有机碳分析仪(仪器型号:toc-vcph,制造商:日本岛津)测定实施例和对比例中净化前/后的钨酸钠浸出液中的toc浓度,结果如表1所示,其中toc去除率=(净化前toc浓度-净化后toc浓度)/净化前toc浓度。(2)以实施例1为例,采用电感耦合-等离子体发射光谱仪(仪器型号:optima5300dv,制造商:美国珀金埃尔默)检测得到的仲钨酸钠中主要杂质元素含量,结果如表2所示。表1不同处理工艺中toc去除效果由表1可知,实施例中toc的减少量为46.2~95.1%,在优化条件下经过净化处理后,浸出液中表面活性剂的含量大幅度降低;而对比例1不进行高级氧化,toc的减少量仅为28.3%,即经过净化处理的浸出液中仍然还有大量的表面活性剂;对比例2中的toc的减少量为96.2%,但使用的焙烧法存在诸多缺点,例如焙烧过程温度高导致能耗高,劳动强度大,作业环境差,并且会产生大量污染性的烟气,造成环境污染,特别是会造成金属原料损失。上述结果证明,本发明提供的方法,能够有效的去除金属原料浸出液中的表面活性剂。相比直接氧化去除金属原料的表面活性剂,本发明选择在金属浸出之后再进行除表面活性剂操作,这样,表面活性剂均匀分散于浸出溶液中去除效果更佳,并且残余少量有机物不影响后续操作。同时能够降低金属原料损失、避免浸取剂浪费,并且具有能耗低、劳动强度低、作业环境良好、无污染气体释放等优点。对比实施例1和2可知,在高级氧化步骤之前进行冷冻结晶步骤(实施例1),表面活性剂去除更加彻底,这是由于大部分金属原料的浸出剂均选用碳酸钠,因此浸出液中会剩余一部分碳酸根离子,而碳酸根离子对于高级氧化反应具有一定的抑制作用,对此,采用冷冻结晶的方法去除浸出液中的碳酸根离子,能够促进高级氧化反应,进一步优化表面活性剂的去除效果。对比实施例1、3、4可知,当选择臭氧和过氧化氢共同作为高级氧化的氧化剂时(实施例1),能够达到更佳的去除表面活性剂的效果,缺少其中任意一种(实施例3、4),效果均会变差,这是因为臭氧和过氧化氢两种氧化剂共同作用,具有更高的羟基自由基生成率,更彻底地去除表面活性剂。对比实施例1、5~10可知,高级氧化的温度为25~75℃时(实施例1、5~8),特别是30~50℃时(实施例1、5、6),去除表面活性剂更加彻底。对比实施例1、11~15可知,当金属原料浸出液的ph为7.5~14(实施例1、11~14),特别是8.5~10.5时(实施例1、11、12),效果更佳。对比实施例1、18~21可知,当所述臭氧与所述金属原料浸出液中表面活性剂对应toc的质量比为4~10:1时,去除表面活性剂的效果最好,再增加臭氧的量,效果提升不高,且成本增加。表2仲钨酸铵产品中杂质元素含量元素alasbicacdcocrcufe含量(ppm)260.565320.55元素mnmgnipbsbsisntiv含量(ppm)2230.5280.532由表2可知,实施例1得到的仲钨酸铵产品质量符合仲钨酸铵产品国家标准(gbt10116-2007)中apt-0级品要求,表明本发明提供的去除金属原料浸出液中表面活性剂的方法有效去除了表面活性剂,解决了表面活性剂在萃取工艺中污染萃取剂而影响萃取效果的问题。申请人声明,本发明通过上述实施例来说明本发明的详细工艺设备和工艺流程,但本发明并不局限于上述详细工艺设备和工艺流程,即不意味着本发明必须依赖上述详细工艺设备和工艺流程才能实施。所属
技术领域:
的技术人员应该明了,对本发明的任何改进,对本发明产品各原料的等效替换及辅助成分的添加、具体方式的选择等,均落在本发明的保护范围和公开范围之内。当前第1页12