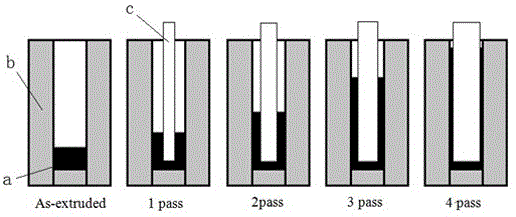
本发明涉及金属材料制备成形
技术领域:
,更具体地,涉及一种制备al-cu-mg合金弹壳的新型冷冲工艺及应用。
背景技术:
:随着我国航母的高速发展和远海作战能力的增强,传统的铁质、铜质弹壳已难以满足海、空军对子弹质量轻、耐腐蚀、数量大、价格低的要求,国家从战略层面急需研发出铝质弹壳,以提升我军远海作战能力。而高强韧铝合金弹壳可以替代传统的钢质、铜质弹壳,显著降低弹壳重量,提高单兵携弹量和作战机动性。因此,急需开发一种具有高强度高韧性的铝合金材料来制备轻量化弹壳。al-cu-mg合金因具有强度高、加工成形性及耐热性好等优点,已被广泛应用于航空航天及军工领域。然而,采用现有常规技术制备得到的al-cu-mg合金依然无法满足在弹壳方面的应用要求。强塑性变形(spd)技术作为改善铝合金微结构、获得微米甚至纳米级细晶材料的重要手段,越来越引起国内外学者更为深入的研究和探索。目前,常用的spd技术包括高压扭转法、等径角挤压法、叠层轧合技术和反复折皱-压直等方法,国内外对上述方法的研究深入而广泛。murayama在a1-cu二元合金的等径挤压变形中观察到呈针状的θ'过渡相在数道次等径角挤压过程中逐步分解成短链状颗粒直至回溶进入基体。张孜昭等研究了多向压缩变形对al-cu合金析出相的影响,发现由强塑性变形诱导析出相回溶形成的过饱和固溶体,再析出相的析出顺序与加热温度、变形量及变形后的晶粒尺寸相关。xu等研究了室温等径角挤压变形对al-cu合金θ”相、θ'相和θ相的回溶和再析出行为,发现θ”相回溶速度最快,θ相回溶速度最慢,继续强变形直接析出θ相。spd法制备微纳米材料的变形细化机制比较复杂,针对不同的材料采用的工艺方法也大不相同,目前尚未见将该方法用于处理铝合金弹壳用al-cu-mg合金的相关报道。技术实现要素:针对现有技术中铝合金弹壳用al-cu-mg合金存在的不足,本发明的目的在于提供一种制备al-cu-mg合金弹壳的新型冷冲工艺。该工艺基于喷射成形al-cu-mg合金,采用新型快速冷冲工艺能够显著改善合金组织和提高合金力学性能,制备出高强韧轻量化铝合金弹壳。本发明的另一目的在于提供所述制备al-cu-mg合金弹壳的新型冷冲工艺在制备弹壳方面的应用。本发明的目的通过以下技术方案实现:提供一种制备al-cu-mg合金弹壳的新型冷冲工艺,包括多道次快速冷冲处理步骤,快速冷冲处理过程中,所述冲头直径为8~30mm,所述冷冲压速度为10~40mm/s,所述al-cu-mg合金是采用3d喷射成形-快速凝固技术制备而成。本发明采用一种新型快速冷冲工艺,通过强变形导致合金中较粗的长条状析出相发生破碎,并诱发析出相回溶,使基体重新成为过饱和固溶体,在再时效过程中形成弥散分布的颗粒状纳米析出相,显著改善合金组织和提高合金力学性能,制备出高强韧al-cu-mg合金材料;本发明经过大量研究发现,将上述得到的高强韧al-cu-mg合金材料应用于铝合金弹壳中,强度高、韧性好,各项性能均能满足弹壳的使用要求。进一步地,所述冲头直径为10~27mm,所述冷冲压速度为15~30mm/s。进一步地,所述新型冷冲工艺包括四道次快速冷冲处理步骤。进一步地,所述第一道次快速冷冲处理的工艺参数为:所述冲头直径为8~12mm,所述冷冲压速度为30~40mm/s。进一步地,所述第二道次快速冷冲处理的工艺参数为:所述冲头直径为12~15mm,所述冷冲压速度为20~30mm/s。进一步地,所述第三道次快速冷冲处理的工艺参数为:所述冲头直径为16~20mm,所述冷冲压速度为18~24mm/s。进一步地,所述第四道次快速冷冲处理的工艺参数为:所述冲头直径为25~40mm,所述冷冲压速度为10~18mm/s。本发明根据多元al-cu-mg合金的析出相特点,科学合理设计快速冷冲工艺,在四道次快速冷冲制备铝合金弹壳的过程中发现,随着冲压道次的增多,析出相形貌发生改变,长条状析出相在强变形作用下破碎成细小的短棒状颗粒,并发生回溶,使基体重新成为过饱和固溶体,在随后的时效过程中,基体中重新析出弥散分布的颗粒状析出相,析出相数量明显增多,尺寸显著减小,均匀细小的析出相显著提高了合金的力学性能。本发明同时提供所述制备al-cu-mg合金弹壳的新型冷冲工艺在制备弹壳方面的应用。进一步地,所述al-cu-mg合金成分为:cu4~6wt%、mg1~4wt%、mn0.1~0.6wt%、si0~0.05wt%、fe0~0.05wt%,al余量。进一步优选地,所述al-cu-mg合金成分为:cu4.51wt%、mg1.46wt%、mn0.56wt%、si0.02wt%、fe0.01wt%,al余量。进一步地,所述al-cu-mg合金的制备方法如下:取纯度为99.98%的纯铝置于石墨坩埚熔炼炉中,在800~860℃下,加热至全部变为熔融态;依次加入中间合金,降低温度至700~720℃,充分搅拌后,静置15~25min;然后采用通入纯度为99.99%的无水高纯氮气的方法除渣,时间为30~60min;将打渣剂加到铝液表面,静置15~25min后扒渣,得到合金熔体;采用铝合金喷射成形设备对合金熔体进行喷射成形,所述氮气的压力为1.0~2.0mpa,氮气的温度为-25~-15,℃合金熔体的喷射温度为700~720℃,冷却速度约为103~105k/s;喷射距离为200~300mm,制备出al-cu-mg合金材料。与现有技术相比,本发明的有益效果是:本发明是基于3d喷射成形-快速凝固技术,首先制备出多元al-cu-mg合金,在此基础上利用快速冷冲技术制备出具有高强韧性能的al-cu-mg合金弹壳,根据多元al-cu-mg合金的析出相特征,科学合理设计四道次快速冷冲工艺及其参数,不但可以制备出符合轻武器使用要求的铝合金弹壳,还可为进一步探索快速冷冲过程中al-cu-mg合金析出相的回溶机制提供理论基础,实用性极强,且具有巨大的经济效益和研究价值。本发明开创性地提供了一种适用于铝合金弹壳用合金材料的新型冷冲工艺,填补了该领域的技术空白,在多道次的快速冷冲工艺作用下,合金中较粗的长条状析出相发生破碎和回溶,使基体重新成为过饱和固溶体,然后在时效过程中形成弥散分布的颗粒状纳米析出相,这些析出相能够显著改善合金组织和提高合金力学性能,从而制备出高强韧轻量化铝合金弹壳。附图说明图1为本发明实施例1中四道次快速冷冲工艺处理al-cu-mg合金试样的示意图。图2为本发明喷射成形后al-cu-mg合金试样析出相形貌的tem图。图3为本发明冷冲2道次后al-cu-mg合金试样析出相形貌的tem图。图4为本发明冷冲4道次后al-cu-mg合金试样时效析出相形貌的tem图。具体实施方式为了便于理解本发明,下文将结合实施例对本发明作更全面、细致地描述,但本发明的保护范围并不限于以下具体的实施例。除非另有定义,下文中所使用的所有专业术语与本领域技术人员通常理解的含义相同。本文中所使用的专业术语只是为了描述具体实施例的目的,并不旨在限制本发明的保护范围。除非另有特别说明,本发明中用到的各种原材料、试剂、仪器和设备等均可通过市场购买得到或者可通过现有方法制备得到。实施例1本实施例所涉及的材料为铝合金弹壳用al-cu-mg合金,各元素的化学成分为:cu4.51wt%、mg1.46wt%、mn0.56wt%、si0.02wt%、fe0.01wt%,al余量。该al-cu-mg合金的制备方法如下:取纯度为99.98%的纯铝置于石墨坩埚熔炼炉中,在840℃下,加热至全部变为熔融态;依次加入中间合金,降低温度至720℃,充分搅拌后,静置15~25min;然后采用通入纯度为99.99%的无水高纯氮气的方法除渣,时间为30min;将打渣剂加到铝液表面,本实施例中选用的打渣剂为jy-d1,按铝合金熔体量的0.1%~0.2%加入,主要成分为氯盐和氟盐,静置15~25min后扒渣,得到合金熔体;采用铝合金喷射成形设备对合金熔体进行喷射成形,所述氮气的压力为1.0~2.0mpa,氮气的温度为-25℃,合金熔体的喷射温度为720℃,冷却速度约为103~105k/s,喷射距离为250mm,制备出al-cu-mg合金材料。本实施例采用四道次快速冷冲工艺对上述al-cu-mg合金材料进行处理,制备出al-cu-mg合金弹壳,其中,第一道次快速冷冲处理过程中,冲头直径为10mm,冷冲压速度为30mm/s;第二道次快速冷冲处理过程中,冲头直径为14mm,冷冲压速度为25mm/s;第三道次快速冷冲处理过程中,冲头直径为20mm,冷冲压速度为20mm/s;第四道次快速冷冲处理过程中,冲头直径为27mm,冷冲压速度为15mm/s。图1为本实施例中四道次快速冷冲工艺处理al-cu-mg合金试样的示意图,其中a为铝合金试样,b为凹模,c为冲头。实施例2本实施例采用的材料和制备方法与实施例1一致,实验参数与实施例1基本相同,不同之处在于本实施例中,第一道次快速冷冲处理工艺参数为:冲头直径为8mm,冷冲压速度为40mm/s。实施例3本实施例采用的材料和制备方法与实施例1一致,实验参数与实施例1基本相同,不同之处在于本实施例中,第二道次快速冷冲处理的工艺参数为:冲头直径为12mm,冷冲压速度为20mm/s。实施例4本实施例采用的材料和制备方法与实施例1一致,实验参数与实施例1基本相同,不同之处在于本实施例中,第三道次快速冷冲处理的工艺参数为:冲头直径为16mm,冷冲压速度为24mm/s。实施例5本实施例采用的材料和制备方法与实施例1一致,实验参数与实施例1基本相同,不同之处在于本实施例中,第四道次快速冷冲处理的工艺参数为:冲头直径为30mm,冷冲压速度为18mm/s。对比例1本对比例采用的材料和制备方法与实施例1一致,实验参数与实施例1基本相同,不同之处在于本对比例中,采用三道次快速冷冲工艺对al-cu-mg合金材料进行处理,三道次快速冷冲工艺参数分别与实施例1中的第一道次、第二道次和第三道次相同。对比例2本对比例采用的材料和制备方法与实施例1一致,实验参数与实施例1基本相同,不同之处在于本对比例中,采用五道次快速冷冲工艺对al-cu-mg合金材料进行处理,前四道次快速冷冲工艺参数分别与实施例1中的第一道次、第二道次、第三道次和第四道次相同,第五道次快速冷冲工艺参数为:冲头直径为32mm,冷冲压速度为9mm/s。对比例3本对比例采用的材料和制备方法与实施例1一致,实验参数与实施例1基本相同,不同之处在于本对比例中,其中,第一道次快速冷冲处理过程中,冲头直径为6mm,冷冲压速度为28mm/s;第二道次快速冷冲处理过程中,冲头直径为10mm,冷冲压速度为18mm/s;第三道次快速冷冲处理过程中,冲头直径为15mm,冷冲压速度为16mm/s;第四道次快速冷冲处理过程中,冲头直径为20mm,冷冲压速度为9mm/s。对比例4本对比例采用的材料和制备方法与实施例1一致,实验参数与实施例1基本相同,不同之处在于本对比例中,其中,第一道次快速冷冲处理过程中,冲头直径为15mm,冷冲压速度为42mm/s;第二道次快速冷冲处理过程中,冲头直径为18mm,冷冲压速度为35mm/s;第三道次快速冷冲处理过程中,冲头直径为24mm,冷冲压速度为25mm/s;第四道次快速冷冲处理过程中,冲头直径为42mm,冷冲压速度为20mm/s。为了进一步验证上述实施例1~5及对比例1~4的性能,将上述经过快速冷冲工艺处理的al-cu-mg合金试样进行时效处理,加热温度为180℃,保温时间为14小时;然后将试样加工成拉伸试样并测试其室温拉伸性能,主要性能指标数据见表1。表1抗拉强度,mpa伸长率,%屈服强度,mpa实施例155015.0460实施例253115.7451实施例352916.4445实施例453515.5454实施例552416.7439对比例152014.0435对比例252213.8437对比例351915.1433对比例450813.2417由表1可知,经过实施例1~5快速冷冲工艺处理的高强韧al-cu-mg合金材料力学性能明显优于对比例1~4。其中实施例1的强度和韧性最佳,分别对其喷射成形试样、快速冷冲2道次以及4道次后时效态试样进行扫描电镜分析,其析出相形貌如图2~4所示,在喷射成形试样中的主要析出相呈长条状,经过两道次的快速冲压后,长条状析出相破碎细化成多个较小的析出相,从而使析出相与基体的接触面积增大,析出相的自由能将大于基体自由能,根据相变理论,高自由能态将向低自由能态转变,此时合金中析出相将回溶于基体中使基体重新成为过饱和固溶体,在随后的时效处理过程中再次析出颗粒状稳定态析出相,从而缩短合金的时效时间。实施例1~5与对比例1~2相比较,本发明的四道次快速冷冲工艺明显优于对比例1~2中的三道次和五道次快速冷冲工艺,采用同样的al-cu-mg合金材料,实施例1~5的性能均优于对比例1~2。实施例1~5与对比例3~4相比较,本发明的快速冷冲工艺参数明显优于对比例3~4中的快速冷冲工艺参数。由上述可知,本发明基于3d喷射成形-快速凝固技术制备出的多元al-cu-mg合金,通过四道次快速冷冲处理,并科学合理设计快速冷冲工艺参数,可以制备出高强韧轻量化的铝合金弹壳。显然,上述实施例仅仅是为清楚地说明本发明的技术方案所作的举例,而并非是对本发明的实施方式的限定。对于所属领域的普通技术人员来说,在上述说明的基础上还可以做出其它不同形式的变化或变动。这里无需也无法对所有的实施方式予以穷举。凡在本发明的精神和原则之内所作的任何修改、等同替换和改进等,均应包含在本发明权利要求的保护范围之内。当前第1页12