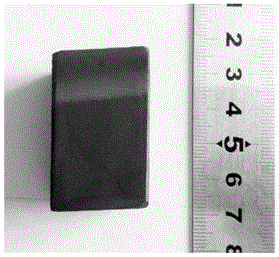
本发明涉及铁路车轮的热处理冷却
技术领域:
,具体是一种铁路车轮的热处理冷却工艺。
背景技术:
:踏面连续大流量喷水强制冷却是当前国内外通用的铁路车轮热处理冷却技术,是实现车轮轮辋部位强硬化,获得细珠光体组织,从而获得优异抗接触疲劳性能、高耐磨性的重要途径。但踏面近表层金属与冷却水直接接触,热量被冷却水直接带走,冷却速度极快,超过钢的下临界冷却速度(完全珠光体转变的最大冷却速度),导致硬而脆的非珠光体组织(即异常组织)的形成,破坏车轮的使用性能,提高车轮踏面剥离发生几率。近些年,随着铁路货运运输快速化、重载化进程的加快,为避免踏面异常磨耗、辗堆等问题的发生,往往提高车轮钢中的碳含量。而采用现有热处理技术必然导致异常组织问题突出,当碳含量在0.7%以上时,车轮单边异常组织深度多达15mm左右,甚至以上,需依赖后续机加工予以切除,严重降低金属利用率,增加刀具的损耗。因此,在获得优异力学性能和使用性能的同时,避免出现异常组织已成为高碳钢车轮设计制造的基本要求,这也逐渐成为了一项技术难题。因此,为解决上述技术难题,制造出对踏面近表层的组织状态有苛刻要求的高品质高碳钢铁路车轮,提供一种切实可行、技术经济效果明显的铁路车轮热处理冷却技术尤为迫切。经检索,中国专利,申请公布号:cn103436678a,申请公布日:2013.12.11,公开了一种工矿、吊车等车轮踏面的喷水淬火技术,其技术方案如下:工矿、吊车等车轮踏面的喷水淬火技术,喷水时车轮处于旋转状态;所述技术的装置采用钢梁架在淬火水槽上;感应淬火后的淬硬层与基体分层明显,过渡层小,受到重载时易开裂,而喷水淬火的车轮踏面淬硬层与基体过渡层比较平缓与合理;踏面能够承受更大的冲击与载荷;所述技术的水泵是放在水槽里的,电动机固定在水槽壁上,小链轮带动大链轮,所述技术的大链轮上面连接圆形转盘,圆形转盘中间焊一个锥形柱用于定位车轮吊运胎具,车轮放在胎具上。该发明阐述的淬火工艺容易导致车轮踏面近表层产生异常组织,影响车轮性能。技术实现要素:发明要解决的技术问题本发明的目的在于克服传统连续大流量喷水强冷导致的车轮踏面近表层组织异常的不足,提供了一种铁路车轮的热处理冷却工艺。本发明在保证轮辋内部组织正常区硬度不下降的前提下,促使从车轮踏面至轮辋内部深处获得均匀冷却,优化车轮轮辋全截面组织转变,减少车轮踏面近表层异常组织的产生,进而改善车轮的力学性能和使用性能。技术方案为解决上述问题,本发明提供的技术方案为:一种铁路车轮的热处理冷却工艺,包括如下方法步骤:s1、加热:将轧制、缓冷后的车轮整体加热至完全奥氏体化;s2、淬火冷却:将加热完成后的车轮转运至淬火台,开启淬火台中的驱动电机使车轮处于转动状态,采用压力阶梯递增式气雾两相流喷射车轮踏面,能够促使从车轮踏面至轮辋内部深处获得均匀冷却,优化车轮轮辋全截面组织转变,减少车轮踏面近表层异常组织的产生,进而改善车轮的力学性能和使用性能;s3、回火:将车轮整体入回火炉保温,然后取出空冷。进一步地,s2步骤中所述的压力阶梯递增式气雾两相流喷射车轮踏面依次包括三个阶段:第一阶段的车轮转速为v1,水压为p1,淬火冷却时间为t1;第二阶段的车轮转速为v2,水压为p2,淬火冷却时间为t2;第三阶段的车轮转速为v3,水压为p3,淬火冷却时间为t3;控制v1>v2>v3,p1<p2<p3,t1<t2<t3,且气雾冷却喷嘴数量逐级增加。通过逐级降低车轮转速,延长冷却时间,增加喷嘴水压和喷嘴数量,能够使车轮踏面至轮辋内部深处获得均衡一致的冷却速度,增加对轮辋内部的冷却能力;另外,随着淬火进程的推进,在强硬度不受影响的前提下,减缓电机转速不仅可以节能,也有利于车轮转动的平稳性,避免较大水压对车轮造成冲击,影响淬火质量。进一步地,所述三个阶段的压缩空气压力p0为0.20~0.40mpa。进一步地,所述第一阶段水压p1为0.10~0.20mpa,第二阶段水压p2为0.20~0.40mpa,第三阶段的水压p3为0.40~0.70mpa。进一步地,淬火冷却总时间t为6~8min。进一步地,所述第一阶段的时间t1为50~90s。进一步地,所述淬火台上的气雾冷却喷嘴沿车轮周向等间距分布,且保持与踏面的距离均匀一致,保证完全覆盖车轮踏面,使得车轮踏面获得均匀冷却。进一步地,所述s2步骤中,第一阶段启动沿车轮周向等间距分布的喷嘴m个,第二阶段启动沿车轮周向等间距分布的喷嘴2m个,第三阶段启动沿车轮周向等间距分布的喷嘴3m个,冷却气雾量呈倍数增加,并结合车轮转速、水压和淬火冷却时间,进一步优化冷却速率和车轮踏面至轮辋内部的均匀性,控制冷却速度略低于车轮钢的下临界冷却速度,促进轮辋全截面完成细珠光体组织转变,完全避免踏面近表层产生异常组织,使轮辋全截面的力学性能趋于一致。其中,m为≥4的自然数。进一步地,所述气雾冷却喷嘴的水流量随水压的增大而增大,在水压调节范围内,最大水流量与最小水量相差12倍,雾化角为75~90°,结合喷嘴数量合理控制流量和雾化角度,进一步优化对车轮踏面的冷却均匀性和冷却速率。进一步地,所述车轮为矿运货车车轮,其主要化学成分以质量百分比计为c:0.72~0.77,si:0.8~1.0,mn:0.7~0.9,cr:0.15~0.25,其余为fe及不可避免的杂质。有益效果采用本发明提供的技术方案,与现有技术相比,具有如下有益效果:(1)本发明提供的一种铁路车轮的热处理冷却工艺,采用压力阶梯递增式气雾两相流喷射车轮踏面,能够促使从车轮踏面至轮辋内部深处获得均匀冷却,优化车轮轮辋全截面组织转变,减少车轮踏面近表层异常组织的产生,进而改善车轮的力学性能和使用性能;(2)本发明提供的一种铁路车轮的热处理冷却工艺,通过逐级降低车轮转速,延长冷却时间,增加喷嘴水压和喷嘴数量,能够使车轮踏面至轮辋内部深的冷却速度更加均衡一致,进一步优化车轮轮辋全截面组织转变;(3)本发明提供的一种铁路车轮的热处理冷却工艺,随着淬火进程的推进,在强硬度不受影响的前提下,减缓电机转速不仅可以节能,也有利于车轮转动的平稳性,避免较大水压对车轮造成冲击,影响淬火质量;(4)本发明提供的一种铁路车轮的热处理冷却工艺,淬火台上的气雾冷却喷嘴沿车轮周向等间距分布,且保持与踏面的距离均匀一致,保证完全覆盖车轮踏面,使得车轮踏面获得均匀冷却;(5)本发明提供的一种铁路车轮的热处理冷却工艺,冷却气雾量呈倍数增加,并结合车轮转速、水压和淬火冷却时间,进一步优化冷却速率和车轮踏面至轮辋内部的均匀性,控制冷却速度略低于车轮钢的下临界冷却速度,促进轮辋全截面完成细珠光体组织转变,完全避免踏面近表层产生异常组织,使轮辋全截面的力学性能趋于一致;(6)本发明提供的一种铁路车轮的热处理冷却工艺,用该工艺处理产生的成品车轮具有良好的残余应力分布,使车轮的使用性能更佳,可有效减缓疲劳裂纹的萌生;(7)本发明提供的一种铁路车轮的热处理冷却工艺,在现有淬火台的基础上,只需简单的水、气环管路改造即可实现本发明目的,经济成本低,且不增加现场操作难度,降低工人劳动强度。附图说明图1、实施例1中的车轮轮辋断面硬度检测结果;图2、对比例中的车轮轮辋组织正常区(去除异常组织后)的断面硬度检测结果;图3、实施例1中的车轮踏面中线处的金相宏观形貌;图4、实施例1中的车轮踏面1~2mm处的金相组织;图5、实施例1中的车轮踏面下10~11mm处的金相组织;图6、实施例1中的车轮踏面下19~20mm处的金相组织;图7、对比例中的车轮踏面中线处的金相宏观形貌;图8、对比例中的车轮踏面下1~2mm处的金相组织;图9、对比例中的车轮踏面下10~11mm处的金相组织;图10、对比例中的车轮踏面下19~20mm处的金相组织;图11、车轮轮辋残余应力测试点分布示意图(沿车轮周向逆时针等间距选取4个位置);图12、在轮辋磨耗到限处以内的残余应力分布测试点选取示意图(在不同深处a、b、c处贴片进行残余应力分布测试);图13、实施例1中的车轮轮辋沿径向的残余应力分布趋势图(“-”表示压应力);图14、实施例1中的车轮轮辋沿周向的残余应力分布趋势图(“-”表示压应力);图15、对比例中的车轮轮辋沿径向的残余应力分布趋势图(“-”表示压应力);图16、对比例中的车轮轮辋沿周向的残余应力分布趋势图(“-”表示压应力);图17、实施例2中的车轮轮辋断面硬度检测结果;图18、实施例2中的车轮踏面中线处的金相宏观形貌;图19、实施例2中的车轮踏面1~2mm处的金相组织;图20、实施例2中的车轮踏面下12~13mm处的金相组织;图21、实施例2中的车轮踏面下19~20mm处的金相组织;图22、实施例2中的车轮轮辋沿径向的残余应力分布趋势图(“-”表示压应力);图23、实施例2中的车轮轮辋沿周向的残余应力分布趋势图(“-”表示压应力);图24、实施例3中的车轮轮辋断面硬度检测结果;图25、实施例3中的车轮踏面中线处的金相宏观形貌;图26、实施例3中的车轮踏面1~2mm处的金相组织;图27、实施例3中的车轮踏面下10~11mm处的金相组织;图28、实施例3中的车轮踏面下20~21mm处的金相组织;图29、实施例3中的车轮轮辋沿径向的残余应力分布趋势图(“-”表示压应力);图30、实施例3中的车轮轮辋沿周向的残余应力分布趋势图(“-”表示压应力)。具体实施方式为进一步了解本发明的内容,结合附图及实施例对本发明作详细描述。实施例1:本实施例中的铁路车轮为矿运货车车轮,公称直径为950~1000mm,重量约为500kg,其主要化学组分及质量百分比(wt%)如表1中所示,该铁路车轮的热处理冷却工艺步骤如下:s1、加热:将轧制、缓冷后的车轮整体加热至完全奥氏体化;s2、淬火冷却:加热完成后将铁路车轮从加热炉中取出,转运至卧式淬火台,开启卧式淬火台中的变频伺服电机使铁路车轮处于转动状态,铁路车轮保持内侧面朝上;然后打开卧式淬火台中的淬火电控单元,控制水、气环管路阀门的启动,采用三阶段压力阶梯递增式气雾两相流喷射车轮踏面;第一阶段的车轮转速为20r/min,沿车轮周向等间距开启5个喷嘴,喷嘴水压为0.15mpa,淬火冷却时间为70s;第二阶段的车轮转速为15r/min,在第一阶段的基础上沿周向等间距再开启5个喷嘴,此时沿周向共有10个等间距分布的喷嘴喷射车轮踏面,喷嘴水压为0.30mpa,淬火冷却时间为150s;第三阶段的车轮转速为10r/min,在第二阶段的基础上沿周向等间距再开启5个喷嘴,此时沿周向共有15个等间距分布的喷嘴喷射车轮踏面,喷嘴水压为0.55mpa,淬火冷却时间较第二阶段进一步延长;所述三个阶段的淬火冷却总时间为7min;压缩空气压力均控制在0.30mpa;s3、回火:将车轮整体入回火炉保温,然后取出空冷。s2步骤中,所述淬火台上的气雾冷却喷嘴沿车轮周向等间距分布,且保持与踏面的距离均匀一致,保证完全覆盖车轮踏面;所述气雾冷却喷嘴的水流量随水压的增大而增大,在水压调节范围内,最大水流量与最小水量相差12倍,雾化角为85°。本实施例中的铁路车轮的热处理冷却工艺,根据所述材质矿运货车车轮用钢的完全珠光体转变速度(即下临界冷却速度),通过淬火设备简单改造,采用压力阶梯递增式气雾两相流冷却工艺,逐级降低车轮转速,延长冷却时间,增加喷嘴水压,控制喷嘴数量,能够增加轮辋内部的冷却能力,使车轮踏面至轮辋内部深处获得均衡一致的冷却速度,且此冷却速度略低于该材质车轮钢的下临界冷却速度,促进轮辋全截面完成细珠光体组织转变,既克服了传统大流量水冷在踏面近表层产生的异常组织,又使轮辋全截面的力学性能趋于一致,显著降低了轮辋径向硬度梯度(即在磨耗方向上的硬度梯度),极大改善了车轮的力学性能和使用性能。另外,随着淬火进程的推进,在强硬度不受影响的前提下,减缓电机转速不仅可以节能,也有利于车轮转动的平稳性,避免较大水压对车轮造成冲击,影响淬火质量。对比例:本对比例中的铁路车轮亦为矿运货车车轮,公称直径为950~1000mm,重量约为500kg,其主要化学组分及质量百分比(wt%)如表1中所示,所用热处理的加热、回火工序及参数与实施例保持一致,只是冷却工序采用现有技术,即踏面连续大流量喷水强制冷却,且淬火过程中水压为恒值,保持在0.30~0.40mpa,单个喷嘴水流量30~50l/min,淬火冷却总时间亦为7min,车轮旋转速度保持在10~15r/min。自淬火冷却开始便启动沿周向等间距分布的12~15个水喷嘴至淬火结束。表1实施例及对比例车轮化学成分(质量百分比,wt%)元素csimncr余量实施例10.750.890.820.22fe及其它实施例20.770.820.720.17fe及其它实施例30.720.960.870.24fe及其它对比例0.740.900.800.21fe及其它实施例1与对比例相比:实施例1中所得车轮的轮辋部位断面硬度如图1所示,车轮的断面最大硬度、最小硬度、平均硬度分别为365、348、355hb,硬度最大值与最小值的绝对差(即硬度梯度)为17hb;对比例中所得车轮的轮辋部位断面硬度如图2所示,车轮的断面最大硬度、最小硬度、平均硬度分别为380、349、363hb,硬度梯度为31hb。因此,实施例1中所得车轮的轮辋硬度梯度合理,且不降低轮辋内部的硬度水平,保证了轮辋部位优异的力学性能和使用性能。在踏面中线处取样进行金相组织分析,如图3至6所示,实施例1中的车轮轮辋全截面为细珠光体+极少量铁素体,显微组织趋于均衡、一致,不存在硬而脆的异常组织;如图7至10所示,对比例车轮踏面近表层含有由回火索氏体和上贝氏体组成的混合组织,也就是硬而脆的异常组织,其深度达到了15mm左右。说明实施例1中的方法可显著改善车轮踏面近表层的组织状态,完全消除异常组织,实现轮辋全截面细珠光体组织转变,保证了车轮的使用安全,同时由于取消了后续机加工工序,因此使制造成本降低,提高了金属利用率。按照图11、12所示方法进行轮辋残余应力分布测试,实施例1与对比例中车轮轮辋的残余应力分布趋势分别如图13至16所示。可见,实施例1中车轮沿径向、周向的残余应力分布差异较小,即轮辋的残余应力波动较小,且磨耗到限处以内的平均残余压应力约140mpa,亦略高于本对比例车轮;良好的残余应力分布,使车轮的使用性能更佳,可有效减缓疲劳裂纹的萌生。实施例2:本实施例中的铁路车轮为矿运货车车轮,公称直径为950~1000mm,重量约为500kg,其主要化学组分及质量百分比(wt%)如表1中所示,该铁路车轮的热处理冷却工艺步骤如下:s1、加热:将轧制、缓冷后的车轮整体加热至完全奥氏体化;s2、淬火冷却:加热完成后将铁路车轮从加热炉中取出,转运至卧式淬火台,开启卧式淬火台中的变频伺服电机使铁路车轮处于转动状态,铁路车轮保持内侧面朝上;然后打开卧式淬火台中的淬火电控单元,控制水、气环管路阀门的启动,采用三阶段压力阶梯递增式气雾两相流喷射车轮踏面;第一阶段的车轮转速为25r/min,沿车轮周向等间距开启4个喷嘴,喷嘴水压为0.20mpa,淬火冷却时间为50s;第二阶段的车轮转速为20r/min,在第一阶段的基础上沿周向等间距再开启4个喷嘴,此时沿周向共有8个等间距分布的喷嘴喷射车轮踏面,喷嘴水压为0.40mpa,淬火冷却时间为120s;第三阶段的车轮转速为15r/min,在第二阶段的基础上沿周向等间距再开启4个喷嘴,此时沿周向共有12个等间距分布的喷嘴喷射车轮踏面,喷嘴水压为0.70mpa,淬火冷却时间较第二阶段进一步延长;所述三个阶段的淬火冷却总时间为6min;压缩空气压力均控制在0.40mpa;s3、回火:将车轮整体入回火炉保温,然后取出空冷。s2步骤中,所述淬火台上的气雾冷却喷嘴沿车轮周向等间距分布,且保持与踏面的距离均匀一致,保证完全覆盖车轮踏面;所述气雾冷却喷嘴的雾化角为90°。本实施例与对比例相比:本实施例中所得车轮的轮辋部位断面硬度如图17所示,车轮的断面最大硬度、最小硬度、平均硬度分别为372、351、361hb,硬度梯度为21hb,其所得车轮的轮辋硬度梯度明显优于对比例,且不降低轮辋内部的硬度水平。在踏面中线处取样进行金相组织分析,如图18至21所示,本实施例中的车轮轮辋全截面仍然主要为细珠光体+极少量铁素体,显微组织趋于均衡、一致,只是在踏面下12~15mm范围内出现了极少量的、断断续续的、零星分布的贝氏体块,经定量,其体积分数低于8%;说明本实施例与对比例相比仍然能够显著改善车轮踏面近表层的组织状态,基本消除异常组织,几乎实现轮辋全截面细珠光体组织转变。本实施例中车轮轮辋的残余应力分布趋势如图22、23所示,与对比例相比较可见,本实施例车轮沿径向、周向的残余应力分布差异较小,即轮辋的残余应力波动较小,且磨耗到限处以内的平均残余压应力约145mpa,亦略高于本对比例车轮。实施例3:本实施例中的铁路车轮为矿运货车车轮,公称直径为950~1000mm,重量约为500kg,其主要化学组分及质量百分比(wt%)如表1中所示,该铁路车轮的热处理冷却工艺步骤如下:s1、加热:将轧制、缓冷后的车轮整体加热至完全奥氏体化;s2、淬火冷却:加热完成后将铁路车轮从加热炉中取出,转运至卧式淬火台,开启卧式淬火台中的变频伺服电机使铁路车轮处于转动状态,铁路车轮保持内侧面朝上;然后打开卧式淬火台中的淬火电控单元,控制水、气环管路阀门的启动,采用三阶段压力阶梯递增式气雾两相流喷射车轮踏面;第一阶段的车轮转速为20r/min,沿车轮周向等间距开启5个喷嘴,喷嘴水压为0.10mpa,淬火冷却时间为90s;第二阶段的车轮转速为15r/min,在第一阶段的基础上沿周向等间距再开启5个喷嘴,此时沿周向共有10个等间距分布的喷嘴喷射车轮踏面,喷嘴水压为0.20mpa,淬火冷却时间为180s;第三阶段的车轮转速为10r/min,在第二阶段的基础上沿周向等间距再开启5个喷嘴,此时沿周向共有15个等间距分布的喷嘴喷射车轮踏面,喷嘴水压为0.40mpa,淬火冷却时间较第二阶段进一步延长;所述三个阶段的淬火冷却总时间为8min;压缩空气压力均控制在0.20mpa;s3、回火:将车轮整体入回火炉保温,然后取出空冷。s2步骤中,所述淬火台上的气雾冷却喷嘴沿车轮周向等间距分布,且保持与踏面的距离均匀一致,保证完全覆盖车轮踏面;所述气雾冷却喷嘴的雾化角为75°。本实施例与对比例相比:本实施例中所得车轮的轮辋部位断面硬度如图24所示,车轮的断面最大硬度、最小硬度、平均硬度分别为364、341、352hb,硬度梯度为23hb,其所得车轮的轮辋硬度梯度明显优于对比例,且不降低轮辋内部的硬度水平。在踏面中线处取样进行金相组织分析,如图25至28所示,本实施例中的车轮轮辋全截面为细珠光体+极少量铁素体,显微组织趋于均衡、一致,不存在硬而脆的异常组织;说明本实施例与对比例相比可显著改善车轮踏面近表层的组织状态,完全消除异常组织,实现轮辋全截面细珠光体组织转变。本实施例中车轮轮辋的残余应力分布趋势如图29、30所示,与对比例相比较可见,本实施例车轮沿径向、周向的残余应力分布差异较小,即轮辋的残余应力波动较小,且磨耗到限处以内的平均残余压应力约138mpa,亦略高于本对比例车轮。以上示意性的对本发明及其实施方式进行了描述,该描述没有限制性,附图中所示的也只是本发明的实施方式之一,实际的结构并不局限于此。所以,如果本领域的普通技术人员受其启示,在不脱离本发明创造宗旨的情况下,不经创造性的设计出与该技术方案相似的结构方式及实施例,均应属于本发明的保护范围。当前第1页12