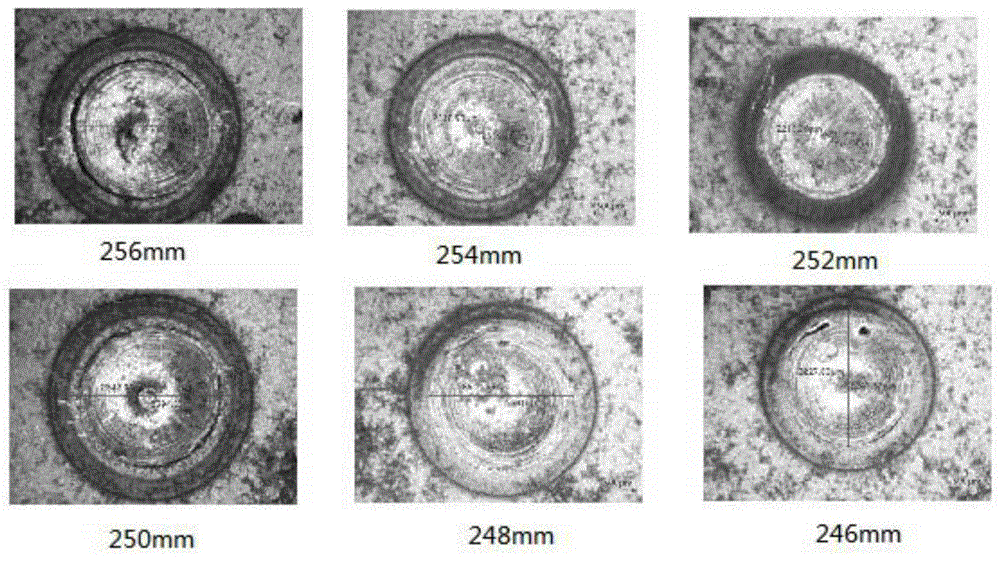
本发明涉及激光熔覆
技术领域:
,尤其涉及一种利用高速激光熔覆技术在铜质基体表面制备熔覆层的工艺。
背景技术:
:激光熔覆是指在被熔覆基体表面通过不同添料方式放置熔覆层材料,经激光辐照使之和基体表面一薄层同时熔化,并快速凝固后形成稀释度低、与基体成冶金结合的表面熔覆层,从而显著改善基层表面的耐磨、耐蚀、耐热、抗氧化及电气特性的工艺方法,达到表面改性或修复的目的,既满足对材料表面特定性能的要求,又可节约大量贵重元素。目前,已经有学者利用二氧化碳激光器或yag激光器进行了结晶器铜板的激光复合熔覆。其中二氧化碳激光熔覆技术得到的熔覆层与基体稀释率较高,热影响区很大,造成熔覆层物理特性降低,基体受热变形率很高,有微型砂眼及气孔;yag激光熔覆技术得到的熔覆层与基体稀释率虽然比二氧化碳激光的熔覆层低,但效率低。对二氧化碳激光器和yag激光器进行激光熔覆工艺存在的问题分析如下:稀释率:激光熔覆层稀释率过高,一般超过10%以上,因此造成熔覆材料特征性能明显下降;热影响区:激光熔覆线速度热影响区较大,一般要超过0.5mm,尺度较大的热影响区呈现的“软带”现象非常显著,因此限制了激光熔覆技术在复杂应力环境条件下的应用场合;搭接区回火:激光熔覆搭接区域因回火现象而导致材料性能较差,造成熔覆层表面性能的不均匀;表面光洁度及加工余量:激光熔覆层表面粗糙度较高,激光加工余量较大,磨削加工的工作量较大,费用较高;总之,目前在结晶器铜板表面进行熔覆的技术还存在很多问题,不能很好地满足工业生产需求。高速激光熔覆技术,是利用超常规、超高速的激光扫描速率,克服传统熔覆技术存在的问题。目前的发展阶段,随着光斑的变小以及光束质量的显著提高,使扫描速率达到了100m/min以上,激光熔覆效率≥1.3m2/h,工作效率显著提高,产品表面粗糙度ra≤10μm,形成高效率、低成本、独具特色的激光熔覆综合技术。高速激光熔覆速度比传统激光熔覆快100~250倍,激光对基体的热影响达到最小,可实现热敏感材料零件的熔覆层制备,而传统方法因热输过高,在热敏感材料上不可能实现;另外这种新工艺还可用于全新的材料组合,例如有色金属或黑色金属熔覆层的制备。完成的熔覆层冶金质量高、稀释率较低、变形小、表面光洁度高,属于先进环保的再制造加工技术,在工业再制造领域能极大地减少企业的后续机加工成本,能有效延长产品使用周期,为企业节省大量后期维修费用。但在铜合金表面进行高速激光熔覆技术具有以下难点:①铜合金的导热性能良好、比热容小、浸湿性能差、表面有坚硬的氧化膜,对光斑的反射率较大,这就使得激光产生的热量在其表面不易停留,不易形成较高的功率密度,不能形成熔池;②铜合金基体与熔覆层的材料体系之间的性能差别很大,熔覆过程中失效问题较严重;③熔覆层内韧性不足,存在热裂和应力等缺陷。技术实现要素:为解决现有技术存在的不足,本发明提供了一种利用高速激光熔覆技术在铜质基体表面制备熔覆层的工艺,形成的熔覆层组织致密、无裂纹、无气孔,稀释率极低,与铜质基体表面能形成良好的冶金结合。为实现上述目的,本发明提供的一种利用高速激光熔覆技术在铜质基体表面制备熔覆层的工艺,使用激光同轴送粉器将熔覆合金材料送入铜质基体表面,同时使用激光器进行逐层高速激光熔覆;所述激光器选用光纤激光器或光纤耦合半导体激光器;所述激光器在熔覆操作过程的工艺参数为:聚焦镜焦距为250~300mm、熔覆功率为2000~8000w、光斑直径为0.3~1.2mm、熔覆扫描速率为100~400mm/s、搭接率为65%。作为对上述技术方案的限定,所述熔覆合金材料包括以下成分:ni:15%~20%;cr:5%~10%;fe:15%~28%;c:6~9%;co:9~20%;b:2~4%;si:3.0~5.0%;p:2%;w3%~4%。作为对上述技术方案的限定,所述熔覆合金材料的粒度为200~800目。作为对上述技术方案的限定,所述利用高速激光熔覆技术在铜质基体表面制备熔覆层的工艺包括以下步骤:a、调整激光器聚焦镜焦距:测定激光实际出光焦点位置,通过对指示红光焦点位置的测量,确定激光离焦量,进而选定聚焦镜焦距范围;b、确定激光器的其它工艺参数:依据激光扫描速率、激光光斑尺寸与激光功率的匹配关系,选定激光器熔覆功率、光斑直径、熔覆扫描速率、与搭接率;c、确定送粉器的工艺参数:采用转盘式双筒送粉器,依据送粉量与单道宽度、单道厚度的关系,选定送粉量;采用高速熔覆专用同轴环形喷嘴,调整粉焦至喷嘴边缘高度,控制激光器的光斑略大于送粉器的粉斑;d、经步骤a~c调控各工艺参数在限定范围内后,操作激光同轴送粉器将熔覆合金材料送入铜质基体表面,并在喷粉同时操作激光器进行逐层高速激光熔覆,得到熔覆层。低速熔覆激光器的离焦量对于熔覆层的性能影响范围很小,但高速熔覆过程离焦量直接影响熔覆效果及熔覆层质量,因此在高速熔覆工艺需确定激光离焦量基础上选定聚焦镜焦距;另外,高速熔覆中送粉与激光熔覆的匹配要求十分高,本发明针对高速熔覆的特性,确定光纤激光器或光纤耦合半导体激光器的熔覆工艺条件,在不需进行任何后续处理的前提下,便能够制备稀释率极低、性能良好的熔覆层。作为对上述技术方案的限定,在喷粉熔覆操作之前,需对铜质基体表面进行抛光与除污处理;使用抛光设备进行抛光处理,使得铜质基体表面光滑有亮泽;使用除污剂进行清洗,去除铜质基体表面的油渍和其它污染物。作为对上述技术方案的限定,得到的熔覆层单层厚度介于80~1200μm之间。综上所述,本发明提供的在铜质基体表面制备熔覆层的工艺,通过利用具有高速扫描速率的激光器,并根据高速熔覆工艺,确定高速激光器的工艺参数,再配以特定的熔覆合金粉末,在不需后续其它处理的前提下,能够在铜质基体表面形成组织致密、无裂纹、无气孔,稀释率极低的熔覆层,并与铜质基体表面能形成良好的冶金结合。为了保证高速激光下熔覆层质量,本发明选取光纤激光器或光纤耦合半导体激光器,在确定光纤激光器或光纤耦合半导体激光器离焦量的基础上选定聚焦镜焦距,并依据激光扫描速率、激光光斑尺寸与激光功率的匹配关系以确定激光器的工艺参数,从而能瞬间形成熔池,产生较小的热影响区,使待熔覆基体只产生微小变形,形成致密度极高、耐磨度更高、稀释率极低、表面改性性能较好且熔覆效率高的熔覆层;另外,在熔覆合金粉末的组成方面,以镍、铁、碳、钴、硼、硅为基础,再结合铬、磷、钨,形成铜质基体表面的熔覆层;利用镍的硬而有延展性的性质以及耐蚀性,使合金能高度磨光,抗腐蚀,提高机械强度;利用铁的耐磨性和磁性,以及元素铁与铬的有效结合,保证合金形成热强性奥氏体结构,并使合金具有高温稳定性和耐热腐蚀性的性能;利用碳对合金组织及性能的重要性,并与铁元素相配合,来获得适当强度、良好韧性和焊接性的合金;利用硼元素可降低熔点、增加流动性的特性,以及硼与氧的亲和力大于金属成分与氧的亲和力,使硼融化时与氧生成氧化硼,融化后浮在熔覆层表面,冷却后形成无孔熔覆层;利用硅增强合金的抗张力、弹性、耐酸性、耐热性、与耐腐蚀性,增大合金的电阻系数;利用磷使基体晶格产生畸变并达到固溶强化,充分发挥镍、铬等合金的高强度合金化能力;还利用钨元素以获得高硬度发碳化物形成弥散强化相,进一步提高熔覆层的耐磨性;本发明的合金粉末通过对各原料组分的匹配筛选,赋予各原料组分对于高速激光熔覆工艺的专用性。附图说明图1为本发明测定激光焦点、工作光斑的示意图;图2为本发明测定激光离焦量的示意图;图3为本发明测定扫描速率时熔覆层的示意图;图4为本发明测定送粉量时熔覆层的示意图;图5为本发明中单道宽度与熔覆层厚度随送粉量大小的变化曲线图;图6为本发明中测定搭接率时熔覆层厚度与面效率的示意图;图7为本发明中测定激光功率时熔覆层厚度的示意图;图8为本发明实施例2中熔覆层的横截面金相图与sem图;图9为本发明实施例2中熔覆层的显微硬度曲线分布图;图10为本发明实施例2中熔覆层及基体的摩擦系数随时间变化曲线;图11为本发明实施例2中熔覆层及基体的磨痕截面形貌、磨痕体积柱状图;图12为本发明实施例2中熔覆层与铜质基体为配副,随温度变化摩擦因数的曲线图;图13为本发明对比例一中选用不同激光器熔覆后的金相显微图和熔覆结合处的扫描电镜图;图14为本发明对比例二中熔覆结合处的金相显微图。具体实施方式下面将结合实施例,对本发明的技术方案进行清楚、完整地描述,显然,所描述的实施例仅仅是本发明一部分实施例,而不是全部的实施例。基于本发明中的实施例,本领域普通技术人员在没有做出创造性劳动前提下所获得的所有其他实施例,都属于本发明保护的范围。实施例一本实施例涉及利用高速激光熔覆技术在铜质基体表面制备熔覆层的工艺。一种利用高速激光熔覆技术在铜质基体表面制备熔覆层,所述熔覆合金材料包括以下质量百分含量的原料组分:ni:15%~20%;cr:5%~10%;fe:15%~28%;c:6~9%;co:9~20%;b:2~4%;si:3.0~5.0%;p:2%;w:3%~4%;其中,熔覆合金材料的粒度为200~800目。各实施例中合金材料的原料配方如下表所示:实施例1.1实施例1.2实施例1.3ni12g16.44g20gcr5.2g8g10gfe16.8g23g28gc5.4g7.4g9gco12g16.5g19.96gb2g3g4gsi3g4g5gp1.2g1.66g2.04gw2.4g3g4g将上表中各实施例的合金材料,利用高速激光熔覆技术在结晶器铜板表面制备熔覆层,其熔覆层的制备工艺包括以下步骤:a、抛光:使用砂纸或抛光机对结晶器铜板表面进行抛光处理,使得结晶器铜板表面光滑有亮泽;b、除污:使用除污剂丙酮对结晶器铜板表面进行清洗,去除结晶器铜板表面的油渍和其它污染物;c、高速激光熔覆:使用光纤激光器高速激光熔覆前,先调整光纤激光器在熔覆操作过程中的工艺参数;c1、激光焦点、工作光斑测定利用光纤激光器测定激光实际出光焦点,通过对指示红光焦点位置的测量,确定激光离焦量,进而选定聚焦镜焦距范围;光纤激光器中激光功率6000w,出光时间0.05s,其打点方式为以激光头聚焦镜片下端为基准面,每打一个点,激光头下降2mm,以此类推,共打6个点,一共做两组实验,光斑直径取其均值。利用体式显微镜对每个点进行尺寸测量,如图1所示,可以看出激光实际出光焦点位置大概位于260mm位置及240mm位置中间处,即252mm位置处。通过对指示红光焦点位置的测量,如图2所示,发现红光焦点位置与实际出光位置存在5mm左右的偏差,即红光焦点位置位于实际出光焦点位置上方5mm左右位置处。红光焦点位置为激光头指示距离,即聚焦镜焦距,通过激光离焦打点的方式可以确定实际出光焦点位置,以实际出光焦点位置来计算工作时的离焦量,进而选定聚焦镜焦距范围。c2、粉焦测定采用高速熔覆专用同轴环形喷嘴,同轴环形喷嘴支持大功率、长时间高速工作,使用散热性能高的紫铜材质,出粉精细,容易形成致密的熔覆层;其性能参数:冷却方式,水冷;粉斑大小,0.6mm;粉末流形状,环形;送粉流量,1~60g/min;粉末粒度,20~150μm;尺寸,100*114.5*49;质量,0.62kg。粉焦至喷嘴边缘高度由上表可知,超高速激光熔覆的送粉系统与常规熔覆送粉系统存在显著不同,不同点在于气体压力、流速、送粉效率、粉末粒度等,同时克服细粉输送存在的堵粉、静电问题。高速激光熔覆头的具有较高的汇聚特性,可以实现粉末粒度200~800目粉末的长距离输送,通过控制粉斑尺寸和光斑尺寸匹配,最大限度提高粉末利用率,不易产生气孔、起伏、方向差异等缺陷,同时还有自适应沉积厚度控制功能,避免熔覆厚度不均匀。c3、扫描速率测定在激光功率、光斑直径、粉斑、送粉量一致的条件下,通过测量在不同扫描速率的情况下单道熔覆效果;其中激光功率为6000w,激光离焦量为5mm,光斑直径为1.0mm,粉焦高度为2mm,送粉气流量为9lpm,送粉气流压力为0.4mpa,保护气流量为13lpm,保护气流压力0.5mpa,送粉量为22g/min,测量扫描速率分别为50mm/s、100mm/s、200mm/s、300mm/s、400mm/s下熔覆效果,得到如图3所示熔覆层的单道金相图;通过金相法检测出的熔覆层起始高度h、熔池深度h,以及相关的熔覆层和基体物理参数,计算得出各扫描速率下的激光熔覆稀释率。由上表可知,在试验误差范围内,在激光参数一定的条件下,激光熔覆层稀释率随扫描速率的增加而减小;另外,由上表和图3可知,激光熔覆层的稀释率极低,在各激光参数的配合下,扫描速率为100mm/s的单道实验效果最好,可见激光器的光斑大小略大于送粉器的光斑。c4、送粉量测定采用转盘式双筒送粉器,转盘式双筒送粉器采用先进的气体动力学原理来实现送粉动能,精确控制对气体流量、粉盘转动、预热温度的要求范围,通过更换不同的送粉粉盘改变送粉效率和粒度,进而扩大其送粉区间和粒度范围,送粉区间为0.4~300g/min,粒度范围为20~250μm。在送粉气为9lpm/mpa,保护气为0.5lpm/mpa,激光离焦量为5mm,粉斑高度为2mm,光斑直径为1.0mm,激光功率为6000w,扫描速率为100mm/s等相关参数不变的情况下,提高送粉量,测定单道宽度、单道厚度。序号送粉量(r/min)厚度(μm)金相宽度(μm)体式宽度(μm)1480167311412510513921016361351223827由上表可知,在激光功率、扫描速率及其他相关参数不变的情况下,提高送粉量,单道厚度增大,宽度降低,如图4所示,表面熔池变窄,团聚于熔覆单道两侧半融化状态的粉末数量增多;单道中心均有大致沿熔覆单道方向的细微裂纹,引起微裂纹的原因多数是因为熔池最后凝固中心出现低熔点金属化合物,韧塑性较差,当熔池凝固冷却的时候受到来自熔覆道两侧的横向拉应力,造成裂纹。如图5所示,在激光功率、扫描速率及其他相关参数不变的情况下,送粉量与单道宽度、熔覆层厚度有一定的比例关系,由图可知,在6r/min即60g/min的送粉量仍然可以在6000w功率下得到与基材结合良好的熔覆层。c5、搭接率测定在激光功率、扫描速率、送粉量等相关参数不变的情况下,测定在不同搭接率下的熔覆层厚度及面效率。因单位时间体成形效率=面效率*单层厚度,结合上表和如图6可知,在可以得到良好冶金结合的基础上,搭接率在65%时,体成形效率越高。c6、激光功率测定在扫描速率、送粉量、搭接率等相关参数不变,测定在不同功率下的熔覆层厚度。如图7和上表可知,在扫描速率、送粉量、搭接率等相关参数不变的情况下,随着激光功率的提高,熔覆层厚度不断增长。经c1-c6调控后,将光纤激光器的工艺参数调整为:聚焦镜焦距为250~300mm、熔覆功率为2000~6000w、光斑直径为0.3~1.2mm、熔覆扫描速率为100~400mm/s、搭接率为65%;使用激光同轴送粉器将粒度为200~800目的熔覆合金材料送入至结晶器铜板表面,同时使用光纤激光器进行逐层高速激光熔覆,形成的熔覆层单层厚度介于0.08~1.2mm之间。实施例二本实施例涉及对实施例一制备的熔覆层性能的检测。将实施例1.1-1.3配比下的熔覆合金材料在本发明工艺下制备得到样品。(1)物相性能的检测随机从所制得的样品中抽取多个作为试品,利用dx-2700x摄像衍射仪对各试品的高速激光熔覆层进行物像分析,均得到如图8(a)所示的熔覆层横截面金相图;由图8(a)可知,上面部分为熔覆层,下面为结晶器铜板,熔覆层与结晶器铜板有明显的界面。在界面处,基体与熔覆层呈冶金结合,熔覆层厚度约为0.4mm,熔覆层内无气孔和裂纹,熔覆层内部质量良好。图8(b)为熔覆层的sem图,显示了熔覆层与结晶器铜板界面的结合情况,其中竖线显示了线扫描的位置和方向。由图8(b)可知,各元素在整个熔覆层分布均匀。(2)硬度性能的检测采用hvs-1000型数字显微硬度计对样品的熔覆层进行维氏硬度测量,加载载荷为200g,加载时间为10s,测量5次后取平均值。从高速激光熔覆层表面垂直向下,每隔0.1mm的距离进行测量,同一垂直距离上沿横向测量三个点,三个点的间隔均为0.2mm,然后取三个点的平均值作为该垂直距离上的维氏硬度值,进而得到如图9所示的样品熔覆层沿厚度方向上的维氏硬度曲线。由图9可知,从显微硬度曲线中可以看出,最高硬度出现在次表层,其最高硬度为786hv,熔覆层平均硬度为567hv,而结晶器铜板的硬度仅为145hv。与结晶器铜板相比较,熔覆层的硬度提高了4~5倍,这也就意味着本发明制得的熔覆层对外接物体入侵的局部抵抗能力较强。(3)耐磨性能的检测随机从所制得的样品中抽取多个作为有熔覆层试品,另外选取多个无熔覆层的结晶器铜板作为对比试品。1.摩擦系数对比图10为熔覆层及结晶器铜板的摩擦系数随时间变化的曲线。从曲线中可以看出,结晶器铜板的最大摩擦系数为0.43,平均摩擦系数为0.4;熔覆层的最大摩擦系数为0.807,平均摩擦系数为0.614,从整个摩擦过程中来看,熔覆层的摩擦运行比较平稳,最终的摩擦系数也在0.6左右波动。2.磨损量对比采用mft-r4000高速往复摩擦磨损试验机对有熔覆层的试品以及无熔覆层试品进行了表面耐磨性的测试,试验结束后,用丙酮清洗试验,干燥后进行摩擦量的测试。摩擦磨损量是通过nanomap500ls扫描三维表面轮廓仪测量而得,其原理是通过扫描探针对试品的磨痕截面进行扫描后,然后用spip5.13软件进行分析。每个试品扫描5次,从而测定出磨痕的平均横截面积,再乘以磨痕长度即得磨痕体积;其中图11(a)为熔覆层和铜质板基体的磨痕截面形貌,图11(b)为熔覆层和铜质板基体的磨痕体积柱状图。由图11(a)可知,结晶器铜板试品的磨痕深度约为70μm左右,宽度为1600μm左右;而熔覆层的磨痕深度约为30μm左右,宽度为1200μm左右。在相同的试验条件下,熔覆层的磨痕、磨宽均小于结晶器铜板结晶器铜板。由图11(b)可知,熔覆层的磨痕体积明显小于结晶器铜板的磨痕体积。表明使用本发明高速激光熔覆工艺对结晶器铜板表面进行高速激光熔覆有利于提高产品的耐磨性,延长了产品的寿命。(4)耐高温性能的检测随机从所制得的样品中抽取多个作为有熔覆层试品,另外选取多个无熔覆层的结晶器铜板作为对比试品。图12是相同摩擦条件下,熔覆层试品与无熔覆层的结晶器铜板为配副,摩擦因数在不同温度下的变化曲线。由图12可知,1、从数值上来讲,熔覆层试品的摩擦因数始终小于无熔覆层的结晶器铜板的摩擦因数,且相差幅度较大;2、从趋势上来讲,随着试验温度的升高,无熔覆层的结晶器铜板的摩擦因数先升高后降低,且波动幅度较大;熔覆层试品的摩擦因数呈逐渐降低趋势,但波动幅度较小。总之,熔覆层试品的摩擦因数受温度变化的影响不大,其耐高温性能远远优于结晶器铜板。对比例一本对比例涉及其它激光器对铜质基体表面熔覆层的影响。选用dl-hl-t10000型co2激光器,用有机玻璃烧斑法选取最佳的激光模式(低阶模),获得稳定的等离子体弧状态,利用红光指示点计算离焦量,其中激光器的工艺参数为:聚焦镜焦距f为200mm,熔覆功率p为6000w,光斑直径d为2mm,熔覆扫描速率v为6m/min,搭接率50%;利用激光器以600mm/min的速度对铜基材进行预热,用红外测温仪测量,当预热温度达400~500℃时快速熔覆镍基合金。如图13(a)为利用二氧化碳激光器熔覆后的金相显微照片,图13(b)为熔覆层与铜基体结合处的扫描电镜照片,从图中可以观察到,熔覆层为明显的层状组织,层间疏松,存在明显的孔洞,而且熔覆层与铜基体之间存在孔隙,界限分明,扫描电镜观察到的间隙,使得熔覆层容易脱落,不耐磨损。选用6000w光纤激光器,采用转盘式双筒送粉器,高速熔覆专用同轴环形喷嘴,操作激光同轴送粉器将熔覆合金材料送入铜质基体表面,并在喷粉同时操作激光器进行逐层高速激光熔覆,得到熔覆层。测定实际出光焦点位置计算激光离焦量,并通过测量指示红光焦点位置,进而确定激光离焦量,其中光纤激光器的具体工艺参数如下:激光功率为6000w,激光离焦量为5mm,光斑直径为1.0mm,粉焦高度为2mm,送粉气流量为9lpm,送粉气流压力为0.4mpa,保护气流压力0.5mpa,送粉量为22g/min。图13(c)和图13(d)为高速熔覆后熔覆层与铜基体结合处的om照片以及sem照片,可以看出激光熔覆后显微组织致密,熔覆层与铜基体为良好的冶金结合。对比例二本对比例涉及不同原料组分的合金粉末对铜质基体表面熔覆层的影响。选用与实施例1.1铜基材成分相近的镍基自熔合金粉末,主要成分为,c:0.018g,si:1.2g,b:0.66g,fe:0.3g,cu:12g,ni:45.822g;选用6000w光纤激光器,采用转盘式双筒送粉器,高速熔覆专用同轴环形喷嘴,操作激光同轴送粉器将熔覆合金材料送入铜质基体表面,并在喷粉同时操作激光器进行逐层高速激光熔覆,得到熔覆层。其中光纤激光器的具体工艺参数如下:激光功率为6000w,激光离焦量为5mm,光斑直径为1.0mm,粉焦高度为2mm,送粉气流量为9lpm,送粉气流压力为0.4mpa,保护气流压力0.5mpa,送粉量为22g/min。观察结合处的金相显微照片如图14所示,发现铜基材被严重稀释,熔覆层有很多孔洞,这些孔洞会造成缺陷和微裂,容易造成应力集中,熔覆层容易脱落,不耐磨损。综上所述,本发明针对高速熔覆的特性,确定激光器的熔覆工艺条件,并配以专用高速熔覆合金粉末,在不需进行任何后续处理的前提下,便可瞬间形成组织致密、无裂纹、无气孔,稀释率极低的熔覆层,并与铜质基体表面能形成良好的冶金结合;另外,待熔覆基体只产生微小变形。当前第1页12