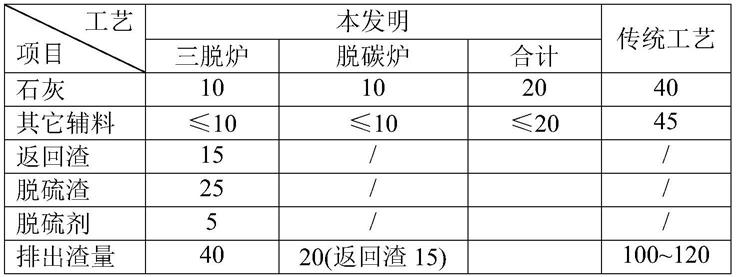
1.本发明属于转炉炼钢领域,特别是提供一种适用于铁水“三脱”预处理与转炉脱碳“双联”工艺采用的炼钢方法。通过提高渣钢反应效率、炉渣阶梯循环利用和在线炉渣改质,大幅减少炼钢炉渣量和完全消除排出渣中的自由氧化钙(cao
f
)含量。
技术背景
2.炼钢的本质是一个氧化提纯过程,即通过吹氧和造渣,使铁水中碳、磷、硅、锰、铬、钛、钒等杂质发生氧化反应,反应生成物(除c以外)进入炉渣,达到钢水提纯的目的。这种传统的炼钢方法存在以下技术问题:
3.(1)钢渣反应效率低,渣量大。以脱磷为例,脱磷效果和渣量决定于渣钢间磷的分配比(l
p
=(%p)/[%p]):当l
p
=100和200时,对相同磷含量的铁水达到相同的终点[p]要求,前者的渣量比后者大1倍。同样,还原条件下脱硫,渣钢间硫分配比(l
s
=(%s)/[%s])为1000;氧化条件下脱硫,l
s
仅为4~6,意味着在相同脱硫效果的前提下,氧化脱硫的渣量约比还原脱硫高160~200倍。
[0004]
(2)倒渣不方便,无法实现炉渣阶梯利用。炼钢渣量决定于化学反应的容量因子和强度因子,即渣量=容量因子
×
强度因子。通常,铁水硅含量是磷、硫含量的10~20倍,硅为容量因子;但脱磷、脱硫要求高碱度(r≥3.5)是脱硅渣碱度要求的2.5倍,为强度因子。所以,常规转炉炼钢为最大的容量因子与最高的强度因子的乘积,造成渣量很大,为100~120kg/t钢。日本开发的murc工艺将炼钢过程分为脱硅、磷期和脱碳期两个阶段,中间倒渣,如图1所示
[1]
。脱碳期渣全部留在炉内供下一炉冶炼使用,比传统炼钢工艺可减少渣量20~30%。但仍存在反应效率不高(l
p
提高不明显),中间倒渣延长5min吹炼时间,降低了转炉生产效率等问题。
[0005]
(3)转炉排出的终渣难以应用。为保证脱磷、脱硫效果,通常碱度r≥3.5,炉渣岩相结构以c3s为主。c3s不稳定,低温下转变为cao
·
sio2或2cao
·
sio2和自由氧化钙cao
f
,造成废弃转炉渣中存在大量cao
f
,极易吸潮,与水反应cao
f
+h2o=ca(ho)2,体积膨胀,造成粉化,限制了转炉渣的应用前景和使用价值。为解决这一问题,国内多采用“闷渣工艺”处理钢渣,效果较好。但对脱除cao
f
的效果不佳(处理后cao
f
为2.63~3.27%)
[2]
;日本开发出“蒸压工艺”,采用密闭容器提高蒸汽压力,进一步降低cao
f
,但渣处理成本高,生产效率低。德国曾试验在电炉出钢后向炉内熔渣喷吹sio2粉末,将高碱度渣在线改质为低碱度渣,如图2所示,但未实现工业化生产
[3]
。
[0006]
(4)大量废弃的高碱度炼钢渣造成严重的环境污染。由于炼钢渣量大、无法循环利用和废弃渣中含大量cao
f
,易水解粉化,性能不稳定等,造成大量炼钢炉渣无法像高炉渣一样生产水泥熟料,完全回收利用。废渣堆积或深埋,不仅占据大量国土面积,而且粉化后形成大量微细白色粉末悬浮在空气中,称为“白色污染”,严重破坏生态环境。
[0007]
为解决传统炼钢方法存在的以上技术问题,全世界炼钢工作者力图改进和优化传统炼钢工艺,进一步提高反应效率,减少渣量;根据各种基元反应特点,实现炉渣的阶梯利
用,并通过炉内在线改质的方法,彻底消除废弃转炉渣中的cao
f
含量,提高废弃转炉渣的回收利用价值。
技术实现要素:[0008]
1.发明原理
[0009]
本发明将传统转炉炼钢过程分解为铁水“三脱”(即脱硅、脱磷和脱硫)预处理和转炉脱碳两个阶段,实现双联生产。在此基础上,采用以下核心技术:
[0010]
(1)提高基元反应效率和减少渣量:利用铁水条件下强还原势,通过控制吹氧、调整炉渣成分和加强熔池搅拌等措施,提高渣钢间磷、硫分配比,减少反应渣量;脱碳炉采用少渣冶炼工艺,控制渣量≤25kg/t钢。
[0011]
(2)实现炉渣阶梯循环利用:利用脱硅渣容量因子大,碱度要求低的技术特点,将脱碳炉和三脱炉脱硫期形成的高碱度炉渣代替石灰,在脱硅期加入。由于脱碳炉终渣或三脱炉脱硫期终渣碱度r≥4.0,和脱硅期要求的炉渣碱度r=1.7~1.8相比,过剩碱度≥2.0。故可采用2吨脱碳炉或脱硫终渣代替1吨石灰,减少石灰加入量。
[0012]
(3)实现在线炉渣改质处理:脱硅期采用吹氧脱硅工艺,喷入的氧气与钢水反应生成大量sio2:2[o]+[si]=(sio2)。反应生成的sio2继续与炉渣反应:
[0013]
cao
f
+sio2=cao
·
sio2[0014]
3cao
·
sio2+sio2=2cao
·
sio2+cao
·
sio2[0015]
2cao
·
sio2+sio2=2(cao
·
sio2)
[0016]
将高碱度脱碳转炉渣或脱硫终渣转变为低碱度脱硅渣,彻底消除易造成炉渣粉化的自由氧化钙cao
f
含量。
[0017]
(4)本发明采用的铁水“三脱”预处理炉具备吹炼过程中连续排渣的功能。在脱硅期开始吹氧后,加入的炉渣迅速与铁水反应,形成泡沫渣。含有大量气体的泡沫化炉渣自动从炉门口溢出,达到连续排渣的目的。排渣量一般要求≥加入渣料的40%。
[0018]
2.技术发明
[0019]
本发明主要用于铁水“三脱”预处理与脱碳转炉双联的生产工艺:铁水“三脱”主要用于铁水提纯,去除铁水中硫、磷、硅、钛等杂质;脱碳转炉主要用于脱碳和升温。以上两个工艺阶段分别在两个独立反应器内单独完成。
[0020]
铁水“三脱”反应器具有连续排渣功能,可在吹炼过程中连续排出泡沫渣,而不需要停止吹炼,倾炉倒渣。脱碳炉与常规转炉相同。“三脱”炉分三期冶炼:第一期为脱硅期,喷吹纯氧并加入造渣剂造渣。第二期和第三期分别为脱磷和脱硫期,通过连续排渣和造新渣,使炉渣的碱度r逐步升高,渣中feo逐步降低。“三脱”炉吹炼结束后将处理后铁水([c]≥3.5%,[si]≤0.1%,[p]≤0.02%,[s]≤0.005%,t≥1300℃)兑入半钢包,尽快加入脱碳炉,吹氧脱碳,升温。由于铁水[si]含量极低,采用少渣冶炼工艺,控制石灰加入量≤10kg/t,其它辅料(如氧化铁皮、镁球或轻烧白云石、萤石等)加入量≤10kg/t,总计渣量≤20kg/t,终渣碱度r≥4.0。典型终渣成分如表1所示。冶炼结束后按常规炼钢方法出钢,出钢后溅渣护炉,并倒尽溅渣后的炉内残渣。倒渣量约为15kg/t。
[0021]
表1脱碳炉终渣典型成份(%)
[0022]
caosio2tfemnomgop2o5sr53.7510.4921.192.089.302.780.0575.37
[0023]
铁水“三脱”炉采用留渣留铁偏心底出铁方式。为减少出铁时下渣量,炉内留铁量为5~10吨,脱硫期产生的高碱度脱硫渣(r≥4.0,tfe≤5%)全部留在炉内,重量约为25~30kg/t
铁
,作为渣料供下一炉脱硅期采用。脱硫渣参考成分列于表2。
[0024]
表2铁水“三脱”炉脱硫期炉渣典型成分(%)
[0025]
caosio2tio2mnop2o5smgotfer44.4110.130.570.461.970.307.475.754.53
[0026]“三脱”炉采用普通高炉铁水作原料,铁水不需要事先进行预脱硅或脱硫处理。兑铁前,加入适量的废钢(废钢比为10~20%)和15~20kg/t已冷凝的脱碳炉终渣,与炉内残留的上一炉脱硫渣混合,经吹氧后形成脱硅渣。当铁水[si]≤0.4%时,脱硅期不用配加石灰;当[si]≥0.4%,适当补加少量石灰。脱硅期一般不需要再加入其它辅助造渣材料。
[0027]
脱硅期吹氧一分钟左右,炉内形成大量泡沫渣,开始从炉门溢渣。可根据炉内渣量、熔池温度和炉渣熔化率,通过调整氧枪枪位,控制炉渣泡沫化,保证合理的溢渣量。即炉内新生渣量为40~50kg/t,溢渣量50~60%,实际炉内渣量维持在20kg/t左右。脱硅期排渣典型成分见表3。
[0028]
表3铁水“三脱”炉脱硅期排渣的典型成分
[0029]
caosio2tio2mnop2o5smgotfer29.4620.011.421.772.060.06110.4718.391.56
[0030]
在随后的脱磷期,根据反应要求补加10~15kg/t的石灰和其它辅助渣料,使渣量进一步增加,炉渣碱度升高,渣中tfe含量降低,炉渣的泡沫性大幅减少,但仍有少量泡沫渣溢出。随吹氧量降低以致停氧,泡沫渣消失,停止溢渣,但炉内渣量基本上维持在20kg/t左右。脱硫期喷吹mg/cao脱硫剂5kg/t,最后炉内剩余残渣25kg/t。
[0031]
图3给出本发明在铁水[si]=0.4%的条件下,整个炼钢过程(包括脱碳炉)造渣工艺方案和炉渣生成与排出量的变化。从图中可以看出:脱碳炉加入石灰10kg/t,其它造渣辅料≤10kg/t,总计渣料≤20kg/t,生成渣量约20kg/t。其中15kg/t回收用于“三脱”炉冶炼。同时炉内留有上一炉脱硫渣25kg/t。脱si期总计生成渣量50kg/t,其中60%渣溢出,约30kg/t。脱磷期加入石灰和辅料≤15kg/t,进一步提高炉渣碱度至r=2.0~2.5。其中溢出渣约10kg/t(溢渣率为50%左右)。喷粉脱硫后不再溢渣,炉内留渣量为25kg/t。
[0032]
表3给出本发明造渣工艺与传统炼钢工艺的比较(铁水[si]=0.4%)。
[0033]
表3本发明造渣工艺与传统炼钢工艺的比较(kg/t,铁水[si]=0.4%)
[0034][0035]
表中可以看出,本发明石灰和造渣辅料消耗各为20kg/t,增加脱硫剂消耗5kg/t,形成炉渣65kg/t,排出炉渣40kg/t。和传统炼钢相比,减少石灰消耗50%,减少辅料消耗60%。排出的总渣量减少60~70%。
[0036]
由于在炉内进行了炉渣改质,将高碱度脱碳炉终渣和“三脱”炉脱硫渣转变为低碱度脱硅渣,彻底消除了渣中cao
f
含量,提高了炉渣的使用性。
附图说明
[0037]
图1日本murc工艺原理示意图
[0038]
图2将氧气和石英砂吹入渣池对钢渣进行改质的工艺原理
[0039]
图3本发明炼钢造渣工艺及炉渣流向图(kg/t)
具体实施方式
[0040]
实施例1:
[0041]
本发明在0.5吨感应炉改装的铁水“三脱”炉中进行炉渣在线改质的热模拟实验,将转炉渣和脱硫渣代替石灰直接用于“三脱”炉脱硅期冶炼,冶炼效果如表4所示。
[0042]
表4本发明0.5t热模拟试验结果
[0043][0044]
试验结果证明:采用本工艺可实现炉渣在线改质,将高碱度炉渣降低为低碱度脱硅渣(r从平均4.53降低到1.56),消除渣中全部自由氧化钙cao
f
,炉渣岩相以硅酸钙、浮氏体和ro相为主,不易粉化。本工艺采用返回渣代替石灰,在脱硅期仍具有较高的脱磷、脱硫效果。
[0045]
实施例2:
[0046]
在传统100t电炉上开展本发明半工业试验:采用80%铁水和20%废钢的炉料结构,电炉冶炼分为脱硅期、脱磷期和脱碳期。将脱碳期生成的高碱度渣全部用于脱硅期冶炼,减少脱硅期石灰加入量,并在脱硅期内通过泡沫渣大量排渣。试验结果如表5所示,不仅减少石灰消耗,而且完成高碱度终渣的炉内改质,排出渣的碱度平均为0.89。
[0047]
表5 100t电炉炉渣改质试验结果
[0048]
吹炼期sio2al2o3mgomnotio2p2o5caot.ferl脱碳期终渣8.481.303.881.810.461.3025.7941.103.0962.9脱硅期14.482.041.593.360.981.6013.3445.820.8912.3