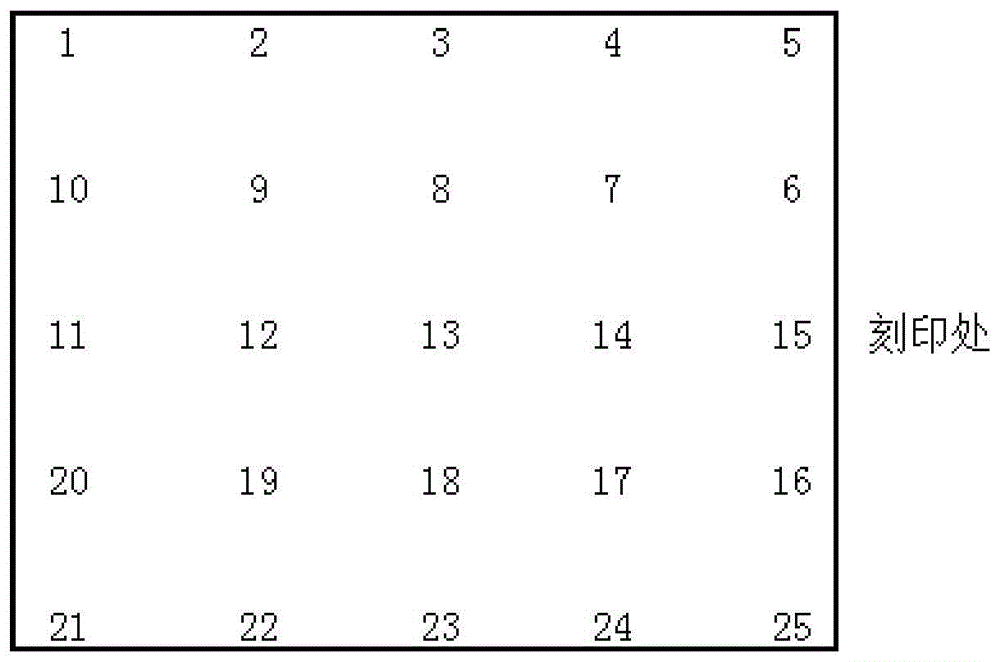
本发明属于干刻上部电极板剥离技术,具体涉及一种剥离液及干刻上部电极板阳极氧化膜的剥离方法。
背景技术:
:阳极氧化膜的剥离是干刻上部电极板(以下简称干刻上部电极板)再生过程中的一道重要工序,干刻上部电极板为一平板结构,表面均匀分布气体扩散孔,其表面阳极氧化膜的厚度一般为40μm左右,孔内的阳极氧化膜厚度为表面氧化膜厚度的70%,氧化膜剥离后规定扩孔率≤0.1mm。阳极氧化膜的剥离是将原有产品表面的氧化膜用化学方法使其溶解脱落,从而露出产品本来的金属表面。阳极氧化膜剥离的效果优劣体现在三个方面:①扩孔率,即剥离膜的同时对铝基材本身的腐蚀量;②氧化膜剥离需要的时间;③氧化膜剥离完后铝基材表面的粗糙度。现有技术中,剥离干刻上部电极板有两种方法:1)15~25%hno3浸泡剥离;2)2~10%naoh腐蚀剥离。但这两种剥离方法均有其不足之处:hno3浸泡剥离所需的时间太长,一般需要浸泡12~16h,浸泡的同时需频繁确认产品的剥离状况,且对干刻上部电极板在客户端使用过程中沾在产品表面的副产物无法形成有效的剥离,导致剥离不净,影响后续的研磨及阳极氧化过程。naoh腐蚀剥离最明显的缺点就是无法保证扩孔率,原因在于naoh与铝及铝阳极氧化膜的反应剧烈,而产品孔内膜的厚度为表面的70%,使得孔内膜完全剥离干净时产品表面仍有残膜,继续剥离则往往使得扩孔率超规;且由于naoh与铝基材反应剧烈,剥离结束后会导致铝基材表面凹凸不平,粗糙度较大,为后期的研磨带来困难,增加研磨量。技术实现要素:本发明的目的在于提供一种剥离液,不仅缩短剥离时间,而且,保证扩孔率,表面粗糙度变化量小。本发明还提供了一种干刻上部电极板阳极氧化膜的剥离方法,利用本发明提供的剥离液进行剥离。本发明具体技术方案如下:一种剥离液,含有以下浓度成分:100-200g/l氢氧化钠、10-30g/l氯化锌、50-100g/l葡萄糖酸钠和2-5g/l十二烷基硫酸钠。所述剥离液的配制采用ph为7±1,电导率≤1us/cm的纯水。进一步,所述的剥离液的配制方法具体为:1)按照配方称取所需氢氧化钠、氯化锌、葡萄糖酸钠、十二烷基硫酸钠和纯水;2)向称取的1/4-1/3量的纯水中加入葡萄糖酸钠和十二烷基硫酸钠,搅拌混匀;3)再加入氢氧化钠,混匀;4)再加入氯化锌,混匀;5)最后加入剩余量的纯水,混匀,即得剥离液。进一步的,步骤3)中加入氢氧化钠过程中通入空气搅拌,并始终保持温度≤60℃。优选的,控制氢氧化钠的加入速度实现温度始终≤60℃。进一步的,步骤4)中加入氯化锌过程中通入空气搅拌,并始终保持温度≤60℃。优选的,控制氯化锌的加入速度实现温度始终≤60℃。由于氢氧化钠与氯化锌溶解于水放热,温度过高水蒸气含有氢氧化钠发出刺激性味道,且容易发生烫伤。本发明提供的一种干刻上部电极板阳极氧化膜的剥离方法,利用上述剥离液进行剥离。具体剥离方法包括以下步骤:s1:将待处理的干刻上部电极板进行脱脂处理;s2:再用剥离液中进行初步剥离;s3:再用硝酸处理;s4:再次进行剥离;s5:重复步骤s3-s4,至剥离满足要求。进一步的,剥离方法还包括:s6:硝酸处理;s7:再碱洗;s8:再硝酸处理s9:冲洗干净,吹干,即可。进一步的,步骤s2初步剥离时间为2~3min。进一步的,步骤s4中剥离时间3~5min。进一步的,步骤s5中,重复步骤s4时,剥离时间为1~3min。所述碱性脱脂剂含35-45%硼砂和三聚磷酸钠5-15%,为市售商品。厂家:麦德美科技(苏州)有限公司。所述硝酸浓度100~300g/l。本发明玻璃液中加入了较高浓度的氢氧化钠,能够有效的对阳极氧化膜进行剥离,同时加入氯化锌、络合剂以及表面活性剂,在氧化膜(成分:三氧化二铝)被反应完全后,通过络合剂作为载体,锌离子将铝置换出来,从而在铝表面形成一层锌钝化膜,延缓氢氧化钠对铝基材的刻蚀速率。优选的,本发明提供的干刻上部电极板阳极氧化膜的剥离方法,包括以下步骤:s1:将待剥离的干刻上部电极板非吊装用螺纹孔用耐酸碱胶塞封堵遮蔽,装挂孔直接上钛合金电极螺丝,然后用角钛挂具开始装挂,装挂完成后用行车吊起干刻上部电极板;s2:先吊进水洗槽处理30~60s,然后吊进浓度20~50g/l,温度60±5℃的碱性脱脂剂进行脱脂浸泡5~10min,期间需来回晃动产品使药液充分进入干刻上部电极板孔穴内,然后再进水洗槽30~60s;此步骤目的是去除产品表面的油脂等脏污;s3:将处理后的干刻上部电极板吊出,用压力≥15mpa高压水枪冲洗表面,确保其表面无脱脂剂残留;s4:再进水洗槽30~60s,然后吊进含上述剥离液的剥离槽中剥离2~3min,期间需来回晃动产品使药液充分进入干刻上部电极板孔穴内,此步骤为初步剥离;s5:再进水洗槽30-60s,然后吊出,检查产品表面有无残胶印痕,有则用240#海绵砂纸手动打磨产品表面;此步骤的作用是:由于产品本身个别区域可能存在残留胶水、制程副产物等附着在产品表面,来料检查时不易发现,经过初步剥离之后能够明显识别,此时可手动打磨,避免其沾在干刻上部电极板氧化膜表面影响剥离效果;s6:再进水洗槽30~60s,然后使用温度35±5℃,浓度100~300g/l硝酸进行中和3~5min,期间需来回晃动产品使药液充分进入干刻上部电极板孔穴内,中和结束后进水洗槽30~60s,此步骤目的为除灰(或叫出光);s7:再使用压力≥15mpa进行高压水枪冲洗,将干刻上部电极板表面冲洗干净;s8:再进水洗槽30~60s,然后进剥离槽3~5min,期间需来回晃动产品使药液充分进入干刻上部电极板孔穴内,然后进水洗槽30~60s;此时在部分露出的铝基材表面能看到灰色钝化膜,阻挡剥离药液进一步与铝基材发生反应腐蚀铝基材,此时测量扩孔率≤0.06mm;s9:再进水洗槽30~60s,然后使用温度35±5℃,浓度100~300g/l硝酸进行中和3~5min,期间需来回晃动产品使药液充分进入干刻上部电极板孔穴内,中和结束后进水洗槽30~60s,此步骤目的为除灰;s10:使用压力≥15mpa进行高压水枪冲洗,将干刻上部电极板表面冲洗干净;s11:进水洗槽30~60s,然后进剥离槽1~3min,期间需来回晃动产品使药液充分进入干刻上部电极板孔穴内,然后进水洗槽30~60s;s12:再进水洗槽30~60s,然后使用温度35±5℃,浓度100~300g/l硝酸进行中和3~5min,期间需来回晃动产品使药液充分进入干刻上部电极板孔穴内,中和结束后进水洗槽30~60s,此步骤目的为除灰以及去除干刻上部电极板表面的钝化膜;s13:吊出干刻上部电极板,水使用压力≥15mpa进行高压水枪冲洗,将干刻上部电极板表面冲洗干净;s14:冲洗结束后,使用ccd耳镜检测孔内膜剥离情况;检查确认孔内剥离完全;s15:吊进30~60s,然后使用温度35±2℃,浓度5~10g/l氢氧化钠进行碱洗10~20s,期间需来回晃动产品使药液充分进入干刻上部电极板孔穴内,然后进槽30~60s;此次碱洗的目的是进一步去除铝基材表面的脏污,同时能使干刻上部电极板表面更加平整均匀;s16:再将干刻上部电极板吊进水洗槽30~60s,然后使用温度35±5℃,浓度100-300g/l硝酸进行中和5~10min,期间需来回晃动产品使药液充分进入干刻上部电极板孔穴内,中和结束后进水洗槽30~60s,此步骤目的为除灰;此时测量扩孔率≤0.07mm;s17:拆除所有螺纹孔的遮蔽胶塞;s18:使用压力≥15mpa进行高压冲洗,重点冲洗干刻上部电极板工作气孔及螺纹孔,确保将干刻上部电极板表面及所有孔冲洗干净,无残留酸或碱;s19:使用干净无油的压缩空气将干刻上部电极板吹干;s20:拆除装挂干刻上部电极板用的角钛挂具及电极螺丝,将装挂用到的螺纹孔用棉签擦拭清洗一遍再用压缩空气吹干螺纹孔,剥离结束。在上述方法中,进水洗槽水洗均是在室温条件下进行。水洗槽水洗的目的是为了除去上一步处理残留在电极板的试剂,以免造成对下一步处理的影响。与现有技术相比,本发明提供的方法,剥离所需时间短;传统工艺剥离一块产品需要12~16h,利用本发明剥离液及剥离方法剥离一块产品仅需2~3h即可完成,效率极大的提高。而且,本发明剥离液保证扩孔率;该类产品扩孔率要求≤0.1mm,现有工艺剥离的产品扩孔率在0.08~0.10mm,而使用本发明剥离液及方法剥离结束后扩孔率仅为0.06~0.07mm;还有,本申请方法剥离后,表面粗糙度变化量小;该类产品剥离之前粗糙度为0.5~1.0μm,现有工艺剥离后的产品粗糙度0.8-1.5μm,产品粗糙度变大量为0.3~0.5μm,而本发明剥离液及剥离方法剥离结束后产品的粗糙度为0.6~1.2μm,产品粗糙度变大量远远低于现有技术。附图说明图1为本发明实施例1-实施例3剥离前孔径及粗糙度测定位置示意图;具体实施方式实施例1一种剥离液,含有以下浓度成分:200g/l氢氧化钠、25g/l氯化锌、75g/l葡萄糖酸钠和5g/l十二烷基硫酸钠。所述的剥离液的配制方法具体为:1)称取所需氢氧化钠、氯化锌、葡萄糖酸钠、十二烷基硫酸钠和纯水;2)室温下将剥离槽洗净,剥离槽中放入称取量1/4-1/3的纯水,测定ph为7±1,电导率≤1us/cm满足要求即可继续配置;否则,继续清洗剥离槽至满足要求;3)加入称取的葡萄糖酸钠和十二烷基硫酸钠,混匀;4)缓慢加入称取氢氧化钠,加入的同时通入空气搅拌,并对温度实时检测,始终保持温度≤60℃;4)再缓慢加入称取的氯化锌,加入的同时需打气搅拌,加入的同时通入空气搅拌,并对温度实时检测,始终保持温度≤60℃;5)药品添加结束后,加入剩余的纯水,混匀,配制完成。利用上述配置的玻璃液对干刻上部电极板阳极氧化膜的剥离的方法,包括以下步骤:先测量待剥离的干刻上部电极板玻璃前的孔径和剥离前粗糙度。测量的位置示意图如图1所示,结果如下表1和表2所示:剥离前孔径范围:1.62-1.65mm,剥离前孔径均值:1.636mm。剥离前粗糙度范围:0.578-0.948um;剥离前粗糙度均值:0.802um。表1剥离前孔径表2剥离前粗糙度位置粗糙度/um位置粗糙度/um位置粗糙度/um10.847110.751210.84620.756120.917220.75930.891130.834230.81940.918140.927240.82750.829150.864250.79460.817160.76470.770170.69280.869180.94890.614190.719100.578200.711具体剥离方法:s1:将待剥离的干刻上部电极板非吊装用螺纹孔用耐酸碱胶塞封堵遮蔽,装挂孔直接上钛合金电极螺丝,然后用角钛挂具开始装挂,装挂完成后用行车吊起干刻上部电极板;s2:先吊进水洗槽处理30~60s,然后吊进浓度45g/l,温度60±5℃的碱性脱脂剂进行脱脂浸泡5min,期间需来回晃动产品使药液充分进入干刻上部电极板孔穴内,然后再进水洗槽30~60s;此步骤目的是去除产品表面的油脂等脏污;s3:将处理后的干刻上部电极板吊出,用压力≥15mpa高压水枪冲洗表面,确保其表面无脱脂剂残留;s4:再进水洗槽30~60s,然后吊进含上述剥离液的剥离槽中剥离2min,期间需来回晃动产品使药液充分进入干刻上部电极板孔穴内,此步骤为初步剥离;s5:再进水洗槽30-60s,然后,检查产品表面有无残胶印痕,有则用240#海绵砂纸手动打磨产品表面;此步骤的作用是:由于产品本身个别区域可能存在残留胶水、制程副产物等附着在产品表面,来料检查时不易发现,经过初步剥离之后能够明显识别,此时可手动打磨,避免其沾在干刻上部电极板氧化膜表面影响剥离效果;s6:再进水洗槽30~60s,然后使用温度35±5℃,浓度280g/l硝酸进行中和5min,期间需来回晃动产品使药液充分进入干刻上部电极板孔穴内,中和结束后进水洗槽30~60s,此步骤目的为除灰;s7:再使用压力≥15mpa进行高压水枪冲洗,将干刻上部电极板表面冲洗干净;s8:再进水洗槽30~60s,然后进剥离槽4min,期间需来回晃动产品使药液充分进入干刻上部电极板孔穴内,然后进水洗槽30~60s;此时在部分露出的铝基材表面能看到灰色钝化膜,阻挡剥离药液进一步与铝基材发生反应腐蚀铝基材;s9:再进水洗槽30~60s,然后使用温度35±5℃,浓度280g/l硝酸进行中和5min,期间需来回晃动产品使药液充分进入干刻上部电极板孔穴内,中和结束后进水洗槽30~60s,此步骤目的为除灰;s10:使用压力≥15mpa进行高压水枪冲洗,将干刻上部电极板表面冲洗干净;s11:进水洗槽30~60s,然后进剥离槽1min,期间需来回晃动产品使药液充分进入干刻上部电极板孔穴内,然后进槽30~60s;s12:再进水洗槽30~60s,然后使用温度35±5℃,浓度280g/l硝酸进行中和3~5min,期间需来回晃动产品使药液充分进入干刻上部电极板孔穴内,中和结束后进水洗槽30~60s,此步骤目的为除灰以及去除干刻上部电极板表面的钝化膜;s13:吊出干刻上部电极板,水使用压力≥15mpa进行高压水枪冲洗,将干刻上部电极板表面冲洗干净;s14:冲洗结束后,目视产品表面氧化膜已完全剥离,使用ccd耳镜检测孔内,确认孔内膜也完全剥离干净;s15:吊进水洗30~60s,然后使用温度35±2℃,浓度5g/l氢氧化钠进行碱洗15s,期间需来回晃动产品使药液充分进入干刻上部电极板孔穴内,然后进槽30~60s;此次碱洗的目的是进一步去除铝基材表面的脏污,同时能使干刻上部电极板表面更加平整均匀;s16:再将干刻上部电极板吊进水洗槽30~60s,然后使用温度35±5℃,浓度浓度280g/l硝酸进行中和10min,期间需来回晃动产品使药液充分进入干刻上部电极板孔穴内,中和结束后水洗30~60s,此步骤目的为除灰;s17:拆除所有螺纹孔的遮蔽胶塞;s18:使用压力≥15mpa进行高压冲洗,重点冲洗干刻上部电极板工作气孔及螺纹孔,确保将干刻上部电极板表面及所有孔冲洗干净,无残留酸或碱;s19:使用干净无油的压缩空气将上部电极板吹干;s20:拆除装挂干刻上部电极板用的角钛挂具及电极螺丝,将装挂用到的螺纹孔用棉签擦拭清洗一遍再用压缩空气吹干螺纹孔,剥离结束,确认剥离后孔径以及粗糙度。结果如下表3和表4。剥离后孔径范围:1.68-1.71mm,剥离后孔径均值:1.698mm,扩孔率:0.062mm。剥离后粗糙度范围:0.691-1.068um,剥离后粗糙度均值:0.924um,剥离后粗糙度变大量:0.122um。表3剥离后孔径位置孔径/mm位置孔径/mm位置孔径/mm11.71111.70211.7021.69121.69221.6931.71131.71231.7041.70141.69241.7151.69151.69251.6961.68161.6971.70171.6981.71181.7091.71191.70101.70201.69表4剥离后粗糙度位置粗糙度/um位置粗糙度/um位置粗糙度/um11.027110.917210.99820.918120.992220.81430.914130.982230.90741.068141.058240.97550.995150.959250.89760.884160.81070.948170.85480.952180.99690.807190.904100.691200.831采用本申请实施例1的剥离液处理后,不仅时间短,而且扩孔率仅仅为扩孔率:0.062mm。剥离后粗糙度范围:0.691-1.068um,剥离后粗糙度变大量仅仅为:0.122um。远远小于现有技术。实施例2一种剥离液,含有以下浓度成分:165g/l氢氧化钠、20g/l氯化锌、55g/l葡萄糖酸钠和4g/l十二烷基硫酸钠。所述的剥离液的配制方法具体为:1)称取所需氢氧化钠、氯化锌、葡萄糖酸钠、十二烷基硫酸钠和纯水;2)室温下将剥离槽洗净,剥离槽中放入所需量1/4-1/3的纯水,测定ph为7±1,电导率≤1us/cm满足要求即可继续配置;3)加入称取葡萄糖酸钠和十二烷基硫酸钠,混匀;4)缓慢加入称取氢氧化钠,加入的同时通入空气搅拌,并对温度实时检测,始终保持温度≤60℃;4)再缓慢加入称取的氯化锌,加入的同时需打气搅拌,加入的同时通入空气搅拌,并对温度实时检测,始终保持温度≤60℃;5)药品添加结束后,加入剩余的纯水,配制完成。利用上述配置的玻璃液对干刻上部电极板阳极氧化膜的剥离的方法,包括以下步骤:先测量待剥离的干刻上部电极板玻璃前的孔径和剥离前粗糙度。测量的位置示意图如图1所示,结果如下表5和表6所示:剥离前孔径范围:1.42-1.44mm,剥离前孔径均值:1.430mm;剥离前粗糙度范围:0.483-0.930um,剥离前粗糙度均值:0.701um。表5剥离前孔径表6剥离前粗糙度位置粗糙度/um位置粗糙度/um位置粗糙度/um10.671110.628210.66420.483120.526220.59130.573130.745230.73540.818140.752240.84250.720150.930250.69860.843160.66770.657170.59480.625180.84790.862190.772100.578200.711具体剥离方法:s1:将待剥离的干刻上部电极板非吊装用螺纹孔用耐酸碱胶塞封堵遮蔽,装挂孔直接上钛合金电极螺丝,然后用角钛挂具开始装挂,装挂完成后用行车吊起干刻上部电极板;s2:先吊进水洗槽处理30~60s,然后吊进浓度45g/l,温度60±5℃的碱性脱脂剂进行脱脂浸泡5min,期间需来回晃动产品使药液充分进入干刻上部电极板孔穴内,然后再进水洗槽30~60s;此步骤目的是去除产品表面的油脂等脏污;s3:将处理后的干刻上部电极板吊出,用压力≥15mpa高压水枪冲洗表面,确保其表面无脱脂剂残留;s4:再进水洗槽30~60s,然后吊进含上述剥离液的剥离槽中剥离3min,期间需来回晃动产品使药液充分进入干刻上部电极板孔穴内,此步骤为初步剥离;s5:再进水洗槽30-60s,然后,检查产品表面有无残胶印痕,有则用240#海绵砂纸手动打磨产品表面;此步骤的作用是:由于产品本身个别区域可能存在残留胶水、制程副产物等附着在产品表面,来料检查时不易发现,经过初步剥离之后能够明显识别,此时可手动打磨,避免其沾在干刻上部电极板氧化膜表面影响剥离效果;s6:再进水洗槽30~60s,然后使用温度35±5℃,浓度280g/l硝酸进行中和5min,期间需来回晃动产品使药液充分进入干刻上部电极板孔穴内,中和结束后进水洗槽30~60s,此步骤目的为除灰;s7:再使用压力≥15mpa进行高压水枪冲洗,将干刻上部电极板表面冲洗干净;s8:再进水洗槽30~60s,然后进剥离槽5min,期间需来回晃动产品使药液充分进入干刻上部电极板孔穴内,然后进水洗槽30~60s;此时在部分露出的铝基材表面能看到灰色钝化膜,阻挡剥离药液进一步与铝基材发生反应腐蚀铝基材;s9:再进水洗槽30~60s,然后使用温度35±5℃,浓度280g/l硝酸进行中和5min,期间需来回晃动产品使药液充分进入干刻上部电极板孔穴内,中和结束后进水洗槽30~60s,此步骤目的为除灰;s10:使用压力≥15mpa进行高压水枪冲洗,将干刻上部电极板表面冲洗干净;s11:进水洗槽30~60s,然后进剥离槽2min,期间需来回晃动产品使药液充分进入干刻上部电极板孔穴内,然后进水洗槽30~60s;s12:再进水洗槽30~60s,然后使用温度35±5℃,浓度280g/l硝酸进行中和3~5min,期间需来回晃动产品使药液充分进入干刻上部电极板孔穴内,中和结束后进水洗槽30~60s,此步骤目的为除灰以及去除干刻上部电极板表面的钝化膜;s13:吊出干刻上部电极板,水使用压力≥15mpa进行高压水枪冲洗,将干刻上部电极板表面冲洗干净;s14:冲洗结束后,目视产品表面氧化膜已完全剥离,使用ccd耳镜检测孔内,确认孔内膜也完全剥离干净;s15:吊进水洗槽水洗30~60s,然后使用温度35±2℃,浓度5g/l氢氧化钠进行碱洗15s,期间需来回晃动产品使药液充分进入干刻上部电极板孔穴内,然后进槽30~60s;此次碱洗的目的是进一步去除铝基材表面的脏污,同时能使干刻上部电极板表面更加平整均匀;s16:再将干刻上部电极板吊进水洗槽30~60s,然后使用温度35±5℃,浓度浓度280g/l硝酸进行中和10min,期间需来回晃动产品使药液充分进入干刻上部电极板孔穴内,中和结束后进水洗30~60s,此步骤目的为除灰;s17:拆除所有螺纹孔的遮蔽胶塞;s18:使用压力≥15mpa进行高压冲洗,重点冲洗干刻上部电极板工作气孔及螺纹孔,确保将干刻上部电极板表面及所有孔冲洗干净,无残留酸或碱;s19:使用干净无油的压缩空气将上部电极板吹干;s20:拆除装挂干刻上部电极板用的角钛挂具及电极螺丝,将装挂用到的螺纹孔用棉签擦拭清洗一遍再用压缩空气吹干螺纹孔,剥离结束,确认剥离后孔径以及粗糙度。如下表7和表8。剥离后孔径范围:1.48-1.51mm,剥离后孔径均值:1.493mm,扩孔率:0.063mm。剥离后粗糙度范围:0.614-1.143um,剥离后粗糙度均值:0.856um,剥离后粗糙度变大量:0.155um。表7剥离后孔径位置孔径/mm位置孔径/mm位置孔径/mm11.49111.49211.4921.49121.49221.4931.51131.49231.5041.48141.50241.4951.49151.50251.4961.50161.4971.51171.4981.50181.4991.48191.49101.49201.50表8剥离后粗糙度位置粗糙度/um位置粗糙度/um位置粗糙度/um10.812110.849210.82320.614120.627220.77530.627130.948230.80940.829140.829241.12450.781151.143250.94660.917160.84370.769170.72980.859181.05491.059190.946100.769200.921采用本申请实施例2的剥离液处理后,不仅时间短,而且扩孔率仅仅为扩孔率:0.063mm。剥离后粗糙度范围:0.614-1.143um,剥离后粗糙度变大量:0.155um。远远小于现有技术。实施例3一种剥离液,含有以下浓度成分:100g/l氢氧化钠、10g/l氯化锌、35g/l葡萄糖酸钠和2g/l十二烷基硫酸钠。所述的剥离液的配制方法具体为:1)称取所需氢氧化钠、氯化锌、葡萄糖酸钠、十二烷基硫酸钠和纯水;2)室温下将剥离槽洗净,剥离槽中放入所需量1/4-1/3的纯水,测定ph为7±1,电导率≤1us/cm满足要求即可继续配置;3)加入称取葡萄糖酸钠和十二烷基硫酸钠,混匀;4)缓慢加入称取氢氧化钠,加入的同时通入空气搅拌,并对温度实时检测,始终保持温度≤60℃;4)再缓慢加入称取的氯化锌,加入的同时需打气搅拌,加入的同时通入空气搅拌,并对温度实时检测,始终保持温度≤60℃;5)药品添加结束后,加入剩余的纯水,配制完成。利用上述配置的玻璃液对干刻上部电极板阳极氧化膜的剥离的方法,包括以下步骤:先测量待剥离的干刻上部电极板玻璃前的孔径和剥离前粗糙度。测量的位置示意图如图1所示,结果如下表9和表10所示:剥离前孔径范围:1.10-1.12mm,剥离前孔径均值:1.111mm;剥离前粗糙度范围:0.537-0.814um,剥离前粗糙度均值:0.698um。表9剥离前孔径位置孔径/mm位置孔径/mm位置孔径/mm11.10111.12211.1121.12121.11221.1231.11131.10231.1141.11141.11241.1151.12151.12251.1161.12161.1171.11171.1181.10181.1191.11191.11101.11201.11表10剥离前粗糙度具体剥离方法:s1:将待剥离的干刻上部电极板非吊装用螺纹孔用耐酸碱胶塞封堵遮蔽,装挂孔直接上钛合金电极螺丝,然后用角钛挂具开始装挂,装挂完成后用行车吊起干刻上部电极板;s2:先吊进水洗槽处理30~60s,然后吊进浓度45g/l,温度60±5℃的碱性脱脂剂进行脱脂浸泡5min,期间需来回晃动产品使药液充分进入干刻上部电极板孔穴内,然后再进水洗槽30~60s;此步骤目的是去除产品表面的油脂等脏污;s3:将处理后的干刻上部电极板吊出,用压力≥15mpa高压水枪冲洗表面,确保其表面无脱脂剂残留;s4:再进水洗槽30~60s,然后吊进含上述剥离液的剥离槽中剥离3min,期间需来回晃动产品使药液充分进入干刻上部电极板孔穴内,此步骤为初步剥离;s5:再进水洗槽30-60s,然后,检查产品表面有无残胶印痕,有则用240#海绵砂纸手动打磨产品表面;此步骤的作用是:由于产品本身个别区域可能存在残留胶水、制程副产物等附着在产品表面,来料检查时不易发现,经过初步剥离之后能够明显识别,此时可手动打磨,避免其沾在干刻上部电极板氧化膜表面影响剥离效果;s6:再进水洗槽30~60s,然后使用温度35±5℃,浓度280g/l硝酸进行中和5min,期间需来回晃动产品使药液充分进入干刻上部电极板孔穴内,中和结束后进水洗槽30~60s,此步骤目的为除灰;s7:再使用压力≥15mpa进行高压水枪冲洗,将干刻上部电极板表面冲洗干净;s8:再进水洗槽30~60s,然后进剥离槽5min,期间需来回晃动产品使药液充分进入干刻上部电极板孔穴内,然后进水洗槽30~60s;此时在部分露出的铝基材表面能看到灰色钝化膜,阻挡剥离药液进一步与铝基材发生反应腐蚀铝基材;s9:再进水洗槽30~60s,然后使用温度35±5℃,浓度280g/l硝酸进行中和5min,期间需来回晃动产品使药液充分进入干刻上部电极板孔穴内,中和结束后进水洗槽30~60s,此步骤目的为除灰;s10:使用压力≥15mpa进行高压水枪冲洗,将干刻上部电极板表面冲洗干净;s11:进水洗槽30~60s,然后进剥离槽2min,期间需来回晃动产品使药液充分进入干刻上部电极板孔穴内,然后进水洗槽30~60s;s12:再进水洗槽30~60s,然后使用温度35±5℃,浓度280g/l硝酸进行中和3~5min,期间需来回晃动产品使药液充分进入干刻上部电极板孔穴内,中和结束后进水洗槽30~60s,此步骤目的为除灰以及去除干刻上部电极板表面的钝化膜;s13:吊出干刻上部电极板,水使用压力≥15mpa进行高压水枪冲洗,将干刻上部电极板表面冲洗干净;s14:冲洗结束后,目视产品表面氧化膜已完全剥离,使用ccd耳镜检测孔内,确认孔内膜也完全剥离干净;s15:吊进30~60s,然后使用温度35±2℃,浓度5g/l氢氧化钠进行碱洗15s,期间需来回晃动产品使药液充分进入干刻上部电极板孔穴内,然后进槽30~60s;此次碱洗的目的是进一步去除铝基材表面的脏污,同时能使干刻上部电极板表面更加平整均匀;s16:再将干刻上部电极板吊进水洗槽30~60s,然后使用温度35±5℃,浓度280g/l硝酸进行中和10min,期间需来回晃动产品使药液充分进入干刻上部电极板孔穴内,中和结束后进水洗30~60s,此步骤目的为除灰;s17:拆除所有螺纹孔的遮蔽胶塞;s18:使用压力≥15mpa进行高压冲洗,重点冲洗干刻上部电极板工作气孔及螺纹孔,确保将干刻上部电极板表面及所有孔冲洗干净,无残留酸或碱;s19:使用干净无油的压缩空气将上部电极板吹干;s20:拆除装挂干刻上部电极板用的角钛挂具及电极螺丝,将装挂用到的螺纹孔用棉签擦拭清洗一遍再用压缩空气吹干螺纹孔,剥离结束,确认剥离后孔径以及粗糙度。如表11和表12所示。剥离后孔径范围:1.17-1.19mm,剥离后孔径均值:1.176mm,扩孔率:0.065mm;剥离后粗糙度范围:0.691-0.984um,剥离后粗糙度均值:0.823um,剥离后粗糙变大量:0.125um。表11剥离后孔径位置孔径/mm位置孔径/mm位置孔径/mm11.17111.19211.1721.18121.17221.1831.17131.18231.1841.17141.18241.1751.18151.19251.1861.19161.1871.17171.1781.17181.1791.17191.18101.17201.17表12剥离后粗糙度位置粗糙度/um位置粗糙度/um位置粗糙度/um10.725110.748210.85720.771120.927220.71630.793130.814230.83940.810140.837240.78150.831150.691250.71860.791160.89770.814170.98480.973180.82090.927190.816100.883200.815采用本申请实施例3的剥离液处理后,不仅时间短,而且扩孔率仅仅为扩孔率:0.065mm。剥离后粗糙度范围:0.691-0.984um,剥离后粗糙变大量:0.125um远远小于现有技术。当前第1页1 2 3