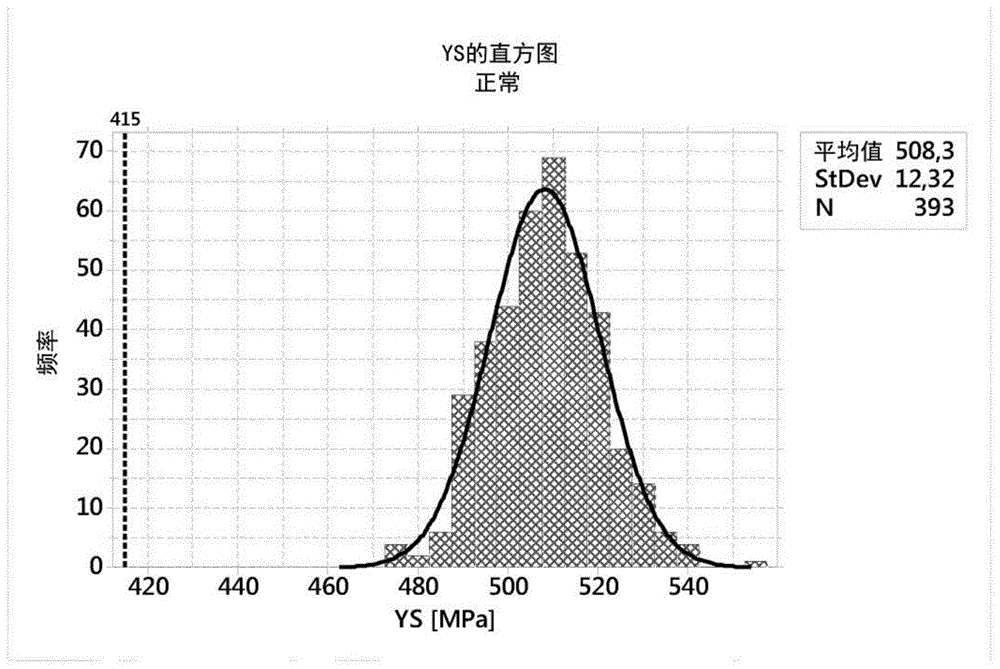
本发明涉及一种可用于制造压力容器、气体输送管道和建筑材料的高强度超低碳钢材。本发明还涉及用于制造高强度超低碳钢材的方法。
背景技术:
:钢发展的总体趋势是朝向更高的强度和低温冲击韧性以及良好的可焊性结合。常规和标准的厚板压力容器钢,(例如astma537cl2)在传统上使用碳含量为0.1至0.2重量百分比(wt.%)制造,以获得足够的强度。由于高碳含量,这些钢的可焊性下降,韧性差且对氢致开裂(hic)的抵抗力低。因此,为了良好的可成形性、低碳当量(ce)、低冲击转变温度、良好的裂纹顶端张开位移(ctod)以及对焊后热处理(pwht)的抵抗力高,有必要降低钢中的碳含量。已经开发了其中碳不是主要强度来源的低碳(c)钢,因为高碳浓度可能导致较差的可焊性和焊接韧性。此外,高碳浓度可能会损害钢的冲击韧性。对极低碳钢进行的首批研究之一是1967年来自福特汽车公司的mcevily等人。他们表明,0.04c-3.0ni-3.0mo-0.05nb给出的屈服强度约为700mpa,转变温度约为-75℃。然而,该组成是高度合金化的,寻求提供同等性能的更经济的合金元素。为了补偿由于低碳含量引起的强度损失,合金设计理念一直基于具有成本效益的微合金元素(例如铌(nb)、钛(ti)、钒(v)和硼(b))与中等含量的其他合金元素(例如锰(mn)、硅(si)、铬(cr)、钼(mo)和铜(cu)结合)的先进使用,以提高奥氏体的淬透性。(微)合金元素与低碳含量结合的前述组合的成熟使用可以产生屈服强度范围为500mpa至900mpa的钢。这些(微)合金元素通过微观结构细化、沉淀硬化和固溶强化以及通过微观结构改性而强化来提高强度。通常,低碳微合金钢是通过热机械控制工艺(tmcp)进行加工的,tmcp传统地由三个阶段组成。在第一个粗轧制阶段,由于重结晶过程的重复循环,奥氏体晶粒尺寸得以细化。在第二个受控轧制阶段,奥氏体在非再结晶温度范围内变形,这对最终的铁素体微观结构带来了显著的细化。在最后阶段,可以采用加速冷却来进一步细化所得到的铁素体晶粒尺寸,同时抑制多边形铁素体的形成,并促进形成低温相变产物(诸如不同类型贝氏体)。因此,这些具有高强度的低碳微合金钢通常被称为低碳贝氏体(lcb)钢。低碳和超细铁素体晶粒尺寸的结合提供了强度和韧性的良好组合,并且由于低碳和低合金含量而具有良好的可焊性。tmcp的组合和(微)合金的应用对与机械性能有关的微观结构发展有影响。在连续冷却的低碳微合金钢中,主要的奥氏体分解产物是铁素体。但是,母体奥氏体的一部分也可能不发生转变,而是可能在室温下保留或部分转变以生成马氏体-奥氏体(ma)微成分。在很高的冷却速度下,即使是具有足够淬透性的极低碳钢也可能转变成马氏体。lcb钢的微观结构通常很复杂,由不同铁素体形态的混合物组成,从多边形铁素体到板条状马氏体不等。日本钢铁协会贝氏体委员会(isij)提出的分类系统和术语可用于表征低碳钢中形成的所有可能的铁素体形态。所有六个铁素体形态的简短描述如下。1.多边形铁素体(pf)表现为大致等轴晶粒且边界光滑。2.准多边形铁素体(qf)表现为晶粒具有起伏的边界,该起伏的边界可能会越过先前的奥氏体边界,该先前的奥氏体边界包含位错亚结构和偶尔的ma微成分。这也称为块状铁素体。3.魏氏铁素体(wf)表现出拉长的铁素体晶体,具有最小的位错亚结构。4.颗粒状贝氏体(gb)呈现出一连串细长的铁素体晶体(颗粒或等轴形状),具有低定向障碍和高位错密度,包含大致等轴的ma成分岛。5.贝氏体铁素体(bf),也称为针状铁素体(af),具有一些平行的铁素体板条或薄板,该铁素体板条或薄板由低角度边界隔开,并具有很高的位错密度。保留在铁素体晶体之间的ma成分具有针状形态。6.错位立方马氏体表现出高度错位的板条状形态,保留了先前的奥氏体边界。ep2484792a1涉及具有三相微观结构的低碳钢,该三相微观结构由以面积分数计的5%至70%的贝氏体和3%至20%的ma成分组成,其余的是准多边形铁素体。为了确保强度,准多边形铁素体的面积分数优选10%或更大。5%至70%的贝氏体确保基材的韧性。3%到20的ma成分确保较低的屈服比以及基材的韧性。三相微观结构排除了多边形铁素体或其他微观结构的存在。低碳钢具有低屈服比、高强度、高韧性和优异的抗应变时效性。低碳钢通过包括以下步骤的方法生产:加热至在1000℃至1300℃范围的温度;在最终轧制温度不低于ar3转变温度下热轧制,其中奥氏体非再结晶温度范围内的累积轧制压缩为50%或更大;加速冷却至500℃至680℃的停止温度;并重新加热至550℃至750℃的温度。ep2380997a1描述了用于焊接结构的低碳钢,该低碳钢具有优异的高温强度、低温韧性和受到抑制的焊接裂纹参数。通过共添加cr和nb来确保高温强度,这有助于转变强化和析出强化。包含贝氏体结构的低碳钢通过包括以下步骤的方法制造:加热至1000℃至1300℃,优选1050℃至1250℃范围的温度;以800℃或更高,优选800℃或更高的最终热轧制温度热轧制;并加速冷却至550℃或更低,优选520℃至300℃的停止温度。jp2007119861(a)或jp2007277679(a)还涉及用于焊接结构的低碳钢,该低碳钢具有优异的高温强度、低温韧性和受到抑制的焊接裂纹参数。包含马氏体-奥氏体混合相(即ma成分)的低碳钢通过包括以下步骤的方法制造:加热至1000℃至1300℃范围内的温度;以750℃或更高的最终轧制温度进行热轧制,其中奥氏体非再结晶温度范围中的累积轧制压缩比为30%或更高;并且加速冷却至350℃或更低的停止温度。在说明书中注意到,当在230℃的温度下使加速冷却停止时,厚度为50mm的钢板的表面与中心之间的硬度差变得极大,使得可弯曲性和扩孔性会受到不利影响。kr20030054424(a)涉及具有高可焊性、高韧性和高于600mpa的高抗拉强度的非热处理低碳钢。发现需要防止在奥氏体晶界中形成多边形铁素体以确保强度。为了获得优异的韧性,必须在奥氏体非再结晶温度区域中将累积轧制压缩控制在30%至60%的范围内。如果在奥氏体非再结晶温度范围内的累积轧制压缩不足30%,则不能有效地提高低温韧性。如果在奥氏体非再结晶温度范围内的累积轧制压缩过度增加并且超过60%,则降低转变温度的效果饱和,而各向异性增加,使得在使用期间会发生板变形问题。本发明的目的在于进一步开发一种高强度低碳钢及其制造方法,使得可以获得具有不受损的机械性能以及经济优势的新型钢材。技术实现要素:鉴于现有技术,本发明的目的是解决提供例如在熔焊压力容器和结构的应用中所需的低温冲击韧性、可弯曲性/可成形性和可焊性优异的高强度低碳钢的问题。通过将具有成本效益的(微)合金设计与具有成本效益的tmcp程序相结合,可以解决该问题,该结合产生主要包含准多边形铁素体的金相微观结构。在第一方面,本发明提供了高强度钢材,该高强度钢材包含由按重量百分比(wt.%)计的以下物质组成的组成或组合物:c0.02-0.05,优选0.03-0.045si0.1-0.6,优选0.2-0.6,更优选0.3-0.5mn1.1-2.0,优选1.35-1.8al0.01-0.15,优选0.02-0.06nb0.01-0.08,优选0.025-0.05cu≤0.5,优选0.15-0.35cr≤0.5,优选0.1-0.25ni≤0.7,优选0.1-0.25cu≤0.03,优选0.005-0.03mo≤0.1v≤0.1,优选≤0.05b≤0.0005p≤0.015,优选≤0.012s≤0.005其余为铁和不可避免的杂质。钢材是低合金的,具有成本效益的合金元素,例如c、si、mn、al和nb。其他元素(例如cu、cr、ni、ti、mo、v和b)可能会作为残留含量存在,该残留含量不会有意添加。残留物含量与不可避免的杂质之间的差异在于,残留物含量是受控数量的不被视为杂质的合金元素。通过工业方法正常地控制的残余含量对合金没有本质的影响。优选地,钢材包括平均夹杂物尺寸为直径1μm至4μm范围内的非金属夹杂物,并且其中95%的夹杂物的直径小于4μm。在第二方面,本发明提供了用于制造高强度钢材的方法,该方法包括以下步骤:-将具有根据权利要求1所述的组成或组合物的钢坯加热至950℃至1350℃的范围内的温度;-在多个热轧制道次中对经加热的钢坯进行热轧制,其中i.钢坯在高于奥氏体非再结晶温度的温度下经受第一批多个轧制道次;ii.将来自步骤(i)的钢坯冷却至低于奥氏体非再结晶温度的温度,iii.来自步骤(ii)的钢坯在低于奥氏体非重结晶温度的温度下经受第二批多个受控轧制道次,其中受控轧制道次的压缩比至少为1.5,优选2.0,更优选2.5,并且其中最终轧制温度范围为800℃至880℃。-以至少5℃/s的冷却速度加速连续冷却至低于230℃的温度。在低于奥氏体非再结晶温度tnr的温度下经受的受控轧制道次导致奥氏体变形的累积,该奥氏体变形的累积导致伸长的晶粒和变形带的形成。晶界和形变带可以作为奥氏体向铁素体(γ-α)转变的成核位点。由于奥氏体晶粒伸长,晶界也越来越接近,从而增加了成核密度。与加速连续冷却导致的高成核速率结合,该工艺最终导致了超细的铁素体晶粒尺寸。在加速连续冷却之后,可选的是在580℃至650℃的范围内的温度下执行额外的回火步骤0.5小时至1小时。额外的回火步骤可以可选地是在通常580℃至700℃的范围内的温度下感应回火1分钟至60分钟。优选地,热轧制的累积压缩比在4.0至35的范围内。必须严格控制加工参数以改善机械性能,特别是韧性,其中涉及的主要参数是加热温度、低于奥氏体非再结晶温度的温度下的受控轧制道次的累积压缩比、最终轧制温度和加速连续冷却停止温度。钢材是厚度为6mm至65mm,优选地10mm至45mm的带(strip)或板。所获得的钢材具有包括基体的微观结构,该基体由按体积百分比(yol.%或体积%)计的以下物质组成:准多边形铁素体40-多边形铁素体和贝氏体20-60珠光体和马氏体≤20,优选≤5,更优选≤2。优选地,该微观结构包括含量为20体积%至40体积%的多边形铁素体。优选地,微观结构包含含量为20体积%或更少的贝氏体。强度和韧性的良好组合与基于准多边形铁素体的微观结构有关。钢材具有以下机械性能:至少400mpa的屈服强度,优选至少415mpa,更优选415mpa至650mpa的范围;至少500mpa的极限抗拉强度,优选在500mpa至690mpa的范围内,更优选在550mpa至690mpa的范围内;在-50℃至-100℃的范围内的温度下,夏比-v冲击韧性为至少34j/cm2,优选至少150j/cm2,更优选至少300j/cm2。该钢材表现出优异的可弯曲性或可成形性。该钢材在纵向或横向上的最小弯曲半径为5.0t或更小,优选3.0t或更小,更优选0.5t,并且其中t为钢带或钢板的厚度。因此,可以实现诸如低温冲击韧性、可弯曲性/可成形性和可焊性以及耐hic和耐pwht等性能的改善。在500℃至680℃范围的温度下进行1小时至8小时,或在600℃至640℃的温度下进行4小时至8小时的焊后热处理对钢材有很少的负面影响或没有负面影响。附图说明图1是示出一生产批次的2000吨板的屈服强度(ys)的图。图2是示出一生产批次的2000吨板的极限抗拉强度(uts)的图。图3是示出一生产批次的2000吨板的总伸长率(tel)的图。图4是示出一生产批次的2000吨板在-45℃(kv)下的冲击韧性值的图。图5是示出具有不同厚度的板的夏比-v冲击韧性的图。图6是示出具有不同厚度的板的nacetm0284hic测试结果的图。图7是示出在输送或pwht条件下具有不同厚度的板的机械性能(ys,uts,tel)的图。图8是示出厚度为12mm、25mm和41mm的板的全厚度抗拉试验结果的图。图9是示出具有不同厚度的板的冲击韧性水平的图。图10是示出轧制参数对厚度为25mm的板中的纵向夏比-v冲击韧性的影响的图。图11是示出轧制参数对厚度为41mm的板中的纵向夏比-v冲击韧性的影响的图。图12图示测试试样的微观结构。具体实施方式术语“钢”定义为包含碳(c)的铁合金。术语“(微)合金元素”用于表示-微合金元素(mae),例如铌(nb)、钛(ti)、钒(v)和硼(b);和/或-中等含量的合金元素,例如锰(mn)、硅(si)、铬(cr)、钼(mo)和铜(cu)。术语“非金属夹杂物”是指在制造过程中发生的污染、化学反应和物理效应的产物。非金属夹杂物包括氧化物、硫化物、氮化物、硅酸盐和磷化物。术语“奥氏体非再结晶温度”(tnr)被定义为低于在轧制道次之间没有发生奥氏体的完全静态再结晶的温度的温度。术语“受控轧制(cr)”是指在低于奥氏体非再结晶温度(tnr)的温度下的热轧制。术语“压缩比”是指通过轧制工艺获得的厚度压缩的比。通过将轧制工艺之前的厚度除以轧制工艺之后的厚度来算出压缩比。2.5的压缩比对应于厚度减小60%。术语“受控轧制比”是指通过在低于tnr的温度下进行受控轧制而获得的压缩比。术语“累积压缩比”是指通过在高于和低于tnr的温度下进行热轧制而获得的总压缩比。术语“加速连续冷却(acc)”是指以一定冷却速率下不间断地加速冷却到一定温度的过程。术语“间断加速冷却(iac)”是指在一定温度范围内以冷却速率进行加速冷却,然后将其空气冷却至低于该温度范围的温度的过程。术语“韧性-脆性转变温度(dbtt)”定义为其中钢具有吸收特定量的能量而不会破裂的最低温度。在高于dbtt的温度下,钢在撞击时会像塑料一样弯曲或变形;而在低于dbtt的温度下,钢在冲击时具有更大的断裂或破碎倾向。术语“极限抗拉强度(uts,rm)”是指极限值,在该极限值下,钢在拉伸下断裂,因此是最大拉伸应力。术语“屈服强度(ys,rp0.2)”是指0.2%的偏移屈服强度,其定义为将导致0.2%的塑性应变的应力的量。术语“总伸长率(tel)”是指材料在断裂之前可以拉伸的百分比;粗略的可成形性指标,通常表示为在测量伸长计的固定标距上的百分比。两种常见的标距长度为50mm(a50)和80mm(a80)。术语“最小弯曲半径(ri)”用于指可以施加到测试片材而不会出现裂纹的最小弯曲半径。术语“可弯曲性”是指ri与片材厚度(t)的比率。符号“kv”是指在用摆锤式冲击试验机进行试验时,破坏所规定的形状和尺寸的v形缺口测试件所需的吸收能量。钢的合金含量以及加工参数决定了微观结构,而微观结构又决定了钢的机械性能。合金设计是开发具有目标机械性能的钢材时要考虑的首要问题之一。通常,可以说,碳含量越低且目标强度水平越高,为了获得同等强度水平,需要更高含量的替代的(微)合金元素。接下来更详细地描述化学组成,其中每种组分的%是指重量百分比。碳c的使用范围为0.02至0.05。碳合金化通过固溶强化来提高钢的强度,因此碳含量决定了强度水平。碳含量小于0.02%可能导致强度不足。但是,碳对钢的可焊性、焊接韧性和冲击韧性具有有害的影响。碳也提高了dbtt。因此,将碳含量设定为不超过0.05。优选地,碳的使用范围为0.03至0.045%。硅6i的使用范围为0.1%至0.6%。硅是有效的脱氧剂或镇静剂(killingagent),该脱氧剂或镇静剂可在炼钢过程中从熔体中除去氧气。硅合金化通过固溶强化来提高强度,并通过增加奥氏体淬透性来提高硬度。硅的存在还可以稳定残余奥氏体。但是,硅含量高于0.6%可能会不必要地增加碳当量(ce)值,从而削弱可焊性。此外,如果过量存在硅,则表面质量可能劣化。优选地,硅的使用范围为0.2至0.6,并且更优选地为0.3%至0.5%。锰mn的使用范围为1.1%至2.0%。锰是改善强度与低温韧性之间的平衡的必要元素。较高的锰含量与较高的强度水平之间似乎存在粗略的关系。锰合金化通过固溶强化来提高强度,并通过提高奥氏体淬透性来提高硬度。但是,锰含量超过2.0%的合金化会不必要地增加ce值,从而削弱了可焊性。如果锰含量过高,则钢的淬透性增加,使得不仅热影响区(haz)韧性劣化,而且促进了钢板的中心线偏析,结果,钢板的中心的低温韧性受损。优选地,锰的使用范围为1.35至1.8%。铝al的使用范围为0.01至0.15%。铝是有效的脱氧剂或镇静剂,该脱氧剂或镇静剂可在炼钢过程中从熔体中除去氧气。铝还可以通过形成稳定的aln颗粒来去除氮并提供细化晶粒,该细化晶粒效果促进高韧性,尤其是在低温下促进高韧性。铝还稳定残余奥氏体。但是,过量的铝可能会增加非金属夹杂物,从而劣化清洁度。优选地,铝的使用范围为0.02%至0.06%。铌nb的使用范围为0.01%至0.08%。铌形成碳化物nbc和碳氮化物nb(c,n)。铌被认为是主要的晶粒细化元素。铌通过四种方式促进钢的强化和增韧:i.通过引入细小的nb(c,n)析出物,在高温下的再加热和均热阶段,由于nb(c,n)的钉扎效应,使奥氏体晶粒结构细化;ii.在高温(>1000℃)下,由于铌溶质拖曳效应而延迟了再结晶动力学,并防止了在较低温度下由于应变诱发的沉淀而导致再结晶的发生,从而有助于微观结构的细化;iii.γ-α转化过程中和/或之后(或随后的热处理)的析出强化;和iv.将相变延迟到较低的温度,导致相变硬化和增韧。在这些钢中,铌是一种优选的合金元素,因为它促进了准多边形铁素体/贝氏体晶粒微观结构的形成,而不是多边形铁素体的形成。然而,由于进一步增加铌含量不会对进一步提高强度和韧性产生显著影响,因此应将铌的添加量限制为0.08%。铌可能对haz韧性有害,因为铌可能通过形成相对不稳定的tinbn或tinb(c,n)沉淀物来促进粗粒上层贝氏体结构的形成。优选地,铌的使用范围为0.02至0.05%。铜cu的使用范围为0.5%或更低。铜可以促进低碳贝氏体结构,导致固溶强化并有助于沉淀强化。铜还具有对抗hic和硫化物应力腐蚀开裂(sscc)的有益效果。当过量添加时,铜会劣化现场可焊性和haz韧性。因此,其上限设定为0.5%。优选地,铜的使用范围为0.15%至0.35%。铬cr的使用范围为0.5%或更低。作为中等强度的碳化物形成元素,铬提高母钢和焊缝的强度,而稍微牺牲了冲击韧性。铬合金化通过提高奥氏体淬透性来提高强度和硬度。但是,如果铬的使用含量超过0.5%,则haz韧性和现场可焊性可能受到不利影响。优选地,铬的使用范围为0.1%至0.25%。镍ni的使用范围为0.7%或更低。镍是改善奥氏体淬透性从而增加强度而又不损失韧性和/或haz韧性的合金元素。但是,如果镍含量超过0.7%,则在没有重大技术改进的情况下,会使合金成本增加太多。过量的镍可能会产生劣化钢材的表面质量的高粘度的铁氧化物皮。由于增加的ce值和裂纹敏感性系数,较高的镍含量也会对可焊性产生负面影响。优选地,镍的使用范围为0.1%至0.25%。钛ti的使用范围为0.或更低。通过与nbc一起形成稳定的tin,添加钛来结合有害于韧性的游离氮,可以有效地防止在高温下的再加热阶段中奥氏体晶粒的生长。tin沉淀物可以进一步防止焊接过程中haz的晶粒粗化,从而提高韧性。tin的形成抑制了fe23c6的形成,从而刺激了多边形铁素体的成核。tin的形成还抑制了bn的析出,从而使b自由地参与其对淬透性的贡献。为此目的,ti/n之比至少为3.4。然而,如果ti含量太高,则tin的粗化和由于tic引起的沉淀硬化发展,并且可能劣化低温韧性。因此,必须限制钛,使其小于0.03%,优选小于0.02%。优选地,ti的使用范围为0.00至0.03%。钼mo的使用含量为0.1%或更低。钼具有在抑制多边形铁素体形成的同时促进低碳贝氏体结构的作用。钼合金化改善了低温韧性和耐回火性。钼的存在还通过提高奥氏体淬透性来提高强度和硬度。在硼合金化的情况下,通常需要钼以确保硼的有效性。但是,钼在经济上不是可接受的合金元素。如果钼的使用含量高于0.1%,则韧性可能劣化,从而增加了脆性的风险。过量的钼也可能会降低硼的作用。钒v的使用含量为0.1%或更低。钒具有与nb基本相同但较小的效果。钒是强碳化物和氮化物的形成元素,但是v(c,n)也可以形成,并且其在奥氏体中的溶解度高于nb或ti。因此,钒合金化具有分散和沉淀强化的潜力,因为大量的钒溶解并且可在铁素体中沉淀。然而,由于形成多边形铁素体而不是贝氏体,因此添加超过0.1%的钒会对可焊性和淬透性产生负面影响。优选地,钒的使用含量为0.05%或更低。硼b的使用含量为0.0005%或更低。硼是成熟的微合金化元素,用于抑制诸如多边形铁素体的扩散转变产物的形成,从而促进低碳贝氏体结构的形成。有效的硼合金化将需要ti的存在以防止bn的形成。在硼存在下,ti含量可以降低到小于0.02%,这对于低温韧性是非常有益的。然而,当硼含量超过0.0005%时,低温韧性和haz韧性迅速劣化。不可避免的杂质可以是含量为0.01或更低,优选0.012%或更低的磷;硫的含量为0.005或更低。其他不可避免的杂质可以是氮、氢、氧和稀土金属(rem)等。为了确保优异的机械性能,例如冲击韧性,它们的含量受到限制。采用洁净的炼钢工艺以尽量减少不可避免的杂质,这些杂质可能会作为非金属夹杂物的出现。非金属夹杂物破坏了结构的均匀性,因此它们对机械性能和其他性能的影响可能很大。在因扁平、锻造和/或冲压而引起的变形中,非金属夹杂物会导致钢的开裂和疲劳破坏。因此,平均夹杂物尺寸通常限制为1μm至4μm,其中95的夹杂物的直径小于4μm。高强度钢材可以是典型厚度为6mm至65mm,优选10mm至45mm的带或板。调节tmcp的参数以实现具有该化学组成的最佳微观结构。在加热阶段,将板坯加热到950℃至1350℃(通常为1140℃)范围内的排料温度,这对于控制奥氏体晶粒的生长非常重要。加热温度升高会导致微合金沉淀物的溶解和粗化,从而导致晶粒异常生长。在热轧制阶段,根据板坯和最终产品的厚度,对板坯进行热轧制,通常采用16-18个热轧制道次。优选地,在热轧制阶段结束时,累积压缩比在4.0至35的范围内。在高于奥氏体非再结晶温度的温度下进行第一个热轧制工艺,然后在低于tnr的温度下进行受控轧制之前,将板坯冷却至低于tnr的温度。在低于奥氏体非再结晶温度的温度下进行受控轧制会导致奥氏体晶粒伸长,并产生铁素体晶粒的起始位点。形成煎饼状的奥氏体晶粒,从而在奥氏体晶粒中积累应变(即位错),可通过充当奥氏体向铁素体相变的成核位点而促进铁素体晶粒细化。至少为1.5,优选2.0,更优选2.5的受控轧制比确保奥氏体晶粒充分变形。采用4至10个轧制道次可实现2.5的受控轧制压缩比,其中每道次的压缩比约为10.25%。奥氏体非再结晶区中的变形的最显著结果是韧性性能的提高。令人惊讶地,发明人发现将受控轧制压缩比从1.8提高至2.5或更高可以显著降低转变温度,从而提高低温冲击韧性。最终轧制温度通常在800℃至880℃的范围内,这有助于微观结构的细化。将热轧制产品以至少5℃/s的冷却速率加速冷却至低于230℃的温度,优选室温。在从高于ar3的温度到冷却停止温度的快速加速冷却期间,促进了铁素体晶粒的细化。在加速冷却步骤中也形成了诸如贝氏体的低温转变微观结构。任选地,进行诸如回火或退火的热处理的后续步骤,以微调微观结构。优选地,在580℃至650℃的范围内的温度内进行回火0.5小时至1小时。回火的额外步骤可以可选地是通常在580℃至700℃的范围内的温度内的感应回火1分钟至60分钟。在加速连续冷却期间,在降低的温度下,先发生多边形铁素体转变,然后依次进行准多边形铁素体转变、贝氏体转变和马氏体转变。最终的钢材具有基于准多边形铁素体的混合微观结构。微观结构包括按体积百分比计的40%至80%的准多边形铁素体和20至60%的多边形铁素体和贝氏体,其余的20%以下,优选5%以下,更优选2%为珠光体和马氏体。任选地,该微观结构包括按体积百分比计的20至40的多边形铁素体。任选地,该微观结构包含按体积百分比计的20%或更少的贝氏体。有时,可以在微观结构中检测到ma成分的岛。钢的良好韧性和尤其低dbtt通常与高密度的高角度边界有关,而高角度边界通常存在于微观结构中,因此是有益的,因为这些边界会阻碍裂隙扩展。准多边形铁素体占主导地位的微观结构有利于在准多边形铁素体与颗粒贝氏体铁素体的界面之间形成高角度边界,而准多边形铁素体的形成消除了微观结构中先前的奥氏体晶界。准多边形铁素体为主的微观结构还减小了ma微成分的尺寸和比例,ma微成分被认为是脆性断裂的有利成核位点。ma成分的分布仅限于微观结构的颗粒状贝氏体铁素体部分。如果在ma微成分附近引发裂解微裂纹,则由于相邻的高角度边界,该微裂纹的传播容易钝化并暂时停止。为了使微裂纹达到临界长度(超过该临界长度,微裂纹会以不稳定的方式传播),需要更多的能量来通过例如短的微裂纹以剪切模式旋转来连接和链接相邻的微裂纹。因此,具有准多边形铁素体为主的微观结构的钢具有改进的冲击韧性和尤其低dbtt。该钢材的屈服强度至少为400mpa,优选至少为415mpa,更优选415mpa至650mpa;极限抗拉强度为至少500mpa,优选在500mpa至690mpa的范围内,更优选在550mpa至690mpa的范围内。在-50℃至-100℃的范围内的温度内,钢材的夏比-v冲击韧性为至少34j/cm2,优选至少150j/cm2,更优选至少300j/cm2。该钢材在纵向或横向上的最小弯曲半径为5.0t或更小,优选3.0t或更小,更优选0.5t,并且其中t为钢带或钢板的厚度。即使在将钢材在500℃至680℃的范围内的温度内进行焊后热处理1小时至8个小时,优选地在600℃至640℃的范围内的温度内进行焊后热处理4小时至8个小时后,也可以保持改善的机械性能。以下实施例进一步描述和说明了本发明范围内的实施方式。给出这些实施例仅出于说明的目的,而不应解释为对本发明的限制,因为在不脱离本发明范围的情况下其可有许多变型。实施例1表1列出了用于生产被测板的化学组成。表1实施例1的化学组成(wt.%)。csimnalnbcucrnitimov目标0.0350.41.550.030.030.250.20.150.01500最小值0.0250.31.480.020.0250.150.10.10.005最大值0.050.51.60.060.050.350.250.250.030.070.03被测板是通过包括以下步骤的方法制备的:-加热到1140℃的温度;-热轧制,其中受控轧制压缩比为2.5,最终轧制温度范围为840℃至880℃内;-加速连续冷却至约100℃;和-在约640℃下回火。微观结构微观结构可以通过sem显微照片来表征,体积分数可以使用点计数或图像分析方法来确定。被测板的微观结构包括40%至80%的准多边形铁素体、20%至40%的多边形铁素体和20%或更少的贝氏体,其余为珠光体和马氏体。屈服强度屈服强度使用一生产批次的2000吨板的横向试样根据astme8标准确定。横向屈服强度的平均值(rp0.2)为508±12mpa(图1)。抗拉强度抗拉强度使用一生产批次的2000吨板的横向试样根据astme8标准确定。横向极限抗拉强度(rm)的平均值为590±1mpa(图2)。伸长率伸长率使用一生产批次的2000吨板的横向试样根据astme8标准确定。横向总伸长率(a50)的平均值为30±1.4%(图3)。可弯曲性弯曲试验包括通过使用单冲程的三点弯曲对测试件进行塑性变形,直到卸载后达到指定的弯曲角度90°。在整个测试系列中,对弯曲的检查和评估是一个连续的过程。这样可以决定是否应增大、保持或减小冲头半径(r)。如果在纵向和横向上均使用相同的冲头半径(r)满足最小3m的弯曲长度(无任何缺陷),则可以在测试系列中确定材料的可弯曲性(r/t)极限。裂纹、表面颈缩痕迹和平坦弯曲(明显的颈缩)被记录为缺陷。根据弯曲试验,该板在纵向和横向上的最小弯曲半径(ri)为板厚度(t)的0.5倍,即ri=0.t。耐pwht即使在620℃进行8小时的严格pwht处理后,仍保持优异的抗拉性能,例如至少415mpa的屈服强度和至少550mpa的极限抗拉强度。夏比-v冲击韧性根据a6me(美国机械工程师学会)标准,通过夏比-v形缺口测试获得了-45℃时的冲击韧性值。图4示出,使用一生产批次的2000吨板的6.7mmx10mm的横向试样测得的平均冲击韧性值为274j。图5示出了在纵向和横向上具有不同厚度的板的夏比-v冲击韧性结果。表1-1总结了横向上不同厚度的板的夏比-v冲击韧性结果。表1-1不同厚度板的夏比-v冲击韧性厚度(mm)kv(j/cm2)温度(℃)方向10338-100横向20587-80横向30583-60横向41573-60横向在横向方向上,厚度为10mm的测试板在-100℃的温度下的冲击韧性为338j/cm2;厚度为20mm的测试板在-80°的温度下的冲击韧性为587j/cm2;厚度为20mm的测试板在-60℃的温度下的冲击韧性为583j/cm2;厚度为41mm的测试板在-60℃的温度下的冲击韧性为573j/cm2。可焊性可焊性测试在41mm厚的板上进行。通过使用尺寸为41mmx200mmx1000mm的测试件焊接三个对接接头来执行可焊性测试。沿主轧制方向从板上切下测试件,使得1000mm长的对接焊缝平行于轧制方向。使用0.8kj/mm的热量输入,采用药芯焊丝电弧焊fcaw工艺no.136,并且使用3.5kj/mm的热量输入,采用单丝埋弧焊工艺no.121,来焊接接头。板的焊接前的预热温度在125℃至130℃的范围内,层间温度在125℃至200℃的范围内。使用坡口角度为25°的半v形坡口制备来焊接对接接头。可消耗用于fcaw工艺的所选焊接材料为具有en/aws分类t50-6ni-p-m21-1-h5/e81t1-m21ani1-h4的esabfilarcpz6138。可消耗用于saw工艺的所选焊接材料为具有en/aws分类s-46-7-fb-s2ni2/f7a1eni2-ni2的esabokflux10.62和esabokautrod13.27焊丝。在焊接状态和pwht条件下均测试了通过3.5kj/mm的热量输入进行焊接的焊缝。施加的pwht在600℃的温度下在4小时的保持时间内进行。表1-2总结了以下焊接接头的机械测试结果:-矩形试样的两次横向拉伸试验;-在-40℃和-50℃下用三个10mmx10mm试样从以下位置进行斜面的夏比-v形试验:融合线+1mm(fl+1)和融合线+5mm(fl+5);和-维氏硬度hv10交叉焊缝硬度分布图。力学测试结果表明,钢试样在低温下具有出色的可焊性和出色的haz韧性。耐hichic测试是根据nace(美国腐蚀工程师协会)tn0284进行的。图6显示了具有不同厚度的板的nacetm0284hic测试结果。被测板均显示出低于15%的平均(avg.)裂纹长度比(clr),这表明该钢在酸性气体环境中具有出色的性能。符号“csr”是指裂纹敏感度比。符号“ctr”是指裂纹厚度比。实施例2表2列出了用于生产测试板的化学组成。板坯编号c002是比较例。通过实施例1中所述的方法制备被测板。最终轧制温度(frt)和低于奥氏体非再结晶温度的受控轧制(cr)道次的累积压缩比是决定微观结构和力学性能的主要参数。表2-1总结了被测板的厚度、frt和cr压缩比。板坯编号c002和c002-是比较例。表2-1被测板的厚度、frt和cr压缩比的总结板坯编号厚度(mm)frt(℃)cr压缩比55106261258201.855106262258201.855106331258003.055106031418201.855106032418201.855106012418002.555106049418503.0e002-1418383.0c002-1417781.8c002-2417772.5抗拉性能抗拉性能使用横向的、40mm宽的且矩形的试样根据astme8确定。图7显示,在输送条件下,所有厚度为10mm至41mm的被测板的屈服强度均高于480mpa,极限抗拉强度均高于550mpa。输送条件定义为在用于制造实施例2的被测板的热机械控制处理(tmcp)中的加速连续冷却(acc)和回火(t)的步骤之后没有任何进一步处理的tmcp-acc-t条件。在600℃下进行4小时的焊后热处理(pwht)对抗拉性能的影响很小(图7)。在厚度为12mm、25mm或41mm的板上进行了全厚度抗拉测试。失效前横截面减小的百分比越大,反映出钢在z方向上的延展性越大。图8显示,横截面积减少的百分比为77.6%至81.,远大于标准等级as7ma537cl2所需的35%。夏比-v冲击韧性根据astme23,使用厚度为10mm的7.5mm×10mm的纵向板和厚度为15mm、20mm、25mm或41mm的10mm×10mm的纵向板来测定冲击韧性。如图9所示,对于不同厚度的板,夏比-v冲击韧性有所不同。表2-2总结了纵向上不同厚度的板的夏比-v冲击韧性结果。表2-2不同厚度板的夏比-v冲击韧性厚度(mm)kv(j/cm2)温度(℃)方向10>300-68纵向15375-68纵向20300-60纵向25375-60纵向41320-52纵向10mm厚和15mm厚的板的冲击韧性水平在-68时位于大于300j/cm2的上层搁板中,在输送条件下15mm厚的板的能量为375j/cm2。在-60℃下,输送条件或pwht条件下厚度为20mm和25mm的板的冲击韧性水平分别为300j/cm2和375j/cm2。在-52℃下,41mm厚的板的冲击韧性水平为320j。图10和图11分别显示了受控轧制压缩比对25mm和41mm厚板(表2-1)的冲击韧性的影响。图10显示了在25mm厚的板中将受控轧制压缩比从1.8提高到3使得转变温度从-52℃降低到-60℃。在41mm厚的板中,将受控轧制压缩比从1.8升高到2.5将转变温度从-40降低到-60°(图11)。当受控轧制压缩比为3.0时(图10和图11),可以获得最佳结果。耐pwht在600℃下进行4小时的焊后热处理(pwht)对抗拉性能,例如屈服强度、极限抗拉强度和伸长率(图7)或夏比-v冲击韧性结果(图9至图11)的影响很小。可弯曲性使用实施例1中描述的方法测量可弯曲性。厚度为41mm的板在纵向和横向两者上的最小弯曲半径为板厚度的0.49倍(ri=0.49t)。微观结构使用实施例1中所述的方法对微观结构进行表征。如图12所示,厚度为41mm的钢的微观结构(表2-1)包括准多边形铁素体、多边形铁素体和贝氏体。受控轧制(cr)压缩比的水平和最终轧制温度(frt)对晶粒尺寸有影响。通过受控轧制压缩比3.0和最终轧制温度838°的组合,可以得到如图9(a)所示的e002-1所需的微观结构。较高的受控轧制压缩比产生更多的铁素体晶粒的起始位点,从而减小晶粒尺寸。当所施加的最终轧制温度低于800℃时,例如c002-的情况下为798℃[图9(b)]或在c002-的情况下温度为777℃[图9(c)],晶粒尺寸大于施加的最终轧制温度高于800℃时的晶粒尺寸[图9(a)]。实施例3表3列出了用于生产被测板的化学组成。板坯编号c003是比较例。通过实施例1中所述的方法制备被测板。表3-1总结了被测板的冷却参数。加速连续冷却停止温度对机械性能的影响很小或没有影响(表3-2)。但是,加速连续冷却停止温度是决定低温韧性的重要参数(表3-3)。在41mm厚的板上进行了中断加速冷却的轧制试验,这表明加速连续冷却至低于230℃的温度对于低温韧性非常重要。在250℃至290℃的范围内的温度下中断加速冷却时(表3-1),在-60°的温度下,夏比-v冲击韧性急剧劣化(表3-3)。当前第1页12