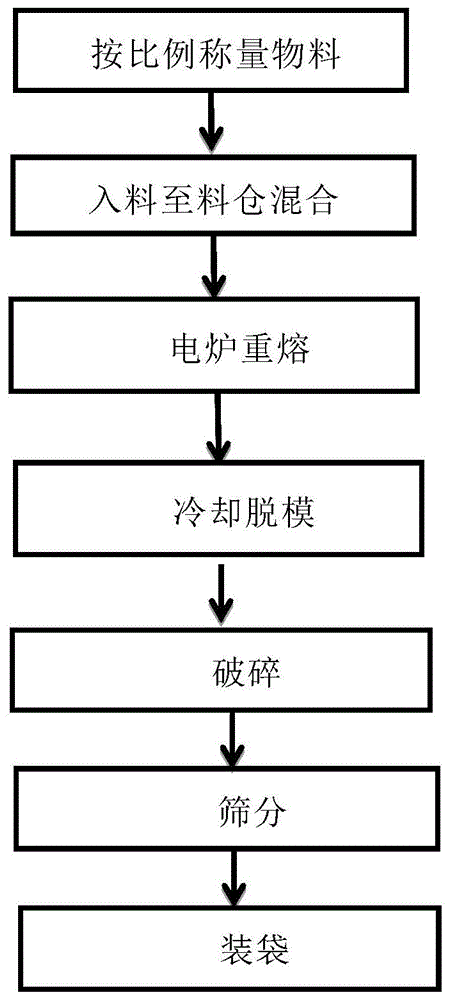
本发明涉及一种炼钢调渣用化渣剂及制备方法,主要应用于炼钢钢液表面渣的粘度调节
技术领域:
。
背景技术:
:目前,钢铁行业在炼钢调渣工艺中普遍使用萤石来调节钢渣的粘度。使用萤石存在以下不足之处:第一,萤石属于矿产资源,近年来由于环保压力的增加,萤石的市场价格飞涨造成钢铁企业生产成本大幅度增加;第二,从矿山上挖出来的萤石由于含量分布不均匀,给钢铁企业检测,工人使用操作带来大量的麻烦;第三,萤石的大量使用导致氟化物大气污染;针对现有钢铁企业使用萤石的上述这些问题,应采用新方法对现有的方法进行改进。技术实现要素:本发明的技术解决问题:克服现有技术的不足,提供一种炼钢调渣用化渣剂及制备方法,在达到萤石相同的调渣效果下,用量仅为萤石(80%含量)的一半。由于主要原料来自于成本低廉的工业副产物,大大节约了炼钢成本以及降低了氟元素对环境的污染。本发明技术解决方案:一种炼钢调渣用化渣剂,由磷化工副产品氟硅酸钠(na2sif6)以及铝熔炼行业副产品铝灰按一定比例配置而成。具体包括如下组份及质量百分数:氟元素(f)30~55%,铝元素(al)5~20%,钠元素(na)10~30%,钙元素(ca)1~10%,硅元素(si)2~15%,氧元素(o)5~20%。进一步优选为,氟离子(f)35~50%,铝元素(al)5~15%,钠元素(na)15~25%,钙元素(ca)1~10%,硅元素(si)2~15%,氧元素(o)5~20%。生产出的产品的稳定性更好,而且可以在达到相同性能情况下,使用普通铝灰配置而成,从而降低成本。如图1所示,本发明一种制备炼钢调渣用化渣剂的方法,包括以下步骤:(1)称取原料氟硅酸钠及铝灰,按照前述的化渣剂组份及质量百分数计算出与之相关应的原料,并称量待用;(2)将原料放入电感应炉中,调节电流5-25a、感应温度1500-1800℃、熔炼时间30min后倒入至钢制模具中,冷却后至室温后脱模倒出,再使用破碎机破碎后即制得化渣剂产品。一种炼钢调渣用化渣剂的表征方法,所述化渣剂从520摄氏度开始熔化,在720摄氏度大部分已熔化为液态。本发明一种炼钢调渣用化渣剂的使用方法,在转炉精炼炉电炉中均可替代萤石,不需要改变炼钢生产工艺,只需要按比例减少化渣剂添加量。具体替代萤石实验包括以下步骤:(1)确定实验炉次,通知生产不得在实验炉次使用萤石而改用新型化渣剂。(2)实验炉次对“使用化渣剂炉次”记录清楚:①达到生产所需炉渣效果时所有化渣剂用量(参考用量以平时萤石用量的50%),化渣剂用量根据渣子情况由少到多逐渐调整;②石灰用量。(3)使用化渣剂的炉次,选取至少3炉终点渣样。(4)实验炉次,车间安排钢包热修观察钢包侵蚀情况,并做好记录。(5)将“原用萤石炉次”与“使用化渣剂炉次”成本对比,是否降低成本;结合现场使用情况,判定化渣剂是否达到要求。本发明与现有技术相比的优点在于:(1)与现有钢铁企业萤石化渣相比,用量只有80%萤石的40-70%左右,生产成本可以控制在比萤石更低;同时本发明的产品与现有的萤石化渣剂相比稳定性大大提高;(2)利用其它行业副产品,节约宝贵的萤石自然资源,给子孙后代留下财富;(3)萤石在工业生产中,由于消耗量大,产生的sif4有毒气体严重,使用本产品有毒气体量会有所减少,有利于环保。附图说明图1为本发明化渣剂的制备方法的流程图;图2为本发明的本发明化渣剂dta曲线。具体实施方式下面结合附图及具体实施例详细介绍本发明。但以下的实施例仅限于解释本发明,本发明的保护范围应包括权利要求的全部内容,不仅仅限于本实施例。本发明的化渣剂产品由氟硅酸钠以及铝灰按一定比例搅拌均匀,之后可采用重熔破碎工艺制成钢厂易于使用的颗粒状产品。实施例1(1)按比例称取定量氟硅酸钠和铝灰,放入料仓中混合,混合后各元素质量百分比如下:元素名称质量百分数na16.70%ca1.45%al24.50%f41.38%o13.94%si2.03%(2)将料仓中物料投入到电感应炉中,调节电流5-25a、感应温度1600℃、熔炼时间30min后倒入至钢制模具中;(3)待重熔物冷却后至室温后脱模倒出。对脱模后的产品使用鄂氏破碎机破碎;(4)筛分破碎后产品,获得粒径为5-70mm部分,装袋制得化渣剂产品;(5)本发明的化渣剂与现有80%萤石实验数据对比如下:本发明化渣剂与80%萤石在同样钢种及炉况下使用量对比:化渣剂平均每炉用量:56.33kg;萤石平均每炉用量:175.5kg。本发明的优点:(a)降低成本:80%萤石的市场价格约3000rmb/吨,化渣剂约3600rmb/吨,平均每炉成本降低约3rmb/kg*175.5kg-3.6rmb/kg*56.33=323.712rmb。每炉钢水重量约70吨,吨钢成本降低约4.6rmb。(b)sif4排放量减少:由于sif4无色无味,在钢厂敞开式操作模式下现行技术难以检测其浓度,本发明从sif4源头f加入量推测sif4的减少量。使用萤石每炉总氟加入量:175.5kg*38.97%=68.40kg使用本发明的化渣剂每炉总氟加入量:56.33kg*41.38%=23.31kg在炼钢生产中,sif4的产生量与投入物料氟总量成正比关系。使用化渣剂可以减少sif4排放量为:(68.40-23.32)/68.40=65.91%。总之上述可以看出,本发明具体实施例1使吨钢使用成本降低4.6rmb,sif4有毒气体产生量减少65.91%。实施例2(1)按比例称取定量氟硅酸钠和铝灰,放入料仓中混合,混合后各元素质量百分比如下:元素名称质量百分数na11.18%ca2.99%al27.26%f38.37%o19.15%si1.05%(2)将料仓中物料投入到电感应炉中,调节电流5-25a、感应温度1600℃、熔炼时间30min后倒入至钢制模具中;(3)待重熔物冷却后至室温后脱模倒出。对脱模后的产品使用鄂氏破碎机破碎;(4)筛分破碎后产品,获得粒径为5~70mm部分,装袋制得化渣剂产品;(5)本发明的化渣剂与现有80%萤石实验数据对比如下:本发明的化渣剂与80%萤石在同样钢种及炉况下使用量对比:化渣剂平均每炉用量:232.5kg萤石平均每炉用量:433.33kg本发明的优点:(a)降低成本80%萤石的市场价格约3000rmb/吨,化渣剂约3600rmb/吨,平均每炉成本降低约3rmb/kg*433.33kg-3.6rmb/kg*232.5kg=462.99rmb。每炉钢水重量约120吨,吨钢成本降低约3.85rmb。(b)sif4排放量减少使用萤石每炉总氟加入量:433.33kg*38.97%=168.86kg使用化渣剂每炉总氟加入量:232.5kg*38.37%=89.21kg在炼钢生产中,sif4的产生量与投入物料氟总量成正比关系。使用化渣剂可以减少sif4排放量为:(168.86-89.21)/168.86=47.17%。总之可以看出,本发明具体实施例2可以使吨钢使用成本降低3.85rmb,sif4有毒气体产生量减少47.17%。实施例3(1)按比例称取定量氟硅酸钠和铝灰,放入料仓中混合,混合后各元素质量百分比如下:元素名称质量百分数na17.79%ca2.58%al15.66%f50.82%o11.34%si1.80%(2)将料仓中物料投入到电感应炉中,调节电流5-25a、感应温度1600℃、熔炼时间30min后倒入至钢制模具中;(3)待重熔物冷却后至室温后脱模倒出。对脱模后的产品使用鄂氏破碎机破碎;(4)筛分破碎后产品,获得粒径为5~70mm部分,装袋制得化渣剂产品;(5)化渣剂与现有80%萤石实验数据对比如下:炉号钢种石灰(kg)80%萤石(kg)化渣剂(kg)616040848sae1008cr8333170616040849sae1008cr8382380616040850sae1008cr8401330616040851sae1008cr8333140616040852sae1008cr8303100616040853sae1008cr8331290716040944sae1008cr807080716040945sae1008cr816050716040946sae1008cr821080716040947sae1008cr817070716040948sae1008cr825080本发明化渣剂与80%萤石在同样钢种及炉况下使用量对比:化渣剂平均每炉用量:72kg萤石平均每炉用量:240.17kg本发明的优点:(a)降低成本:80%萤石的市场价格约3000rmb/吨,化渣剂约3600rmb/吨,平均每炉成本降低约3rmb/kg*240.17kg-3.6rmb/kg*72kg=461.31rmb。每炉钢水重量约130吨,吨钢成本降低约3.55rmb;(b)sif4排放量减少:使用萤石每炉总氟加入量:240.17kg*38.97%=93.59kg使用化渣剂每炉总氟加入量:72kg*50.82%=36.59kg在炼钢生产中,sif4的产生量与投入物料氟总量成正比关系。使用化渣剂可以减少sif4排放量为:(93.59-36.59)/93.59=60.91%。总之可以看出,本发明具体实施例3可以使吨钢使用成本降低3.55rmb,sif4有毒气体产生量减少60.91%。实施例4(1)按比例称取定量氟硅酸钠和铝灰,放入料仓中混合,混合后各元素质量百分比如下:元素名称质量百分数na12.40%ca4.31%al29.12%f30.73%o18.40%si5.03%(2)将料仓中物料投入到电感应炉中,调节电流5-25a、感应温度1600℃、熔炼时间30min后倒入至钢制模具中;(3)待重熔物冷却后至室温后脱模倒出。对脱模后的产品使用鄂氏破碎机破碎;(4)筛分破碎后产品,获得粒径为5~70mm部分,装袋制得化渣剂产品;(5)本发明的化渣剂与现有80%萤石实验数据对比如下:炉号钢种石灰(kg)80%萤石(kg)化渣剂(kg)3-408520#80030002-912020#40030002-912120#48025002-912220#48020003-409020#56020003-409020#56001003-409120#64002002-912520#64002002-912620#56001503-409320#64001003-409520#80002503-409620#8000100本发明化渣剂与80%萤石在同样钢种及炉况下使用量对比:化渣剂平均每炉用量:157.14kg萤石平均每炉用量:250kg本发明的优点:(a)降低成本80%萤石的市场价格约3000rmb/吨,化渣剂约3600rmb/吨,平均每炉成本降低约3rmb/kg*250kg-3.6rmb/kg*157.14kg=184.30rmb。每炉钢水重量约120吨,吨钢成本降低约1.53rmb;(b)sif4排放量减少使用萤石每炉总氟加入量:250kg*38.97%=97.43kg使用化渣剂每炉总氟加入量:157.14kg*30.73%=48.29kg在炼钢生产中,sif4的产生量与投入物料氟总量成正比关系。使用化渣剂可以减少sif4排放量为:(97.43-48.29)/97.43=50.43%。总之可以看出,本发明具体实施例4可以使吨钢使用成本降低1.53rmb,sif4有毒气体产生量减少48.29%。如图2所示,本发明化渣剂dta曲线,测试样品重量23.077mg,采用perkinelmer公司同步热分析仪sta8000,从30摄氏度按每分钟升温25摄氏度逐步升温至1300摄氏度,观察试样热失重状况。图中横坐标是温度,纵坐标是热重,从上到下曲线分别为曲线1,2,3;线1为重量百分比曲线,曲线2为重量倒数曲线;曲线3为热流曲线。从曲线2可以看出,本发明化渣剂产品从520摄氏度开始熔化,在720摄氏度大部分已熔化为液态,低熔点可以降低炼钢精炼工艺对温度的要求,在相同温度下化渣速度比萤石快。本发明化渣剂产品是由磷化工副产品氟硅酸钠(na2sif6)以及铝熔炼行业副产品铝灰按一定比例配置而成,可在钢厂无需改变现有工艺条件下替代萤石,主要注意点是添加量需根据现场渣状做调节。本发明由此得出结论:与现有钢铁企业萤石化渣相比,用量只有80%萤石的40~70%左右,生产成本可以控制在比萤石更低;化渣剂的使用方法与现行萤石使用方法类似,不需要做工艺变动;利用其它行业副产品,节约宝贵的萤石自然资源,给子孙后代留下财富;萤石在工业生产中,由于消耗量大,产生的sif4有毒气体严重,使用本产品有毒气体量会有所减少,有利于环保。需要说明的是,按照本发明上述各实施例,本领域技术人员是完全可以实现本发明独立权利要求及从属权利的全部范围的,实现过程及方法同上述各实施例;且本发明未详细阐述部分属于本领域公知技术。以上所述,仅为本发明部分具体实施方式,但本发明的保护范围并不局限于此,任何熟悉本领域的人员在本发明揭露的技术范围内,可轻易想到的变化或替换,都应涵盖在本发明的保护范围之内。当前第1页12