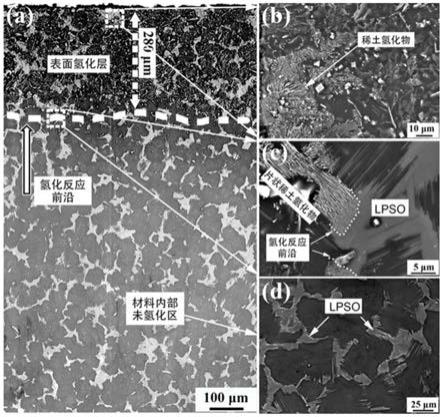
casting alloy,a.f.s.trans.,1976,84,151.)和美国标准(astm standards b80-76,standard specification for magnesium-alloy sand castings,1976)提出了ze63a合金及氢化处理工艺。根据astm standards b80-76,其合金成分为:mg-(5.5~6.0)zn-(2.1~3.0)re-(0.40~1.0)zr(质量百分含量),氢化热处理工艺为:温度482℃,氢气压力1atm。北京航空材料研究院的赵志远等(赵志远,氢化处理zm8高强度铸造镁合金,航空材料,1979,1,1-7)在astm standards b80-76的基础上,用成本较低的含铈45~60%(质量百分数)的混合稀土替代纯nd或ce,发展出了具有我国特色的zm8高强镁合金。无论是ze63a还是zm8,合金中zn的含量约为6%(质量百分含量),稀土(nd,ce,la)等的含量为3%(质量百分含量)。上海交通大学的吴国华等(吴国华,mg-zn-re系镁合金氢化热处理方法,zl201410018239.1)在mg-(4~6)zn-1re(质量百分含量)合金铸件的热处理中引入氢气,进行了氢化处理并取得了一定的效果。以上这些文献和专利,都是为了解决锌含量较高的mg-zn-zr合金比如zk60等铸造性能差、凝固过程中产生热裂纹的问题。在zk60、zk40等合金的基础上添加1~3%左右的稀土元素来克服热裂缺陷,使合金获得优异的铸造性能,从而用于制造航空工业上的大尺度薄壁复杂铸件。但是,在zk60、zk40合金中添加稀土后,稀土与zn元素结合生成w,i(准晶)等物相,这些物相在高温(480~515℃)下非常稳定,在随后的固溶处理中不能溶于镁基体,造成mg-zn-re系合金不能通过人工时效来获得高强度。mg-zn-re系合金的氢化处理,其目的在于高温下稀土与氢结合,从而释放出w,i(准晶)相中的zn元素,在随后的141℃的人工时效处理中生成mg
2
zn等强化相,从而达到通过人工时效来提高mg-zn-re系合金强度的目的。近年来,随着we43和we54等合金的发展,在新版的美国标准(astm standards b80-15,standard specification for magnesium-alloy sand castings,2015)中已经删除了ze63a合金及其热处理方法。
[0006]
最近,r.lapovok等(r.lapovok,et al.,materials science&engineering a 719(2018)171
–
177)报道了mg
–
re(gd,y)
–
zn
–
zr合金的氢化处理。通过氢化处理,合金样品中的lpso相全部转变成为了颗粒状的稀土氢化物相,由于样品中含有的稀土元素全部被氢化,高密度的稀土氢化物取代了lpso相。合金中稀土元素与氢完全反应,稀土被消耗后合金不具备时效硬化效应;氢化处理后,合金强度显著降低、而延伸率增加。这一方法的缺点在于:长时间的氢化处理使氢渗透了试样的整个横截面,合金内部的增强相lpso全部消失,从而使合金丧失了耐热、高强的优异力学性能。本发明聚焦于合金的表面氢化处理,将表面氢化层的厚度控制在0.3mm左右,合金内部的lpso相并没有被氢化,从而保持了材料高强、耐热的性能。同时,通过优化氢化处理工艺,在合金表面层生成了新颖的密集片状结构聚集体,提高了合金的耐蚀性。
技术实现要素:[0007]
本发明所述方法主要针对五元mg
–
re(gd,y)
–
zn
–
zr合金,合金中含有mg、gd、y、zn和zr五种合金元素,经过热处理后lpso相是合金中主要的强化相之一。然而,mg
–
re(gd,y,nd)
–
zn
–
zr系合金中lpso相与α-mg基体构成腐蚀原电池,促进了电偶腐蚀,造成合金耐蚀性不良。针对合金中的lpso结构与α-mg基体构成腐蚀原电池,导致电偶腐蚀的问题,本发明提出在合金的热处理过程中通入氢气,将合金表面层中的lpso相转变为稀土氢化物相,即将合金表面层中的强阴极相(lpso相)转变为弱阴极相(稀土氢化物相),减缓了合金的电偶腐
蚀,达到了改善合金耐蚀性的目的。
[0008]
本发明采用的技术方案为,一种改善lpso增强镁合金耐蚀性的氢化热处理方法,分为以下步骤:
[0009]
s1实验材料的制备。
[0010]
s1.1准备熔炼合金的原材料:高纯镁、高纯锌、镁-钆中间合金、镁-钇中间合金以及镁-锆中间合金。
[0011]
s1.2合金的熔炼与浇铸。将合适数量(根据合金成分和要得到的铸锭的重量,用一个简单的计算公式,再加上一点经验,就可以确定每一种原材料的投料量,此为本领域的公知常识:如要得到约1公斤的铸锭,需要准备0.4公斤的25%镁-钆中间合金,0.1公斤的25%镁-钇中间合金,40克高纯锌和45克25%镁-锆中间合金,其余为高纯镁;具体参见l.wu,et al.,journal of alloys and compounds 626(2015)194
–
202)的99.99%纯镁、99.99%纯锌,25%mg-gd中间合金,25%镁-y中间合金以及mg-zr中间合金置于中碳钢坩埚中、熔剂保护下熔炼,随后浇铸得到合金铸锭。所述合金的化学成分(质量百分含量)范围为:
[0012]
gd的含量:8~15%;
[0013]
y的含量:2~5%;
[0014]
zn的含量:2~4%;
[0015]
zr的含量:0.4~1.0%;
[0016]
其余为mg和少量杂质元素。
[0017]
s2 mg
–
gd
–
y
–
zn
–
zr合金铸锭的固溶热处理
[0018]
将s1制备出的合金铸锭置于电阻炉中在500℃下保温10小时,于约70℃的热水中淬火,使铸态合金中的共晶第二相mg
3
(gd,y)转变为lpso相。
[0019]
s3氢化热处理,具体包括以下步骤:
[0020]
s3.1将s2经过固溶热处理后的合金样品置于氢气炉中进行氢化热处理,温度440~515℃,氢压0.3~10兆帕,时间0.5~10小时;
[0021]
s3.2氢化热处理结束后将合金样品从氢气炉中取出强制空冷或淬火。
[0022]
优选的,s3中合金表面层的氢化热处理温度为482℃,处理时间为4小时,氢气压力为1兆帕。
[0023]
本发明还提供一种采用上述方法制备出的镁合金,所述镁合金的化学成分质量百分含量范围为:
[0024]
gd的含量:8~15%;
[0025]
y的含量:2~5%;
[0026]
zn的含量:2~4%;
[0027]
zr的含量:0.4~1.0%;
[0028]
其余为mg和少量杂质元素。
[0029]
优选的,所述镁合金的化学成分质量百分含量为:
[0030]
gd 10.27%,
[0031]
y 2.71%,
[0032]
zn 2.09%,
[0033]
zr 0.76%,
alloy,corrosion science 142(2018):238-248.)。需要说明的是,本领域技术人员能够根据合金的组分来配比原料,并适当计算合金元素在熔炼中的损失来合理确定投料量;能够利用常规的熔剂保护熔炼方法制备出成分基本准确的合金铸锭。
[0047]
本发明涉及到的固溶热处理方法,已经得到广泛报道(l.wu,et al.,effect of selective oxidation on corrosion behavior of mg-gd-y-zn-zr alloy,corrosion science 142(2018):238-248.),为了避免固溶样品在淬火时出现裂纹,一般采用约70℃的热水作为淬火介质。本发明的关键要点在于固溶后样品的氢化热处理:
[0048]
1)将固溶处理后的的合金样品置于氢气炉中进行氢化热处理,温度440~515℃,氢压0.2~10兆帕,时间0.5~10小时。
[0049]
2)氢化处理结束后将样品从炉中取出强制空冷或淬火。
[0050]
下面结合附图和实施例对本发明进一步说明。
[0051]
实施例1
[0052]
mg
–
10.27gd
–
2.71y
–
2.09zn
–
0.76zr合金经过固溶处理后,进行如下工艺的氢化处理:
[0053]
1)合金表面层的氢化热处理温度为482℃,
[0054]
2)合金表面层的氢化热处理保温时间为10小时,
[0055]
3)合金表面层的氢化热处理氢气压力为0.2兆帕。
[0056]
实施例2
[0057]
mg
–
10.27gd
–
2.71y
–
2.09zn
–
0.76zr合金经过固溶处理后,进行如下工艺的氢化处理:
[0058]
1)合金表面层的氢化热处理温度为482℃,
[0059]
2)合金表面层的氢化热处理保温时间为4小时,
[0060]
3)合金表面层的氢化热处理氢气压力为1.0兆帕。
[0061]
在实施例1中,在482℃、0.2兆帕氢气压力的条件下,合金经过10小时的氢化热处理后,氢化层的微观组织如图1所示。在图1中,合金表面层中块状lpso相完全消失,颗粒状的第二相广泛分布于合金基体。这说明,经过实施例1的氢化热处理,在合金的表面层,稀土氢化物取代了lpso相,成为了合金表面层中主要的第二相。
[0062]
在实施例2中,在482℃、1.0兆帕氢气压力的条件下,合金经过4小时的氢化热处理后,氢化层的微观组织如图2所示。在合金的表面氢化层中,大量的密集片状结构聚集体取代了块状的lpso相(图2b),与图1中颗粒状的第二相有显著的不同。经过4小时的氢化热处理,合金表面氢化层的厚度大约为280μm(图2a)。在图2c中,观察到了在氢化反应的前沿lpso相转化为片状密集结构的界面;在靠近合金表层的方向lpso相已经转变成为了片状的稀土氢化物,而靠近合金芯部的方向,lpso的形态依然保持为块状,并未可见明显的变化。在材料的内部,块状的lpso相沿晶界分布(图2d),增强相lpso相的形态和分布并没有受到氢化热处理的影响。
[0063]
图3示出了实施例2中氢化处理样品的表面x射线衍射图。结合图2和图3可知,氢化处理的样品表面,主要的第二相为gd
0.5
y
0.5
h
1.96
。
[0064]
镁合金在3.5%氯化钠水溶液中浸泡析氢实验是现在常用的一个评价合金耐蚀性的方法,特点是设备简便、灵敏度很高,其原理是镁合金在腐蚀过程中与水反应放出氢气,
通过测量析出氢的体积就可以计算出合金在3.5%氯化钠溶液中的腐蚀失重。合金铸态、固溶态、实施例1、实施例2的析氢曲线如图4所示。从图4中可知,实施例2的样品具有最低的析氢速率,可以推断当合金表面生成密集片状结构聚集体时,合金具有最好的耐蚀性。实施例1的样品表面密集分布着稀土氢化物颗粒,其氢释放速率高于实施例2,反映了其耐蚀性要比实施例2稍差。实施例2和铸态合金都具有较低的氢释放速率,而固溶态样品的氢释放速率最高,这说明固溶处理后合金中lpso相的生成对合金的耐蚀性有不利的影响。
[0065]
综上所述,与实施例1比较,在实施例2中氢压提高至1.0兆帕,热处理时间缩短至4小时。在实施例1中,氢化热处理后,合金表面氢化层中微观组织的主要特征为颗粒状的稀土氢化广泛分布,块状lpso相消失;而在实施例2中,新颖的密集片状结构聚集体取代了块状lpso相。在3.5%氯化钠溶液中浸泡200小时后,合金铸态、固溶态、实施例1和实施例2样品的腐蚀速率见表1所示。
[0066]
表1合金铸态、固溶态、实施例1和实施例2的腐蚀速率
[0067][0068]
从表1中可知,经过实施例2的氢化热处理,合金表面层的耐蚀性有了明显的改善。在480℃下,氢与lpso相中的稀土元素gd、y结合,使电化学特征表现为强阴极的lpso结构由于稀土元素的流失而分解,弱阴极的稀土氢化物生成。将经过实施例2处理过程的横截面样品,表面抛光、脱脂后于3.5%的氯化钠容易中浸泡74小时,取出样品、清洗后于热气流中吹干,再稍微磨去表面腐蚀产物层。横截面样品腐蚀后的低倍形貌如图5所示。在图5中,样品的表面层较为完整,而样品的芯部在3.5%的氯化钠溶液中腐蚀严重,经过74小时的浸泡,形成了较深的蚀坑,这也说明了氢化层的耐蚀性要高于样品的芯部。通过合适的氢化热处理工艺,使合金表面氢化层中生成一种新颖的密集片状结构聚集体,导致了合金表面层伏打电位的降低,可能是氢致合金耐蚀性改善的电化学机制。
[0069]
本发明所述材料是mg
–
re(gd,y)
–
zn
–
zr系合金,其中zn的含量(2%,质量百分含量)远低于mg-zn-re系合金,是最近20年发展起来的新型高强耐热镁合金,其主要特征就是在熔体的凝固和随后的固溶处理中生成了lpso相,其是主要的强化相之一。但是,lpso相与镁基体构成腐蚀原电池,造成合金的耐蚀性较差。本发明的目的在于,通过氢致表面层中lpso相分解,将lpso(强阴极相)转变为稀土氢化物(弱阴极相),从而达到提高合金表面层耐蚀性的目的。本发明通过氢化处理,只是改变了合金表面层的微观组织特征,不影响材料内部强化相lpso的数量和分布,不涉及对材料力学性能的影响。
[0070]
需要特别指出的是,经过优化的氢化处理工艺,本发明报道了氢化处理的样品中生成了一种新颖的密集片状结构聚集体(如图2所示),这一稀土氢化物的新形态与r.lapovok等报道的氢化物的颗粒状形态(如图1所示)完全不同。在3.5%氯化钠溶液中的浸泡实验表明,当合金表面氢化层中氢化物为新颖的密集片状结构聚集体形态时,与生成颗粒状氢化物的氢化处理样品相比,具有更好的耐蚀性。
[0071]
显然,以上实施例的说明只是用于帮助理解本发明的原理及其核心思想。应当指出,对于所述技术领域的普通技术人员来说,在不脱离本发明原理的前提下,还可以对本发明进行若干改进和修饰,这些改进和修饰也落入本发明专利权利要求的保护范围内。