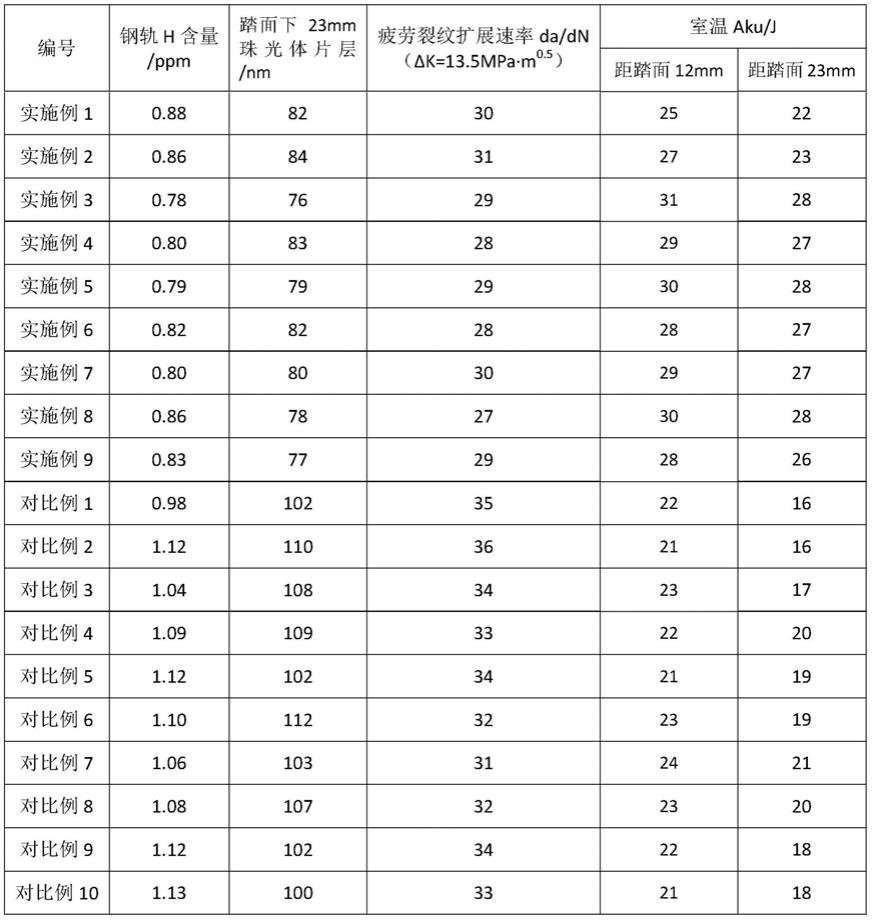
0.8℃/s的冷却速率将钢坯冷却至表面温度为50-150℃;
[0011]
在线热处理包括利用终轧余热对钢轨轨头和轨腰进行压缩空气冷却,冷却速率控制在2.6-4.2℃/s;钢轨轨头冷却初始温度控制在830-880℃,钢轨轨头冷却温度低于500℃时钢轨空冷至室温。
[0012]
优选地,rh真空处理或vd真空处理后,以钢液的总重量为基准,所述钢液的化学成分包括0.3-1.3重量%的c、0.25-0.85重量%的mn、0.3-0.85重量%的si、0.025-0.1重量%的cr、0.04-0.09重量%的ti、≤0.02重量%的p、≤0.02重量%的s、余量的fe和不可避免的杂质。
[0013]
更优选地,rh真空处理或vd真空处理后,以钢液的总重量为基准,所述钢液的化学成分包括0.3-1.3重量%的c、0.25-0.45重量%的mn、0.3-0.85重量%的si、0.025-0.1重量%的cr、0.04-0.09重量%的ti、≤0.01重量%的p、≤0.005重量%的s、余量的fe和不可避免的杂质。
[0014]
优选地,在步骤(1)中,对表面温度为830-870℃的钢坯进行第一阶段冷却,并以0.6-0.8℃/s的冷却速率将钢坯冷却至表面温度为420-470℃。
[0015]
优选地,在步骤(2)中,对表面温度为420-470℃的钢坯进行第二阶段冷却,并以0.4-0.6℃/s的冷却速率将钢坯冷却至表面温度为180-220℃。
[0016]
优选地,在步骤(3)中,对表面温度为180-220℃的钢坯进行第三阶段冷却,并以0.3-0.5℃/s的冷却速率将钢坯冷却至表面温度为80-100℃。
[0017]
优选地,钢坯入加热炉加热的过程包括将钢坯加热至1200-1280℃,控制加热炉中加热的总时间为3-3.5h。
[0018]
优选地,钢坯入加热炉加热后,出炉将钢坯在线轧制成60-75kg/m的钢轨。
[0019]
优选地,所述后处理包括矫直、探伤和加工。
[0020]
本发明另一方面提供了一种前文所述的方法制备的具有抗延迟断裂性能的钢轨,以所述钢轨的总重量为基准,所述钢轨的化学成分包括0.3-1.3重量%的c、0.25-0.85重量%的mn、0.3-0.85重量%的si、0.025-0.1重量%的cr、0.04-0.09重量%的ti、≤0.02重量%的p、≤0.02重量%的s、余量的fe和不可避免的杂质。
[0021]
更优选地,以所述钢轨的总重量为基准,所述钢轨的化学成分包括0.3-1.3重量%的c、0.25-0.45重量%的mn、0.3-0.85重量%的si、0.025-0.1重量%的cr、0.04-0.09重量%的ti、≤0.01重量%的p、≤0.005重量%的s、余量的fe和不可避免的杂质。
[0022]
本发明旨在通过对钢轨生产流程中铸坯连续缓慢冷却技术的实施,使钢坯中h含量溶解度得到有效降低,最大化降低钢坯氢含量、较大程度降低钢坯内部残余应力,同时结合合理成分配比及高精度轧制技术应用,施加钢轨在线热处理工艺,显著提升热轧钢轨典型部位的抗延迟断裂性能。
[0023]
与现有技术相比,本发明具有以下有益效果:
[0024]
1)本发明所述的具有抗延迟断裂性能的钢轨经铸坯连续冷却技术后,其氢含量得到一定程度的降低;
[0025]
2)本发明所述的具有抗延迟断裂性能的钢轨轨头踏面下23mm处珠光体片层间距处于70-85nm范围;
[0026]
3)本发明所述的具有抗延迟断裂性能的钢轨在同等条件下具有更优的裂纹扩展
速率da/dn性能;
[0027]
4)本发明所述的具有抗延迟断裂性能的钢轨在钢轨轨头以下12mm、23mm处的常温冲击韧性均得到显著提升,有效改善钢轨抗延迟断裂性能,广泛应用于高速重载线路。
具体实施方式
[0028]
以下对本发明的具体实施方式进行详细说明。应当理解的是,此处所描述的具体实施方式仅用于说明和解释本发明,并不用于限制本发明。
[0029]
在本文中所披露的范围的端点和任何值都不限于该精确的范围或值,这些范围或值应当理解为包含接近这些范围或值的值。对于数值范围来说,各个范围的端点值之间、各个范围的端点值和单独的点值之间,以及单独的点值之间可以彼此组合而得到一个或多个新的数值范围,这些数值范围应被视为在本文中具体公开。
[0030]
本发明一方面提供了一种具有抗延迟断裂性能的钢轨的制备方法,该方法包括炉料经过转炉冶炼或电炉冶炼成钢液、无铝脱氧、lf精炼、rh真空处理或vd真空处理、钢液连铸成钢坯、钢坯连续冷却、钢坯入加热炉加热、钢坯在线轧制成钢轨、在线热处理和后处理;
[0031]
其中,钢坯连续冷却过程包括以下步骤:
[0032]
(1)第一阶段冷却:对表面温度为830-900℃的钢坯进行第一阶段冷却,并以0.3-1.3℃/s的冷却速率将钢坯冷却至表面温度为350-500℃;
[0033]
(2)第二阶段冷却:对表面温度为350-500℃的钢坯进行第二阶段冷却,并以0.2-1℃/s的冷却速率将钢坯冷却至表面温度为150-250℃;
[0034]
(3)第三阶段冷却:对表面温度为150-250℃的钢坯进行第三阶段冷却,并以0.1-0.8℃/s的冷却速率将钢坯冷却至表面温度为50-150℃;
[0035]
在线热处理包括利用终轧余热对钢轨轨头和轨腰进行压缩空气冷却,冷却速率控制在2.6-4.2℃/s;钢轨轨头冷却初始温度控制在830-880℃,钢轨轨头冷却温度低于500℃时钢轨空冷至室温。
[0036]
本发明所述方法通过工艺控制钢轨晶粒度以及降低钢轨h含量,有效降低钢轨氢致裂纹缺陷,综合提升钢轨抗延迟裂纹性能。在具体实施方式中,本发明通过对成分控制、在线连铸钢坯、多次缓慢连续冷却一系列手段,能够显著降低钢轨内部的h含量,降低钢坯残余应力,降低钢坯内部应力集中。采用本发明所述的方法制备的钢轨在具备强韧化的同时,抗延迟断裂性能显著增强。
[0037]
在本发明所述的方法中,如无特别说明,各个操作所使用的设备均可以为本领域常规使用的设备。
[0038]
在本发明所述的方法中,为了得到目标钢轨,炉料经过转炉或电炉冶炼后得到含有目标钢轨所含化学成分的钢液,然后经过无铝脱氧、lf精炼后尽可能降低钢中s含量,再经过rh真空处理或vd真空处理将钢水成分微调至目标范围内。
[0039]
在本发明所述方法中,rh真空处理或vd真空处理后,以钢液的总重量为基准,所述钢液的化学成分包括0.3-1.3重量%的c、0.25-0.85重量%的mn、0.3-0.85重量%的si、0.025-0.1重量%的cr、0.04-0.09重量%的ti、≤0.02重量%的p、≤0.02重量%的s、余量的fe和不可避免的杂质。
[0040]
在优选实施方式中,rh真空处理或vd真空处理后,以钢液的总重量为基准,所述钢
液的化学成分包括0.3-1.3重量%的c、0.25-0.45重量%的mn、0.3-0.85重量%的si、0.025-0.1重量%的cr、0.04-0.09重量%的ti、≤0.01重量%的p、≤0.005重量%的s、余量的fe和不可避免的杂质。
[0041]
为了使钢轨轨头平均珠光体片层间距得到显著减小,钢轨氢含量得到一定程度降低,裂纹扩展速率和轨头冲击韧性得到优化,钢轨抗延迟断裂性能得到明显提升,需要合理控制钢液中各化学元素的含量范围,以下将详述本发明控制主要元素含量范围的理由。
[0042]
c是珠光体钢轨提高强度、硬度以及促进珠光体转变最重要的元素。在本发明条件下,当c含量<0.3%时,钢轨经热处理后强度、硬度较低,难以满足钢轨的磨耗需求;当c含量>1.3%时,经热处理后钢轨的强硬度过高;同时,还将析出晶界先共析渗碳体,恶化钢轨的韧塑性。因此,c含量限定在0.3%-1.3%。
[0043]
si作为钢中的固溶强化元素存在于铁素体和奥氏体中提高组织的强度;同时,可抑制先共析渗碳体析出,从而提高钢轨的韧塑性,si含量在一定范围内能够改善钢的抗延迟断裂性能。在本发明条件下,当si含量<0.3%时,固溶量偏低导致强化效果不明显;当si含量>0.85%时,将损失钢轨的韧塑性特别是抵抗裂纹扩展性能。因此,si含量限定在0.3%-0.85%。
[0044]
mn与s易结合成mns,氢诱发裂纹一般以mns为起点发生延迟断裂,会增加高强度钢的延迟断裂敏感性,而对淬透性和强度的影响不大。因此将mn含量控制在0.25%-0.45%。
[0045]
p和s是有害元素,它们能使钢的塑性和韧性下降,因此含量越少越好。
[0046]
cr是中强碳化物形成元素,钢中的cr一部分置换铁形成合金渗碳体,提高其稳定性;一部分溶入铁素体中,产生固溶强化,提高铁素体的强度和硬度。由于cr在奥氏体中的扩散速度比较小,加之阻碍碳的扩散,因而可提高奥氏体的稳定性,使c曲线右移,降低临界冷却速度,提高淬透性。当cr元素含量较小时,钢轨淬透性较弱,部分区域晶粒粗大;当cr含量超过一定量后淬火钢中残留奥氏体数量大幅度增加。因此,cr元素含量控制在0.025-0.1%。
[0047]
ti可以细化晶粒,降低晶界元素偏析,与c、n形成亚微米ti化合物在回火时析出,回火时析出的碳氮化钒是有效的氢陷阱。穿晶分布的氢陷阱捕获吸收的氢,使其不能扩散,降低晶界氢浓度,防止晶界开裂。因此,添加ti元素可以抑制钢轨的延迟断裂倾向,提高钢轨抗延迟断裂能力。当ti含量较低时,较低偏析能力不足,当ti含量较高时易与n、o有很大的亲和力而极易成形tin和tio2,钢锭在较低温度时,就形成了较多的非金属夹杂和皮下多孔等缺陷。因此,ti元素含量控制在0.04-0.09%。
[0048]
将满足化学成分要求的钢液连铸成钢坯(优选为410mm
×
320mm钢坯)后,对有余热的连铸坯实施多次连续冷却。
[0049]
在具体实施方式中,在步骤(1)中,可以对表面温度为830℃、840℃、850℃、860℃、870℃、880℃、890℃或900℃的钢坯进行第一阶段冷却;并可以以0.3℃/s、0.4℃/s、0.5℃/s、0.6℃/s、0.7℃/s、0.8℃/s、0.9℃/s、1℃/s、1.1℃/s、1.2℃/s或1.3℃/s的冷却速率将钢坯冷却至表面温度为350℃、360℃、370℃、380℃、390℃、400℃、410℃、420℃、430℃、440℃、450℃、460℃、470℃、480℃、490℃或500℃。
[0050]
在优选实施方式中,在步骤(1)中,对表面温度为830-870℃的钢坯进行第一阶段冷却,并以0.6-0.8℃/s的冷却速率将钢坯冷却至表面温度为420-470℃。
[0051]
在具体实施方式中,在步骤(2)中,可以对表面温度为350℃、360℃、370℃、380℃、390℃、400℃、410℃、420℃、430℃、440℃、450℃、460℃、470℃、480℃、490℃或500℃的钢坯进行第二阶段冷却,并可以以0.2℃、0.3℃、0.4℃、0.5℃、0.6℃、0.7℃、0.8℃、0.9℃或1℃/s的冷却速率将钢坯冷却至表面温度为150℃、160℃、170℃、180℃、190℃、200℃、210℃、220℃、230℃、240℃或250℃。
[0052]
在优选实施方式中,在步骤(2)中,对表面温度为420-470℃的钢坯进行第二阶段冷却,并以0.4-0.6℃/s的冷却速率将钢坯冷却至表面温度为180-220℃。
[0053]
在具体实施方式中,在步骤(3)中,可以对表面温度为150℃、160℃、170℃、180℃、190℃、200℃、210℃、220℃、230℃、240℃或250℃的钢坯进行第三阶段冷却,并可以以0.1℃/s、0.2℃/s、0.3℃/s、0.4℃/s、0.5℃/s、0.6℃/s、0.7℃/s或0.8℃/s的冷却速率将钢坯冷却至表面温度为50℃、60℃、70℃、80℃、90℃、100℃、110℃、120℃、130℃、140℃或150℃。
[0054]
在优选实施方式中,在步骤(3)中,对表面温度为180-220℃的钢坯进行第三阶段冷却,并以0.3-0.5℃/s的冷却速率将钢坯冷却至表面温度为80-100℃。
[0055]
在本发明所述的方法中,采用多次缓慢连续冷却方式进行处理。对有余热的连铸钢坯在线进行第一阶段缓慢冷却时,如果冷却速率过低,对设备的要求及其苛刻,生产成本将急剧升高,如果冷却速率过高,钢坯内部h原子将得不到充分扩散,同时也易造成钢坯表面产生热裂纹,综上,将进行第一阶段冷却钢坯的表面温度控制在830-900℃范围,冷却速率控制在0.3-1.3℃/s,缓慢冷却至表面温度为350-500℃;第二阶段冷却、第三阶段冷却工艺及控制原理与第一阶段冷却过程相似,第二阶段缓慢冷却,将钢坯表面温度控制在350-500℃,冷却速率控制在0.2-1℃/s,缓慢冷却至150-250℃;第三阶段缓慢冷却,将钢坯表面温度控制在150-250℃,冷却速率控制在0.1-0.8℃/s,缓慢冷却至50-150℃。本发明通过精确控制缓慢冷却工艺的各个条件,显著降低了钢坯h含量,多道次缓慢冷却促使钢坯心部游离态氢原子实现氢分子的转变,加快了钢坯心部聚集态h的弥散化。
[0056]
本发明将多次缓慢连续冷却后的钢坯倒入加热炉(优选为步进式加热炉),待完全奥氏体化后在线轧制成钢轨,然后对热轧钢轨采用在线热处理,钢轨空冷至室温后经后处理获得成品钢轨。
[0057]
在本发明所述的方法中,为了提高钢轨抗延迟断裂性能,必须合理控制钢坯在加热炉中的加热过程。在优选实施方式中,所述加热炉为步进式加热炉。
[0058]
钢坯入加热炉加热的过程包括将钢坯加热至1200-1280℃,控制加热炉中加热的总时间为3-3.5h。
[0059]
在具体实施方式中,钢坯入加热炉后,可以将钢坯加热至1200℃、1210℃、1220℃、1230℃、1240℃、1250℃、1260℃、1270℃或1280℃。
[0060]
在具体实施方式中,钢坯在加热炉中加热的总时间可以为3h、3.1h、3.2h、3.3h、3.4h或3.5h。
[0061]
在本发明所述的方法中,钢坯入加热炉加热后,出炉将钢坯在线轧制成60-75kg/m的钢轨。在具体实施方式中,可以将钢坯在线轧制成60kg/m、62kg/m、64kg/m、66kg/m、68kg/m、70kg/m、72kg/m、74kg/m或75kg/m的钢轨。
[0062]
钢轨轧制后,可以利用终轧余热对钢轨轨头和轨腰进行热处理,即利用终轧余热
对钢轨轨头和轨腰进行加速冷却。
[0063]
在具体实施方式中,对钢轨轨头和轨腰进行加速冷却的冷却速率可以控制在2.6℃/s、2.8℃/s、3℃/s、3.2℃/s、3.4℃/s、3.6℃/s、3.8℃/s、4℃/s或4.2℃/s。
[0064]
在具体实施方式中,钢轨轨头冷却初始温度可以控制在830℃、840℃、850℃、860℃、870℃或880℃。
[0065]
在优选实施方式中,当钢轨轨头冷却温度低于500℃时钢轨空冷至室温。更为优选地,当钢轨轨头冷却温度低于490℃时钢轨空冷至室温。
[0066]
为获得较细的珠光体组织,相变需要在更大的过冷度下完成,当冷却速率低于2.6℃/s时,珠光体相变前及相变过程中的过冷度较低,珠光体组织较为粗大,无法实现本发明所述目的,如果冷却速率高于4.2℃/s,由于冷却速率过大,钢轨表层将生成贝氏体、马氏体等异常组织。由此,加速冷却的冷却速率控制范围为2.6-4.2℃/s;并且,当轨头表层温度降至500℃以下时,珠光体相变已全部完成,热处理过程结束。
[0067]
在本发明所述的方法中,所述后处理包括本领域的常规操作。在具体实施方式中,所述后处理可以包括矫直、探伤和加工。
[0068]
本发明另一方面提供了一种前文所述的方法制备的具有抗延迟断裂性能的钢轨,以所述钢轨的总重量为基准,所述钢轨的化学成分包括0.3-1.3重量%的c、0.25-0.85重量%的mn、0.3-0.85重量%的si、0.025-0.1重量%的cr、0.04-0.09重量%的ti、≤0.02重量%的p、≤0.02重量%的s、余量的fe和不可避免的杂质。
[0069]
在优选实施方式中,以所述钢轨的总重量为基准,所述钢轨的化学成分包括0.3-1.3重量%的c、0.25-0.45重量%的mn、0.3-0.85重量%的si、0.025-0.1重量%的cr、0.04-0.09重量%的ti、≤0.01重量%的p、≤0.005重量%的s、余量的fe和不可避免的杂质。
[0070]
采用本发明所述的方法制备的钢轨在具备强韧化的同时,抗延迟断裂性能显著增强。
[0071]
以下将通过实施例对本发明进行详细描述,但本发明的保护范围并不仅限于此。
[0072]
实施例1
[0073]
本发明用于说明具有抗延迟断裂性能的钢轨的制备过程。
[0074]
炉料经过转炉冶炼或电炉冶炼成钢液、无铝脱氧、lf精炼、rh真空处理或vd真空处理、钢液连铸成钢坯、钢坯连续冷却、钢坯入加热炉加热、钢坯在线轧制成钢轨、在线热处理、矫直、探伤和加工;
[0075]
其中,钢坯连续冷却过程包括以下步骤:
[0076]
(1)第一阶段冷却:对表面温度为870℃的钢坯进行第一阶段冷却,并以0.6℃/s的冷却速率将钢坯冷却至表面温度为470℃;
[0077]
(2)第二阶段冷却:对表面温度为470℃的钢坯进行第二阶段冷却,并以0.4℃/s的冷却速率将钢坯冷却至表面温度为220℃;
[0078]
(3)第三阶段冷却:对表面温度为220℃的钢坯进行第三阶段冷却,并以0.3℃/s的冷却速率将钢坯冷却至表面温度为100℃;
[0079]
连续冷却结束后,钢坯入加热炉加热至1200℃,并控制加热总时间为3.2h,出炉后在线轧制成60kg/m的钢轨;
[0080]
在线热处理包括利用终轧余热对钢轨轨头和轨腰进行压缩空气冷却,冷却速率控
制在2.8℃/s;钢轨轨头冷却初始温度控制在830℃,钢轨轨头冷却温度低于500℃时钢轨空冷至室温;
[0081]
rh真空处理或vd真空处理后,所述钢液的化学成分包括0.3-1.3重量%的c、0.25-0.45重量%的mn、0.3-0.85重量%的si、0.025-0.1重量%的cr、0.04-0.09重量%的ti、0.007重量%的p、0.003重量%的s、余量的fe和不可避免的杂质。
[0082]
实施例2
[0083]
本发明用于说明具有抗延迟断裂性能的钢轨的制备过程。
[0084]
炉料经过转炉冶炼或电炉冶炼成钢液、无铝脱氧、lf精炼、rh真空处理或vd真空处理、钢液连铸成钢坯、钢坯连续冷却、钢坯入加热炉加热、钢坯在线轧制成钢轨、在线热处理、矫直、探伤和加工;
[0085]
其中,钢坯连续冷却过程包括以下步骤:
[0086]
(1)第一阶段冷却:对表面温度为850℃的钢坯进行第一阶段冷却,并以0.7℃/s的冷却速率将钢坯冷却至表面温度为450℃;
[0087]
(2)第二阶段冷却:对表面温度为450℃的钢坯进行第二阶段冷却,并以0.5℃/s的冷却速率将钢坯冷却至表面温度为200℃;
[0088]
(3)第三阶段冷却:对表面温度为200℃的钢坯进行第三阶段冷却,并以0.4℃/s的冷却速率将钢坯冷却至表面温度为90℃;
[0089]
连续冷却结束后,钢坯入加热炉加热至1240℃,并控制加热总时间为3h,出炉后在线轧制成60kg/m的钢轨;
[0090]
在线热处理包括利用终轧余热对钢轨轨头和轨腰进行压缩空气冷却,冷却速率控制在3.6℃/s;钢轨轨头冷却初始温度控制在850℃,钢轨轨头冷却温度低于486℃时钢轨空冷至室温;
[0091]
rh真空处理或vd真空处理后,所述钢液的化学成分包括0.3-1.3重量%的c、0.25-0.45重量%的mn、0.3-0.85重量%的si、0.025-0.1重量%的cr、0.04-0.09重量%的ti、0.009重量%的p、0.004重量%的s、余量的fe和不可避免的杂质。
[0092]
实施例3
[0093]
本发明用于说明具有抗延迟断裂性能的钢轨的制备过程。
[0094]
炉料经过转炉冶炼或电炉冶炼成钢液、无铝脱氧、lf精炼、rh真空处理或vd真空处理、钢液连铸成钢坯、钢坯连续冷却、钢坯入加热炉加热、钢坯在线轧制成钢轨、在线热处理、矫直、探伤和加工;
[0095]
其中,钢坯连续冷却过程包括以下步骤:
[0096]
(1)第一阶段冷却:对表面温度为830℃的钢坯进行第一阶段冷却,并以0.8℃/s的冷却速率将钢坯冷却至表面温度为420℃;
[0097]
(2)第二阶段冷却:对表面温度为420℃的钢坯进行第二阶段冷却,并以0.6℃/s的冷却速率将钢坯冷却至表面温度为180℃;
[0098]
(3)第三阶段冷却:对表面温度为180℃的钢坯进行第三阶段冷却,并以0.5℃/s的冷却速率将钢坯冷却至表面温度为80℃;
[0099]
连续冷却结束后,钢坯入加热炉加热至1280℃,并控制加热总时间为3.5h,出炉后在线轧制成65kg/m的钢轨;
[0100]
在线热处理包括利用终轧余热对钢轨轨头和轨腰进行压缩空气冷却,冷却速率控制在4℃/s;钢轨轨头冷却初始温度控制在870℃,钢轨轨头冷却温度低于478℃时钢轨空冷至室温;
[0101]
rh真空处理或vd真空处理后,所述钢液的化学成分包括0.3-1.3重量%的c、0.25-0.45重量%的mn、0.3-0.85重量%的si、0.025-0.1重量%的cr、0.04-0.09重量%的ti、0.01重量%的p、0.005重量%的s、余量的fe和不可避免的杂质。
[0102]
实施例4
[0103]
本发明用于说明具有抗延迟断裂性能的钢轨的制备过程。
[0104]
炉料经过转炉冶炼或电炉冶炼成钢液、无铝脱氧、lf精炼、rh真空处理或vd真空处理、钢液连铸成钢坯、钢坯连续冷却、钢坯入加热炉加热、钢坯在线轧制成钢轨、在线热处理、矫直、探伤和加工;
[0105]
其中,钢坯连续冷却过程包括以下步骤:
[0106]
(1)第一阶段冷却:对表面温度为930℃的钢坯进行第一阶段冷却,并以0.3℃/s的冷却速率将钢坯冷却至表面温度为500℃;
[0107]
(2)第二阶段冷却:对表面温度为500℃的钢坯进行第二阶段冷却,并以0.2℃/s的冷却速率将钢坯冷却至表面温度为150℃;
[0108]
(3)第三阶段冷却:对表面温度为150℃的钢坯进行第三阶段冷却,并以0.8℃/s的冷却速率将钢坯冷却至表面温度为50℃;
[0109]
连续冷却结束后,钢坯入加热炉加热至1260℃,并控制加热总时间为3.3h,出炉后在线轧制成70kg/m的钢轨;
[0110]
在线热处理包括利用终轧余热对钢轨轨头和轨腰进行压缩空气冷却,冷却速率控制在4.2℃/s;钢轨轨头冷却初始温度控制在880℃,钢轨轨头冷却温度低于450℃时钢轨空冷至室温;
[0111]
rh真空处理或vd真空处理后,所述钢液的化学成分包括0.3-1.3重量%的c、0.25-0.45重量%的mn、0.3-0.85重量%的si、0.025-0.1重量%的cr、0.04-0.09重量%的ti、0.01重量%的p、0.005重量%的s、余量的fe和不可避免的杂质。
[0112]
实施例5
[0113]
按照实施例2的方法实施,不同的是,在步骤(1)中,以1.3℃/s的冷却速率对钢坯进行冷却。
[0114]
实施例6
[0115]
按照实施例2的方法实施,不同的是,在步骤(1)中,将钢坯冷却至表面温度为350℃。
[0116]
实施例7
[0117]
按照实施例2的方法实施,不同的是,在步骤(2)中,以1℃/s的冷却速率对钢坯进行冷却。
[0118]
实施例8
[0119]
按照实施例2的方法实施,不同的是,在步骤(2)中,将钢坯冷却至表面温度为250℃。
[0120]
实施例9
[0121]
按照实施例2的方法实施,不同的是,在步骤(3)中,将钢坯冷却至表面温度为150℃。
[0122]
对比例1
[0123]
按照实施例1的方法实施,不同的是,不采用连续冷却工艺,而采用传统冷却工艺,直接将连铸完成的钢坯置于空气中自然冷却至室温;
[0124]
在线热处理时,冷却初始温度控制在790℃,冷却速率控制在1.6℃/s,冷却温度低于580℃时空冷至室温。
[0125]
对比例2
[0126]
按照实施例2的方法实施,不同的是,不采用连续冷却工艺,而采用传统冷却工艺,直接将连铸完成的钢坯置于空气中自然冷却至室温;
[0127]
在线热处理时,冷却初始温度控制在785℃,冷却速率控制在2℃/s,冷却温度低于568℃时空冷至室温。
[0128]
对比例3
[0129]
按照实施例3的方法实施,不同的是,不采用连续冷却工艺,而采用传统冷却工艺,直接将连铸完成的钢坯置于空气中自然冷却至室温;
[0130]
在线热处理时,冷却初始温度控制在780℃,冷却速率控制在2.4℃/s,冷却温度低于554℃时空冷至室温。
[0131]
对比例4
[0132]
按照实施例2的方法实施,不同的是,在步骤(1)中,对表面温度为800℃的钢坯进行第一阶段冷却。
[0133]
对比例5
[0134]
按照实施例2的方法实施,不同的是,在步骤(1)中,将钢坯冷却至表面温度为320℃。
[0135]
对比例6
[0136]
按照实施例2的方法实施,不同的是,在步骤(2)中,将钢坯冷却至表面温度为280℃。
[0137]
对比例7
[0138]
按照实施例2的方法实施,不同的是,在步骤(3)中,将钢坯冷却至表面温度为180℃。
[0139]
对比例8
[0140]
按照实施例2的方法实施,不同的是,在线热处理时,钢轨轨头冷却初始温度控制在900℃。
[0141]
对比例9
[0142]
按照实施例2的方法实施,不同的是,在线热处理时,钢轨轨头和轨腰冷却速率控制在2℃/s。
[0143]
对比例10
[0144]
按照实施例2的方法实施,不同的是,在线热处理时,钢轨轨头冷却温度低于550℃时钢轨空冷至室温。
[0145]
测试例
[0146]
将实施例和对比例中得到的钢轨空冷至室温,按照tb/t2344-2012标准要求位置取氢含量试样(过程严格采用液氮保存)、疲劳裂纹扩展速率da/dn、冲击韧性试样;在轨头踏面下23mm处取金相组织试样,实施例与对比例采用相同的测试部位与测试方法,测试结果如表1所示。
[0147]
表1
[0148][0149]
由表1的结果可以看出,在相同化学成分、冶炼及轧制工艺下,对铸坯开展连续缓慢冷却工艺及轧后采用不同的热处理方式对钢轨的最终性能将产生显著影响,具体表现为:采用本发明所述的方法,钢轨成品氢含量得到有效降低,钢轨轨头踏面下方23mm处关键部位珠光体片层间距更细;钢轨疲劳裂纹扩展速率da/dn显著优于对比例;常温冲击aku在钢轨踏面以下12mm、23mm处均得到显著提升。采用本发明所述的方法制备的钢轨氢含量得到一定程度降低、钢轨晶粒更加细小、组织更加致密,常温冲击韧性得到提升,裂纹扩展速率得到显著降低,同等条件下具有更优的抗延迟断裂性能,提升了钢轨线路服役的安全监测水平。
[0150]
以上详细描述了本发明的优选实施方式,但是,本发明并不限于此。在本发明的技
术构思范围内,可以对本发明的技术方案进行多种简单变型,包括各个技术特征以任何其它的合适方式进行组合,这些简单变型和组合同样应当视为本发明所公开的内容,均属于本发明的保护范围。