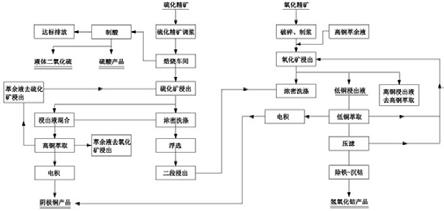
[0001]
本发明属于铜冶炼技术领域,具体涉及到一种硫酸化焙烧-浸出-浮选-萃取-沉钴耦合炼铜的方法。
背景技术:[0002]
铜是一种战略有色金属,被广泛地应用于建筑、交通运输、机械制造、电子电气、日用消费品、航空航天和国防等多个领域。我国的铜金属对外依存度高达75%。
[0003]
自然界中金属态的自然铜很少,铜矿一般分为硫化铜矿、氧化铜矿及它们的混合矿。除铜外,铜矿中通常还伴生各种有价金属,如金、银、镍、钴、铅、锌等。通常硫化铜矿的铜品位较低,需要通过选矿方法加以富集、产出硫化铜精矿,用于铜的冶炼提取。刚果(金)的铜矿石主要为高品位矿石,多数为硫化―氧化铜混合矿;在我国云南、新疆、湖北和西藏等地也存在大量低品位硫化―氧化铜混合矿,估计铜金属总量近千万吨。因此,开发利用此类铜矿资源具有重要意义,尤其是对刚果(金)的铜钴精矿特点,火法冶炼无法发挥自身优势,针对性的特殊工艺方案,支撑国内企业走出去提供技术支撑更具现实意义。从铜矿中提取铜的工艺技术方法主要有火法炼铜和湿法炼铜。
[0004]
火法炼铜主要是造锍熔炼,根据铜精矿类型形成了闪速熔炼法、诺兰达熔炼法、澳斯麦特熔炼法、艾萨熔炼法、水口山熔炼法等工艺,生产处含硫的中间产物冰铜,同时回收其他有价金属。但是针对海外特殊的社会环境,基础设施落后,辅助材料短缺无法自给,专业技术人员不足的现状,对于矿石普遍含钴,不含金、银,氧化矿储量丰富的特性;火法炼铜不能有效回收矿石中的钴,同事火法造锍捕金、规模效益等优势没有发挥出来,辅助材料是国内的5-10倍,因此在海外一些地区不适宜采用火法冶炼工艺直接处理的。
[0005]
由于湿法炼铜所需药剂少,且易于获得,投资少,见效快,因此,对于硫化铜精矿或难选的氧化铜矿采用湿法冶炼工艺。
[0006]
在生物堆浸工艺方面,中国专利cn104109765b公开的“一种次生硫化铜矿两段生物堆浸方法”,第一阶段浸出为:将破碎后的次生硫化铜矿送入堆场筑堆,并采用含有fe
3+
的硫酸喷淋液进行第一阶段浸出,直至最后一层矿石中浸出40%~50%的铜止;第二阶段浸出:采用1.2<ph<1.5的喷淋液对第一阶段浸出矿进行第二阶段浸出;最后将第一阶段浸出和第二阶段浸出的混合浸出液,依次经萃取、反萃和电积后得到阴极铜。该生物堆浸工艺虽然具有能耗低、投资小和规模可大可小等优点,但存在以下缺陷:当矿石破碎粒度粗时,因入堆矿石粒度大造成堆浸周期长、堆浸效率低、尾渣铜品位高的问题,而当矿石破碎粒度细时,因入堆矿石粉矿多造成渗透性差、铜浸出率低等不足的问题。
[0007]“硫酸化焙烧―浸出―电积”生产阴极铜工艺是曾广泛应用于硫化铜精矿提铜工艺,但是由于硫酸化焙烧,铜焙砂在浸出过程中,溶液中的酸循环累积,必须中和或者外排一部分萃余液才能维持系统酸平衡;且硫酸化焙烧浸出率低一般在95%左右,浸出渣中含铜2%左右,排放造成资源的极大浪费;萃余液回收金属钴,萃余液中的酸没有得到利用,还要用石灰中和造成酸资源的浪费和辅助药剂的消耗。上述的缺点造成湿法电解铜回收率低,
硫综合利用率低。此外,由于铜精矿颗粒中部分铜被其他物相包裹,较低酸度条件下无法使被包裹的铜浸出,因此,为了保证铜浸出率,采用高酸浸出,这不仅增加了酸耗,而且高浓度酸也提高了设备要求。
[0008]
综上,上述现有工艺不能使资源综合回收,效益最大化,存在铜回收率低,或是处理成本高,设备要求严格等不足,都未能很好地回收铜精矿和氧化矿的有价金属。
技术实现要素:[0009]
本发明所要解决的技术问题是提供一种能够解决铜精矿和氧化矿铜经济回收的问题,在解决传统“硫酸化焙烧―浸出―电积”系统涨液(液体量大量增加)和酸涨肚(系统产生的酸难以消纳)的同时,实现铜的高效回收利用。
[0010]
为了解决上述技术问题,本发明提供的一种硫酸化焙烧-浸出-浮选-萃取-沉钴耦合炼铜的方法,包括以下步骤:(1)硫酸化焙烧工序:硫化铜精矿硫酸化焙烧,控制温度和氧化还原气氛,使铜大部分生成硫酸铜,控制铁酸铜和硅酸铜的生成量。
[0011]
(2)浸出联合浮选工序:焙砂进行一段浸出,经酸浸破坏焙砂颗粒表面的铁酸铜及硅酸铜等难溶矿物后,颗粒内部未被完全燃烧的硫化矿物裸露出来。一段浸出矿浆经固液分离得到高铜浸出液和一段浸出渣。一段浸出渣调整ph值后进行浮选,浮选精矿进行二段浸出。
[0012]
通过浸出联合浮选工序,不仅使一段浸出渣中未浸出的铜物相通过浮选得到富集,降低了二段浸出提铜的难度,提高铜浸出率,而且减少了高酸浸出的规模,降低了设备投资,减少了酸耗。
[0013]
(3)铜精矿和氧化铜矿耦合浸出工序:所用原料为氧化铜矿和步骤(2)得到的二段浸出矿浆。步骤(2)得到的二段浸出矿浆并入氧化铜矿浸出槽,氧化铜矿浸出槽浸出后得到的矿浆经浓密机固液分离得到高铜浸出液和浸出渣,浸出渣经压滤机洗涤得到低铜浸出液和浸出尾渣。
[0014]
通过铜精矿和氧化矿联合浸出工序,不仅有效回收利用二段浸出矿浆中的多余酸,有效解决了酸涨肚问题,而且省略了步骤(2)得到的二段浸出矿浆固液分离工序,减少操作步骤,节省投资。
[0015]
(4)高铜浸出液处理工序:将步骤(2)和步骤(3)得到的高铜浸出液进行萃取,高铜萃余液返回步骤(2)的一段浸出流程,铜萃取液进入电积流程得到1#阴极铜。
[0016]
通过高铜浸出液处理工序,可以回收高铜萃余液中的酸,减轻整个工艺系统的酸涨肚问题。
[0017]
(5)低铜浸出液处理工序:将步骤(2)得到的低铜浸出液进行萃取,铜萃取液进入电积流程得到阴极铜;低铜萃余液一部分直接返回步骤(2)的一段浸出流程,剩余一部分低铜萃余液先采用氧化矿中和萃余液中过量的酸,经压滤机固液分离后,压滤渣返回步骤(2)并入氧化铜矿浸出槽,压滤液进行除铁沉钴,回收钴、铜。
[0018]
通过低铜浸出液处理工序不仅可以回收利用浸出液中富裕的酸,而且作为电解液净化功能设施,经过除铁沉钴可以提高电积流程制备阴极铜的效率及阴极铜品位。
[0019]
进一步地,步骤(1)所述铜精矿中主元素质量百分含量为:铜 cu 15~50%,钴 co 0.1~10.0%,硫 s 10~35%。
[0020]
进一步地,步骤(1)所述铜精矿焙砂中含酸为3-5kg/t矿。
[0021]
进一步地,步骤(1)的硫酸化焙烧温度相对偏低,为500-650℃;空气过剩系数相对偏高,为1.2-1.8。
[0022]
进一步地,步骤(2)的一段浸出工艺为低酸浸出,浸出终点ph值为1~2.5,浸出温度15-80℃,浸出时间1-6h,浸出所用酸来自铜精矿焙砂带入的酸和后续萃取工序返回的铜萃余液,铜萃余液含酸10~50g/l。
[0023]
进一步地,步骤(2)的二段浸出工艺为高酸浸出,浸出终点含酸量为100~400g/l,浸出所用酸为浓硫酸和后续萃取工序返回的铜萃余液,浸出矿浆浓度为:30-60%,浸出温度40-80℃,浸出时间1-6h。
[0024]
进一步地,步骤(3)中所述氧化铜矿的主要元素质量百分含量为:铜 cu 0.5~5%,钴 co 0.1~2%,硫 s 1.5~3.5%。
[0025]
进一步地,步骤(3)中二段浸出矿浆浓度15~50%,浸出终点ph值0.5-2,浸出温度15-80℃,浸出时间1-6h。
[0026]
进一步地,步骤(2)和步骤(3)得到的高铜浸出液含铜20~30g/l,步骤(3)得到的低铜浸出液含铜4~8g/l。
[0027]
进一步地,步骤(2)中一段浸出渣主要元素质量百分含量为:铜 cu 1.5~5%,钴 co 0.01~2.0%,硫 s 0.5~4%;一段浸出渣浮选精矿质量百分含量为:铜 cu 5~30%,钴 co 1~10.0%,硫 s 10~35%。
[0028]
本发明提出了以硫化铜精矿和氧化铜矿为原料,采用硫化铜精矿硫酸化焙烧—焙砂浸出联合浮选工艺—铜精矿和氧化矿耦合浸出工艺—萃取电积的新工艺回收利用其中的有价元素铜和钴。为传统的硫酸化焙烧—浸出—电积工艺的系统酸涨肚和水涨肚问题提供了一种经济环保的新工艺思路。本发明与现有硫化铜精矿冶炼工艺对比,具有以下优势:(1)工艺可操作性强,硫化铜精矿焙砂一段低酸浸出,操作成本低且试剂消耗量小,处理能力大,设备效率高。
[0029]
(2)工艺衔接性好,硫化铜精矿焙砂二段高酸浸出矿浆直接并入氧化矿浸出,省略高酸矿浆的固液分离,减少工艺操作困难,减少设备投资。
[0030]
(3)工艺环境友好,硫化铜精矿焙砂浸出采用浓密机联合压滤机进行固液分离,减少系统水涨肚;整个系统酸循环利用率高,酸耗小且无废酸排放。
[0031]
(4)浸出选择性好,有价金属回收率高,铜回收率大于99%,钴回收率大于90%。
附图说明
[0032]
图1是本发明的工艺流程图。
具体实施方式
[0033]
以下结合附图对本发明做进一步说明。
[0034]
如图1所示,本发明的一种处理混合铜精矿和氧化矿的湿法工艺包括以下步骤:(1)硫酸化焙烧工序:将硫化铜精矿进行硫酸化焙烧得到铜精矿焙砂。
[0035]
(2)浸出联合浮选工序:将步骤(1)得到的铜精矿焙砂进行一段浸出,浸出矿浆经固液分离得到高铜浸出液和一段浸出渣。一段浸出渣经调ph后进行渣浮选,浮选精矿进行二段浸出,得到二段浸出矿浆。
[0036]
(3)铜精矿和氧化矿联合浸出工序:将步骤(2)得到的二段浸出矿浆并入氧化矿浸出槽,浸出矿浆经浓密机固液分离得到高铜浸出液和浸出尾渣,浸出尾渣经压滤机洗涤得到低铜浸出液和浸出尾渣。
[0037]
(4)高铜浸出液处理工序:将步骤(2)和步骤(3)得到的高铜浸出液进行萃取,高铜萃余液返回步骤(2)的一段浸出工序,高铜萃取液进入电积流程可得到阴极铜。
[0038]
(5)低铜浸出液处理工序:将步骤(3)得到的低铜浸出液进行萃取,铜萃取液进入电积流程,低铜萃余液一部分直接返回步骤(2)的铜精矿和氧化矿联合浸出工序,剩余一部分低铜萃余液先采用氧化矿中和萃余液中过量的酸,经压滤机固液分离后,压滤渣返回步骤(2)的铜精矿和氧化矿联合浸出工序,压滤液进行除铁沉钴回收钴工序。
[0039]
实施例1硫化铜精矿经沸腾焙烧后得到焙砂,按液固比11,加入含酸30g/l的高铜萃余液进行一段浸出,浸出终点ph为2,其中铜浸出率95%,经浓密机和三级带滤机洗涤得到高铜浸出液和一段浸出渣。一段浸出渣含水20%,调整ph至碱性后,进行渣浮选,浮选精矿按液固比1,补入含酸30g/l的高铜萃余液和98%的浓硫酸,浸出终点含酸100g/l。二段浸出矿浆并入氧化铜精矿浸出槽中,按液固比3,加入含酸10g/l的低铜萃余液进行浸出,经浓密机得到高铜浸出液和浸出渣,浸出渣经压滤机洗涤得到低铜浸出液和浸出尾渣。高铜浸出液经萃取得到高铜萃取液和高铜萃余液。高铜萃取液经电积得到1#阴极铜,高铜萃余液返回一段浸出工序。低铜浸出液进行萃取,铜萃取液进入电积工序,低铜萃余液10%直接返回铜精矿和氧化矿联合浸出工序,剩余90%低铜萃余液先采用氧化矿中和萃余液中过量的酸,经压滤机固液分离后,压滤渣再返回铜精矿和氧化矿联合浸出工序,压滤液进行除铁沉钴回收钴。
[0040]
实施例2.硫化铜精矿经沸腾焙烧后得到焙砂,按液固比10,加入含酸30g/l的高铜萃余液进行一段浸出,浸出终点ph为1.5,其中铜浸出率95%,经浓密机和三级带滤机洗涤得到高铜浸出液和一段浸出渣。一段浸出渣含水20%,调整ph至碱性后,进行渣浮选,浮选精矿按液固比1,补入含酸30g/l的高铜萃余液和98%的浓硫酸,浸出终点含酸100g/l。二段浸出矿浆并入氧化铜精矿浸出槽中,按液固比3,加入含酸10g/l的低铜萃余液进行浸出,经浓密机得到高铜浸出液和浸出渣,浸出渣经压滤机洗涤得到低铜浸出液和浸出尾渣。高铜浸出液经萃取得到高铜萃取液和高铜萃余液。高铜萃取液经电积得到1#阴极铜,高铜萃余液返回一段浸出工序。低铜浸出液进行萃取,铜萃取液进入电积工序,低铜萃余液10%直接返回铜精矿和氧化矿联合浸出工序,剩余90%低铜萃余液先采用氧化矿中和萃余液中过量的酸,经压滤机固液
分离后,压滤渣再返回铜精矿和氧化矿联合浸出工序,压滤液进行除铁沉钴回收钴。
[0041]
实施例3.硫化铜精矿经沸腾焙烧后得到焙砂,按液固比9,加入含酸2/l的高铜萃余液进行一段浸出,浸出终点ph为2,其中铜浸出率90%,经浓密机和三级带滤机洗涤得到高铜浸出液和一段浸出渣。一段浸出渣含水20%,调整ph至碱性后,进行渣浮选,浮选精矿按液固比1,补入含酸30g/l的高铜萃余液和98%的浓硫酸,浸出终点含酸100g/l。二段浸出矿浆并入氧化铜精矿浸出槽中,按液固比3,加入含酸10g/l的低铜萃余液进行浸出,经浓密机得到高铜浸出液和浸出渣,浸出渣经压滤机洗涤得到低铜浸出液和浸出尾渣。高铜浸出液经萃取得到高铜萃取液和高铜萃余液。高铜萃取液经电积得到1#阴极铜,高铜萃余液返回一段浸出工序。低铜浸出液进行萃取,铜萃取液进入电积工序,低铜萃余液10%直接返回铜精矿和氧化矿联合浸出工序,剩余90%低铜萃余液先采用氧化矿中和萃余液中过量的酸,经压滤机固液分离后,压滤渣再返回铜精矿和氧化矿联合浸出工序,压滤液进行除铁沉钴回收钴。
[0042]
实施例4.硫化铜精矿经沸腾焙烧后得到焙砂,按液固比12,加入含酸25g/l的高铜萃余液进行一段浸出,浸出终点ph为2,其中铜浸出率96%,经浓密机和三级带滤机洗涤得到高铜浸出液和一段浸出渣。一段浸出渣含水20%,调整ph至碱性后,进行渣浮选,浮选精矿按液固比1,补入含酸30g/l的高铜萃余液和98%的浓硫酸,浸出终点含酸100g/l。二段浸出矿浆并入氧化铜精矿浸出槽中,按液固比3,加入含酸10g/l的低铜萃余液进行浸出,经浓密机得到高铜浸出液和浸出渣,浸出渣经压滤机洗涤得到低铜浸出液和浸出尾渣。高铜浸出液经萃取得到高铜萃取液和高铜萃余液。高铜萃取液经电积得到1#阴极铜,高铜萃余液返回一段浸出工序。低铜浸出液进行萃取,铜萃取液进入电积工序,低铜萃余液10%直接返回铜精矿和氧化矿联合浸出工序,剩余90%低铜萃余液先采用氧化矿中和萃余液中过量的酸,经压滤机固液分离后,压滤渣再返回铜精矿和氧化矿联合浸出工序,压滤液进行除铁沉钴回收钴。