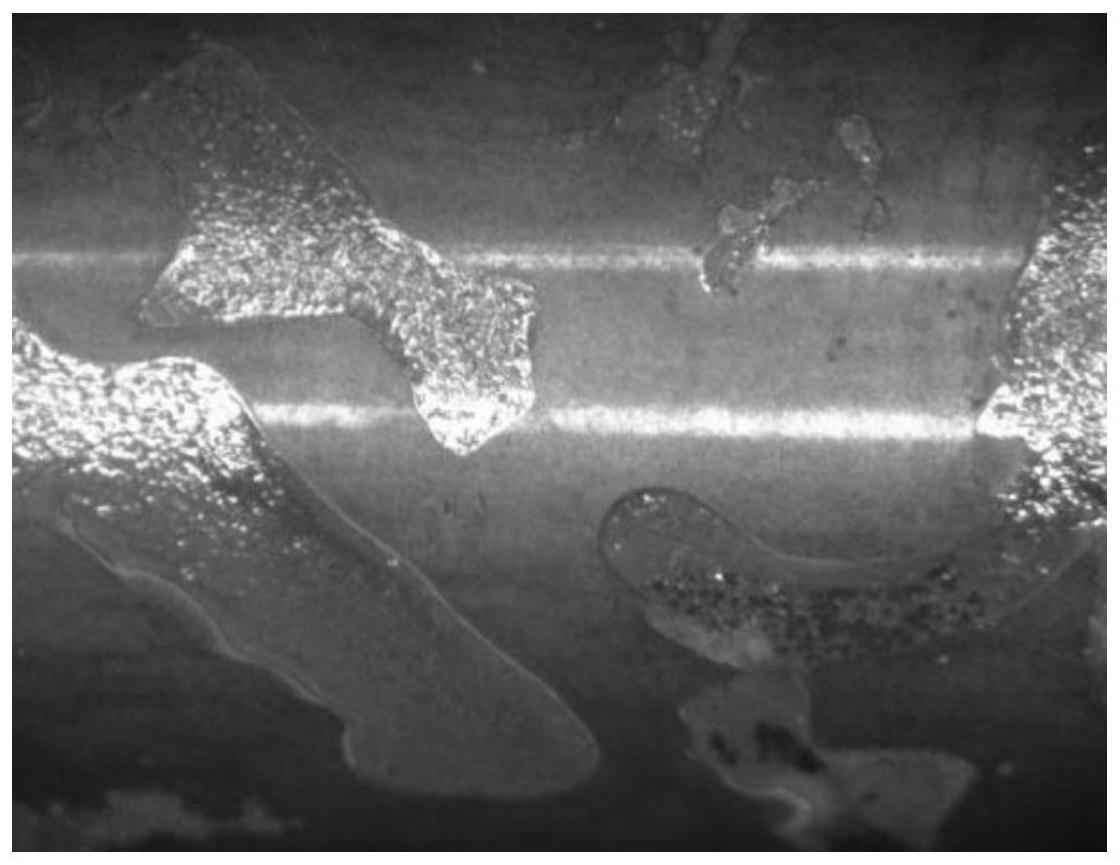
1.本发明属于合金材料技术领域,具体涉及一种中碳低合金高强钢及其制备方法。
背景技术:2.海洋工程中的海底井口和采油装备是海洋油气田开发中的重要单元装备,也是海底采油系统的关键装备。由于处于海底高压、低温、海水和油气腐蚀等恶劣的工况下,海底装备的性能和质量对油井安全起着至关重要的作用。目前海工装备已由浅海装备向深海大型装备发展,这对海洋井口材料提出了更高的要求。
3.海底井口和采油装备对材料各项性能的要求不断提高,但是仅依靠改善热处理制度来提高材料的综合性能,其效果非常有限,导致现有的井口设备材料的强度和韧性较低,耐低温冲击和耐腐蚀较差。
技术实现要素:4.鉴于上述分析,本发明旨在提供一种中碳低合金高强钢及其制备方法,解决了现有技术中的海底井口和采油装备材料的强度和韧性较低,耐低温冲击和耐腐蚀较差的问题。
5.本发明的目的主要是通过以下技术方案实现的:
6.本发明提供了一种中碳低合金高强钢,其组成按重量百分比计包括:c 0.20~0.30、mn 0.70~0.90、si 0.15~0.35、cr 0.70~1.00、mo 0.30~0.50、p≤0.01、s≤0.01、ni 0.50~0.70、v≤0.05、cu≤0.15、nb≤0.015、ti≤0.015其余成分为fe和不可避免杂质。
7.进一步地,上述中碳低合金高强钢的组成按重量百分比计包括:c 0.23~0.27、mn 0.75~0.80、si 0.20~0.25、cr 0.80~0.95、mo 0.35~0.45、p≤0.01、s≤0.01、ni 0.55~0.60、v 0.03~0.04、cu 0.01~0.1、nb 0.001~0.010、ti 0.001~0.010、其余为fe和不可避免的杂质。
8.进一步地,上述中碳低合金高强钢中,最终组织为回火索氏体,抗拉强度为880~900mpa,屈服强度为810~830mpa,延伸率为17~21%,断面收缩率为73~74%,
‑
18℃的冲击功为200~210j。
9.本发明还提供一种中碳低合金高强钢的制备方法,用于制备上述中碳低合金高强钢,上述制备方法包括如下步骤:
10.步骤s1:按照中碳低合金高强钢的组成,利用冶炼得到铸锭;
11.步骤s2:对铸锭进行热加工,得到坯料;
12.步骤s3:对坯料进行热处理,得到中碳低合金高强钢。
13.进一步地,上述步骤s2包括如下步骤:
14.步骤s21:将铸锭加热到1100℃~1250℃保温5h~10h进行均质化热处理,随炉冷却至室温,需要说明的是,上述加热方式可以采用铸锭随炉加热或者将铸锭放入已加热至1100℃~1250℃的炉中;
15.步骤s22:对均质化热处理后的铸锭进行加热锻造,加热保温温度1100℃~1180℃,加热保温时间2h~5h,锻造比不小于3,坯料开锻温度不低于1100℃。
16.进一步地,上述步骤s3包括如下步骤:
17.步骤s31:将坯料加热至850℃~900℃(ac3温度以上)保温2h~8h,随炉冷却进行等温转变,空冷至室温;
18.步骤s32:将空冷后的坯料加热到850℃~900℃(ac3温度以上)保温1h~8h进行淬火;
19.步骤s33:将淬火后的坯料加热到580℃~650℃(ac1温度以下)保温2h~24h进行回火。
20.进一步地,上述步骤s31中,采用两阶段升温,第一段升温为从室温以280℃/h~330℃/h的升温速率升温至750℃,第二段升温为从750℃以120℃/h~230℃/h的升温速率升温至850℃~900℃。
21.进一步地,上述步骤s32中,采用两阶段升温,第一段升温为从室温以280℃/h~330℃/h的升温速率升温至750℃,第二段升温为从750℃以120℃/h~230℃/h的升温速率升温至850℃~900℃。
22.进一步地,采用水淬和/或油淬的方式冷却至80℃~100℃以下。
23.进一步地,上述步骤s33中,回火的次数为至少两次。
24.与现有技术相比,本发明至少可实现如下有益效果之一:
25.a)本发明提供的中碳低合金高强钢及其制备方法,通过组成和制备方法的多次设计、优化和匹配,例如,组分、微观组织和热处理工艺等,能够获得力学性能和加工性能优异且具有抗h2s腐蚀性能的中碳低合金高强钢。
26.b)本发明提供的中碳低合金高强钢具有高强度、高韧性、耐低温冲击和耐腐蚀等特点,适当降低c含量,提高了ni元素含量,以提高基体韧性,添加少于0.05%的v元素,细化晶粒,提高强韧性及耐腐蚀性能。本发明通过适当降低c含量,提高ni元素含量和添加少量v元素获得强度、韧性和塑性的良好匹配,适用于海底井口钻采设备上的关键部件。
27.c)本发明提供的中碳低合金高强钢的制备方法中,通过高温均质化热处理,使得偏析元素得到充分扩散,同时也能够达到去氢的目的;通过锻造能够达到细化晶粒的目的,从而为提高上述中碳低合金高强钢的综合性能打下良好的基础。
28.d)本发明提供的中碳低合金高强钢的制备方法中,经正火(步骤s31)后,坯料能够获得较为细小和均匀的晶粒;控制淬火,能够起到晶粒的二次细化效果;控制回火温度,能够促进强度、塑性和韧性的良好匹配,促进微观组织中碳化物弥散分布,且尺寸小于50nm。
29.e)本发明提供的中碳低合金高强钢的制备方法中,通过正火(步骤s31)、淬火(步骤s32)、回火(步骤s33)以及控制回火温度在580℃~650℃,能够在钢中形成回火索氏体结构,回火索氏体有利于上述中碳低合金高强钢的抗硫化氢腐蚀性能。
30.本发明的其他特征和优点将在随后的说明书中阐述,并且,部分的从说明书中变得显而易见,或者通过实施本发明而了解。本发明的目的和其他优点可通过在所写的说明书以及附图中所特别指出的结构来实现和获得。
附图说明
31.附图仅用于示出具体发明的目的,而并不认为是对本发明的限制,在整个附图中,相同的参考符号表示相同的部件。
32.图1为本发明实施例1提供的中碳低合金高强钢抗硫化氢腐蚀后试样表面结果;
33.图2为本发明实施例2提供的中碳低合金高强钢抗硫化氢腐蚀后试样表面结果。
具体实施方式
34.下面结合附图来具体描述本发明的优选发明,其中,附图构成本发明的一部分,并与本发明的发明一起用于阐释本发明的原理。
35.本发明提供了一种中碳低合金高强钢,其组成按重量百分比计包括:c 0.20~0.30、mn 0.70~0.90、si 0.15~0.35、cr 0.70~1.00、mo 0.30~0.50、p≤0.01、s≤0.01、ni 0.50~0.70、v≤0.05、cu≤0.15、nb≤0.015、ti≤0.015其余成分为fe和不可避免杂质。
36.与现有技术相比,本发明提供的中碳低合金高强钢具有高强度、高韧性、耐低温冲击和耐腐蚀等特点,适当降低c含量,提高了ni元素含量,以提高基体韧性,添加少于0.05%的v元素,细化晶粒,提高强韧性及耐腐蚀性能。本发明通过适当降低c含量,提高ni元素含量和添加少量v元素获得强度、韧性和塑性的良好匹配,适用于海底井口钻采设备上的关键部件。
37.具体来说,上述中碳低合金高强钢中,各组分的作用如下:
38.c:在合理范围内尽量降低c含量,能够有效改善钢的塑韧性及低温冲击韧性,降低韧脆转变温度。
39.mn:能够提高材料的淬透性,且具有固溶强化作用,适量的mn加入能够提高基体韧性,降低韧脆转变温度;但是,mns夹杂物是引起湿硫化氢腐蚀的主要因素,会导致应力腐蚀开裂的敏感性增加,因此,综合考虑mn对钢的力学性能与腐蚀性的影响,mn的加入量控制在0.70~0.90的范围内。
40.si:能够提高材料的淬透性,且具有固溶强化作用,但是,si在低合金高强钢中,易偏析在晶粒的边界,助长晶间裂纹,因此,si的加入量控制在0.15~0.35的范围内。
41.cr:能够有效提高上述中碳低合金高强钢的淬透性、热强性和抗硫化氢应力腐蚀性能,且具有固溶强化作用,cr含量对上述中碳低合金高强钢的抗硫化性能的影响很大,有利于减轻硫化物对上述中碳低合金高强钢的相对腐蚀。在高温h2s的腐蚀介质中,上述中碳低合金高强钢中cr具有抑制硫醇吸附的作用,因此,cr的加入量控制在0.70~1.00的范围内。
42.mo:能够促进上述中碳低合金高强钢的钝化,提高其在硫酸、盐酸及部分有机酸中的耐蚀性和抗点蚀能力;在高温回火时,mo能够抑制磷等杂质在晶界偏聚而导致的脆性现象,从而增强基体抗h2s腐蚀性能,同时,mo的加入还能够有效提高上述中碳低合金高强钢的淬透性和热强性,且具有固溶强化作用,因此,mo的加入量控制在0.30~0.50的范围内。
43.ni:促使上述中碳低合金高强钢形成稳定奥氏体组织的主要元素,但由于含镍钢上的析氢过电位最低,氢离子易于放电,强化吸氢过程,使得钢中的硫化物破裂敏感性增加,因此,在上述中碳低合金高强钢的设计过程中,ni的加入量不能接近或达到1%,ni的加入量控制在0.50~0.70的范围内。
44.v:强碳化合物形成元素,能够细化晶粒,提高抗硫化物应力腐蚀(ssc)敏感性,但是,如果v的加入量过大,由于vc过硬易产生磨削裂纹,会导致钢的磨削和焊接性较差,因此,v的加入量控制在v≤0.05的范围内。
45.cu:能够加速氢原子的再结合速度,进而减少氢的活动性,提高上述中碳低合金高强钢在酸性介质中的耐蚀性和抗点蚀能力,增强抗h2s应力腐蚀能力;但是,cu的加入量过大,会导致钢的高温强度和韧性较低,焊接性变差,因此,cu的加入量控制在≤0.10的范围内。
46.ti:能够有效改善硫化物开裂的敏感性,为强碳化合物形成元素,减少固溶碳量,从而减少未回火马氏体的形成,降低硬度,因此,ti的加入量控制在≤0.015的范围内。
47.nb:能够减少上述中碳低合金高强钢组织的不均匀,提高上述中碳低合金高强钢的抗硫化物腐蚀性能;同时,nb与mo复合添加时,能够进一步提高抗裂性,因此,nb的加入量控制在≤0.015的范围内。
48.p:作为吸氢过程的促进剂,其非金属夹杂物容易引起层状撕裂裂纹和焊道尾部裂纹,与应力腐蚀裂纹相重合后能使裂纹加速扩展,因此,应严格控制p含量在1%以内。
49.s:作为钢中硫化物夹杂是氢脆源之一,易沿夹杂物边界开裂,也是导致z向断裂的因素;与p的危害相似,其非金属夹杂物,也容易引起层状撕裂裂纹和焊道尾部裂纹,与应力腐蚀裂纹相重合后能使裂纹加速扩展,应严格控制s含量在0.01%以内。
50.为了进一步优化上述中碳低合金高强钢的性能,其组成按重量百分比计包括:c 0.23~0.27、mn 0.75~0.80、si 0.20~0.25、cr 0.80~0.95、mo 0.35~0.45、p≤0.01、s≤0.01、ni 0.55~0.60、v 0.03~0.04、cu 0.01~0.1、nb 0.001~0.010、ti 0.001~0.010、其余为fe和不可避免的杂质。
51.本发明还提供一种中碳低合金高强钢的制备方法,用于制备上述中碳低合金高强钢,上述制备方法包括如下步骤:
52.步骤s1:按照中碳低合金高强钢的组成,利用冶炼得到铸锭;
53.步骤s2:对铸锭进行热加工,得到坯料;
54.步骤s3:对坯料进行热处理,得到中碳低合金高强钢。
55.与现有技术相比,本发明提供的中碳低合金高强钢的制备方法的有益效果与上述的中碳低合金高强钢的有益效果基本相同,在此不一一赘述。
56.具体来说,上述步骤s2包括如下步骤:
57.步骤s21:将铸锭加热到1100℃~1250℃保温5h~10h进行均质化热处理,随炉冷却至室温,需要说明的是,上述加热方式可以采用铸锭随炉加热或者将铸锭放入已加热至1100℃~1250℃的炉中;
58.步骤s22:对均质化热处理后的铸锭进行加热锻造,加热保温温度1100℃~1180℃,加热保温时间2h~5h,锻造比不小于3,坯料开锻温度不低于1100℃,需要说明的是,锻造完成后可以选择回炉进行去应力退火也可以直接选择空冷,具体处理方式可根据样件尺寸以及现场条件灵活处理,并不局限于上述两种处理方式。
59.步骤s2采用上述方式,通过高温均质化热处理,使得偏析元素得到充分扩散,同时也能够达到去氢的目的;通过锻造能够达到细化晶粒的目的,从而为提高上述中碳低合金高强钢的综合性能打下良好的基础。
60.上述步骤s3包括如下步骤:
61.步骤s31:将坯料加热至850℃~900℃(ac3温度以上)保温2h~8h,随炉冷却进行等温转变,空冷至室温;
62.步骤s32:将空冷后的坯料加热到850℃~900℃(ac3温度以上)保温1h~8h进行淬火;
63.步骤s33:将淬火后的坯料加热到580℃~650℃(ac1温度以下)保温2h~24h进行回火。
64.上述热处理方法,经正火(步骤s31)后,坯料能够获得较为细小和均匀的晶粒;控制淬火,能够起到晶粒的二次细化效果;控制回火温度,能够促进强度、塑性和韧性的良好匹配,促进微观组织中碳化物弥散分布,且尺寸小于50nm。
65.此外,通过正火(步骤s31)、淬火(步骤s32)、回火(步骤s33)以及控制回火温度在580℃~650℃,能够在钢中形成回火索氏体结构,回火索氏体有利于上述中碳低合金高强钢的抗硫化氢腐蚀性能。
66.具体来说,采用上述中碳低合金高强钢的组成和制备方法制得的中碳低合金高强钢,其微观组织中基本上全部是回火索氏体,抗拉强度为880~900mpa,屈服强度为810~830mpa,延伸率为17~21%,断面收缩率为73~74%,
‑
18℃的冲击功为200~210j。
67.为了在保证坯料温度均匀性的基础上提高正火的升温效率,上述步骤s31中,采用两阶段升温,第一段升温为从室温以280℃/h~330℃/h的升温速率升温至750℃,第二段升温为从750℃以120℃/h~230℃/h的升温速率升温至850℃~900℃。第一段升温采用快速加热是因为坯料具有一定的厚度,在室温
‑
750℃的温度范围内,钢中的微观组织转变基本没有影响,快速加热能够有效提高升温效率;第二段升温采用慢速加热是因为,在750℃左右,钢中的微观组织会发生奥氏体转变,慢速加热有利于坯料的温度均匀化。
68.同样地,为了在保证坯料温度均匀性的基础上提高淬火的升温效率,上述步骤s32中,采用两阶段升温,第一段升温为从室温以280℃/h~330℃/h的升温速率升温至750℃,第二段升温为从750℃以120℃/h~230℃/h的升温速率升温至850℃~900℃。第一段升温采用快速加热是因为坯料具有一定的厚度,在室温
‑
750℃的温度范围内,钢中的微观组织转变基本没有影响,快速加热能够有效提高升温效率;第二段升温采用慢速加热是因为,在750℃左右,钢中的微观组织会发生奥氏体转变,慢速加热有利于坯料的温度均匀化。
69.对于淬火冷却的方式,具体来说,可以采用水淬和/或油淬的方式冷却至80℃~100℃以下。
70.需要说明的是,为了达到更好的使用性能,上述步骤s33中,回火的次数为至少两次,通过多次回火,能够进一步促进强度、塑性和韧性的良好匹配,促进微观组织中碳化物弥散分布。
71.综上,本发明提供的中碳低合金高强钢及其制备方法,通过组成和制备方法的多次设计、优化和匹配,例如,组分、微观组织和热处理工艺等,能够获得力学性能和加工性能优异且具有抗h2s腐蚀性能的中碳低合金高强钢。
72.实施例1
73.本发明实施例1的化学成分及配料,以重量百分含量计(%),包括:c 0.26、mn 0.86、si 0.25、cr 0.93、mo 0.40、p≤0.005、s≤0.0018、ni 0.60、v 0.031、cu 0.15、nb<
0.005、ti≤0.010;其余成分为fe和不可避免的杂质。
74.对实施例1的钢锭采用如下热加工工艺:将钢锭加热到1230℃保温10h进行均质化热处理,随后炉冷至室温。随后进行热加工,保温温度1160℃,保温4h,加热完成后出炉锻造,锻造比为5.6,锻造完成后空冷。
75.对实施例1采用如下热处理工艺:将锻件加热至900℃保温2h后随炉冷却至700℃然后空冷至室温,再将锻件加热到870℃保温2h后水冷进行淬火,最后加热到650℃保温4h然后随炉冷却进行回火。
76.实施例2
77.本发明实施例2的化学成分及配料,以重量百分含量计(%),包含:c 0.24、mn 0.78、si 0.21、cr 0.84、mo 0.38、p≤0.005、s 0.0014、ni 0.56、v 0.031、cu 0.011、nb<0.010、ti≤0.010;其余成分为fe和不可避免的杂质。
78.对实施例2钢锭采用如下热加工工艺:将钢锭加热到1230℃保温10h进行均质化热处理,随后炉冷至室温。随后进行热加工,保温温度1160℃,保温4h,加热完成后出炉锻造,锻造比为5.6,锻造完成后空冷。
79.对实施例2采用如下热处理工艺:将锻件加热至900℃保温2h后随炉冷却至700℃然后空冷至室温,再将锻件加热到890℃保温1h水冷进行淬火,最后加热到650℃保温4h进行然后随炉冷却进行回火。
80.通过上述热处理,本发明2个实施例中,碳低合金钢均获得了非常优异的强度、塑性和韧性的综合性能,尤其是
‑
18℃低温冲击韧性,得到大幅提高,另外,经过高温回火后得到的回火索氏体具有非常优异的耐腐蚀性能。
81.以某公司改进型8630作为对比例,具体化学成分如表1所示。材料经电炉熔炼后,可通过真空除气(vd)、氩气搅拌除气、氩氧脱碳(aod)、电渣重熔(esr)或真空电弧重熔(var)精炼;锻造时锻比应不小于3.0;正火899
‑
972℃;淬火871
‑
927℃;回火677
‑
722℃。
82.本发明的实施例1、实施例2和对比例1的组成对比,参见表1;本发明的实施例1、实施例2和对比例1的性能对比,参见表2。
83.表1实施例1、实施例2与对比例1的组成对比
84.85.表2本发明的实施例1、实施例2和对比例1的性能对比
[0086][0087]
由表2可以看出,实施例1和实施例2各项性能更加优异,尤其是低温冲击功,
‑
18℃条件下分别达到207j和201j;根据nace tm0177
‑
2016标准开展抗硫化氢腐蚀腐蚀(ssc 2区),耐蚀性能良好,腐蚀后外观形貌(10x照片),参见图1和图2。
[0088]
以上所述仅为本发明较佳的具体实施方式,但本发明的保护范围并不局限于此,任何熟悉本技术领域的技术人员在本发明揭露的技术范围内,可轻易想到的变化或替换,都应涵盖在本发明的保护范围之内。