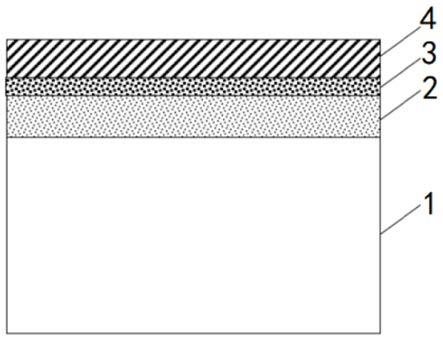
1.本发明属于燃料电池技术领域,具体涉及一种用于金属双极板成形的导电耐蚀预涂层及其制备方法。
背景技术:2.质子交换膜燃料电池(proton exchange membrane fuel cell,简称pemfc)以氢气为燃料进行发电,并且产物为水无污染,对环境十分友好,其应用范围已经包括汽车,无人机、固定电站等。而在质子交换膜燃料电池电堆中双极板发挥着重要作用,其占据了电堆重量的80%以及电堆成本的45%,主要承担着气体分配、热量传导以及一定的支撑作用。而在众多的质子交换膜燃料电池双极板材料当中,包括金属、石墨以及复合材料等。金属双极板具有优异的导电导热性以及良好的机械性能已作为燃料电池极板材料的首选,但是未经表面改性的金属双极板易发生严重腐蚀造成大量离子析出污染催化剂,表面生成的氧化保护膜造成其导电性的急剧下降,因此仍需对金属极板进行表面改性以提高其导电性和耐蚀性。
3.金属双极板从原材料到加工成产品需要经历很多道工艺,主要包括金属薄板的冲压成型、阴极板和阳极板的焊接、金属双极板的表面改性处理以及密封。采用间歇式的加工方法会因为加工工序的繁琐而造成金属双极板生产效率的下降以及良品率的降低,因此为了提高其生产效率,直接制备出具有优异导电耐蚀性能的金属薄板用于后续的冲压焊接具有重要意义。专利文献cn110129727a公开了一种采用卷对卷物理气相沉积方法制备金属带预涂层的方法,可以极大地降低金属双极板的生产成本,虽然其金属过渡层加上石墨化镀层的结构具有良好的导电耐蚀性能,但是其结合性能和延展性能不足。专利文献cn1875128a公开了一种涂覆金属涂层的不锈钢带的制备方法,并在抗拉测试中钢带被单轴拉断而不会出现涂层的剥落和开裂现象,但其腐蚀性能还有待改善。
4.为了提高金属双极板的导电性和耐蚀性,研究人员已经开发出了多种类型涂层,包括贵金属涂层、金属碳化物涂层、金属氮化物涂层以及碳基涂层,同时为了提高这些导电耐蚀涂层和金属基材的结合性能并降低基材中的离子析出,通常需要在两者之间沉积一层或者多层金属过渡层。但是在金属薄板的冲压过程中,薄板上的应变超过20%,甚至达到30%。在如此大的应变条件下,涂覆有上述金属过渡层的导电耐蚀涂层会发生开裂现象,甚至会从基材上剥离,造成腐蚀溶液渗入基材加速腐蚀。因此,开发一种沉积在金属薄板上具有优异导电耐蚀性能、结合性能以及延展性能的预涂层,用于金属双极板加工成形对提高金属双极板的生产效率,降低金属制造成本实现商业化具有重要意义。
技术实现要素:5.本发明的目的是提供一种用于金属双极板成形的导电耐蚀预涂层及其制备方法,以避免预涂层在冲压成型过程中发生开裂以及剥落现象。
6.本发明的技术方案如下:
7.本发明的一种用于金属双极板成形的导电耐蚀预涂层,其特征在于,从金属基材向上,依次包括:覆盖在所述金属基材表面上的离子注入层,覆盖在所述离子注入层表面的界面扩散层,以及沉积在所述界面扩散层表面导电层;所述离子注入层的离子种类为贵金属au、ag、pt,过渡金属ti、cr、nb、ta、w、mo或非金属c、n、si对应离子中的一种或多种;所述界面扩散层的材质为过渡金属ti、cr、nb、ta、w、mo的碳化物或氮化物,或非金属c、si;所述表面导电层的材质为贵金属au、ag、pt,或导电碳材料(如:类金刚石碳、类石墨碳、类聚合物碳),优选导电碳材料为类石墨碳;所述离子注入层用于改善涂层的腐蚀性能和成形性能,所述界面扩散层用于消除离子注入产生的缺陷,并提高涂层和基材之间的结合力,所述表面导电层进一步优化涂层的导电性能。
8.进一步地,所述离子注入层覆盖在所述金属基材表面,有部分以柱型、锯齿型或者混合型结构嵌入到所述金属基材的内部,增加了离子注入层和金属基材之间的结合性能;所述离子注入层厚度为10~1000nm,优选10~500nm。
9.所述界面扩散层的制备方法包括热辅助扩散、电辅助扩散、激光辅助扩散、等离子体辅助扩散中的一种;包括两方面功能:第一是通过在所述离子注入层和所述金属基材之间的界面扩散来改善离子注入层均匀性,提高所述离子注入层结合性能;第二,如图2所示,离子注入过程中由于离子能量的随即分散性会产生过高能量的离子,对基材表面轰击过于猛烈而产生高能离子缺陷,缺陷形成的通路会导致腐蚀溶液渗入基材造成损伤,过低能量的离子则会附着在基材表面形成低能离子缺陷,造成结合性能下降,所述界面扩散层可以填充与扩散消除上述离子注入层中的两种缺陷。
10.进一步地,所述界面扩散层的制备方法,还包括采用稀有气体元素(例如:he、ne、ar、kr、xe等)进行等离子体辉光放电处理,或者通过表面离子渗碳、离子渗氮/碳氮共渗处理。
11.进一步地,所述表面导电层通过物理气相沉积、化学气相沉积或者离子镀的方法,将所述贵金属或者导电碳材料沉积附着在所述界面扩散层的表面,进一步提高涂层的导电性能,可为单层或者多层结构,总厚度低于5μm,优选低于1μm。
12.进一步地,在本发明的所述导电耐蚀预涂层中,当所述离子注入层的材质为贵金属au、ag、pt或者非金属c时,所述表面导电层可以省略,贵金属及c离子注入层自身就能作为一种表面导电层;而当所述离子注入层的材质为其它元素时,则所述表面导电层必须存在。
13.本发明所述的一种用于金属双极板成形的导电耐蚀预涂层的制备方法,其特征在于,包括以下步骤:
14.(1)在真空环境中对所述金属基材进行清洗,除去其表面的杂质和氧化膜;
15.(2)将金属离子或者非金属离子注入所述金属基材的表面或内部,形成与所述金属基材紧密结合的所述离子注入层;
16.(3)在ar、he、n2或h2的气氛中,对所述金属基材进行界面扩散处理,在所述离子注入层的外表面形成所述扩散处理层;
17.(4)在所述扩散处理层的外表面上,沉积一层或多层所述表面导电层;即可得到带有本发明所述的导电耐蚀预涂层的金属双极板板材;
18.在所述步骤(1)中,所述清洗为离子源清洗、射频清洗、自偏压清洗中的一种;处理
温度为25~500℃,优选100~300℃;预处理时间2~60min,优选5~20min。
19.在所述步骤(2)中,所述离子注入的能量为0.01~10mev,优选0.1~1mev;所述温度为25~1000℃,优选400~800℃;所述气压为0.1~100pa,优选1~10pa;注入为时间0.1~10h,优选0.1~3h。
20.优选地,在所述步骤(3)中,如果所述界面扩散处理采用热辅助方法,则处理温度为600~800℃;如果所述界面扩散处理采用其它扩散方法,则处理温度为200~500℃;处理气压在0.1~1000pa,优选10~100pa,处理时间1~100min,优选5~50min。
21.在所述步骤(4)中,所述表面导电层的制备方法包括磁控溅射沉积、化学气相沉积、脉冲激光沉积、离子镀等沉积方法,沉积温度200~800℃,优选500~600℃,沉积气压0.01~10pa,优选0.4~10pa,沉积时间0.1~5h,优选0.1~1h。
22.本发明所述导电耐蚀预涂层的制备方法,在单个真空腔室内完成,或者在多个腔体的连续设备上连续完成。
23.所述导电耐蚀涂层具有优异的结合性能和延展性能,在涂覆涂层的薄板冲压成形成金属双极板之后,涂层形貌完整,表面未出现涂层的开裂和剥离现象。
24.与现有技术相比,本发明通过离子注入和辅助扩散的有效结合提高了涂层和基材之间的结合性能,扩散处理层消除了涂层缺陷并提高了均匀性,并结合传统沉积方法进行涂层的表面改性,表面导电层具有优异导电耐蚀延展性能,所得到的预涂层不仅具备良好的导电性能和耐蚀性能,同时涂层本身具有优异的延展性能,并和基材之间结合牢靠,在薄板冲压成形过程中有效地避免了涂层开裂和剥离现象,对于降低金属制造成本实现商业化具有重要意义。
附图说明
25.图1为本发明的预涂层剖视结构示意图;
26.图2为本发明中界面扩散处理作用示意图;
27.图3为本发明实施例1中涂层后冲压成形和冲压成形后涂层的腐蚀电流密度对比;
28.图4为本发明实施例1中涂层后冲压成形和冲压成形后涂层的接触电阻对比;
29.图中标记说明:1
‑
基材,2
‑
离子注入层,3
‑
界面扩散层,4
‑
表面导电层,11
‑
高能离子缺陷,12
‑
低能离子缺陷。
具体实施方式
30.下面结合附图和具体实施例对本发明进行详细说明。本实施例以本发明技术方案为前提进行实施,给出了详细的实施方式和具体的操作过程,但本发明的保护范围不限于下述的实施例。
31.实施例1
32.一种用于金属双极板成形的导电耐蚀预涂层,采用以下步骤制备:
33.(1)将不锈钢基材置于样品架上,将样品架送入涂层沉积设备腔体,抽真空至低于本底真空8e
‑
3pa,温度至200℃,通入氩气使气压维持在0.1pa,样品架上施加
‑
700v的偏压进行清洗,除去不锈钢基材表面的杂质、油污和氧化膜;
34.(2)在同一个腔体内,维持该腔体温度和气压不变,在不锈钢基材表面进行金属ti
离子的注入,注入能量为0.1mev,注入时间1h,形成厚度为50nm的离子注入层;
35.(3)提高该腔体温度至600℃,充入更多氮气维持气压在0.4pa,如图1所示,样品架在氮气氛围内静置,进行热辅助扩散,在离子注入层表面形成厚度为10nm的氮化钛界面扩散层,扩散时长30min;
36.(4)将腔体冷却降温至300℃,采用磁控溅射方法制备非晶碳涂层,沉积气压0.4pa,沉积时间1h,厚度为2μm;最后在真空中冷却,即可得到本发明所述的导电耐蚀预涂层。
37.图3为实施例1中涂层后冲压成形和冲压成形后涂层的腐蚀电流密度对比;图4为实施例1中涂层后冲压成形和冲压成形后涂层的接触电阻对比。
38.实施例2
39.一种用于金属双极板成形的导电耐蚀预涂层,采用以下步骤制备:
40.(1)将不锈钢基材置于涂层沉积设备中的样品架上,腔体抽真空至低于本底真空8e
‑
3pa,开启温度至250℃,通入氩气使气压维持在0.1pa,样品架上施加
‑
700v的偏压进行清洗,除去不锈钢基材表面的杂质、油污和氧化膜;
41.(2)在同一个腔体内,维持腔体气压不变,温度升至400℃,在不锈钢基材表面进行金属ti离子和nb离子的共注入,注入能量为0.08mev,注入时间40min,形成厚度为35nm的ti/nb复合离子注入层;
42.(3)降低腔体温度至200℃,充入更多乙炔维持气压在1pa,样品在乙炔氛围内静置,进行等离子体辅助扩散,放电电压3000v,形成厚度为20nm的tic和nbc的界面扩散层,扩散时长10min;如图2所示,离子注入过程中由于离子能量的随即分散性会产生过高能量的离子,对基材表面轰击过于猛烈而产生高能离子缺陷11,缺陷形成的通路会导致腐蚀溶液渗入基材造成损伤,过低能量的离子则会附着在基材表面形成低能离子缺陷12,造成结合性能下降,界面扩散层可以填充与扩散消除上述离子注入层中的两种缺陷;
43.(4)采用磁控溅射方法制备薄贵金属ag涂层,维持腔体温度200℃,通入氩气气压0.5pa,沉积时间40min,厚度为1μm;最后在真空中冷却,即可得到本发明所述的导电耐蚀预涂层。
44.实施例3
45.一种用于金属双极板成形的导电耐蚀预涂层,采用以下步骤制备:
46.(1)将不锈钢基材置于涂层沉积设备中的样品架上,腔体抽真空至低于本底真空8e
‑
3pa,开启温度至300℃,通入氩气使气压维持在0.1pa,样品架上施加
‑
700v的偏压进行清洗,除去不锈钢基材表面的杂质、油污和氧化膜;
47.(2)维持该腔体气压不变,升高温度至500℃,在不锈钢基材表面进行非金属c离子的注入,注入能量为0.2mev,注入时间2h,形成厚度为100nm的c离子注入层;
48.(3)维持腔体温度在400℃,充入乙炔维持气压在4pa,样品在乙炔氛围内静置,进行等离子体辅助扩散,放电电压3000v,形成厚度为120nm的类石墨的界面扩散层,扩散时长20min;最后在真空中冷却,即可得到本发明所述的导电耐蚀预涂层。
49.对比例1
50.传统的金属双极板涂层作为对比例,采用以下步骤制备:
51.(1)将不锈钢基材预先冲压成形焊接成未带有涂层的不锈钢金属双极板;
52.(2)将未带有涂层的金属双极板置于涂层沉积设备中的样品架上,腔体抽真空至低于本底真空8e
‑
3pa,开启温度至200℃,通入氩气使气压维持在0.1pa,样品架上施加
‑
700v的偏压进行清洗,除去不锈钢基材表面的杂质、油污和氧化膜;
53.(3)在同一个腔体内,维持该腔体温度和气压不变,进行金属ti离子的注入,注入能量为0.1mev,注入时间30min,在表面形成离子注入层;
54.(4)提高该腔体温度至600℃,充入更多氮气维持气压在0.4pa,样品架在氮气氛围内静置,进行热辅助扩散,在离子注入层表面形成氮化钛扩散层,扩散时长20min;
55.(5)将腔体冷却降温至300℃,采用磁控溅射方法制备非晶碳涂层,沉积气压0.4pa,沉积时间1h;最后在真空中冷却,即可得到带有本发明所述的导电耐蚀预涂层的金属双极板。
56.实施例1~3涂覆了本发明所述的导电耐蚀预涂层的不锈钢板,经过薄板冲压方式形成双极板。将实施例1~3和对比例1得到的金属双极板,采用光学显微镜观察涂层表面的裂纹;采用电化学方法测试腐蚀性能,测试电位1.6v,测试时间10h;采用表面接触电阻测试评价涂层导电性能,测试压力0.6mpa,测试结果列于表1中。
57.表1实施例1~3和对比例1的测试结果
[0058] 涂层表面腐蚀电流密度(a/cm2)导电性能(mω
·
cm2)实施例1无裂纹4.5e
‑
53.8实施例2无裂纹5.4e
‑
55.1实施例3无裂纹6.0e
‑
54.0对比例1无裂纹5.2e
‑
54.2
[0059]
从表1中可以看出,实施例1~3涂覆了本发明所述的导电耐蚀预涂层的不锈钢板,在冲压形成极板之后,表面没有观察到开裂和剥离现象;且实施例1~3的涂层经过冲压成形与对比例1的先冲压后涂层的腐蚀性能和导电性能均保持一致,证明该预涂层在冲压成形过程中保持完好,通过基材预涂层工艺对于降低金属制造成本实现商业化具有重要意义。