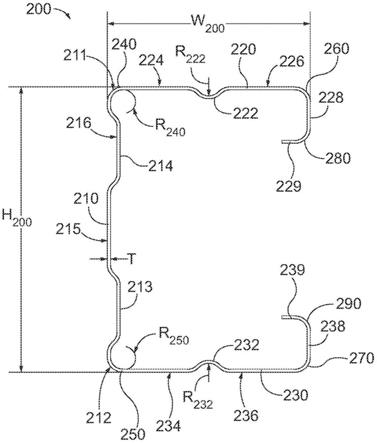
strength,low
‑
alloy,hot rolled and cold rolled with improved atmospheric corrosion resistance)。耐候钢以如下两种类型供应:类型2,其包含基于铸件或熔炼分析(热分析,heat analysis)至少0.20%铜(对于产品检查而言,最少0.18%cu);和类型4,其包含另外的合金元素以提供如通过astm g101用于评估低合金钢的耐大气腐蚀性的标准指南(standard guide for estimating the atmospheric corrosion resistance of low
‑
alloy steels)计算的至少6.0的腐蚀指数,并且提供比具有或不具有铜添加的碳钢的耐腐蚀性水平显著更好的耐腐蚀性水平。
7.在本发明之前,耐候钢典型地被限于小于700mpa的屈服强度和小于1000mpa的抗拉强度。而且,在本发明之前,耐候钢的强度性质典型地是通过时效硬化而实现的。美国专利no.10,174,398(引入本文作为参考)是通过时效硬化而实现的耐候钢的实例。
8.由于强度限制和腐蚀限制,钢例如g100或gr70钢尚不十分适合于很多产品例如诸如在太阳能装置中使用的迫进到土地中的桩或钢底座(地基,foundation)和/或高速公路行业例如诸如支承护栏、标牌等。如本文中使用的,太阳能装置为在例如设计用于供应太阳能以在电网等中使用的光伏发电站的太阳能农场(solar farm)上支承太阳能电池的结构体。地下水和土壤组成物的腐蚀性质要求远超2.5mm的材料厚度以维持对于这些结构部件所需的完整性。因此,热浸镀锌钢转而用于这样的用途。为改善下面的材料性质的耐腐蚀性将热浸镀锌钢涂覆锌。因此,对于结构桩依赖于由镀锌的50ksi w6或w8工字梁钢设计的桩一直是太阳能行业的惯例。然而,锌涂层负面地与地下水和土壤组成物反应,造成污染其的可能。锌涂层还只提供有限的保护程度。一旦锌氧化使锌涂层劣化,金属氧化就仍然开始使下面的材料的结构完整性劣化和/或需要增大的材料厚度来维持对于这些结构部件所需的完整性。
技术实现要素:9.因此,本公开着手于提供由替代桩或钢底座所依赖的现有材料的轻型超高强度耐候钢制造的桩或钢底座设计。具体地,本公开着手于提供具有由薄铸金属带制造的成型体(shape)的轻量型桩或钢底座。本公开的成型体着手于增大桩或钢底座的强度和耐久性以经受住由为将结构部件迫进到土地中所需要的力而产生的形变和/或以充当用于地上的外部结构体例如诸如太阳能装置、护栏、标牌等的结构部件。具体地,本公开着手于提供由具有2.5mm或更小、2.0mm或更小、或1.6mm或更小的厚度的薄铸钢带冷轧形成的桩或钢底座或,者作为材料厚度为2.5mm或更小、2.0mm或更小、或1.6mm或更小的薄铸钢成型体铸造的桩或钢底座。所述桩或钢底座由已经使用一个或多个轧机机架(辊机架,roll stand)冷轧形成的薄铸钢带制造。另外,还可依赖于冲床系统、cnc等离子体系统和/或轧机系统等提供通孔、槽孔和/或点焊头,如下面指出的。本公开还着手于提供由薄铸钢带冷轧形成的桩或钢底座,其不需要如在热浸镀锌结构部件上设置的单独施加的保护性涂层例如诸如锌涂层。如本文中使用的,单独施加的涂层为独立于钢组成的保护性涂层,其可为表面保护剂。这样的单独施加的保护性涂层的实例包括锌涂层、镀锌(电镀,galvanized)涂层(例如热浸镀锌涂层)、铝
‑
硅耐腐蚀涂层等。更重要地,本公开的桩或钢底座在没有借助于单独施加的涂层的情况下产生耐腐蚀性,如下文阐述的。固有地,按照定义,本文中公开的超高强度耐候钢具备必不可少的否则将依赖于热浸镀锌的耐腐蚀性。从而,本公开的耐候钢将不需要
或不具备锌涂层、热浸镀锌涂层等,其也将不施加这样的涂层。
10.在一组实例中,本公开内容着手于提供通过将包晶点转移成远离碳区域和/或提高组合物的包晶点的转变温度而形成的轻型超高强度耐候钢。具体地,将包晶点转移成远离碳区域和/或提高组合物的包晶点的转变温度似乎抑制缺陷并且导致无缺陷的高强度马氏体钢板。在本实例中,为此依赖于镍的添加,其中镍的添加必须足以将
‘
包晶点’转移成远离否则将存在于未添加镍的相同组合物中的碳区域。还公开由超高强度耐候钢制成的如下产品:其为各种形状的(如本文中另外公开),并且具有以前不可获得的改善的强度性质。
11.在另一组实例中,本公开内容着手于消除原奥氏体晶界凹坑,但维持抹平(模糊,抹光,smear)图案。在本组实例中,薄铸钢带经历高摩擦轧制条件,其中晶界凹坑在至少薄铸钢带表面处形成抹平图案。具体地,本实例着手于在从表面消除原奥氏体晶界凹坑且改善钢带或钢产品的成形性时形成原奥氏体晶界凹坑的抹平图案。通过改善钢带的成形性,以前不可获得的具有各种形状的(如本文中另外公开的)并且具有改善的强度性质的产品变为可获得的。本实例不仅适用于前述的超高强度耐候钢,而且可另外适用于马氏体钢、其它耐候钢、和/或呈现原奥氏体晶界凹坑的钢带或产品。
12.然而此外,在另一组实例中,本公开内容着手于消除晶界凹坑和由其形成的抹平图案。在本组实例中,薄铸钢带经历表面均匀化,从而消除抹平图案。结果,薄铸钢带具有不仅不含原奥氏体晶界凹坑而且另外不含作为高摩擦轧制条件的结果产生的抹平图案的表面,以在一些实例中提供具有不超过2.5μm的表面粗糙度(ra)的薄铸钢带表面。本实例不仅适用于前述的超高强度耐候钢,而且可另外适用于马氏体钢、其它耐候钢、和/或呈现原奥氏体晶界凹坑的钢带或产品。
13.超高强度耐候钢
14.首先,当前公开了通过包括如下的步骤制成的轻型超高强度耐候钢板:(a)准备熔融钢熔体,其包括:(i)以重量计,0.20%和0.35%之间的碳、小于1.0%的铬、0.7%和2.0%之间的锰、0.10%和0.50%之间的硅、0.1%和1.0%之间的铜、小于或等于0.12%的铌、小于0.5%的钼、0.5%和1.5%之间的镍,且为含有小于0.01%铝的硅镇静的,以及(ii)余量为铁和由熔炼产生的杂质;(b)以大于10.0mw/m2的热通量凝固成厚度小于或等于2.5mm的钢板并且将所述板在快速冷却前和/或当热轧时在热轧前在非氧化气氛中以大于15℃/s的冷却速率冷却到1080℃以下且ar3温度以上;和(c)快速冷却以形成具有拥有以体积计至少75%马氏体的微观结构、700和1600mpa之间的屈服强度、1000和2100mpa之间的抗拉强度以及1%和10%之间的伸长率的钢板。
15.此处和在本公开内容中的其它地方,伸长率意指总伸长率。“快速冷却”意指以大于100℃/s的速率冷却到100和200℃之间。快速冷却添加有镍的本发明组合物实现最高达大于95%马氏体相的钢带。在一个实例中,快速冷却形成具有拥有以体积计至少95%马氏体的微观结构的钢板。镍的添加必须足以将
‘
包晶点’转移成远离否则在未添加镍的相同组合物中将存在的碳区域。具体地,据认为,在组合物中包含镍有助于将包晶点转移成远离碳区域和/或提高该组合物的包晶点的转变温度,这似乎抑制缺陷并导致无缺陷的高强度马氏体钢板。在一个实例中,还可将轻型超高强度耐候钢板在快速冷却前热轧到在15%和50%之间压下率。
16.本发明钢板中的碳水平优选地不在0.20%以下以抑制钢板的包晶开裂。提供镍的
添加以进一步抑制钢板的包晶开裂,但这样做与依赖于单独的碳组成无关。镍对腐蚀指数的影响体现在用于确定腐蚀指数计算结果的以下方程式中:cu*26.01+ni*3.88+cr*1.2+si*1.49+p*17.28
–
cu*ni*7.29
–
ni*p*9.1
–
cu*cu*33.39(其中各元素以重量百分数计)。
17.可将该熔融熔体以大于10.0mw/m2的热通量凝固成厚度小于2.5mm的钢板,并且可将该板在快速冷却前和/或当热轧时在热轧前在非氧化气氛中以大于15℃/s的冷却速率冷却到1080℃以下且ar3温度以上。非氧化气氛为典型地惰性气体例如氮气或氩气或其混合物的气氛,其包含以重量计小于约5%氧气。在另一实例中,可将所述板在快速冷却前和/或当热轧时在热轧前在非氧化气氛中以大于15℃/s的冷却速率冷却到1100℃以下且ar3温度以上。
18.在一些实例中,钢板中的马氏体可由晶粒尺寸大于100μm的奥氏体形成。在其它实例中,钢板中的马氏体可由晶粒尺寸大于150μm的奥氏体形成。
19.将钢板快速冷却以形成具有拥有至少75%马氏体的微观结构、700和1600mpa之间的屈服强度、1000和2100mpa之间的抗拉强度以及1%和10%之间的伸长率的钢板。在其它实例中,将钢板快速冷却以形成具有拥有至少75%的马氏体加贝氏体的微观结构的钢板。在一个具体实例中,快速冷却形成具有拥有以体积计至少95%马氏体加贝氏体的微观结构的钢板。
20.在一些实例中,可将钢板在快速冷却前热轧到15%和35%之间压下率。在其它实例中,可将钢板在快速冷却前热轧到15%和50%之间压下率。
21.用于制造超高强度耐候钢板的熔融钢为硅镇静的(即经硅脱氧的),其包括以重量计0.10%和0.50%之间的硅。钢板可进一步包括以重量计小于0.008%铝或小于0.006%铝。该熔融熔体可具有5
‑
70ppm之间或5
‑
60ppm之间的游离氧含量。钢板可具有大于50ppm的总氧含量。夹杂物包括典型地其中50%为小于5μm尺寸的mnosio2并且具有增强微观结构演变(evolution)和由此的带机械性质的潜力。
22.还公开了轻型超高强度耐候钢板的制造方法,其包括如下步骤:(a)准备熔融钢熔体,其包括:(i)以重量计,0.20%和0.35%之间的碳、小于1.0%的铬、0.7%和2.0%之间的锰、0.10%和0.50%之间的硅、0.1%和1.0%之间的铜、小于0.12%的铌、小于0.5%的钼、0.5%和1.5%之间的镍,且为含有小于0.01%铝的硅镇静的,以及(ii)余量为铁和由熔炼产生的杂质;(b)将该熔融熔体形成为被支承在其间具有夹区的一对经冷却的铸造辊的铸造表面上的铸造池;(c)使铸造辊反向旋转且以大于10.0mw/m2的热通量凝固,从而产生厚度小于2.5mm的钢板,和将所述板在快速冷却前和/或当热轧时在热轧前在非氧化气氛中以大于15℃/s的冷却速率冷却到1080℃以下且ar3温度以上,和(d)快速冷却以形成具有拥有至少75%马氏体的微观结构、700和1600mpa之间的屈服强度、1000和2100mpa之间的抗拉强度以及1%和10%之间的伸长率的钢板。在一个具体实例中,快速冷却形成具有拥有以体积计至少95%马氏体加贝氏体的微观结构的钢板。可将所述板在快速冷却前和/或当热轧时在热轧前在非氧化气氛中以大于15℃/s的冷却速率冷却到1100℃以下且ar3温度以上。钢板组合物不能被制成具有低于0.20%的碳水平,因为其对于钢板的包晶开裂不起作用。在一个实例中,可将轻型超高强度耐候钢板在快速冷却前热轧至15%和50%之间压下率。
23.进一步地,轻型超高强度耐候钢板的制造方法可包括将钢板在150℃和250℃之间的温度回火2
‑
6小时的步骤。
24.该熔融熔体可具有5
‑
70ppm之间或5
‑
60ppm之间的游离氧含量。钢板可具有大于50ppm的总氧含量。可将该熔融熔体以大于10.0mw/m2的热通量凝固成厚度小于2.5mm的钢板,并且在快速冷却前和/或当热轧时在热轧前在非氧化气氛中以大于15℃/s的冷却速率冷却至1080℃以下且ar3温度以上。在另一实例中,可将所述板在快速冷却前和/或当热轧时在热轧前在非氧化气氛中以大于15℃/s的冷却速率冷却至1100℃以下且ar3温度以上。
25.在一些实施方式中,钢板中的马氏体可来自于晶粒尺寸大于100μm的奥氏体。在其它实施方式中,钢板中的马氏体可来自于晶粒尺寸大于150μm的奥氏体。
26.轻型超高强度耐候钢板的制造方法可进一步包括将钢板热轧至15%和35%之间压下率,并且之后快速冷却以形成具有拥有至少75体积%马氏体的微观结构、700和1600mpa之间的屈服强度、1000和2100mpa之间的抗拉强度以及1%和10%之间的伸长率的钢板。在一些实施方式中,轻型超高强度钢板的制造方法可进一步包括将钢板热轧至15%和50%之间压下率,并且之后快速冷却以形成具有拥有至少75体积%马氏体加贝氏体的微观结构、700和1600mpa之间的屈服强度、1000和2100mpa之间的抗拉强度以及1%和10%之间的伸长率的钢板。此外,热轧的轻型超高强度钢板的制造方法可包括将钢板热轧至15%和35%之间压下率,并且之后快速冷却以形成具有拥有至少75体积%马氏体加贝氏体的微观结构、700和1600mpa之间的屈服强度、1000和2100mpa之间的抗拉强度以及1%和10%之间的伸长率的钢板。在上面的具体实例中,热轧钢板并且之后快速冷却形成具有拥有以体积计至少95%马氏体加贝氏体的微观结构的钢板。
27.还公开了包括由具有如下组成的碳合金钢板冷轧形成的一个或多个凸缘(flange)和腹板(web)的钢桩:其包括以重量计0.20%和0.35%之间的碳、小于1.0%的铬、0.7%和2.0%之间的锰、0.10%和0.50%之间的硅、0.1%和1.0%之间的铜、小于或等于0.12%的铌、小于0.5%的钼、0.5%和1.5%之间的镍,且为含有小于0.01%铝的硅镇静的,其中所述碳合金钢板具有拥有至少75体积%马氏体或马氏体加贝氏体的微观结构、700和1600mpa之间的屈服强度、1000和2100mpa之间的抗拉强度、1%和10%之间的伸长率、并且具有6.0或更大的腐蚀指数。
28.高摩擦轧制的高强度耐候钢
29.第二,在一组实例中,当前公开了具有小于或等于2.5mm的铸态(as cast)厚度的碳合金薄铸钢带。这些实例不仅适用于前述的超高强度耐候钢,而且可另外适用于马氏体钢、其它耐候钢、和/或呈现原奥氏体晶界凹坑的钢带或产品。碳合金薄铸钢带可包括以重量计0.20%和0.40%之间的碳、小于1.0%的铬、0.7%和2.0%之间的锰、0.10%和0.50%之间的硅、0.1%和1.0%之间的铜、小于或等于0.12%的铌、小于0.5%的钼、0.5%和1.5%之间的镍,且为含有小于0.01%铝的硅镇静的,以及余量为铁和由熔炼产生的杂质。在高摩擦热轧后,碳合金薄铸钢带的厚度减少铸态厚度的15%
‑
50%。热轧的钢带包括主要不含、基本上不含或不含原奥氏体晶界凹坑且具有抹平图案的一对相反的高摩擦热轧的表面。在一些实施方式中,钢带包括具有以体积计至少75%马氏体或至少75%马氏体加贝氏体的微观结构、700和1600mpa之间的屈服强度、1000和2100mpa之间的抗拉强度、以及1%和10%之间的伸长率。在一些实例中,钢带为具有6.0或更大的腐蚀指数的耐候钢。
30.在一些实例中,该对相反的高摩擦热轧的表面基本上不含原奥氏体晶界凹坑。在一些实例中,该对相反的高摩擦热轧的表面主要不含原奥氏体晶界凹坑。
31.还公开了热轧的碳合金钢带的制造方法,该热轧的碳合金钢带包括以重量计0.20%和0.40%之间的碳、小于1.0%的铬、0.7%和2.0%之间的锰、0.10%和0.50%之间的硅、0.1%和1.0%之间的铜、小于或等于0.12%的铌、小于0.5%的钼、0.5%和1.5%之间的镍,且为含有小于0.01%铝的硅镇静的,以及余量为铁和由熔炼产生的杂质,所述方法包括如下步骤:
32.(a)准备熔融钢熔体;
33.(b)将熔体形成为被支承在其间具有夹区的一对经冷却的铸造辊的铸造表面上的铸造池;
34.(c)使所述铸造辊反向旋转并且将熔融熔体以大于10.0mw/m2的热通量凝固成从夹区向下输送的厚度小于或等于2.5mm的钢带,和将所述带在非氧化气氛中以大于15℃/s的冷却速率冷却到1080℃以下且ar3温度以上;
35.(d)将薄铸钢带高摩擦热轧到铸态厚度的15%和50%之间压下率的热轧厚度,产生主要不含、基本上不含或不含原奥氏体晶界凹坑且具有抹平图案的热轧钢带。
36.主要不含、基本上不含或不含原奥氏体晶界凹坑且具有抹平图案的高摩擦热轧的薄铸钢带可为具有6.0或更大的腐蚀指数的耐候钢。而且,高摩擦热轧的钢带可包括具有以体积计至少75%马氏体或至少75%马氏体加贝氏体的微观结构、700和1600mpa之间的屈服强度、1000和2100mpa之间的抗拉强度、以及1%和10%之间的伸长率。
37.高摩擦轧制的高强度马氏体钢
38.第三,在又一组实例中,当前公开了碳合金薄铸钢带,其包括在已经高摩擦轧制时已经被表面均匀化的一对相反的高摩擦热轧的表面。这些本发明实例不仅适用于前述的超高强度耐候钢,而且可另外适用于马氏体钢、其它耐候钢、和/或呈现原奥氏体晶界凹坑的钢带或产品。在被表面均匀化时,该对相反的高摩擦热轧的表面不含作为高摩擦轧制过程的结果而先前形成的抹平(模糊,抹光,smear)的晶界凹坑。在一些实施方式中,碳合金薄铸钢带可进一步包括具有以体积计至少75%马氏体或至少75%马氏体加贝氏体的微观结构以及700和1600mpa之间的屈服强度、1000和2100mpa之间的抗拉强度、以及1%和10%之间的伸长率。在一些实施方式中,钢带包括具有以体积计至少90%马氏体或至少90%马氏体加贝氏体的微观结构。在一些实施方式中,权利要求1的钢带包括具有以体积计至少95%马氏体或至少95%马氏体加贝氏体的微观结构。
39.在本公开内容范围内的示例性的均匀化钢带可包括以重量计0.20%和0.40%之间的碳、小于1.0%的铬、0.7%和2.0%之间的锰、0.10%和0.50%之间的硅、0.1%和1.0%之间的铜、小于或等于0.12%的铌、小于0.5%的钼、0.5%和1.5%之间的镍,且为含有小于0.01%铝的硅镇静的,和余量为铁和由熔炼产生的杂质。
40.还公开了热轧的碳合金钢带的制造方法。该方法可包括如下步骤:
41.(a)准备熔融钢熔体;
42.(b)将熔体形成为被支承在其间具有夹区的一对经冷却的铸造辊的铸造表面上的铸造池;
43.(c)使所述铸造辊反向旋转并且将熔融熔体以大于10.0mw/m2的热通量凝固成从夹区向下输送的厚度小于或等于2.5mm的钢带,和将所述带在非氧化气氛中以大于15℃/s的冷却速率冷却到1080℃以下且ar3温度以上;
44.(d)将薄铸钢带高摩擦轧制至铸态厚度的15%和50%之间压下率的热轧厚度,产生不含原奥氏体晶界凹坑且具有抹平图案的热轧钢带;和
45.(e)将高摩擦热轧的钢带进行表面均匀化以消除抹平图案。
46.高摩擦热轧的均匀化的薄铸钢带可包括具有以体积计至少75%马氏体或至少75%马氏体加贝氏体的微观结构、700和1600mpa之间的屈服强度、1000和2100mpa之间的抗拉强度、以及1%和10%之间的伸长率,从而提供高强度马氏体钢。进一步地,高摩擦热轧的均匀化的钢带可包括以重量计0.20%和0.40%之间的碳、小于1.0%的铬、0.7%和2.0%之间的锰、0.10%和0.50%之间的硅、0.1%和1.0%之间的铜、小于或等于0.12%的铌、小于0.5%的钼、0.5%和1.5%之间的镍,且为含有小于0.01%铝的硅镇静的,以及余量为铁和由熔炼产生的杂质。
47.本公开进一步阐述超高强度耐候钢桩可如何依赖于如所描述的薄铸钢带、以上组成和/或以上性质的每一者。具体地,在一个实例中,超高强度耐候钢桩包括多个侧壁,各侧壁具有约2.5mm或更小、2.0mm或更小、或1.6mm或更小的厚度。所述桩可由钢带形成。具体地,所述桩可由铸态钢带形成。所述桩可由热轧的铸态钢带形成。而且,所述桩可冷轧形成。所述桩可具有包括如下的组成:以重量计,0.20%和0.35%之间的碳、少于1.0%的铬、0.7%和2.0%之间的锰、0.10%和0.50%之间的硅、0.1%和1.0%之间的铜、少于或等于0.12%的铌、少于0.5%的钼、0.5%和1.5%之间的镍,且为含有小于0.01%铝的硅镇静的,以及余量为铁和由熔炼产生的杂质。所述桩可进一步包括或具有6.0或更大的腐蚀指数、700和1600mpa之间的屈服强度、1000和2100mpa之间的抗拉强度、和/或1%和10%之间的伸长率。
48.在一些实例中,桩的组成包括足以将包晶点转移成远离碳区域和/或提高包晶点的转变温度以形成具有至少75体积%马氏体或马氏体加贝氏体的微观结构的碳合金钢带的量的镍。在一些实例中,桩可由钢带形成,其中将钢带的铸态厚度热轧成具有铸态厚度的15%和50%之间压下率的热轧厚度。可将热轧的材料高摩擦轧制以提供高摩擦轧制的厚度。
49.本文中进一步描述超高强度耐候钢的多个特征和形状。这些特征可以组合或彼此独立地提供。在一些实例中,超高强度耐候钢桩可为c槽形(槽钢,channel),其中多个侧壁为腹板和一个或多个凸缘。更具体地,超高强度耐候钢桩可为卷边c槽形和/或波纹c槽形,其中多个侧壁为腹板和一个或多个凸缘。在一些实例中,超高强度耐候钢桩可为管,其中多个侧壁形成管。更具体地,超高强度耐候钢桩可为正方形管或矩形管。此外,超高强度耐候钢桩可为总体上正方形管或矩形管,其中多个侧壁的一个或多个进一步包括一个或多个波纹。所述多个侧壁不包括单独施加的涂层。所述多个侧壁为未镀锌的。所述多个侧壁的至少一个侧壁可为卷边。更具体地,卷边c槽形的一个或多个凸缘可为单卷边。一个或多个凸缘的各单卷边的第一层和第二层可通过一个或多个点焊头固定(紧固)在一起。一个或多个凸缘的第一层可通过泪滴状转接头(转接,transition)而转接到第二层。另外地或替代地,所述多个侧壁的至少一个可包括一个或多个波纹。在一些实例中,c槽形的腹板可包括一个或多个波纹。另外地或替代地,c槽形的一个或多个凸缘可包括一个或多个波纹。
50.在一些实例中,超高强度耐候钢桩包括约2.5mm或更小、2.0mm或更小、或1.6mm或更小的厚度。桩可由薄铸钢带形成,所述薄铸钢带被冷轧形成为具有多个侧壁的腐蚀指数
为6.0或更大的钢桩。超高强度耐候钢桩可进一步包括700和1600mpa之间的屈服强度、1000和2100mpa之间的抗拉强度、以及1%和10%之间的伸长率。超高强度耐候钢桩的组成可包括足以将包晶点转移成远离碳区域和/或提高包晶点的转变温度以形成具有至少75体积%马氏体或马氏体加贝氏体的微观结构的碳合金钢带的量的镍。在一种实例中,超高强度耐候钢桩具有包括如下的材料组成:以重量计,0.20%和0.35%之间的碳、少于1.0%的铬、0.7%和2.0%之间的锰、0.10%和0.50%之间的硅、0.1%和1.0%之间的铜、少于或等于0.12%的铌、少于0.5%的钼、0.5%和1.5%之间的镍,且为含有小于0.01%铝的硅镇静的,以及余量为铁和由熔炼产生的杂质。
51.本文中还讨论太阳能装置。所述太阳能装置可包括超高强度耐候钢桩,其包括多个侧壁,各侧壁具有约2.5mm或更小、2.0mm或更小、或1.6mm或更小的厚度。太阳能装置的超高强度耐候钢桩可包括以重量计0.20%和0.35%之间的碳、少于1.0%的铬、0.7%和2.0%之间的锰、0.10%和0.50%之间的硅、0.1%和1.0%之间的铜、少于或等于0.12%的铌、少于0.5%的钼、0.5%和1.5%之间的镍,且为含有小于0.01%铝的硅镇静的,以及余量为铁和由熔炼产生的杂质。所述太阳能装置的超高强度耐候钢桩可包括700和1600mpa之间的屈服强度、1000和2100mpa之间的抗拉强度、以及1%和10%之间的伸长率。在该实例中,超高强度耐候钢桩的部分长度迫进到地面中并且一个或多个太阳能电池通过超高强度耐候钢桩支承在地面上方。因此,太阳能装置的超高强度耐候钢桩可另外地或替代地具有如上文和在本公开的其余部分中描述的很多特征。
附图说明
52.可参考附图更充分地说明和解释本发明,在图中:
53.图1说明引入线上热轧机和卷取机的带铸造设备。
54.图2说明双辊带铸造机的细节。
55.图3为具有拥有至少75%马氏体的微观结构的钢板的显微照片。
56.图4为说明镍将包晶点转移成远离碳区域的效果的相图。
57.图5为根据本公开内容的一个或多个方面的工艺的流程图。
58.图6为显示在表面均匀化过程之后的经高摩擦条件热轧的钢带表面的图像。
59.图7为显示尚未均匀化的具有抹平图案的经高摩擦条件热轧的钢带表面的图像。
60.图8是为了对于特定的一对工作辊、轧机比力和相应的压下率测定摩擦系数而制作的摩擦系数模型图表。
61.图9为钢的连续冷却转变(cct)图。
62.图10为由根据本公开的一个或多个方面的薄铸钢带冷轧形成的桩或钢底座的卷边c槽形成型体的横截面。
63.图11为由根据本公开的一个或多个方面的薄铸钢带冷轧形成的图10的桩或钢底座的透视图。
64.图12为由根据本公开的一个或多个方面的薄铸钢带冷轧形成的桩或钢底座的波纹c槽形成型体的横截面。
65.图13为由根据本公开的一个或多个方面的薄铸钢带冷轧形成的桩或钢底座的波纹c槽形成型体的横截面。
66.图14为由根据本公开的一个或多个方面的薄铸钢带冷轧形成的钢桩或钢底座的具有刚性部件的正方形管的横截面。
67.图15为由根据本公开的一个或多个方面的薄铸钢带冷轧形成的钢桩或钢底座的具有刚性部件的矩形管的横截面。
68.图16为说明具有其代表性图像的现有技术的热浸镀锌(g324)钢材料的测试结果的图示。
69.图17为说明具有其代表性图像的现有技术的(g100)钢材料的测试结果的图示。
70.图18为说明具有其代表性图像的现有技术的(gr70)钢材料的测试结果的图示。
71.图19为说明本公开的轻型超高强度耐候钢桩材料的测试结果的图示。
具体实施方式
72.在本文中在一个实例中描述了轻型超高强度耐候钢板。轻型超高强度耐候钢板可由熔融熔体制成。可将该熔融熔体通过双辊铸造机加工。在一个实例中,轻型超高强度耐候钢板可通过包括如下的步骤制成:(a)准备熔融钢熔体,其包括:(i)以重量计,0.20%和0.35%之间的碳、小于1.0%的铬、0.7%和2.0%之间的锰、0.10%和0.50%之间的硅、0.1%和1.0%之间的铜、小于或等于0.12%的铌、小于0.5%的钼、0.5%和1.5%之间的镍,且为含有小于0.01%铝的硅镇静的,和(ii)余量为铁和由熔炼产生的杂质;(b)以大于10.0mw/m2的热通量凝固,从而产生厚度小于2.5mm的钢板,并且在快速冷却前和/或当热轧时在热轧前在非氧化气氛中以大于15℃/s的冷却速率冷却到1080℃以下且ar3温度以上;和(c)快速冷却以形成钢板,其具有拥有至少75体积%马氏体或马氏体加贝氏体的微观结构、700和1600mpa之间的屈服强度、1000和2100mpa之间的抗拉强度、以及1%和10%之间的伸长率。在一个实例中,还可将轻型超高强度耐候钢板在快速冷却前热轧至15%和50%之间压下率。可将所述板在快速冷却前和/或当热轧时在热轧前在非氧化气氛中以大于15℃/s的冷却速率冷却至1100℃以下且ar3温度以上。ar3温度为在冷却期间奥氏体开始转变为铁素体的温度。也就是说,ar3温度为奥氏体转变点。在各实例中,镍将包晶点转移成远离碳区域和/或提高钢板组合物的包晶点的转变温度以提供无缺陷的钢板。镍对腐蚀指数的影响体现在用于确定腐蚀指数计算结果的以下方程式中:cu*26.01+ni*3.88+cr*1.2+si*1.49+p*17.28
–
cu*ni*7.29
–
ni*p*9.1
–
cu*cu*33.39(其中各元素以重量百分数计)。
73.本文中还描述具有如下的热轧的外部侧表面的薄铸钢带:所述外部侧表面的特征在于主要不含、基本上不含或不含原奥氏体晶界凹坑但具有抹平、或伸长的表面结构,例如在高摩擦轧制高强度马氏体钢的实例中。本文中还描述用于制造其的方法或工艺。这些实例不仅适用于前述的超高强度耐候钢,而且可另外适用于马氏体钢、其它耐候钢、和/或呈现原奥氏体晶界凹坑的钢带或产品。
74.本文中进一步描述具有如下的热轧的外部侧表面的薄钢带:所述外部侧表面的特征在于主要不含、基本上不含或不含原奥氏体晶界凹坑并且不含抹平、或伸长的表面结构,例如在高摩擦轧制高强度耐候钢的实例中。本文中还描述用于制造其的方法或工艺。这些实例不仅适用于前述的超高强度耐候钢,而且可另外适用于马氏体钢、其它耐候钢、和/或具有原奥氏体晶界凹坑的钢带或产品。
75.如本文中使用的,主要不含意指各相反的热轧的外部侧表面的小于50%包含原奥
氏体晶界或酸蚀刻(酸洗)后的原奥氏体晶界凹坑。至少基本上不含所有的原奥氏体晶界或原奥氏体晶界凹坑意指各相反的热轧的外部侧表面的10%或更小包含原奥氏体晶界凹坑或酸蚀刻(酸洗)后的原奥氏体晶界凹坑。所述凹坑在酸蚀刻(也称为酸洗)后形成蚀刻的晶界凹坑而使得原奥氏体晶界在250x放大倍率下可见。在其它情形中,不含意味着各相反的热轧的外部侧表面不含(也就是完全没有)原奥氏体晶界凹坑,其包括在酸蚀刻后不含任何原奥氏体晶界凹坑。强调的是,原奥氏体晶界可仍旧在热轧后的带的材料内存在,其中表面上的晶界凹坑和间隔已经通过本文中描述的技术(例如其中热轧在a
r3
温度以上的温度下使用等于或大于0.20的辊缝摩擦系数发生)的方式除去。
76.图1和图2说明用于连续铸造本发明的钢带或钢板的带铸造机的相继部件。双辊铸造机11可连续产生铸造钢带12,其在运输路径10中穿过导向台13传送至具有夹送辊14a的夹送辊机架14。所述带在离开夹送辊机架14后立即传送到具有一对工作辊16a和背辊16b的热轧机16中,在热轧机16中将铸带热轧以压下期望的厚度。热轧的带传送到输出辊道17上,其中带进入经由水射流18(或其它适合手段)的强烈冷却部分。经轧制和冷却的带然后传送通过包括一对夹送辊20a的夹送辊机架20和然后至卷取机19。
77.如图2中显示,双辊铸造机11包括主机框架21,其支承一对横向定位的具有铸造表面22a的铸造辊22。将熔融金属在铸造操作期间从盛钢桶(未显示)供应到中间包23、通过耐火砖套(shroud)24至分配器或可活动中间包25、和然后从分配器或可活动中间包25通过金属输送嘴26至铸造辊22之间在夹区27上方。输送至铸造辊22之间的熔融金属形成在夹区上方的被支承在铸造辊上的铸造池30。铸造池30在铸造辊的端部处通过一对侧封坝或板28约束,所述侧封坝或板28可通过包括连接至侧板保持器的液压缸单元(未显示)的一对推进器(未显示)而被推靠着铸造辊端部。铸造池30的上表面(通常称为“弯液面”型液面)通常在输送嘴下端的上方,使得输送嘴下端浸没在铸造池30内。将铸造辊22以内部方式进行水冷却,使得壳当其传送通过铸造池时凝固在移动的铸造辊表面上,并且在它们之间在夹区27处被组合在一起以产生铸造带12,其从在铸造辊之间的夹区向下输送。
78.双辊铸造机可为在美国专利no.5,184,668、5,277,243、5,488,988和/或作为美国公布no.2009/0236068a1公布的美国专利申请no.12/050,987中相当详细地说明和描述的类型。对于可在本发明实例中使用的双辊铸造机的适当构造细节,参考这些专利和公布,将其引入作为参考。
79.在使用任何期望的工艺、例如以上结合图1和图2描述的带铸造工艺形成(铸造)薄钢带后,可将所述带热轧和冷却以形成具有至少主要不含、基本上不含或不含原奥氏体晶界凹坑的相反的热轧的外部侧表面的期望的薄钢带。如图1中说明的,线上热轧机16提供来自铸造机的带的15%至50%压下率。在输出辊道17上,冷却可包括用于控制奥氏体转变的冷却速率以实现期望的微观结构和材料性质的水冷却部分。
80.图3显示具有拥有来自晶粒尺寸为至少100μm的原奥氏体的至少75%马氏体的微观结构的钢板的显微照片。在一些实例中,将钢板快速冷却以形成具有拥有至少90体积%马氏体或马氏体和贝氏体的微观结构的钢板。在另一实例中,将钢板快速冷却以形成具有拥有至少95体积%马氏体或马氏体和贝氏体的微观结构的钢板。在这些实例的每个中,可另外地在快速冷却前将钢板热轧至15%和50%之间压下率。
81.重新参考图1,说明热箱15。如图1显示的,在带已经形成后,其可传送到环境受控
的箱(称为热箱15)中,其中其在通过热轧机16热轧成其最终规格前继续被动冷却。维持具有保护性气氛的环境受控的箱直至进入到热轧机16中。在热箱内,使带在导向台13上移动到夹送辊机架14。在本公开内容的实例中,不期望的热蚀刻可在热箱15中发生。基于热蚀刻是否已经在热箱中发生,带可在基于下面更详细地限定的参数的高摩擦轧制条件下热轧。
82.在特定情形中,形成薄钢带的方法进一步包括使用一对反向的工作辊热轧薄钢带,所述工作辊产生足以产生薄钢带的如下的相反的热轧的外部侧表面的增高的摩擦系数(μ):所述外部侧表面的特征在于主要不含、基本上不含或不含原奥氏体晶界凹坑,并且特征在于具有与在剪切下通过塑性形变形成的表面抹平图案相关的伸长的表面结构。在某些情况下,这对反向的工作辊在a
r3
温度以上的温度下产生等于或大于0.20、0.25、0.268或0.27的摩擦系数(μ),其各自在使用或不使用润滑的情况下产生。认识到,摩擦系数可通过增大工作辊表面的表面粗糙度、消除任何润滑的使用、减少使用的润滑的量和/或选择使用特定类型的润滑而增大。除先前描述的机制外还可另外地或单独地使用如可为普通技术人员所知晓的用于增大摩擦系数的其它机制。以上工艺在本文中通常称为高摩擦轧制。
83.如以上提到的,认识到高摩擦轧制可通过增大一个或多个工作辊的表面的表面粗糙度而实现。这在本文中通常称为工作辊表面织构化。工作辊表面织构化可通过在高摩擦轧制应用中使用的各种参数而改变和测量。例如,工作辊轮廓的平均粗糙度(ra)可提供用于产生对于如以上在实例中指出的辊缝必不可少的摩擦系数的基准点。为通过工作辊表面织构化的方式实现高摩擦轧制,在一个实例中,新磨削和织构化的工作辊可具有在2.5μm和7.0μm之间的ra。新磨削和织构化的工作辊在本文中更通常地称为新工作辊。在具体实例中,新工作辊可具有3.18μm和4.0μm之间的ra。新工作辊的平均粗糙度可在使用期间或在磨损时减小。因此,也可依赖于用过的工作辊来产生上述的高摩擦轧制条件,只要用过的工作辊具有在一个实例中的2.0μm和4.0μm之间的ra。在具体实例中,用过的工作辊可具有1.74μm和3.0μm之间的ra,同时仍然实现上述的高摩擦轧制条件。
84.另外地或替代地,还可依赖于工作辊轮廓的平均表面粗糙度深度(rz)作为实现上述高摩擦轧制条件的标识符。新工作辊可具有20μm和41μm之间的rz。在一个具体实例中,新工作辊可具有21.90μm和28.32μm之间的rz。在一个实例中对于上述的高摩擦轧制条件可依赖于用过的工作辊,只要其在停止服务前维持10μm和20μm之间的rz。在一个具体实例中,用过的工作辊在停止服务前具有13.90μm和20.16μm之间的rz。
85.然而此外,以上参数可进一步由在轮廓各处的峰间的平均间距(sm)定义。为产生高摩擦轧制条件而依赖的新工作辊可包括90μm和150μm之间的sm。在一个具体实例中,为产生高摩擦轧制条件而依赖的新工作辊包括96μm和141μm之间的sm。在一个实例中对于上述的高摩擦轧制条件可依赖于用过的工作辊,只要其维持115μm和165μm之间的sm。
86.下表1说明为产生高摩擦轧制条件而依赖的工作辊表面织构化的随工作辊上的位置测量的测试数据,并且进一步提供新工作辊参数和在用过的工作辊将要停止服务前的用过的工作辊参数之间的比较:
[0087][0088][0089][0090]
*“os qtr”为操作人员侧四分之一区;且“avg”为平均值
[0091]
**“ctr”为带中央;且“avg”为平均值
[0092]
***“ds qtr”为驱动侧四分之一区;且“avg”为平均值
[0093]
确定高摩擦轧制是否适用于本公开内容的实例可取决于热蚀刻是否已经在热箱中发生。热蚀刻为将钢带表面处的原奥氏体晶界凹坑暴露的铸造工艺的副作用或后果。如以上指出的,原奥氏体晶界凹坑可易于在进一步酸蚀刻时导致沿着蚀刻的原奥氏体晶界凹坑的前述缺陷现象。具体地,当钢在惰性气氛中暴露于高温例如热箱时,热蚀刻通过在原奥氏体晶界凹坑和表面之间的交叉处形成凹槽而显露钢带中的原奥氏体晶界凹坑。这些凹槽使得原奥氏体晶界凹坑在表面处可见。因此,本工艺的实例将高摩擦轧制确认为在热箱中热蚀刻时产生期望的钢性质的步骤。不管是否存在热蚀刻以及原奥氏体晶界凹坑的证据,都可提供高摩擦轧制以增加薄钢带的再结晶。
[0094]
图5为说明用于施加高摩擦轧制和/或表面均匀化的工艺的流程图。在本实例中,确定钢带或钢产品是否应经历高摩擦轧制取决于不期望的热蚀刻是否已经在热箱510中发生。若热蚀刻尚未在热箱中发生,则不需要且不采取高摩擦轧制来(1)抹平原奥氏体晶界凹坑,(2)增大钢产品例如诸如超高强度耐候钢的成形性,和/或(3)改善耐氢(h2)脆化性。然而,即使热蚀刻尚未在热箱中发生,为实现再结晶520或为产生如本文中另外公开的微观结构,仍然可追求高摩擦轧制。若热蚀刻已经在热箱510中发生,则进行高摩擦轧制530以(1)抹平原奥氏体晶界凹坑,(2)增大超高强度耐候钢的成形性,和/或(3)通过除去原奥氏体晶界凹坑和消除在120小时腐蚀测试之后作为缺陷形成的弱点而改善耐氢(h2)脆化性。在本公开内容的一个实例中,产生具有抹平图案的超高强度耐候钢550。在本公开内容的另一实施方式中,除去抹平图案,由此改善耐点蚀性540,例如在汽车应用中需要的耐点蚀性。这样的实施方式产生例如高强度马氏体钢560。抹平图案可通过表面均匀化过程的方式除去。图5另外说明表面均匀化过程540。关于本公开内容在下文中更详细地讨论表面均匀化过程的适用性。代表性实例也在下文中更详细地讨论。
[0095]
超高强度耐候钢
[0096]
在一些实施方式中,轻型超高强度耐候钢板可由熔融熔体制成。熔融熔体可通过双辊铸造机加工。在一个实例中,轻型超高强度耐候钢板可通过包括如下的步骤制成:(a)准备熔融钢熔体,其包括:(i)以重量计,0.20%和0.35%之间的碳、小于1.0%的铬、0.7%和2.0%之间的锰、0.10%和0.50%之间的硅、0.1%和1.0%之间的铜、小于或等于0.12%的铌、小于0.5%的钼、0.5%和1.5%之间的镍,且为含有小于0.01%铝的硅镇静的,以及(ii)余量为铁和由熔炼产生的杂质;(b)以大于10.0mw/m2的热通量凝固,从而产生厚度小于2.5mm的钢板并且在快速冷却前和/或当热轧时在热轧前在非氧化气氛中以大于15℃/s的冷却速率冷却到1080℃以下且ar3温度以上;和(c)快速冷却以形成具有拥有至少75体积%马氏体或马氏体加贝氏体的微观结构、700和1600mpa之间的屈服强度、1000和2100mpa之间的抗拉强度、以及1%和10%之间的伸长率的钢板。在一个实例中,还可将轻型超高强度耐候钢板在快速冷却前热轧至15%和50%之间压下率。可将所述板在快速冷却前和/或当热轧时在热轧前在非氧化气氛中以大于15℃/s的冷却速率冷却到1100℃以下且ar3温度以上。ar3温度为在冷却期间奥氏体开始转变为铁素体的温度。也就是说,ar3温度为奥氏体转变点。在各实例中,镍将包晶点转移成远离碳区域和/或提高钢板组合物的包晶点的转变温度以提供无缺陷的钢板。镍对腐蚀指数的影响体现在用于确定腐蚀指数计算结果的以下方程式中:cu*26.01+ni*3.88+cr*1.2+si*1.49+p*17.28
–
cu*ni*7.29
–
ni*p*9.1
–
cu*cu*
33.39(其中各元素以重量百分数计)。
[0097]
本发明钢板实例提供镍的添加以在维持或改善硬化性的同时进一步防止包晶开裂。特别地,添加以重量计0.5%和1.5%之间的镍。镍的添加被认为防止带壳由在铸造辊上的相转变期间包晶区域的体积变化导致的翘曲,并且因此增强在带凝固期间的均匀传热。据认为,镍的添加将包晶点转移成远离碳区域和/或提高组合物的包晶点的转变温度以形成无缺陷的钢板。图4的相图说明这点。具体地,图4的相图说明0.0重量%镍100、0.2重量%镍110和0.4重量%镍120各自的影响。如图4说明的,在液相+δ相90、δ+γ相50、和液相+γ相60的交叉处发现的包晶点p
100
、p
110
和p
120
是随镍的增多而将更低的质量百分比的碳(c)转移到更高温度。否则,碳含量使钢带易于在具有高屈服强度的钢带中在更低温度下受缺陷影响。镍的添加将包晶点转移成远离碳区域和/或提高钢板的包晶点的转变温度以提供具有高屈服强度的无缺陷的马氏体钢带。
[0098]
镍对腐蚀指数的影响体现在用于确定腐蚀指数计算结果的以下方程式:cu*26.01+ni*3.88+cr*1.2+si*1.49+p*17.28
–
cu*ni*7.29
–
ni*p*9.1
–
cu*cu*33.39(其中各元素以重量百分数计)。
[0099]
下表2显示本公开内容的轻型超高强度耐候钢板的若干种组成实例。
[0100]
表2
[0101][0102]
在表2中,lecon为测量的重量百分比的氮气(n2)且ceaws为测量的重量百分比的碳当量(ce)。
[0103]
对于硬化性而言所依赖的其它元素通过将包晶点转移到更接近碳区域而产生相反效果。这样的元素包括为增大硬化性而依赖的但最终导致包晶开裂的铬和钼。通过镍的添加,使硬化性改善和包晶开裂减少以提供具有高强度的全淬火的马氏体等级钢带。
[0104]
在本发明组合物中,镍的添加可与有限量的铬和/或钼组合,如本文中描述的。结果,镍减轻这些硬化元素可具有的产生包晶开裂的任何影响。然而,在一个实例中,另外的
镍不会与硼的故意添加组合。故意添加为5ppm的硼或更多。也就是说,在一个实例中,镍的添加将与实质上没有硼或小于5ppm的硼组合使用。另外,轻型超高强度耐候钢板可通过进一步将钢板在150℃和250℃之间的温度下回火2
‑
6小时而制成。将钢板回火提供改善的伸长率以及最少的强度损失。例如,在如本文中描述的回火后,具有1250mpa的屈服强度、1600mpa的抗拉强度和2%的伸长率的钢板被改善为1250mpa的屈服强度、1525mpa的抗拉强度和5%的伸长率。
[0105]
轻型超高强度耐候钢板可为硅镇静的,含有以重量计小于0.008%的铝或小于0.006%的铝。熔融熔体可具有5
‑
70ppm之间或5
‑
60ppm之间的游离氧含量。钢板可具有大于50ppm的总氧含量。夹杂物包括典型地其中50%为小于5μm尺寸的mnosio2并且具有增强微观结构演变和由此的带机械性质的潜力。
[0106]
熔融熔体可以大于10.0mw/m2的热通量凝固成厚度小于2.5mm的钢板,并且在非氧化气氛中以大于15℃/s的冷却速率冷却至1080℃以下且ar3温度以上。非氧化气氛为典型地惰性气体例如氮气或氩气或其混合物的气氛,其包含以重量计小于约5%氧气。
[0107]
在一些实施方式中,钢板中的马氏体可由晶粒尺寸大于100μm的奥氏体形成。在其它实施方式中,钢板中的马氏体可由晶粒尺寸大于150μm的奥氏体形成。以大于10mw/m2的热通量的快速凝固使得能够产生响应于受控冷却的奥氏体晶粒尺寸以实现无缺陷的板的制造。
[0108]
另外可将钢板热轧至15%和50%之间压下率并且之后快速冷却以形成具有拥有至少75%马氏体加贝氏体的微观结构、700和1600mpa之间的屈服强度、1000和2100mpa之间的抗拉强度、以及1%和10%之间的伸长率的钢板。进一步地,可将钢板热轧至15%和35%之间压下率并且之后快速冷却以形成具有拥有至少75%马氏体加贝氏体的微观结构、700和1600mpa之间的屈服强度、1000和2100mpa之间的抗拉强度、以及1%和10%之间的伸长率的钢板。在一个实例中,将钢板热轧至15%和50%之间压下率并且之后快速冷却以形成具有拥有至少90体积%马氏体或马氏体和贝氏体的微观结构的钢板。在甚至又一个实例中,将钢板热轧至15%和50%之间压下率并且之后快速冷却以形成具有拥有至少95体积%马氏体或马氏体和贝氏体的微观结构的钢板。
[0109]
很多产品可由本文中描述的类型的轻型超高强度耐候(“uhsw”)钢板制造。可由轻型超高强度耐候钢板制造的产品的一个实例包括钢桩。更具体地,用于太阳能装置的桩或底座为由轻型超高强度耐候钢板制造的产品的用途实例。如本文中使用的,如本文中使用的,太阳能装置为在例如设计用于供应太阳能以在电网等中使用的光伏发电站的太阳能农场上支承太阳能电池的结构体。高速公路行业对于例如诸如用于支承护栏、标牌等的底座具有类似需求。桩或钢底座可由已经使用一个或多个轧机机架冷轧形成的薄铸钢带制造。另外,还可依赖于冲床系统、cnc等离子体系统和/或轧机系统等提供通孔、槽孔、连续焊接、部分焊接和/或点焊接,如下面指出的。
[0110]
在一个实例中,钢桩包括由以上描述的各种碳合金钢带冷轧形成的腹板和一个或多个凸缘。图10和图12
‑
15说明由薄铸钢带冷轧形成的uhsw钢桩的横截面实例。在图10中,uhsw钢桩100为包括腹板110、第一凸缘120和第二凸缘130的c槽形,并且为在本文中称为卷边c槽形或nxw桩的示例性实例。腹板110沿钢桩100的高度h
100
延伸并且在弯曲转接头140处转接到在腹板100的第一端112处的第一凸缘120中。腹板110另外在弯曲转接头150处转接
到在腹板110的与腹板110的第一端112相反的第二端113处的第二凸缘130中。在本实例中,各弯曲转接头140、150具有各自的半径r
140
、r
150
,各自形成延伸90度的圆弧。因此,各凸缘120、130垂直于腹板110。在图10中,第一凸缘120与第二凸缘130平行和相对。第一凸缘120和第二凸缘130两者从腹板110且在相同方向上沿钢桩100的宽度w
100
延伸。
[0111]
在图10中,第一凸缘120和第二凸缘130包括卷边结构。具体参考第一凸缘120,卷边结构为包括第一层122和第二层124的单卷边,其中第一层122从弯曲转接头140在钢桩100的宽度w
100
方向上延伸至泪滴状转接头160。泪滴状转接头160为转接至闭合卷边的开放卷边。泪滴状转接头160在钢桩的宽度w
100
和高度h
100
两个方向上朝着相对的第二凸缘130向钢桩100内部行进。在一个具体实例中,第一层122以相对于钢桩宽度w
100
方向45度的角度λ
160
行进到泪滴状转接头160的第一腿162。泪滴状转接头160从第一腿162行进通过圆弧至第二层124。第二层124定位到第一层122的在闭合卷边处的外侧。第二层124抵接第一层122并且与第一层122平行行进。在图10中,第二层124沿钢桩宽度w
100
延伸至弯曲转接头140。另外,泪滴状转接头160维持在由各自分别的第一凸缘120和第二凸缘130的卷边部分限定的钢桩高度h
100
内。
[0112]
仍然参考图10,并且类似于第一凸缘120但与其反向,第二凸缘130包括卷边结构。第二凸缘的卷边结构包括第一层132和第二层134,其中第一层132从弯曲转接头150在钢桩100的宽度w
100
方向上延伸到泪滴状转接头170。泪滴状转接头170为如下转接到闭合卷边的开放卷边。泪滴状转接头170在钢桩的宽度w
100
和高度h
100
两个方向上朝着相对的第一凸缘120向钢桩100内部行进。在一个具体实例中,第一层132以相对于钢桩宽度w
100
方向45度的角度行进到泪滴状转接头170的第一腿172。泪滴状转接头170从第一腿172行进通过圆弧至第二层134。第二层134定位到第一层132在闭合卷边处的外侧。第二层134抵接第一层132并且与第一层平行地行进。在图10中,第二层134沿钢桩宽度w
100
延伸到弯曲转接头150。泪滴状转接头170维持在由各自分别的第一凸缘120和第二凸缘130的卷边部分限定的钢桩高度h
100
内。在图10的实例中,形成钢桩100的钢板的厚度t为0.062英寸(“)(1.575mm)。从而,卷边部分为0.124”(3.15mm)。在一些实例中,形成钢桩100的钢板的厚度可为2mm或更小。在其它实例中,形成钢桩100的钢板的厚度可为2.5mm或更小。
[0113]
图11说明图10钢桩100在第一凸缘120处的透视图。钢桩100具有长度l
100
,其中腹板110、第一凸缘120和第二凸缘130沿钢桩长度l
100
延伸。一个或多个点焊头180可设置在第一凸缘120和第二凸缘130处以维持第一层122、132分别与第二层124、134的抵接关系(如图10说明的)。点焊头180可沿着钢桩长度l
100
以6”至24”隔开。点焊头180还可相对于钢桩宽度w
100
居中或相对于钢桩宽度w
100
偏置。此外,点焊头180可一致地隔开或点焊头180的间距可沿着钢桩长度l
100
变化。在一个实例中,第一点焊头距离钢桩的第一端102为0.50”并且沿着剩余钢桩长度l
10
以13.22”均匀隔开。点焊头180还可相对于钢桩宽度w
100
居中或相对于钢桩宽度w
100
偏置或其组合。在一个实例中,点焊头定位成距离分别的泪滴状转接头160、170的最外切线2.68”。
[0114]
仍然参考图11,第一凸缘120和/或第二凸缘130可另外地包括一个或多个通孔190和/或一个或多个槽孔192。通孔190和槽孔192可设置成用于将物品固定到钢桩例如诸如太阳能装置、高速公路护栏等。一个或多个通孔190和/或一个或多个槽孔192可另外地或替代地设置在腹板110中。该透视图也代表图12
‑
15的钢桩轮廓的透视图。
[0115]
在图10
‑
11的uhsw钢桩100实例中,uhsw钢桩包括恒定厚度t。恒定厚度可小于或等于2.5mm、小于或等于2.0mm或小于或等于1.6mm。恒定厚度t通过每个如上描述的特征而维持。更具体地,恒定厚度为由钢板冷成形uhsw钢桩的产物(结果)。在一个实例中,钢板宽度为50”。图11的c槽形的轮廓由所述宽度的钢板产生并且于是具有50”或更小的总横截面材料长度。更具体地,总横截面材料长度可为钢板宽度的一半或三分之一,在卷边凸缘处,在各层上维持材料厚度t。然而,通过抵接第一层122、132和第二层124、134并且尽管材料厚度维持为t,凸缘厚度已经加倍,如图10中由t
x2
反映的。在图10中,加倍的凸缘厚度t
x2
从泪滴状转接头160延伸到弯曲转接头140。在图10的实例中,钢桩高度h
100
大于钢桩宽度w
100
。在图10的实例中,钢桩100关于平分钢桩100高度h
100
的轴对称。图10的典型的uhsw钢桩可例如为6x4、6x6、8x6、8x8、10x8、10x10、12x8、12x10、12x12、14x10、14x12、14x14(以英寸计)的c槽形(具有或不具有波纹)以及其间的任意值等。
[0116]
现转向图12,说明c槽形uhsw钢桩200。c槽形包括腹板210、第一凸缘220和第二凸缘230,并且为在本文中称为波纹c槽形或ncw桩的示例性实例。腹板210沿钢桩200高度h
200
延伸并且在弯曲转接头240处转接到在第一端211处的第一凸缘220。腹板210还在弯曲转接头250处转接到第二端212处的第二凸缘230。在本实例中,各弯曲转接头240、250具有各自的半径r
240
、r
250
。各半径r
240
、r
250
形成大于90度的圆弧。还有,各凸缘220、230保持总体上垂直于腹板210。腹板210进一步包括一个或多个腹板波纹。在图12中,腹板210包括第一腹板波纹213和第二腹板波纹214。为形成腹板波纹,腹板210的外侧表面215在钢桩宽度w
200
方向上偏离腹板210的一个或多个内侧表面216。外侧表面215和各内侧表面216两者均在钢桩高度h
200
方向上延伸,其中外侧表面215和各内侧表面216垂直于第一凸缘220和/或第二凸缘230。外侧表面215和各内侧表面216形成腹板200的大部分使得腹板被称为保持总体上垂直于第一凸缘220和/或第二凸缘230。各弯曲转接头240、250从各自的第一凸缘220或第二凸缘230沿着分别以半径r
240
、r
250
形成的圆弧延伸。如上指出的,各弯曲转接头240、250的圆弧以大于90度延伸而在各自的内侧表面216处形成腹板波纹,其然后转接到外侧表面215。外侧表面215在腹板210上相对于钢桩高度h
200
中心定位。在图12中,以半径r
240
形成的圆弧和以半径r
250
形成的圆弧各自进一步包括在钢桩高度h
200
方向上与外侧表面215对齐的切线。
[0117]
图12的uhsw钢桩的腹板波纹213、214各自包括垂直于第一凸缘220和第二凸缘230的表面。从各自分别的弯曲转接头240、250起,腹板210凹陷,形成两个腹板波纹213、214。各腹板波纹然后回到全宽度w
200
且通过腹板210的外侧表面215连接。与之相比,并且如下面由凸缘波纹222、232说明的,波纹可完全由圆弧形成。
[0118]
仍然参考图12,第一凸缘220还可包括一个或多个波纹。在图12的实例中,第一凸缘220包括沿着钢桩宽度w
200
在中心形成的一个凸缘波纹222。凸缘波纹222为从凸缘220的第一外侧表面224和第二外侧表面226之间向内延伸的以半径r
222
形成的圆弧。与腹板210相对,第一前缘(唇部,lip)228从第一凸缘220在弯曲转接头260处延伸。第一前缘在钢桩高度h
200
方向上延伸并且平行于腹板210的内侧表面216和外侧表面215。第一前缘228可进一步包括到返回(return)部分229中的弯曲转接头280。返回部分229从第一前缘228朝着腹板210向内延伸。返回部分229与凸缘220的第一外侧表面224和第二外侧表面226平行。
[0119]
类似于第一凸缘220,第二凸缘230也可包括一个或多个波纹。在图12的实例中,第二凸缘230包括沿着钢桩宽度w
200
在中心形成的一个凸缘波纹232。凸缘波纹232为从凸缘
230的第一外侧表面234和第二外侧表面236之间向内延伸的以半径r
232
形成的圆弧。与腹板210相对,第二前缘238从在弯曲转接头270处的第二凸缘230延伸。第二前缘在钢桩高度h
200
的方向上延伸并且平行于腹板210的内侧表面216和外侧表面215。第二前缘228可进一步包括到返回部分239中的弯曲转接头290。返回部分239从前缘228朝着腹板210向内延伸。返回部分239与第二凸缘230的第一外侧表面234和第二外侧表面236平行。在图12的实例中,形成钢桩200的钢板的厚度t为0.062英寸(“)(1.575mm)。在一些实例中,形成钢桩200的钢板的厚度可为2mm或更小。在其它实例中,形成钢桩200的钢板的厚度可为2.5mm或更小。图12的uhsw钢桩200的第一凸缘220和/或第二凸缘230可另外地包括一个或多个通孔和/或一个或多个槽孔。通孔和槽孔可设置成用于将物品固定到钢桩例如诸如太阳能装置、高速公路护栏等。一个或多个通孔和/或一个或多个槽孔可另外地或替代地设置在腹板210中。
[0120]
在图12的uhsw钢桩200实例中,uhsw钢桩包括恒定厚度t。恒定厚度可小于或等于2.5mm、小于或等于2.0mm或小于或等于1.6mm。恒定厚度t通过每个如上描述的特征而维持。更具体地,恒定厚度为由钢板冷成形uhsw钢桩的产物。在一个实例中,钢板宽度为50”。图11的c槽形的轮廓由所述宽度的钢板产生并且于是具有50”或更小的总横截面材料长度。更具体地,总横截面材料长度可为钢板宽度的一半或三分之一。在波纹处,材料厚度t在各层和转接(头)处维持不变。在图12的实例中,钢桩高度h
200
大于钢桩宽度w
200
。在图12的实例中,钢桩200关于平分钢桩200的高度h
200
的轴对称。图12的典型的uhsw钢桩可为例如6x4、6x6、8x6、8x8、10x8、10x10、12x8 12x10、12x12、14x10、14x12、14x14(以英寸计)的c槽形(具有或不具有波纹)以及其间的任意值等。
[0121]
现转向图13,作为包括腹板310、第一凸缘320和第二凸缘330的c槽形的uhsw钢桩300示出并且为波纹c槽形或ncw桩的另一实例。类似于图12的钢桩,图13的钢桩300的腹板310沿钢桩300的高度h
300
延伸并且在弯曲转接头340处转接到第一端311处的第一凸缘320。腹板310还在弯曲转接头350处转接到第二端312处的第二凸缘330。各弯曲转接头340、350分别具有半径r
340
、r
350
。图13中,腹板310包括单腹板波纹313。单腹板波纹313相对于钢桩高度h
300
在中心定位。这与其中腹板210包括第一腹板波纹213和第二腹板波纹214的图12形成对比。为形成图13的腹板波纹,腹板310的外侧表面315在钢桩宽度w
300
的方向上偏离腹板310的内侧表面316。外侧表面315和内侧表面316两者均在钢桩高度h
300
的方向上延伸,其中外侧表面315和内侧表面316垂直于第一凸缘320和/或第二凸缘330。外侧表面315和各内侧表面316形成腹板300的大部分使得腹板被称为保持总体上垂直于第一凸缘320和/或第二凸缘330。各弯曲转接头340、350从分别的第一凸缘320或第二凸缘330沿着分别以半径r
340
、r
350
形成的圆弧延伸。还有,与图12相比,图13的弯曲转接头340、350的圆弧只延伸90度,因为单腹板波纹313在腹板310上在中心定位并且独立于弯曲转接头340、350。
[0122]
图13的uhsw钢桩的单腹板波纹313包括垂直于第一凸缘320和第二凸缘330的内侧表面316。内侧表面316可另外地或替代地被称为相对于腹板310或腹板310的外侧表面315是凹陷的。与之相比并且如下面由凸缘波纹322、332说明的,波纹可完全由圆弧形成。
[0123]
仍然参考图13,第一凸缘320还可包括一个或多个波纹。在图13实例中,第一凸缘320包括沿着钢桩宽度w
300
在中心形成的一个凸缘波纹322。凸缘波纹322为从凸缘320的第一外侧表面324和第二外侧表面326之间向内延伸的以半径r
322
形成的圆弧。与腹板310相对,第一前缘328从第一凸缘320在弯曲转接头360处延伸。第一前缘在钢桩高度h
300
的方向
上延伸并且平行于腹板310的内侧表面316和外侧表面315。第一前缘328可进一步包括至返回部分329的弯曲转接头380。返回部分329从第一前缘328朝着腹板310向内延伸。返回部分329平行于凸缘320的第一外侧表面324和第二外侧表面326。
[0124]
类似于第一凸缘320,第二凸缘330也可包括一个或多个波纹。在图13实例中,第二凸缘330包括沿着钢桩宽度w
300
在中心形成的一个凸缘波纹332。凸缘波纹332为从凸缘330的第一外侧表面334和第二外侧表面336之间向内延伸的以半径r
332
形成的圆弧。与腹板310相对,第二前缘338从第二凸缘330在弯曲转接头370处延伸。第二前缘在钢桩高度h
300
的方向上延伸并且平行于腹板310的内侧表面316和外侧表面315。第二前缘328可进一步包括至返回部分339的弯曲转接头390。返回部分339从前缘328朝着腹板310向内延伸。返回部分339平行于第二凸缘330的第一外侧表面334和第二外侧表面336。在图13实例中,形成钢桩300的钢板的厚度t为0.062英寸(“)(1.575mm)。在一些实例中,形成钢桩300的钢板的厚度可为2mm或更小。在其它实例中,形成钢桩300的钢板的厚度可为2.5mm或更小。图13的uhsw钢桩300的第一凸缘320和/或第二凸缘330可另外地包括一个或多个通孔和/或一个或多个槽孔。通孔和槽孔可设置成用于将物品固定到钢桩例如诸如太阳能装置、高速公路护栏等。一个或多个通孔和/或一个或多个槽孔可另外地或替代地设置在腹板310中。
[0125]
在图13的uhsw钢桩300实例中,uhsw钢桩包括恒定厚度t。恒定厚度可小于或等于2.5mm、小于或等于2.0mm、或小于或等于1.6mm。恒定厚度t通过每个如上描述的特征而维持。更具体地,恒定厚度为uhsw钢桩由钢板冷成形的产物。在一个实例中,钢板宽度为50”。图11的c槽形的轮廓由所述宽度的钢板产生,并且于是具有50”或更小的总横截面材料长度。更具体地,总横截面材料长度可为钢板宽度的一半或三分之一。在波纹处,材料厚度t在各层和转接处维持不变。在图13实例中,钢桩的高度h
300
大于钢桩的宽度w
300
。在图13实例中,钢桩300关于平分钢桩300的高度h
300
的轴对称。典型的图13的uhsw钢桩可为诸如6x4、8x6、10x8、12x8 12x10、14x10、14x12(以英寸计)c槽形(具有或不具有波纹)等。
[0126]
现转向图14,说明具有管状横截面的uhsw钢桩400。图14的钢桩400为正方形。钢桩400包括第一侧壁410、第二侧壁420、第三侧壁430和第四侧壁440。第一侧壁410与第三侧壁430总体上平行。第二侧壁420与第四侧壁440总体上平行。而且,第一侧壁410和第三侧壁430总体上垂直于第二侧壁420和第四侧壁440。如本上下文中使用的,“总体上”是指波纹除外的侧壁布置,如下面进一步描述的。图14钢桩400的高度h
400
和宽度w
400
相同,形成总体上为正方形的横截面。再次,如本上下文中使用的,“总体上”是指波纹除外的壁布置。也就是说,钢桩400的各侧壁的横截面的总体上尺度相同。弯曲转接头设置在各侧壁之间。更具体地,第一弯曲转接头450设置在第一侧壁410和第二侧壁420之间;第二弯曲转接头460设置在第二侧壁420和第三侧壁430之间;第三弯曲转接头470设置在第三侧壁430和第四侧壁440之间;并且第四弯曲转接头470设置在第四侧壁440和第一侧壁410之间。各弯曲转接头450、460、470和480为以分别的半径r
450
、r
460
、r
470
和r
480
形成的圆弧。
[0127]
图14钢桩400的一个或多个侧壁可各自包括一个或多个波纹。在图14实例中,各侧壁410、420、430、440分别包括一个波纹412、422、432、442。图14中,各侧壁和波纹为相同的布置和尺寸。于是,图14的横截面沿着在纵轴x
axis
上延伸的任意平面对称。类似于图12
‑
13的腹板波纹,各波纹412、422、432、442分别包括内侧表面413、423、433、443,其分别偏离且平行于侧壁410、420、430、440的外侧表面411、421、431、441。在图14实例中,设置倾斜侧壁
480以从内侧表面转接到外侧表面。图14中,各内侧表面包括相对的倾斜侧壁414、424、434、444。可设置圆弧以在各表面之间、在各表面和倾斜侧壁之间等转接。如上指出的,波纹充当钢桩的刚性体(stiffener)。图14中,各波纹412、422、432、442向内延伸。在其它实例中,波纹可各自向外延伸、交替进行(alternate)或形成相对的两半。在一些实例中,侧壁的一个或多个可包括多个波纹例如诸如图10的腹板波纹。另外地或替代地,波纹可完全由圆弧例如如图12
‑
13说明的凸缘波纹形成。波纹可为相对于图14描述的波纹和完全由圆弧形成的波纹的组合。
[0128]
在图14的uhsw钢桩400实例中,uhsw钢桩包括恒定厚度t。恒定厚度可小于或等于2.5mm、小于或等于2.0mm、或小于或等于1.6mm。恒定厚度t通过每个如上描述的特征而维持。更具体地,恒定厚度为uhsw钢桩由钢板冷成形的产物。在一个实例中,钢板宽度为50”。图14的管的轮廓由所述宽度的钢板产生并且于是具有50”或更小的总横截面材料长度。更具体地,总横截面材料长度为钢板宽度的一半或三分之一。而且,可提供焊接、铆接、搭接和/或接头以当由钢板成形时闭合图14的管状钢桩。焊接可为连续焊接、部分焊接和/或点焊。焊接、铆接、搭接和/或接头可定位在圆弧上、在波纹上、在内侧表面上、在外侧表面上和/或在倾斜侧壁上。典型的图14的uhsw钢桩可为诸如4x4、6x6、8x8、12x12(以英寸计)的钢管(具有或不具有波纹)以及其间的任意值等。
[0129]
现转向图15,说明具有管状横截面的uhsw钢桩500。与图14的正方形钢桩相比,图15的钢桩500为矩形的。类似于图14的钢桩,钢桩500包括第一侧壁510、第二侧壁520、第三侧壁530和第四侧壁540。第一侧壁510与第三侧壁530总体上平行。第二侧壁520与第四侧壁540总体上平行。而且,第一侧壁510和第三侧壁530总体上垂直于第二侧壁520和第四侧壁540。如本上下文中使用的,“总体上”是指波纹除外的侧壁布置,如下面进一步描述的。图15的钢桩500的高度h
500
大于宽度w
500
,形成总体上上矩形管。再次,如本上下文中使用的,“总体上”是指波纹除外的壁布置。也就是说,第一侧壁510和第三侧壁530的总尺度与第二侧壁520和第四侧壁540的总尺度相同。弯曲转接头设置在各侧壁之间。更具体地,第一弯曲转接头550设置在第一侧壁510和第二侧壁520之间;第二弯曲转接头560设置在第二侧壁520和第三侧壁530之间;第三弯曲转接头570设置在第三侧壁530和第四侧壁540之间;以及第四弯曲转接头570设置在第四侧壁540和第一侧壁510之间。各弯曲转接头550、460、570和580为以分别的半径r
550
、r
560
、r
570
和r
580
形成的圆弧。
[0130]
图15钢桩500的一个或多个侧壁可各自包括一个或多个波纹。在图15实例中,各侧壁510、520、530、540分别包括一个波纹512、522、532、542。在图15中,第一侧壁510和第三侧壁530的波纹相同而第二侧壁520和第四侧壁540包括相同的不同于第一和第三侧壁的波纹。于是,图15的横截面沿着在纵轴x
axis
上延伸的任意平面角对角地对称。类似于图10、12
‑
13的腹板波纹,各波纹512、522、532、542分别包括内侧表面513、523、533、543,其分别偏离且平行于侧壁510、520、530、540的外侧表面511、521、531、541。在图15实例中,提供倾斜侧壁514、524、534、544以从内侧表面转接到外侧表面。图15中,各内侧表面包括相对的倾斜侧壁。可提供圆弧以在各表面之间、在各表面和倾斜侧壁之间等转接。如上指出的,波纹充当钢桩的刚性体。图15中,各波纹512、522、532、542向内延伸。在其它实例中,波纹可各自向外延伸、交替进行或形成相对的两半。在一些实例中,侧壁的一个或多个可包括多个波纹例如诸如图10的腹板波纹。另外地或替代地,波纹可由圆弧例如如图12
‑
13说明的凸缘波纹完全
形成。波纹可为以上相对于图15描述的波纹和完全由圆弧形成的波纹的组合形成。
[0131]
在图15的uhsw钢桩500实例中,uhsw钢桩包括恒定厚度t。恒定厚度可小于或等于2.5mm、小于或等于2.0mm或小于或等于1.6mm。恒定厚度t通过每个如上描述的特征而维持。更具体地,恒定厚度为uhsw钢桩由钢板冷成形的产物。在一个实例中,钢板宽度为50”。图15的管的轮廓由所述宽度或小于所述宽度的钢板产生并且于是具有50”或更小的总横截面材料长度。更具体地,总横截面材料长度可为钢板宽度的一半或三分之一。而且,可提供焊接、铆接、搭接和/或接头以将图15管状钢桩当由钢板成形时闭合。焊接可为连续焊接、部分焊接和/或点焊。焊接、铆接、搭接和/或接头可定位在圆弧上、在波纹上、在内侧表面上、在外侧表面上和/或在倾斜侧壁上。典型的图15的uhsw钢桩可为诸如6x4、8x6、10x8、12x8 12x10、14x10、14x12(以英寸计)的钢管(具有波纹)以及其间的任意值等。
[0132]
以上描述的形状提供经受住如下面进一步描述的桩或钢底座所遭受的负荷的另外的结构完整性。进一步地,通过以形状方式增大结构完整性,可依赖于比传统的镀锌工字梁薄得多的材料制造钢桩。因此,为了在维持必不可少的强度和完整性同时迫进到土地中,薄得多的材料还需要较小的力,因为本发明uhsw钢桩的横截面相较于先前的桩和结构底座而言减小。
[0133]
使用时,将钢桩的部分长度迫进到土地或土壤中以提供结构底座。使用夯(撞击装置,ram)例如活塞或锤子将钢桩迫进到土地或土壤中。夯可为桩驱动器的一部分并且至少受桩驱动器驱动。夯撞击或冲击钢桩,迫使钢桩进入土地或土壤中。由于冲击,先前的钢桩在夯的冲击下可翘曲或变形。为避免对先前的钢桩的翘曲或损害,桩驱动器的rpm或力维持在损害阈值以下。本发明钢桩已经说明与现有钢桩相比在未翘曲或损害钢桩的情况下对钢桩施加的rpm或力的增大的能力,如由钢桩的强度性质所反映的。具体地,如测试的,尺寸特征相当的现有钢桩被驱动且在结构上失败,其中本公开的钢桩提供25%的rpm增幅。而且,现有钢桩另外在不存在镀锌或锌表面的情况下不是耐候钢。于是,现有钢桩由于其放置于外部条件(包括土地和土壤条件)中而易受腐蚀的影响,或需要另外处理例如诸如镀锌。再次,本发明钢桩提供对于经受住这些条件所需的腐蚀指数。就这样的产品而言,本发明强度性质和腐蚀性质之前尚未组合地见到过。
[0134]
如上由图10描述和说明的卷边c槽形的卷边的凸缘、如上由图12
‑
13描述和说明的波纹c槽形的波纹腹板和凸缘、和如上由图14
‑
15描述和说明的波纹管进一步增大钢桩的刚度以防止翘曲和/或经受住驱动力,如上指出的。通过提供卷边c槽形、波纹c槽形和波纹管的特征和形状,形成超高强度耐候钢桩的薄铸钢带的材料厚度可另外地维持在2.5mm或更小、2.0mm或更小或1.6mm或更小,如本文中描述的。材料厚度的减小进一步有助于通过减小在超高强度耐候钢桩和地面之间的横截面阻力而减小用于将超高强度耐候钢桩驱动到地面(例如土地或土壤)中所需的驱动力。而且,因为超高强度耐候钢桩不具有单独施加的耐腐蚀性涂层,所以这样的涂层不易受在安装过程期间当接触地面时和/或可另外在与地下水和/或土壤条件反应时负面地受其影响而刮掉或除去的影响。如本文中使用的,单独施加的涂层为作为与钢组成无关的表面保护剂的保护性涂层。这样的单独施加的保护性涂层的实例包括锌涂层、镀锌涂层(例如热浸镀锌涂层)、铝
‑
硅耐腐蚀涂层等。更重要地,本公开的桩或钢底座在没有单独施加的涂层的辅助下产生耐腐蚀性,如下文阐述的。固有地,按照定义,包括本文中公开的超高强度耐候钢的耐候钢具备必不可少的耐腐蚀性,否则单独施加
的热浸镀锌涂覆工艺将产生。于是,本公开的耐候钢将不需要或具备锌涂层、热浸镀锌涂层等。
[0135]
已经将由本公开的轻型超高强度耐候钢形成的钢桩与现有钢桩材料就操作寿命和耐腐蚀潜力进行比较测试。现有钢桩材料包括热浸镀锌(“hdg”)桩例如诸如g235等级钢以及未镀锌的钢例如诸如g100、gr 70等。在太阳能装置中,出于结构意图使用由镀锌的50ksi钢w6工字梁钢设计的桩一直为太阳能行业的惯例。经常对土壤类型进行氧化还原分析以确认土壤的腐蚀特性。然后依赖于这些特性测定放置于土壤中的材料的腐蚀速率。对于电阻、ph、氯化物和硫酸盐,可另外地或替代地分析土壤条件。钢桩必须指定为经受住负荷要求而不管腐蚀如何。为了比较测试用于轻型超高强度耐候(“uhsw”)钢桩的本发明材料的操作寿命和耐腐蚀潜力,采用盐
‑
雾测试将uhsw钢片直接与不同材料例如g235、g100和gr70的钢片对比测试。具体地,测试根据astm b117
‑
18标准规范对如下不同材料的四种钢片而进行:“g235”、“g100”、“gr70”和“uhsw”。测试文件规定使用以250小时检查间隔的1000
‑
小时盐雾测试。选择来自各材料类型的随机片(4个中的1个)进行检查,并且图16
‑
19和下表3显示对于g235、g100、gr70和uhsw以250小时间隔在各角处采集的以定量和定性两种表述的厚度测量结果的平均值。厚度测量结果通过卡尺采集,并且因此代表包膜(envelope)的厚度。初步测量结果因氧化的材料的初始集结而偏离;然而,各片显示在250小时后相对稳定的材料损耗率。描述各片的颜色和近似百分数覆盖率。白色显色表示锌氧化且红色显色表示钢氧化。对比测试结果在下表3中再现。图16
‑
19说明伴有代表性图像的以图表格式的相同测试结果,其中图16说明钢等级g325,图17说明钢等级g100,图18说明钢等级gr70,和图19说明uhsw钢。
[0136]
表3
[0137][0138][0139]
*厚度值为在所述片的各角处采集的四个读数的平均值。
[0140]
为比较所测试的材料的相对腐蚀速率,测量各样品的在每小时材料损耗方面的差
异,并且排除初始数据读数,因为氧化外观通常使结果偏离。也就是说,氧化外观使所测量的厚度增大。250小时后,结果通常更为线性。使用下表4中显示的该运行(exercise)的平均值产生在uhsw钢片与其它片的腐蚀速率之间的相对关系:
[0141]
表4
[0142][0143]
单独使用该关系,uhsw片表现得优于镀锌片。可注意到,uhsw的测量结果极大地胜过其它钢片。本公开的超高强度耐候钢呈现出普通技术人员否则将依赖于单独施加的金属涂层或镀锌来实现的耐腐蚀性。从而,超高强度耐候钢与以上成型体(形状)的益处组合地呈现出必不可少的强度和腐蚀性质的组合,以作为桩或结构底座使用,其中否则在钢上需要单独施加的涂层来实现否则不存在于现有耐候钢中的相同的强度性质。
[0144]
下表5说明表3
‑
4的以上结果中所依赖的uhsw钢片的钢等级和化学成分。
[0145]
表5
[0146][0147]
进行另外的测试以评价对于不同的几何形状、埋置持续期和模拟老化的uhsw钢的腐蚀速率与镀锌(“hdg”)钢的腐蚀速率的比较。下表6
‑
7说明来自这些测试的结果。将材料在适度含盐的低电阻土壤中测试,该土壤还可设计为“非常腐蚀的”。所测试的材料几何形状包括小角度形状的柱(stake)和全尺寸冷轧成形的c形桩。标记为“施加电流”的材料接受对于人工引起近似24小时的腐蚀足够高的电压,以尝试模拟较长期的安装效果。在该对比分析中,uhsw钢材料的测得速率从hdg钢材料的测得速率的77%至99%变化。
[0148]
表6
[0149][0150]
表7
[0151][0152]
以上对比测试和结构能力计算结果说明,由薄铸钢带制造的钢桩胜过热浸镀锌(“hdg”)钢桩以及现有钢桩。本公开的uhsw钢桩提供更大的耐腐蚀性并且以薄得多的材料厚度提供。在维持这些改善的同时还维持容许uhsw钢桩当迫进到土地中时抵抗形变的合乎需要的强度和伸长率性质。如还由材料厚度说明的,uhsw钢桩以比现有钢桩低得多的重量制成。具体地,与由重量为每英尺7磅(lbs)的w6x7工字梁或由重量为每英尺9磅(lbs)的w6x9工字梁构造的钢桩相比,总横截面相当的uhsw卷边c槽形或nxw桩的重量为每英尺5磅(lbs)并且横截面相当的uhsw波纹c槽形或ncw桩的重量为每英尺3.5磅(lbs)。还提供不具有热浸镀锌涂层或锌涂层的本公开的uhsw钢桩。于是,本公开的uhsw钢桩消除任何不期望的在土壤或地下水和锌涂层之间的否则在hdg钢桩的情况下存在的相互作用。本公开的uhsw钢桩显著胜过不具有单独施加的涂层的钢桩的其它替代品例如本文中测试的其它的未镀锌的钢桩。
[0153]
甚至在镀锌涂层的情况下,hdg钢桩结构能力和使用寿命也没有胜过较薄的uhsw钢桩的结构能力和使用寿命。镀锌层完全腐蚀的时间通过使用厚度除以腐蚀速率来估计。然后,将剩余时间乘以钢腐蚀速率以确定最终材料厚度。例如,考虑0.124”厚的g235板金属组件:若应用在腐蚀性土壤条件中锌层和基体金属之间的腐蚀速率的标准比率并且g235(2.1密耳/面)镀锌钢的锌涂层腐蚀速率估计为0.0003”/y,则基体钢腐蚀速率应该为大约0.0021”/y,在使用寿命为30年的情况下每面的总减少如下计算:
[0154]
[0155]
0.0021
″
/年/面
×
23年
×
2面=0.0966
″
[0156]
总金属损耗将为大约0.1008”并且这在使用寿命结束时将留下0.0232”厚的组件。
[0157]
假设具有0.062”厚度的uhsw材料以与锌相同的速率腐蚀,最终厚度在前两年后更简单地如下计算:
[0158]
0.3密耳/年/面
×
30年
×
2面=18密耳在30年结束时导致0.0440”的材料厚度。该温和的腐蚀性情况证明所述材料的寿命如何能够胜过锌+碳钢结构,并且与碳钢相比极大地增大的强度实现在实质上任何负荷场景中显著更大的能力。
[0159]
在一些实例中,超高强度耐候钢桩包括具有小于或等于2.5mm、小于或等于2.0mm、或小于或等于1.6mm的厚度的铸态材料。铸态材料厚度为冷轧形成为具有腹板和一个或多个凸缘的腐蚀指数为6.0或更大的钢桩的薄铸钢带。超高强度耐候钢桩可进一步包括700和1600mpa之间的材料屈服强度、1000和2100mpa之间的材料抗拉强度、以及1%和10%之间的材料伸长率。超高强度耐候钢桩的材料组成可包括足以将包晶点转移成远离碳区域和/或提高包晶点的转变温度以形成具有至少75体积%马氏体或马氏体加贝氏体的微观结构的碳合金钢带的量的镍。
[0160]
uhsw钢桩可为包括腹板和一个或多个凸缘、或为由碳合金钢带形成的上述成型体之一的钢桩,该碳合金钢带具有包括如下的组成:以重量计,0.20%和0.35%之间的碳、少于1.0%的铬、0.7%和2.0%之间的锰、0.10%和0.50%之间的硅、0.1%和1.0%之间的铜、少于或等于0.12%的铌、少于0.5%的钼、0.5%和1.5%之间的镍,且为含有少于0.01%铝的硅镇静的,其中所述碳合金钢带具有拥有至少75体积%马氏体或马氏体加贝氏体的微观结构、700和1600mpa之间的屈服强度、1000和2100mpa之间的抗拉强度、1%和10%之间的伸长率并且具有6.0或更大的腐蚀指数。在一个实例中,钢桩可由以小于或等于2.5mm的铸造厚度铸造的碳合金钢带冷轧形成。在另一实例中,钢桩可由小于或等于2.0mm或者小于或等于1.6mm的钢带冷轧形成。在甚至又一实例中,钢桩可由厚度为在1.4mm至1.5mm之间或1.4mm或1.5mm的钢板形成。钢桩可为槽形例如c槽形、箱槽形、双槽形等。钢桩可另外地或替代地为工字形部件、角形、结构t形、中空结构截面形(hollow structural section)、双角形、s
‑
形状、管等。而且,这些部件的很多可连接在一起例如焊接在一起以形成单钢桩。本文中认识到,可由轻型超高强度耐候钢板制成另外的产品。另外,本文中认识到,另外的产品可由不是通过双辊铸造机制造的超高强度耐候钢制成,而是反而超高强度产品可通过其它方法制成。
[0161]
下面提供超高强度耐候钢的另外实例:
[0162]
轻型超高强度钢板,其包括:以小于或等于2.5mm的铸造厚度铸造的碳合金钢带,其具有包括如下的组成:
[0163]
(i)以重量计,0.20%和0.35%之间的碳、小于1.0%的铬、0.7%和2.0%之间的锰、0.10%和0.50%之间的硅、0.1%和1.0%之间的铜、小于或等于0.12%的铌、小于0.5%的钼、0.5%和1.5%之间的镍,且为含有小于0.01%铝的硅镇静的,和
[0164]
(ii)余量为铁和由熔炼产生的杂质;
[0165]
其中在所述组成中镍将包晶点转移成远离碳区域和/或提高包晶点的转变温度以形成具有拥有至少75体积%马氏体或马氏体加贝氏体的微观结构、700和1600mpa之间的屈服强度、1000和2100mpa之间的抗拉强度、以及1%和10%之间的伸长率的无缺陷的碳合金
钢带。
[0166]
在上面的一种实例中,轻型超高强度钢板具有拥有至少75体积%马氏体的微观结构。在上面的另一实例中,轻型超高强度钢板具有拥有至少90体积%马氏体的微观结构。在上面的又一实例中,轻型超高强度钢板具有拥有至少95%马氏体的微观结构。
[0167]
在上面的一种实例中,轻型超高强度钢板包括小于5ppm硼。
[0168]
在上面的一种实例中,轻型超高强度钢板包括0.05%和0.12%之间的铌。
[0169]
在上面的一种实例中,钢板中的马氏体来自于晶粒尺寸大于100μm的奥氏体。
[0170]
在上面的一种实例中,钢板中的马氏体来自于晶粒尺寸大于150μm的奥氏体。
[0171]
在上面的一种实例中,钢板可另外地在快速冷却前热轧至15%和50%之间压下率。
[0172]
在上面的一种实例中,碳合金钢板在快速冷却前热轧至铸造厚度的15%和35%之间压下率的热轧厚度。
[0173]
在上面的一种实例中,钢板为具有6.0或更大的腐蚀指数的耐候钢。
[0174]
轻型超高强度耐候钢板的制造方法,其包括如下步骤:
[0175]
(a)准备熔融钢熔体,其包括:
[0176]
(i)以重量计,0.20%和0.35%之间的碳、小于1.0%的铬、0.7%和2.0%之间的锰、0.10%和0.50%之间的硅、0.1%和1.0%之间的铜、小于或等于0.12%的铌、小于0.5%的钼、0.5%和1.5%之间的镍,具有小于0.01%铝的硅镇静的,以及
[0177]
(ii)余量为铁和由熔炼产生的杂质;
[0178]
(b)将熔体形成为被支承在其间具有夹区的一对经冷却的铸造辊的铸造表面上的铸造池;
[0179]
(c)使所述铸造辊反向旋转并且将熔融熔体以大于10.0mw/m2的热通量凝固成厚度小于2.5mm的从夹区向下输送的钢板,并且将所述板在非氧化气氛中以大于15℃/s的冷却速率冷却至1100℃以下且ar3温度以上;和
[0180]
(d)快速冷却以形成具有拥有至少75体积%马氏体或马氏体加贝氏体的微观结构、700和1600mpa之间的屈服强度、1000和2100mpa之间的抗拉强度、以及1%和10%之间的伸长率的钢板,其中镍将包晶点转移成远离碳区域和/或提高包晶点的转变温度以抑制高强度马氏体钢板中的裂纹或缺陷形成。
[0181]
在上面的一种实例中,微观结构具有至少75体积%马氏体。在上面的另一实例中,微观结构具有至少90体积%马氏体。在上面的又一实例中,微观结构具有至少95体积%马氏体。
[0182]
在上面的一种实例中,形成具有小于5ppm硼的碳合金钢板。
[0183]
在上面的一种实例中,碳合金钢板包括0.05%和0.12%之间的铌。
[0184]
在上面的一种实例中,钢板中的马氏体来自于晶粒尺寸大于100μm的奥氏体。
[0185]
在上面的一种实例中,钢板中的马氏体来自于晶粒尺寸大于150μm的奥氏体。
[0186]
在上面的一种实例中,钢板在快速冷却前热轧至铸造厚度的15%和50%之间压下率的热轧厚度。
[0187]
在上面的一种实例中,钢板在快速冷却前热轧至铸造厚度的15%和35%之间压下率的热轧厚度。
[0188]
在上面的一种实例中,高强度钢板为无缺陷的。
[0189]
还公开了钢桩,其包括由以小于或等于2.5mm铸造厚度铸造的碳合金钢板冷轧形成的腹板和一个或多个凸缘,所述碳合金钢板具有包括如下的组成:以重量计,0.20%和0.35%之间的碳、小于1.0%的铬、0.7%和2.0%之间的锰、0.10%和0.50%之间的硅、0.1%和1.0%之间的铜、小于或等于0.12%的铌、小于0.5%的钼、0.5%和1.5%之间的镍,且为含有小于0.01%铝的硅镇静的,其中碳合金钢板具有拥有至少75体积%马氏体或马氏体加贝氏体的微观结构、700和1600mpa之间的屈服强度、1000和2100mpa之间的抗拉强度、1%和10%之间的伸长率并且是无缺陷的。
[0190]
在上面的一种实例中,轻型超高强度钢板具有拥有至少75体积%马氏体的微观结构。在上面的另一实例中,轻型超高强度钢板具有拥有至少90体积%马氏体的微观结构。在上面的又一实例中,轻型超高强度钢板具有拥有至少95%马氏体的微观结构。
[0191]
在上面的一种实例中,钢桩的碳合金钢板包括小于5ppm硼。
[0192]
在上面的一种实例中,钢桩的碳合金钢板包括0.05%和0.12%之间的铌。
[0193]
在上面的一种实例中,钢桩中的马氏体来自于晶粒尺寸大于100μm的奥氏体。
[0194]
在上面的一种实例中,钢桩中的马氏体来自于晶粒尺寸大于150μm的奥氏体。
[0195]
在上面的一种实例中,钢板可另外地在快速冷却前热轧至15%和50%之间压下率。
[0196]
在上面的一种实例中,碳合金钢板在快速冷却前热轧至铸造厚度的15%和35%之间压下率的热轧厚度。
[0197]
在上面的一种实例中,碳合金钢板为具有6.0或更大的腐蚀指数的耐候钢。
[0198]
高摩擦轧制的高强度耐候钢
[0199]
在下面的实例中,公开了高摩擦轧制高强度耐候钢板。超高强度耐候钢板的一种实例通过包括如下的步骤制成:(a)准备熔融钢熔体,其包括:(i)以重量计,0.20%和0.40%之间的碳、小于1.0%的铬、0.7%和2.0%之间的锰、0.10%和0.50%之间的硅、0.1%和1.0%之间的铜、小于或等于0.12%的铌、小于0.5%的钼、0.5%和1.5%之间的镍,且为含有小于0.01%铝的硅镇静的,以及(ii)余量为铁和由熔炼产生的杂质;(b)以大于10.0mw/m2的热通量凝固成小于或等于2.5mm的厚度的钢板并且将所述板在快速冷却前在非氧化气氛中以大于15℃/s的冷却速率冷却至1080℃以下且ar3温度以上;(c)将薄铸钢带高摩擦轧制至铸态厚度的15%和50%之间压下率的热轧厚度,产生主要不含、基本上不含或不含原奥氏体晶界凹坑且具有抹平图案的热轧的钢带;和(d)快速冷却以形成具有拥有以体积计至少75%马氏体或至少75%马氏体加贝氏体的微观结构、700和1600mpa之间的屈服强度、1000和2100mpa之间的抗拉强度、以及1%和10%之间的伸长率的钢板。此处和在本公开内容中的其它地方,伸长率意指总伸长率。“快速冷却”意指以大于100℃/s的速率冷却至100和200℃之间。将添加有镍的本发明组合物快速冷却实现最高达大于95%的马氏体相钢带。在一个实例中,快速冷却形成具有拥有以体积计至少95%马氏体或至少95%马氏体加贝氏体的微观结构的钢板。镍的添加必须足以将
‘
包晶点’转移成远离否则将存在于未添加镍的相同组合物中的碳区域。具体地,所述组合物中的镍被认为有助于将包晶点转移成远离碳区域和/或提高所述组合物的包晶点的转变温度,这似乎抑制缺陷并且产生无缺陷的超高强度耐候钢板。
[0200]
将超高强度耐候钢高摩擦轧制进一步改善超高强度耐候钢的成形性。成形性的度量由astm a370弯曲测试标准阐述。在实施方式中,本公开内容的超高强度耐候钢将通过3t 180度弯曲测试并且将始终如此。特别地,高摩擦轧制由原奥氏体晶界凹坑在剪切下通过塑性形变产生抹平。以抹平图案为特征的这些伸长的表面结构对于超高强度耐候钢的性质是合乎需要的。具体地,超高强度耐候钢的成形性因所述抹平图案而改善。
[0201]
钢带可进一步包括以重量计大于0.005%的铌或大于0.01%或0.02%的铌。钢带可包括以重量计大于0.05%的钼或大于0.1%或0.2%的钼。钢带可为硅镇静的,包含以重量计小于0.008%的铝或小于0.006%的铝。该熔融熔体可具有5
‑
70ppm之间的游离氧含量。钢带可具有大于50ppm的总氧含量。夹杂物包括典型地其中50%为小于5μm尺寸的mnosio2并且具有增强微观结构演变和由此的带机械性质的潜力。
[0202]
该熔融熔体可以大于10.0mw/m2的热通量凝固成厚度为小于2.5mm的钢带,并且在非氧化气氛中以大于15℃/s的冷却速率冷却至1080℃以下且ar3温度以上。非氧化气氛为典型地惰性气体例如氮气或氩气或其混合物的气氛,其包含以重量计小于约5%氧气。
[0203]
在一些实施方式中,钢带中的马氏体可来自于晶粒尺寸大于100μm的奥氏体。在其它实施方式中,钢带中的马氏体可来自于晶粒尺寸大于150μm的奥氏体。以大于10mw/m2的热通量的快速凝固使得能够产生响应于在随后热轧后的受控冷却的奥氏体晶粒尺寸以实现无缺陷的带的制造。
[0204]
如以上指出的,本组实例的钢带可包括具有马氏体或马氏体加贝氏体的微观结构。马氏体在碳钢中通过奥氏体的快速冷却或淬火而形成。奥氏体具有称为面心立方(fcc)的特定晶体结构。若容许自然冷却,则奥氏体转变成铁素体和渗碳体。然而,当将奥氏体快速冷却或淬火时,面心立方奥氏体转变成被碳过饱和的高度应变的体心四方(bct)形式的铁素体。作为结果的剪切形变产生大量位错,这是钢的主要强化机制。在冷却期间当奥氏体达到马氏体起始温度且母体奥氏体变得热力学不稳定时马氏体反应开始。随着样品被淬火,越来越大百分比的奥氏体转变成马氏体直至达到较低的转变温度,此时转变完成。
[0205]
然而,马氏体钢易于产生在由低摩擦条件轧制钢形成的冷却的薄钢带的热轧的外表面上观察到的大的原奥氏体晶界凹坑。酸洗或酸蚀刻的步骤放大导致缺陷和间隔的这些瑕疵。现引入高摩擦轧制作为克服对于低摩擦条件轧制马氏体钢确认的问题的替代方案。高摩擦轧制产生抹平的边界(晶界)图案。抹平的边界图案在本文中可更通常地称为抹平图案。另外,抹平的边界图案可替代地描述性地称为鱼鳞图案。
[0206]
正如依赖于以上的超高强度耐候钢产生产品形状和构造例如以上描述的桩那样,很多产品可由本文中描述的类型的高摩擦轧制高强度耐候钢板产生。如上文那样,可由高摩擦轧制高强度耐候钢板制造的产品的一个实例包括钢桩。在一个实例中,钢桩包括由以上描述的各种碳合金钢带冷轧形成的腹板和一个或多个凸缘。钢桩可进一步包括长度,其中所述腹板和所述一个或多个凸缘使所述长度延伸。使用时,将钢桩的长度迫进到土地或土壤中以提供结构底座。使用夯例如活塞或锤子将钢桩迫进到土地或土壤中。夯可为桩驱动器的一部分并且至少受桩驱动器驱动。夯撞击或冲击钢桩,迫使钢桩进入到土地或土壤中。由于冲击,先前的钢桩在夯的冲击下可翘曲或变形。为避免对先前的钢桩的翘曲或损害,将桩驱动器的rpm或力维持在损害阈值以下。本发明钢桩已经说明与先前的钢桩相比使对钢桩施加的rpm或力增大而未使钢桩翘曲或损害的能力,如由所述钢桩的强度性质所反
映的。具体地,如测试的,尺度特征相当的先前的钢桩被驱动并且结构上遭破坏,其中本公开内容的钢桩提供25%的rpm增幅。而且,先前的钢桩另外不是耐候钢。因此,先前的钢桩由于其放置在外部条件(包括土地和土壤条件)中而易受腐蚀。再次,本发明钢桩提供对于经受住这些条件所必需的腐蚀指数。对于这样的产品,本发明的强度性质和腐蚀性质之前尚未组合地见到过。
[0207]
在一个实例中,钢桩可由以小于或等于2.5mm铸造厚度的本实例的碳合金钢带铸件形成。在另一实例中,钢桩可由小于或等于2.0mm的本实例的钢带形成。在甚至又一实例中,钢桩可由厚度为1.4mm
‑
1.5mm之间或1.4mm或1.5mm的本实例的钢板形成。钢桩可为槽形例如c槽形、箱槽形、双槽形等。钢桩可另外地或替代地为工字形部件、角形、结构t形、中空结构截面形、双角形、s
‑
形状、管等。而且,这些部件的很多可连接在一起例如焊接在一起,以形成单钢桩。本文中认识到,另外的产品可由高摩擦轧制超高强度耐候钢板制成。
[0208]
高摩擦轧制的高强度马氏体钢
[0209]
在本公开内容的实施方式中,还公开了高强度马氏体钢板。下面的高强度马氏体钢板实例可另外地包括耐候特性。因此,本文中的高强度马氏体钢板实例由于这样的性质也可称为超高强度耐候钢板。马氏体钢被越来越多地用在需要高强度的应用中诸如汽车工业中。马氏体钢提供汽车工业所必需的强度,同时减少能耗和改善燃料经济性。马氏体在碳钢中通过奥氏体的快速冷却或淬火而形成。奥氏体具有称为面心立方(fcc)的特定晶体结构。若容许自然冷却,则奥氏体转变成铁素体和渗碳体。然而,当将奥氏体快速冷却或淬火时,面心立方奥氏体转变成被碳过饱和的高度应变的体心四方(bct)形式的铁素体。作为结果的剪切形变产生大量位错,这是钢的主要强化机制。在冷却期间当奥氏体达到马氏体起始温度且母体奥氏体变得热力学不稳定时马氏体反应开始。随着样品被淬火,越来越大百分比的奥氏体转变成马氏体直至达到较低的转变温度,此时转变完成。
[0210]
然而,马氏体钢易于产生在由低摩擦条件轧制钢形成的冷却的薄钢带的热轧的外表面上观察到的大的原奥氏体晶界凹坑。酸洗或酸蚀刻步骤放大导致缺陷和间隔的这些瑕疵。现引入高摩擦轧制作为用于克服对于低摩擦条件轧制马氏体钢确认的问题的替代方案,然而,还已经观察到高摩擦轧制产生不期望的表面光洁度。特别地,高摩擦轧制产生与不均匀的表面光洁度组合的抹平的边界图案。抹平的边界图案可更通常地在本文中称为抹平图案。另外,抹平的边界图案可替代地描述性地称为鱼鳞图案。然后,具有抹平图案的不均匀的表面光洁度(例如当薄钢带经历随后的酸蚀刻时)变得易于截留酸和/或导致过度腐蚀,从而导致过量的点蚀。鉴于此,对于一些钢带或产品例如汽车应用中使用的马氏体钢板,有必要进行另外的表面处理以提供如下表面:其中从该表面除去抹平图案和/或不均匀的表面光洁度。
[0211]
为减少或消除抹平图案和/或不均匀的表面光洁度,薄钢带在热轧机后经历表面均匀化工艺。表面均匀化工艺的实例包括喷磨例如诸如通过使用砂轮、喷丸、喷砂、湿法喷磨、其它磨料加压施加等。表面均匀化工艺的一种具体实例包括环保酸洗的(eco
‑
pickled)表面(本文中称为“eps”)。表面均匀化工艺的其它实例包括将磨料介质强有力施加到钢带表面上以将钢带表面均匀化。对于强有力施加,还可依赖于加压组分(组件)。例如,流体可推进磨料介质。如本文中使用的流体包括液体和空气。另外地或替代地,机械装置可提供强有力施加。表面均匀化工艺在薄铸钢带达到室温后发生。也就是说,表面均匀化工艺不在使
用热轧机的线上工艺中发生。表面均匀化工艺可在与热轧机和/或双铸造轧机分开的位置或从其离线地发生。在一些实例中,表面均匀化工艺可在卷取后发生。
[0212]
如本文中使用的,表面均匀化工艺将表面改变成不含抹平图案或消除抹平图案。不含抹平图案或其中抹平图案已经被消除的薄钢带表面为通过120小时腐蚀测试而没有任何表面点蚀的表面。未经历表面均匀化工艺的试样在120小时腐蚀测试期间在24小时后由于表面腐蚀而破裂(断裂)。图6为显示使用eps进行表面均匀化的高摩擦热轧钢带的图像。作为对比,图7为显示尚未经历表面均匀化工艺的具有抹平图案的高摩擦热轧钢带表面的图像。如以上指出的,抹平图案,除非其通过表面均匀化工艺被除去,否则可在酸蚀刻时截留酸并且因此易于过度点蚀和/或腐蚀。总之并且如本文中使用的,已经经历表面均匀化的表面为不含先前通过高摩擦轧制条件形成的抹平图案的表面。
[0213]
在热轧后,将热轧的薄钢带冷却。在每个实施方式中,钢带在冷却后经历表面均匀化工艺。认识到,冷却可通过任意已知方式实现。在某些情况下,当冷却薄钢带时,将薄钢带冷却到等于或小于马氏体起始转变温度m
s
的温度,以由此由薄钢带内的原奥氏体形成马氏体。
[0214]
高强度马氏体钢板的一个实施方式通过包括如下的步骤制成:(a)准备熔融钢熔体,其包括:(i)以重量计,0.20%和0.40%之间的碳、小于1.0%的铬、0.7%和2.0%之间的锰、0.10%和0.50%之间的硅、0.1%和1.0%之间的铜、小于或等于0.12%的铌、小于0.5%的钼、0.5%和1.5%之间的镍,且为含有小于0.01%铝的硅镇静的,以及(ii)余量为铁和由熔炼产生的杂质;(b)以大于10.0mw/m2的热通量凝固成厚度小于或等于2.5mm的钢板并且将所述板在快速冷却前在非氧化气氛中以大于15℃/s的冷却速率冷却至1080℃以下且ar3温度以上;(c)将薄铸钢带高摩擦轧制至铸态厚度的15%和50%之间压下率的热轧厚度,产生不含原奥氏体晶界凹坑的热轧钢带;(d)快速冷却以形成具有拥有以体积计至少75%马氏体或至少75%马氏体加贝氏体的微观结构、700和1600mpa之间的屈服强度、1000和2100mpa之间的抗拉强度、以及1%和10%之间的伸长率的钢板;和将高摩擦热轧的钢带进行表面均匀化,产生具有不含抹平图案的一对相反的高摩擦热轧的均匀化表面的高摩擦热轧钢带。此处和在本公开内容中的其它地方,伸长率意指总伸长率。“快速冷却”意指以大于100℃/s的速率冷却至100和200℃之间。将添加有镍的本发明组合物快速冷却实现最高达大于95%马氏体相的钢带。在一个实例中,快速冷却形成具有拥有以体积计至少95%马氏体或至少95%马氏体加贝氏体的微观结构的钢板。镍的添加必须足以将
‘
包晶点’转移成远离否则将存在于未添加镍的相同组合物中的碳区域。具体地,组合物中的镍被认为有助于将包晶点转移成远离碳区域和/或提高组合物的包晶点的转变温度,这似乎抑制缺陷并且导致无缺陷的高强度马氏体钢板。
[0215]
高摩擦轧制高强度马氏体钢的实例的另外变型于下。在一些实例中,钢带可包括基本上不含原奥氏体晶界凹坑和抹平图案的一对相反的高摩擦热轧的均匀化表面。在又一实例中,钢带可进一步包括主要不含原奥氏体晶界凹坑和抹平图案的一对相反的高摩擦热轧的均匀化表面。在这些实例的每个中,表面可具有不超过2.5μm的表面粗糙度(ra)。
[0216]
在一些实例中,进一步可将薄钢带在150℃和250℃之间的温度下回火2
‑
6小时。将钢带回火提供改善的伸长率以及最少的强度损失。例如,在如本文中描述的回火后,具有1250mpa的屈服强度、1600mpa的抗拉强度和2%的伸长率的钢带被改善为1250mpa的屈服强
度、1525mpa的抗拉强度和5%的伸长率。
[0217]
钢带可进一步包括以重量计大于0.005%的铌或大于0.01%或0.02%的铌。钢带可包括以重量计大于0.05%的钼或大于0.1%或0.2%的钼。钢带可为硅镇静的,包含以重量计小于0.008%的铝或小于0.006%的铝。熔融熔体可具有5
‑
70ppm的游离氧含量。钢带可具有大于50ppm的总氧含量。夹杂物包括典型地其中50%为小于5μm尺寸的mnosio2并且具有增强微观结构演变和由此的带机械性质的潜力。
[0218]
可将熔融熔体以大于10.0mw/m2的热通量凝固成厚度小于2.5mm的钢带,并且在非氧化气氛中以大于15℃/s的冷却速率冷却至1080℃以下且ar3温度以上。非氧化气氛为典型地惰性气体例如氮气或氩气或其混合物的气氛,其包含以重量计小于约5%氧气。
[0219]
在一些实施方式中,钢带中的马氏体可来自于晶粒尺寸大于100μm的奥氏体。在其它实施方式中,钢带中的马氏体可来自于晶粒尺寸大于150μm的奥氏体。以大于10mw/m2的热通量的快速凝固使得能够产生响应于在随后热轧后的受控冷却的奥氏体晶粒尺寸以实现无缺陷带的制造。
[0220]
可提供高摩擦轧制钢板以在热冲压应用中使用。通常,为了在热冲压应用中使用而依赖的钢板为不锈钢组合物或需要铝
‑
硅耐腐蚀涂层。在热冲压应用中,在维持高强度性质和有利的表面结构特性的同时,耐腐蚀保护层为期望的。本发明高摩擦轧制组合物已经实现所述期望的性质而不依赖于不锈钢组合物或另外地提供铝
‑
硅耐腐蚀涂层。相反,本发明高摩擦轧制组合物依赖于如以上各种实例中说明的镍、铬和铜的混合物来改善耐腐蚀性。在热冲压应用中,高摩擦轧制钢板经历在900℃和930℃之间以6分钟和10分钟之间的时长的奥氏体化条件。在一个实例中,高摩擦轧制钢板经历在900℃以6分钟时长的奥氏体化条件。在另一实例中,高摩擦轧制钢板经历在900℃以10分钟时长的奥氏体化条件。在又一实例中,高摩擦轧制钢板经历在930℃以6分钟时长的奥氏体化条件。在甚至又一个实例中,高摩擦轧制钢板经历在930℃以10分钟时长的奥氏体化条件。下表8说明高摩擦轧制钢板的性质维持在对于热冲压应用的1500mpa的最小抗拉强度、1100mpa的最小屈服强度、和3%的最小伸长率以上。
[0221]
表8
[0222]
奥氏体化条件抗拉强度(mpa)屈服强度(mpa)伸长率(%)900℃,6分钟1546.981155.067.3900℃,6分钟1576.651154.377.0900℃,10分钟1591.141168.866.4900℃,10分钟1578.031152.306.6930℃,6分钟1566.301146.097.3930℃,6分钟1566.991178.526.5930℃,10分钟1509.031109.526.6930℃,10分钟1521.451129.536.4
[0223]
在这些实例中,为在热冲压应用中使用而提供的钢板可包括以上公开的钢板的实例的任一个的组成,但为可仍然未淬火的钢板。特别地,为在热冲压应用中使用而提供的钢板可通过包括如下的步骤制成:(a)准备熔融钢熔体,其包括:(i)以重量计,0.20%和0.40%之间的碳、小于1.0%的铬、0.7%和2.0%之间的锰、0.10%和0.50%之间的硅、
0.1%和1.0%之间的铜、小于或等于0.12%的铌、小于0.5%的钼、0.5%和1.5%之间的镍,且为含有小于0.01%铝的硅镇静的,以及(ii)余量为铁和由熔炼产生的杂质;(b)以大于10.0mw/m2的热通量凝固成厚度为小于或等于2.5mm的钢板并且将所述板在快速冷却前在非氧化气氛中以大于15℃/s的冷却速率冷却至1080℃以下且ar3温度以上;(c)将薄铸钢带高摩擦轧制至铸态厚度的15%和50%之间压下率的热轧厚度,产生主要不含、基本上不含或不含原奥氏体晶界凹坑且具有抹平图案的热轧钢带;和(d)以小于100℃/s冷却以形成具有主要为贝氏体的微观结构的钢板。也就是说,为在热冲压应用中使用而提供的钢板可为除如下外的以上公开的钢板的实例的任一个:未将钢板快速冷却并且因此,未形成主要或基本上具有马氏体或马氏体加贝氏体的微观结构。相反,为热冲压应用中使用而提供的钢板以小于100℃/s冷却。
[0224]
热轧,包括低摩擦热轧和高摩擦热轧
[0225]
下面进一步描述如本公开内容的以上实例中依赖的热轧(和更具体地,低摩擦轧制和高摩擦轧制)。如下描述的构思可按需应用到以上提供的实例以实现各分别实例的性质。通常,在每个热轧实例中,在将带冷却,例如在具体实施方式中冷却至钢中的奥氏体转变成马氏体的温度前,将带传送通过热轧机以减小铸态厚度。在特定情形中,热凝固带(铸造带)可在处于大于1050℃和在某些情况下最高达1150℃的进入温度的同时传送通过热轧机。在带离开热轧机后,将带冷却,例如在某些示例性情况中冷却到钢中的奥氏体转变成马氏体的温度,这通过冷却到等于或小于马氏体起始转变温度ms的温度进行。在某些情况下,该温度≤600℃,其中马氏体起始转变温度m
s
取决于具体组成。冷却可通过利用任何已知机制(包括以上描述的机制)的任何已知方法而实现。在某些情况下,冷却足够快速以避免可观的铁素体的始发(出现,onset),其也受组成的影响。在这样的情况下,例如,冷却配置成以每秒约100℃至200℃的速率降低带的温度。
[0226]
热轧使用一对或多对反向的工作辊进行。工作辊常用于减小基材例如板或带的厚度。这通过将基材传送通过布置在该对工作辊之间的间隙而实现,该间隙小于基材的厚度。该间隙也称为辊缝。在热加工期间,由工作辊对基材施加力,从而在基材上施加轧制力以由此实现基材厚度的期望压下率。这样做时,当基材平移通过该间隙时在基材和各工作辊之间产生摩擦。该摩擦称为辊缝摩擦。
[0227]
传统上,期望是,在钢板和带的热轧期间减小缝摩擦。通过减小缝摩擦(和因此的摩擦系数),使轧制负荷和辊磨损减小而延长机器寿命。已经采用多种技术来减小辊缝摩擦和摩擦系数。在某些示例性情形中,将薄钢带润滑以减小辊缝摩擦。润滑可采取如下形式:施加到辊和/或薄钢带的油,或在热轧前沿着薄钢带外部形成的氧化皮。通过使用润滑,热轧可在低摩擦条件下发生,其中辊缝的摩擦系数(μ)小于0.20。
[0228]
在一个实例中,摩擦系数(μ)基于由hatch对于具体的一组工作辊开发的热轧模型而测定。该模型显示于图8中,其提供沿着x
‑
轴的以百分比计的薄钢带厚度压下率和沿着y
‑
轴的以kn/mm计的比力“p”。比力p为由工作辊施加到基材的法向(垂直)力。该模型包括五(5)条曲线,各自表示摩擦系数并且提供压下率和工作辊力之间的关系。对于各摩擦系数,基于测量的压下率获得预期的工作辊力。在操作中,在热轧期间,目标摩擦系数通过调节工作辊润滑而预设,目标压下率通过为满足特定的客户订单而在轧机出口处需要的期望带厚度而设定,并且将调节实际的工作辊力以实现目标压下率。图8显示对于具体的摩擦系数而
言为实现目标压下率所需的典型力。
[0229]
在某些示例性情形中,摩擦系数等于或大于0.20。在其它示例性情形中,摩擦系数等于或大于0.25、等于或大于0.268或等于或大于0.27。认识到,这些摩擦系数在用于奥氏体钢(其为图中显示的实例中使用的钢合金)的某些条件下足以至少从热轧的表面主要或基本上消除原奥氏体晶界凹坑并且产生通过剪切而塑性形成的伸长的表面特征,其中在热轧期间钢为奥氏体但在冷却后形成具有存在的原奥氏体晶粒和原奥氏体晶界凹坑的马氏体。如前所述,可改变各种因素或参数以在某些条件下达成期望的摩擦系数。注意到,对于先前描述的摩擦系数值,对于在热轧前具有5mm或更小的厚度的基材而言,在基材进入该对工作辊并且以45
‑
75米/分钟(m/min)的速率平移或前进时,在进入工作辊的基材的温度大于1050℃、和在某些情况下最高达1150℃的情况下,在热轧期间施加到基材的法向力可为600至2500吨。对于这些摩擦系数,工作辊具有400
‑
600mm的直径。当然,可按需使用在这些参数范围的每个以外的变化以实现不同摩擦系数,如可对于实现本文中描述的热轧的表面特性而言期望的。
[0230]
在一个实例中,热轧在摩擦系数为0.25的高摩擦条件下以60米/分钟(m/min)以22%的压下率在工作辊力近似为820吨的情况下进行。在另一实例中,热轧在摩擦系数为0.27的高摩擦条件下以60米/分钟(m/min)以22%的压下率在工作辊力近似为900吨的情况下进行。
[0231]
如本公开内容的实例中依赖的,薄钢带的热轧当薄钢带在a
r3
温度以上的温度下时进行。ar3温度为在冷却期间奥氏体开始转变为铁素体的温度。也就是说,ar3温度为奥氏体转变点。ar3温度在比a3温度低几度的位置。在ar3温度以下,α铁素体形成。这些温度显示在图9中的示例性cct图中。图9中,a
3 170表示在平衡时铁素体的稳定性结束的上部温度。ar3为在冷却时铁素体的稳定性结束的上限温度。更具体地,ar3温度为在冷却期间奥氏体开始转变为铁素体的温度。也就是说,ar3温度为奥氏体转变点。作为对比,a
1 180表示在平衡时铁素体的稳定性结束的下限温度。
[0232]
还参考图9,铁素体曲线220表示产生1%铁素体的微观结构的转变温度,珠光体曲线230表示产生1%珠光体的微观结构的转变温度,奥氏体曲线250表示产生1%奥氏体的微观结构的转变温度,和贝氏体曲线(b
s
)240表示产生1%贝氏体的微观结构的转变温度。如先前更详细地描述的,马氏体起始转变温度m
s
由马氏体曲线190表示,其中马氏体开始由薄钢带内的原奥氏体形成。图9进一步说明的是表示具有至少50%马氏体的微观结构的50%马氏体曲线200。另外,图9说明表示具有至少90%马氏体的微观结构的90%马氏体曲线210。
[0233]
在图9中显示的示例性cct图中,显示马氏体起始转变温度m
s 190。在传送通过冷却器时,带中的奥氏体转变为马氏体。特别地,在该情形中,将带冷却至600℃以下导致粗奥氏体的转变,其中在马氏体内析出细小的铁碳化物的分布。
[0234]
尽管本发明已经在前面的图和说明书中进行说明和描述,但其应被认为是在特征方面说明性的且非限制性的,将理解,已经显示和描述其仅为说明性的实施方式,并且期望保护落在由所附权利要求所描述的本发明精神内的所有变化和改变。对于本领域技术人员而言,在考虑说明书时,本发明的另外特征将变得明晰。在不背离本发明的精神和范围的情况下可进行改变。